Selecting Conveyor Roller Pulley Systems
A conveyor roller pulley is a critical component in the mechanics of conveyor belt systems, used primarily to guide and drive the belt as well as manage the load being transported. Conveyor roller pulley devices change the direction of the belt or drive it with precision,ensure optimal tension and efficiency. These pulleys are strategically positioned along the conveyor system and can be tailored in various sizes and materials depending on the application’s specific requirements. The design and functionality of a conveyor roller pulley ensure that the belt moves efficiently and aligns correctly, preventing any slippage or misalignment that could lead to operational issues.The importance of these pulleys within the conveyor system cannot be overstated. They not only support the movement and direction of the conveyor belt but also significantly contribute to the overall stability and efficiency of the transportation process. Properly functioning conveyor roller pulleys reduce the wear and tear on the belt, extend its lifespan, and decrease the energy consumption of the entire system.
Conveyor Pulleys
Conveyor Head and Tail Pulley
The head and tail pulleys in a conveyor system are vital components that play significant roles in the operation and efficiency of conveyor systems. These conveyor roller pulleys are located at either end of the conveyor system, with the head pulley at the discharge end and the tail pulley at the loading end. Their primary function is to drive the conveyor belt and control its tension, which is crucial for steady and reliable movement of materials across the system.
Roles of Head and Tail Pulleys
Driving the Conveyor Belt:The head pulley is connected to the motor and gearbox components of the conveyor system. This conveyor roller pulley is responsible for transferring the driving force to the conveyor belt, enabling it to move materials efficiently from one point to another. Its surface may be covered with a rubber lagging that helps to increase friction between the belt and the pulley, which prevents the belt from slipping.
Controlling Belt Tension:The tail pulley, located at the loading end, helps maintain the desired tension on the conveyor belt. Proper tension is critical to avoid slippage and ensure smooth operation of the belt. The position of the tail conveyor roller pulley can be adjusted to control the belt’s tension throughout its continuous loop.
Supporting Belt Return:After the conveyor belt discharges the conveyed materials, it must return to the loading end. The tail pulley also supports this return segment, ensuring that the belt travels smoothly and stays aligned.
Enhancing System Stability:Both the head and tail pulleys contribute to the overall stability of the conveyor system. By correctly aligning and driving the belt, these conveyor roller pulleys prevent the belt from wandering and reduce the risk of it coming off the track.
Key Features and Designs
Material Construction:Typically, these pulleys are made from heavy-duty steel for durability. Stainless steel or aluminum might also be used in specific applications, particularly where weight or corrosion resistance is a concern.
Lagging Types:Pulleys can have different types of lagging, such as rubber, ceramic, or diamond-patterned, which enhance grip and reduce wear under different operating conditions.
Shaft Mounting:Head and tail pulleys can be mounted using fixed bearings or can employ a more flexible suspension system to accommodate shifts in the load and prevent misalignment.
Face Widths:The face width of these pulleys is designed according to the width of the conveyor belts they will be driving, ensuring there is no overhang that could lead to belt damage.
Common Issues and Replacement Needs
Wear and Tear:Over time, the conveyor roller pulley surfaces can wear down, particularly the lagging, which can lead to decreased friction and increased slippage.
Misalignment:Improper installation or heavy loads can lead to pulley misalignment, causing uneven belt wear, increased energy consumption, and potential system failures.
Bearing Failure:Bearings within the pulley assembly can fail due to overloading or lack of maintenance, leading to a complete halt in operations until repairs are made.
Structural Integrity:Continuous operation under harsh conditions can compromise the structural integrity of the pulleys, necessitating their replacement to prevent catastrophic failures.
Regular inspections and maintenance are essential to identify and rectify these issues promptly. Implementing a scheduled maintenance program can help extend the life of conveyor roller pulleys and prevent the need for frequent replacements, thereby ensuring the continuous and efficient operation of the conveyor system. This proactive approach not only saves time and costs but also enhances safety by reducing the risk of unexpected breakdowns.
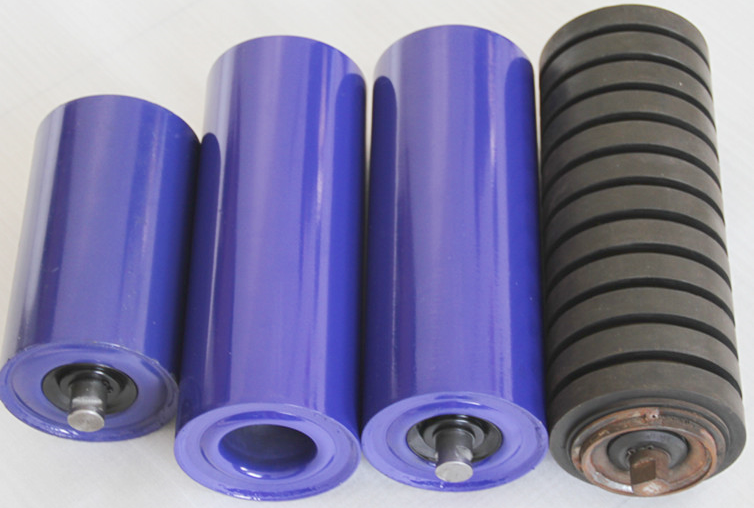
Tail Pulley in Conveyor Belts
The tail pulley, a key type of conveyor roller pulley, plays an indispensable role in conveyor belt systems. It is typically located at the feeding end of the conveyor system and serves multiple critical functions, primarily revolving around maintaining tension and contributing to the belt’s tracking and alignment. Understanding the operational dynamics and maintenance requirements of the tail pulley can significantly enhance the efficiency and longevity of a conveyor system.
