Conveyor Roller Motor of Conveyor Systems
In modern material handling and logistics, conveyor roller systems play an essential role in moving goods efficiently across facilities. At the heart of these systems are the motors that power the rollers, enabling them to transport a wide variety of items from one location to another. These motors, commonly referred to as conveyor roller motors, are pivotal for the seamless operation of conveyor systems. Conveyor roller motor provide a safe and energy efficient alternative to conveyors traditionally powered by large electric motors.They come in various types, each designed to meet specific industrial needs and applications. For instance, AC motors are widely used for their reliability and ease of maintenance, while DC motors offer the advantage of variable speed control, making them ideal for applications requiring precision handling. Furthermore, specialized motors like servo motors can be utilized in conveyor systems that demand high precision and control. The choice of a conveyor roller motor significantly affects the efficiency, reliability, and cost-effectiveness of the conveyor system, making it a critical consideration in the design and operation of material handling systems.
What is Conveyor Roller Motor
Definition of a Conveyor Roller Motor
A conveyor roller motor is a key component of conveyor systems, providing the necessary power to drive the movement of rollers along the conveyor path. It converts electrical energy into mechanical energy, enabling the smooth and efficient transportation of goods or materials.
Importance of Motorized Rollers in Modern Conveyor Systems
- Enhanced Efficiency: Motorized rollers streamline the operation of conveyor systems by providing consistent and controlled movement, reducing the need for manual intervention and optimizing workflow.
- Increased Productivity: With automated motorized rollers, conveyor systems can operate at higher speeds and handle heavier loads, leading to improved productivity and throughput in various industries.
- Flexibility in Layout Design: The use of motorized rollers offers greater flexibility in conveyor layout design, allowing for curves, inclines, and declines to be easily incorporated into the system to accommodate space constraints or specific operational requirements.
- Reduced Maintenance: Compared to traditional belt-driven systems, motorized rollers require less maintenance due to their simpler design and fewer moving parts, resulting in lower downtime and maintenance costs.
- Improved Safety: Motorized rollers feature built-in safety mechanisms such as overload protection and emergency stop functions, enhancing workplace safety by minimizing the risk of accidents or injuries caused by conveyor malfunctions.
- Noise Reduction: The direct-drive mechanism of motorized rollers produces less noise compared to conventional conveyor systems, creating a quieter working environment for operators and nearby personnel.
- Energy Efficiency: By eliminating the need for external drive mechanisms such as belts and pulleys, motorized rollers consume less energy during operation, contributing to overall energy savings and environmental sustainability.
- Precise Control: Motorized rollers offer precise speed and torque control, allowing operators to adjust conveyor performance according to specific production demands or material handling requirements.
General Benefits of Using Motorized Conveyor Rollers
Incorporating motorized conveyor rollers into industrial operations brings about a multitude of benefits:
- Efficiency: Motorized rollers ensure smooth and continuous material flow, minimizing bottlenecks and maximizing throughput.
- Safety: The automated operation of motorized rollers reduces manual handling and associated risks, promoting a safer work environment.
- Reliability: With fewer mechanical components prone to wear and tear, motorized rollers offer greater reliability and uptime compared to traditional conveyor systems.
- Cost-effectiveness: Despite the initial investment, the long-term cost savings associated with reduced maintenance and increased productivity make motorized conveyor rollers a financially viable choice.
- Space Optimization: Motorized rollers allow for compact and space-efficient conveyor layouts, optimizing floor space utilization in warehouses or manufacturing facilities.
- Versatility: Motorized rollers are adaptable to various applications and industries, offering versatility in material handling solutions.
- Quality Assurance: The precise control provided by motorized rollers ensures consistent product quality and integrity throughout the manufacturing or distribution process.
- Employee Satisfaction: By automating repetitive tasks, motorized rollers contribute to employee satisfaction by reducing physical strain and allowing workers to focus on more value-added activities.
The integration of motorized conveyor rollers revolutionizes material handling processes, offering unparalleled efficiency, safety, and reliability in modern industrial environments.
Types of Conveyor Roller Motors
Conveyor roller motors are essential components in material handling systems, providing the necessary drive to move products along a conveyor belt. Here are the main types of conveyor roller motors:
- AC Induction Motors:
- Single-phase AC Motors: Typically used in smaller conveyor systems where less power is required.
- Three-phase AC Motors: Commonly used in industrial applications due to their higher power and efficiency.
