The Role of Conveyor Sealing Systems in Industrial Safety
Conveyor sealing systems are vital in industrial applications for controlling dust, preventing spillage, and ensuring efficient material handling. These systems minimize fugitive dust and fine particulates from escaping the conveyor belt, which is crucial for maintaining a clean and safe work environment. Key components of conveyor sealing systems include dust sealing systems, belt skirting, and tail sealing boxes. Effective sealing systems provide numerous benefits such as improved operational efficiency, reduced maintenance costs, and enhanced safety. By investing in high-quality conveyor sealing systems, industries can achieve better control over material flow and ensure compliance with environmental regulations.
Conveyor Sealing Systems: Benefits and Applications
Benefits of Using Conveyor Sealing Systems
Conveyor sealing systems play a crucial role in industrial operations by ensuring that material handling processes are efficient, safe, and clean. These systems are designed to prevent spillage, control dust, and minimize material loss, thereby enhancing the overall productivity of the facility. Let’s delve deeper into the various benefits of using conveyor sealing systems.
Improved Efficiency and Reduced Maintenance Costs
One of the primary advantages of conveyor sealing systems is the significant improvement in operational efficiency. By sealing the conveyor belt, these systems prevent spillage and dust from escaping, which means that more material is retained on the belt. This results in higher throughput and less downtime for cleaning and maintenance.
Additionally, conveyor sealing systems help to reduce wear and tear on conveyor components. Dust and spillage can cause abrasive damage to the conveyor belt, idlers, and other components, leading to frequent maintenance and replacement. By containing these materials, sealing systems extend the lifespan of conveyor components, thereby reducing maintenance costs and downtime.
Enhanced Safety and Cleaner Work Environment
Safety is a critical concern in any industrial setting. Conveyor sealing systems contribute to a safer work environment by containing dust and preventing it from becoming airborne. Dust inhalation can pose serious health risks to workers, leading to respiratory issues and other health problems. By controlling dust, sealing systems help to protect the health and well-being of employees.
Moreover, spillage can create slip hazards on walkways and work areas, increasing the risk of accidents and injuries. Conveyor sealing systems help to keep these areas clean and free from hazardous materials, enhancing overall workplace safety.
A cleaner work environment also translates to better equipment performance. Dust and spillage can contaminate machinery and other equipment, leading to malfunction and increased maintenance. By keeping the work area clean, sealing systems help to maintain the efficiency and reliability of all equipment involved in the material handling process.
Prevention of Material Loss and Environmental Contamination
Material loss during transportation can be a significant issue, especially when dealing with valuable or hazardous materials. Conveyor sealing systems effectively prevent material loss by ensuring that all material stays on the conveyor belt. This not only improves the efficiency of the operation but also maximizes the profitability by reducing waste.
In addition to preventing material loss, conveyor sealing systems also play a crucial role in preventing environmental contamination. Dust and spillage can contaminate soil, water, and air, leading to serious environmental issues and potential regulatory fines. By containing these materials, sealing systems help to protect the environment and ensure compliance with environmental regulations.
Additional Benefits
Beyond the primary advantages mentioned above, there are several other benefits to using conveyor sealing systems. For instance, these systems can help to reduce noise levels in the facility. Dust and spillage can create noise when they hit the ground or other surfaces, contributing to a noisy work environment. By containing these materials, sealing systems help to reduce noise levels, creating a more comfortable work environment.
Furthermore, conveyor sealing systems can enhance the overall appearance of the facility. A clean and well-maintained facility reflects positively on the company, showcasing a commitment to quality and safety. This can be particularly important when hosting visitors or potential clients.
Innovations in Conveyor Sealing Systems
Innovations in Conveyor Sealing Systems
Conveyor sealing systems have undergone significant advancements over the years, driven by the need to enhance efficiency, safety, and environmental compliance in industrial applications. These innovations have not only improved the performance of sealing systems but also provided solutions to some of the most pressing challenges faced by industries. In this section, we will explore recent advancements in conveyor sealing systems and highlight case studies or examples of successful implementations.
