Conveyor Roller Manufacturing Process Technology Innovations
Conveyor rollers are pivotal components used extensively across various industries to facilitate the smooth and efficient transport of goods. They play a critical role in production lines and material handling systems, enhancing productivity and operational efficiency. Over the years, the technology behind conveyor rollers has evolved significantly, leading to improvements in their design and functionality. This advancement has been driven by the growing demands of industries for higher efficiency and lower maintenance costs. This article aims to explore the conveyor roller manufacturing process in detail. By understanding how these essential components are made, businesses can make informed decisions that optimize their operations and improve overall efficiency. This exploration will cover the complete conveyor roller manufacturing process,highlighting the technological innovations and methodologies employed in creating these indispensable industrial tools.
What is the Conveyor Roller Manufacturing Process
Conveyor rollers are fundamental components in the automation and material handling industries, serving as critical elements in the facilitation of bulk material transport. At its core, the conveyor roller manufacturing process involves precision engineering and meticulous quality control to produce rollers that meet stringent industry standards. These rollers drastically reduce the amount of effort required to move large volumes of materials, streamline operations, and enhance workplace safety.Conveyor roller manufacturing process require machining, welding, and polishing for optimal performance. Enable easy object movement by hand, gravity, or power.
What are Conveyor Rollers and Their Key Functions
Conveyor rollers are cylindrical tubes designed to rotate smoothly and with minimal friction. They are mounted within frames to support and move goods along a defined path. Their key functions include:
- Load Support: They bear the weight of the materials being transported.
- Movement and Control: Rollers facilitate the smooth and controlled movement of goods.
- Reduction of Friction: They minimize the friction between the conveyor belt and the material.
- Speed Regulation: Conveyor rollers help in controlling the speed at which materials move, ensuring efficiency and safety.
- System Integration: Rollers are integral to the modular design of conveyor systems, allowing for flexibility and scalability.
These functions are essential across various applications, underscoring the importance of the conveyor roller manufacturing process, which ensures that rollers are produced to fulfill these roles effectively.
Roller Conveyor Working Principle and Applications
The working principle of roller conveyors is based on the conversion of rotational motion from the rollers into the linear motion of the conveyor belt. This movement is typically powered by motors and linked by belts or chains to the rollers. The simplicity of this mechanism makes it reliable and easy to maintain, which is vital for industries that rely on continuous and efficient operations.
Applications of conveyor rollers are widespread, including:
- Manufacturing and Assembly Lines: Where they are used to move parts between different stations efficiently.
- Warehousing and Distribution: Rollers expedite the process of sorting, packaging, and distributing goods.
- Food and Beverage: They are employed in production lines to move products through various processing stages.
- Pharmaceuticals: Rollers ensure the gentle handling of sensitive medical products across the production floor.
- Airport Baggage Handling: Where they streamline the sorting and loading of luggage.
Each application benefits distinctly from the conveyor roller manufacturing process, which tailors features like roller diameter, material, and coating to specific industry needs.
Types of Conveyor Rollers and Their Specific Usages
Conveyor rollers come in various types, each designed for particular applications and industries. The selection of roller type is a critical decision in the conveyor roller manufacturing process, influencing everything from system efficiency to maintenance costs.
- Gravity Rollers: These are the simplest form, used in gravity conveyors where items move by manual push or gravity pull.
- Motorized Rollers: These rollers are powered and used when automatic movement and speed control are necessary.
- Impact Rollers: Positioned at conveyor feed points to absorb shock and protect against damage to the belt.
- Tapered Rollers: Ideal for curves in conveyor systems, helping maintain the orientation and alignment of items.
- Plastic Rollers: Used in food production for their cleanliness and corrosion resistance, which metal rollers cannot offer.
The conveyor roller manufacturing process for each type involves specific materials and technologies to ensure performance according to the intended application. For example, plastic rollers may involve injection molding, while steel rollers might require welding and assembly of multiple components.
Through the careful selection of roller types and adherence to precise manufacturing processes, conveyor systems can achieve optimal performance, enhancing the efficiency and productivity of various industrial operations. This chapter sets the foundation for understanding how each component within the conveyor roller manufacturing process plays a pivotal role in the functionality of these systems.
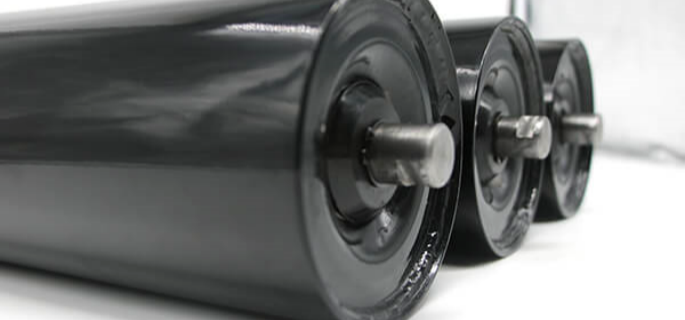
Deep Dive into the Conveyor Roller Manufacturing Process
The conveyor roller manufacturing process is a critical element in the production of efficient conveyor systems. This chapter explores the meticulous design and engineering phases that precede the manufacturing stage, focusing on the importance of precision in roller specifications and the utilization of sophisticated design software and comprehensive PDF guides.