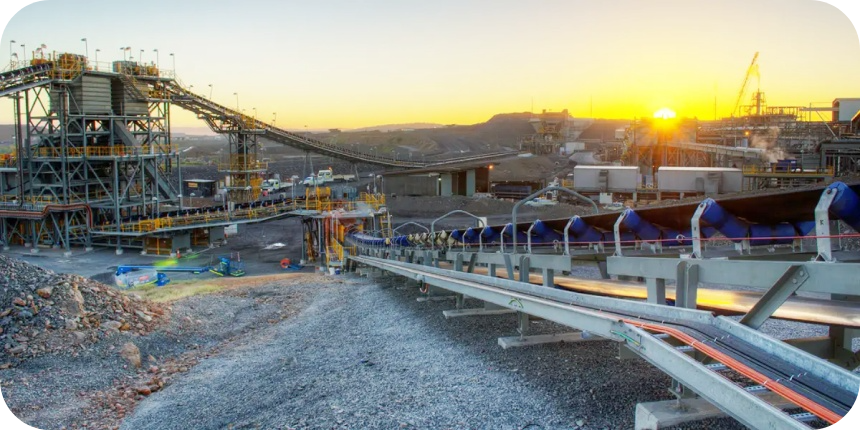
Working and Significance of Tail Pulleys
Maintaining Belt Tension:The tail conveyor roller pulley is pivotal in maintaining the proper tension of the conveyor belt. Adequate tension is crucial as it prevents the belt from slipping on the drive pulley and ensures smooth operation. The ability to adjust the tail pulley’s position allows for easy tension modifications as the belt stretches or wears after prolonged use.
Contributing to Belt Tracking:Apart from tension adjustment, the tail conveyor roller pulley also plays a significant role in belt tracking, which is the adjustment of the belt’s alignment to ensure it runs straight along the conveyor’s structure. Misalignment can lead to uneven belt wear, increased energy consumption, and potential operational hazards.
Facilitating Belt Cleaning:As the return side of the belt comes into contact with the tail conveyor roller pulley, it is an optimal location for installing belt cleaners. These cleaners help remove residual material from the belt’s surface, which is crucial for preventing material buildup that can disrupt the conveyor’s functionality and lead to premature belt wear.
Supporting the Conveyor Belt’s Return Path:The tail pulley supports the return path for the conveyor belt, which is essential after the material has been discharged. This support helps prevent sagging and misalignment of the return path, which could otherwise lead to operational inefficiencies.
Common Maintenance Issues and Solutions
Pulley Misalignment:Misalignment of the tail conveyor roller pulley can cause serious issues such as uneven belt wear, belt wandering, and reduced operational efficiency. Regular inspections should be performed to ensure the pulley is properly aligned. Adjustments can often be made by realigning the pulley frame and making sure that all components are level and square.
Wear and Tear on Pulley Surface:The surface of the tail conveyor roller pulley can wear over time, especially in environments with abrasive materials. Applying appropriate lagging, such as rubber or ceramic, can extend the pulley’s lifespan by providing a protective layer that reduces wear and increases friction.
Bearing Failures:Bearings in the tail conveyor roller pulley are susceptible to failure due to overloading, improper installation, or lack of lubrication. Regular maintenance checks should include inspecting, cleaning, and lubricating bearings. Replacing bearings at the first sign of wear can prevent more serious issues.
Material Buildup:Accumulation of transported material on or around the tail conveyor roller pulley can lead to belt misalignment and increased wear. Installing scrapers or cleaners on the tail pulley and performing regular clean-up can help mitigate material buildup.
By addressing these maintenance issues promptly and adhering to a routine inspection schedule, the reliability and efficiency of tail conveyor roller pulleys in conveyor belts can be substantially improved. This proactive approach not only minimizes downtime but also extends the overall lifespan of the conveyor belt system. This section underscores the critical importance of tail pulleys within conveyor belt systems and highlights practical strategies for maintaining them effectively.