- DC Motors:
- Brushed DC Motors: Suitable for applications requiring precise speed control.
- Brushless DC Motors: Offer higher efficiency and lower maintenance compared to brushed motors.
- Stepper Motors:
- Ideal for applications requiring precise positioning and speed control. Common in packaging and assembly line conveyors.
- Servo Motors:
- Provide high precision and control, often used in automated systems requiring exact movements.
- Gear Motors:
- Combine an electric motor with a gearbox to provide high torque at low speeds, ideal for heavy-duty conveyor applications.
- Drum Motors:
- Also known as motorized pulleys, these motors are enclosed within the roller itself, providing a compact and efficient solution.
- Linear Motors:
- Use electromagnetic force to move the conveyor directly, ideal for high-speed and high-precision applications.
- Synchronous Motors:
- Run at constant speed regardless of the load, used in applications where precise speed control is essential.
- Asynchronous Motors:
- Commonly used due to their simple design and reliability, suitable for most general conveyor applications.
- Hydraulic Motors:
- Used in applications where hydraulic power is readily available, providing high torque and smooth operation.
- Pneumatic Motors:
- Operate using compressed air, suitable for applications where explosive environments are a concern.
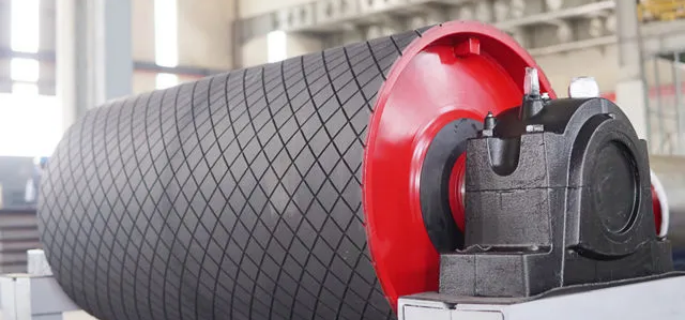
Features of Conveyor Roller Motor
Conveyor roller motors, also known as motorized rollers or drum motors, are integral components of conveyor systems. They are designed to drive conveyor belts or rollers directly, offering a compact and efficient solution for material handling. Here are some key features of conveyor roller motors:
- Compact Design:
- Integrated motor and gearbox within the roller.
- Space-saving, reducing the need for external motors and complex gear arrangements.
- Efficiency:
- Direct drive eliminates the need for chains, belts, or external gearboxes, leading to higher efficiency.
- Lower energy consumption compared to traditional conveyor systems.
- Ease of Installation and Maintenance:
- Simplified installation process due to the compact, all-in-one design.
- Reduced maintenance requirements with fewer external components and moving parts.
- Safety:
- Enclosed motor reduces the risk of injuries from exposed moving parts.
- Low voltage options available to further enhance safety.
- Versatility:
- Suitable for a wide range of applications, including logistics, packaging, food processing, and manufacturing.
- Can handle various conveyor belt types and load capacities.
- Durability and Reliability:
- Robust construction designed for continuous operation.
- High resistance to dust, water, and other environmental factors, often with IP66 or higher ratings.
- Quiet Operation:
- Reduced noise levels compared to traditional motor setups, ideal for environments where noise reduction is important.
- Control and Automation:
- Compatibility with various control systems for precise speed and torque regulation.
- Often equipped with integrated sensors and communication interfaces for smart automation.
- Scalability:
- Modular design allows for easy scalability and integration into existing conveyor systems.
- Flexible configuration options to suit specific application requirements.
- Energy Efficiency:
- Variable frequency drive (VFD) options to optimize energy use.
- Energy recovery options in regenerative braking systems.
These features make conveyor roller motors a preferred choice in modern conveyor systems, offering efficiency, reliability, and flexibility in material handling applications.