Recent Advancements and Innovations
Advanced Material Technologies
- Recent innovations in conveyor sealing systems have focused on the development of advanced materials that offer superior durability and performance. High-quality elastomers and engineered polymers are now commonly used in skirting and sealing components, providing excellent resistance to wear, tear, and abrasion. These materials also offer enhanced flexibility, allowing for better conformity to the conveyor belt surface and reducing gaps where material can escape.
Modular Sealing Systems
- Modular sealing systems have revolutionized the way conveyor sealing is approached. These systems consist of interchangeable components that can be easily installed, replaced, or upgraded without the need for extensive downtime. This modularity not only simplifies maintenance but also allows for customized sealing solutions tailored to specific conveyor applications. The ability to quickly replace worn or damaged sections reduces maintenance costs and improves overall system reliability.
Innovative Dust Control Technologies
- Dust control is a critical aspect of conveyor sealing systems, and recent advancements have led to the development of more effective dust suppression technologies. These include the use of air knives, misting systems, and foam-based dust suppression solutions. Air knives create a high-velocity air curtain that prevents dust from escaping, while misting and foam systems capture and settle airborne particles, significantly reducing dust levels around conveyor operations.
Enhanced Skirting Designs
- Skirting is a key component of conveyor sealing systems, and innovations in skirting designs have greatly improved their effectiveness. Modern skirting systems feature adjustable and self-adjusting mechanisms that maintain optimal contact with the conveyor belt, even as the belt and material load vary. This ensures a consistent seal and minimizes material spillage. Additionally, the use of dual-sealing skirting systems, which incorporate primary and secondary seals, provides an added layer of protection against material loss.
Automated Monitoring and Control
- The integration of automated monitoring and control systems has brought a new level of sophistication to conveyor sealing systems. Sensors and IoT (Internet of Things) technologies can now be used to continuously monitor the performance of sealing components, detecting wear, misalignment, or other issues in real-time. This data-driven approach allows for proactive maintenance and immediate adjustments, ensuring optimal sealing performance and reducing unexpected downtime.
Case Studies and Examples of Successful Implementations
Case Study 1: Mining Industry
- In a large mining operation, the implementation of advanced conveyor sealing systems led to a substantial reduction in material spillage and dust emissions. The use of high-performance elastomer skirting and modular sealing components allowed for quick and efficient maintenance, minimizing operational disruptions. The introduction of automated dust control technologies further enhanced air quality, improving working conditions for employees and ensuring compliance with environmental regulations.
Case Study 2: Cement Manufacturing
- A cement manufacturing plant faced challenges with dust control and material loss in its conveyor systems. By adopting the latest innovations in conveyor sealing systems, including dual-sealing skirting and automated monitoring, the plant achieved significant improvements in efficiency and cleanliness. The new sealing system not only reduced spillage and dust but also extended the lifespan of conveyor components, resulting in lower maintenance costs and increased operational uptime.
Case Study 3: Food Processing
- In the food processing industry, maintaining a clean and safe environment is paramount. A food processing facility implemented innovative conveyor sealing systems to address issues with material contamination and spillage. The use of advanced materials and modular designs allowed for easy cleaning and maintenance, ensuring that the facility met stringent hygiene standards. The result was a more efficient production process with fewer instances of contamination and product loss.
Conveyor Sealing Systems
What are Conveyor Sealing Systems?
Conveyor sealing systems are critical components in the efficient operation of conveyor belts used across various industries, including mining, material handling, and manufacturing. These systems are specifically designed to address common issues such as dust, spillage, and material loss that occur during the transportation of bulk materials. By creating a controlled environment around the conveyor belt, conveyor sealing systems help to maintain the integrity of the material being transported, ensuring that it reaches its destination without unnecessary loss or contamination.
