Choosing Quality: Conveyor Roller Manufacturing Insights
Conveyor rollers play an indispensable role in the seamless operation of numerous industrial systems, forming the backbone of material handling sectors, packaging lines, and assembly processes. The right conveyor roller manufacturing can dramatically improve the efficiency and longevity of these systems. In industries ranging from mining to food processing, these rollers must be precise, durable, and perfectly suited to their specific environmental conditions. Therefore, selecting a proficient conveyor roller manufacturing partner is crucial. A partner that not only understands the nuances of your industry but also offers innovative solutions that enhance the performance and reliability of conveyor systems. This introduction underscores the importance of meticulous design and manufacturing in meeting the operational demands of various industries through high-quality conveyor rollers. The choice of manufacturer can directly influence the productivity and downtime of critical industrial operations, making it a key strategic decision for any business relying on material handling systems.
The Surge in Conveyor Roller Demand in Conveyor Roller Manufacturing
The demand for conveyor rollers has seen a significant uptick across various sectors, underscoring the pivotal role of conveyor roller manufacturing in meeting modern industrial requirements. This surge can be attributed to the expanding scope of automation and continuous improvement in material handling processes.
- E-commerce and Logistics: The boom in online shopping has drastically increased the need for efficient conveyor systems to handle large volumes of packages. Conveyor roller manufacturing has had to adapt to produce more sophisticated and durable rollers to keep up with the relentless pace of sorting and distribution facilities.
- Food and Beverage: Regulatory requirements and the need for sanitary processing environments have driven demand for stainless steel and non-corrosive conveyor rollers that are easier to clean and maintain.
- Pharmaceuticals: The critical nature of pharmaceutical manufacturing and the need for precise handling of sensitive materials necessitate the highest quality in conveyor roller manufacturing, ensuring rollers are reliable and capable of precise movements.
- Manufacturing and Automotive: As manufacturers strive to optimize production lines and reduce operational costs, the demand for robust, high-efficiency conveyor rollers that can withstand heavy loads and high speeds has increased significantly.
- Mining and Heavy Industry: The harsh environments of mining and heavy industries require conveyor rollers that are not only tough but also customized to handle abrasive materials, which puts additional pressure on conveyor roller manufacturing to innovate.
Advancements in technology have further amplified the need for efficient and durable conveyor rollers. Innovations such as smart conveyor systems equipped with IoT sensors demand precision-engineered rollers that can provide feedback on system performance and predict maintenance needs. These technological advancements push conveyor roller manufacturing to not only focus on the materials and durability of rollers but also integrate smart features that enhance the functionality and longevity of conveyor systems. The strategic importance of selecting the right conveyor roller manufacturing partner has never been more apparent, as they play a critical role in the operational success and innovation within these key sectors.
Choosing the Right Conveyor Roller Manufacturer in Conveyor Roller Manufacturing
Selecting the right conveyor roller manufacturing company is critical to ensuring the efficiency, reliability, and longevity of conveyor systems.
- Manufacturing Capabilities and Technology: Assess the technological advancements and manufacturing capabilities of the conveyor roller manufacturing company. It’s essential that they use the latest manufacturing technologies, which allow for precision engineering, customization options, and high-quality production standards.
- Quality and Durability: The quality of the rollers determines their durability and operational efficiency. High-quality conveyor rollers reduce the need for frequent replacements, minimize downtime, and maintain smooth operations. Opt for manufacturers with stringent quality control processes and certifications that attest to their rollers’ durability.
- Product Range and Customization: The ability to provide a wide range of products and customization options is a hallmark of a versatile conveyor roller manufacturing partner. Whether you need standard rollers or custom-designed ones for specific applications, the right manufacturer should be able to accommodate your needs.
- Customer Service and Technical Support: Effective customer service and robust technical support are crucial. The manufacturer should offer excellent pre-sale and after-sale support, helping with the selection of the right rollers, troubleshooting, and providing timely and effective maintenance services.
- Industry Experience and Reputation: Consider the experience and reputation of the conveyor roller manufacturing company in the industry. Manufacturers with long-standing operations and a solid reputation are likely to provide more reliable and high-quality rollers. They can demonstrate their expertise through case studies, customer testimonials, and an extensive portfolio of successful implementations.
