Top Picks: Conveyor Rollers for Sale – Essential Info
In industries ranging from manufacturing to warehousing, conveyor rollers play an indispensable role in facilitating the smooth and efficient movement of goods. As the backbone of conveyor systems, these rollers support and move loads of various sizes and weights along a fixed path, minimizing manual handling and enhancing operational efficiency. The quest for high-quality conveyor rollers for sale highlights the critical importance of selecting the right type of rollers to meet specific application needs. Whether for light-duty tasks or heavy-duty industrial use, choosing the appropriate conveyor rollers can significantly impact the productivity and longevity of the conveyor system. Consequently, understanding the different types of conveyor rollers available in the market, their features, and their suitability for various applications becomes a pivotal decision-making factor for businesses looking to optimize their operations and reduce downtime.
What is Conveyor Rollers: Key to Finding the Best Conveyor Rollers for Sale
Conveyor rollers are fundamental components of material handling systems, designed to facilitate the smooth and efficient transport of goods across short or long distances within a facility. These cylindrical devices, often mounted within the frame of a conveyor system, use the principle of rotation to move products with ease, minimizing the need for manual labor and enhancing workflow efficiency. The hunt for roller conveyor for sale underscores the importance of integrating these pivotal elements into various sectors, including manufacturing, logistics, and distribution, among others.
Types of Conveyor Rollers and Their Functions
When searching for conveyor rollers for sale, it’s crucial to understand the different types available to ensure the selection meets the specific needs of your application. Here are three primary types of conveyor rollers, each designed for particular use cases:
- Gravity Conveyor Rollers: Operate without an external power source, relying on gravity and manual force to move items. These rollers are ideal for light to medium loads and are commonly used in picking, packing, and assembly lines. They are cost-effective and easy to install and maintain.
- Motorized Conveyor Rollers: Equipped with internal motors, these rollers automate the movement of goods, providing consistent and controllable flow. They are suitable for heavier loads and applications requiring precise speed control, such as in food processing and heavy manufacturing environments.
- Heavy-duty Conveyor Rollers: Designed to handle extremely heavy loads, these rollers are built with robust materials and can often withstand harsh industrial conditions. Heavy-duty rollers are essential in sectors like mining, construction, and metalworking, where durability and reliability are paramount.
Examples of Conveyor Roller Applications
- Gravity Rollers in retail warehouses facilitate the manual sorting and distribution of goods to different delivery trucks.
- Motorized Rollers in baggage handling systems at airports ensure smooth and consistent movement of luggage to and from aircraft.
- Heavy-duty Rollers in steel manufacturing plants transport heavy metal sheets through the production line.
The exploration for conveyor rollers for sale should begin with a thorough understanding of these types, their functionalities, and how they align with the operational needs. Whether upgrading an existing system or integrating a new conveyor setup, selecting the right conveyor rollers is a strategic decision that influences efficiency, safety, and productivity in any material handling operation.
How to Choose Replacement Conveyor Rollers: Enhancing Your Search for Conveyor Rollers for Sale
Choosing the right replacement conveyor rollers is a critical task that can significantly impact the efficiency and longevity of your conveyor system. When searching for conveyor rollers for sale for replacement purposes, several key factors must be considered to ensure compatibility, performance, and durability. Here are six essential aspects to evaluate:
- Load Capacity: Assess the maximum weight the rollers need to support. Ensuring the rollers can handle the load is crucial to prevent failures and maintain operational efficiency.
- Roller Material and Coating: Different materials and coatings offer varying levels of durability, friction, and resistance to environmental factors. Choose a material and coating that suit the nature of the goods being transported and the environment in which they operate.
- Roller Diameter and Length: The size of the roller affects its ability to handle loads and the types of items it can convey. It’s essential to match the diameter and length to the requirements of your system to ensure smooth operation.
- Bearing Type: Bearings play a significant role in the performance and maintenance needs of conveyor rollers. Consider the type of bearing that best suits your operational speed, load capacity, and maintenance capabilities.