Definition and Purpose of Conveyor Sealing Systems
Conveyor sealing systems are assemblies of various components, including skirting rubber, belt sealing strips, and dust sealing cloths, that work together to create a barrier between the conveyor belt and the surrounding environment. The primary purpose of these systems is to prevent the escape of material and dust from the conveyor belt, which can lead to significant operational inefficiencies and environmental concerns.
The sealing system typically includes side skirts that run along the length of the conveyor belt, sealing strips that fit tightly against the belt, and dust suppression components that control airborne particles. By implementing these components, conveyor sealing systems effectively minimize the amount of material that escapes during transport, ensuring that the conveyor belt operates at optimal efficiency.
How Conveyor Sealing Systems Work to Minimize Dust, Spillage, and Material Loss
Conveyor sealing systems are designed to address several key issues that can arise during the transportation of bulk materials. Here’s how they work to minimize dust, spillage, and material loss:
- Dust Control: Dust is a common byproduct of transporting bulk materials on a conveyor belt. When material is loaded onto the belt, it often generates fine particles that can become airborne, leading to respiratory hazards for workers and contamination of the surrounding environment. Conveyor sealing systems include dust suppression components, such as dust sealing cloths and misting systems, that capture and contain these particles, preventing them from escaping into the air.
- Spillage Prevention: Spillage occurs when material falls off the sides of the conveyor belt during transport. This can happen due to a variety of factors, including belt misalignment, overloading, or the nature of the material being transported. Conveyor sealing systems employ side skirts and sealing strips that fit snugly against the belt, creating a barrier that prevents material from spilling over the sides. These components are typically made from durable materials that can withstand the abrasive nature of bulk materials, ensuring a long service life.
- Material Loss Reduction: Material loss can significantly impact the efficiency and profitability of a conveyor system. When material escapes from the conveyor belt, it not only reduces the amount of product that reaches its destination but also creates additional cleanup and maintenance tasks. Conveyor sealing systems are designed to keep material on the belt, reducing waste and ensuring that the maximum amount of product reaches its intended destination. This is achieved through the use of high-quality sealing strips and skirting rubber that maintain a tight seal against the belt, even under heavy loads and challenging conditions.
In addition to these primary functions, conveyor sealing systems also contribute to improved conveyor belt life and reduced maintenance costs. By minimizing the amount of material that escapes from the belt, these systems reduce the wear and tear on the belt and other conveyor components, leading to fewer breakdowns and longer service intervals.
The Importance of Proper Installation and Maintenance
To achieve the best results from conveyor sealing systems, it is essential to ensure proper installation and regular maintenance. Improperly installed sealing systems can fail to create an effective barrier, leading to continued issues with dust, spillage, and material loss. Similarly, neglected maintenance can result in worn or damaged components that no longer function effectively.
When installing a conveyor sealing system, it is important to follow the manufacturer’s guidelines and use the recommended components for your specific conveyor setup. Regular inspections should be conducted to check for signs of wear and tear, and any damaged components should be replaced promptly to maintain the integrity of the system.
Conveyor sealing systems play a vital role in the efficient operation of conveyor belts by minimizing dust, spillage, and material loss. By creating a controlled environment around the conveyor belt, these systems help to ensure that bulk materials are transported safely and efficiently, reducing waste and improving overall productivity. Proper installation and maintenance are key to achieving the best results from these systems, making them an essential investment for any operation that relies on conveyor belts for material handling.
Industry Applications for Conveyor Sealing Systems
Common Industries that Benefit from Conveyor Sealing Systems
Conveyor sealing systems are essential components in various industries where bulk material handling is critical. By preventing dust, spillage, and material loss, these systems enhance operational efficiency and safety. Here, we will explore the primary industries that benefit from conveyor sealing systems and provide specific examples of how these systems improve operations.
Mining
The mining industry heavily relies on conveyor systems to transport extracted materials from mines to processing plants. Conveyor sealing systems play a crucial role in this sector by minimizing dust generation and preventing material spillage. In mining operations, dust control is vital for maintaining air quality and protecting workers’ health. The use of dust suppression components in conveyor sealing systems ensures that fine particles generated during the transportation of ores and minerals are contained, reducing the risk of respiratory issues for workers and preventing contamination of the surrounding environment.
