Essentials of Conveyor Roller Shaft Selection
In the vast expanse of industrial operations, the conveyor roller shaft stands out as a pivotal component, integral to the seamless execution of material handling tasks across various sectors. From manufacturing lines to distribution centers, these shafts are the backbone that supports the efficient movement of goods, underscoring their indispensable role in enhancing productivity and operational flow. The shaft size, in particular, plays a critical role in the overall performance of conveyor rollers, dictating their capacity to withstand loads and maintain stability during operation. A precisely sized shaft ensures optimal balance and alignment, which are crucial for minimizing wear and tear on the system and extending the lifespan of the equipment. Thus, understanding and selecting the appropriate conveyor roller shaft is paramount for achieving efficient and reliable conveyor system operations, highlighting its significance in industrial mechanics.
What are Conveyor Roller Shafts
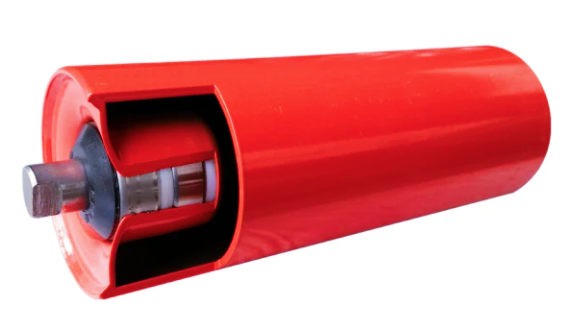
The conveyor roller shaft serves as the core structural component within a conveyor roller, around which the roller cylinder rotates. Essentially, it is the axle of the roller, providing the necessary support and allowing the roller to turn smoothly within the conveyor frame. These shafts play a pivotal role in various systems, such as in baggage handling at airports, packaging lines in the food industry, assembly lines in manufacturing, and sorting systems in distribution centers. By ensuring the efficient and uninterrupted flow of materials, conveyor roller shafts significantly contribute to the productivity and efficiency of operational processes.
The relationship between the size of the conveyor roller shaft and the performance of the conveyor system is a critical aspect of conveyor design. A well-sized shaft not only supports the weight of the materials being transported but also reduces the risk of deflection, which can lead to misalignment, wear, and eventual failure of the roller. The diameter and material of the shaft must be selected based on the load requirements and the environment in which the conveyor will operate. For example, heavier loads or corrosive environments may necessitate larger diameters or more robust materials to ensure reliability and longevity of the conveyor system. Thus, the correct sizing and material selection of the conveyor roller shaft are fundamental to optimizing conveyor performance, minimizing maintenance requirements, and extending the service life of the system.
Conveyor Roller Shaft Size
The standard dimensions of conveyor roller shafts is essential for the design and operation of an efficient conveyor system. Typically, the diameter of a conveyor roller shaft can vary widely depending on the application, ranging from small shafts of 20mm for light-duty applications to larger shafts up to and beyond 50mm for heavy-duty industrial use. The length of the shaft also varies according to the width of the conveyor belt or roller frame, ensuring it can adequately support the rollers and the load they carry. These standard dimensions serve as a guideline, but customization is often necessary to meet specific operational needs.
Measuring and specifying the correct size for your conveyor roller shaft is crucial for system performance and longevity. The process involves several key steps:
- Determine the Load: Understand the maximum load the conveyor will need to support. This includes both the weight of the materials being transported and the weight of the conveyor roller itself.
- Assess the Environment: Consider the operating environment, as factors like temperature, humidity, and exposure to chemicals can affect material choice and shaft size.
- Calculate the Required Diameter: Use engineering formulas or software to calculate the necessary shaft diameter to support the identified load without excessive deflection or stress.
- Select Material: Choose a shaft material that offers the best combination of strength, durability, and cost-effectiveness for your application. Common materials include steel, stainless steel, and aluminum.
- Specify the Length: The length of the conveyor roller shaft must be sufficient to extend across the roller bearings and any frame or mounting hardware, with a small allowance for manufacturing tolerances and thermal expansion.
By carefully measuring and specifying the conveyor roller shaft size, you can ensure that your conveyor system operates smoothly, efficiently, and with a minimal need for maintenance. This attention to detail in the planning phase can significantly impact the overall success and reliability of the conveyor system.