Conveyor Head Pulley
The conveyor head pulley, located at the discharge end of the conveyor system, is an essential conveyor roller pulley that drives the conveyor belt and importantly, is involved in the discharge of the materials being conveyed. This pulley is not only crucial for the mechanical function of moving the belt but also affects the operational efficiency and the belt’s lifespan. Its roles and common issues are detailed below to help maintain the health and efficiency of the entire conveyor system.
Function of the Conveyor Head Pulley
- Driving the Conveyor Belt:The primary function of the head conveyor roller pulley is to drive the conveyor belt. This involves transferring power from the motor to the conveyor belt to move the belt and the material loaded on it. Effective power transfer depends on the pulley’s grip, which can be enhanced with different types of lagging (rubber, ceramic, etc.) applied to the surface of the pulley.
- Material Discharge:As the conveyor roller pulley positioned at the discharge end, the head pulley also plays a pivotal role in the offloading process. It helps in the smooth transition of materials from the belt into the discharge chute or bin, which is crucial for maintaining a consistent flow rate and preventing bottlenecks.
- Belt Tracking and Alignment:Proper alignment of the head conveyor roller pulley is essential to maintain the belt’s trajectory. Misaligned pulleys can cause the belt to run off-track and suffer from edges wearing, which could potentially lead to belt failure.
- Maintaining Belt Tension:The head pulley is integral in maintaining the right tension on the conveyor belt. Correct tension is crucial to avoid slippage between the belt and the pulley, ensuring efficient operation and preventing wear and tear on the belt.
Common Problems and Solutions
- Pulley Wear:Frequent contact with the conveyor belt can wear down the surface of the head conveyor roller pulley. Worn pulleys may not provide effective grip, leading to belt slippage. Solution: Applying appropriate lagging or replacing the pulley when wear exceeds acceptable limits can prevent slippage and extend the pulley’s life.
- Pulley Misalignment:Misalignment of the head pulley can cause the conveyor belt to run off-center, leading to rapid edge wear and potential system failures. Solution: Regularly check and adjust the alignment of the head conveyor roller pulley. Laser alignment tools can be used to ensure precise alignment.
- Bearing Failure:Bearings in the head conveyor roller pulley can fail due to high loads or insufficient lubrication, causing the pulley to operate inefficiently and risk a catastrophic failure. Solution: Perform regular inspections and maintenance on bearings; replace them using high-quality bearings and ensure they are properly lubricated.
- Lagging Peeling Off:The lagging on the head pulley can peel off due to poor adhesive application or extreme operational conditions. Solution: Regular inspection of pulley lagging should be conducted to check for signs of peeling or wear. Re-lagging the pulley can restore its efficiency and grip on the conveyor belt.
By understanding these critical functions and common issues associated with the head conveyor roller pulley, maintenance teams can take proactive steps to ensure the reliability and productivity of conveyor systems. Regular inspections and timely maintenance not only reduce downtime but also extend the life of the conveyor belt and the system as a whole. This detailed examination not only underscores the importance of the head pulley in conveyor belt operations but also provides practical solutions to common problems, ensuring continuous and efficient operation.
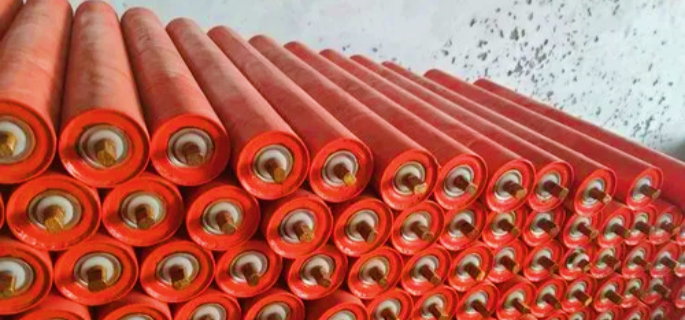
Different Types of Conveyor Belt Pulleys
Conveyor systems utilize a variety of conveyor roller pulley types, each designed to fulfill specific functions within the system. Understanding the differences among these pulleys—namely the drive pulley, idler pulley, snub pulley, and take-up pulley—is crucial for anyone involved in the design, maintenance, or operation of a conveyor system. Below, we provide detailed descriptions and comparative data to elucidate how these pulleys operate and their roles in ensuring efficient conveyor system performance.
Types of Conveyor Belt Pulleys
Each conveyor roller pulley plays a pivotal role in the conveyor’s functionality:
Functionality of Different Conveyor Roller Pulleys
These pulleys are integral to a conveyor belt’s operation and efficiency. The drive pulley provides the necessary power to move the belt. In contrast, the idler and snub pulleys modify the belt’s path and tension to optimize performance and prolong the belt’s lifespan. Meanwhile, the take-up pulley allows for minor adjustments in belt tension caused by thermal changes, load variations, or other operational factors. Understanding these roles highlights the importance of regular maintenance checks and adjustments to ensure that each conveyor roller pulley is performing its function correctly. This proactive maintenance helps in avoiding costly downtime and extends the overall lifespan of the conveyor system.