The Role of Design Processes in Conveyor Roller Manufacturing
In the conveyor roller manufacturing process, the design stage serves as the blueprint for production. It involves detailed planning and modeling to ensure that the final product meets specific operational requirements. Roller conveyor design PDFs are essential resources that provide guidelines, technical specifications, and dimensional data for designing conveyor rollers.
- Material Specifications: Detailing the types of materials suitable for different conveyor environments.
- Dimensional Parameters: Providing the sizes and tolerances needed for various roller types.
- Load Capacities: Outlining the maximum load each roller type can handle efficiently.
- Speed Recommendations: Suggesting optimal speeds at which conveyor systems should operate to maximize efficiency and longevity.
- Installation Guidelines: Offering step-by-step instructions on installing rollers to the conveyor framework.
Importance of Roller Conveyor Diagrams
A well-thought-out roller conveyor diagram is pivotal for efficient construction and seamless operational integration. These diagrams provide a visual representation of the conveyor system’s layout and are critical for:
- Assembly Accuracy: Ensuring each part is correctly positioned for optimal function and reliability.
- Maintenance Planning: Helping technicians identify and access parts that require regular maintenance or replacement.
- Error Minimization: Reducing the likelihood of mistakes during assembly, which can lead to costly downtime.
- Operational Efficiency: Facilitating smooth and efficient conveyor operations by providing a clear roadmap for system layout and component integration.
- Safety Enhancements: Highlighting potential safety issues and incorporating features to mitigate risks to operators.
Diagrams not only assist in the assembly and installation phases but also support the ongoing maintenance and troubleshooting processes, making them invaluable throughout the lifespan of the conveyor system.
Factors Influencing Conveyor Roller Types and Specifications
Several factors dictate the types of rollers used in conveyor systems and their specific specifications. Understanding these factors is crucial in the conveyor roller manufacturing process to produce rollers that are fit for purpose and durable. Key considerations include:
- Material Handled: The type of materials the conveyor will transport. Heavy or abrasive materials require more robust and durable rollers.
- Environment: The operating environment, whether it is exposed to high moisture, corrosive substances, or extreme temperatures, influences material choice and design specifics.
- Load Weight: Heavier loads require rollers with higher load capacities, which impacts material selection and roller diameter.
- Conveyor Speed: Higher speeds might necessitate rollers designed to minimize friction and wear.
- Installation Space: The available space for the conveyor system can affect roller width and spacing.
These factors are meticulously considered during the design phase to tailor the conveyor roller manufacturing process to meet the precise needs of the application. Engineers and designers use advanced software to simulate roller functions and performance under various conditions to ensure reliability and efficiency.
The design and engineering stages of the conveyor roller manufacturing process are as crucial as the manufacturing stage itself. By thoroughly planning and designing each component, manufacturers can ensure that the final product not only fits perfectly within the system but also performs optimally over its service life. This attention to detail in the design phase underpins the functionality and durability of conveyor rollers, making it a critical focus area for industry professionals.
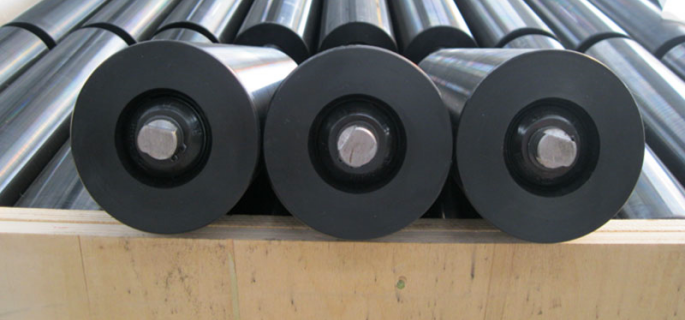
The Five Most Common Traditional Conveyor Roller Manufacturing Methods
- Process: A flat sheet of metal, typically steel or aluminum, is fed into a rolling machine. The machine rolls the sheet into a cylindrical shape, and the edges are welded together to form a seamless tube.
- Advantages: This method ensures a uniform and consistent diameter, which is crucial for the roller’s smooth operation.
- Applications: Used for standard and heavy-duty conveyor rollers due to its strength and precision.
End-Cap Welding
- Process: Metal end caps are fabricated separately and then welded onto both ends of the rolled tube. The welding process must be precise to ensure the end caps are aligned correctly.
- Advantages: Provides structural integrity and houses the bearings securely, ensuring the roller can handle significant loads without deformation.
- Applications: Common in rollers used in mining, manufacturing, and material handling industries.
Shaft Insertion
- Process: A metal shaft, usually made of hardened steel, hardened steel roller is inserted through the length of the tube and the welded end caps. The shaft is often fixed in place using set screws, retaining rings, or welding.
- Advantages: The shaft provides a sturdy axis for the roller, ensuring it can rotate efficiently under load.
- Applications: Essential for rollers that will be subjected to high rotational speeds and heavy weights.
Bearing Assembly
- Process: Bearings are fitted into the end caps. This can involve press-fitting the bearings into the end caps or using retaining rings to secure them. The bearings reduce friction and allow for smooth rotation.
- Advantages: Bearings extend the life of the rollers by minimizing wear and tear and ensuring smooth operation.
- Applications: Critical for all conveyor systems, especially those requiring high-speed operation or transporting heavy loads.
Surface Coating
- Process: The roller surface is coated with materials like rubber, PVC, or polyurethane. The coating can be applied through dipping, spraying, or wrapping processes.