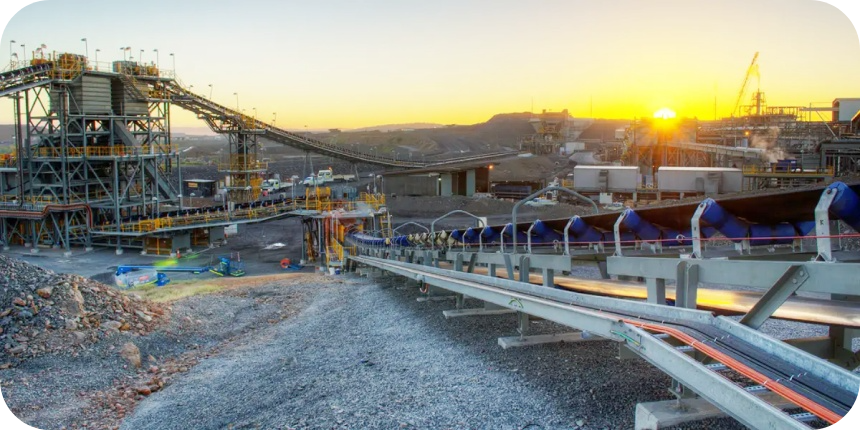
Selecting the Right Conveyor Roller Shaft
Selecting the right conveyor roller shaft is a critical decision that affects the efficiency, durability, and cost-effectiveness of your conveyor system. Several key factors must be considered to ensure that the shaft you choose meets the requirements of your specific application:
- Load Capacity: The most critical factor to consider is the load the shaft must support. Choose from the right conveyor roller shaft, designed for easy installation and optimal load support on conveyor frames or stands. This includes not only the weight of the materials being conveyed but also the weight of the roller itself. A shaft that is too small may bend or break under load, while an unnecessarily large shaft can increase costs and reduce efficiency.
- Operating Environment: The environment in which the conveyor will operate influences the choice of shaft material. Factors such as exposure to chemicals, moisture, temperature extremes, and abrasive materials must be considered to ensure the selected material can withstand the conditions without corroding or degrading.
- Speed of Operation: The speed at which the conveyor will operate affects the type of shaft needed. Higher speeds may require shafts with greater tolerance and balance to maintain efficient operation without excessive vibration.
- Maintenance Requirements: The ease of maintenance and the expected lifespan of the shaft are also important considerations. Selecting a shaft that can be easily replaced or maintained can significantly reduce downtime and operational costs.
When it comes to materials, the choice of conveyor roller shaft material significantly impacts its performance and suitability for different applications.
- Steel: Steel shafts are renowned for their strength and durability, making them ideal for heavy-duty applications where high load-bearing capacity is required. They are commonly used in industrial and manufacturing settings.
- Stainless Steel: For environments prone to corrosion, such as those with high moisture levels or exposure to chemicals, stainless steel roller shafts are preferred. They offer excellent corrosion resistance and are suitable for food processing, pharmaceutical, and marine applications.
- Aluminum: Aluminum shafts are lighter than steel and stainless steel, making them suitable for applications where weight is a concern, such as in packaging or distribution centers. They offer good corrosion resistance and are easier to handle and install.
- Composite Materials: Composite shafts, made from materials such as fiberglass or carbon fiber, are used in specialized applications where weight savings, corrosion resistance, and non-conductivity are critical. These are often found in aerospace, automotive, and food processing industries where traditional metal shafts are not suitable.
Selecting the right conveyor roller shaft involves a careful balance of these factors, ensuring that the chosen shaft meets the specific needs of the application while optimizing performance and cost.
Replacing Conveyor Roller Shafts
Replacing conveyor roller shafts is a critical maintenance activity that ensures the smooth operation of a conveyor system. A systematic approach to replacement not only minimizes downtime but also extends the lifespan of the conveyor rollers. Here is a step-by-step guide to effectively replace conveyor roller shafts:
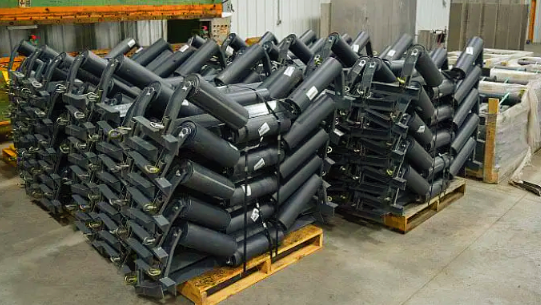
- Safety First: Always start by ensuring the conveyor is powered off and locked out to prevent accidental start-ups. Safety should be the primary concern during any maintenance work.
- Inspect and Prepare: Carefully inspect the conveyor to identify the shafts that need replacement. Gather all necessary tools and replacement shafts before starting the work to minimize downtime.