Size of Conveyor Roller Pulley
The size of conveyor roller pulleys can vary significantly based on the specific requirements of the conveyor system. Below is a table summarizing the common sizes and factors influencing the size of conveyor roller pulleys:
Key Considerations for Sizing Pulleys
- Belt Width: The pulley length should accommodate the full width of the conveyor belt.
- Load and Tension: Larger diameters are preferred for handling higher loads and tensions to reduce stress on the belt and pulley.
- Speed: Higher belt speeds may require larger pulleys to reduce the wear on the belt.
- Space Constraints: The installation space available can limit the size of the pulleys.
- Material and Environment: Special considerations for abrasive, wet, or corrosive environments may influence pulley size and construction materials.
If you need specific sizes or recommendations for a particular application, please provide more details about your conveyor system and operational requirements.
Selecting The Right Conveyor Roller Pulley
Selecting the right conveyor roller pulley involves considering several factors to ensure optimal performance and longevity of the conveyor system. Here’s a detailed guide to help you make the right choice:
Key Factors to Consider
- Load Requirements:
- Weight of Material: Consider the weight of the material being conveyed.
- Belt Load: The pulley should support the maximum load the belt will carry.
- Belt Specifications:
- Belt Width: The pulley width should match or slightly exceed the belt width.
- Belt Speed: Ensure the pulley can handle the operational speed of the belt.
- Pulley Position:
- Drive Pulley: Requires higher friction and torque.
- Tail Pulley: Focus on supporting the belt tension.
- Snub, Take-Up, Bend Pulleys: Designed for specific functions like increasing wrap angle or maintaining tension.
- Environmental Conditions:
- Temperature: Consider pulleys with materials that can withstand the operational temperature range.
- Corrosion Resistance: In corrosive environments, use pulleys made of stainless steel or with appropriate coatings.
- Material Handling:
- Type of Material: Different materials (abrasive, sticky, wet) may require pulleys with specific designs (e.g., wing pulleys for self-cleaning).
- Lagging Requirements:
- Rubber Lagging: Provides better grip and reduces belt slippage.
- Ceramic Lagging: Offers high wear resistance for abrasive materials.
- Maintenance and Accessibility:
- Ease of Maintenance: Consider the ease of access for regular inspection and maintenance.
- Spare Parts Availability: Ensure spare parts are readily available to minimize downtime.
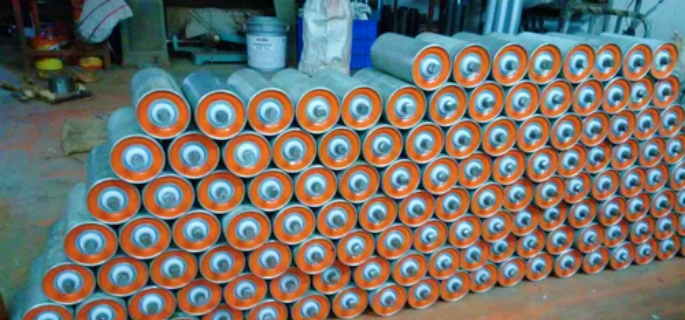
Selection Process
- Define Application Requirements:
- List all operational and environmental factors that the pulley must handle.
- Choose Pulley Type:
- Select the appropriate type (drive, tail, snub, take-up, bend) based on its function within the conveyor system.
- Determine Size and Material:
- Select the diameter, length, and material based on the load, belt width, speed, and environmental conditions.
- Consider Additional Features:
- Decide if additional features like lagging or special coatings are necessary for your application.
Example Table for Selection
Practical Steps
- Consult Manufacturer’s Guidelines: Refer to the pulley manufacturer’s recommendations and specifications.
- Perform Calculations: Calculate the required pulley size and strength based on load, speed, and tension.
- Get Expert Advice: Consult with experts or suppliers to ensure the selected pulley meets all operational requirements.
Pulley Roller Wheels: Integral Components of Conveyor Roller Pulley Systems
Pulley roller wheels are crucial elements within conveyor roller pulley systems, serving to reduce friction and facilitate the smooth and efficient movement of conveyor belts. These wheels are particularly pivotal in systems where changes in direction and speed are frequent. Understanding the variety and functionality of different pulley roller wheels can significantly enhance the performance and reliability of a conveyor system.
Introduction to Pulley Roller Wheels
Pulley roller wheels, or simply roller wheels, are installed in various parts of a conveyor system and are designed to support and guide the conveyor belt efficiently. These wheels vary widely in size, material, and design, each tailored to specific needs and operational demands.
- Load Support: Roller wheels provide critical support for conveyor belts loaded with materials. By evenly distributing the weight, these wheels help maintain the belt’s shape and alignment, thereby preventing sagging and minimizing stress on the belt.