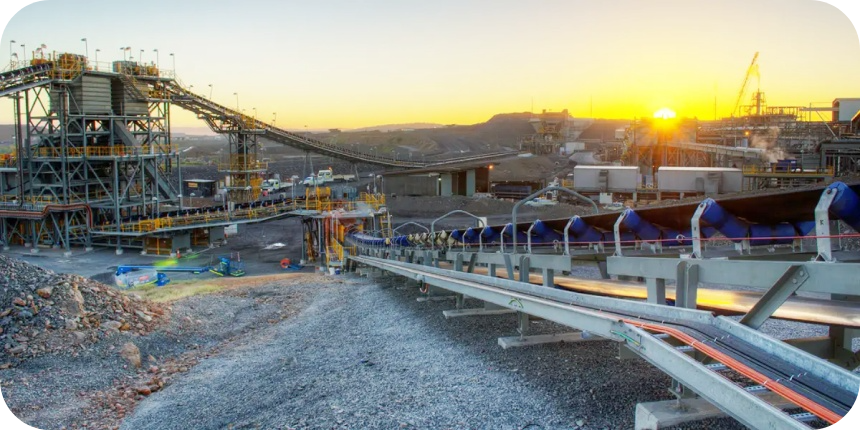
The Importance of Proximity
Finding a conveyor roller manufacturing company near you can significantly enhance collaboration and logistics. Proximity can lead to better communication, faster delivery times, and reduced shipping costs, which are crucial for maintaining the efficiency of supply chains and production lines. Local manufacturers can provide quicker responses to urgent needs and are easier to audit and visit regularly, which helps in building a strong partnership based on trust and mutual understanding.
Moreover, partnering with a local conveyor roller manufacturing company can foster alignment with regional regulatory requirements and environmental conditions. This geographical advantage ensures that the rollers are designed with a deep understanding of local industry standards and operational challenges, which can further optimize the performance and reliability of your conveyor systems. Choosing a manufacturer that combines these key factors with the convenience of proximity can significantly streamline the implementation and maintenance of conveyor roller systems, ensuring they contribute positively to the overall productivity and efficiency of your operations.
Key Players in the Conveyor Roller Manufacturing Arena
The conveyor roller manufacturing sector is dominated by several key players whose innovative approaches and technological advancements have significantly shaped the industry. Here’s a look at five leading companies and their contributions:
- Interroll Group: Known globally, Interroll is acclaimed for its extensive range of rollers, drives, conveyors, and modules for automation and material flow. Their commitment to quality and sustainability has set high standards in conveyor roller manufacturing, focusing on energy-efficient solutions and advanced system integrations.
- Daifuku Wynright Conveyors: A leader in the provision of advanced automated conveyor systems, Wynright (a Daifuku company) excels in manufacturing rollers that are integral to the customization of material handling solutions. Their innovative designs ensure high throughput and flexibility for various industrial applications.
- Hytrol Conveyor Co., Inc.: Hytrol is a top conveyor roller manufacturing company known for its innovative conveyor designs and personalized system solutions. Their commitment to technological integration in conveyors maximizes operational efficiency and supports industries ranging from retail to distribution.
- Omni Metalcraft Corp.: Omni Metalcraft is renowned for its ability to produce a wide variety of reliable and durable conveyor rollers. Specializing in both standard and custom solutions, they provide rollers made from materials that withstand different environmental challenges, enhancing system reliability and service life.
- Titan Conveyors: Titan’s approach to conveyor roller manufacturing focuses on heavy-duty designs and an extensive product line that includes specialized rollers for high impact and abrasive materials, which are crucial for industries such as mining and quarrying.
Innovative Approaches and Technological Advancements
These companies not only lead in production volumes but also in the innovation and technological enhancement of conveyor roller manufacturing:
- Precision Manufacturing: Interroll utilizes precision laser machining and robotics in the production process to ensure high-quality, dimensionally accurate rollers that require minimal maintenance.
- Smart Technology Integration: Wynright has pioneered the integration of smart technologies in conveyor systems, including the use of IoT sensors and AI to predict maintenance needs and optimize roller performance.
- Eco-Friendly Solutions: Hytrol has introduced eco-friendly rollers made from recycled materials, reducing the carbon footprint of their manufacturing processes while maintaining performance and durability.
