Enhanced Durability with Conveyor Roller with Bracket Mount
Conveyor roller with bracket mounts are crucial components widely used across various industries to facilitate the movement of goods and materials efficiently. These brackets play a pivotal role in securing conveyor rollers, which are essential for the seamless operation of conveyor systems. The types of brackets available range from lightweight options for less demanding applications to heavy-duty brackets designed for robust industrial use. Each type offers specific features tailored to different operational requirements, ensuring versatility and reliability in transporting goods within facilities.
Types of Conveyor Roller with Bracket Mount
Conveyor roller with bracket mounts are essential components in the design and functionality of conveyor systems. These brackets play a key role in securing the conveyor rollers, which in turn support and move loads across a facility. The right choice of bracket depends on several factors including the environment, load requirements, and the specific application needs of the system. In this section, we’ll explore the various types of conveyor roller brackets mount available, including standard, heavy-duty, and used brackets, each tailored for different operational demands.
Standard Conveyor Roller with Bracket Mount
Standard conveyor roller with bracket mount are essential for typical operational setups, providing stability and precision in handling systems.
- Description and General Applications:
- Essential in automated material handling to reduce manual labor.
- Commonly used in logistics to streamline package sorting and distribution.
- Integral to light-industrial applications such as electronics assembly.
- Support smooth operation in printing and paper industries.
- Used in food processing for handling packaged goods gently.
- Vital in pharmaceutical manufacturing for transporting sensitive materials.
- Employed in textile industries for moving fabrics.
- Utilized in auto parts distribution centers.
- Necessary in furniture manufacturing for assembly lines.
- Materials Typically Used:
- Galvanized steel for enhanced corrosion resistance.
- Stainless steel for superior strength and hygiene.
- Aluminum for its light weight and corrosion resistance.
- Carbon steel for its cost-effectiveness and durability.
- Powder-coated finishes to improve aesthetics and extra protection.
- Nylon and reinforced plastics for quieter operations.
- Brass or bronze in explosive environments to prevent sparking.
Heavy Duty Conveyor Roller with Bracket Mount
Heavy duty brackets are designed to meet the rigorous demands of industrial environments, ensuring longevity and reliability.
- Characteristics and Benefits:
- Built to handle high-volume and heavy load operations.
- Provides stability and security in harsh working conditions.
- Tailored for high-impact and high-abrasion processes.
- Often feature enhancements for anti-vibration.
- Equipped with specialized coatings to resist chemicals and heat.
- Designed to operate smoothly under extreme temperature variations.
- Crafted to maintain performance during continuous operations.
- Configurations available to suit specialized industrial applications.
- Manufactured to reduce operational downtime and maintenance costs.
- Comparison with Standard Brackets:
- Superior load handling and weight capacity.
- More durable under industrial stresses and strains.
- Higher resistance to environmental factors like dirt and moisture.
- Crafted with tougher materials to withstand wear and tear.
- Adapted to more demanding mechanical and thermal conditions.
- Offer enhanced safety features to protect workers and machinery.
Used Conveyor Roller with Bracket Mount
Used brackets provide a practical option for budget-conscious operations without compromising quality.
- Advantages:
- Significantly lower costs than new equipment.
- Immediate availability can drastically reduce project timelines.
- Previous usage proves effectiveness and resilience.
- Some options come partially refurbished, extending their usable life.
- Flexibility in adapting to existing systems with minor adjustments.
- Eco-friendly choice by minimizing waste and reusing resources.
- Ideal for supplementary or backup systems in large operations.
- Provides an economical solution for expanding existing lines.
- Supporting sustainable practices within the industry.
- Considerations:
- Thorough inspection to assess mechanical wear and overall condition.
- Compatibility with existing roller systems is crucial.
- Verification of the brackets’ load-bearing capacity.
- Potential for hidden costs in repairs and modifications.
- Sourcing of compatible parts for maintenance or repair.
- Examination of previous usage environments to assess potential degradation.
- Ensuring compliance with current safety standards.
- Clarifying terms of sale, warranties, and returns.
- Estimating the long-term operational costs and potential downtime.
This detailed outline provides a deeper insight into the different types of conveyor roller with bracket mount, emphasizing their applications, benefits, and considerations to aid in informed decision-making for businesses looking to invest in or upgrade their conveyor systems.