- Advantages: Surface coatings enhance the durability of the rollers, provide additional grip, reduce noise, and protect against corrosion and wear.
- Applications: Used in various industries, including food processing, packaging, and warehousing, where specific roller surface properties are required.
These traditional manufacturing methods combine to produce conveyor rollers that are durable, reliable, and suitable for a wide range of industrial applications. The process starts with creating a robust tube, securely attaching end caps, inserting a sturdy shaft, fitting high-quality bearings, and finally applying a surface coating to enhance the roller’s performance and longevity.
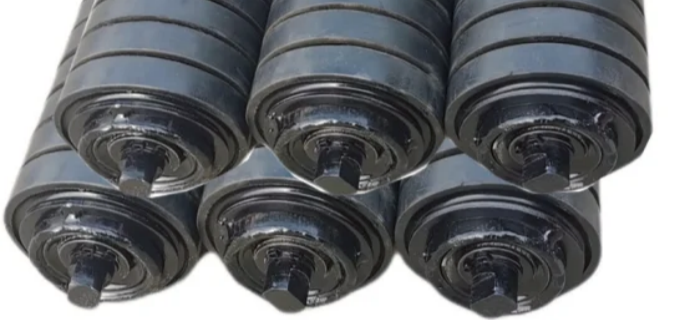
The Comprehensive Conveyor Roller Manufacturing Process
The conveyor roller manufacturing process is intricate and methodical, ensuring that each roller is built to meet exacting standards of durability and functionality. This process is divided into several key stages—from material selection to final quality assurance—each designed to optimize the quality and performance of the conveyor rollers produced.
Preparation Stage
Selection of Materials Based on Conveyor Roller Price and Quality:
The first step in the conveyor roller manufacturing process involves the selection of materials. This decision is crucial as it affects both the cost and quality of the final product. Materials are typically chosen based on their durability, cost-effectiveness, and suitability for specific environments. Common materials include:
- Steel: Highly durable and ideal for heavy-duty applications.
- Stainless Steel: Used in food processing and pharmaceutical industries where corrosion resistance is necessary.
- Plastic: Lightweight and suitable for lighter loads and quieter operation.
- Rubber-Coated: To increase grip and reduce noise.
The choice of material directly impacts the conveyor roller’s price and operational efficiency, making this a critical consideration for manufacturers.
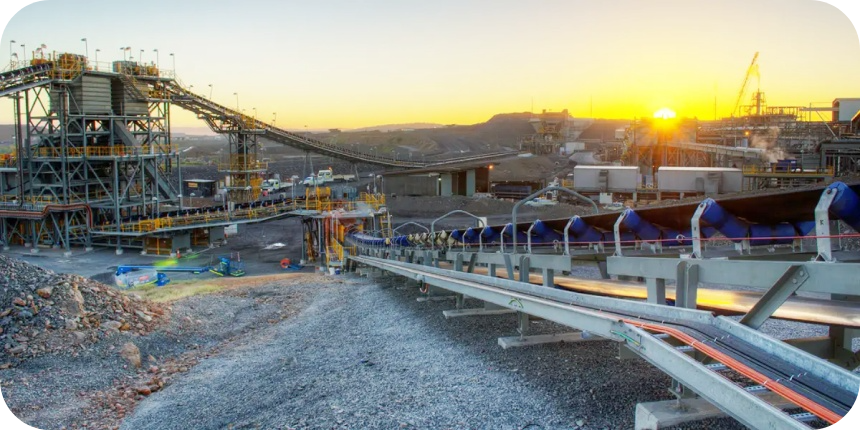
Cutting and Shaping of Steel Tubes as Per Industrial Conveyor Roller Specifications:
Once the materials are selected, steel tubes are precisely cut and shaped according to predefined industrial specifications. This step requires high precision to ensure that all rollers are uniform and compatible with the conveyor system. Techniques involved include:
- Tube Cutting: Utilizing high-speed circular saws or laser cutting for precision.
- Shaping: Employing CNC machining to achieve the exact dimensions and profiles needed.
- Drilling: Making holes for axles and attachment points.
These processes are meticulously controlled to maintain strict adherence to the conveyor roller manufacturing process specifications, ensuring every roller fits perfectly within the system.
Assembly Line Production
Incorporation of Advanced Machinery to Assemble Various Components:
Advanced automated machinery plays a vital role in the assembly of conveyor rollers. Robots and automated assembly lines are used to ensure high efficiency and consistency. The assembly process typically involves:
- Component Alignment: Aligning tubes, bearings, and shafts for assembly.
- Automated Assembly: Using robotic arms to insert bearings and press-fit components together.
Step-by-Step Illustration of the Process from the Conveyor Roller Manufacturing Process PDF:
Detailed diagrams and step-by-step instructions from the conveyor roller manufacturing process PDF guide the assembly. These documents ensure that each phase of the assembly adheres to technical standards, from component placement to final assembly.
Welding, Installation of Axles and Bearings, and Ensuring the Precision of Parts:
Welding is occasionally used to secure parts together, particularly in heavy-duty rollers. The installation of axles and bearings is critical, as these must be precisely positioned to ensure smooth operation and minimal wear. Each part is meticulously checked for precision, using tools like calipers and micrometers, to confirm that they meet the exact specifications.