Additionally, conveyor sealing systems help prevent spillage of valuable materials such as coal, iron ore, and precious metals. By maintaining a tight seal along the conveyor belt, these systems ensure that the maximum amount of material reaches its destination, reducing waste and increasing the overall efficiency of mining operations. This is particularly important in underground mining, where spillage can create hazardous conditions and impede the movement of equipment and personnel.
Cement
In the cement industry, conveyor sealing systems are critical for handling raw materials such as limestone, clay, and gypsum, as well as finished cement products. Cement production involves the transportation of large volumes of these materials, often under challenging conditions. Conveyor sealing systems help maintain the integrity of the materials being transported, preventing dust and spillage that can lead to significant losses and operational inefficiencies.
For example, during the clinker production process, fine particles of raw material are prone to becoming airborne, posing health risks and causing environmental pollution. Conveyor sealing systems equipped with dust sealing cloths and side skirts effectively contain these particles, ensuring a cleaner and safer working environment. Additionally, by preventing spillage, these systems help reduce material wastage and the associated costs of cleanup and maintenance.
Aggregate Processing
Aggregate processing involves the handling of materials such as sand, gravel, and crushed stone, which are used in construction and infrastructure projects. Conveyor sealing systems are essential in this industry to manage the dust and spillage associated with transporting these abrasive materials. The use of skirting rubber and sealing strips in conveyor sealing systems ensures that aggregates remain on the conveyor belt, minimizing material loss and preventing the buildup of debris along the conveyor path.
In a typical aggregate processing plant, conveyor sealing systems help maintain the quality of the final product by preventing contamination from dust and foreign particles. This is particularly important in the production of high-quality aggregates used in concrete and asphalt, where consistency and purity are crucial. By reducing the need for frequent maintenance and cleanup, conveyor sealing systems also contribute to lower operational costs and improved productivity in aggregate processing facilities.
Food Production
The food production industry requires stringent hygiene and cleanliness standards to ensure the safety and quality of food products. Conveyor sealing systems are vital in this sector for handling bulk food ingredients such as grains, sugar, and flour. These systems help prevent contamination and ensure that materials are transported in a controlled and sanitary manner.
For example, in a flour milling plant, conveyor sealing systems equipped with dust suppression components prevent flour dust from becoming airborne and settling on surfaces, reducing the risk of cross-contamination and maintaining a clean processing environment. Similarly, in sugar processing, conveyor sealing systems help contain fine sugar particles, preventing product loss and ensuring that the final product meets quality standards.
Specific Examples of How Sealing Systems Improve Operations
- Mining: In a coal mining operation, conveyor sealing systems equipped with advanced dust suppression technology can significantly reduce airborne coal dust, improving air quality and reducing the risk of explosions. This not only protects workers’ health but also enhances the safety and efficiency of the mining process.
- Cement: In a cement plant, conveyor sealing systems with robust side skirts and sealing strips can prevent the spillage of raw materials such as limestone and clay, ensuring that the materials reach the kiln with minimal loss. This improves the overall efficiency of the cement production process and reduces the cost associated with material wastage and cleanup.
- Aggregate Processing: In an aggregate quarry, conveyor sealing systems can prevent the loss of valuable crushed stone and gravel during transport. By maintaining a tight seal along the conveyor belt, these systems reduce the need for frequent maintenance and minimize downtime, leading to increased productivity and profitability.
- Food Production: In a grain processing facility, conveyor sealing systems with high hygiene standards ensure that grains are transported without contamination. This helps maintain the quality of the final product and meets regulatory requirements for food safety, ultimately protecting consumer health and enhancing the reputation of the food producer.
