Best Deals on Conveyor Roller for Sale Philippines
The Philippines’ industrial sector is rapidly expanding, driven by a growing demand for efficient and robust logistic solutions. This surge highlights the critical role of conveyor systems, particularly conveyor rollers, in enhancing productivity across various industries. As businesses strive to optimize operations and reduce downtime, the search for reliable conveyor roller for sale philippines becomes increasingly important. These components are vital for the smooth operation of conveyor systems, which in turn supports the scaling and modernization of production facilities in the region.
Types of Conveyor Roller for Sale Philippines Available
Used Conveyor Rollers
Opting for used conveyor rollers provides numerous advantages, particularly in cost savings and sustainability. Here are fifteen benefits of choosing used rollers:
Cost-Effectiveness: Significantly cheaper than new models, used rollers allow for budget allocation to other areas of business.
Eco-Friendliness: Reusing equipment reduces waste and environmental impact.
Immediate Availability: Unlike new orders, used rollers are often readily available with no lead time.
Proven Reliability: Used rollers have been tested in real-world conditions.
Flexibility in Purchase: Often, smaller quantities can be purchased rather than bulk orders.
Ease of Replacement: Compatible with existing systems without the need for extensive modifications.
Variety of Choices: Access to discontinued models or types not available new.
Lower Depreciation: Lesser loss of value over time compared to new equipment.
Tested Durability: Already tested in operational conditions, proving their durability.
Opportunity for Refurbishment: Can be refurbished to extend their life further.
Short-Term Solutions: Ideal for temporary or seasonal use.
Less Stringent Buying Criteria: Less pressure on having the latest technology.
Reduced Initial Investment: Lowers the barrier for startup operations.
Insurance Cost Savings: Lower values can reduce insurance premiums.
Supports Circular Economy: Supports business practices that promote reuse and recycling.
The recommended industries for these used conveyor rollers include:
- Warehousing: Managing inventory and logistics with frequent loading and unloading cycles.
- Agriculture: Handling bulk materials like grains or fertilizers.
- Recycling Facilities: Moving various types of recyclables through sorting processes.
- Manufacturing: Transporting parts and products through different stages of production.
- Food Processing: Applications where high levels of cleanliness are not strictly necessary.
- Construction Materials: Handling robust materials like bricks or tiles.
- Packaging: Integrating into existing packing lines for boxed or bagged goods.
- Event Setup: Useful for temporary setups that require material movement.
Considering used conveyor roller for sale philippines can be a strategic choice for businesses looking to enhance their operations while managing costs and supporting environmental sustainability. This segment of the market provides a practical solution across a diverse range of industries, helping businesses maintain productivity without the high expense of new equipment.
Small Conveyor Rollers
Small conveyor rollers are crucial components in systems where space is limited and precise handling is necessary. These rollers are particularly beneficial in various settings due to their versatility and adaptability. Here are seven key applications where small conveyor rollers are commonly used:
Electronic Component Assembly: Small rollers are ideal for moving delicate electronic parts through assembly lines without causing damage.
Pharmaceutical Packaging: Used in environments where cleanliness and precision are paramount for handling sensitive medical products.
Food and Beverage Production: Useful in processing areas where space is at a premium and gentle handling of food items is necessary to maintain integrity.
Printing and Publishing: Essential for the precise and smooth transport of paper materials through printing presses.
Textile Manufacturing: Facilitates the movement of fabric and other materials through treatment and cutting areas.
Jewelry and Watchmaking: Helps in the meticulous assembly process where components are exceptionally small and fragile.
Laboratory Automation: Supports the transportation of samples and reagents in compact automated analyzers and other lab equipment.
Regarding the types and materials of small conveyor rollers available, these are designed to cater to a broad spectrum of industrial requirements:
Types of Small Conveyor Rollers
Gravity Rollers: Operate by gravity or manual force, ideal for lightweight items.
Motorized Rollers: Powered rollers that provide controlled movement and can adjust speeds based on the process requirements.
Guide Rollers: Ensure materials stay aligned on the conveyor, critical in precise applications.
Grooved Rollers: Designed to handle belts within the roller frame, suitable for light to medium loads.
Spring Loaded Rollers: Allow for easy installation and maintenance, automatically adjusting to varying loads.
Materials Used in Small Conveyor Rollers:
Steel: Offers durability and strength, suitable for a wide range of industrial applications.
Stainless Steel: Best for applications requiring corrosion resistance, such as in food processing or pharmaceuticals.
Plastic: Provides a lightweight and corrosion-resistant option, often used in sterile environments.
Rubber Coated: Reduces noise and minimizes damage to delicate items during transport.