- Customization Flexibility: Omni Metalcraft’s ability to provide highly customized rollers allows them to serve specific industrial needs, which include high-temperature and corrosive environments, showcasing their advanced material science expertise.
- Enhanced Roller Durability: Titan Conveyors has developed a proprietary sealing system for rollers, which significantly extends their lifespan and reduces the need for frequent replacements in harsh industrial conditions.
These key players in the conveyor roller manufacturing arena continue to advance the industry with their innovative products and smart solutions, setting the standards for efficiency, reliability, and sustainability in conveyor technology. Their efforts not only enhance the capabilities of conveyor rollers but also support the global trend towards automation and continuous improvement in industrial logistics and material handling.
Conveyor Roller Specifications in Conveyor Roller Manufacturing
Proper specification of conveyor rollers is essential to optimize the functionality and efficiency of conveyor systems. Specifications vary widely depending on the application, but understanding these can significantly enhance system performance. This section delves into the significance of conveyor roller dimensions, particularly focusing on the commonly used 4-inch diameter conveyor rollers, and provides insights into the selection process for belt conveyor drive rollers, a critical component in conveyor roller manufacturing.
Significance of Roller Dimensions
The dimension of a conveyor roller can influence various aspects of a conveyor system’s functionality, including load capacity, speed, and the distribution of goods.
- Load Capacity: A 4-inch diameter roller is commonly used because it effectively balances load capacity and versatility. These rollers are well-suited for moderate to heavy loads typical in industrial and distribution applications.
- Speed Consistency: The diameter of conveyor rollers affects the speed at which materials move through a system. A 4-inch roller provides a practical speed range that is adequate for various automated systems, maintaining efficiency and reducing wear on the conveyor belt.
- Product Orientation: The size and shape of the roller determine the stability of goods being transported. The 4-inch diameter is optimal for ensuring that items remain upright and aligned during transit, which is crucial for packaging and sorting operations.
- Conveyor Belt Health: Larger rollers tend to extend the life of conveyor belts. A 4-inch diameter roller reduces the strain on the belt as it provides a larger surface area to distribute the load, thereby minimizing wear and tear.
- System Versatility: Using a standard 4-inch roller simplifies the integration of various components and replacement processes. This uniformity allows for easier maintenance and compatibility across different parts of the conveyor system.
Selection Process for Belt Conveyor Drive Rollers
Choosing the right belt conveyor drive rollers is critical to the functionality of conveyor systems. These rollers power the belt and therefore must be selected with particular attention to their compatibility with the rest of the system. Here are key insights into their selection process:
- Material Compatibility: The material of the roller must be compatible with the conveyor belt to prevent wear and slippage. For instance, a rubber-coated drive roller provides excellent traction, reducing the risk of slippage which is crucial in maintaining the efficiency of the conveyor system.
- Diameter and Length: The diameter and the length of the drive roller must suit the width and the speed of the conveyor belt. Typically, a larger diameter drive roller is used for belts that need to handle heavier loads or are required to run at higher speeds.
- Surface Treatment: Drive rollers often undergo various surface treatments to enhance their performance. Textured surfaces or coatings such as rubber can increase friction, which helps in the effective transmission of force from the roller to the conveyor belt.
- Load Requirements: The load requirements of the system significantly affect the choice of drive rollers. Heavier loads require rollers with higher load capacities, which are typically made from stronger materials or designed with a thicker wall.
- Environmental Factors: Environmental conditions such as exposure to chemicals, temperature extremes, and moisture can dictate the selection of drive rollers. For example, stainless steel or coated rollers can be used to resist corrosion in humid or chemically aggressive environments.
Understanding these specifications and selection criteria is crucial in conveyor roller manufacturing, as it ensures that the conveyor system operates smoothly, efficiently, and with minimal downtime. Properly specified rollers lead to optimized system performance, longevity of the system components, and overall operational efficiency.
Dive into Conveyor Roller Parts and Types in Conveyor Roller Manufacturing
Understanding the components and variations of conveyor rollers is essential for optimizing any material handling system. Conveyor roller manufacturing involves precision and expertise to assemble rollers that meet specific industrial needs. This section provides an overview of the parts that make up a conveyor roller and explores the different types available, including heavy-duty, industrial, and custom conveyor rollers.
