Conveyor Roller Rubber Sleeve: Benefits and Applications
In the fast-paced world of industrial operations, conveyor systems stand as the backbone of numerous sectors, including manufacturing, logistics, and packaging. These systems are crucial for the seamless and efficient movement of goods across different stages of production and distribution. However, the performance of these conveyor systems heavily relies on the durability and efficiency of their components, particularly the rollers. Herein lies the significance of the conveyor roller rubber sleeve, a simple yet transformative addition to the conveyor roller. By outfitting rollers with these rubber sleeves, industries can significantly enhance the grip, durability, and overall performance of their conveyor systems. This introduction not only highlights the critical role of conveyor systems across various industries but also sets the stage for a deeper exploration into how roller sleeves, especially those made of rubber, are pivotal in optimizing conveyor roller function.
What are Conveyor Roller Rubber Sleeves
In the world of material handling and logistics, conveyor systems play a pivotal role in moving products efficiently from one point to another. An integral part of these systems is the conveyor roller, and more specifically, the conveyor roller rubber sleeve, which significantly enhances the functionality and longevity of conveyor rollers. This detailed exploration aims to demystify conveyor roller rubber sleeves, elucidating their definition, purposes, and comparing rubber sleeves with their polyurethane counterparts.
Defining Conveyor Roller Rubber Sleeves and Their Purposes
Conveyor roller rubber sleeves are cylindrical covers made from rubber material that are fitted over the surface of conveyor rollers. These sleeves are designed to offer protection, grip, and noise reduction for conveyor systems. They play a crucial role in various industries, including manufacturing, packaging, and distribution. Here are seven primary purposes of conveyor roller rubber sleeves:
- Increased Traction: The rubber material provides excellent grip, reducing slippage between the conveyor belt and the roller, which is crucial for the smooth transportation of goods.
- Wear Protection: Conveyor roller rubber sleeves protect the rollers from direct contact with materials, thus reducing wear and extending the life of the rollers.
- Noise Reduction: They act as a cushion and dampen the operational noise, creating a quieter working environment.
- Shock Absorption: The elasticity of rubber helps in absorbing shocks and vibrations, which is particularly beneficial for fragile goods.
- Corrosion Resistance: Rubber sleeves provide a protective layer against corrosive materials or environments, preventing rust and corrosion on the rollers.
- Product Protection: The soft rubber surface minimizes damages to the goods being transported, reducing losses due to breakage or scratches.
- Customizability: These sleeves can be customized in terms of hardness, surface pattern, and size, making them versatile for different applications and products.
Rubber vs. Polyurethane Conveyor Roller Sleeves: A Comparison
When it comes to choosing the material for conveyor roller sleeves, rubber and polyurethane are the two most common options. Each material offers distinct benefits:
- Rubber Sleeves: Conveyor roller rubber sleeves are renowned for their durability and elasticity. They provide excellent traction and shock absorption, making them ideal for heavy-duty applications. Rubber’s resistance to wear and tear extends the lifespan of conveyor rollers, making it a cost-effective solution for many industries. Additionally, rubber’s noise-dampening properties contribute to a more pleasant working environment.
- Polyurethane Sleeves: Polyurethane sleeves, on the other hand, offer superior abrasion resistance and are less prone to marking products. They can handle a wider range of temperatures and resist chemicals and oils better than rubber. Polyurethane sleeves are also highly customizable in terms of hardness, allowing for precise control over the grip and flexibility of the conveyor rollers.
The choice between conveyor roller rubber sleeves and polyurethane sleeves depends on the specific requirements of the application, including the nature of the materials being conveyed, environmental conditions, and desired longevity. Rubber sleeves excel in providing grip, durability, and noise reduction, making them suitable for a wide range of industrial applications. Understanding the unique advantages of each material helps in optimizing conveyor systems for efficiency, safety, and productivity.
Key Benefits of Using Conveyor Roller Rubber Sleeve and Polyurethane Sleeves
The integral components of modern conveyor systems—specifically, the conveyor roller rubber sleeve and polyurethane sleeves—serve a pivotal role in enhancing the functionality and efficiency of these systems. These sleeves not only extend the operational life of conveyor rollers but also bring forth a multitude of benefits, from improved material handling to noise reduction. Below, we delve into the key advantages provided by these innovative solutions.
Durability and Protection
One of the foremost benefits of employing a conveyor roller rubber sleeve or a polyurethane sleeve is the significant increase in durability and protection for conveyor rollers. These sleeves act as a protective barrier, safeguarding the rollers from the harsh impacts of abrasion, chemicals, oil, grease, and moisture. The robust nature of rubber and polyurethane materials ensures that the underlying rollers are shielded against the typical wear and tear experienced in rigorous industrial environments. This layer of protection is vital for maintaining the integrity and longevity of the conveyor system, leading to reduced maintenance costs and longer intervals between roller replacements.