Aluminum: Lightweight and corrosion-resistant, ideal for applications requiring ease of handling and moderate strength.
Small conveyor roller for sale philippines are widely sought after for their flexibility and efficiency in various industries, especially where space constraints exist. These rollers enhance productivity and are essential for the seamless operation of numerous small-scale and precision-focused industries.
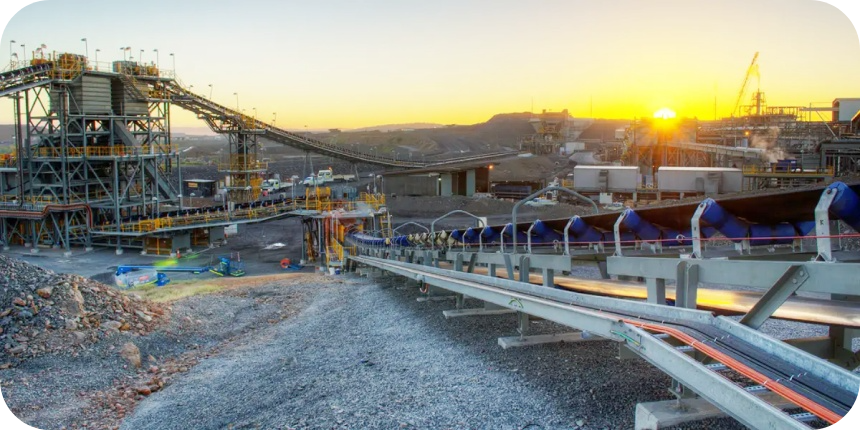
Industrial Conveyor Rollers
Industrial conveyor rollers are specifically designed to meet the rigorous demands of heavy-duty operational environments. These rollers are integral components in industries such as manufacturing, bulk material handling, and heavy machinery operations. Here are twelve key features and design elements that define industrial conveyor rollers, along with an overview of their durability and performance metrics:
Key Features and Designs
High Load Capacity: Built to support substantial weight without compromise, ensuring continuous operation even under high-load conditions.
Robust Construction: Typically manufactured from heavy-duty metals like steel or heavy-gauge stainless steel to withstand tough industrial environments.
Impact Resistance: Engineered to endure impacts from bulky or rough materials, reducing wear and tear and extending service life.
Precision Bearings: Equipped with high-quality, sealed bearings that minimize friction and maximize efficiency, crucial for maintaining smooth operations.
Enhanced Sealing Systems: Advanced sealing mechanisms protect the roller internals from dust, debris, and other contaminants common in industrial settings.
Temperature Resistance: Capable of operating effectively in a range of temperatures, making them suitable for industries like steelworks or foundries.
Chemical Resistance: Materials and coatings that resist corrosion from chemicals, beneficial in sectors like chemical processing or waste treatment.
Variable Sizes and Configurations: Available in various diameters and lengths to suit different conveyor setups and material handling needs.
Customization Options: Can be customized with features such as grooves, sprockets, or other modifications to meet specific operational requirements.
Low Maintenance Design: Engineered for ease of maintenance to ensure minimal downtime and lower long-term operating costs.
Energy Efficiency: Designed to operate with minimal energy consumption, contributing to reduced operational costs.
Speed Capabilities: Capable of handling varying speeds, essential for production lines that require different processing times.
Durability and Performance Metrics
- Lifespan: Industrial conveyor rollers are built to last, often designed for years of service with minimal maintenance.
- Load Performance: Tested to handle specified maximum loads without deformation or failure.
- Operational Efficiency: Demonstrates high efficiency in power transfer and load movement, ensuring operational cost savings.
- Wear Resistance: Materials and surface treatments are chosen for their ability to resist wear under constant use in abrasive environments.
These features make industrial conveyor rollers a reliable choice for businesses in the Philippines looking to maintain high levels of productivity and efficiency in demanding industrial applications. Conveyor roller for sale philippines offers a range of options that can be tailored to meet the specific needs of various industrial sectors, ensuring that each system achieves optimal performance and longevity.
Heavy Duty Conveyor Rollers
Heavy duty conveyor rollers are engineered to meet the stringent demands of industries that manage high-load, abrasive, and often unevenly distributed materials. These rollers are particularly suited for sectors like mining, construction, quarrying, steel processing, and heavy manufacturing. The robust construction of these rollers ensures they can withstand the harsh environments and heavy operational demands typical of these industries.
Suitability for Heavy-Load Industries
- Mining: Essential for transporting large quantities of raw extracted materials, which may vary greatly in size and weight.
- Construction: Used for moving building materials across construction sites, handling everything from packed cement to large stones and beams.