Components of a Conveyor Roller
A conveyor roller typically consists of several key components:
- Tube: The tube, or shell, is the cylindrical body of the roller and can be made from materials such as steel, plastic, or aluminum, depending on the application requirements.
- Shaft: The shaft runs through the center of the tube and can be either spring-loaded or fixed, which connects the roller to the conveyor frame.
- Bearings: Bearings are critical as they reduce the friction between the shaft and the tube, allowing the roller to turn smoothly. They are usually selected based on load capacity and environmental conditions.
- Seals: Seals are used to protect the bearings from dirt, dust, and other contaminants that can reduce the life of the roller.
- End Caps: End caps are placed on both ends of the tube to house the bearings and seals, providing a finished look and additional protection against contaminants.
Types of Conveyor Rollers
Conveyor rollers can be categorized based on their design and the specific needs they fulfill within various industries.
- Heavy-Duty Rollers: Designed for environments where they must withstand high loads and harsh conditions, such as in mining and quarrying operations. Heavy-duty rollers are built with thicker tubes and robust bearings to handle the extra stress.
- Industrial Rollers: Typically used in manufacturing and packaging facilities, industrial rollers must be precise and can handle moderate to high speeds. They often feature specialized coatings to improve grip and reduce noise.
- Gravity Rollers: One of the most simple and widely used, gravity rollers do not use power but rather rely on inclined planes or manual force to move items. These are suitable for light to medium loads and are cost-effective solutions for many logistical setups.
- Grooved Rollers: These rollers have grooves that can accommodate round belts for driven applications. Grooved rollers are often used in conjunction with other roller types to create complex conveyor configurations.
- Custom Rollers: Custom conveyor rollers are tailored to meet specific requirements dictated by the environment they will operate in or the materials they will handle. Customizations can include unique dimensions, materials, bearing configurations, and surface treatments.
Each type of roller plays a crucial role in the efficiency and functionality of conveyor systems. The selection of roller type depends on various factors including the load requirements, environmental conditions, operational speeds, and the physical properties of the materials being transported. In conveyor roller manufacturing, understanding these nuances is key to delivering products that not only meet the expected performance criteria but also optimize overall system efficiency. This comprehensive understanding ensures that systems are tailored perfectly to industrial needs, enhancing both productivity and reliability.
The Manufacturing Process: From Design to Delivery in Conveyor Roller Manufacturing
The conveyor roller manufacturing process is intricate and involves several critical steps from design to delivery. Each stage of the process is essential for ensuring the production of high-quality rollers that meet specific industrial requirements. This section will detail these steps, focusing on key activities such as the cutting of steel tubes, laser etching, assembly, and testing.
Design Phase
- Specification and Customization: The process begins with defining the specifications of the conveyor rollers, which include the diameter, length, material type, and load capacity. Custom requirements, such as special coatings or dimensions, are also determined at this stage.
- Engineering and Prototyping: Using CAD software, engineers design the rollers according to the specified requirements. Prototypes may be created to test the design under simulated conditions to ensure it meets all operational standards.
Manufacturing Phase
- Cutting of Steel Tubes: The manufacturing process starts with the precise cutting of steel tubes to the required lengths. This is typically done with high-speed tube cutting machines, which ensure clean cuts and high consistency across all pieces.
- Machining: Once cut, the tubes are machined to achieve the necessary tolerances needed for the bearings and shafts. This step may involve various machining processes, including drilling and turning.
- Laser Etching: For customization and traceability, laser etching is used to imprint serial numbers, logos, or custom designs directly onto the surface of the rollers. This method provides a permanent mark that does not affect the structural integrity of the tube.
- Assembly: The assembly process involves several sub-steps:
- Bearing Installation: Bearings are precisely installed at each end of the tube. The type of bearing used depends on the roller specifications and may include ball bearings, roller bearings, or spherical bearings.
- Shaft Insertion: The shaft is inserted through the bearings. In some designs, the shaft is fixed, while in others, it may be a spring-loaded or retractable design.
- Sealing and Cap Fitting: Seals are installed to protect the internal components from dust, debris, and other contaminants. End caps are then fitted to enclose the bearings and seals within the tube.
Finishing Phase
- Surface Treatment: Rollers often undergo surface treatment to enhance their performance. This could include galvanization, powder coating, or rubber coating. These treatments provide corrosion resistance, improved traction, and noise reduction.