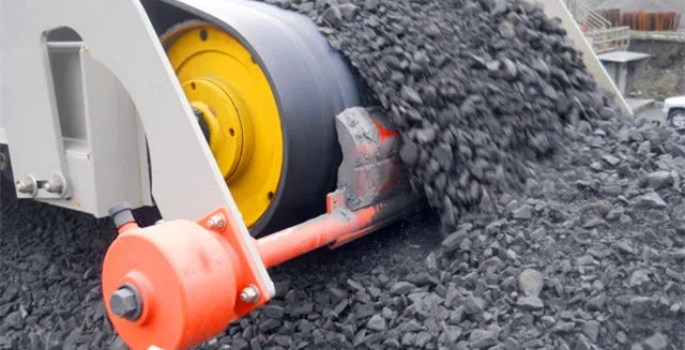
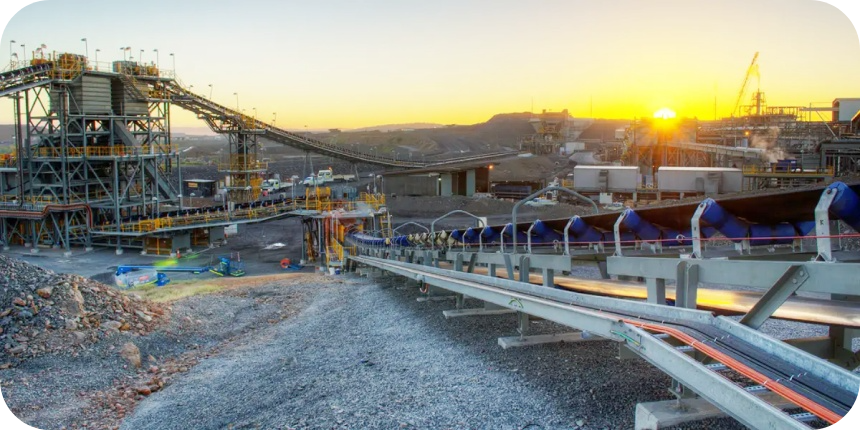
Conveyor Roller Motor Specifications and Options
Motor Specifications and Options for Conveyor Roller Motors
When selecting conveyor roller motors, it’s essential to consider various specifications and options to ensure optimal performance and compatibility with specific conveyor requirements.
Common Motor Specifications:
- Voltage: Conveyor roller motors typically operate at either 24V DC or 110V AC, depending on the application and power supply availability.
- Power Rating: The power rating of the motor determines its output capacity and ability to drive the conveyor rollers efficiently. Common power ratings range from a few watts to several hundred watts, depending on the load and speed requirements.
- Speed: Motor speed, measured in rotations per minute (RPM), influences the conveyor’s throughput and material handling efficiency. Higher speeds enable faster transportation of goods, while lower speeds may be necessary for precise positioning or delicate handling tasks.
- Torque: Torque refers to the rotational force produced by the motor and is crucial for overcoming frictional resistance and moving heavy loads along the conveyor. Motors with higher torque ratings are capable of handling larger payloads and overcoming inclines or declines in the conveyor path.
- Motor Type: Conveyor roller motors can be either brushed or brushless DC motors, each offering unique advantages in terms of efficiency, reliability, and maintenance requirements.
- Enclosure Rating: Motors may have different enclosure ratings to protect against dust, moisture, and other environmental factors, ensuring long-term durability and reliability in various operating conditions.
Varieties in Motor Capabilities Based on Conveyor Needs:
- Speed: Conveyor systems may require variable speed capabilities to accommodate different processing speeds or material handling requirements. Motors with adjustable speed settings or variable frequency drives (VFDs) offer flexibility in controlling conveyor speed according to specific production demands.
- Torque: Depending on the weight and type of materials being transported, conveyor systems may need motors with varying torque outputs to ensure smooth and reliable operation. High-torque motors are essential for handling heavy loads or starting/stopping under load conditions without stalling.
- Power: The power requirements of conveyor roller motors depend on factors such as conveyor length, load capacity, incline/decline angles, and desired throughput. Motors with higher power ratings can handle larger loads and operate more efficiently, minimizing energy consumption and maximizing productivity.
By carefully considering these motor specifications and options, businesses can select the most suitable conveyor roller motors to optimize performance, efficiency, and reliability in their material handling operations.
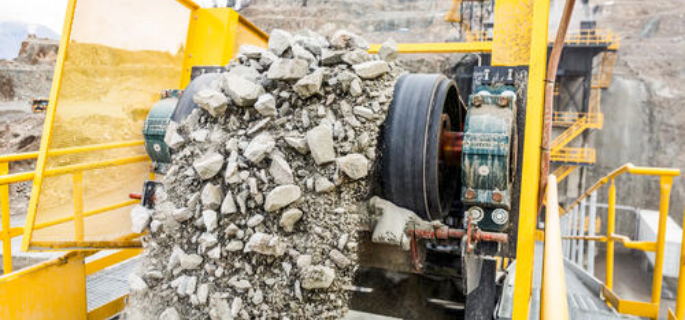
Choosing the Right Conveyor Roller Motor
When selecting the right conveyor roller motor for your application, it’s essential to consider various factors to ensure optimal performance and efficiency:
- Load Capacity: Determine the maximum weight or load that the conveyor system will need to transport. Choose a motor with sufficient torque and power to handle the expected loads without strain.
