Conveyor Roller Mounting Brackets: Selection and Uses
Conveyor systems are integral to the operations of a wide range of industries, from manufacturing and packaging to distribution and logistics. These systems are critical for the efficient, timely, and safe handling of materials, which is paramount for maintaining high productivity and operational standards. At the heart of these conveyor systems are the conveyor roller mounting brackets, which play a crucial role in ensuring the stability and performance of conveyor rollers. These brackets support the rollers that move materials along the conveyor belt, making them essential components for the optimal performance of conveyor systems. By securing the rollers in place, conveyor roller mounting brackets not only stabilize the conveyor belt but also enhance the system’s overall efficiency and safety. Their importance cannot be overstated, as they directly impact the functionality and reliability of the conveyor system.
Key Components of Conveyor Systems: Emphasizing Conveyor Roller Mounting Brackets
Conveyor systems are essential in various industries for the smooth and efficient transport of materials from one point to another. Central to these systems are the conveyor rollers, which facilitate the movement of materials with minimal effort. Below, we delve deeper into the roles and complexities of these components, particularly focusing on conveyor roller mounting brackets.
Conveyor Rollers: The Backbone of Material Handling
Conveyor rollers are cylindrical components that rotate to move materials along a set path or direction. They are mounted on the frame of the conveyor system and can vary significantly in size, material, and design based on the application they are designed for. The primary role of conveyor rollers is to support and move the conveyor belt or the materials directly placed on the rollers smoothly and efficiently.
The effectiveness of conveyor rollers in material handling is evident in industries like mining, automotive, and packaging, where they reduce manual labor and enhance the speed and safety of production processes. By using gravity or motor power, they manage to transfer heavy or bulky materials with ease, showcasing their versatility and indispensability in industrial operations.
Overview of Conveyor Roller Parts
Conveyor rollers consist of several key components that ensure their effective operation. These include the roller shell, shaft, bearings, and the mounting brackets which are critical yet often overlooked. Each component plays a pivotal role in the functionality and longevity of the conveyor roller.
- Roller Shell: This is the outer tube of the roller and can be made from various materials such as steel, plastic, or rubber, depending on the application.
- Shaft: The shaft runs through the center of the roller shell and is connected at both ends to the conveyor frame, typically via mounting brackets. The shaft’s material and diameter are chosen based on the load it needs to support.
- Bearings: Bearings allow the roller shell to rotate smoothly around the shaft with minimal friction. They are crucial for the efficiency of the conveyor rollers, as they directly affect the motion and control of the conveyor belt.
- Conveyor Roller Mounting Brackets: These components are essential for securing the shafts to the conveyor frame, ensuring the rollers are aligned and stable. Conveyor roller mounting brackets are designed to withstand the load and environmental challenges of the application. They come in various designs, such as fixed or adjustable, to accommodate different types of rollers and installation requirements.
The Critical Role of Conveyor Roller Mounting Brackets
Conveyor roller mounting brackets are not merely peripheral components; they are central to the precise and stable setup of conveyor rollers. These brackets must be robust and accurately configured to maintain the alignment of rollers, which is crucial for the uniform distribution of materials and the prevention of belt misalignment issues.
In essence, conveyor roller mounting brackets not only support the physical structure of the conveyor but also enhance the system’s overall functionality and efficiency. They ensure that the rollers are mounted at the correct height and angle, crucial for optimal material transport and minimal wear on the system.
Conveyor systems, with their reliance on conveyor rollers, demonstrate the intricate interplay of engineering and practical design. Each component, especially the conveyor roller mounting brackets, is vital for the system’s efficiency and reliability, highlighting the importance of thoughtful design and material selection in industrial equipment.
The Critical Role of Conveyor Roller Mounting Brackets
Conveyor roller mounting brackets are pivotal in the assembly and effective operation of conveyor systems. They secure the conveyor rollers to the conveyor frame, ensuring stability, proper alignment, and smooth operation of the entire system. This detailed examination not only explores what conveyor roller mounting brackets are but also delves into the different types available and the criteria for selecting the appropriate type for specific applications.
Learning Conveyor Roller Mounting Brackets
Conveyor roller mounting brackets are specialized hardware used to install rollers on a conveyor system. These brackets are designed to hold the roller in place, providing the necessary support and alignment to maintain an efficient pathway for materials handling. They are typically made from metals such as steel or aluminum for durability and strength, as conveyor systems often operate in demanding industrial environments where reliability is critical.