Types of Conveyor Sealing Systems
Conveyor sealing systems are critical in maintaining the efficiency and cleanliness of industrial operations involving material handling. They are designed to prevent the escape of dust and other particulates, ensuring a safer and more productive working environment. In this section, we will explore the different types of conveyor sealing systems, including dust sealing systems, belt skirting systems, and tail sealing boxes. We will also compare their features and use cases to help you understand which system might be best suited for your needs.
Dust Sealing Systems
Dust sealing systems are specifically designed to contain dust and other fine materials within the conveyor system. They are essential in industries where dust control is crucial, such as mining, cement production, and bulk material handling.
Features
- Enclosure Design: Dust sealing systems typically feature a fully enclosed design to prevent dust from escaping.
- Flexible Skirts: These systems often include flexible skirts that conform to the conveyor belt’s contours, providing an effective seal.
- Airflow Control: Some dust sealing systems incorporate airflow control mechanisms to manage the movement of air and dust within the enclosure.
- Easy Maintenance: Designed for easy access, these systems allow for straightforward maintenance and cleaning.
Use Cases
- Mining Operations: In mining, where large quantities of dust are generated, dust sealing systems are crucial for maintaining air quality and reducing health risks.
- Cement Production: These systems help contain fine cement particles, preventing them from contaminating the work environment.
- Bulk Material Handling: Any operation that involves the transport of fine, dry materials can benefit from dust sealing systems.
Belt Skirting Systems
Belt skirting systems are designed to prevent material spillage from the conveyor belt, especially at loading and transfer points. They are widely used in various industries to enhance the efficiency and cleanliness of conveyor operations.
Features
- Skirtboards: Belt skirting systems use skirtboards made from durable materials like rubber or polyurethane, which are positioned along the sides of the conveyor belt.
- Adjustable Mounting: Many systems offer adjustable mounting options, allowing for easy installation and maintenance.
- Abrasion Resistance: The materials used in skirtboards are typically highly resistant to abrasion, ensuring a long service life.
- Low Friction: Designed to minimize friction between the skirt and the belt, reducing wear and energy consumption.
Use Cases
- Aggregate Handling: In industries dealing with aggregates, such as gravel and sand, belt skirting systems help prevent material loss and maintain a clean work area.
- Recycling Plants: These systems are beneficial in recycling operations, where various materials need to be conveyed without spillage.
- Food Processing: In food processing facilities, belt skirting systems help maintain hygiene by preventing spillage and contamination.
Tail Sealing Boxes
Tail sealing boxes are installed at the tail end of conveyor systems to prevent material from escaping and causing spillage. They are particularly useful in applications where the conveyor belt returns to the loading point.
Features
- Sealed Enclosure: Tail sealing boxes feature a sealed enclosure that effectively contains material at the conveyor’s tail end.
- Flexible Flaps: These systems often incorporate flexible flaps or curtains that conform to the belt, ensuring a tight seal.
- Easy Access: Designed for easy access, tail sealing boxes allow for quick inspection and maintenance.
- Durable Construction: Built to withstand harsh industrial environments, these systems are made from robust materials.
Use Cases
- Coal Handling: In coal handling operations, tail sealing boxes help contain coal dust and particles, preventing them from contaminating the surrounding area.
- Fertilizer Production: These systems are useful in fertilizer production, where material containment is critical to avoid environmental contamination.
- Grain Processing: In grain processing facilities, tail sealing boxes help maintain product integrity by preventing spillage and loss.
Comparison of Conveyor Sealing Systems
When comparing the different types of conveyor sealing systems, it’s important to consider the specific requirements of your operation. Dust sealing systems are ideal for environments where dust control is a primary concern. Belt skirting systems are best suited for preventing material spillage at loading and transfer points, making them versatile for a range of industries. Tail sealing boxes are essential for operations that require effective containment at the conveyor’s tail end, particularly in applications involving fine or dusty materials.
