Choosing the Right Conveyor Roller Set for Industry
Roller conveyors are defined as mechanical systems consisting of a series of rollers mounted within a rigid frame, designed specifically for transporting objects across flat or inclined planes. The core component of these systems, the conveyor roller set, plays a crucial role in facilitating smooth, efficient movement of goods. Typically utilized in warehouses, manufacturing plants, and distribution centers, roller conveyors can handle a diverse range of items including boxes, crates, and trays.To enhance functionality, a conveyor roller set can be integrated with additional features such as bends, gates, and turntables, allowing for a more flexible material handling solution. The rollers themselves are available in various materials such as steel, galvanized steel, plastic, and stainless steel, catering to different industry needs based on durability, friction, and environmental conditions. This versatility makes roller conveyors an indispensable tool in many industrial applications.
Historical Background of Conveyor Roller Sets
The historical journey of the conveyor roller set begins with the awarding of the first roller conveyor patent in 1908. This innovation laid the groundwork for what would become a pivotal element in manufacturing and logistics industries. The true mainstream adoption of roller conveyors was catalyzed by Henry Ford’s implementation of the assembly line in 1913, which prominently featured these systems. The conveyor roller set proved to be not only effective but essential for mass production.
As the decades progressed, the utilization of the conveyor roller set evolved significantly. In the 1920s, roller conveyors were adapted for longer distances within manufacturing processes, reflecting the growing scale of industrial operations. The technological demands of World War II spurred further developments, particularly in terms of materials and efficiency, as industries sought more robust and versatile handling systems.
From the 1970s to the present day, the conveyor roller set has seen substantial advancements, particularly with the integration of synthetic materials and increased automation. These innovations have enabled roller conveyors to meet the ever-increasing demands for speed and reliability in a wide range of industries, proving that the evolution of the conveyor roller set is closely intertwined with the progression of modern industrial practices.
Industrial Use-Cases for Conveyor Roller Sets
Conveyor roller sets are pivotal in various sectors, significantly enhancing operational efficiencies across numerous industries.
- Logistics and Distribution: In the logistics sector, conveyor roller sets are crucial for the streamlined movement of goods through distribution centers and warehouses. They facilitate the quick and easy transfer of packages across various points in the supply chain, from unloading shipments to sorting and final dispatch.
- Manufacturing: Manufacturing facilities utilize conveyor roller sets extensively to move raw materials, components, and finished products between different stages of the production process. This not only speeds up production but also reduces labor costs and the potential for workplace injuries associated with manual handling.
- Food Processing and Packaging: In the food industry, conveyor roller sets are designed to meet strict hygiene standards, often made from stainless steel or other non-corrosive materials. They are used for transporting products through various stages of processing, cooking, cooling, and packaging, ensuring minimal contact with the products to prevent contamination.
- Mail and Parcel Services: Conveyor roller sets are integral to the operations of mail and parcel service providers, enabling efficient sorting and handling of vast quantities of mail and packages daily. This system ensures that items are swiftly sorted and directed to their respective destinations, optimizing workflow and delivery speed.
In each of these use cases, the conveyor roller set proves to be an indispensable component, tailored to meet the specific demands of different industrial environments, thereby enhancing productivity and operational efficiency.
Benefits of Gravity Roller Conveyor Roller Sets
Gravity roller conveyor roller sets are an economical and efficient solution for many material handling needs, characterized by their reliance on gravity to move items along the conveyor track. This simplicity of design offers several significant advantages:
- Cost-effectiveness: One of the primary benefits of using a gravity roller conveyor roller set is its cost-effectiveness. Since these conveyors utilize gravity to move products, there is no need for motorized power sources, which significantly reduces operational costs. This makes them particularly suitable for businesses looking to decrease energy expenditures and increase profitability.
- Environmental Impact: Gravity roller conveyor roller sets have a lower environmental impact compared to their powered counterparts. By eliminating the need for electricity or fuel to operate, these conveyor systems contribute to a reduction in energy consumption and carbon footprint, making them a more sustainable choice for eco-conscious operations.
- Maintenance: With fewer moving parts and no reliance on electrical or mechanical components, gravity roller conveyor roller sets require less maintenance. This not only reduces downtime but also lowers the long-term maintenance costs associated with wear and tear on motors and other power-driven components. Their simplicity ensures that they are less likely to encounter operational issues, thus enhancing reliability and extending the lifespan of the conveyor system.
These benefits make gravity roller conveyor roller sets an appealing option for a wide range of industries, particularly those where cost reduction and environmental sustainability are priorities.
Limitations of Gravity Roller Conveyor Roller Sets
Despite the many benefits offered by gravity roller conveyor roller sets, they come with specific limitations that might affect their suitability in certain industrial applications. One of the primary challenges associated with gravity roller conveyor roller sets is speed control. Since these systems rely solely on gravity to move items, controlling the speed at which items travel can be problematic.
The absence of powered mechanisms means that once items are in motion, their speed is influenced by weight, the slope of the conveyor, and friction between the items and the rollers. This can lead to situations where items move too quickly or gather too much momentum, potentially resulting in collisions, product damage, or disruptions in the sorting and handling processes. For delicate or fragile items, this can increase the risk of breakage or degradation during transit, leading to higher product wastage and reduced efficiency.
Addressing this limitation often requires careful design considerations, such as adjusting the angle of incline or installing speed controlling devices like brakes or regulators at critical points along the conveyor. However, these additions can somewhat negate the cost-effectiveness and simplicity that make gravity roller conveyor roller sets appealing in the first place.