Types of Conveyor Roller Mounting Brackets
There are several types of conveyor roller mounting brackets, each suited for different applications and roller types. The choice of bracket type affects the conveyor’s maintenance ease, the speed of installation, and the system’s overall stability and performance.
Criteria for Selecting the Right Conveyor Roller Mounting Bracket
Selecting the right conveyor roller mounting brackets is critical for ensuring the optimal performance and longevity of the conveyor system. Here are eight essential criteria to consider when choosing a mounting bracket:
- Load Capacity: The bracket should support the weight and type of material being transported without bending or breaking.
- Material Compatibility: Choose a bracket material that is compatible with the roller material and the environment (e.g., corrosion-resistant if exposed to chemicals).
- System Speed: For high-speed conveyor systems, select brackets designed to handle dynamic loads and reduce vibrations.
- Environmental Conditions: If the conveyor will operate in harsh environments, such as extreme temperatures or wet conditions, the brackets must be durable enough to withstand these conditions.
- Installation Ease: Consider the ease of installation, as complex brackets can increase setup time and maintenance costs.
- Maintenance Requirements: Some brackets are easier to maintain and replace than others; opting for these can reduce downtime and operational costs.
- Adjustability: Adjustable brackets allow for finer control and alignment of the conveyor rollers, which can be crucial for the precise handling of materials.
- Cost: While not the only factor, the cost of the brackets should be considered in relation to their life expectancy and the value they add to the conveyor system.
Conveyor roller mounting brackets play a critical role in the functionality and efficiency of conveyor systems. They ensure that the rollers are securely attached to the conveyor frame, properly aligned, and capable of handling the designated loads. By understanding the different types of brackets available and considering the appropriate criteria for selection, companies can significantly enhance their conveyor system’s reliability and performance. This strategic approach to selecting conveyor roller mounting brackets helps in optimizing material handling processes and minimizing potential downtime and maintenance issues.
Types of Conveyor Roller Mounting Brackets
Conveyor roller mounting brackets are integral to the assembly and functionality of conveyor systems, securing the rollers to the frame and ensuring efficient material transfer. These brackets vary widely in design and specification, often tailored for specific uses or environments. This section explores the distinct types of conveyor roller mounting brackets, including used brackets, heavy-duty brackets, and guide rail brackets.
Used Conveyor Roller Mounting Brackets
Advantages:
- Cost-Effective: Purchasing used conveyor roller mounting brackets can significantly reduce costs, which is particularly beneficial for budget-conscious businesses.
- Eco-Friendly: Opting for used brackets minimizes waste, supporting sustainability efforts by reusing materials and resources.
- Tested Durability: Used brackets have been tested in real-world conditions, offering evidence of their durability and reliability.
- Immediate Availability: Unlike new brackets that may require manufacturing or delivery time, used brackets are often available immediately.
- Wide Selection: Buyers might find a broader range of styles or types of used brackets available from surplus or decommissioned systems.
- Regulatory Compliance: Used brackets often meet existing safety and operational standards, providing assurance of compliance.
Considerations:
- Wear and Tear: Assessing the condition is crucial as used brackets may have wear that could impact performance.
- Compatibility: Ensuring that the used brackets fit with existing systems is essential to avoid mismatches that can cause operational failures.
- Lifespan: Used brackets may have a shorter remaining lifespan, which could lead to earlier replacement needs.
- Maintenance: They might require more maintenance or adjustments to perform optimally.
- Availability of Replacements: Finding exact matches for replacements or additional brackets can be challenging.
- Corrosion or Damage: Inspecting for corrosion, stress fractures, or other damages that could impair functionality is necessary.
- No Warranty: Used brackets typically come without a warranty, increasing the risk if failures occur.
- Supplier Reliability: The source of the used brackets should be reputable to ensure the quality and condition of the parts.
- Safety Standards: It’s important to verify that the used brackets still meet all current safety standards.
- Customization Limits: Used brackets may offer limited customization options, which might not fully meet specific needs.
Heavy Duty Conveyor Roller Mounting Brackets
Heavy-duty conveyor roller mounting brackets are designed to withstand extreme conditions, including high loads, severe impacts, and harsh environments. These brackets are crucial for applications where ordinary brackets would fail.
Applications:
- Mining and Quarrying: Handling sharp, heavy materials that could damage standard brackets.
- Automotive Manufacturing: Supporting the heavy loads and high throughput of automotive parts.
- Construction Materials: Carrying weighty materials like cement and metals with high abrasion resistance.
- Heavy Machinery: Used in the manufacturing and assembly of large machines.
- Food Processing: Withstand the intensive cleaning processes and heavy bins in food production.