Each type of conveyor sealing system offers unique advantages and can be selected based on factors such as the type of material being conveyed, the operational environment, and maintenance requirements. By understanding the features and use cases of each system, you can make an informed decision to enhance the efficiency and cleanliness of your conveyor operations.
Notable Brands and Products in Conveyor Sealing Systems
Conveyor sealing systems play a critical role in enhancing the efficiency and cleanliness of industrial operations by preventing dust, spillage, and material loss. In this section, we will delve into some of the leading brands in the market and highlight key products such as the Trellex dust control system, emphasizing their unique features and advantages.
Overview of Leading Brands in the Market
Several brands have established themselves as leaders in the conveyor sealing systems market, offering innovative and reliable solutions for various industrial applications. Two notable brands in this space are Metso and Martin Engineering, each providing a range of products designed to meet the diverse needs of their customers.
Metso Trellex Dust Sealing
Metso is renowned for its high-quality industrial equipment, and its Trellex line of conveyor sealing systems is no exception. Trellex products are designed to provide superior dust control and material containment, making them ideal for a wide range of industries.
Key Products and Features
- Trellex Dust Control System: The Trellex dust control system is engineered to minimize dust emissions from conveyor systems. It features a combination of skirting, sealing, and dust suppression components that work together to create a cleaner and safer work environment.
- Modular Design: The system’s modular design allows for easy installation and maintenance, reducing downtime and operational costs.
- Durable Materials: Made from high-quality, durable materials, the Trellex dust control system offers long-lasting performance even in the harshest industrial conditions.
- Effective Dust Suppression: The system includes efficient dust suppression mechanisms that capture and contain dust particles, preventing them from escaping into the surrounding environment.
- Trellex Flexopipe®: This innovative product is designed for enclosed material transport, providing excellent dust and spillage control.
- Flexible Design: The Flexopipe® system is highly flexible, allowing for the transport of materials around tight curves and over long distances without compromising on sealing efficiency.
- Sealed Conveying: The sealed conveying design ensures that materials remain contained within the system, reducing the risk of contamination and spillage.
Martin Conveyor Catalog
Martin Engineering is another leading brand in the conveyor sealing systems market, known for its comprehensive range of products designed to improve conveyor efficiency and safety.
Key Products and Features
- Martin® ApronSeal™ Single Skirting: This product provides effective sealing along the conveyor belt, preventing material spillage and reducing dust emissions.
- Dual-Sealing System: The ApronSeal™ system features a dual-sealing mechanism that combines a primary and secondary seal to ensure maximum containment of materials.
- Easy Installation: Designed for easy installation, the ApronSeal™ system can be quickly and efficiently mounted on existing conveyor systems, minimizing downtime.
- Long-Lasting Performance: Made from durable materials, the ApronSeal™ system offers long-lasting performance and reduced maintenance needs.
- Martin® Tail Sealing Box: This product is designed to prevent spillage at the tail end of the conveyor, providing an effective solution for material containment.
- Robust Construction: The tail sealing box is constructed from high-quality materials, ensuring durability and reliable performance in demanding industrial environments.
- Adjustable Sealing Flaps: The adjustable sealing flaps conform to the conveyor belt, providing a tight seal that prevents material from escaping.
- Easy Maintenance: The design of the tail sealing box allows for easy access and maintenance, reducing downtime and maintenance costs.
Unique Features of Notable Products
Trellex Dust Control System
The Trellex dust control system from Metso stands out due to its modular design, which allows for easy customization and scalability. This system can be tailored to meet the specific needs of different industrial applications, providing a versatile solution for dust control. Its durable construction ensures long-term performance, making it a cost-effective choice for businesses looking to improve their conveyor systems’ efficiency and cleanliness.
Martin® ApronSeal™ Single Skirting
The Martin® ApronSeal™ Single Skirting system is notable for its dual-sealing mechanism, which provides superior containment of materials. This product’s ease of installation and maintenance makes it a popular choice among industries looking to minimize downtime and improve operational efficiency. Its robust design ensures reliable performance even in the most challenging industrial environments.