Components and Accessories for Conveyor Roller with Bracket Mount
Conveyor systems rely on precision-engineered components to efficiently transport materials within various industrial environments. This section delves into the critical roles and specifications of conveyor rollers and their parts, essential for maintaining the functionality and longevity of conveyor systems.
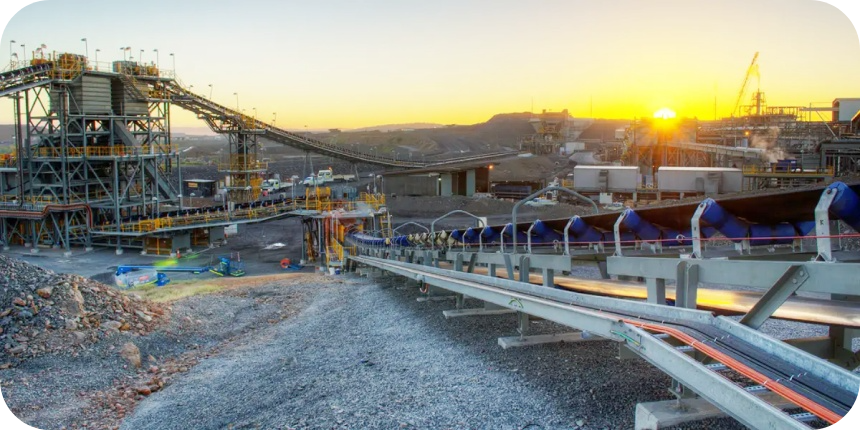
Conveyor Rollers
Conveyor rollers are pivotal in facilitating the smooth and efficient movement of goods. They enable the automated transportation of materials, significantly reducing manual labor and enhancing workflow efficiency. Designed to handle everything from small, delicate items to large, heavy loads, their role in optimizing operational processes across industries cannot be overstated.
- Types of Rollers:
- Heavy Duty Rollers: Engineered to handle substantial loads, these rollers are crucial in industries such as mining and construction where robustness is key.
- Wide Rollers: These rollers are designed to support larger items, ensuring stability and balance in the transport of wide loads.
- Small Diameter Rollers: Perfect for confined spaces, these rollers handle smaller loads and operate efficiently in restricted areas.
- Specialized Rollers: Includes options like grooved for belt traction, impact for absorbing shocks, tapered for curved paths, and rubber-coated for delicate handling.
- Materials and Environmental Suitability:
- Steel Rollers: Known for their strength and durability, ideal for heavy-duty applications.
- Aluminum Rollers: Offer a lightweight alternative, beneficial in corrosion-sensitive environments.
- Plastic and Nylon Rollers: These provide a quieter operation, suitable for light-duty tasks where cost efficiency is key.
- Stainless Steel Rollers: Best for applications requiring cleanliness and resistance to corrosion, such as in food processing or pharmaceuticals.
Conveyor Roller Parts
The efficiency of a conveyor system heavily depends on the quality and regular maintenance of its parts. Maintaining these components ensures that the system operates smoothly, reduces downtime, and extends the life of the equipment. Regular checks and timely updates of parts like bearings, shafts, and rollers are crucial for the system’s reliability and overall performance.
- Key Components:
- Bearings: Facilitate smooth roller movement, critical for the consistent flow of materials.
- Shafts and Mounting Brackets: Provide structural support and alignment, essential for the stability of the conveyor rollers.
- Sprockets and Motorized Pulleys: Drive the movement of the conveyor, crucial for automated systems.
- Spacer Tubes and End Caps: Help maintain the correct positioning and integrity of the rollers.
- Maintenance Tips:
- Regular Lubrication: Necessary to reduce friction and wear, extending the lifespan of moving parts.
- Alignment Checks: Crucial for preventing misalignments that can lead to operational disruptions.
- Timely Replacement of Worn Parts: Ensures that the system remains efficient and reduces downtime.
- Routine Cleaning: Maintains optimal performance and prevents material build-up that could affect the system’s functionality.
Understanding these components and their maintenance will not only help in extending the life of the conveyor system but also optimize its performance and efficiency.
Installation and Maintenance Tips for Conveyor Roller with Bracket Mount
Conveyor systems are essential components in many industrial settings, facilitating the efficient movement of goods across various stages of production or packaging. A crucial part of these systems is the conveyor roller with bracket mount, which support and align the rollers that transport materials. Proper installation and regular maintenance of these brackets are key to maximizing the conveyor’s performance and longevity. This guide provides comprehensive steps and tips for both installing and maintaining these brackets to ensure they function effectively and last longer.
