Conveyor Roller Stands: Essential Workflow Tools
Conveyor roller stands are pivotal components in the movement and management of materials across various industrial and manufacturing settings. These stands serve as critical support systems, enabling the smooth transfer of items along production lines by supporting and stabilizing conveyor belts or rollers. Their use spans multiple industries, highlighting their significance in streamlining operations and enhancing efficiency in production environments. By reducing manual handling, roller conveyor stands not only improve productivity but also increase workplace safety, making them indispensable in modern material handling processes.
Types of Conveyor Roller Stands
Conveyor roller stands are a fundamental element in various material handling sectors, designed to optimize workflow and efficiency. These stands vary significantly in terms of design, capacity, and durability, tailored to meet different industrial needs. Here, we explore the two primary categories: Standard Roller Conveyor Stands and Heavy-Duty roller stand conveyor, each serving unique functions and applications.
Standard Roller Conveyor Stands
Standard roller conveyor stands are essential for efficiently managing lightweight to medium-weight materials in various industrial settings. These stands are particularly favored for their:
- Capacity and Use: Ideal for handling items weighing up to 500 pounds. Commonly employed in industries such as electronic assembly and light manufacturing where delicate handling is crucial.
- Design Flexibility: These stands are adjustable, making them suitable for different operational heights and setups. Their mobility allows for easy relocation, adapting to various workspace layouts.
- Material and Build: Constructed from metals like aluminum and light-gauge steel, they combine durability with lightweight properties, facilitating easy manipulation and integration into existing systems.
- Operational Applications: Frequent use in sectors like packaging, where products need steady movement along the assembly line without heavy-duty requirements.
- Feature Rich: Some models offer lockable rollers to secure the stand in place during operations, and others may fold for compact storage, enhancing space efficiency.
- Ease of Integration: Can be used as independent units or as part of larger conveyor systems, providing flexibility in design and utility.
- Maintenance Needs: Typically low maintenance, thanks to their simple mechanical design which avoids the complexity and wear associated with heavier duty models.
- Cost Benefits: Provides a cost-effective solution for businesses that require efficient material handling without the robustness of industrial-grade equipment.
Heavy-Duty Conveyor Roller Stands
Heavy-duty conveyor roller stands are designed to withstand the rigors of more intensive industrial applications. They are characterized by:
- Sturdy Construction: Built to support significant weights, often exceeding 1,000 pounds. Their construction involves heavy-duty steel that can handle the stress of constant, heavy loads.
- Durability Features: These stands feature larger, industrial-strength rollers and enhanced bearings that ensure durability and a longer lifespan even under strenuous use.
- Base and Frame Design: The stability is enhanced by wider bases and solid frames that maintain balance and prevent shifts during operation with heavy items.
- Resistance to Harsh Conditions: Equipped with coatings that resist environmental challenges like moisture, chemicals, and extreme temperatures, making them suitable for tough industrial settings.
- Adjustability and Versatility: While they are robust, these stands still offer adjustability in height and width to accommodate various sizes and types of materials.
- Application Range: Commonly used in sectors such as construction and heavy manufacturing, where materials like metal beams, large automotive parts, and heavy machinery components need transport.
- Precision and Efficiency: High-quality bearings and design precision reduce the need for frequent maintenance and ensure smooth operations.
- Investment Worth: Though more costly upfront, their reliability and effectiveness in high-demand environments make them a valuable long-term investment for businesses.
Features of Conveyor Roller Stands
Conveyor roller stands are engineered to support the dynamic needs of modern industrial operations, enhancing both efficiency and safety. These stands are designed with key features that address adjustability, flexibility, and material quality to meet various operational demands. Below, we delve into the specifics of these features, emphasizing their critical role in industrial applications.
Adjustability and Flexibility
The adjustability and flexibility of roller conveyor stand are critical for adapting to various industrial tasks:
- Height Adjustability: Stands can be adjusted to different heights, making them versatile for operations that involve varying material sizes or require ergonomic adjustments for operator comfort.
- Width Adjustability: This feature enables the stands to accommodate materials of differing widths, which is essential for processes that handle a wide range of product sizes.
- Angle Adjustments: Adjustable angles allow the stands to align more effectively with the input and output of other machinery, optimizing the flow of materials.
- Portability: Equipped with casters or folding mechanisms, these stands can be easily relocated to different parts of a facility as needed, enhancing workflow flexibility.
- Locking Mechanisms: Stability during operations is ensured through locking mechanisms that prevent unwanted movement of the stand, crucial for maintaining precision and safety.
- Modular Designs: Modular systems allow for quick assembly and reconfiguration, supporting dynamic production environments that frequently change layouts.