- Speed Requirements: Consider the desired conveyor speed for your application. Choose a motor with adjustable speed settings or variable frequency drives (VFDs) if variable speeds are required.
- Environment Conditions: Assess the operating environment, including temperature, humidity, dust, and moisture levels. Select a motor with appropriate enclosure ratings to ensure durability and reliability in harsh conditions.
- Duty Cycle: Determine the expected duty cycle or operating hours of the conveyor system. Choose a motor with a duty cycle rating that matches or exceeds the anticipated usage to avoid premature failure or overheating.
- Space Constraints: Consider the available space for motor installation within the conveyor system. Choose compact motorized rollers that can fit within the designated space without obstructing other components or workflow.
- Integration Compatibility: Ensure compatibility with existing conveyor equipment and control systems. Choose motorized rollers that can seamlessly integrate with your current setup to minimize installation time and costs.
- Maintenance Requirements: Evaluate the maintenance needs of different motor options. Choose motors with minimal maintenance requirements, such as brushless DC motors, to reduce downtime and maintenance costs.
- Energy Efficiency: Opt for energy-efficient motorized rollers to minimize operating costs and environmental impact. Look for motors with high efficiency ratings and energy-saving features such as regenerative braking.
- Brand Reputation: Research and compare different brands and models of conveyor roller motors. Consider factors such as reliability, performance, warranty coverage, and customer support when selecting a trusted brand like Interroll.
- Cost: Compare the upfront cost of different motor options with their long-term benefits and return on investment. Choose a motorized roller solution that offers the best balance of performance, reliability, and cost-effectiveness for your specific application.
Conveyor Roller Motor Manufacturers
Several manufacturers specialize in the production of conveyor roller motors, each offering unique solutions tailored to various industrial applications. Here are some prominent manufacturers in the field:
- Interroll:
- Known for high-quality drum motors and conveyor rollers.
- Offers a wide range of products suitable for different industries, including food processing, packaging, and distribution.
- Rulmeca:
- Specializes in motorized pulleys and conveyor components.
- Products are designed for heavy-duty applications, including mining, logistics, and bulk material handling.
- Van der Graaf:
- Provides drum motors and other conveyor components.
- Known for robust design and durability, suitable for harsh industrial environments.
- Itoh Denki:
- Pioneers in the development of motorized conveyor rollers.
- Offers innovative solutions with integrated control options for various automation needs.
- SEW-Eurodrive:
- Produces a wide range of drive technology solutions, including motorized rollers.
- Known for high efficiency and advanced control features.
- Hytrol Conveyor Company:
- Provides conveyor systems and components, including motorized rollers.
- Focuses on customized solutions for material handling.
- Dorner:
- Offers motorized roller conveyors and other conveyor systems.
- Specializes in flexible and customizable conveyor solutions for various industries.
- Ammeraal Beltech:
- Known for conveyor belts and motorized pulleys.
- Provides comprehensive solutions for conveyor system needs.
- Siemens:
- Produces a range of industrial automation products, including motorized rollers.
- Known for integrating advanced technology and control systems.
- Sparks Belting:
- Offers motorized pulleys and conveyor components.
- Focuses on providing efficient and reliable solutions for material handling.
These manufacturers are recognized for their quality, innovation, and reliability in the conveyor roller motor market. They provide a range of products to meet the specific needs of different industries, ensuring efficient and effective material handling solutions.
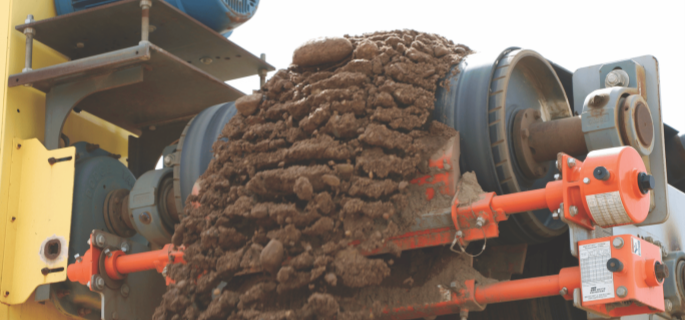
Installation and Maintenance of Conveyor Roller Motors
Installation of Conveyor Roller Motors
Installing motorized conveyor rollers requires careful attention to ensure proper functionality and performance. Follow these step-by-step guidelines for successful installation:
- Preparation: Gather all necessary tools and equipment, including mounting brackets, bolts, and electrical wiring components. Ensure that the conveyor system is powered off and safely secured before beginning the installation process.