- Recycling Facilities: Managing the unpredictable loads and potential impacts from recycled materials.
- Maritime and Dockside: Resisting corrosion from salty sea air and water exposure.
- Agricultural: Handling large volumes of raw agricultural products.
- Aerospace: Capable of supporting the stringent requirements and heavy components in aerospace facilities.
These brackets are typically made from hardened steel or alloys for enhanced strength and durability. They may feature reinforced structures or thicker bodies to handle the additional stress.
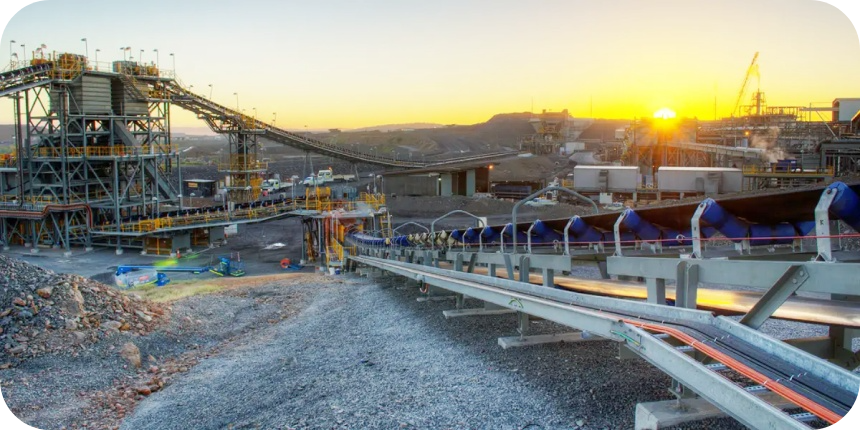
Conveyor Guide Rail Brackets
Conveyor guide rail brackets play a pivotal role in maintaining the alignment and tracking of conveyor belts and rollers, crucial for the consistent and reliable movement of materials.
Functionality:
- Precision Alignment: These brackets hold guide rails that direct the conveyor belt’s path, crucial in avoiding misalignment that can cause material spillage or damage.
- Enhanced Stability: By securing the rails in place, these brackets ensure that the conveyor operates smoothly, even under high-speed or variable load conditions.
- Versatile Installation: Guide rail brackets can be adjusted and installed at various points along the conveyor frame, allowing for customized pathway control.
Each type of conveyor roller mounting brackets, from used to heavy-duty to guide rail brackets, serves a specific purpose and offers unique benefits. Selecting the right type involves considering the operational demands, environmental conditions, and the desired lifespan of the conveyor system. These choices directly impact the efficiency, safety, and cost-effectiveness of material handling operations.
Specialized Conveyor Rollers with Conveyor Roller Mounting Brackets
Conveyor systems are integral to numerous industrial and manufacturing processes, facilitating the efficient and smooth transport of goods. Specialized conveyor rollers and their conveyor roller mounting brackets play pivotal roles in optimizing these systems for specific applications. Let’s delve deeper into the configurations, applications, and necessities of various specialized conveyor rollers.
4 Conveyor Roller Setups
Configurations and Applications
Four-roller setups are specifically designed to enhance the distribution and control of loads across the conveyor system. These configurations often involve two sets of rollers placed at strategic intervals and angles to stabilize the conveyed materials effectively. Conveyor roller mounting brackets in these setups are critical for:
- Ensuring precise alignment and spacing between the rollers.
- Reducing the stress on individual rollers, thus extending the system’s lifespan.
- Providing the needed flexibility to handle various material sizes and weights.
- Minimizing the conveyor belt’s slippage by maintaining optimal tension and traction.
- Facilitating easier maintenance and replacement of rollers.
- Improving the conveyor’s overall efficiency through better load distribution.
- Enhancing the smooth operation of the conveyor, which is crucial for sensitive cargo.
Heavy Duty Conveyor Rollers
Necessity and Use-Cases
Heavy-duty conveyor rollers are built to withstand the rigorous conditions of industrial environments, such as high load capacities and continuous operation. These rollers, combined with robust conveyor roller mounting brackets, are essential for:
- Mining operations where they transport raw extracted materials.
- The construction industry for moving large building materials.
- Manufacturing sectors, especially in metal processing and automotive assembly.
- Agricultural applications for handling large volumes of produce or feed.
- Waste management facilities in sorting and processing large debris.
- Steel mills and heavy machinery industries.
- Dockyards and shipping containers where heavy goods are loaded and unloaded.