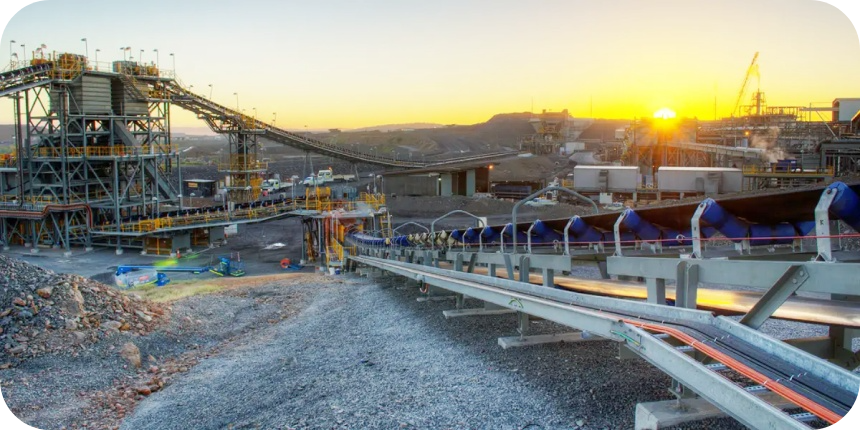
Benefits of Powered Conveyor Roller Sets
Powered conveyor roller sets offer distinct advantages over their gravity-fed counterparts, making them indispensable in various industrial environments where precision and control are crucial. Here are the key benefits:
- Long-Distance Capabilities: One of the standout features of powered conveyor roller sets is their ability to efficiently transport goods over long distances within facilities. Unlike gravity roller conveyors, powered rollers provide consistent movement and speed, ensuring that items can travel extensive lengths without the need for manual assistance or gravity slopes. This makes them particularly beneficial in large manufacturing plants and distribution centers.
- Process Control: With powered conveyor roller sets, speed control is not only possible but also highly precise. This control allows for better handling of goods, minimizing the risk of damage and ensuring smoother transitions from one process to another. Adjustable speed settings also accommodate different workflow requirements, which can vary widely depending on the type and volume of goods being transported.
- Load Handling: Powered conveyor roller sets are particularly adept at managing heavier loads, which are prevalent in industries like manufacturing, mining, and heavy equipment logistics. The motorized rollers distribute the weight evenly and keep goods moving without the strain that manual handling or gravity-dependent systems might incur, reducing wear and tear on both the conveyor system and the products.
- Zoned Operation: One of the most innovative features of powered conveyor roller sets is the ability to control individual zones independently. Each segment of the conveyor can be activated or deactivated as needed, which not only increases operational efficiency but also reduces energy consumption and operational costs. This zoned control is ideal for assembly lines and sorting operations, where different sections of the conveyor may need to operate based on the specific processing stages or varying workflow demands.
Overall, the powered conveyor roller set provides robust solutions that enhance productivity, reduce labor costs, and improve overall operational efficiency in complex industrial settings.
FAQs About Conveyor Roller Set
Rollers on a conveyor, also known as conveyor rollers, are cylindrical components that rotate to facilitate the movement of materials along the conveyor belt or within the conveyor frame. These rollers are typically mounted on bearings and aligned in a series to form a path that supports and moves items from one point to another. They can be made from various materials including metal, plastic, or rubber, depending on the application and the types of loads they need to handle. Rollers are crucial in reducing friction and ensuring smooth, efficient transportation of goods across different sections of the conveyor system.
A roller conveyor is a type of conveyor system that utilizes a series of rollers mounted within a frame to transport items across a flat or inclined plane. Roller conveyors can be powered by motors, or they can be gravity-fed to move items through manual force or downward inclines. This type of conveyor is versatile and commonly used in various industries such as manufacturing, logistics, and packaging. It is particularly favored for its ability to handle items of varying sizes and weights, and for its adaptability to different warehouse or factory layouts.
A roller conveyor consists of several key components that work together to ensure efficient material handling. These include:
Rollers: The main elements that directly contact and move the cargo.
Frame: Supports the rollers and is usually constructed from materials like steel or aluminum.
Bearings: Facilitate the smooth rotation of the rollers.
Drive System (for powered conveyors): Includes motors and belts to drive the rollers.
Control System: Manages the operation and speed of the conveyor, especially in powered models.
Support Legs: Provide stability and proper elevation to the conveyor. Each component is critical for the conveyor’s operation and must be maintained to keep the system running smoothly.
The formula for designing a conveyor roller typically involves calculations to determine the appropriate roller spacing, load per roller, and the type of rollers needed based on the weight and type of materials being transported. This formula helps ensure that the load is supported by at least three rollers at any given time, reducing stress and potential deformation. Additionally, the load capacity per roller must be considered, which involves the weight distribution, the type of materials used for the rollers, and environmental factors such as temperature and humidity. Design engineers will use these calculations in conjunction with manufacturer specifications to create an optimal conveyor system tailored to specific operational needs.
Improve efficiency with our top-notch conveyor rollers.
Last Updated on July 17, 2024 by Jordan Smith
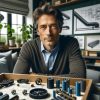
Jordan Smith, a seasoned professional with over 20 years of experience in the conveyor system industry. Jordan’s expertise lies in providing comprehensive solutions for conveyor rollers, belts, and accessories, catering to a wide range of industrial needs. From initial design and configuration to installation and meticulous troubleshooting, Jordan is adept at handling all aspects of conveyor system management. Whether you’re looking to upgrade your production line with efficient conveyor belts, require custom conveyor rollers for specific operations, or need expert advice on selecting the right conveyor accessories for your facility, Jordan is your reliable consultant. For any inquiries or assistance with conveyor system optimization, Jordan is available to share his wealth of knowledge and experience. Feel free to reach out at any time for professional guidance on all matters related to conveyor rollers, belts, and accessories.