Quality Control and Testing
Procedures for Testing the Strength and Durability of Rollers:
Quality control is paramount in the conveyor roller manufacturing process. Testing procedures involve:
- Load Testing: To ensure rollers can withstand the weight specifications.
- Speed Testing: Rollers are tested at varying speeds to ensure stability.
- Durability Testing: Long-term use simulations to check wear resistance.
Ensuring Adherence to the Roller Conveyor Working Principle and Standards:
The final stage of the manufacturing process is ensuring that all rollers adhere to the foundational principles of roller conveyor operation and meet all industry standards. This includes checks for:
- Alignment and Movement: Ensuring rollers are perfectly aligned and roll smoothly.
- Material Integrity: Verifying that materials have no defects and are correctly hardened or treated.
- Compliance with Specifications: Each roller is measured against established specifications for dimensions, material properties, and operational efficiency.
Each of these stages in the conveyor roller manufacturing process is crucial for producing high-quality rollers that efficiently and reliably move goods across various industries. This detailed and regimented approach ensures the longevity and effectiveness of conveyor systems globally.
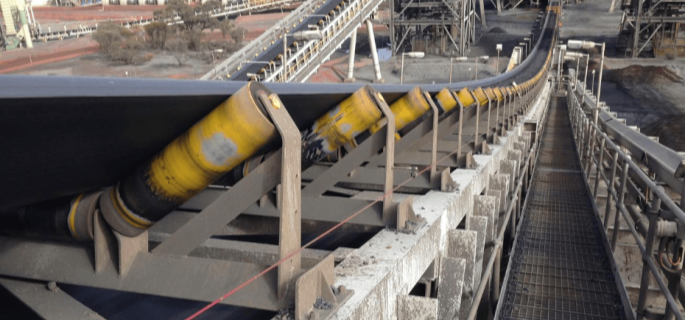
Production Process of Conveyor Idlers
Conveyor idlers play a crucial role in the smooth and efficient operation of conveyor systems. The production process of conveyor idlers involves several stages, each ensuring that the final product meets the required standards of durability, performance, and reliability. Here is a detailed breakdown of the production process:
Material Selection and Preparation
- Material Choice: Typically, steel is used for the rollers, shafts, and frames due to its strength and durability. Depending on the application, materials like stainless steel, aluminum, or composites might be chosen.
- Cutting and Shaping: Steel sheets and rods are cut and shaped into the required dimensions for the idler components using CNC machines or other cutting tools.
Tube Manufacturing
- Tube Rolling: Flat steel sheets are fed into a rolling machine to form cylindrical tubes. The edges of the tubes are then welded together to create a seamless tube.
- Welding: The welding process must ensure strong and uniform seams to maintain the tube’s integrity and durability.
End-Cap Manufacturing
- Fabrication: End caps are fabricated separately from steel or another suitable material. They are precision-machined to ensure they fit perfectly onto the ends of the tubes.
- Welding or Press-Fitting: The end caps are either welded onto the tube ends or press-fitted, depending on the design specifications. This step is crucial for housing the bearings securely.
Shaft Manufacturing
- Cutting and Machining: Steel rods are cut to the required length for the idler shafts. The ends of the shafts are machined to fit into the end caps and bearings precisely.
- Hardening and Coating: Depending on the application, the shafts might undergo heat treatment to enhance their strength and durability. Coatings may be applied to prevent corrosion.
Bearing Assembly
- Bearing Selection: High-quality bearings are selected based on load and speed requirements. Common types include ball bearings and roller bearings.
- Insertion: Bearings are press-fitted into the end caps. Proper alignment and secure fitting are crucial to ensure smooth rotation and minimize wear.
Roller Assembly
- Shaft Insertion: The machined shaft is inserted through the tube and the bearings. The alignment must be precise to ensure the roller rotates smoothly and efficiently.
- Balancing: The assembled roller is dynamically balanced to prevent vibrations during operation. Balancing ensures longer life and better performance of the idler.
Frame and Bracket Manufacturing
- Cutting and Welding: Steel sheets and rods are cut and welded to form the idler frame and brackets. These components hold the rollers in place and provide structural support.
- Surface Treatment: Frames and brackets may undergo surface treatments such as painting, powder coating, or galvanizing to protect against corrosion and wear.
Final Assembly
- Mounting Rollers: The rollers are mounted onto the frames or brackets. The alignment and spacing must be precise to ensure the conveyor belt runs smoothly.
- Inspection: The assembled idlers undergo rigorous inspection to check for dimensional accuracy, rotational smoothness, and overall quality.
Quality Control and Testing
- Load Testing: Idlers are tested under load conditions to ensure they can handle the specified weight and operate smoothly.
- Durability Testing: Accelerated wear tests simulate long-term use to ensure the idlers’ durability and reliability.
- Final Inspection: Each idler is inspected for defects and adherence to design specifications before being approved for shipping.
Packaging and Shipping
- Packaging: Finished idlers are carefully packaged to prevent damage during transportation. Proper labeling ensures easy identification and handling.
- Shipping: The packaged idlers are shipped to customers or warehouses, ready for installation in conveyor systems.
The production process of conveyor idlers involves multiple stages, from material selection and preparation to final assembly and quality control. Each step is critical to ensuring the idlers are durable, reliable, and capable of supporting the efficient operation of conveyor systems. By adhering to precise manufacturing standards and rigorous testing, manufacturers can produce high-quality conveyor idlers that meet the demands of various industrial applications.