Small Diameter Conveyor Rollers
Advantages
Small diameter rollers are tailored for lightweight materials and tighter spaces where standard rollers cannot operate effectively. The integration of compatible conveyor roller mounting brackets offers several advantages:
- Improved handling of small or delicate items, reducing damage during transport.
- Enhanced precision in product orientation and positioning, which is vital for assembly lines in electronics and pharmaceuticals.
- Greater flexibility in system design, allowing for curves and tight turns.
- Reduced system weight, which can lower energy consumption.
- Easier integration into compact spaces, maximizing the use of the available area.
- Lower rolling resistance, which enhances the efficiency of the conveyor system.
- The capability to operate at higher speeds due to reduced inertia.
Wide Conveyor Rollers
Applications and Benefits
Wide conveyor rollers are designed to handle larger and heavier loads, which can streamline operations in various industrial applications. The proper conveyor roller mounting brackets are crucial for:
- Ensuring the stability and balance of wide loads, preventing tipping or misalignments.
- Distributing the weight of heavy or bulky items more evenly across the system.
- Minimizing the wear on the conveyor belt and infrastructure.
- Allowing for smoother and more consistent movement of large items.
- Reducing the energy required to move heavy loads by decreasing rolling resistance.
- Facilitating the transport of wide materials such as panels, sheets, and large assemblies.
- Enhancing safety by preventing accidents related to load instability.
Choosing the right type of specialized conveyor rollers and conveyor roller mounting brackets is critical for meeting the specific needs of various industrial applications. Each type of roller setup offers distinct benefits and is designed to handle particular challenges associated with different materials and environmental conditions. Proper selection and installation ensure the longevity and efficiency of the conveyor system, ultimately impacting the operational success of the processes they support.
Enhancing Conveyor Efficiency with Lid Clamps and Conveyor Roller Mounting Brackets
Conveyor systems are pivotal in industrial settings, streamlining the movement and management of materials. To optimize these systems, various accessories are employed, including lid clamps and conveyor roller mounting brackets. These components not only enhance the functionality and safety of conveyor systems but also improve their operational efficiency. Here, we delve into the roles of these accessories and provide detailed tips on maintaining and inspecting conveyor roller parts to ensure longevity and reliability.
Conveyor Lid Clamps and Their Utility
Conveyor lid clamps are designed to secure the covers or guards of conveyor systems. These clamps are crucial for preventing dust and debris from contaminating the product and protect the moving parts of the conveyor from environmental factors, which can lead to wear and tear or damage during operation.
Functions of Conveyor Lid Clamps:
- Safety Enhancement: Keeps protective covers in place, preventing accidental contact with moving parts.
- Contamination Prevention: Helps to shield the conveyor’s contents, maintaining the quality and integrity of materials.
- Maintenance Simplification: Allows for quick access to conveyor internals for repairs and cleaning by easily securing and releasing covers.
In addition to lid clamps, the integration of robust conveyor roller mounting brackets is essential. These brackets hold the rollers firmly, reducing vibrations and minimizing the risk of misalignments or operational halts, which are critical for maintaining a smooth and efficient workflow.
Importance of Conveyor Roller Mounting Brackets
Conveyor roller mounting brackets are key to the structural integrity and efficiency of conveyor systems. They provide the necessary support for the rollers, ensuring that they remain in the correct positional alignment with minimal wobble, which is vital for the even distribution of materials across the belt.
Core Advantages:
- Stabilizes Rollers: Prevents lateral movement of rollers, which can cause uneven wear and tear on the conveyor belt.
- Facilitates Maintenance: Makes the installation and replacement of rollers easier, reducing downtime and maintenance costs.
- Enhances System Longevity: By maintaining proper alignment, these brackets reduce the strain on the conveyor belt and other mechanical components.
Tips for Maintaining and Inspecting Conveyor Roller Parts
Regular maintenance and inspection of conveyor parts are critical to avoid downtime and ensure efficient operation. Below are 12 practical tips for maintaining the longevity and reliability of conveyor rollers and their components, including conveyor roller mounting brackets:
- Regular Cleaning: Keep the rollers and brackets free from dust and debris to prevent build-up that can impair functionality.
- Lubrication: Periodically lubricate bearings and moving parts to reduce friction and wear.
- Check Alignment: Regularly inspect the alignment of rollers and adjust brackets as necessary to prevent misalignment-related wear.
- Inspect for Wear: Look for signs of wear and tear on rollers and brackets. Replace parts that show significant damage.
- Tighten Fasteners: Ensure that all mounting fasteners are tightened properly as they can loosen over time due to vibrations.