- Directional Guidance: In curved sections of a conveyor, roller wheels guide the belt as it transitions through various angles. This guidance is crucial to prevent the belt from slipping off the tracks and to reduce the wear on the edges of the belt.
- Friction Reduction: By minimizing the contact area with the conveyor belt, roller wheels reduce friction, which in turn lowers the power consumption of the system and extends the life of the belt.
- Speed Variation: Certain roller wheel designs can influence the speed of the conveyor belt at different sections of the track. This is particularly useful in systems where different operations on the belt require varying speeds.
Types and Functions of Roller Wheels in Pulley Systems
The table below provides a comparative look at different types of roller wheels used in various conveyor roller pulley systems, highlighting their unique features and applications:
Each type of wheel is suited to specific tasks within the conveyor system, influenced by factors such as load weight, conveyor speed, environmental conditions, and required friction levels. Solid steel wheels are preferred in industrial environments where heavy loads and high durability are essential. In contrast, rubber-coated and polyurethane wheels are chosen for their additional properties like noise reduction and non-marking characteristics, which are crucial in consumer-facing and sensitive environments.
The selection of the appropriate roller wheel type is critical to the efficiency and longevity of conveyor roller pulley systems. Operators must consider the specific needs of their conveyor operations, including the materials handled, the operational environment, and the desired longevity of the conveyor system, to choose the most appropriate roller wheels. Proper maintenance and regular inspections are also vital to ensure that these roller wheels perform optimally throughout their service life. By understanding these components and their critical roles, facilities can make informed decisions that enhance operational efficiency and safety.

Conveyor Roller Pulley Systems
The conveyor roller pulley is a fundamental component in the mechanics of conveyor systems, functioning as a critical support and driving unit across various industrial applications. These pulleys guide, drive, and provide tension to the conveyor belt, ensuring efficient and continuous operations. This section provides comprehensive insights into the structure, operation, and maintenance of conveyor roller pulleys, and highlights their importance across different industrial sectors.
Structure and Operation of Conveyor Roller Pulleys
Conveyor Roller Pulley Structure:
A conveyor roller pulley typically consists of a cylindrical body, usually made from materials like steel or heavy-duty metals that offer durability and can withstand substantial wear and tear. The key components of a conveyor roller pulley include:
- Shell: The outer surface of the pulley, which comes in direct contact with the belt.
- Shaft: A central rod that runs through the shell and attaches to the bearings and the conveyor frame.
- Bearings: Positioned at both ends of the pulley to support the shaft, allowing smooth rotation.
- Hub: Connects the shell to the shaft.
- Lagging: A rubber, ceramic, or composite coating applied to the surface of the shell to increase friction and protect against wear.
Operational Mechanics:
The operation of a conveyor roller pulley involves several mechanical processes:
- Transmission of Power: The drive pulley is connected to a motor, which transmits mechanical power to the belt, propelling the conveyor.
- Tension Regulation: Take-up pulleys adjust the tension on the belt, ensuring optimal performance and preventing slippage or excessive wear.
- Belt Alignment: Idler and snub pulleys maintain the belt’s alignment and manage its course to prevent lateral movements that could lead to operational issues.
Maintenance of Conveyor Roller Pulleys
Maintaining conveyor roller pulleys is critical to preventing downtime and ensuring efficient operations. Key maintenance practices include:
- Regular Inspection: Scheduled checks for wear and tear, especially on the shell and lagging.
- Proper Lubrication: Bearings should be regularly lubricated to reduce friction and prevent overheating.
- Alignment Checks: Regularly ensuring that all pulleys are correctly aligned to avoid uneven belt wear.
- Lagging Replacement: Periodically replacing worn lagging to maintain friction levels and protect the pulley’s shell.
Significant Use of Conveyor Pulley in Various Industrial Sectors
Mining and Quarrying:
In the mining industry, conveyor roller pulleys are used extensively to transport raw materials such as coal and ores from the mine to processing facilities. The durability and robustness of these pulleys are crucial in handling abrasive materials and adverse operating conditions.
Manufacturing:
Manufacturing facilities use conveyor roller pulleys to move products through production lines. In automobile manufacturing, for example, pulleys are used at various stages of assembly to move parts efficiently across the plant.
Food Processing:
In the food processing industry, stainless steel or polymer-coated conveyor roller pulleys are preferred for their resistance to corrosion and ease of cleaning, which are essential for maintaining hygiene standards.
Packaging:
Conveyor systems equipped with specialized conveyor roller pulleys are integral to the packaging industry, where they are used to transport, sort, and package various goods rapidly and with precision.
Logistics and Distribution:
Warehousing and distribution sectors utilize conveyor roller pulleys to sort, distribute, and load goods for shipping. The efficiency of pulleys ensures that products are moved swiftly through the distribution process, enhancing overall throughput and reducing labor costs.