- Quarrying: Critical for the movement of large rocks and aggregates in rough quarry environments.
- Steel Processing: Capable of handling heavy steel products, such as beams and coils, under extreme temperatures.
- Heavy Manufacturing: Supports the transportation of heavy machinery parts and products within production facilities.
- Bulk Material Handling: Ideal for industries like cement and grain processing, where large volumes of materials need to be moved efficiently.
Construction Materials and Load Capacity
- Materials Used: Heavy duty conveyor rollers are typically constructed from thick steel or reinforced composites to provide superior strength and durability. The choice of material depends on the specific environmental conditions, such as exposure to chemicals, moisture, or extreme temperatures.
- Design Features: These rollers may include reinforced bearings and heavy-duty shafts to support additional weight. The rollers are often designed with a larger diameter to distribute the load more evenly, reducing stress on individual rollers.
- Load Capacity: Heavy duty rollers are designed to handle significantly higher load capacities compared to standard rollers. They are tested rigorously to ensure performance under continuous heavy loads, often exceeding several tons depending on the application.
- Durability: The durability of these rollers is enhanced through protective coatings and treatments that resist wear, corrosion, and buildup of materials, extending the operational life and reducing maintenance needs.
Manufacturers about Conveyor Roller for Sale philippines
The Philippines boasts a robust industrial sector that heavily relies on efficient conveyor systems, making the role of conveyor roller manufacturers critical. These manufacturers offer a wide range of products to meet diverse operational needs across various industries, from mining and agriculture to manufacturing and logistics. Here’s a detailed look at the landscape of conveyor roller manufacturers in the Philippines, focusing on their product offerings and the customization options they provide.
Overview of Leading Manufacturers and Their Product Offerings
Philbelt Conveyor Belts: Specializing in heavy-duty belts and rollers for industrial uses.
Beta Equipment Sales Corporation: Offers a comprehensive range of conveyor products, including rollers and systems for bulk handling.
UNITEC Enterprise Systems Corporation: Known for their innovative conveyor solutions tailored to food processing and pharmaceutical industries.
R. Dan and Co., Inc.: Provides a wide array of conveyor rollers and related machinery, serving primarily the paper and pulp industries.
Conveyor World System: Specializes in custom conveyor systems and rollers for small to medium enterprises.
Elixir Industrial Equipment: Offers both standard and custom-designed conveyor rollers for various sectors.
ESCO Philippines Inc.: Focuses on heavy-duty conveyor systems and rollers suitable for mining and quarrying.
Integrated Conveying Systems: Delivers high-performance conveyor rollers designed to withstand harsh industrial environments.
Royal Jade Machinery Philippines Corp.: Provides innovative conveyor solutions with a focus on automation and efficiency.
Powertrans Manufacturing: Specializes in the design and manufacture of custom conveyor rollers and systems for heavy loads.
Tsubaki Conveyor Systems: Offers a range of durable and reliable conveyor rollers, particularly for automotive and manufacturing industries.
Fastrack Conveyors: Known for their quick delivery and installation services along with customizable conveyor options.
Mechanical Handling Equipment Company Inc.: Offers a broad range of conveyor rollers designed to improve operational workflow.
Prime Global Corporation: Provides high-quality rollers that cater to the specific needs of diverse industrial applications.
Syscore Conveyor and Automation: Focuses on providing innovative and efficient conveyor rollers for logistics and distribution centers.
Customization Options and Support Provided by Local Manufacturers
- Tailored Designs: Most manufacturers offer the ability to customize conveyor rollers based on specific industry requirements. This includes adjusting roller diameters, lengths, and materials to suit particular applications.
- Material Choices: Depending on the operational environment, manufacturers provide rollers made from steel, stainless steel, plastic, or coated with special materials for additional durability and performance.
- Technical Support: Comprehensive technical support is available, including assistance with design, installation, and maintenance. This ensures that the conveyor systems operate efficiently and continue to meet the evolving needs of businesses.
- After-Sales Service: Robust after-sales service including maintenance, repairs, and parts replacement, which is crucial for minimizing downtime and extending the lifespan of the equipment.
- Consultation Services: Many manufacturers also offer consultation services to help businesses optimize their conveyor system setups and improve operational efficiencies.
The conveyor roller manufacturers in the Philippines are well-equipped to meet the growing demands of the industrial sector, providing high-quality products and services that are crucial for the smooth operation of businesses across the country. With their focus on innovation and customer service, these manufacturers play a pivotal role in the industrial landscape of the Philippines.