- Removal of the Old Shaft: Begin by removing any components that obstruct access to the shaft, such as guards or brackets. Using appropriate tools, gently remove the roller from its frame. In some cases, this may require loosening fasteners or using a rubber mallet to tap the roller free.
- Install the New Shaft: Once the old shaft is removed, check the roller and the inside of the bearing housings for any wear or damage. Clean any debris or buildup before sliding the new shaft into place. Ensure that the shaft is correctly aligned and seated within the roller.
- Reassemble and Test: After installing the new shaft, reattach any components that were removed and ensure all fasteners are securely tightened. Power on the conveyor and test the roller to ensure it operates smoothly without any misalignment or noise.
To minimize downtime during conveyor roller shaft replacement, consider the following tips:
- Preventative Maintenance: Regularly inspect shafts and rollers for signs of wear and tear. Early identification of potential issues can prevent unexpected breakdowns.
- Keep Spare Parts Handy: Maintain a stock of essential spare parts, including shafts and bearings, to avoid delays in sourcing replacements during critical maintenance.
- Train Maintenance Staff: Ensure that maintenance staff are well-trained and familiar with the conveyor system. Skilled personnel can perform replacements more quickly and efficiently.
- Schedule Downtime Strategically: Plan for maintenance and replacement activities during off-peak hours or scheduled production downtimes to minimize the impact on operations.
By following these guidelines and tips, you can effectively manage the replacement of conveyor roller shafts, ensuring minimal disruption to your operations and maintaining the efficiency of your conveyor system.
Ensure productivity with our conveyor rollers. Contact us!
Shaft Roller Bearings
Shaft roller bearings play an integral role in the functionality and efficiency of conveyor systems, acting as the intermediary that allows the conveyor roller shaft to rotate smoothly under the burden of heavy loads. These bearings are crucial for several reasons:
- Reduced Friction: Shaft roller bearings significantly reduce the friction between the shaft and the roller, enabling the conveyor to operate more efficiently and with less wear on the components.
- Load Distribution: They help distribute the load evenly across the conveyor roller, ensuring that the system can handle heavy and uneven loads without failure.
- Increased Lifespan: By minimizing direct contact between moving parts, bearings extend the lifespan of both the rollers and the shafts, reducing the need for frequent replacements.
- Enhanced Performance: Bearings ensure that the conveyor operates smoothly and quietly, improving the overall performance of the conveyor system.
Selecting the right bearings for your conveyor roller shafts involves several key considerations:
- Load Capacity: Choose bearings that can handle the maximum expected load of the conveyor system. This includes considering both the weight of the materials being transported and the weight of the conveyor roller itself.
- Operating Environment: The environment in which the conveyor operates can significantly affect the performance and lifespan of bearings. For harsh environments with high levels of dust, moisture, or corrosive materials, select bearings made from materials that can withstand these conditions, such as stainless steel or coated bearings.
- Speed Requirements: The operational speed of the conveyor system dictates the type of bearing required. High-speed operations may need bearings designed to reduce friction and heat buildup effectively.
- Maintenance and Replacement: Consider the ease of maintenance and replacement of the bearings. Bearings that are sealed and lubricated for life reduce maintenance requirements but may be more difficult to replace. Conversely, bearings that require regular maintenance might be easier to replace but necessitate more downtime.
By carefully considering these factors, you can ensure that you select the right shaft roller bearings for your conveyor roller shafts, thereby optimizing the performance and reliability of your conveyor system. This careful selection process not only improves efficiency but also reduces the need for costly maintenance and downtime, contributing to the overall productivity of your operations.
Conveyor Roller Shaft Parts and Assembly
A conveyor roller system is composed of several key components, each playing a vital role in the system’s operation and efficiency. At the heart of these components is the conveyor roller shaft, which serves as the central axis for the roller’s operation. Understanding the parts and their assembly is crucial for maintaining the performance and longevity of the conveyor system.
Key Components:
- Conveyor Roller Shaft: The core component that provides support and the rotational axis for the roller.
- Roller Tube: The cylindrical part that encases the shaft and actually makes contact with the conveyed material.
- Bearings: Positioned at both ends of the conveyor roller tube, bearings allow the shaft to rotate smoothly within the tube.
- Seals: These protect the bearings from contaminants, ensuring longevity and smooth operation.
- End Caps: Attached to the ends of the roller tube, they hold the bearings and seals in place and can be used for mounting the roller in the conveyor frame.
- Casing or Housing: External structure that may encase the bearings and other inner components for additional protection and to facilitate mounting.