The extensive use of conveyor roller pulleys across these sectors underscores their versatility and essential role in modern industrial operations. Proper understanding, regular maintenance, and timely upgrades of these pulleys can lead to significant improvements in conveyor system performance, highlighting the pulley’s pivotal role in industrial productivity and efficiency.
Roller Lagging Tape: Enhancing the Performance of Conveyor Roller Pulley Systems
Roller lagging tape is a crucial component designed to enhance the functionality and longevity of conveyor roller pulleys. This specialized tape is applied to the surface of pulleys to improve traction, protect against wear, and extend the overall life of both the pulley and the conveyor belt. Understanding its role and the correct installation procedures can significantly impact the efficiency and durability of conveyor systems.
Roller Lagging Tape
Roller lagging tape is typically made from materials such as rubber, polyurethane, or ceramics that provide increased friction and offer protective qualities. The primary functions of lagging tape in a conveyor roller pulley system include:
- Enhancing Traction: The increased friction provided by lagging helps to reduce slippage between the conveyor belt and the pulley. This is especially important in driving pulleys where powerful forces are at play.
- Minimizing Wear: Lagging protects the pulley’s surface from the abrasive action of the belt, which can wear down metal surfaces over time, leading to inefficiencies and the need for replacement.
- Preventing Belt Slippage: By improving grip, lagging ensures that the belt runs smoothly, which is vital for maintaining the timing and placement of materials being transported.
- Dissipating Heat: During operation, conveyor roller pulleys can generate significant heat, which lagging helps to dissipate, protecting both the belt and the pulley from thermal damage.
How to Properly Install Roller Lagging Tape for Optimum Performance
Step 1: Surface Preparation
- Clean the Pulley: Begin by thoroughly cleaning the conveyor roller pulley surface. Remove all dust, dirt, and grease, which can prevent the lagging tape from adhering correctly. Use a degreaser or solvent if necessary.
- Surface Roughening: If the pulley surface is too smooth, roughen it slightly with a wire brush or sandpaper. This helps in creating a better bond with the adhesive.
Step 2: Measurement and Cutting
- Measure the Pulley: Measure the circumference of the pulley to determine how much lagging tape is required. It is essential to get accurate measurements to cover the entire surface without overlap.
- Cut the Tape: Cut the tape to the length based on your measurements. It’s advisable to cut a little extra to ensure complete coverage without stretching the tape too much, which could affect its performance.
Step 3: Application of the Tape
- Apply Adhesive: If the lagging tape does not come with a pre-applied adhesive layer, apply a uniform layer of adhesive to the pulley surface. Use an adhesive recommended by the tape manufacturer for best results.
- Install the Tape: Carefully position the tape at the edge of the pulley and slowly roll the pulley to wrap the tape around it. Ensure the tape is applied tightly and evenly without any air bubbles or creases.
Step 4: Securing the Tape
- Secure the Edges: Once the tape is in place, secure the edges with additional adhesive to prevent peeling. Some tapes might require a sealing product or a specific finish to ensure the edges are well-protected against lifting.
- Curing Time: Allow the adhesive to cure according to the manufacturer’s instructions. This might range from a few hours to a day, depending on the adhesive type.
Step 5: Inspection and Testing
- Inspect the Installation: After the adhesive has cured, inspect the lagging for any signs of lifting or gaps. Ensure that the tape is securely bonded to the pulley surface.
- Test Run: Perform a test run of the conveyor to check the effectiveness of the lagging. Listen for any unusual noises and observe the traction and alignment of the belt.
Proper installation of roller lagging tape on a conveyor roller pulley not only enhances the grip and reduces wear but also contributes to the optimal performance and extended lifespan of the conveyor system. By following these detailed steps, operators can ensure that their conveyor systems run more efficiently, with reduced maintenance costs and downtime. This careful approach to installing roller lagging tape underscores its significance in maintaining the health and efficiency of conveyor belts and pulley systems.
Wing Pulley: Specialized Features of Conveyor Roller Pulley Systems
A wing pulley is a specialized type of conveyor roller pulley used primarily to manage the cleanliness of a conveyor belt’s contact surface. It features unique design elements that distinguish it from other types of pulleys used in conveyor systems. Understanding the design, functionality, and appropriate applications of wing pulleys can significantly optimize the performance of a conveyor system, particularly in challenging environments.
Detailed Explanation of a Wing Pulley
Design and Construction:
A wing pulley incorporates a series of angular, diagonal fins (or wings) that extend outward from a central hub. These fins are usually spaced evenly around the circumference of the pulley. The key characteristics of a wing conveyor roller pulley include:
- Materials: Like most pulleys, wing pulleys are constructed from durable materials such as steel. However, they can also incorporate other materials depending on the specific application needs, including stainless steel for corrosion resistance.