Enhanced Grip and Reduced Slippage
Another critical advantage is the enhanced grip and reduced slippage afforded by these sleeves. Conveyor roller rubber sleeves, in particular, are designed to maximize contact with the conveyed materials, providing an exceptional grip that significantly lowers the risk of slippage. This is especially beneficial in heavy-duty applications where the secure transportation of materials is paramount. The improved traction ensures that materials are moved smoothly and efficiently along the conveyor, enhancing overall productivity and reducing the likelihood of bottlenecks or material spillage.
Noise Reduction and Cushioning
Conveyor roller sleeves contribute significantly to creating a more conducive working environment by reducing operational noise. The rubber and polyurethane materials absorb vibrations and dampen the sound generated during the conveyor’s operation, leading to a quieter workplace. This noise reduction is crucial in maintaining a comfortable environment for workers and complying with occupational health and safety standards. Additionally, the cushioning effect provided by these sleeves protects delicate materials from damage during transportation, minimizing the risk of breakages and ensuring the integrity of goods.
Application Versatility
Lastly, the versatility of conveyor roller rubber and polyurethane sleeves cannot be overstated. These sleeves are adept at meeting the requirements of a wide range of applications, from heavy industrial use to delicate food-grade operations. The ability to customize the hardness, texture, and material composition of the sleeves means they can be tailored to suit specific environmental conditions, including those requiring high levels of cleanliness and resistance to contamination. This adaptability makes conveyor roller sleeves an invaluable component in diverse sectors, enhancing the efficiency and reliability of conveyor systems across the board.
The incorporation of conveyor roller rubber sleeves and polyurethane sleeves into conveyor systems presents a host of benefits. From extending the life of conveyor rollers through enhanced durability and protection to improving the handling of materials with increased grip and reduced slippage, these sleeves are instrumental in optimizing conveyor performance. Additionally, their contribution to noise reduction and the versatility they offer in various applications underscore their critical role in the modern material handling landscape.
Types of Conveyor Roller Rubber Sleeve
The selection of the appropriate conveyor roller sleeve is critical to the performance and efficiency of conveyor systems. Conveyor roller rubber sleeves, along with other types, play a vital role in providing protection, reducing slippage, and extending the life of the rollers. Below is a detailed overview of the different types of conveyor roller sleeves available, each catering to specific needs within various industrial applications.
Each type of conveyor roller sleeve offers unique benefits, from the heavy-duty protection and grip provided by rubber sleeves to the customizable hardness and noise reduction properties of polyurethane rollers. Vinyl guard covers and grip tape offer more flexible, temporary solutions for protection and traction enhancement. Selecting the right type of sleeve depends on the specific requirements of the application, including the materials being handled, the environment of operation, and the desired longevity of the conveyor system.
Innovative Solutions in the Market: Conveyor Roller Rubber Sleeve Alternatives
In the evolving landscape of industrial material handling, innovative solutions that enhance the efficiency and durability of conveyor systems are constantly being developed. Among these innovations, the conveyor roller rubber sleeve and its alternatives stand out for their ability to protect rollers, reduce maintenance costs, and improve system performance. Here, we delve into some of the notable solutions in the market that represent advancements in conveyor roller covering technology.
Kastalon Koat-A-Roll® Sleeves
Kastalon’s Koat-A-Roll® sleeves are a prime example of innovation in conveyor roller covering. These sleeves feature a unique “friction-fit” system that allows for easy installation on standard and custom-sized rollers. Designed to significantly increase the grip and protection of rollers, Koat-A-Roll® sleeves are ideal for a variety of applications, including those in harsh industrial environments. The durability and versatility of these sleeves make them a preferred choice for businesses looking to enhance the operation of their conveyor systems without extensive modifications.
Polyurethane Products Corporation
Polyurethane Products Corporation specializes in slip-on roll covers made from high-quality polyurethane. These covers are designed for easy application, offering an immediate upgrade to the operation of conveyor rollers. The slip-on design ensures a secure fit, providing excellent resistance to abrasion, chemicals, and impact. By extending the life of conveyor rollers and improving their performance, Polyurethane Products Corporation’s range of roll covers serves as an efficient solution for businesses seeking to minimize downtime and enhance material handling processes.
Grainger’s Assortment
Grainger offers a diverse assortment of roller covers, including options made from rubber, polyurethane, and specialized materials like heat shrink and shock-absorbing sleeves. This variety caters to specific industry needs, from high-temperature applications to environments where reducing vibration and noise is crucial. Grainger’s selection of conveyor roller covers allows businesses to find the perfect fit for their systems, ensuring that they can achieve optimal performance across a wide range of operational conditions.
Each of these innovative solutions highlights the industry’s move towards more efficient, durable, and adaptable conveyor system components. Whether through the unique “friction-fit” design of Kastalon’s Koat-A-Roll® sleeves, the easy application of Polyurethane Products Corporation’s slip-on covers, or the wide variety of options provided by Grainger, these advancements in conveyor roller rubber sleeve technology and alternatives offer businesses the opportunity to enhance their material handling systems in both standard and challenging applications.