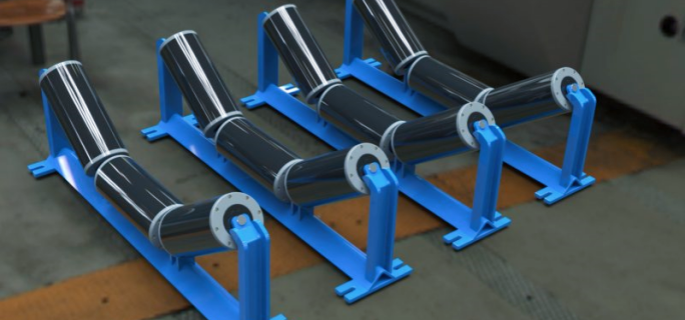
3 Innovative Technologies for a Better Roller Design
Composite Materials
- Technology: The use of advanced composite materials such as carbon fiber, fiberglass, and reinforced polymers in roller construction.
- Advantages: These materials are significantly lighter than traditional steel, reducing the overall weight of the conveyor system and improving energy efficiency. Composites also offer high strength-to-weight ratios, excellent corrosion resistance, and reduced noise levels during operation.
- Applications: Ideal for industries where weight reduction is crucial, such as aerospace, automotive, and high-speed logistics.
Smart Sensors and IoT Integration
- Technology: Incorporation of smart sensors and Internet of Things (IoT) technology within rollers to monitor their performance in real-time.
- Advantages: Smart rollers can track parameters such as temperature, vibration, rotational speed, and load. This data is transmitted to a central system for analysis, enabling predictive maintenance, reducing downtime, and extending the lifespan of the rollers. Real-time monitoring also enhances safety by detecting potential failures before they occur.
- Applications: Widely used in modern manufacturing, warehousing, and distribution centers where real-time data can optimize operations and maintenance schedules.
Energy-Efficient Roller Drives
- Technology: Development of energy-efficient roller drives, including low-friction bearings and advanced lubrication systems.
- Advantages: These innovations reduce the energy consumption required to move the rollers, leading to significant cost savings and environmental benefits. Low-friction bearings minimize resistance, ensuring smoother operation, while advanced lubrication systems reduce maintenance requirements and enhance the rollers’ durability.
- Applications: Suitable for all industries utilizing conveyor systems, particularly those with high operational hours, such as mining, food processing, and large-scale manufacturing.
These innovative technologies significantly enhance roller design by improving efficiency, durability, and overall performance. Composite materials offer lightweight and corrosion-resistant options, smart sensors enable real-time monitoring and predictive maintenance, and energy-efficient roller drives reduce operational costs and environmental impact. Adopting these technologies can lead to more reliable and cost-effective conveyor systems across various industries.
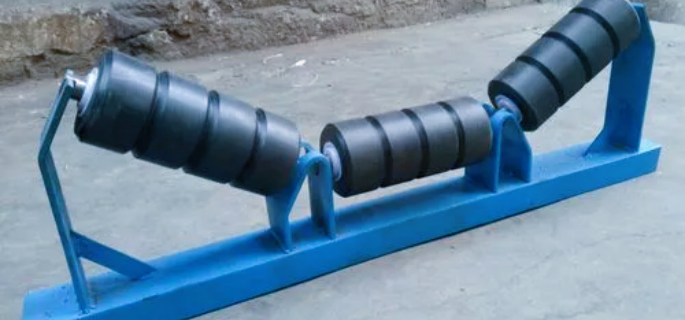
Revolutionizing the Conveyor Roller Manufacturing Process with Modern Technology
The conveyor roller manufacturing process has seen significant transformations with the adoption of innovative technologies. These advancements aim to enhance automation, increase efficiency, and ensure the production of high-quality conveyor rollers. By integrating modern technologies with traditional manufacturing techniques, the industry is able to meet the increasing demands for more sophisticated and reliable conveyor systems.
Automation and Efficiency in the Conveyor Roller Manufacturing Process
Automation is at the heart of modernizing the conveyor roller manufacturing process. The integration of new technologies has not only streamlined production but has also significantly increased output quality and consistency. Here are five key examples of how automation and innovative technologies are applied:
CNC Machining:
- Application: Automated control of machining tools like drills, lathes, and mills.
- Benefits: Enhances precision in the cutting and shaping of roller components, drastically reducing human error.
Laser Cutting Technology:
- Application: Utilizes high-powered lasers to cut metals with extreme precision.
- Benefits: Provides smoother finishes that require less processing and are ideal for creating complex shapes quickly and with high repeatability.
Robotic Assembly Lines:
- Application: Robots perform the assembly of bearings, shafts, and tubes.
- Benefits: Increases assembly speed and accuracy, reduces labor costs, and improves worker safety by handling high-load and precision tasks.
3D Printing:
- Application: Additive manufacturing processes used for producing complex roller parts directly from CAD models.
- Benefits: Allows for rapid prototyping, testing of new roller designs, and the ability to produce parts on demand without the need for extensive tooling.
Automated Inspection and Testing:
- Application: Use of sensors and cameras to automatically inspect dimensions and surface integrity.
- Benefits: Ensures high quality and compliance with specifications through detailed, real-time inspections at various stages of production.