- Wing Design: The wings are designed to allow material that might stick to the belt, such as mud or granular products, to fall through the gaps between them, thereby preventing build-up on the pulley itself.
- Self-Cleaning Mechanism: The principal advantage of a wing conveyor roller pulley is its self-cleaning feature. As the pulley rotates, materials that would otherwise accumulate on the pulley face are expelled out and away, reducing the risk of material build-up that can cause belt misalignment or damage.
Features and Benefits
- Reduced Belt Wear: By preventing material build-up, wing pulleys extend the lifespan of the conveyor belt.
- Improved Performance: The self-cleaning mechanism ensures that the belt runs smoothly, enhancing overall conveyor system performance.
- Versatility: Wing pulleys can be used in a variety of environments but are particularly beneficial in applications where material build-up is a concern, such as in the handling of loose materials like sand or coal.
When and Why to Use a Wing Pulley
Appropriate Applications:
- Handling Sticky or Wet Materials: Wing pulleys are ideal for use in environments where the conveyed materials are wet or sticky and prone to adhering to the belt surface.
- High Debris Applications: They are also advantageous in settings where debris can build up quickly, such as in wood processing or aggregate industries.
Advantages of Using a Wing Pulley:
- Maintenance Reduction: The self-cleaning property of wing pulleys decreases the need for manual cleaning and maintenance.
- Increased Safety: By maintaining a clean belt, wing pulleys reduce the risk of slip-and-fall accidents due to debris on the walking surfaces around the conveyor.
- Enhanced Efficiency: Clean belts and pulleys improve the efficiency of the conveyor system, as dirty belts can lead to slippage and increased energy consumption.
In conclusion, the wing conveyor roller pulley is a critical component designed for challenging environments where preventing material build-up is crucial to maintaining system efficiency. Its unique winged design not only facilitates cleanliness and extends the belt’s lifespan but also enhances the safety and operational efficiency of the entire conveyor system. Industries that process materials which are prone to sticking or accumulating on surfaces should consider integrating wing pulleys into their conveyor systems to leverage these benefits. This specialized conveyor roller pulley is a robust solution tailored to meet the demands of high-maintenance conveyor system applications.
Need Selecting Conveyor Roller Recommendations? Contact Us Through This Form.
FAQs About Conveyor Roller Pulley
Pulleys and rollers are both essential components of conveyor systems, but they serve different purposes and are constructed differently. A pulley is typically a wheel on an axle or shaft that is designed to support the movement and change of direction of a conveyor belt or other flexible mediums. Pulleys are used to drive the conveyor belt, creating tension and providing the necessary power to move the belt and the materials loaded on it. They are usually made from durable materials such as metal or heavy-duty plastics and might include features such as lagging, which enhances their grip on the belt.
Rollers, on the other hand, are used to support the conveyor belt and stabilize the conveyed materials. Rollers are cylindrical and rotate on their axes to allow the conveyor belt to move smoothly. They reduce the friction and wear on the belt, extending its lifespan and improving the efficiency of the conveyor system. Rollers can be made from various materials, including metal, plastic, or rubber, depending on the application’s needs.
A pulley on a conveyor, also known as a conveyor roller pulley, is a critical component that drives the conveyor belt or affects its tension. There are several types of pulleys used on conveyors, each serving a specific function:
Drive Pulley: This pulley is powered and provides the necessary force to move the conveyor belt. It is usually covered with rubber lagging to increase friction and improve belt traction.
Tail Pulley: Located at the tail end of the conveyor, this pulley is used to provide tension to the belt and guide it as it begins its return cycle.
Idler Pulley: These are not powered and are used to support the belt as it travels. Their main function is to maintain the structural integrity and depth of the conveyor belt.
Snub Pulley: A snub pulley is used to increase the angle of contact between the conveyor belt and the drive pulley, enhancing the friction between the belt and the pulley.
Take-Up Pulley: This type helps adjust the belt’s tension, ensuring optimal performance of the conveyor.
Each type of conveyor roller pulley plays a pivotal role in the functionality and efficiency of a conveyor system.
The rollers on a conveyor, often simply called conveyor rollers, are the cylindrical components that the conveyor belt rides on. The primary purpose of conveyor rollers is to support the belt and the material being transported along the length of the conveyor. Depending on their role, conveyor rollers can be classified into several types:
Carrying rollers: These are the most common types of rollers and are used to carry the belt and the materials it transports.
Return rollers: These rollers support the return side of the belt as it travels back to the beginning after offloading the material.
Impact rollers: Positioned at points where material falls onto the belt, impact rollers are designed to absorb the shock and reduce the load and wear on other rollers and the belt.
Guide rollers: These are used to ensure that the conveyor belt travels in a consistent line and does not wander off the path.
Rollers must be precisely manufactured and installed to ensure they effectively support the belt and contribute to the smooth functioning of the conveyor system.