- Scalability: Easily scalable, these stands can be integrated into larger systems for expanded operations or reduced for smaller, more focused tasks.
- Customizability: Offers customization options such as the choice of roller material, stand size, and additional features like side guides, meeting specific operational requirements.
Material and Build Quality
Material choice and construction quality are essential for the durability and functionality of conveyor roller bracket:
- Heavy Gauge Steel: Utilized for its strength and durability, heavy gauge steel can withstand the rigors of heavy loads and continuous operation without warping or bending.
- Ball Bearing Rollers: These rollers ensure smooth and efficient transfer of materials across the stand, reducing the physical strain on the machinery and minimizing maintenance needs.
- Aluminum Construction: Provides a lightweight yet robust alternative, suitable for applications where ease of movement and resistance to corrosion are important.
- Stainless Steel Options: Ideal for environments that are prone to moisture or chemical exposure, stainless steel resists corrosion and maintains its integrity over time.
- Powder Coating: Applied as a protective and decorative finish, powder coatings enhance the stand’s resistance to scratches, chipping, and fading.
- Reinforced Structures: Key stress points may be reinforced to prevent structural failure under load, ensuring longevity and reliability.
- Sealed Bearings: Protect the internal components from dust and particulate matter, crucial in maintaining operational efficiency in environments with high levels of debris.
- Eco-Friendly Materials: Some stands are made using sustainable materials or methods, appealing to companies committed to reducing their environmental impact.
These features collectively ensure that conveyor roller stands can effectively meet the diverse needs of modern industries, providing reliable and adaptable support for various material handling tasks.
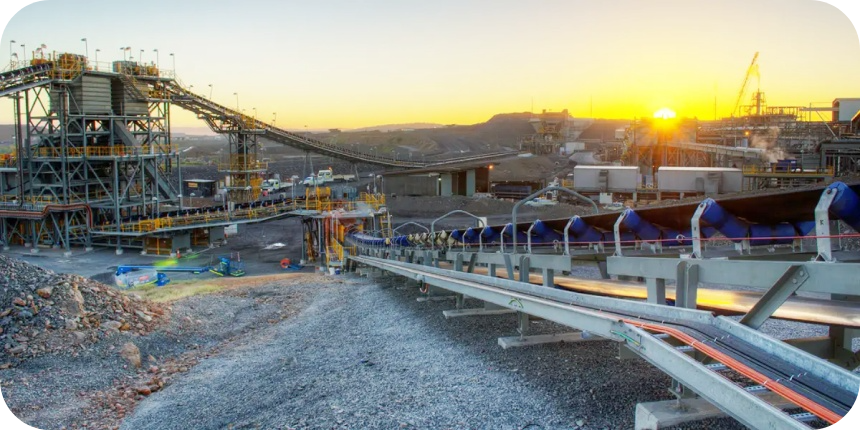
Specialized Conveyor Roller Stands
Specialized conveyor roller stands are designed to meet specific industrial needs, enhancing efficiency and functionality in material handling processes. These stands incorporate advanced features that cater to specialized applications, offering greater precision, durability, and adaptability. We will explore two prominent types: Ball Bearing Roller Stands and ToughBuilt Roller Stands, which are recognized for their unique capabilities and construction attributes.
Ball Bearing Roller Stands
Ball Bearing Roller Stands are crucial for their role in facilitating smooth, multidirectional movement of materials within various settings. These stands are particularly valued for:
- Smoothness and Efficiency: They provide seamless movement, minimizing effort and reducing wear on the system.
- Handling Capabilities: Ideal for scenarios where goods need to change directions easily without manual intervention.
- Load Support: Ball bearings enhance the load-bearing capacity, allowing for the handling of heavier objects with ease.
- Longevity and Maintenance: Designed to last, these stands require less frequent maintenance due to their robust construction.
- Operational Versatility: Their ability to operate under different environmental conditions makes them versatile.
- Energy Conservation: The efficiency of ball bearings translates into lower energy consumption during operations.
- Quiet Operation: Reduces operational noise, a critical factor in many work environments.
- Accuracy in Placement: Precisely positions materials, which is vital for automated processes.
ToughBuilt Roller Stands
ToughBuilt Roller Stands are known for their exceptional strength and adaptability, making them suitable for rigorous industrial use:
- Robust Construction: Designed to endure tough industrial environments with the ability to handle significant weight and pressure.
- Functional Flexibility: Their adjustable features cater to a broad range of industrial tasks, enhancing usability across various projects.
- Mobility and Storage: Easy to transport and store, which is beneficial in multi-use spaces or where space is at a premium.
