Conveyor Snub Roller: Introduction and Overview
Conveyor snub roller is critical components of conveyor belt systems, designed to maintain optimal tension and alignment of the belt. Positioned near the drive pulleys at either end of the conveyor, these rollers help prevent the belt from sagging or slipping by increasing the belt’s contact area with the drive rollers. Their strategic placement is vital for the smooth operation of the conveyor system, ensuring efficient handling and movement of materials across various industries. Through their function, conveyor snub rollers play a key role in reducing downtime and maintenance costs.
Types and Designs of Conveyor Snub Roller
Conveyor snub rollers are integral to the efficiency and safety of conveyor systems, playing a vital role in various industries including manufacturing, mining, and distribution. These rollers are strategically designed to ensure optimal tension and alignment of the conveyor belt, thus preventing slippage and minimizing wear and tear. Their importance extends beyond mere functionality; they enhance system reliability and can significantly reduce operational costs by improving the lifespan of the conveyor belt. Effective use of snub rollers leads to smoother operations, fewer interruptions, and reduced need for frequent maintenance checks.
Overview of Different Types of Snub Rollers
Conveyor snub rollers come in a variety of designs, each tailored to meet specific operational demands. This diversity allows for optimized performance in different scenarios, from standard operations to specialized tasks.
- Standard Conveyor Snub Roller: These rollers are the backbone of many systems, providing reliable support and tension control in standard conveyor setups.
- Idler Snub Rollers: These are specialized for integration with idler assemblies, enhancing the precise control of belt tension and alignment.
- Adjustable Snub Rollers: Offering versatility, these rollers can be manually adjusted to adapt to varying operational needs, ensuring optimal tension at all times.
- Impact Snub Rollers: Engineered to absorb significant impacts, these rollers are crucial in heavy-duty applications where sudden loads are common.
- Retractable Snub Rollers: Designed for ease of maintenance, these rollers can be retracted from the conveyor setup, facilitating easier access for cleaning and repairs.
- Rubber-Coated Snub Rollers: These provide enhanced grip to maintain belt traction in challenging conditions, while also dampening operational noise.
- Motorized Snub Rollers: Equipped with individual motors, these rollers offer dynamic tension control, improving the conveyor system’s responsiveness.
- High-Temperature Snub Rollers: Constructed to endure extreme temperatures, these rollers are essential in high-heat applications like metalworking or ceramics production.
- Specialized Material Handling Snub Rollers: Tailored to handle specific materials, these rollers ensure the safe and efficient transport of sensitive or abrasive materials.
Materials Commonly Used in Snub Roller Construction
Selecting the right materials for conveyor snub rollers is crucial for ensuring their durability and functionality in various environments.
- Steel: Durable and strong, steel rollers are the standard in many industrial applications, capable of handling heavy loads and resistant to deformation.
- Rubber: Often used to coat steel rollers, rubber provides extra traction and noise reduction, beneficial in environments where operational silence is valued.
- Polyurethane: This material is selected for its exceptional wear resistance and ability to reduce the wear on the conveyor belt itself.
- Nylon: Lightweight and cost-effective, nylon rollers are suitable for lighter applications where reducing system weight is a priority.
- Stainless Steel: Essential for applications requiring sanitary conditions, stainless steel offers excellent resistance to corrosion and contamination.
- Aluminum: Chosen for its strength-to-weight ratio, aluminum rollers are used in applications where reducing overall system weight enhances efficiency.
- Composite Materials: These are engineered for specific properties like enhanced durability or reduced weight, ideal for specialized industrial applications.
- High-Density Polyethylene (HDPE): Known for its low friction and high impact resistance, HDPE is ideal for environments with abrasive conditions.
Understanding the various types and materials of conveyor snub roller helps in selecting the right components for specific applications, thereby enhancing the performance and reliability of conveyor systems.
Conveyor Snub Roller: A Unique Component in Conveyor Systems
Conveyor snub rollers serve a specialized role distinct from other rollers in conveyor systems. They are crucial for maintaining the proper tension and alignment of the conveyor belt, which is essential for efficient operation and to prevent slippage and excessive wear. By understanding the unique properties and functions of snubber roller conveyor compared to other types, organizations can optimize their conveyor setups for better performance and longevity.