Conveyor roller for Sale Philippines of Conveyor Machine Integration
Integrating conveyor rollers into full conveyor systems is a critical process that involves meticulous planning, design, and execution to ensure seamless operation and maximum efficiency. This section explores how conveyor rollers are integrated within broader conveyor systems, highlighting the importance of compatibility and thoughtful system design. The focus here is to provide insights into how these components work together to form cohesive material handling solutions, specifically addressing the conveyor roller for sale in the Philippines market.
Integration of Conveyor Rollers into Full Systems
Conveyor rollers are fundamental elements of conveyor systems, serving as the interface between the conveyor belt and the mechanism that drives it. The integration process begins with the selection of the appropriate type of rollers that match the specific requirements of the application, considering factors such as load capacity, operational environment, and material characteristics.
- Design Considerations: The design of the conveyor system dictates the configuration and spacing of the rollers. Engineers must ensure that the rollers are spaced closely enough to support the belt and the goods it carries, but not so close as to increase friction and wear unnecessarily.
- Selection of Roller Type: Depending on the application, different types of rollers may be used. For instance, gravity rollers might be selected for light applications, whereas motor-driven rollers could be necessary for heavier or more complex tasks.
- Mounting and Installation: Proper installation is crucial to the system’s functionality. Rollers must be precisely aligned to ensure smooth operation and to prevent the belt from wandering or slipping off the tracks.
- Integration with Drive Systems: Rollers must be compatible with the drive system, which may involve direct connection to motors or linkage via belts and chains. Ensuring that the rollers and the drive system are synchronized is essential to avoid discrepancies in speed and torque that could lead to system failures.
- System Testing and Optimization: Once assembled, the entire conveyor system is tested under various loads and operational conditions. Adjustments are made to optimize performance, such as modifying roller alignment, tensioning the belt, or fine-tuning the motor outputs.
Importance of Compatibility and System Design
The effectiveness of a conveyor system hinges on the compatibility between all its components and the overall system design. This synergy is crucial not only for operational efficiency but also for the longevity and reliability of the system.
Material Compatibility: The materials used in the rollers must be suitable for the goods they will carry. For example, chemical resistance might be necessary for rollers in a pharmaceutical plant, or high-temperature tolerance might be required in a steel processing facility.
Load and Speed Compatibility: The rollers must be capable of handling the expected load without deforming or failing. Similarly, they should be able to operate at speeds that match the throughput requirements of the facility.
Environmental Considerations: The design must also account for the operating environment, including factors like temperature, humidity, and exposure to corrosive substances. These factors influence the choice of materials and protective coatings for the rollers.
Maintenance Requirements: A well-designed system considers ease of maintenance. Rollers should be easily accessible for inspection and replacement. Systems designed with modular components allow for quicker repairs and less downtime.
Future Scalability: Effective system design anticipates future needs. This might include provisions for easy expansion or reconfiguration of the conveyor system to accommodate new products or increased production capacity.
Conveyor Roller for Sale Philippines of Purchasing and Installation
When considering the acquisition and setup of conveyor rollers, it’s crucial to make informed decisions to ensure efficiency, durability, and cost-effectiveness. This section provides detailed guidance on selecting the right conveyor rollers and offers practical advice on installation, specifically focusing on conveyor roller for sale in the Philippines.
Tips for Selecting the Right Conveyor Roller
- Assess Load Requirements: Understand the maximum weight each conveyor roller will need to support. This ensures that the rollers you choose can handle the load without failure.
- Consider the Roller Material: Select material based on the environment in which the rollers will operate. For instance, stainless steel might be necessary for corrosive environments, while plastic rollers might suffice for lighter applications.
- Determine the Roller Diameter: Larger diameters are generally capable of carrying heavier loads and reduce the rotation speed, which can prolong the life of the roller.
- Check the Roller Length: Ensure the roller length matches the width of the materials to be conveyed to provide proper support and balance.
- Understand the Speed Requirements: The speed at which your conveyor will operate should influence the type of rollers you purchase, as different bearings are designed to accommodate varying speeds.
- Analyze the Operating Environment: Factors like temperature, humidity, and exposure to chemicals should guide your roller material and coating decisions.
- Plan for Maintenance and Accessibility: Choose rollers that are easy to maintain and replace. Consider the ease of access to the conveyor system for regular maintenance tasks.
- Review Manufacturer Specifications: Always check that the rollers meet industry standards and specifications. Rely on products from reputable manufacturers with good warranties and customer support.
- Seek Custom Solutions if Necessary: If standard rollers do not meet your needs, inquire about custom solutions that can be tailored to your specific requirements.
- Compare Costs and Lifespan: Evaluate the total cost of ownership, including initial purchase, maintenance, and potential downtime costs, against the expected lifespan of the rollers.