These technologies collectively contribute to a more streamlined, efficient, and error-free conveyor roller manufacturing process. They enable manufacturers to keep up with the demands for higher performance and durability in conveyor systems.
Integration of Modern Technology with Traditional Manufacturing
The fusion of modern technology and traditional manufacturing methods has reshaped the conveyor roller manufacturing process. This integration not only enhances efficiency but also improves the overall quality of the rollers. Below are key aspects of this integration:
- Precision Engineering: Modern CAD (Computer-Aided Design) and CAM (Computer-Aided Manufacturing) software guide the design and manufacturing stages, improving precision in roller dimensions and alignment.
- Material Science Innovations: The development and use of advanced materials that are lighter, stronger, and more durable are central to producing high-quality rollers. These materials withstand harsh environments and reduce wear and tear on the system.
- Quality Control Software: Software that monitors every stage of the manufacturing process to ensure that each roller meets strict standards. This software can predict potential defects and prevent them before rollers are finalized.
- Sustainable Manufacturing Practices: Modern technologies facilitate more sustainable manufacturing practices by reducing waste and energy consumption. This not only lowers production costs but also minimizes the environmental impact of manufacturing activities.
- IoT and Data Analytics: The integration of IoT (Internet of Things) sensors and data analytics in the manufacturing process allows for real-time monitoring and optimization of production lines. This leads to smarter, more responsive manufacturing systems that can adapt to changing conditions and demands.
By embracing these modern technologies, the conveyor roller manufacturing process remains at the forefront of industrial manufacturing, capable of delivering products that meet the evolving needs of industries around the world. These advancements not only improve the efficiency and quality of conveyor rollers but also extend their service life and reliability, reinforcing the infrastructure of numerous industrial operations.
High-quality conveyor rollers available – inquire here!
Navigating the Conveyor Roller Manufacturing Process to Market Integration
The journey of conveyor rollers from the manufacturing floor to their final integration into conveyor systems encapsulates a complex chain of processes, each meticulously managed to ensure quality, efficiency, and cost-effectiveness. This chapter delves into the trajectory that conveyor rollers follow post-manufacturing, the pricing strategies involved, and the quality assurance practices that manufacturers employ to remain competitive in the market.
The Journey from Fabrication to Integration
Once conveyor rollers have completed the conveyor roller manufacturing process, they begin their transition towards integration into conveyor systems, a journey that includes several key phases:
Quality Assurance Testing:
- Post-manufacture, every batch of conveyor rollers is subjected to rigorous testing to ensure they meet the industry standards in terms of durability, load capacity, and performance.
Packaging and Logistics:
- Rollers are then packaged securely to prevent any damage during transit, considering the logistical needs to deliver them from the factory floor to client sites across the globe.
Installation:
- At their destination, these rollers are integrated into existing or new conveyor systems, a process that might involve customization to meet specific operational requirements.
Operational Testing:
- Once installed, the rollers undergo further testing as part of the complete conveyor system to confirm that they function well within the intended setup.
Maintenance Training:
- Finally, end-users are trained on proper maintenance practices to maximize the lifespan and effectiveness of the rollers.
This comprehensive journey from fabrication to integration is critical in ensuring that the rollers perform optimally in their designated roles within conveyor systems.
Conveyor Roller Price Range and Factors Affecting Cost
The cost of conveyor rollers can vary significantly based on several factors that influence manufacturing, distribution, and integration. Understanding these factors is essential for both manufacturers and buyers to make informed decisions. Key factors include:
Material Costs:
- The type of materials used (steel, stainless steel, plastic, rubber-coated) significantly affects the overall cost due to variations in raw material prices.
Manufacturing Complexity:
- Rollers requiring more complex designs or higher precision in manufacturing tend to cost more due to the increased time and resources needed.
Volume of Order:
- Larger orders often reduce the cost per unit due to economies of scale, which allow manufacturers to optimize production efficiency and material usage.
Customization Requirements:
- Customized rollers, which are tailored to specific operational needs (like temperature resistance or load capacity), can also increase costs due to additional research, design, and testing.
Market Demand and Economic Conditions:
- Fluctuations in market demand or changes in economic conditions (like tariffs or material shortages) can affect roller prices.
These factors collectively contribute to the pricing strategy of conveyor rollers, which can range widely to accommodate different industry needs and budget constraints.
Maintaining Quality While Offering Competitive Pricing
Roller conveyor manufacturers are constantly challenged to maintain high quality while also offering competitive pricing. They achieve this balance through several practices:
- Lean Manufacturing:
- Adopting lean manufacturing techniques to reduce waste and improve operational efficiency, thereby lowering production costs without compromising quality.
- Automation:
- Utilizing automation in the conveyor roller manufacturing process to enhance precision and consistency, which reduces errors and defects and lowers the cost of rework.
- Supplier Relationships:
- Establishing strong relationships with material suppliers to negotiate better prices for high-quality materials, which helps in maintaining the cost-efficiency of the production process.
- Continuous Improvement:
- Implementing continuous improvement strategies to refine processes and technologies, which helps in reducing costs over time while enhancing product quality.
- Quality Control Systems:
- Investing in advanced quality control systems that ensure each roller meets strict standards, thereby reducing the likelihood of failures that could result in costly warranties or recalls.