Assembly Instructions:
Proper assembly of conveyor roller parts is essential for optimal performance. Here are four key steps to ensure correct assembly:
- Prepare the Shaft: Start by inspecting the conveyor roller shaft for any imperfections or damage. Ensure it is clean and ready for assembly. Apply a light coat of industrial lubricant to the shaft to facilitate smooth bearing movement.
- Install Bearings and Seals: Slide the bearings onto each end of the shaft. Next, place the seals outside the bearings. It’s crucial that the bearings are oriented correctly to support the load and allow for smooth rotation. Seals should be snug against the bearings to prevent any contaminants from entering.
- Attach the Roller Tube: Carefully slide the roller tube over the shaft and bearings assembly. Ensure that the tube is centered and that both ends are aligned properly with the end caps.
- Secure End Caps: Attach the end caps to the ends of the roller tube, ensuring that they are tightly secured. The end caps not only keep the bearings and seals in place but also provide the mounting points for the roller in the conveyor frame.
Following these steps carefully will ensure that the conveyor roller parts are assembled correctly, resulting in a roller that operates smoothly and efficiently. Regular maintenance and inspection of these components, especially the conveyor roller shaft, are vital to prolong the system’s life and minimize downtime.
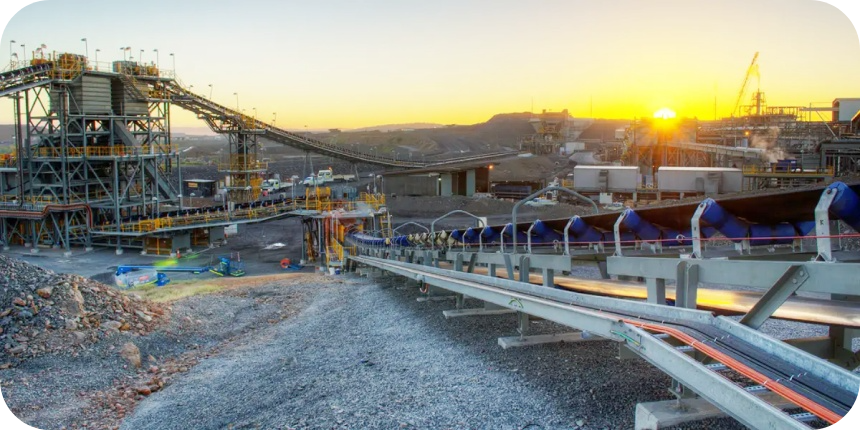
The Mechanics of Conveyor Roller Shaft
The mechanics of conveyor rollers revolve around the harmonious interaction between the rollers themselves and the conveyor roller shafts. This synergy is essential for the smooth and efficient movement of materials along the conveyor system. The conveyor roller shaft acts as the core around which the roller rotates, providing the necessary support and stability for the operation.
How Conveyor Rollers and Shafts Work Together:
Conveyor rollers are cylindrical tubes that rotate around a central axle, the conveyor roller shaft. Bearings housed within the roller allow it to spin smoothly around the shaft with minimal friction. This rotation is crucial for transporting materials across the conveyor system efficiently. The shaft’s role is not just supportive; it also ensures that the roller maintains its position and alignment, preventing it from drifting or skewing, which could disrupt the movement of materials or damage the conveyor.
Common Issues and Troubleshooting:
Despite their simplicity, conveyor rollers and shafts can encounter several issues that impede their operation. Understanding how to identify and troubleshoot these problems is vital for maintaining a productive conveyor system.
- Misalignment: If rollers or shafts become misaligned, they can cause uneven wear, material spillage, or jam the conveyor. Check for worn bearings or loose conveyor roller mounting brackets and adjust or replace as necessary to realign the system.
- Excessive Noise: Unusual noise often indicates a problem with the roller or shaft, such as worn bearings, insufficient lubrication, or debris caught in the roller. Inspect the components, clean or lubricate bearings, and replace any damaged parts.
- Reduced Rotation Efficiency: Difficulty in roller rotation can be due to overloading, improper installation, or wear and tear on the bearings. Ensure the load is within the conveyor’s capacity, check the installation for errors, and replace worn bearings to restore efficiency.
- Wear and Tear: Regular wear can degrade rollers and shafts over time, leading to decreased performance or failure. Regular inspections can identify wear early, and parts should be replaced before they cause system downtime.
By understanding the mechanics of how conveyor rollers and shafts work together and being vigilant about common issues, maintenance teams can troubleshoot problems effectively. This proactive approach ensures the conveyor system remains operational, minimizing downtime and maintaining productivity.