- Quality Control and Testing: Each roller is subjected to rigorous testing to ensure it meets the required specifications. Tests might include load testing, speed testing, and durability testing. This phase is crucial to verify the performance and reliability of the conveyor rollers.
Packaging and Delivery
- Packaging: Completed rollers are carefully packaged to prevent damage during transportation. Packaging materials are chosen based on the size and sensitivity of the rollers.
- Logistics and Delivery: Finally, the packaged rollers are shipped to the client or distribution centers. The logistics are planned to optimize delivery times and reduce costs, ensuring the rollers arrive in perfect condition ready for installation.
The comprehensive steps involved in conveyor roller manufacturing, from the precise cutting of steel tubes to the detailed testing phase, highlight the industry’s commitment to producing high-quality, reliable components. Each phase of the process is optimized to ensure the final product not only meets the predefined specifications but also contributes effectively to the operational efficiency of conveyor systems. Through these meticulous manufacturing practices, manufacturers are able to deliver superior conveyor rollers that play a pivotal role in industrial operations.
Innovations and Enhancements in Roller Manufacturing in Conveyor Roller Manufacturing
In the field of conveyor roller manufacturing, continuous innovations and enhancements are crucial for improving the durability and efficiency of conveyor rollers. Manufacturers are increasingly investing in research and development to extend the lifespan of rollers, enhance their performance under extreme conditions, and reduce maintenance needs. This section discusses these innovations and highlights specific improvements that have significantly impacted the industry.
Technological Innovations
- High-Performance Materials: The use of advanced materials such as reinforced composites and ultra-high-molecular-weight polyethylene (UHMWPE) in roller construction enhances wear resistance and reduces noise. These materials ensure the rollers can withstand harsher environments and more abrasive materials without degrading.
- Precision Engineering: Modern conveyor rollers are designed with precision engineering techniques including computer-aided design (CAD) and computer-aided manufacturing (CAM). These techniques allow for more precise dimensions and tighter tolerances, which improve the roller’s efficiency and load-bearing capabilities.
- Smart Rollers: Integration of IoT sensors within conveyor rollers is a breakthrough in conveyor roller manufacturing. These sensors can monitor the roller’s performance in real-time, including speed, temperature, and load capacity. This data is crucial for predictive maintenance and reducing downtime.
Specific Improvements
- New Roller Seal Structures: One of the significant enhancements in conveyor roller manufacturing is the development of advanced seal structures. These new seals are designed to prevent oil spillage, which is essential in maintaining the lubrication of bearings and ensuring the longevity of the rollers. The innovative seal designs provide superior protection against contaminants, which is critical in harsh industrial environments.
- Shock-Absorbing Designs: To reduce the impact on the conveyor rollers during high-load operations, manufacturers have developed shock-absorbing designs that incorporate resilient materials and structures. These designs help in absorbing vibrations and shocks, thereby prolonging the service life of the rollers and reducing damage rates.
- Corrosion-Resistant Coatings: Applying corrosion-resistant coatings such as zinc, nickel-chrome, and even more advanced options like epoxy or polyurethane coatings protect the rollers from corrosive substances and extend their operational life, especially in industries dealing with chemicals or high moisture.
- Thermal Treatments: Thermal treatments are used to enhance the mechanical properties of the rollers, such as toughness and hardness. Processes like heat treating and cryogenic hardening refine the grain structure of the metal, increasing its durability and wear resistance.
- Redesigned Bearing Configurations: Innovations in bearing designs include the use of sealed and greased-for-life bearings that require minimal maintenance. These bearings are better protected against dust, dirt, and other particulates, which greatly reduces the risk of failure and extends the roller’s service life.
These innovations in conveyor roller manufacturing not only enhance the physical attributes and operational efficiencies of the rollers but also contribute to environmental sustainability by reducing the need for frequent replacements and maintenance. Through advanced materials, precision engineering, and innovative designs, conveyor roller manufacturers are setting new standards in the durability and functionality of conveyor systems. This proactive approach in integrating cutting-edge technologies and improvements is what keeps the conveyor manufacturing industry at the forefront of industrial automation and efficiency.
