Comprehensive Conveyor Roller Size Chart & Selection Guide
Within the intricate systems of modern industries, conveyor rollers play a crucial role, significantly impacting overall productivity. Their importance is largely due to their ability to minimize friction, bear comprehensive loads, and ensure the seamless operation of conveyor belts. Deciding on the ideal conveyor roller isn’t a mere stroke of luck but a strategic process where the conveyor roller size chart serves as a comprehensive reference tool. This chart successfully guides the selection process towards choosing the right roller size, diameter, and material that fits specific conveyor system needs. By providing clear, standardized metrics, a conveyor roller size chart ensures the design compatibility between the conveyor belt and rollers, a critical aspect of achieving long-term operational efficiency. In essence, understanding and applying the information conveyed through a conveyor roller size chart is crucial to the engineering and maintenance of conveyor systems.
What is a Conveyor Roller Size Chart?
A conveyor roller size chart is a vital visual and downloadable tool that provides detailed insights into the various dimensions and specifications of conveyor rollers necessary for selecting the right components for a conveyor system. This chart outlines critical technical data including roller diameter, length, shaft size, and bearing capacity, which are imperative for ensuring the conveyor operates efficiently and effectively. By utilizing a conveyor roller size chart, engineers, maintenance professionals, and system designers can access a comprehensive reference to guide them through the selection process of conveyor rollers.
Dimensions and Measurements
A key component of the conveyor roller size chart is its detailed breakdown of dimensions and measurements for each roller type. This includes not only the visible measurements such as roller diameter and length but also the less apparent specifications like shaft diameter, which is pivotal for ensuring the roller can withstand the applied loads. Additionally, the chart clarifies how these dimensions influence the roller’s compatibility with the conveyor belt and its overall performance in material handling operations.
Key Terms in Conveyor Roller Sizing
To fully leverage the conveyor roller size chart, understanding the key terms related to conveyor roller specifications is crucial. These terms, which are detailed in the size chart, help clarify the selection process:
- Bearing Type: This refers to the type of bearing used within the roller, which can significantly affect the roller’s load-bearing capacity and operational smoothness.
- Roller Material: The construction material of the roller can vary from steel to plastic, depending on the application. The choice of material influences the roller’s durability, wear resistance, and performance in different environmental conditions.
- Tubing Thickness: This specifies the thickness of the roller’s wall, which is essential for understanding the roller’s ability to handle heavy loads or operate in demanding environments. Thicker tubing generally indicates a higher capacity for load bearing and resistance to deformation under stress.
Each of these terms plays a significant role in the practical application of the conveyor roller size chart. By familiarizing oneself with these terms and how they relate to the needs of their specific conveyor system, users can make more educated decisions on roller selection, ensuring optimal system performance and longevity.
Conveyor Roller Size Chart
In the complex world of material handling and logistics, the conveyor roller size chart stands as a fundamental tool for engineers and designers. It facilitates a deeper understanding of the various roller sizes available, giving special attention to commonly used diameters such as the 1-inch and 4-inch conveyor rollers. This chart is crucial for selecting the right roller size, ensuring operational efficiency, compatibility, and longevity of the conveyor system.
The Significance of 1-Inch Diameter Rollers
Among the varied options presented in the conveyor roller size chart, the 1-inch diameter conveyor rollers hold a unique position. They are particularly suited for lightweight applications and are predominantly used in industries where precision and delicacy are paramount. For instance, these rollers are a common sight in sectors like pharmaceuticals, food and beverages, and electronics manufacturing, where they handle items with care and minimum pressure.
The small diameter of these rollers allows for a tighter turn radius, making them ideal for compact spaces and conveyor systems requiring intricate routings. Furthermore, their reduced size contributes to lower system inertia, enabling faster start and stop actions without compromising the safety or integrity of the conveyed products.
Understanding the Role of 4-Inch Diameter Rollers
Conversely, 4-inch diameter conveyor rollers, as detailed in the conveyor roller size chart, are designed for heavier and more demanding applications. These rollers are the backbone of heavy industries such as mining, construction, and large-scale manufacturing. The larger diameter provides greater surface area contact with the conveyor belt, which translates to improved load distribution and the ability to handle heavier loads without significant deformation or wear.
The robustness of 4-inch rollers also means they are better suited for environments where abrasive materials are common or where high impact loads are expected. Their design ensures that, despite the harsh conditions, the rollers function efficiently, minimizing maintenance needs and operational downtimes.
Selecting the Ideal Idler Roller Size
When it comes to idler rollers, understanding their sizes, parameters, and the selection process is crucial. The conveyor roller size chart plays an essential role here, offering detailed specifications that help in choosing the correct size for your specific needs. Here’s a structured process for selecting the ideal idler roller size:
- Assessment of Conveyor Requirements:
- Material Weight: Determine the weight of materials the conveyor will carry. This influences the choice of roller size and material.