- Shaft Attachment: The method of attaching the roller to the conveyor frame—whether through a spring-loaded, fixed, or threaded shaft—affects the ease of installation and maintenance. Choose an attachment method that aligns with your system’s design and your maintenance practices.
- Environmental Conditions: Factors such as exposure to moisture, chemicals, or extreme temperatures can affect the performance and lifespan of conveyor rollers. Select rollers with materials and construction designed to withstand your specific environmental conditions.
Measuring and Sizing for Replacement
Accurate measurement and sizing are fundamental when purchasing roller conveyor for sale for replacement to ensure seamless integration with your existing system. Follow these steps:
- Determine the Roller Diameter: Measure the outer diameter of the roller. This dimension influences the roller’s capacity to support loads and affects the speed at which items can be moved.
- Measure the Roller Length: Measure the length of the roller between the frames where it sits. This ensures the roller fits properly within the conveyor system without causing disruptions.
- Identify the Shaft Size: Measure the diameter and length of the shaft to ensure the replacement roller can be securely attached to the conveyor frame.
- Assess the Bearing Type and Size: Identify the bearing type and size used in the current rollers to maintain performance consistency with replacements.
Taking the time to accurately assess and measure for replacement conveyor rollers ensures that the new rollers will fit, perform as expected, and last, thereby enhancing the overall efficiency of your conveyor system. Whether upgrading individual components or undertaking a comprehensive overhaul, integrating the right conveyor rollers for sale into your system is a step towards optimized operation and reduced downtime.
Heavy Duty Conveyor Rollers for Industrial Use: Optimal Performance with Conveyor Rollers for Sale
In the realm of material handling, heavy-duty conveyor rollers stand out as the backbone of industrial applications, where durability and the ability to handle extreme conditions are non-negotiable. When sourcing conveyor rollers for sale, selecting heavy-duty options offers a plethora of advantages, crucial for maintaining high efficiency and reliability in challenging environments.
Advantages of Heavy-Duty Rollers in Industrial Settings
- Enhanced Durability: Designed to withstand heavy loads and continuous operation, heavy-duty rollers have a longer lifespan, reducing the need for frequent replacements.
- Increased Load Capacity: Capable of handling substantial weights, these rollers are essential for industries like mining, construction, and metal processing, where bulk materials and heavy products are the norms.
- Resistance to Harsh Environments: Constructed with materials that can withstand exposure to corrosive substances, extreme temperatures, and abrasive conditions, making them ideal for use in harsh industrial settings.
- Reduced Maintenance Needs: The robust design and construction of heavy-duty rollers minimize wear and tear, leading to lower maintenance costs and less downtime.
- Versatility: Suitable for a wide range of applications, heavy-duty rollers can be customized with various coatings and materials to meet specific operational requirements.
- Improved Safety: Their strength and reliability contribute to safer operations, reducing the risk of accidents related to equipment failure.
Overview of Heavy-Duty Gravity Roller Conveyors and Industrial Rollers
When exploring conveyor rollers for sale for industrial use, heavy-duty gravity roller conveyors are a significant consideration. These systems leverage gravity to move items, eliminating the need for a power source, which can be particularly beneficial in environments where electrical use is restricted or where simplicity is valued.
Heavy-Duty Gravity Roller Conveyors are characterized by their robust construction, using thicker tubes and larger bearings, designed to carry heavier loads efficiently. They are commonly used for moving large containers, pallets, and other heavy items across flat or slightly inclined paths.
Industrial Rollers, on the other hand, include both gravity and powered options but are built to meet the rigorous demands of industrial applications. These might feature specialized coatings, such as rubber or polyurethane, for added grip and noise reduction, or be constructed from stainless steel or other materials that offer resistance to chemicals and temperature extremes.
Selecting the right conveyor rollers for sale requires a deep understanding of the operational demands and environmental conditions of the industrial setting. Whether for mining, construction, heavy manufacturing, or any sector where durability and performance under pressure are required, heavy-duty conveyor rollers provide the reliability and efficiency necessary for optimal operation. Their investment is justified by their performance and the value they add to the industrial processes, making them an essential component of any robust material handling system.