- Monitor Load Capacities: Avoid overloading the conveyor system which can stress rollers and brackets.
- Listen for Noises: Unusual noises often indicate a problem. Investigating noises promptly can prevent further damage.
- Replace Damaged Rollers: Damaged rollers can cause further harm to the conveyor belt and should be replaced promptly.
- Use Correct Parts: Always use the right type of rollers and brackets for your specific conveyor system to ensure compatibility and efficiency.
- Schedule Regular Inspections: Establish a routine inspection schedule to catch issues early and keep the conveyor system in optimal condition.
- Educate Your Team: Make sure that all personnel are trained on the proper care and maintenance of conveyor systems.
- Keep Records: Maintain detailed records of inspections, maintenance, and replacements to help predict future needs and ensure continuity.
By following these tips and utilizing essential accessories like conveyor lid clamps and conveyor roller mounting brackets, businesses can significantly enhance the efficiency, safety, and longevity of their conveyor systems. These practices not only safeguard the machinery and the materials they transport but also optimize overall operational productivity.
Choosing the Right Conveyor Roller Mounting Brackets
Selecting the correct conveyor roller mounting brackets is a crucial step in ensuring the efficiency, safety, and longevity of a conveyor system. These brackets play a significant role in maintaining the alignment, stability, and performance of the conveyor rollers. Here, we explore the essential factors to consider and the importance of compatibility in choosing the right mounting brackets for your conveyor system.
Factors to Consider
- Load Capacity: The brackets must support the maximum expected load without deforming or failing. Assess the weight and distribution of the materials to be conveyed and choose brackets accordingly.
- Environment: Consider the operating environment. For corrosive, wet, or particularly dusty environments, select brackets made from materials resistant to such conditions.
- Application Type: The nature of the application influences bracket selection. Food processing applications may require easy-to-clean and sanitary brackets, whereas heavy industrial applications demand robust and durable designs.
- Material and Coating: The material of the bracket and its coating can significantly impact its durability and suitability for specific environments. Stainless steel or coated metal brackets are ideal for harsh conditions.
- Adjustability and Installation: Look for brackets that offer adjustability to align rollers perfectly within the system. Also, consider the ease of installation and maintenance.
- Compatibility with Rollers: Ensure the brackets fit the diameter and length of the rollers. Misfit can lead to operational issues and increased wear.
Importance of Compatibility
- With Conveyor Rollers: Compatibility between the brackets and rollers ensures smooth operation, reduces wear, and extends the lifespan of both the rollers and the conveyor belt.
- With Overall System Design: The brackets should integrate seamlessly into the system design, supporting efficient load transfer and maintaining alignment throughout the conveyor’s path.
- Ease of Maintenance: Compatible brackets facilitate easier maintenance and replacement of rollers, reducing downtime.
- Operational Efficiency: Properly selected brackets contribute to the conveyor system’s overall efficiency by minimizing disruptions and maintaining consistent flow.
- Safety: Incompatible or poorly chosen brackets can lead to roller misalignment, posing safety risks to operators and potentially leading to product damage.
- Cost-effectiveness: Choosing the right brackets from the start can prevent costly modifications or replacements down the line, ensuring cost-effective operation.
- Flexibility and Scalability: Compatible brackets can accommodate future system modifications or expansions more easily, offering greater flexibility and scalability.
- Warranty and Support: Compatibility with the conveyor system’s specifications often aligns with manufacturer warranties and support services, ensuring access to parts and maintenance advice.
The careful selection of conveyor roller mounting brackets is fundamental to the construction and operation of a reliable and efficient conveyor system. By considering factors such as load capacity, environment, and compatibility with rollers and system design, you can ensure your conveyor performs optimally, with minimal downtime and maximum productivity.
Last Updated on June 21, 2024 by Jordan Smith
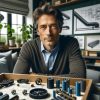
Jordan Smith, a seasoned professional with over 20 years of experience in the conveyor system industry. Jordan’s expertise lies in providing comprehensive solutions for conveyor rollers, belts, and accessories, catering to a wide range of industrial needs. From initial design and configuration to installation and meticulous troubleshooting, Jordan is adept at handling all aspects of conveyor system management. Whether you’re looking to upgrade your production line with efficient conveyor belts, require custom conveyor rollers for specific operations, or need expert advice on selecting the right conveyor accessories for your facility, Jordan is your reliable consultant. For any inquiries or assistance with conveyor system optimization, Jordan is available to share his wealth of knowledge and experience. Feel free to reach out at any time for professional guidance on all matters related to conveyor rollers, belts, and accessories.