Contrast Between Conveyor Snub Roller and Other Rollers
Before diving into specifics, it’s important to understand that each type of roller in a conveyor system has a role that supports the system’s overall functionality. Here’s a more detailed look at how snub rollers compare with idler and drive rollers.
Differences Between Roller Conveyors and Belt Conveyors
Roller conveyors and belt conveyors cater to different needs within the material handling industry, each with its own set of advantages depending on the application.
- Functionality: Roller conveyors excel in transporting solid, rigid items, making them ideal for assembly lines, while belt conveyors can handle a broader range of materials, including loose and delicate items.
- Flexibility: Belt conveyors can easily be configured to include curves and inclines, making them highly adaptable to various spaces and processes.
- Load Capacity: Generally, roller conveyors are constructed to support heavier loads, making them suitable for industrial applications.
- Maintenance: With more moving parts, roller conveyors often demand more regular maintenance compared to the relatively simpler belt conveyors.
- Cost: Though roller conveyors may have a lower initial cost, their maintenance and energy costs can accumulate over time, potentially outweighing the initial savings.
- Speed Control: Belt conveyors provide superior control over the speed at which materials move, which is crucial in applications requiring careful handling of materials.
- Energy Efficiency: Belt conveyors tend to be more energy-efficient, especially over longer distances, as they reduce friction and the associated power loss.
- Noise Level: The operation of roller conveyors typically generates more noise due to the numerous contact points and moving parts, whereas belt conveyors are quieter.
- Application Specificity: Roller conveyors are preferred in applications where precise item placement and orientation are necessary, while belt conveyors are more versatile, supporting a wide range of applications across different industries.
Each type of conveyor system brings its own set of benefits and considerations, influencing the choice between roller and belt conveyors based on the specific requirements of the operation.
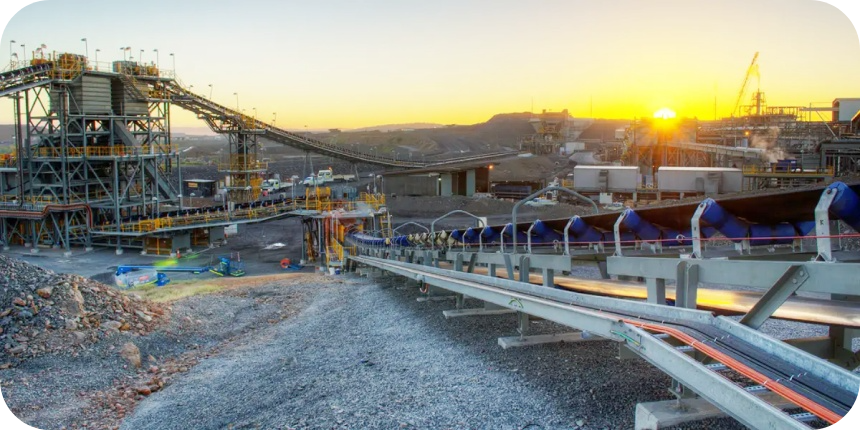
Operational Mechanics of Conveyor Snub Roller
Conveyor snub rollers are an integral component of the conveyor system, which often goes unnoticed yet plays a crucial role in maintaining the efficiency and safety of the entire operation. Positioned strategically along the conveyor frame, snub rollers are designed to enhance the performance of the conveyor belt and ensure its longevity by managing multiple aspects of its operation. These rollers function to enhance contact between the belt and the drive rollers, manage tension and alignment, and respond dynamically to changes in load and operational conditions. This detailed exploration into the mechanics of conveyor snub roller will delve into how they function within conveyor systems and their significant contributions to operational efficiency and safety.
How Conveyor Snub Rollers Work Within Conveyor Systems
In conveyor systems, snub rollers play an essential role in enhancing the system’s performance and reliability. These rollers primarily help to adjust the belt’s tension, correct alignment, and manage friction between the conveyor belt and other rollers. By providing additional contact points for the belt, snub rollers improve the grip and traction, which is crucial for the efficient transport of materials. Here’s a deeper look into their various functions:
Engagement: Conveyor snub rollers are critical in ensuring the belt’s effective engagement with the drive rollers. By increasing the belt’s contact area with the drive rollers, snub rollers enhance traction, which is essential for the stable and efficient movement of materials along the conveyor.