Where to Find Conveyor Rollers for Sale: Your Comprehensive Guide
When it comes to enhancing or repairing your conveyor system, finding the right roller conveyors for sale can seem like a daunting task. However, with a strategic approach, you can navigate the market to find the best options available, whether through online marketplaces, direct suppliers, or local searches. Here’s a breakdown of where to start your search and how to find the best deals and quality for your specific needs.
Online Marketplaces vs. Direct Suppliers
Online Marketplaces: Platforms like eBay offer a wide range of roller conveyor for sale, from used options for budget-conscious buyers to brand-new, high-spec models for those requiring specific features. The advantage of online marketplaces is the breadth of choice and the potential for competitive pricing. However, the key is to look for sellers with high ratings and reviews to ensure product quality and reliability.
Direct Suppliers: Purchasing directly from manufacturers or specialized suppliers, such as Ultimation Industries or Warehouse1, can offer a level of expertise, customization, and customer support that is hard to match. These suppliers often provide a broad selection of conveyor rollers for sale, including:
- Ultimation Industries: Known for their extensive range of conveyor components and systems, Ultimation Industries offers both standard and custom-designed rollers, catering to various industrial needs.
- Warehouse1: Offers a comprehensive selection of material handling equipment, including heavy-duty conveyor rollers designed for industrial applications. Their expertise can guide you to the perfect solution tailored to your operational requirements.
How to Search for “Conveyor Rollers for Sale Near Me”
Finding local suppliers of conveyor rollers for sale can reduce shipping times and costs, and also offer the advantage of face-to-face support and service.
- Online Search Engines: Use specific search terms like “conveyor rollers for sale near me” in search engines to find suppliers in your vicinity. Most search engines will use your location to tailor the search results to include nearby businesses.
- Industry Directories and Forums: Look for directories that list industrial suppliers by location, and check out forums related to material handling equipment. These can be great resources for recommendations and reviews of local suppliers.
- Trade Shows and Industry Events: Attending trade shows and industry events can connect you directly with manufacturers and suppliers of conveyor rollers. These events often offer the chance to see products firsthand and discuss your needs directly with experts.
When searching for roller conveyors for sale, whether near you or online, it’s crucial to consider the supplier’s reputation, the quality of the products, and the level of customer service offered. This approach will help ensure that you find the best conveyor rollers to meet your operational needs and support the efficiency and productivity of your conveyor systems.
The Market for Used Conveyor Rollers: Navigating Conveyor Rollers for Sale
The search for conveyor rollers for sale often leads to the consideration of purchasing used conveyor rollers. This can be an economical and environmentally friendly option for many businesses. Understanding the benefits and knowing how to assess the quality of used conveyor rollers can ensure you make a wise investment.
Benefits of Buying Used Conveyor Rollers
- Cost Savings: The most apparent advantage is the potential for significant cost savings. Used rollers can be considerably cheaper than new ones, making them an attractive option for budget-conscious businesses.
- Quick Availability: Used conveyor rollers are often available for immediate purchase and delivery, bypassing the lead times associated with ordering new rollers from manufacturers.
- Environmental Sustainability: Purchasing used rollers contributes to sustainability efforts by recycling and reusing equipment, reducing waste and the demand for new manufacturing materials.
- Tested Durability: Used rollers have already been tested in real-world conditions, potentially offering evidence of their durability and reliability.
- Wide Selection: The used market can provide access to discontinued models or unique sizes not available in current catalogs, offering more customization options for your system.
- Opportunity for Upgrades: The savings garnered from buying used could allow you to purchase higher-quality rollers or more units than if you were buying new, optimizing your conveyor system further.
Tips for Assessing the Quality of Used Rollers
- Inspect for Physical Damage: Look for signs of wear, such as cracks, dents, or corrosion on the rollers, which could affect performance and longevity.
- Check for Smooth Rotation: Ensure the rollers rotate smoothly without any hitches or noise, indicating well-maintained bearings.