Conveyor Roller Shaft Maintenance
Maintaining the conveyor roller shaft is crucial for ensuring the longevity and efficiency of conveyor systems. Proper maintenance not only prolongs the life of the equipment but also prevents costly downtime and repairs. Here are essential maintenance tips and practices for keeping conveyor roller shafts in optimal condition:
Maintenance Tips:
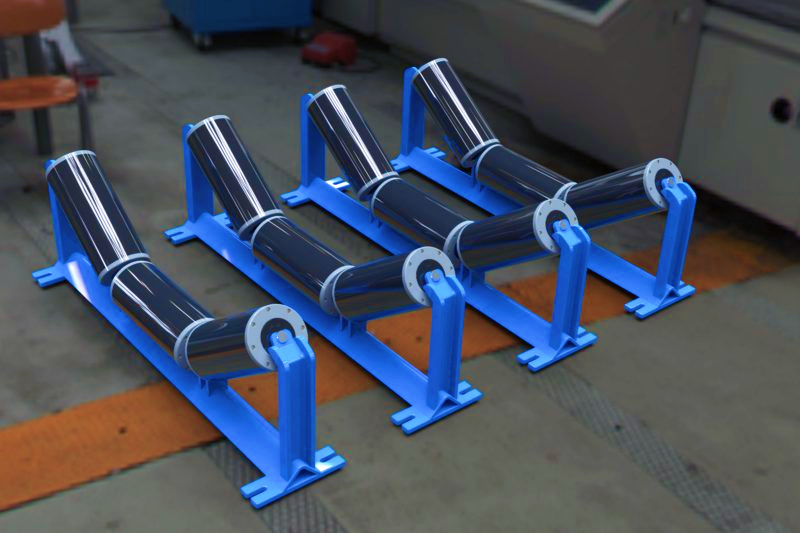
- Regular Lubrication: Proper lubrication reduces friction between the shaft and bearings, minimizing wear and extending their lifespan. Use the correct type of lubricant as recommended by the manufacturer, and apply it at regular intervals to ensure smooth operation.
- Cleanliness: Keeping the conveyor roller shafts clean from dust, debris, and other contaminants is essential. Accumulation of such materials can lead to increased friction, wear, and even corrosion. Regular cleaning schedules should be established to prevent buildup.
- Inspection for Wear and Damage: Regularly inspect the shafts and bearings for signs of wear, damage, or corrosion. Pay special attention to any irregularities, such as cracks, bends, or excessive wear, and replace any components that are not in good condition.
- Alignment Checks: Misalignment of the conveyor roller shafts can lead to uneven wear and tear, reduced efficiency, and potential damage to the conveyor. Ensure that shafts are correctly aligned and make adjustments as necessary.
Schedules and Procedures for Regular Maintenance Checks:
- Daily Checks: Perform visual inspections for obvious signs of wear, damage, or misalignment. Check for any unusual noises or vibrations that could indicate a problem.
- Weekly Maintenance: Conduct a more thorough inspection of the conveyor roller shafts, including cleaning and lubricating as needed. Verify the condition of the bearings and alignment of the shafts.
- Monthly Reviews: Perform a comprehensive review of the conveyor system, focusing on the roller shafts, bearings, and other critical components. Look for signs of wear or damage that may have been missed during shorter inspections.
- Annual Overhaul: Plan for a detailed annual maintenance check, potentially during a scheduled shutdown. This is the time to perform any necessary replacements, deep cleaning, and re-lubrication of the entire system. Consider using this opportunity to upgrade components as necessary to improve efficiency and performance.
By adhering to these maintenance tips and following a structured schedule for regular checks, you can significantly enhance the performance and lifespan of conveyor roller shafts. Effective maintenance not only ensures the reliability of the conveyor system but also maintains its efficiency, reducing the overall cost of operation and maintenance in the long term.
Global Standards and Compliance for Conveyor Roller Shaft
In the world of conveyor systems, the conveyor roller shaft plays a crucial role in the seamless operation of the entire assembly. Adherence to global standards and compliance is not just a matter of legal requirement but also a cornerstone of quality, safety, and efficiency in the manufacturing and distribution of these components. Understanding and complying with these standards, including the Harmonized System (HS) codes for international trade, is essential for manufacturers and suppliers worldwide.