Tension Adjustment: Snub rollers are pivotal in adjusting the belt’s tension. This adjustment capability is vital for keeping the belt adequately tight, preventing slippage, and ensuring smooth operations. Fine-tuning tension is crucial for maintaining the belt’s integrity and operational readiness.
Alignment Correction: Misalignment issues can cause significant disruptions in conveyor operations. Snub rollers play a key role in correcting any deviations in the belt’s path by adjusting their position, guiding the belt back to its intended trajectory and ensuring it runs smoothly.
Load Distribution: These rollers help in evenly distributing the load across the belt’s surface. Uniform load distribution is essential to prevent excessive stress on any part of the belt, which can prolong the belt’s life and reduce the likelihood of premature wear.
Friction Management: Managing the amount of friction between the belt and the rollers is another critical function of snub rollers. By modifying friction levels, they help maintain the desired speed and efficiency of the conveyor, ensuring optimal performance.
Preventive Maintenance: Regular adjustment of snub rollers can preempt maintenance issues by addressing minor deviations before they escalate into more significant problems. This proactive approach in maintenance helps in avoiding unexpected downtime and costly repairs.
Energy Efficiency: The proper use of snub rollers significantly reduces the energy required to operate the conveyor. By minimizing unnecessary resistance and improving the system’s mechanical efficiency, snub rollers contribute to more energy-efficient operations.
Dynamic Response: Snub rollers dynamically respond to changes in the load and belt speed, adjusting the belt tension accordingly. This responsiveness is crucial for maintaining operational stability under varying conditions.
Enhanced Lifespan: By ensuring optimal tension and alignment, snub rollers contribute significantly to extending the operational lifespan of the conveyor belt. This not only improves efficiency but also reduces the frequency and cost of belt replacements.
Contribution of Conveyor Snub Roller to Efficiency and Safety
Reduced Downtime: Effective tension management by snub rollers helps in minimizing operational halts, which are often caused by belt slippage or misalignment. This reduction in downtime is crucial for maintaining productivity and operational flow.
Safety Enhancement: Properly tensioned and aligned belts are less prone to mishaps, thereby enhancing the safety of the conveyor system. This is especially critical in environments where safety is paramount to prevent accidents and injuries.
Operational Consistency: Snub rollers ensure that the belt moves smoothly and consistently, which is essential for maintaining quality control in automated and continuous production lines. Consistency in belt movement helps in achieving uniform product handling and processing.
Wear and Tear Reduction: By reducing the wear on the conveyor belt and other mechanical components, snub rollers decrease the need for frequent repairs and replacements, thereby cutting down on maintenance costs and extending the equipment’s service life.
Improved Product Handling: Better control over the belt movement ensures that materials are handled gently and with care, reducing the likelihood of material damage during transport. This is crucial for industries where product integrity is critical.
Noise Reduction: Well-maintained snub rollers contribute to quieter conveyor operations by stabilizing the belt and reducing vibrations and noise, which is beneficial for creating a more comfortable working environment.
Adaptability to Loads: Snub rollers adapt to varying weights and types of loads, maintaining stability and consistency in the conveyor’s performance. This adaptability is key to handling different materials efficiently.
Prevention of Belt Stretching: They play a significant role in preventing the belt from stretching and becoming misshapen, which can adversely affect the conveyor’s functionality and lead to further issues.
Cost Efficiency: Improving the overall efficiency of the conveyor system through the optimal use of snub rollers helps in reducing operational costs. This cost efficiency is achieved by enhancing performance, reducing wear and tear, and cutting down energy consumption.
Understanding the detailed operational mechanics and significant contributions of conveyor snub roller is essential for optimizing the performance and safety of conveyor systems. These rollers are pivotal in ensuring that the system operates smoothly and efficiently, thus enhancing both the effectiveness and safety of conveyor operations.