Through these methods, manufacturers not only succeed in producing high-quality conveyor rollers but also manage to offer them at competitive prices, ensuring they meet the client’s budgetary and operational needs. This strategic approach in the conveyor roller manufacturing process aids in sustaining long-term business relationships and a strong market presence.
Selecting a Partner in the Conveyor Roller Manufacturing Process
Choosing the right manufacturer is crucial in ensuring the effectiveness and reliability of your conveyor rollers, which are integral components of your operational infrastructure. This decision can significantly impact the efficiency of your conveyor system, the downtime you experience, and, ultimately, your bottom line. Here, we will guide you through the process of selecting a suitable conveyor roller manufacturer by outlining key criteria and recommending reputable manufacturers in the industry.
A Guide to Selecting a Suitable Conveyor Roller Manufacturer
Selecting the right conveyor roller manufacturer involves thorough research and comparison based on several aspects beyond just cost. Consider these steps in your selection process:
Assess Your Needs:
- Understand the specific needs of your conveyor system including load capacity, speed, material type, and environmental conditions.
Search for Manufacturers:
- Look for manufacturers that specialize in the conveyor roller manufacturing process. Use industry contacts, trade shows, and business directories to create a list of potential manufacturers.
Evaluate Technical Capabilities:
- Review the technical specifications offered by the manufacturers to ensure they meet your requirements.
Check Compliance and Certifications:
- Ensure the manufacturers comply with industry standards and hold certifications that validate their quality processes, such as ISO 9001.
Consider Manufacturing Technology:
- Evaluate the technology and machinery used in the conveyor roller manufacturing process as this impacts the quality and reliability of the rollers.
Read Customer Reviews and Case Studies:
- Look at reviews and case studies to gauge the manufacturer’s reliability and the performance of their rollers in real-world applications.
Discuss Customization Options:
- If you need customized rollers, discuss whether the manufacturer can accommodate these modifications and at what cost.
Request Quotes and Compare:
- Obtain and compare quotes from various manufacturers considering not only the price but also the value-added services like delivery terms, payment options, and after-sales support.
By following these steps, you can select a manufacturer who not only meets your technical requirements but also offers the best overall value.
Criteria That Define a Reliable Conveyor Roller Manufacturer
When filtering through potential manufacturers, consider these five essential criteria to find the most reliable one for your needs:
Experience and Industry Presence:
- Manufacturers with long-standing operations and a strong presence in the industry are generally more reliable, possessing extensive knowledge about the conveyor roller manufacturing process.
Technological Sophistication:
- A focus on using advanced manufacturing technologies indicates a commitment to quality and efficiency.
Quality Assurance Practices:
- Reliable manufacturers have comprehensive quality assurance practices in place, including regular testing and inspections throughout the manufacturing process.
Customer Service and Technical Support:
- Look for manufacturers who provide responsive customer service and robust technical support, which are crucial for resolving issues quickly and maintaining system uptime.
Flexibility and Scalability:
- The ability to handle orders of any size and to customize products as per customer specifications is a significant indicator of a manufacturer’s capability.
Connect with us for superior conveyor roller options.
Recommended List of Reputable Manufacturers in the Industry
Based on the above criteria, here are some reputable conveyor roller manufacturers known for their robust conveyor roller manufacturing process:
- Precision Conveyor Rollers Corp.:
- Known for high precision and reliability, and extensive use of automation in manufacturing.
- Global ConveyTech Solutions:
- Offers a wide range of customized solutions and excellent customer service, with compliance to international quality standards.
- Durable Rollers Systems Inc.:
- Specializes in producing heavy-duty rollers, known for durability and performance under demanding conditions.
- Efficient Material Handling Equipments:
- Uses state-of-the-art technology to manufacture rollers that improve system efficiencies and reduce operational costs.
- QualityRoller Manufacturers Ltd.:
- Focuses on sustainable practices and high-quality materials, backed by comprehensive customer support and scalability in production capabilities.
Selecting the right manufacturer involves careful consideration of their capabilities, the quality of their conveyor roller manufacturing process, and their ability to meet your specific needs. The right partnership can enhance your system’s efficiency, reduce downtime, and provide a competitive edge in your operational activities. By utilizing the criteria and suggestions provided, you can make an informed decision that ensures long-term benefits and consistent performance from your conveyor rollers.
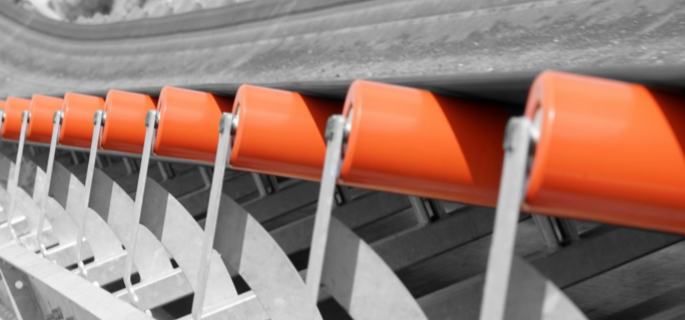
FAQs About Conveyor Roller Manufacturing Process
Conveyor rollers are made through a systematic and precise manufacturing process that involves multiple stages. Initially, the selection of material takes place which largely depends on the application requirements. Common materials include steel, stainless steel, plastic, and sometimes rubber-coated surfaces for specific needs.