Roller Shaft HS Code and International Trade Compliance:
The HS code for conveyor roller shafts is a standardized numerical method of classifying traded products. It is used by customs authorities around the world to identify products for the application of duties and taxes. Accurate classification of conveyor roller shafts under the correct HS code is crucial for manufacturers and exporters to ensure compliance with international trade regulations, avoid costly delays, and streamline customs processes.
Importance of Abiding by Global Standards in Manufacturing Conveyor Rollers:
- Safety: Global standards ensure that conveyor roller shafts are designed and manufactured to prevent accidents and injuries in the workplace. This includes specifications for strength, durability, and materials to ensure that they can safely support the intended loads without failure.
- Interoperability: Adherence to standardized dimensions and tolerances ensures that conveyor roller shafts can be used in systems worldwide, facilitating international trade and the exchange of products. This compatibility is crucial for companies operating in multiple countries or sourcing parts from different manufacturers.
- Quality Assurance: Global standards provide a benchmark for quality, helping manufacturers maintain consistent product quality. This consistency is vital for consumer trust and the reputation of manufacturers in the global market.
- Environmental Compliance: Many standards include guidelines for environmentally friendly manufacturing processes and materials. Compliance with these standards helps companies minimize their environmental impact, meet regulatory requirements, and appeal to environmentally conscious consumers.
Manufacturers and suppliers of conveyor roller shafts must stay informed about the relevant global standards and regulatory requirements in their industry. This includes continuous monitoring of changes in trade laws, safety regulations, and quality standards across different countries and regions. By prioritizing compliance and adherence to these global standards, companies can ensure the safety, reliability, and efficiency of their conveyor roller shafts, fostering trust and confidence among their customers and partners worldwide.
Quality Suppliers of Conveyor Roller Shafts and Parts
In the realm of material handling and conveyance, the quality of components such as conveyor roller shafts and parts cannot be overstated. These components are critical for the efficient, reliable, and safe operation of conveyor systems. Among the plethora of suppliers in the market, names like Gram Conveyor, Misumi, Ashland Conveyor, and McMaster-Carr stand out for their commitment to quality, range of offerings, and exceptional customer service.
Introduction to Reputable Suppliers
Gram Conveyor:
- Renowned for its innovative designs and high-quality materials, Gram Conveyor offers a diverse range of conveyor roller shafts and parts. Their products, including the well-regarded “GRAM Nylon Series,” are designed for durability and easy maintenance, making them ideal for industries such as chemical manufacturing and cleanrooms. Gram Conveyor’s focus on customization ensures that clients receive components tailored to their specific needs, enhancing compatibility and performance.
Misumi:
- Known for its extensive selection of mechanical components, Misumi provides a wide range of conveyor roller shafts and parts. Their ability to offer both standard and custom parts allows for precise applications, ensuring optimal performance and compatibility. Misumi’s strength lies in their commitment to providing high-quality components that meet the exact specifications of their customers.
Ashland Conveyor:
- Specializing in conveyor system parts, Ashland Conveyor offers a comprehensive range of products, including roller shafts that cater to various industrial needs. Their products are known for their durability and reliability, making them a preferred choice for industries requiring robust conveyor solutions. Ashland Conveyor’s dedication to quality ensures that their components perform efficiently and last longer.
McMaster-Carr:
- With a vast inventory of industrial tools and supplies, McMaster-Carr is a one-stop-shop for conveyor roller shafts and parts. Their extensive catalog features thousands of items, ensuring that customers can find exactly what they need for their conveyor systems. McMaster-Carr is known for its exceptional customer service and often provides same-day shipping, making it a convenient and reliable supplier.
Each of these suppliers brings a unique set of strengths to the table, ensuring that businesses have access to high-quality conveyor roller shafts and parts that meet their specific requirements. By choosing reputable suppliers like Gram Conveyor, Misumi, Ashland Conveyor, and McMaster-Carr, companies can ensure the longevity and efficiency of their conveyor systems.
How to Choose the Right Supplier for Your Conveyor Parts Needs
Selecting the right supplier for conveyor roller shafts and parts involves several considerations to ensure you receive high-quality components that meet your system’s requirements:
- Product Range and Availability: Look for suppliers with a wide range of products and the availability of stock to meet your immediate needs. This includes a variety of shaft sizes, materials, and bearing types to suit different applications.
- Customization Options: Depending on your specific conveyor system, you may need customized parts. Suppliers who offer customization services can provide parts that precisely fit your requirements.
- Quality and Reliability: Assess the quality of the products by reviewing specifications, materials used, and compliance with global standards. Reliable suppliers often have positive reviews and testimonials from satisfied customers.