Replacement and Maintenance: Ensuring Longevity in Conveyor Roller Manufacturing
Proper maintenance and timely replacement of conveyor rollers are crucial to maintaining the efficiency and longevity of conveyor systems. In the realm of conveyor roller manufacturing, understanding when and how to replace rollers and parts ensures that the systems remain in optimal working condition, thus preventing costly downtime and maintenance issues. This section highlights the importance of these practices and provides a guide on identifying the right time for replacement.
Importance of Timely Roller Replacement
- Prevent Breakdowns: Regular replacement of worn-out rollers can prevent unexpected conveyor system failures, which are costly in terms of repairs and operational downtime.
- Maintain Efficiency: Worn rollers can cause the conveyor belt to slip or misalign, which reduces the system’s efficiency and can lead to further mechanical issues.
- Reduce Wear on Other Components: Consistently maintaining and replacing conveyor rollers helps to distribute the load evenly across the system, reducing undue wear and tear on other components like bearings and the conveyor belt itself.
- Improve Safety: A failing conveyor roller can lead to accidents involving the sudden halting of materials or even system breakages, posing serious safety risks to operating personnel.
- Ensure Product Quality: In industries where product integrity is critical (such as in pharmaceuticals or food processing), maintaining optimal conveyor condition is essential to avoid contamination that can result from malfunctioning or degraded components.
Guide to Identifying Replacement Needs
Visual Inspection: Regular visual inspections are the first and most straightforward method to determine if a conveyor roller needs replacement. Signs such as visible wear, cracks, or accumulation of debris on the rollers are clear indicators.
Auditory Inspection: Listening for unusual noises such as grinding, squeaking, or rattling during operation can also indicate that rollers or bearings need to be replaced. These sounds often suggest that the components are not rotating smoothly.
Operational Checks: Observing the conveyor system in operation can help identify issues such as uneven belt movement, slippage, or slow roller rotation, which can signal the need for roller replacements.
Measure Wear Patterns: Measuring the wear patterns on rollers can help predict their remaining lifespan. Excessive wear in the middle of the roller, for instance, often indicates overloading and may necessitate a change to a roller with a higher load capacity.
Scheduled Maintenance: Adhering to a scheduled maintenance program based on the manufacturer’s recommendations and past operational data is critical. This program should include detailed records of replacements and maintenance activities to help predict future needs.
Technical Performance Testing: Conducting regular performance tests can assess the functionality and efficiency of conveyor rollers. Tests might include load testing, speed tests, and monitoring for vibration levels to ensure that all components are operating correctly.
Implementation of Replacement Strategy
Implementing a proactive replacement strategy involves several steps:
- Establishing a Maintenance Schedule: Based on the manufacturer’s recommendations and the specific operational conditions of the conveyor system, establish a regular maintenance and inspection schedule.
- Training Personnel: Ensure that maintenance personnel are properly trained not only to perform inspections and identify wear and damage but also to understand the best practices for roller replacement and system calibration.
- Using Quality Parts: Always use high-quality replacements that conform to conveyor roller manufacturing standards. This ensures compatibility and reliability, preserving or enhancing the system’s overall performance.
- Maintaining Replacement Parts Inventory: Keep a stock of essential parts on hand to facilitate quick replacements. This reduces downtime and ensures that maintenance can be conducted without delay.
- Documentation and Review: Keep detailed records of all maintenance activities, including what replacements were made, when, and by whom. Review these records periodically to refine the maintenance strategy and improve practices.
By following these guidelines, businesses can maximize the lifespan and efficiency of their conveyor systems. Regular maintenance and timely replacement of conveyor rollers, guided by a thorough understanding of conveyor roller manufacturing processes, are essential to this end. This proactive approach not only saves time and money but also ensures continuous production efficiency and safety in industrial operations.
Custom Solutions for Unique Industry Needs in Conveyor Roller Manufacturing
In the dynamic field of conveyor roller manufacturing, customization is key to addressing the unique needs of different industries. Manufacturers adept at producing custom conveyor rollers are able to enhance system efficiency and adapt to the specific operational requirements and environmental conditions of their clients’ industries. This section showcases how custom solutions in conveyor roller manufacturing are developed and implemented, providing several examples of these adaptations.
Fill Out the Form to Explore Our Conveyor Roller Options.
Catering to Industry-Specific Needs
Custom conveyor rollers are designed to meet the particular demands of various sectors by considering factors like load capacity, speed requirements, environmental resistance, and integration capabilities. These considerations ensure that the conveyor system performs optimally under unique operational conditions.