- Conveyor Belt Width: Identify the width of the conveyor belt to ensure the selected rollers are compatible and provide adequate support.
- Operational Speed: Consider the speed at which the conveyor will operate. This affects the choice of bearing type and roller design.
- Environmental Conditions: Evaluate the operational environment (e.g., temperature, presence of chemicals) to select rollers made of suitable materials.
- Matching Requirements with Roller Specifications:
- Utilize the conveyor roller size chart to find rollers that match the assessed conveyor requirements. Considerations include:
- Roller Diameter: Ensures the roller can support the weight and operational speed.
- Shaft Size: Compatible with the roller bearings and frame supports.
- Bearing Type: Chosen based on the load and speed requirements.
- Material: Selected based on environmental conditions and material handling needs.
- Utilize the conveyor roller size chart to find rollers that match the assessed conveyor requirements. Considerations include:
- Determining Idler Roller Spacing:
- The chart aids in deciding how far apart idler rollers should be spaced along the conveyor frame. This decision is based on:
- The maximum load the conveyor will carry.
- The type of material being conveyed (to prevent material sag between rollers).
- The width of the belt, as wider belts may require more support to prevent sagging.
- The chart aids in deciding how far apart idler rollers should be spaced along the conveyor frame. This decision is based on:
- Review and Selection:
- Review the specifications matched against the conveyor roller size chart.
- Select the idler roller size that best fits the operational requirements, ensuring optimal support, minimal wear, and efficient material handling.
- Final Verification:
- Double-check all parameters and selections with the conveyor design to ensure no aspect has been overlooked.
- Consider future operational changes or scaling that might influence the current selection.
By adopting this point-by-point approach, utilizing the detailed insights from the conveyor roller size chart, designers and engineers can optimize the selection of idler rollers, enhancing the conveyor system’s efficiency, reliability, and overall performance.
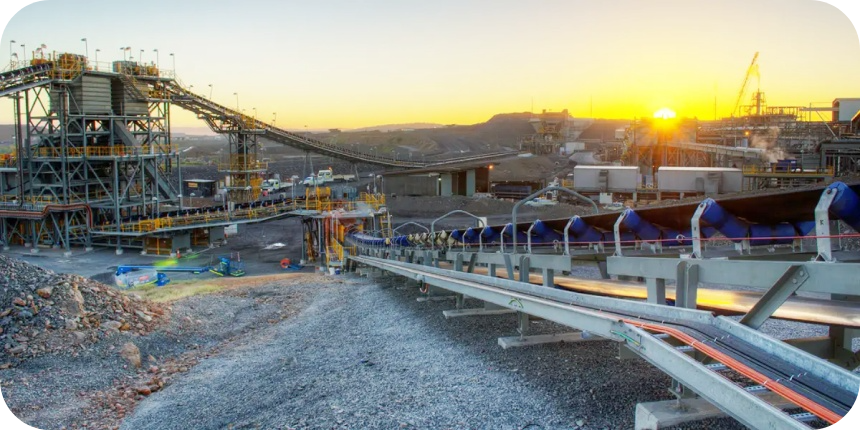
Conveyor Roller Size Chart: Choosing the Right Conveyor Roller Diameter
When it comes to optimizing a conveyor system, one of the critical decisions lies in selecting the correct roller diameter. A misalignment between roller size and belt width can lead to decreased operational efficiency and increased wear and tear on the system. The conveyor roller size chart serves as an indispensable tool for making informed decisions about roller diameter, based on belt widths and operational demands.
Roller Diameter for Different Belt Widths
The conveyor roller size chart provides detailed insights into the recommended roller diameters for various belt widths, a key consideration in the design and implementation of conveyor systems. This correlation ensures that the rollers adequately support the belt, preventing sagging and uneven wear that could disrupt operations and shorten the lifespan of both the belt and rollers.
While roller diameter requirements may vary based on specific material handling needs, some general rules apply:
- Conveyor belts that are 18 inches wide or less typically require rollers with a diameter of 1.5 inches or 2 inches.
- For belts that are 24 to 36 inches wide, roller diameters generally range from 2 inches to 3.5 inches.
- Wider conveyor belts, about 48 inches or more, commonly use rollers with a diameter of 4 inches or greater.
These dimensions, alongside more specific data, can be obtained from the conveyor roller size chart, ensuring each conveyor system is optimally supported by its rollers.
Impact on Belt Speed and Operational Efficiency
Choosing the right conveyor roller diameter based on the conveyor roller size chart significantly affects the belt speed and operational efficiency of a conveyor system.