- Positioning: Identify the placement of motorized conveyor rollers along the conveyor path, considering factors such as load distribution, spacing between rollers, and accessibility for maintenance.
- Mounting: Securely mount the motorized rollers to the conveyor frame using appropriate mounting brackets and hardware. Ensure that the rollers are aligned and leveled to prevent uneven loading and premature wear.
- Electrical Wiring: Connect the electrical wiring of the motorized rollers according to the manufacturer’s instructions and local electrical codes. Verify proper wiring connections, including power supply, ground, and control signals, to prevent electrical issues during operation.
- Testing: Conduct thorough testing of the conveyor system to verify the functionality of the motorized rollers. Check for smooth operation, proper alignment, and responsiveness to control commands before putting the system into full operation.
- Final Adjustment: Make any necessary adjustments to the motorized rollers, such as speed settings or torque limits, to optimize performance for specific material handling tasks. Monitor the system during initial operation and fine-tune as needed to achieve desired results.
Maintenance of Conveyor Roller Motors
To ensure long-term reliability and efficiency of conveyor roller motors, regular maintenance is essential. Follow these maintenance tips to keep your motorized rollers in optimal condition:
- Routine Inspection: Regularly inspect motorized rollers for signs of wear, damage, or misalignment. Address any issues promptly to prevent further damage and maintain smooth operation.
- Lubrication: Apply lubrication to the bearings and moving parts of the motorized rollers according to the manufacturer’s recommendations. Proper lubrication helps reduce friction and extend the lifespan of components.
- Cleaning: Keep motorized rollers clean and free from debris, dust, and contaminants that can affect performance. Use compressed air or a vacuum to remove buildup from rollers, bearings, and motor housings.
- Tension Adjustment: Check and adjust tension on conveyor belts or chains connected to motorized rollers to ensure proper alignment and prevent slippage or excessive wear.
- Electrical Connections: Inspect electrical connections and wiring for signs of corrosion, damage, or loose connections. Tighten connections and replace damaged wiring or components as needed to maintain electrical integrity.
- Temperature Monitoring: Monitor the operating temperature of motorized rollers and surrounding components to prevent overheating. Ensure adequate ventilation and cooling to prevent thermal damage to motors and electronics.
- Alignment: Periodically check the alignment of motorized rollers to ensure smooth and efficient operation. Misaligned rollers can cause uneven wear and increased friction, leading to premature failure.
- Vibration Analysis: Perform vibration analysis on motorized rollers to detect potential issues such as unbalanced loads or misalignment. Address any abnormal vibrations promptly to prevent further damage.
- Component Replacement: Replace worn or damaged components, such as bearings, belts, or motor brushes, as part of regular maintenance to prevent unexpected downtime and costly repairs.
- Training: Train maintenance personnel on proper inspection, maintenance, and troubleshooting procedures for motorized conveyor rollers to ensure effective upkeep of the system.
Troubleshooting Common Issues
Despite regular maintenance, conveyor roller motors may encounter occasional issues that require troubleshooting. Here are some common problems and their potential solutions:
- Motor Overheating: Check for blocked ventilation or excessive load on the conveyor system. Reduce load or improve ventilation to prevent overheating.
- Excessive Noise: Inspect for worn bearings, misalignment, or loose components. Replace worn parts and realign rollers to reduce noise levels.
- Intermittent Operation: Check electrical connections for loose or damaged wires. Tighten connections or replace damaged wiring to restore proper functionality.
- Inconsistent Speed: Verify power supply voltage and motor settings. Adjust voltage or speed settings as needed to achieve consistent operation.
- Motor Stalling: Check for mechanical obstructions or excessive load on the conveyor system. Clear obstructions and reduce load to prevent motor stalling.
- Erratic Behavior: Inspect control systems and sensors for malfunctions or interference. Calibrate sensors and troubleshoot control circuits to resolve erratic behavior.