Examples of Customization in Conveyor Roller Manufacturing
Food and Beverage Industry:
- Design Need: Non-corrosive and easy-to-clean surfaces to maintain hygiene and comply with food safety regulations.
- Custom Solution: Stainless steel rollers with a polished surface and sealed bearings prevent contamination and facilitate cleaning processes. Some rollers are also designed with minimal crevices to avoid bacteria build-up.
Chemical Manufacturing:
- Design Need: Resistance to chemicals and volatile substances.
- Custom Solution: Rollers coated with chemical-resistant materials such as polyurethane or specialized plastics that withstand exposure to harsh chemicals and reduce the risk of corrosion and degradation.
Outdoor and Heavy-Duty Applications (e.g., Mining, Quarrying):
- Design Need: High durability and resistance to extreme environmental conditions including dust, water, and variable temperatures.
- Custom Solution: Heavy-duty steel rollers with reinforced designs and enhanced sealing systems to protect against dirt, water ingress, and operational wear-and-tear. Thermal treatments might be used to increase hardness and resistance to physical impacts.
Packaging Industry:
- Design Need: Precision movement for handling delicate products.
- Custom Solution: Rollers with very smooth surfaces and precision bearings to ensure gentle handling of products. Rollers can also be customized to handle specific shapes and sizes of packages, incorporating soft materials like rubber to cushion the products.
Pharmaceutical Applications:
- Design Need: Ultra-clean operations for aseptic conditions.
- Custom Solution: Rollers made from high-grade stainless steel or ceramics that are easy to sterilize and do not react with pharmaceutical products. Designs often include minimal joints and crevices to ensure cleanliness.
High-Temperature Applications (e.g., Steel Mills, Foundries):
- Design Need: Resistance to high temperatures.
- Custom Solution: Use of heat-resistant metals such as high-grade stainless steel and coatings capable of withstanding temperatures without losing structural integrity. Bearings and seals specially designed to operate at higher temperatures are also used.
Implementing Custom Solutions
The process of implementing these custom solutions involves close collaboration between the manufacturer and the client. The stages typically include:
- Consultation and Requirement Analysis: Understanding the specific needs of the client, including environmental conditions and operational requirements.
- Design and Prototyping: Creating initial designs and prototypes, which are then tested to ensure they meet the required specifications.
- Manufacturing: Once the design is finalized and approved, manufacturing of the custom rollers begins, using materials and processes that align with the client’s needs.
- Testing and Quality Assurance: Comprehensive testing to ensure the rollers meet all functional requirements, followed by quality assurance checks to confirm they adhere to industry standards.
- Delivery and Integration: The custom conveyor rollers are delivered and integrated into the existing system, with support from the manufacturer to ensure optimal performance.
By providing these tailored solutions, conveyor roller manufacturers play a crucial role in enhancing the efficiency and reliability of industry-specific conveyor systems. Custom conveyor rollers not only meet the unique demands of diverse operational environments but also contribute to the prolonged durability and enhanced functionality of the systems they are a part of.
FAQs About Conveyor Roller Manufacturing
The manufacturing process of a conveyor roller involves several key steps from initial design to final assembly and testing. Initially, precise specifications including diameter, length, and material are determined based on the intended use of the roller. Here’s a typical manufacturing process:
Designing: Engineers use CAD (Computer-Aided Design) software to create detailed blueprints of the rollers, taking into account all necessary specifications.
Material Selection: Based on the roller’s requirements, appropriate materials are chosen. Common materials include steel, stainless steel, aluminum, or plastic for the tube, and steel or stainless steel for the shaft.
Tube Cutting: The selected material for the tube is cut to specified lengths using high-speed cutting machines, which ensure clean and precise cuts.
Machining: The cut tubes and shafts are machined to achieve the required tolerances and dimensions. This often involves drilling, welding, and turning processes.
Assembly: Components like bearings, seals, and the shaft are assembled together with the tube. Bearings are pressed into the tube ends, and shafts are inserted through the bearings. Seals are added to protect the bearings from contaminants.
Surface Finishing: Rollers might undergo surface treatments such as galvanizing, painting, or coating with materials like rubber to enhance their performance, durability, and aesthetic appeal.