- Verify Load Capacity: Confirm that the used rollers can handle the weight and type of materials you plan to transport, ensuring they meet your operational requirements.
- Assess Compatibility: Make sure the used rollers fit your conveyor system in terms of size, type, and mounting methods to avoid integration issues.
- Inquire About History: Ask about the age of the rollers, previous usage conditions, and any maintenance or repairs they have undergone.
- Seek Guarantees or Returns Policy: Look for sellers who offer some guarantee or are willing to accept returns if the rollers don’t meet the promised conditions.
Where to Find Used Conveyor Rollers for Sale
Online Platforms: Websites like eBay and Craigslist often have listings for used conveyor rollers, offering a wide selection from various sellers across different locations.
Industrial Auctions: Keep an eye on auctions for industrial equipment, where you can sometimes find high-quality used conveyor rollers at a fraction of the cost of new ones.
Local Suppliers: Some material handling equipment suppliers may offer used or refurbished rollers. These suppliers can provide the advantage of seeing the product in person before purchasing.
Specialized Online Marketplaces: There are websites and online marketplaces dedicated to used and surplus industrial equipment, where you can specifically search for conveyor rollers for sale.
When exploring the market for used conveyor rollers, thorough research, and due diligence are key to finding quality components that match your needs. Assessing the quality of the rollers and understanding their previous usage can help ensure that the used conveyor rollers you purchase will serve your operations effectively, offering a balance between cost-efficiency and operational reliability.
Popular Conveyor Roller Options: Finding the Best Conveyor Rollers for Sale
When searching for conveyor rollers for sale, understanding the variety of options available can help you select the best components for your conveyor system. Among the vast selection, certain types and sizes of rollers stand out for their popularity and versatility in various applications. Here’s an overview of some of the most sought-after conveyor roller options in the market.
Popular Sizes
One of the most common sizes that many industries rely on is the 4″ conveyor roller. This size is particularly favored due to its versatility in handling a wide range of products and materials. It strikes a balance between strength and compatibility, making it suitable for both light and medium-duty applications. Whether for distribution centers, manufacturing plants, or packaging lines, the 4″ roller is a staple in many conveyor systems, offering reliable performance and adaptability.
Specialty Rollers
For more specific applications, specialty rollers provide enhanced functionality tailored to unique operational needs. Two notable examples include:
- Polyurethane Coated Rollers: These rollers are designed with a polyurethane coating that offers excellent grip, noise reduction, and protection against abrasions. The coating also minimizes damage to delicate items during transport, making these rollers ideal for industries where product integrity is paramount, such as electronics manufacturing or food processing.
- Grooved Rollers: Grooved rollers are designed to engage with belts or to sort and align products on the conveyor. The grooves can help maintain the orientation of items as they move, which is crucial in applications requiring precise placement or in systems where items need to be directed to different areas or tracks.
When exploring conveyor rollers for sale, considering these popular and specialty options can significantly enhance the efficiency and effectiveness of your conveyor system. The choice between standard sizes like the 4″ roller and specialty rollers such as polyurethane coated or grooved variants should be guided by your specific operational requirements, the nature of the materials being transported, and the environmental conditions of the workspace.
Investing in high-quality conveyor rollers that match your system’s needs not only optimizes the performance of your material handling operations but also contributes to the longevity and reliability of the conveyor system itself. Whether you’re upgrading an existing setup or designing a new system from scratch, integrating the right conveyor rollers for sale into your operation is a pivotal step towards achieving operational excellence.
DIY and Custom Solutions: Enhancing Your System with Conveyor Rollers for Sale
For those who operate specialized conveyor systems, finding conveyor rollers for sale that fit unique specifications can sometimes be a challenge. This is where DIY and custom solutions come into play, offering the flexibility to meet specific operational requirements that off-the-shelf products cannot. Whether you’re building a new system from scratch or modifying an existing setup, understanding when and how to consider custom-made conveyor rollers can make a significant difference in your project’s success.
When and How to Consider Custom-Made Conveyor Rollers
When to Consider Custom Solutions:
- Unique Applications: If your conveyor system handles materials or products with unusual shapes, weights, or requires special handling, custom rollers may be necessary.