A roller conveyor is a type of conveyor system where the principal mechanism of movement is a series of rollers that are mounted on axles and spaced strategically. Roller conveyors are used primarily for handling solid objects like boxes, trays, pallets, etc. They are especially advantageous in situations where the items being conveyed are solid and have a sufficient base to rest on the rollers. These conveyors can be powered or gravity-operated:
Powered Roller Conveyors: These conveyors use geared motors to turn the rollers and move the conveyor belt. They are suitable for moving heavier loads and can be controlled more precisely.
Gravity Roller Conveyors: These utilize the force of gravity to move items. They are inclined slightly downwards to facilitate the movement of items from one point to another without motor power.
Roller conveyors are versatile, efficient, and typically require less maintenance than belt conveyors. They are also modular, making them easy to install and reconfigure according to changing needs.
The pulley in a conveyor belt system is commonly referred to as a conveyor pulley. There are several types of conveyor pulleys, including the drive pulley, tail pulley, snub pulley, bend pulley, and take-up pulley. Each type serves a specific function within the conveyor system. The drive pulley, usually located at the discharge end of the conveyor, is powered by a motor and is responsible for driving the belt. The tail pulley is found at the opposite end and helps maintain tension on the belt. Snub pulleys are used to increase the belt wrap angle on the drive pulley, enhancing traction, while bend pulleys change the direction of the belt. Take-up pulleys maintain the proper belt tension.
The rollers on a conveyor are called conveyor rollers or idlers. These cylindrical components support the conveyor belt and the materials being transported, ensuring smooth movement along the conveyor system. Conveyor rollers come in various types, including carrying rollers, return rollers, impact rollers, and training rollers. Carrying rollers support the loaded belt, while return rollers support the empty belt on its return journey. Impact rollers, positioned at loading points, are designed to absorb the impact of falling materials, protecting the belt from damage. Training rollers help to keep the belt aligned and centered on the conveyor frame, preventing mis-tracking and potential damage to the belt and conveyor structure.
A conveyor tail pulley is located at the end of a conveyor belt system, opposite the drive pulley. Its primary function is to provide a point for the conveyor belt to change direction as it wraps around the pulley and returns to the drive pulley. The tail pulley also helps to maintain proper tension in the conveyor belt, ensuring smooth and efficient operation. Tail pulleys are often adjustable, allowing for tension adjustments to accommodate belt stretch and wear over time. They can also be equipped with features such as lagging to improve traction and reduce belt slippage, as well as to extend the lifespan of the belt and pulley.
A bend pulley on a conveyor is used to change the direction of the conveyor belt. Bend pulleys are typically installed where the belt needs to be redirected, ensuring smooth transitions and maintaining proper belt tension. These pulleys are essential in complex conveyor systems with multiple turns and changes in direction. Bend pulleys help to guide the belt, reducing stress and preventing misalignment. They are constructed to withstand the operational stresses of belt movement and are often equipped with lagging to increase friction between the pulley and the belt, enhancing grip and reducing wear.
No, a conveyor belt is not a pulley. A conveyor belt is a continuous loop of material, such as rubber, fabric, or metal, that is used to transport materials from one point to another within a conveyor system. The belt is supported by and moves over a series of rollers and pulleys. Pulleys, on the other hand, are mechanical devices that drive or change the direction of the conveyor belt. They are critical components in the conveyor system, providing the necessary force to move the belt and the load it carries. Pulleys include drive pulleys, tail pulleys, bend pulleys, snub pulleys, and take-up pulleys.
Conveyor rollers work by providing a rotating surface that supports and moves the conveyor belt and the materials placed on it. These cylindrical components are mounted on a frame and typically consist of a tube, shaft, and bearings. As the rollers rotate, driven either by the motion of the conveyor belt or by a mechanical drive system, they facilitate the smooth movement of the belt and the materials. Carrying rollers support the loaded belt, while return rollers support the belt on its return journey. Impact rollers, placed at loading points, absorb the impact of materials, protecting the belt. Training rollers help keep the belt aligned, preventing mis-tracking and ensuring efficient operation.
Last Updated on July 30, 2024 by Jordan Smith
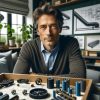
Jordan Smith, a seasoned professional with over 20 years of experience in the conveyor system industry. Jordan’s expertise lies in providing comprehensive solutions for conveyor rollers, belts, and accessories, catering to a wide range of industrial needs. From initial design and configuration to installation and meticulous troubleshooting, Jordan is adept at handling all aspects of conveyor system management. Whether you’re looking to upgrade your production line with efficient conveyor belts, require custom conveyor rollers for specific operations, or need expert advice on selecting the right conveyor accessories for your facility, Jordan is your reliable consultant. For any inquiries or assistance with conveyor system optimization, Jordan is available to share his wealth of knowledge and experience. Feel free to reach out at any time for professional guidance on all matters related to conveyor rollers, belts, and accessories.