By following these installation, maintenance, and troubleshooting guidelines, you can ensure the reliable performance and longevity of your conveyor roller motors, minimizing downtime and maximizing productivity in your material handling operations.
Conveyor Roller Motor Replacement and Parts
When and Why to Consider Replacing a Conveyor Roller Motor
Replacing a conveyor roller motor becomes necessary under various circumstances to ensure optimal performance and prevent downtime in material handling operations. Consider the following situations:
- Wear and Tear: Over time, conveyor roller motors experience wear and tear due to continuous operation, leading to decreased efficiency and reliability. Consider replacement when motors show signs of excessive wear, such as decreased performance, increased noise, or frequent breakdowns.
- Damage or Failure: Motors may become damaged due to mechanical impact, electrical faults, or environmental factors such as moisture or debris ingress. In cases of irreparable damage or catastrophic failure, replacement is necessary to restore conveyor functionality.
- Obsolete Technology: As technology advances, older conveyor roller motors may become obsolete or incompatible with newer conveyor systems or control technologies. Consider upgrading to modern motor options to benefit from improved efficiency, reliability, and functionality.
- Increased Load Requirements: If the conveyor system experiences an increase in load capacity or throughput demands beyond the capabilities of existing motors, replacement with higher-capacity motors may be necessary to meet operational requirements.
Guide to Finding and Purchasing the Right Motor and Parts
When seeking to replace conveyor roller motors or parts, follow this guide to ensure a smooth and successful procurement process:
- Identify Specifications: Determine the required specifications for the replacement motor, including voltage, power rating, speed, torque, and mounting dimensions. Refer to manufacturer documentation or consult with a qualified technician to ensure compatibility with existing conveyor systems.
- Research Suppliers: Research reputable suppliers or manufacturers of conveyor roller motors and parts, considering factors such as product quality, reliability, pricing, and customer support. Look for suppliers with a track record of providing high-quality aftermarket services and compatibility with a wide range of conveyor systems.
- Check Availability: Verify the availability of the desired motor or parts from the selected supplier, considering factors such as lead time, stock availability, and shipping options. Ensure timely delivery to minimize downtime and disruptions to material handling operations.
- Assess Compatibility: Evaluate the compatibility of replacement motors or parts with existing conveyor systems, considering factors such as mounting configuration, electrical connections, and control interfaces. Ensure proper fit and functionality to avoid compatibility issues during installation.
- Consider Aftermarket Services: Look for suppliers that offer comprehensive aftermarket services, including installation support, technical assistance, and warranty coverage. Choose suppliers that prioritize customer satisfaction and provide ongoing support throughout the lifecycle of the conveyor roller motor.
- Review Pricing and Terms: Compare pricing and terms from multiple suppliers to ensure competitive pricing and favorable terms. Consider factors such as warranty coverage, return policies, and aftermarket support when making your purchasing decision.
Focus on Aftermarket Services and Compatibility
When replacing conveyor roller motors or parts, prioritize aftermarket services and compatibility to ensure a seamless integration and long-term reliability of the replacement components. Choose suppliers that offer comprehensive support and ensure compatibility with existing conveyor systems, minimizing downtime and maximizing operational efficiency. By focusing on aftermarket services and compatibility, you can streamline the replacement process and achieve optimal performance from your conveyor roller motors.
Cost Considerations of Conveyor Roller Motor
Analysis of Conveyor Roller Motor Price Points
When considering the cost of conveyor roller motors, it’s essential to analyze various price points to make an informed decision:
- Initial Investment: The upfront cost of purchasing conveyor roller motors includes the cost of the motors themselves, as well as any additional components or accessories required for installation. Prices can vary depending on factors such as motor specifications, brand reputation, and supplier pricing policies.
- Operating Costs: In addition to the initial investment, consider the ongoing operating costs associated with conveyor roller motors, including energy consumption, maintenance, and potential downtime. Opting for energy-efficient and low-maintenance motors can help reduce long-term operating costs and enhance overall cost-effectiveness.
- Total Cost of Ownership (TCO): Evaluate the total cost of ownership over the expected lifespan of the conveyor system, taking into account not only the initial purchase price but also maintenance, repairs, and energy consumption. A comprehensive TCO analysis can provide a more accurate assessment of the overall cost-effectiveness of different motor options.