- Harsh Environments: Operations in environments with extreme temperatures, corrosive substances, or abrasive materials may require rollers made from special materials or with protective coatings.
- Integration with Existing Systems: Custom rollers might be needed to ensure compatibility with older systems or those with non-standard dimensions.
- Improving Efficiency: Tailor-made rollers can be designed to optimize speed, reduce noise, or enhance handling precision, directly impacting productivity.
- Addressing Specific Challenges: Whether it’s reducing downtime, enhancing safety, or minimizing maintenance, custom solutions can address particular operational challenges.
How to Proceed with Custom Solutions:
- Define Your Requirements: Clearly outline what you need from your rollers in terms of size, load capacity, material, and any other specific features.
- Consult with Experts: Work with engineers or specialists who can advise on the best materials and designs for your custom rollers.
- Prototype and Test: Before full-scale production, prototype testing is crucial to ensure the custom rollers meet your needs and perform as expected.
- Choose the Right Manufacturer: Select a manufacturer experienced in producing custom conveyor rollers and who can provide quality assurance and support.
Options for DIY and Custom Roller Solutions
For those inclined towards DIY or needing bespoke solutions, here are several options to consider:
- Custom Machining and Fabrication: Work with a machine shop that can fabricate rollers to your exact specifications, including special materials or finishes.
- 3D Printing: For less conventional designs or materials, 3D printing offers the flexibility to create rollers with complex shapes or with materials not easily machined.
- Retrofitting Kits: Some manufacturers offer kits that allow you to modify standard rollers for specific applications or environments.
- Material Coatings: Applying specialty coatings yourself or through a service can enhance the performance of standard rollers, such as increasing grip or resistance to wear.
- Bearing Modifications: Altering or replacing the bearings in existing rollers can adjust the load capacity or reduce maintenance requirements.
- Custom Shaft Attachments: Designing custom shafts can help integrate new rollers into an existing system or facilitate the repair of older equipment.
Conveyor rollers for sale for DIY and custom solutions opens up a realm of possibilities for enhancing your conveyor system. By carefully considering your system’s unique needs and leveraging the available options for customization, you can significantly improve the efficiency, reliability, and longevity of your conveyor operations. Whether through collaboration with specialists, employing innovative manufacturing techniques, or modifying existing products, custom and DIY solutions can provide the perfect fit for your specific conveyor challenges.
Pricing and Purchasing Tips: Securing the Best Deals on Conveyor Rollers for Sale
When it comes to acquiring conveyor rollers for sale, understanding the pricing landscape and knowing how to secure the best deals are crucial steps in making an informed purchasing decision. Whether you’re in the market for new or used conveyor rollers, a clear grasp of expected price ranges and strategic purchasing tips can help you maximize value while minimizing costs.
General Pricing Guide for New and Used Conveyor Rollers
New Conveyor Rollers:
- Standard Steel Rollers: Prices typically range from $15 to $50 per roller, depending on size and load capacity.
- Polyurethane Coated Rollers: Expect to pay between $30 and $100 per roller, with costs varying by coating thickness and roller dimensions.
- Heavy-Duty Industrial Rollers: Prices can start from $100 and go up to several hundred dollars per roller for those designed to handle extreme loads and conditions.
- Motorized Rollers: These can range from $200 to $1000+ per unit, heavily influenced by power, size, and integrated control features.
- Stainless Steel Rollers for Food Grade Applications: Typically priced between $50 and $200 per roller, reflecting the premium for corrosion resistance and sanitary design.
- Custom-Designed Rollers: Costs can vary widely, starting at $100 and potentially reaching several thousand dollars, depending on complexity and materials.
Used Conveyor Rollers:
- Standard Steel Rollers: Used options might range from $5 to $25 per roller, offering significant savings.
- Polyurethane Coated Rollers: Available for as low as $20 to $50, depending on condition and wear.
- Heavy-Duty Rollers: Prices can be reduced to $50 to $250, depending on the age and condition of the rollers.