Installation Advice and Common Pitfalls
- Pre-Installation Check: Before installation, inspect all components for defects or shipping damages to avoid delays during setup.
- Accurate Alignment: Ensure that the conveyor frame and rollers are perfectly aligned to prevent uneven wear and tear on the belt and rollers.
- Proper Tensioning: Incorrect belt tension can lead to slippage and premature wear. Adjust the tension according to the manufacturer’s recommendations.
- Regular Testing: After installation, test the conveyor system with varying loads to check for any issues in roller movement or belt alignment.
- Avoid Overloading: Never exceed the maximum load capacity as it can lead to roller damage and system failure.
- Educate Your Team: Make sure that those involved in operating and maintaining the conveyor are well-trained and aware of the system’s capabilities and limits.
Common Pitfalls to Avoid
- Ignoring Environmental Factors: Not considering the impact of environmental factors on material choice can lead to rapid degradation of the rollers.
- Skimping on Quality: Opting for cheaper, lower-quality rollers can result in higher long-term costs due to increased maintenance and replacements.
- Neglecting Regular Maintenance: Failing to schedule regular inspections and maintenance can lead to critical failures and costly downtime.
- Improper Installation: Poorly installed rollers can cause operational inefficiencies and potential hazards in the workplace.
By following these tips and being aware of common installation pitfalls, businesses in the Philippines can optimize their investment in conveyor rollers, ensuring a reliable, efficient conveyor system that meets their operational demands.
Interested in our conveyor rollers? Fill out the form for more details.
FAQs about Conveyor Roller for Sale Philippines
The rollers on a conveyor are commonly referred to as “conveyor rollers.” These are cylindrical components that fit within the frame of a conveyor belt system to support and move the conveyor belt along smoothly. Conveyor rollers can be designed to handle various types of loads, speeds, and applications. They play a critical role in the functionality of a conveyor system, aiding in the transportation of materials from one point to another efficiently. The rollers help reduce the friction between the belt and the structure, allowing the belt to move with minimal resistance and wear.
The standard size of a conveyor roller typically varies depending on the application and the load requirements. However, common diameters for conveyor rollers range from 25mm to 102mm. The length of the roller can also vary widely based on the width of the conveyor belt it needs to support, with common sizes ranging from a few hundred millimeters to over a meter. It is essential to select the right diameter and length to ensure proper functionality of the conveyor system, as these dimensions directly influence the load capacity and the distribution of weight across the system.
Making a conveyor roller involves several key steps that require precision and attention to detail to ensure that the roller is effective and durable. Here’s a basic outline of the process:
Material Selection: Choose a material that suits the application (e.g., steel, stainless steel, or plastic). The material should support the load and withstand the operational environment.
Cutting: Cut the material to the required length of the roller.
Machining: Machine the ends of the roller to ensure they are smooth and fit well into the bearings and the conveyor system.
Assembly: Insert bearings into each end of the roller. These bearings are crucial for smooth rotation.
Finishing: Apply any necessary finishes, such as painting or coating, to enhance the roller’s resistance to wear and environmental factors.
Testing: Finally, test the roller to ensure it rotates freely and meets the required specifications.
Measuring a conveyor roller accurately is vital to ensure it fits perfectly within the conveyor system and functions as intended. To measure a conveyor roller, you need to determine three key dimensions:
Diameter: Measure across the circular end of the roller with a caliper to get the diameter.
Length: Measure the length of the roller from one end to the other, excluding the shafts protruding on either side.
Shaft Diameter: Measure the diameter of the shafts at both ends of the roller, as this will need to fit into the corresponding parts of the conveyor frame. These measurements are crucial when replacing a roller or designing a new conveyor system to ensure compatibility and efficient operation.
Last Updated on July 31, 2024 by Jordan Smith
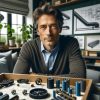
Jordan Smith, a seasoned professional with over 20 years of experience in the conveyor system industry. Jordan’s expertise lies in providing comprehensive solutions for conveyor rollers, belts, and accessories, catering to a wide range of industrial needs. From initial design and configuration to installation and meticulous troubleshooting, Jordan is adept at handling all aspects of conveyor system management. Whether you’re looking to upgrade your production line with efficient conveyor belts, require custom conveyor rollers for specific operations, or need expert advice on selecting the right conveyor accessories for your facility, Jordan is your reliable consultant. For any inquiries or assistance with conveyor system optimization, Jordan is available to share his wealth of knowledge and experience. Feel free to reach out at any time for professional guidance on all matters related to conveyor rollers, belts, and accessories.