- Influence on Belt Speed:
- Large Diameter Rollers: Rollers with a larger diameter enable higher belt speeds. Their size reduces the bending frequency of the belt around the roller, minimizing friction, and hence enabling smoother and quicker movement of the belt. This factor becomes particularly prevalent in high-speed conveyor systems where efficiency and productivity are crucial.
- Small Diameter Rollers: Conversely, rollers with smaller diameters can reduce belt speed due to increased friction. This characteristic, however, can be beneficial in conveyor systems involving delicate handling or where slow, precise movement of materials is required.
- Effect on Operational Efficiency:
- Reduced Maintenance Needs: Larger conveyor rollers significantly reduce wear and tear on the belt material due to lesser bends. This aspect minimizes the need for regular maintenance and replacement of the conveyor belt, saving time and resources thereby adding to operational efficiency.
- Improved Material Handling: Smaller roller diameters, while possibly reducing belt speed, can improve specific types of material handling. They allow for a tighter turning radius, thereby improving the belt routing, which can boost efficiency in settings with limited space or intricate layouts.
- Energy Cost Savings: Choosing the right roller diameter based on the conveyor roller size chart ensures appropriate alignment with the belt width. This alignment contributes to the smooth operation of the conveyor system, reducing energy waste, and potentially lowering electricity costs.
By accurately consulting the conveyor roller size chart and considering these impacts, businesses can make informed decisions to optimize their conveyor systems’ belt speed, operational efficiency, and cost-effectiveness.
Conveyor Roller Size Chart: Idler Roller Specifications
The conveyor roller size chart is not just a tool; it’s a comprehensive guide that significantly influences the selection and implementation of idler rollers in a conveyor system. Understanding the specifications of idler rollers—critical components that support the conveyor belt and materials being transported—is vital for efficiency, longevity, and overall performance of the system.
Idler Roller Specification and Its Relevance in Roller Selection
Idler roller specifications outline the technical dimensions and characteristics each roller must possess to function effectively within a conveyor setup. These specifications include the roller’s diameter, length, shaft size, bearing type, and material composition. When navigating through the conveyor roller size chart, these details lay the groundwork for selecting rollers that are precisely aligned with the system’s requirements, leading to optimized performance and reduced wear and tear.
Selecting idler rollers based on a thorough understanding of their specifications is crucial. The correct specifications ensure that the conveyor system operates smoothly under the expected load and environmental conditions, thus preventing premature failures and maintenance issues. It also ensures compatibility with the conveyor belt, reducing the risk of belt slippage or misalignment.
Relationship Between Roller Diameter and Idler Roller Specification
The diameter of an idler roller is a pivotal specification that directly influences several aspects of conveyor system design and operation. Let’s explore this relationship from three critical points:
- Load Support and Distribution:
The diameter of the roller plays a crucial role in how well the load is supported and distributed across the surface of the conveyor belt. Larger diameters generally offer better support for heavier loads, reducing the belt’s sag between rollers and decreasing stress on individual components. The conveyor roller size chart helps designers select a roller diameter that matches the load requirements, enhancing the system’s durability and reducing the need for frequent maintenance. - Conveyor Belt Life:
The life expectancy of the conveyor belt is also significantly affected by the choice of roller diameter. A roller that is too small in diameter can cause the belt to undergo unnecessary stress and flex, leading to increased wear and potential damage over time. Conversely, a roller with a larger diameter, as recommended by the conveyor roller size chart, can extend the belt’s life. It does so by ensuring a more gentle bending motion of the belt around the roller, which minimizes wear and tear. - Operational Efficiency and Energy Consumption:
The relationship between roller diameter and idler roller specification extends to operational efficiency and energy consumption. Larger diameter rollers can reduce the resistance encountered by the conveyor belt as it moves, leading to lower energy consumption and potentially lower operating costs. This optimized efficiency is particularly noticeable in systems where conveyors operate continuously over long periods. It’s the conveyor roller size chart that guides this crucial aspect of roller selection, ensuring that the system is as energy-efficient as possible.
Through the conveyor roller size chart, businesses can make informed decisions regarding idler roller specifications, particularly roller diameter. These choices are foundational to creating a conveyor system that is not only efficient and cost-effective but also durable and reliable over its operational lifespan.
Conveyor Roller Size Chart: Designing Your Conveyor System
When designing an efficient and dependable conveyor system, the careful consideration of various parameters is crucial. An essential component of this design process is the conveyor roller size chart, which guides the selection of the right roller size.
Key Considerations in Roller Conveyor Design
Designing a roller conveyor system requires knowledge of several core principles. Below is a table introducing three important knowledge points:
Importance of Selecting the Correct Roller Size in Design and Planning
The conveyor roller size chart plays a vital role in conveyor system design and planning, with its importance underscored by the following points:
- System Efficiency: The right roller size can enhance system efficiency by minimizing resistance and ensuring smooth material handling. The diameter and length of rollers, as specified by the conveyor roller size chart, can optimize belt alignment and speed.