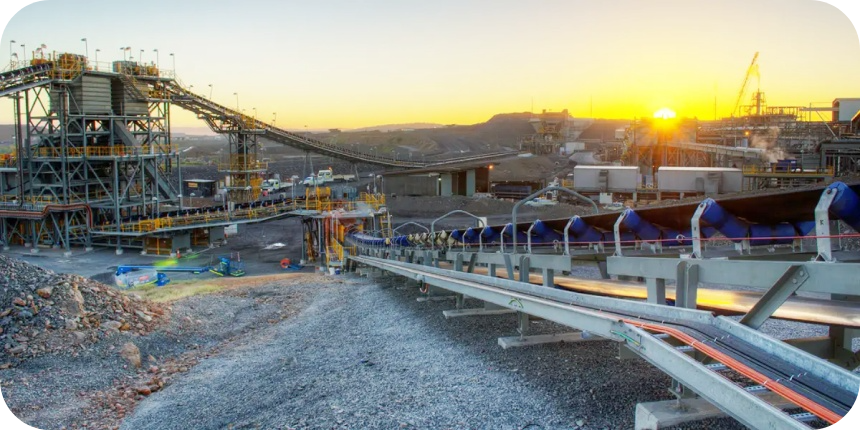
Selecting the Right Sleeve for Your Conveyor Rollers: A Comprehensive Guide
Choosing the appropriate conveyor roller rubber sleeve or alternative material for your conveyor system is a critical decision that impacts the efficiency, durability, and operational cost of your material handling process. The selection process involves a thorough evaluation of the application, environment, and material handling requirements of your conveyor system. Here are ten key guidelines to help you choose the correct sleeve material and type, along with eight essential factors to consider.
Guide on How to Choose the Correct Sleeve Material and Type
- Understand the Application: Begin by assessing the primary function of your conveyor system. Different applications may require different levels of grip, resistance to abrasion, or flexibility.
- Analyze the Environment: Consider the working environment of the conveyor system. Factors such as exposure to chemicals, extreme temperatures, and moisture can significantly influence the choice of sleeve material.
- Evaluate Material Handling Needs: Determine the types of materials the conveyor will transport. This includes considering the weight, size, and nature (abrasive, corrosive, delicate, etc.) of the materials.
- Assess Roller Compatibility: Ensure that the sleeve material is compatible with the existing conveyor rollers, especially in terms of diameter and material.
- Consider Durability Requirements: Evaluate the expected lifespan of the sleeve in the given application and environment. Opt for materials that offer the best balance between durability and cost.
- Factor in Maintenance and Replacement: Choose sleeve materials that are easy to maintain and replace, considering your facility’s operational capabilities.
- Look for Customization Options: Some applications may benefit from customized sleeve solutions, such as specific textures or hardness levels.
- Prioritize Safety and Compliance: Ensure that the sleeve material complies with industry regulations and safety standards, especially in food handling or pharmaceutical applications.
- Evaluate Cost-Effectiveness: While initial costs are important, consider the long-term savings in maintenance, replacement, and efficiency improvements.
- Consult with Experts: When in doubt, consult with manufacturers or experts in conveyor system components for recommendations tailored to your specific needs.
Factors to Consider
- Roller Diameter: The sleeve must fit snugly over the roller. Incorrect sizing can lead to slippage or uneven wear.
- Material Compatibility: The sleeve material should not react chemically with the materials being transported or the environment it is exposed to.
- Intended Use: The specific tasks the conveyor system performs can dictate the need for certain sleeve properties, such as anti-static features for electronics manufacturing.
- Environmental Conditions: Temperature extremes, moisture, and exposure to UV light can degrade certain materials faster than others.
- Abrasion Resistance: In applications involving abrasive materials, choose sleeves with high abrasion resistance to extend their service life.
- Chemical Resistance: For environments where chemicals or oils are present, select sleeves that can withstand such conditions without degrading.
- Flexibility and Grip: Ensure the sleeve material provides the necessary flexibility for the conveyor’s operation and adequate grip for transporting materials.
- Regulatory Requirements: Certain industries may have specific regulations that dictate the types of materials that can be used, especially in direct contact with food or pharmaceuticals.
Selecting the right conveyor roller rubber sleeve or alternative involves a careful analysis of these guidelines and considerations. By taking into account the specific needs of your conveyor system, you can choose a sleeve that enhances performance, extends the lifespan of your rollers, and ultimately contributes to the efficiency and cost-effectiveness of your operations.
Need help selecting the perfect conveyor roller? Contact us now!
Last Updated on July 9, 2024 by Jordan Smith
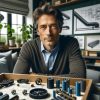
Jordan Smith, a seasoned professional with over 20 years of experience in the conveyor system industry. Jordan’s expertise lies in providing comprehensive solutions for conveyor rollers, belts, and accessories, catering to a wide range of industrial needs. From initial design and configuration to installation and meticulous troubleshooting, Jordan is adept at handling all aspects of conveyor system management. Whether you’re looking to upgrade your production line with efficient conveyor belts, require custom conveyor rollers for specific operations, or need expert advice on selecting the right conveyor accessories for your facility, Jordan is your reliable consultant. For any inquiries or assistance with conveyor system optimization, Jordan is available to share his wealth of knowledge and experience. Feel free to reach out at any time for professional guidance on all matters related to conveyor rollers, belts, and accessories.