- Technical Support and Customer Service: A supplier’s ability to offer expert advice, technical support, and responsive customer service is crucial, especially when dealing with complex conveyor systems. This support can be invaluable in selecting the right components and troubleshooting potential issues.
- Pricing and Delivery: Competitive pricing, without compromising on quality, is important. Also, consider the supplier’s delivery times and shipping options to ensure that you receive your parts when you need them.
Used Conveyor Roller Shafts
Advantages of Using Pre-Owned Shafts
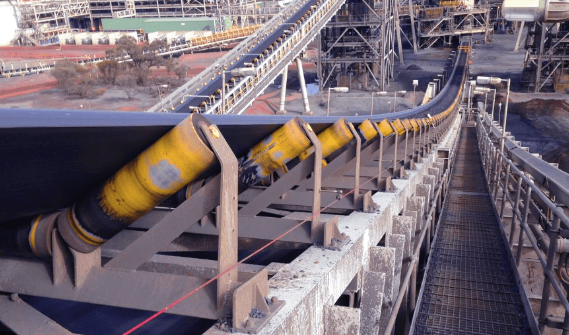
- Cost Benefits and Availability of Used Conveyor Roller Shafts
- One of the primary advantages of opting for used conveyor roller shafts is the significant cost savings. Pre-owned shafts are generally available at a fraction of the cost of new ones, making them an economical choice for businesses looking to reduce expenses without compromising on functionality.
- The availability of used shafts is another key benefit. With a growing market for second-hand industrial equipment, it is often easier and quicker to source used conveyor roller shafts, especially for older conveyor systems where new parts may no longer be in production.
- By purchasing used shafts, companies can also contribute to sustainability efforts. Reusing industrial components reduces waste and minimizes the environmental impact associated with manufacturing new parts.
- Considerations When Purchasing Used Shafts
- When buying used conveyor roller shafts, it is crucial to consider the condition and history of the parts. Knowing the previous usage can provide insights into the wear and tear the shafts have experienced.
- Compatibility is another important factor. Ensure that the used shafts match the specifications and requirements of your existing conveyor system. Mismatched components can lead to operational inefficiencies and potential system failures.
- It is also advisable to purchase from reputable suppliers or sellers who provide warranties or guarantees on their used parts. This can offer additional peace of mind and protection against unforeseen issues.
Quality Checks
- Important Quality Checks and Inspections for Used Shafts
- Before integrating used conveyor roller shafts into your system, thorough quality checks and inspections are essential. Begin with a visual inspection to identify any obvious signs of damage such as cracks, excessive wear, or corrosion.
- Measurement checks should be conducted to ensure the shafts meet the required dimensions and tolerances. Any deviations can affect the alignment and performance of the conveyor system.
- It is also important to inspect the surface finish of the shafts. Smooth and even surfaces are crucial for reducing friction and wear during operation.
- Ensuring Durability and Reliability in Pre-Owned Components
- To ensure durability and reliability, consider the material composition of the used shafts. High-quality materials like stainless steel or hardened alloys typically offer better longevity and performance.
- Conducting non-destructive testing (NDT) such as ultrasonic or magnetic particle inspection can help detect internal flaws that may not be visible during a visual inspection. This step is particularly important for critical applications where shaft failure can lead to significant downtime and costs.
- Finally, it is advisable to consult with a qualified engineer or technician to assess the suitability of the used shafts for your specific application. Professional assessment can provide a more comprehensive evaluation and ensure that the pre-owned components will perform reliably in your conveyor system.
By carefully evaluating these factors, you can select a quality supplier for conveyor roller shafts and parts that will meet your operational needs, support the efficiency and reliability of your conveyor system, and provide value over time. Reputable suppliers like Misumi, Ashland Conveyor, and McMaster-Carr not only offer high-quality products but also the expertise and support to ensure the success of your mining conveyor projects.
FAQs About Conveyor Roller Shaft
A conveyor shaft, often referred to as a conveyor roller shaft, is a fundamental component of a conveyor system that serves as the axle for the rollers, enabling them to rotate smoothly. This cylindrical rod extends across the width of the conveyor frame and is critical for the movement and support of the conveyor belt or rollers. The design and material of the shaft are pivotal in determining the conveyor’s capacity to handle various loads, speeds, and operational stresses. Conveyor shafts must be precisely manufactured to fit the bearings and the inner diameter of the rollers, ensuring efficient and uninterrupted operation. The choice of shaft is influenced by factors such as load weight, conveyor speed, environmental conditions, and the intended use of the conveyor system. Proper selection and maintenance of conveyor shafts are crucial for minimizing wear and tear, reducing downtime, and ensuring the longevity and reliability of the conveyor system.