Installation Guide
Introduction: Installing conveyor roller with bracket mount correctly is crucial for the optimal functioning of the conveyor system. Here’s a detailed step-by-step guide to ensure a precise and secure installation.
- Assess the Conveyor Layout: Begin by reviewing the entire layout of the conveyor system. This helps in identifying the most effective locations for the brackets, ensuring they support the rollers adequately across the entire line.
- Gather Necessary Tools: Prepare all required tools beforehand. Typically, this includes drills for creating pilot holes, bolts and nuts for securing the brackets, and measuring tapes for precise placement.
- Mark the Installation Points: With a permanent marker, clearly mark the points on the conveyor frame where each bracket will be installed. This ensures accuracy in alignment during the actual mounting.
- Position the Brackets: Align the mounting brackets with the pre-marked spots on the frame. It’s crucial that they are perfectly positioned to maintain the alignment of the rollers.
- Secure the Brackets: Attach each bracket using the appropriate fasteners. Tighten them securely to prevent any movement that could misalign the rollers or disrupt the conveyor’s operation.
- Install the Rollers: Carefully place the rollers into the brackets. Ensure each roller is correctly seated and secured to prevent them from dislodging during operation.
- Check Alignment: Double-check the alignment of all installed rollers. They should be parallel to each other and the conveyor frame to guarantee smooth material flow.
- Test the Installation: Run the conveyor system to ensure everything is installed correctly. Look for any unusual vibrations or noise, which could indicate misalignment or loose components.
- Perform a Safety Check: Finally, conduct a comprehensive safety check. Verify that all components are securely fastened and the conveyor area is clear of any tools or loose parts.
Maintenance Advice
Introduction: Regular maintenance is essential to keep the conveyor system running efficiently and to prolong the lifespan of its components, including the roller mounting brackets. Here are detailed tips to help you maintain these components effectively.
- Regular Cleaning: Dust, debris, and other particulates can accumulate on the rollers and brackets, leading to increased wear and tear. Clean these parts regularly to prevent buildup.
- Lubrication: Apply lubrication to all moving parts involved with the brackets and rollers. This reduces friction, which can cause premature wear and energy inefficiency.
- Tighten Fasteners: Over time, vibrations from the conveyor operation can loosen fasteners. Check and tighten these periodically to ensure the brackets remain stable.
- Inspect for Wear: Regularly inspect the brackets and rollers for any signs of damage, such as cracks or excessive wear. Replace damaged parts promptly to avoid further issues.
- Alignment Checks: Misalignment can lead to uneven wear and inefficiencies. Regularly check and adjust the alignment of the rollers.
- Rust Prevention: If the conveyor operates in a damp or corrosive environment, apply rust-preventive treatments to protect metal components from corrosion.
- Update Maintenance Records: Maintain detailed logs of all maintenance procedures. This helps in tracking the performance over time and planning future maintenance schedules.
- Train Staff: Ensure that all personnel involved in the maintenance and operation of the conveyor are well-trained in these procedures.
By adhering to these installation and maintenance guidelines, the efficiency and lifespan of conveyor roller with bracket mount can be significantly enhanced, supporting the overall performance and reliability of the conveyor system.
Fill Out the Inquiry Form for Conveyor Roller Availability and Pricing.
Last Updated on July 30, 2024 by Jordan Smith
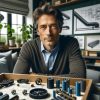
Jordan Smith, a seasoned professional with over 20 years of experience in the conveyor system industry. Jordan’s expertise lies in providing comprehensive solutions for conveyor rollers, belts, and accessories, catering to a wide range of industrial needs. From initial design and configuration to installation and meticulous troubleshooting, Jordan is adept at handling all aspects of conveyor system management. Whether you’re looking to upgrade your production line with efficient conveyor belts, require custom conveyor rollers for specific operations, or need expert advice on selecting the right conveyor accessories for your facility, Jordan is your reliable consultant. For any inquiries or assistance with conveyor system optimization, Jordan is available to share his wealth of knowledge and experience. Feel free to reach out at any time for professional guidance on all matters related to conveyor rollers, belts, and accessories.