Cost-Benefit Analysis of Investing in Quality Motorized Rollers versus Traditional Systems
Investing in quality motorized rollers offers several cost-benefit advantages over traditional conveyor systems:
- Improved Efficiency: Motorized rollers offer enhanced efficiency compared to traditional belt-driven systems, resulting in higher throughput and productivity. The increased efficiency can translate into cost savings through reduced labor requirements and increased output.
- Reduced Maintenance Costs: Quality motorized rollers typically have lower maintenance requirements compared to traditional conveyor systems, resulting in reduced downtime and maintenance costs over time. With fewer moving parts and simplified design, motorized rollers offer greater reliability and longevity, minimizing the need for costly repairs and replacements.
- Energy Savings: Energy-efficient motorized rollers consume less power during operation compared to traditional conveyor systems, resulting in lower energy bills and reduced environmental impact. Investing in energy-efficient motors can lead to significant long-term cost savings and contribute to sustainability initiatives.
- Enhanced Safety: Motorized rollers incorporate built-in safety features such as overload protection and emergency stop functions, reducing the risk of accidents and injuries in the workplace. By prioritizing safety, businesses can avoid potential liability costs associated with workplace incidents.
Long-Term Financial Benefits of Energy-Efficient and Durable Motorized Rollers
The long-term financial benefits of investing in energy-efficient and durable motorized rollers include:
- Energy Savings: Energy-efficient motorized rollers consume less power during operation, resulting in lower electricity bills and reduced operational costs over time. By investing in energy-efficient motors, businesses can achieve significant long-term savings on energy expenses.
- Reduced Maintenance Costs: Durable motorized rollers require less frequent maintenance and repairs compared to traditional conveyor systems, leading to lower maintenance costs and decreased downtime. By minimizing maintenance requirements, businesses can allocate resources more efficiently and focus on core operations.
- Extended Lifespan: Quality motorized rollers are built to withstand heavy-duty usage and harsh operating conditions, resulting in longer service life and reduced replacement costs. By investing in durable rollers, businesses can avoid frequent replacements and associated expenses, contributing to overall cost savings.
- Improved Productivity: Motorized rollers enable smoother and more efficient material handling, leading to increased productivity and throughput. By optimizing workflow and reducing processing times, businesses can maximize revenue potential and achieve higher returns on investment.
- Enhanced Reliability: Durable motorized rollers offer greater reliability and uptime compared to traditional conveyor systems, reducing the risk of unexpected downtime and production delays. By ensuring continuous operation, businesses can maintain customer satisfaction and avoid potential revenue losses due to interruptions in service.
Find the right conveyor roller for your specific requirements.
Where to Buy Conveyor Roller Motor
Recommendations for Purchasing Conveyor Roller Motors
When looking to purchase conveyor roller motors, consider the following recommendations to ensure a smooth and successful procurement process:
- Direct from Manufacturers: Purchase conveyor roller motors directly from reputable manufacturers to ensure product quality, warranty coverage, and technical support. Manufacturers often offer customization options and competitive pricing for bulk orders.
- Authorized Distributors: Buy from authorized distributors of conveyor roller motors to ensure authenticity and reliability of products. Authorized distributors typically have access to a wide range of inventory and can provide valuable support and assistance throughout the purchasing process.
- Online Marketplaces: Explore online marketplaces such as Amazon, Alibaba, or eBay for a variety of conveyor roller motors from different suppliers and brands. Be sure to read product reviews, compare prices, and verify seller reputation before making a purchase.
- Industrial Suppliers: Purchase conveyor roller motors from specialized industrial suppliers or distributors catering to material handling and automation industries. These suppliers often carry a comprehensive range of conveyor components and can provide expert advice on product selection and compatibility.
- Trade Shows and Exhibitions: Attend trade shows and exhibitions focused on material handling, logistics, and automation to discover new products and suppliers in the conveyor roller motor market. These events offer opportunities to network with industry professionals and explore the latest innovations in conveyor technology.
- Consult with Experts: Seek guidance from experienced engineers, consultants, or technicians specializing in conveyor systems and motorized rollers. Consulting with experts can help you identify the most suitable motor options for your specific application and operational requirements.
Highlight on Heavy-Duty Roller Conveyor and Wide Conveyor Rollers for Specific Industrial Needs
For heavy-duty industrial applications requiring robust and durable conveyor solutions, consider heavy-duty roller conveyors and wide conveyor rollers. These specialized conveyor systems are designed to handle heavy loads, withstand harsh environments, and facilitate efficient material handling in demanding industrial settings.