Conveyor roller shafts are typically made from materials that offer a balance of strength, durability, and cost-effectiveness. The most common material used is steel, including carbon steel and stainless steel, due to its high tensile strength and resistance to wear and deformation under heavy loads. Carbon steel is preferred for general applications, providing a robust and cost-effective solution. Stainless steel, on the other hand, is used in environments where resistance to corrosion is crucial, such as in food processing or chemical industries. For applications requiring lighter weights or specific environmental considerations, aluminum and composite materials (such as reinforced plastics) are also used. These materials offer benefits including reduced weight, corrosion resistance, and non-magnetic properties, making them suitable for a wide range of applications depending on the specific requirements of the conveyor system.
The rollers on a conveyor, known as conveyor rollers, are the moving parts that support and propel the conveyor belt or items being transported. They are mounted within the conveyor frame and can vary in size, material, and design based on the application. Conveyor rollers play a crucial role in guiding and supporting the belt or items, allowing for smooth and efficient movement across the conveyor system. These rollers are typically cylindrical and can be either powered, propelling the belt or items with mechanical force, or non-powered (gravity rollers), relying on gravity or manual force for movement. The choice of roller type, material, and spacing is determined by the load requirements, operational speed, and environmental conditions of the conveyor system. Materials commonly used for conveyor rollers include steel, plastic, and rubber, each offering different properties in terms of strength, friction, and resistance to environmental factors.
A roller conveyor is a type of conveyor system that uses a series of rollers mounted within a frame to move materials or objects from one place to another. Roller conveyors are versatile, efficient, and commonly used in a wide range of industries, including manufacturing, logistics, and retail, for the handling of items that are too heavy or bulky for manual transportation. They can be powered, using motors to move the rollers and transport items along the conveyor, or non-powered (gravity conveyors), where items move down an incline or are manually pushed along the conveyor. Roller conveyors are favored for their simplicity, durability, and the ease with which they can be customized to fit specific operational needs. They can handle a variety of items, from boxes and pallets to individual parts, and can be designed with features like adjustable speeds, accumulation capabilities, and integration with other conveyor types, making them a flexible solution for material handling challenges.
Conveyor rollers come in a variety of standard dimensions, tailored to suit different types of conveyor systems and applications. Typically, conveyor rollers are available in diameters ranging from 1 inch (25.4 mm) to 8 inches (203.2 mm), with lengths varying from 6 inches (152.4 mm) to 60 inches (1524 mm). The specific dimensions depend on the intended use, whether for light, medium, or heavy-duty applications.
For instance, standard roller diameters for light-duty conveyors often fall between 1 inch (25.4 mm) and 2 inches (50.8 mm). These are commonly used in applications such as package handling and small parts transfer. Medium-duty conveyors typically use rollers with diameters from 2 inches (50.8 mm) to 4 inches (101.6 mm), suitable for handling larger packages and heavier loads.
Heavy-duty conveyor rollers, designed for demanding applications like mining, bulk material handling, and industrial manufacturing, usually range from 4 inches (101.6 mm) to 8 inches (203.2 mm) in diameter. These rollers are built to withstand significant wear and tear and support substantial loads.
In terms of length, the choice depends on the conveyor’s width and the specific requirements of the material being transported. Standard lengths generally range from 6 inches (152.4 mm) to 60 inches (1524 mm), accommodating a wide array of conveyor designs.
Overall, selecting the appropriate conveyor roller dimensions is crucial for ensuring efficient operation, load handling capacity, and longevity of the conveyor system.
Last Updated on June 28, 2024 by Jordan Smith
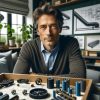
Jordan Smith, a seasoned professional with over 20 years of experience in the conveyor system industry. Jordan’s expertise lies in providing comprehensive solutions for conveyor rollers, belts, and accessories, catering to a wide range of industrial needs. From initial design and configuration to installation and meticulous troubleshooting, Jordan is adept at handling all aspects of conveyor system management. Whether you’re looking to upgrade your production line with efficient conveyor belts, require custom conveyor rollers for specific operations, or need expert advice on selecting the right conveyor accessories for your facility, Jordan is your reliable consultant. For any inquiries or assistance with conveyor system optimization, Jordan is available to share his wealth of knowledge and experience. Feel free to reach out at any time for professional guidance on all matters related to conveyor rollers, belts, and accessories.