- Motorized Rollers: You might find these for $100 to $500, a fraction of the cost of new ones if they’re in good working condition.
- Stainless Steel Rollers: These can be found from $25 to $100, offering a cost-effective option for food-grade applications.
- Bulk Purchases: Buying used rollers in bulk can further lower the price per unit, offering an opportunity for additional savings.
How to Get the Best Deals and Avoid Overpaying
- Compare Suppliers: Don’t settle on the first conveyor rollers for sale offer you find. Compare prices and terms from multiple suppliers to find the best deal.
- Buy in Bulk: Many suppliers offer discounts for bulk purchases. If you have the storage space and a long-term need, buying in bulk can lead to significant savings.
- Consider Used or Refurbished: For operations where brand new isn’t a necessity, used or refurbished rollers can provide substantial cost savings.
- Negotiate: Especially when buying in larger quantities or sourcing custom solutions, there’s often room to negotiate on price. Don’t hesitate to ask for a better deal.
- Look for Closeouts or Overstock Sales: Suppliers may offer discounts on overstock items or models being discontinued, which can be an excellent opportunity to save.
- Factor in Shipping and Handling: When comparing prices, consider the total cost, including shipping and handling fees, to ensure you’re getting the best overall deal.
By following these pricing and purchasing tips for conveyor rollers for sale, you can ensure you’re making the most cost-effective decisions for your material handling needs. Whether opting for new, used, or custom rollers, a strategic approach to sourcing can lead to significant savings and a more efficient conveyor system.
Installation and Maintenance: Maximizing the Lifespan of Conveyor Rollers for Sale
Proper installation and regular maintenance are crucial for ensuring the optimal performance and extending the lifespan of conveyor rollers for sale that you have purchased. This section provides a basic guide on how to correctly install conveyor rollers and essential maintenance tips to keep them in top condition.
Basic Guide on How to Install Conveyor Rollers
- Preparation: Before installation, ensure that the conveyor frame is level and clean of any debris. This will facilitate a smoother installation process and better roller performance.
- Measurement and Alignment: Measure the spacing between rollers according to the manufacturer’s specifications or your system’s requirements. Accurate alignment is crucial for uniform weight distribution and smooth operation.
- Installation of Brackets: If your system requires brackets for roller installation, secure them in place on the conveyor frame first, ensuring they are tightly fastened and aligned.
- Placing the Rollers: Carefully place the rollers into the brackets or frame slots. For systems with a spring-loaded mechanism, compress the springs and insert the ends of the rollers into the designated slots.
- Securing the Rollers: Once the rollers are in place, ensure they are secured according to the system’s design. This may involve tightening fasteners or ensuring spring-loaded mechanisms are properly engaged.
- Testing: After installation, manually rotate the rollers to ensure they move freely without resistance. It’s also advisable to run the conveyor system empty to check for proper roller alignment and smooth operation.
Maintenance Tips to Extend the Lifespan of the Rollers
- Regular Cleaning: Keep the rollers and the conveyor track free of dust, debris, and any material spillage. Accumulation of debris can cause rollers to stick or bind, leading to premature wear.
- Lubrication: Periodically lubricate the bearings of the rollers, if applicable, according to the manufacturer’s recommendations. Proper lubrication reduces friction and wear, extending the life of the rollers.
- Inspection and Replacement: Regularly inspect the rollers for signs of wear, damage, or misalignment. Replace any rollers that show significant wear or damage to prevent further issues with the conveyor system.
- Alignment Checks: Periodically check the alignment of the rollers and the conveyor frame. Misaligned rollers can cause uneven wear and lead to operational problems.
- Tension Adjustment: For systems that use belt-driven rollers, regularly check and adjust the tension of the belts. Incorrect tension can lead to premature wear of both the belts and the rollers.
- Load Distribution: Ensure that the loads conveyed on the system are evenly distributed across the width of the conveyor. Uneven load distribution can cause excessive wear on certain rollers and lead to system imbalance.