Key Components of Conveyor Sealing Systems
Conveyor sealing systems play a crucial role in enhancing the efficiency and longevity of conveyor systems in various industries. These systems are designed to prevent material spillage and control dust emissions, ensuring a cleaner and safer working environment. Below, we delve into the key components of conveyor sealing systems, which include conveyor belt skirting, sealing strips, and dust control systems. Understanding these components and their interplay is essential for optimizing conveyor performance.
Conveyor Belt Skirting
Conveyor belt skirting is a fundamental component of conveyor sealing systems. It refers to the flexible, rubber or polymer strips that are installed along the edges of the conveyor belt. The primary function of conveyor belt skirting is to prevent materials from spilling over the sides of the belt during transportation. This not only reduces material loss but also minimizes the risk of debris accumulating around the conveyor structure, which can lead to maintenance issues and potential safety hazards.
The skirting is usually installed on the sides of the conveyor belt, running parallel to the belt’s movement. It is designed to be adjustable to accommodate different belt widths and material types. The flexibility of the skirting material allows it to maintain a close seal against the belt, even when handling irregular or bulky materials. This ensures that the skirting remains effective in preventing spillage throughout the conveyor’s operation.
Sealing Strips
Sealing strips are another vital component of conveyor sealing systems. These strips are typically made from durable rubber or polyurethane and are placed between the conveyor belt and the conveyor structure. The primary purpose of sealing strips is to create a tight seal that prevents fine particles and dust from escaping the conveyor system. This is particularly important in industries where dust control is a significant concern, such as mining, cement production, and bulk material handling.
Sealing strips work in conjunction with conveyor belt skirting to provide a comprehensive sealing solution. While the skirting prevents larger materials from spilling, the sealing strips ensure that finer particles are contained within the conveyor system. The strips are designed to be flexible and wear-resistant, allowing them to maintain their sealing effectiveness over time, even under harsh operating conditions.
Dust Control Systems
Dust control systems are an integral part of conveyor sealing systems, especially in environments where airborne dust poses health and safety risks. These systems are designed to capture and contain dust generated during material handling processes, preventing it from escaping into the surrounding environment.
Dust control systems typically include components such as dust collectors, containment hoods, and air filtration units. Dust collectors are used to capture and filter dust particles from the air, ensuring that only clean air is released back into the workplace. Containment hoods are installed over transfer points, where material is transferred from one conveyor to another, to capture dust at its source. Air filtration units further purify the air by removing any remaining dust particles.
The effectiveness of dust control systems depends on their ability to work seamlessly with other components of the conveyor sealing systems. For example, well-designed conveyor belt skirting and sealing strips can significantly reduce the amount of dust generated, making the job of dust control systems easier and more efficient.
Enhancing Performance through Component Integration
The key to maximizing the performance of conveyor sealing systems lies in the integration of its components. Conveyor belt skirting, sealing strips, and dust control systems must work together harmoniously to achieve optimal results. When properly integrated, these components can effectively prevent material spillage, control dust emissions, and reduce the need for frequent maintenance.
One way to enhance the integration of these components is through regular inspection and maintenance. Ensuring that conveyor belt skirting and sealing strips are in good condition and properly adjusted can prevent gaps that may allow material or dust to escape. Additionally, maintaining dust control systems by regularly replacing filters and cleaning dust collectors can ensure their continued effectiveness.
Installation and Maintenance Tips for Conveyor Sealing Systems
The effectiveness of conveyor sealing systems in preventing material spillage and controlling dust emissions hinges on proper installation and diligent maintenance. Adhering to best practices during installation and implementing regular maintenance routines can ensure these systems perform optimally and have a long service life. Below are detailed guidelines for the installation and maintenance of conveyor sealing systems.