- System Longevity: Using rollers with correct size can reduce wear and tear on the conveyor belt and other system components, thus extending their service life.
- Cost-Effectiveness: Proper roller sizing can lead to energy savings, reduced maintenance costs, and longer component lifespans, translating into overall cost-effectiveness of the system.
Integrating Conveyor Roller Size Charts into Overall System Design
The conveyor roller size chart is integrated into the overall system design by informing the selection of appropriate roller diameters, lengths, and material compositions. This, together with the provision of ideal capacity figures, directly influences the system design, from the power supply requirements to the physical dimensions of the system.
Using Design PDF Guides with Size Charts for Optimized Conveyor Planning
Design PDF Guides enrich the design process by integrating real-world specifications and standards with size charts. They allow engineers and system designers to reference industry-accepted specifications and provide context to various parameters on the conveyor roller size chart, fostering more effective planning and optimized system design.
Through the careful application of the conveyor roller size chart and sound knowledge of roller conveyor design principles, businesses can design an efficient and reliable conveyor system matching their specific operational needs.
Get in touch for personalized conveyor roller recommendations.
FAQs about Conveyor Roller Size Chart
The sizes of conveyor rollers can vary significantly depending on the application and the materials being transported. Generally, roller diameters can range from as small as 5/8 inches for lightweight applications to over 8 inches for heavy-duty applications. The lengths of these rollers can also vary, typically ranging from a few inches to several feet, to accommodate the width of the conveyor belt or the materials being handled. It’s important to reference a conveyor roller size chart for guidance on standard sizes and to ensure that the chosen rollers fit the specific needs of the conveyor system, including the weight and size of materials, the type of conveyor belt, and the overall design of the system.
Measuring a conveyor roller accurately is crucial for replacement or system design purposes. To measure a conveyor roller, start by measuring the diameter of the roller, which is the distance across the roller’s center in a straight line. This can be done using a caliper or a tape measure. Next, measure the length of the roller, which is the distance from one end of the roller to the other, including any endcaps or flanges; this length should match the width of the conveyor belt or the frame slot it fits into. Lastly, measure the shaft or bore size, typically found at the center of the roller. This measurement is vital for ensuring the roller fits onto its axis or stand. Always measure twice to ensure accuracy, and refer to the conveyor system’s specifications when replacing or adding rollers.
Choosing the right conveyor rollers involves several key considerations to ensure system efficacy and longevity. First, consider the load the rollers will need to support, which includes not just the weight of the materials being conveyed, but also the weight of the conveyor belt itself. This determines the material and diameter of the rollers required: heavier loads generally necessitate larger, more robust rollers. Next, consider the environment in which the conveyor will operate; factors such as exposure to chemicals, water, or extreme temperatures can dictate the need for specialized materials or coatings. Additionally, the speed at which the conveyor will operate and the type of materials being conveyed (e.g., abrasive, delicate) can affect roller material and design choices. It’s advisable to consult a conveyor roller size chart for guidance on dimensions and to engage with suppliers or manufacturers who can provide insights based on experience with similar applications.
The diameter of a conveyor roller is a critical specification that directly influences the conveyor system’s performance and compatibility with the conveyor belt and the materials being transported. Roller diameters can range broadly, typically from 5/8 inches to 8 inches or more, to accommodate different applications and load requirements. The chosen diameter affects the conveyor’s load capacity, belt longevity, and operational efficiency. For instance, larger diameters are better suited for heavier loads and can help reduce the belt’s wear and prolong its life by minimizing the belt’s curvature around the roller. The specific diameter needed for a particular application can be determined by considering the weight of the materials to be conveyed, the type of conveyor belt used, and the overall design of the conveyor system. Consulting a conveyor roller size chart can provide a good starting point for selecting the appropriate roller diameter.
Last Updated on July 16, 2024 by Jordan Smith
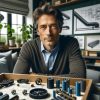
Jordan Smith, a seasoned professional with over 20 years of experience in the conveyor system industry. Jordan’s expertise lies in providing comprehensive solutions for conveyor rollers, belts, and accessories, catering to a wide range of industrial needs. From initial design and configuration to installation and meticulous troubleshooting, Jordan is adept at handling all aspects of conveyor system management. Whether you’re looking to upgrade your production line with efficient conveyor belts, require custom conveyor rollers for specific operations, or need expert advice on selecting the right conveyor accessories for your facility, Jordan is your reliable consultant. For any inquiries or assistance with conveyor system optimization, Jordan is available to share his wealth of knowledge and experience. Feel free to reach out at any time for professional guidance on all matters related to conveyor rollers, belts, and accessories.