Testing: The assembled rollers are tested for functionality and durability. Tests might include load and speed tests, as well as checks for balance and alignment.
Packaging and Shipping: Finally, the rollers are packaged securely and shipped to the customer or storage facilities.
This streamlined process ensures that each roller is robust, efficient, and ready for use in various industrial applications.
Manufacturing a roller, particularly for conveyor systems, requires precision and attention to detail through the following phases:
Planning and Design: Detailed designs are formulated using engineering drawings to match the specifications needed for the application. This phase includes selecting the type and size of the roller, materials, and the detailed architecture of components like the inner shaft, bearings, and the outer tube.
Material Cutting and Preparation: Materials for the shaft and tube are cut to the required sizes. Common methods include CNC machining, which provides precise cuts and allows for high consistency across multiple units.
Component Machining: Each part of the roller is machined to specifications. This includes the inner bore of the tube and the external surface which may need to be smooth or have grooves, depending on the design.
Assembly: Components are assembled in a systematic process. Bearings are typically pressed into the tube ends first, followed by the insertion of the shaft through the bearings. Additional components like snap rings or end caps may be added to secure the assembly.
Testing: Assembled rollers are tested under operational conditions similar to those they will experience in actual use. This includes testing for rotational freedom, load-bearing capacity, and noise levels.
Finishing Touches: Rollers may be painted, sealed, or treated with anti-corrosion materials depending on the environment in which they will be used. This not only improves their lifespan but also their performance.
Quality Control: Throughout the manufacturing process, quality control measures are in place to ensure each roller meets the company’s and customers’ standards. This involves dimensional checks, material quality inspections, and final performance reviews.
Each step is crucial to produce a high-quality roller capable of performing under the demanding conditions of industrial applications.
Conveyor rollers can be made from a variety of materials, each selected based on the specific needs of the application they are designed for. Common materials include:
Steel: Highly durable and strong, ideal for heavy-duty applications. It is used for both the tubes and shafts of rollers.
Stainless Steel: Used in applications requiring corrosion resistance, such as in food processing or pharmaceutical industries.
Aluminum: Lighter than steel and resistant to corrosion, suitable for lighter applications or where reduced weight is beneficial.
Plastic: Often used for the tube component of rollers, particularly where noise reduction is important. Plastic rollers are less durable than metal ones but suitable for light applications and environments that require corrosion resistance, such as chemical processing.
Rubber or Polyurethane Coating: Applied to metal rollers to increase grip, reduce noise, and prevent damage to delicate materials being conveyed.
Each material offers different benefits, and the choice depends on factors such as load capacity, environmental conditions, operational speed, and cost-effectiveness.
Determining the “best” roller conveyor manufacturer depends on several factors including the specific needs of the application, budget, lead times, and the level of customer service offered. However, some renowned manufacturers are known for their high-quality products and extensive industry experience. Companies like Interroll, Hytrol, and Daifuku Wynright are leaders in the field, offering a wide range of products and custom solutions. These manufacturers are noted for:
Interroll: Offers a vast array of roller solutions with a focus on energy efficiency and low operational cost.
Hytrol: Known for durable products and excellent customer service, Hytrol provides tailored solutions based on comprehensive system analysis.
Daifuku Wynright: Specializes in automated material handling systems and is renowned for innovative and technologically advanced conveyor solutions.
When choosing a manufacturer, consider factors such as the variety of available products, customization options, engineering support, and the company’s reputation in the market to ensure that you receive the best possible product and service for your needs.
Last Updated on July 30, 2024 by Jordan Smith
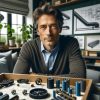
Jordan Smith, a seasoned professional with over 20 years of experience in the conveyor system industry. Jordan’s expertise lies in providing comprehensive solutions for conveyor rollers, belts, and accessories, catering to a wide range of industrial needs. From initial design and configuration to installation and meticulous troubleshooting, Jordan is adept at handling all aspects of conveyor system management. Whether you’re looking to upgrade your production line with efficient conveyor belts, require custom conveyor rollers for specific operations, or need expert advice on selecting the right conveyor accessories for your facility, Jordan is your reliable consultant. For any inquiries or assistance with conveyor system optimization, Jordan is available to share his wealth of knowledge and experience. Feel free to reach out at any time for professional guidance on all matters related to conveyor rollers, belts, and accessories.