Steps in the manufacturing process:
Material Selection: Depending on the application (load, environment, speed, and friction requirements), materials like steel, stainless steel, or reinforced plastics are chosen for durability and efficiency.
Cutting and Shaping: The chosen material is then cut into tubes. This can be done using laser cutting, sawing, or plasma cutting methods which provide precision and allow for mass production without significant variability.
Machining: Once the tubes are cut, they undergo machining to create exact dimensions and finishes. CNC lathes and turning centers are typically used to ensure each roller is uniform, which is crucial for the conveyor system’s efficiency.
Assembly: The next step involves assembling the cut and shaped tubes with bearings and shafts. Automated assembly lines or robotic arms are often used to insert bearings which minimize human error and enhance the assembly speed.
Welding and Joining: Some rollers require welding, especially when dealing with heavy-duty materials or designs. Advanced welding techniques are employed to ensure strong joins that can withstand the operational demands.
Coating and Finishing: Finally, the rollers might be painted, coated, or finished to enhance their functionality. For example, rubber coatings might be applied to improve grip and reduce noise.
Each of these steps needs to be meticulously controlled to ensure that the rollers are made to the highest standards of quality and precision.
Rollers are manufactured through a dedicated process that involves design, material selection, precision engineering, assembly, and testing. The process starts with the detailed design of the rollers, utilizing CAD software to simulate and adjust the design for optimal performance.
Detailed Manufacturing Steps:
Design Specification: Engineers draft detailed designs and specifications using CAD software, which guides the production process and ensures that all rollers meet the necessary standards.
Material Procurement: Materials are procured based on the design requirements. Common materials include various grades of steel, PVC, and sometimes specialized composites for high-performance needs.
Tube Formation: The material is formed into tubes, generally through rolling and welding. This process must be closely controlled to ensure that the tubes are straight and uniform.
Machining: The tubes are then machined to smooth their surfaces and bring them to the correct diameters. Precision machining tools are used to achieve the necessary tolerances.
Component Assembly: Bearings, shafts, and other components are assembled into the tubes. This process often uses automated machinery to ensure consistent quality and high throughput.
Testing and Inspection: After assembly, each roller is tested under operational conditions to ensure it meets all performance criteria. Inspection might include x-rays, ultrasonic tests, and load tests.
This methodical approach ensures each roller is robust, durable, and ready for long-term operational use.
The process of conveyor manufacturing involves several key stages, from initial design to final installation. The core component, conveyor rollers, plays a pivotal role in the entire system’s function.
Conveyor Manufacturing Process:
System Design: Initially, a comprehensive system design is prepared, which includes detailed schematics of the conveyor layout, the type of rollers needed, and the specific requirements of the operation.
Roller Design and Production: As described earlier, rollers are designed and produced through a process of material selection, cutting, shaping, machining, assembly, and testing to ensure they fit the system’s requirements perfectly.
Framework Construction: Parallel to roller production, the conveyor frame is constructed. This typically involves metalworking and welding to create a robust support structure.
Assembly of Conveyor Components: With frames and rollers prepared, the assembly involves installing the rollers onto the frame and mounting the motor and gearbox components.
Electrical and Control Systems Installation: Electrical systems that drive the motors and control systems for managing the conveyor’s speed and efficiency are installed.
Testing and Quality Assurance: The completed conveyor system is tested extensively to ensure it operates correctly under expected loads and conditions. Quality assurance checks are crucial to certify the system’s safety and efficiency.
This process requires precise coordination between different engineering disciplines, including mechanical, electrical, and computer engineering, to ensure the conveyor system is reliable and efficient.
The choice of materials for conveyor rollers depends on their specific application needs, such as load capacity, environment, speed requirements, and operational conditions. The most commonly used materials include:
Steel: Known for its high strength and durability, steel is commonly used for heavy-duty applications. It can handle significant loads and is very wear-resistant.
Stainless Steel: Used in applications requiring corrosion resistance, such as in food processing or pharmaceutical industries.
Plastic: Typically used where lower weight is required or where the operational environment might lead to corrosion (e.g., in chemical processing).
Rubber-Coated: These are used when additional grip is needed on the roller surface, which helps in moving materials smoothly, especially in incline or decline configurations.
Aluminum: Offers a lighter alternative to steel and is used in applications where weight reduction is crucial.
Each material is chosen based on its properties to meet the specific operational demands of the conveyor system, ensuring efficiency, durability, and cost-effectiveness. This material selection process is a critical part of the conveyor roller manufacturing process, influencing the overall design and functionality of the conveyor system.
Last Updated on June 21, 2024 by Jordan Smith
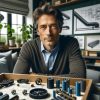
Jordan Smith, a seasoned professional with over 20 years of experience in the conveyor system industry. Jordan’s expertise lies in providing comprehensive solutions for conveyor rollers, belts, and accessories, catering to a wide range of industrial needs. From initial design and configuration to installation and meticulous troubleshooting, Jordan is adept at handling all aspects of conveyor system management. Whether you’re looking to upgrade your production line with efficient conveyor belts, require custom conveyor rollers for specific operations, or need expert advice on selecting the right conveyor accessories for your facility, Jordan is your reliable consultant. For any inquiries or assistance with conveyor system optimization, Jordan is available to share his wealth of knowledge and experience. Feel free to reach out at any time for professional guidance on all matters related to conveyor rollers, belts, and accessories.