By following these installation and maintenance guidelines for conveyor rollers for sale, you can significantly enhance the performance and longevity of your conveyor system. Regular maintenance not only prevents downtime but also ensures that the conveyor operates efficiently, supporting your operational needs effectively.
FAQs About Conveyor Rollers for Sale
The standard size of a conveyor roller can vary significantly depending on the application and the type of conveyor system it is designed for. However, one of the most common diameters for conveyor rollers is 4 inches (approximately 101.6mm). This size is widely used because it offers a good balance between durability and capability for handling a variety of materials and load sizes. Roller lengths can also vary, typically ranging from a few inches to several feet, to match the width of the conveyor belt or the materials being transported. The choice of roller size directly impacts the conveyor’s efficiency, its load-bearing capacity, and the smoothness of material flow. Manufacturers often provide a range of standard sizes but can also customize rollers to specific dimensions based on the unique needs of the application, ensuring optimal performance and integration with the conveyor system.
Conveyor rollers are measured based on their diameter, length, and the type of bearing or shaft that they use. The diameter is measured across the roller’s widest part and is a critical factor in determining the roller’s load capacity and the types of materials it can transport. The length of the roller is measured from end to end, which should closely match the width of the conveyor belt or frame to ensure proper support and distribution of materials. When measuring for replacement rollers, it’s also important to consider the bearing type and the shaft size, as these elements must be compatible with the existing conveyor system. Accurate measurements are crucial for maintaining the efficiency and functionality of the conveyor, preventing issues such as misalignment, uneven wear, and material spillage. It is recommended to consult with the conveyor manufacturer or a specialist when selecting or replacing rollers to ensure precise fitment and optimal performance.
The kind of roller used for a conveyor belt largely depends on the conveyor system’s application, the environment it operates in, and the materials it handles. Gravity rollers, which rely on the force of gravity to move materials, are commonly used for lightweight applications and require manual or slight incline assistance. Driven rollers, including belt-driven and motorized rollers, are suitable for heavier loads and automated systems, providing controlled movement and speed. For environments with special requirements, such as food processing or chemical exposure, coated rollers (e.g., polyurethane or rubber-coated) are used to prevent contamination, reduce noise, or increase grip. Heavy-duty rollers are designed for industrial applications where high load capacities and durability are essential. Selecting the appropriate type of roller ensures the conveyor system operates efficiently, safely, and effectively, tailored to the specific operational demands.
While there isn’t a universal “formula” for a conveyor roller, as design considerations can vary widely depending on the application, some basic calculations are commonly used to determine the appropriate roller specifications for a conveyor system. One key formula relates to the roller load capacity, which helps in selecting a roller capable of supporting the weight of the materials it will carry. This formula considers the weight of the material per foot of conveyor, the spacing between rollers, and the maximum load per roller. Another important calculation is for roller spacing, ensuring that the conveyor belt has adequate support without unnecessary friction or sagging. This involves the length of the material being conveyed and the desired support density. Additionally, roller speed calculations might be required for motorized systems, incorporating factors such as motor RPM, roller diameter, and gear ratios to achieve the desired conveyor belt speed. Consulting with a conveyor specialist or manufacturer is recommended to accurately determine the optimal roller specifications for a specific application, ensuring efficient and reliable system performance.
Last Updated on May 28, 2024 by Jordan Smith
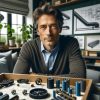
Jordan Smith, a seasoned professional with over 20 years of experience in the conveyor system industry. Jordan’s expertise lies in providing comprehensive solutions for conveyor rollers, belts, and accessories, catering to a wide range of industrial needs. From initial design and configuration to installation and meticulous troubleshooting, Jordan is adept at handling all aspects of conveyor system management. Whether you’re looking to upgrade your production line with efficient conveyor belts, require custom conveyor rollers for specific operations, or need expert advice on selecting the right conveyor accessories for your facility, Jordan is your reliable consultant. For any inquiries or assistance with conveyor system optimization, Jordan is available to share his wealth of knowledge and experience. Feel free to reach out at any time for professional guidance on all matters related to conveyor rollers, belts, and accessories.