Heavy-duty roller conveyors feature sturdy construction, reinforced rollers, and high-capacity bearings to support heavy loads and withstand frequent use. They are ideal for applications such as automotive manufacturing, logistics, and distribution centers where large and heavy items need to be transported efficiently.
Wide conveyor rollers, also known as extra-wide rollers or mega rollers, are designed to accommodate oversized or irregularly shaped materials that may not fit on standard conveyor systems. These rollers provide increased surface area and support for larger loads, enabling seamless transportation of bulky items such as pallets, machinery, or industrial equipment.
Mention of Reputable Suppliers and Brands, Emphasizing Interroll Products
When purchasing conveyor roller motors, consider reputable suppliers and brands known for their quality, reliability, and innovation in the field of material handling equipment. Interroll is a leading global provider of motorized rollers and conveyor components, offering a wide range of products tailored to various industrial applications.
Interroll’s motorized rollers are renowned for their high performance, energy efficiency, and durability, making them a preferred choice for businesses worldwide. With a focus on innovation and customer satisfaction, Interroll continues to set industry standards for conveyor technology, offering solutions that enhance productivity, safety, and efficiency in material handling operations.
To ensure you’re getting genuine Interroll products and exceptional service, purchase conveyor roller motors from authorized Interroll distributors or directly from the manufacturer. By choosing Interroll, you can trust in the quality and reliability of your conveyor roller motors, backed by expert support and a commitment to excellence in material handling solutions.
FAQs about Conveyor Roller Motor
Roller conveyors are versatile and used in various industries for material handling. The type of motor used in roller conveyors can vary depending on the application and the required load capacity. Commonly, roller conveyors use gear motors that allow for control over speed and torque. These motors are typically AC motors for constant speed applications; however, brushless DC motors can also be used for their efficiency and control over a wide range of speeds. For heavier-duty tasks or more precise control, servo motors might be implemented. The choice of motor is essential to the system’s efficiency, reliability, and maintenance requirements.
A motorized roller conveyor, also known as a powered roller conveyor, is a type of conveyor system where the rollers that help move the cargo along the belt are powered by motors. This differs from traditional gravity conveyors, where objects move down the conveyor by the force of gravity or manual pushing. In motorized roller conveyors, each roller or a series of rollers have an integrated motor inside or connected through a chain drive system. These motors control the movement and speed of the rollers, allowing for smooth, consistent, and adjustable transportation of goods, which can be essential for timing and synchronizing various processes within industrial operations.
Rollers in conveyor systems can be categorized broadly into two types: drive rollers and idler rollers. Drive rollers are powered rollers that are connected to a motor and responsible for moving the conveyor belt or directly propelling materials along the system. On the other hand, idler rollers are not motorized and typically serve to support the belt and materials being transported or guiding and routing the belt as it moves. These rollers can be made from various materials, including metal, plastic, or rubber, depending on the application needs, such as the weight of the materials being conveyed and the surrounding environment (e.g., temperature, chemicals present).
A conveyor roller is a cylindrical component that sits within a frame or bracket and is an integral part of a conveyor belt system. These rollers work in conjunction to facilitate the smooth and efficient transport of goods and materials from one point to another. They can be individually linked to a motorized system or be part of a gravity-fed or manual push conveyor arrangement. Conveyor rollers vary in size, material, and design based on their specific role and the conveyor’s operational requirements. The design includes consideration for load-bearing capacity, durability, friction levels, and resistance to environmental factors like moisture, chemicals, and temperature.
Last Updated on July 29, 2024 by Jordan Smith
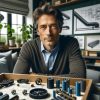
Jordan Smith, a seasoned professional with over 20 years of experience in the conveyor system industry. Jordan’s expertise lies in providing comprehensive solutions for conveyor rollers, belts, and accessories, catering to a wide range of industrial needs. From initial design and configuration to installation and meticulous troubleshooting, Jordan is adept at handling all aspects of conveyor system management. Whether you’re looking to upgrade your production line with efficient conveyor belts, require custom conveyor rollers for specific operations, or need expert advice on selecting the right conveyor accessories for your facility, Jordan is your reliable consultant. For any inquiries or assistance with conveyor system optimization, Jordan is available to share his wealth of knowledge and experience. Feel free to reach out at any time for professional guidance on all matters related to conveyor rollers, belts, and accessories.