Best Practices for Installing Conveyor Sealing Systems
Planning and Preparation
Before beginning the installation of conveyor sealing systems, thorough planning and preparation are crucial. This includes selecting the appropriate type and size of skirting, sealing strips, and dust control systems based on the specific needs of your conveyor operation. Proper preparation involves:
- Surveying the Conveyor System: Inspect the entire conveyor system to identify areas where sealing is most needed. Focus on transfer points, loading zones, and areas with high dust generation.
- Choosing the Right Materials: Depending on the type of material being transported, select skirting and sealing strips made from materials that can withstand the operational environment. For abrasive materials, choose wear-resistant rubber or polyurethane.
- Gathering Tools and Materials: Ensure you have all necessary tools and materials ready for installation, including mounting brackets, fasteners, and any specialized equipment for cutting and fitting skirting and sealing strips.
Installation Steps
- Clean the Conveyor Area: Before installation, thoroughly clean the conveyor structure, especially the areas where the skirting and sealing strips will be attached. Remove any debris, dust, or old sealing materials.
- Install Mounting Brackets: Securely attach mounting brackets along the conveyor edges where the skirting will be installed. These brackets provide a stable base for the skirting material and ensure it remains in place during operation.
- Attach Conveyor Belt Skirting: Cut the skirting material to the desired length and attach it to the mounting brackets. Ensure the skirting forms a tight seal against the conveyor belt without causing excessive friction. Adjust the skirting as necessary to accommodate changes in belt movement and material load.
- Install Sealing Strips: Place sealing strips between the conveyor belt and the conveyor structure. These strips should be positioned to prevent fine particles from escaping. Ensure they are fitted snugly to maintain an effective seal.
- Integrate Dust Control Systems: If dust control systems are part of the installation, position dust collectors and containment hoods at key points along the conveyor. Connect air filtration units to ensure they capture and filter dust effectively.
Tips for Regular Maintenance to Ensure Longevity and Optimal Performance
Routine Inspections
Regular inspections are essential for maintaining the performance of conveyor sealing systems. Conduct routine checks to identify wear and tear, misalignment, or damage to the skirting, sealing strips, and dust control components. Key inspection points include:
- Skirting and Sealing Strips: Look for signs of wear or damage, such as cracks, tears, or excessive wear. Ensure the skirting maintains a tight seal against the belt and that sealing strips are intact.
- Dust Control Systems: Check dust collectors and filters for clogs or buildup. Ensure containment hoods are properly positioned and functioning effectively.
Maintenance Actions
- Clean and Clear: Regularly clean the conveyor system to remove accumulated dust and debris. This helps prevent material buildup that can affect the performance of the sealing systems.
- Adjust and Tighten: Periodically adjust the skirting and sealing strips to maintain a proper seal. Tighten any loose fasteners and ensure all components are securely in place.
- Replace Worn Components: Replace skirting, sealing strips, and dust control filters as needed. Using high-quality replacement parts can extend the life of the conveyor sealing systems and improve overall efficiency.
- Lubricate Moving Parts: Lubricate any moving parts of the conveyor sealing systems to reduce friction and wear. This can help maintain smooth operation and extend the life of the components.
- Monitor System Performance: Keep track of the performance of the conveyor sealing systems. If you notice an increase in spillage or dust emissions, investigate and address the issue promptly.
Last Updated on June 5, 2024 by Jordan Smith
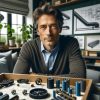
Jordan Smith, a seasoned professional with over 20 years of experience in the conveyor system industry. Jordan’s expertise lies in providing comprehensive solutions for conveyor rollers, belts, and accessories, catering to a wide range of industrial needs. From initial design and configuration to installation and meticulous troubleshooting, Jordan is adept at handling all aspects of conveyor system management. Whether you’re looking to upgrade your production line with efficient conveyor belts, require custom conveyor rollers for specific operations, or need expert advice on selecting the right conveyor accessories for your facility, Jordan is your reliable consultant. For any inquiries or assistance with conveyor system optimization, Jordan is available to share his wealth of knowledge and experience. Feel free to reach out at any time for professional guidance on all matters related to conveyor rollers, belts, and accessories.