- Enhanced Stability: Equipped with mechanisms that ensure a stable base, crucial for maintaining safety and accuracy.
- Customization Options: Offers add-ons and attachments that extend their functionality, suitable for diverse operational needs.
- Material Quality: Uses high-grade materials that are not only durable but also resistant to environmental challenges like rust and corrosion.
Buying Guide: Conveyor Roller Stands for Sale
When looking to purchase conveyor roller stands, several factors should be considered to ensure that you choose the right equipment for your specific needs. Here’s what to consider:
- Capacity: Evaluate the weight capacity each stand can handle to match it with your operational requirements.
- Size: Consider the dimensions of the stands in relation to the workspace and the size of the materials they need to support.
- Material: Choose materials that suit your environment—whether it’s corrosion-resistant stainless steel for wet conditions or durable steel for heavy-duty use.
- Durability: Look for robust construction that can withstand the rigors of your operational demands.
- Flexibility: Adjustable features such as height and width can accommodate various tasks.
- Portability: Consider if you need stands that can be easily moved around your facility.
- Ease of Assembly: Check if the stand requires complex assembly or if it comes ready to use.
- Cost: Ensure the stand fits within your budget while still meeting your quality and durability needs.
For those considering used conveyor roller stand:
- Reputable Suppliers: Purchase from well-known and trustworthy suppliers to ensure quality and service.
- Condition Check: Inspect the condition of the rollers, bearings, and frame for wear and tear.
- Warranty: Look for options that still carry a warranty or guarantee.
- Maintenance Records: Ask for maintenance logs to understand the history of the stand.
- Operational Testing: If possible, test the stand under load to see it in operation.
- Refurbished Options: Consider refurbished stands which can offer like-new quality at a lower price.
- Availability of Parts: Ensure that replacement parts are readily available.
- Return Policy: Check if there is a return policy in case the stand does not meet expectations post-purchase.
- Comparative Shopping: Compare multiple options for price and condition to find the best deal.
When looking for bracket roller conveyor, whether new or used, paying attention to these details can greatly influence the efficiency and productivity of your operations.
Get Detailed Information About OurConveyor roller stands.
FAQs about Conveyor Roller Stands
Stand rollers, commonly part of roller stands, vary widely in size. They are designed to support and convey materials and can range from small to large depending on the intended load and the width of the material being handled. Typically, the roller diameter can start from as small as one inch for light applications, scaling up to several inches for industrial use. The length of the roller usually matches the width of the stand, which can be adjusted to accommodate different material sizes.
The standard size of a conveyor roller depends on the application and the system requirements. In general, conveyor rollers can range in diameter from about 20 mm for light applications to over 100 mm for heavy industrial environments. The width of the rollers is usually designed to match the width of the conveyor belt or frame, and can vary from a few inches to several feet, based on the needs of the material handling system.
A roller stand is used primarily to support materials as they are being fed into or moved through machinery. Commonly found in woodworking, metalworking, and material handling sectors, roller stands help to stabilize long pieces of material that extend beyond the worktable or sawbench. This support is crucial not only for safety but also for precision in cutting, drilling, or processing materials, ensuring that operations run smoothly and efficiently.
Conveyor rollers come in several types, each designed for specific load types and operational environments:
Gravity Rollers: Operate by the force of gravity and are used for light to medium loads.
Driven Rollers: Powered by motors or belts and can handle heavier loads.
Grooved Rollers: Designed with grooves that interface with belts or chains for driven applications.
Impact Rollers: Positioned at loading points to absorb the impact of falling materials.
Tapered Rollers: Used in curved sections of conveyors to maintain the alignment of the belt. Each type plays an essential role in the functionality of conveyor systems, depending on the industrial application and the nature of the materials being transported.
Last Updated on July 30, 2024 by Jordan Smith
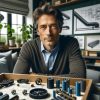
Jordan Smith, a seasoned professional with over 20 years of experience in the conveyor system industry. Jordan’s expertise lies in providing comprehensive solutions for conveyor rollers, belts, and accessories, catering to a wide range of industrial needs. From initial design and configuration to installation and meticulous troubleshooting, Jordan is adept at handling all aspects of conveyor system management. Whether you’re looking to upgrade your production line with efficient conveyor belts, require custom conveyor rollers for specific operations, or need expert advice on selecting the right conveyor accessories for your facility, Jordan is your reliable consultant. For any inquiries or assistance with conveyor system optimization, Jordan is available to share his wealth of knowledge and experience. Feel free to reach out at any time for professional guidance on all matters related to conveyor rollers, belts, and accessories.