How to Choose the Right Conveyor Snub Roller
Selecting the appropriate conveyor snub roller is not just about fitting a component into a system; it’s about enhancing the conveyor’s operational efficiency and prolonging its lifespan. The right snub roller can prevent belt slippage, improve traction, and ensure smooth material flow, thereby reducing downtime and maintenance costs. Additionally, choosing a snub roller that is tailored to specific operational demands and environmental conditions can mitigate the risk of premature wear and failure, ensuring consistent performance under various stresses. When evaluating options, it’s essential to consider a holistic view of your system’s requirements, factoring in load capacities, environmental challenges, and the specific characteristics of the materials being transported. This careful selection process is crucial for optimizing system performance and can result in significant long-term benefits, including energy savings, reduced wear on other conveyor components, and overall system reliability.
Factors to Consider When Selecting Conveyor Snub Roller
When choosing conveyor snub roller, several critical factors must be considered to ensure optimal compatibility and performance within your conveyor system. Each factor plays a significant role in how well the conveyor operates and how long it will last under working conditions. Addressing these considerations will help in selecting a snub roller that enhances the conveyor’s functionality and durability.
- Weight Capacity: It’s vital to select a snub roller that can support the maximum operational load of the conveyor without compromising structural integrity. Overloading a roller can lead to deformation, bearing failure, and system malfunctions, which in turn can cause unexpected shutdowns.
- Belt Size Compatibility: The dimensions of the snub roller must be compatible with the belt width and thickness. A mismatch in size can lead to improper belt support, increased wear, and potential tracking issues, all of which diminish the system’s efficiency and safety.
- Material of Construction: Choose a material that suits the operational environment of the conveyor. For instance, stainless steel rollers are ideal for corrosive environments, while plastic rollers might be preferable in a food production setting for easier cleaning and compliance with hygiene standards.
- Speed Requirements: The snub roller’s design must accommodate the speed of the conveyor belt. High-speed conveyors require rollers that are designed to reduce rotational friction and dissipate heat effectively.
- Maintenance Requirements: Consider rollers that offer ease of maintenance. Features such as easy access to bearings and modular designs that allow for quick replacement can significantly reduce downtime.
- Environmental Conditions: The choice of snub roller must take into account the working environment, such as temperature extremes, moisture, dust, and chemical exposure. Each condition may necessitate different materials or protective measures to ensure longevity and reliability.
- Durability and Wear Resistance: The expected life of the snub roller should align with the operational demands it will face. Rollers designed for high durability and wear resistance are crucial in abrasive environments to prevent frequent replacements.
- Noise Reduction Features: In environments where noise levels are a concern, selecting snub rollers designed to operate quietly can help in complying with regulations and improving the working conditions for personnel.
- Energy Efficiency: Rollers that minimize friction and enhance belt alignment can lead to significant energy savings, especially in large-scale or continuously operating systems.
Customization Options for Conveyor Snub Rollers
Customization of conveyor snub rollers allows for enhanced adaptation to specific system requirements and environmental conditions. By selecting rollers with specific features, you can significantly improve the conveyor’s performance, reduce maintenance needs, and extend the lifespan of both the rollers and the conveyor belt.
- Coating Options: Different coatings can enhance grip, reduce material buildup, and extend roller life. For example, rubber coatings provide increased friction for better belt traction, while non-stick coatings like Teflon are ideal for sticky or wet materials.
- Adjustability Features: Adjustable snub rollers allow for fine-tuning belt tension and alignment, which is critical for maintaining optimal performance and preventing wear. These features enable quick adjustments during regular maintenance checks or under varying load conditions.
- Sealed Bearing Options: In dusty or moist environments, snub rollers with sealed bearings protect against contaminants that can degrade bearing life and lead to roller failure. This feature is crucial for maintaining smooth operation without frequent bearing replacements.
- High-Temperature Resistance: For operations that involve high temperatures, snub rollers can be customized with materials that withstand heat without degrading. This is particularly important in industries like metal processing or ceramics manufacturing.
- Anti-Static Properties: In environments where static electricity is a concern, such as in the electronics manufacturing or explosive materials handling sectors, snub rollers with anti-static properties prevent static buildup, ensuring safety and compliance with industry standards.
- Health and Safety Compliance: Rollers can be designed to meet specific regulatory compliance requirements, such as those for food safety or pharmaceutical production, where non-toxic, easy-to-clean materials are essential.
- Color Coding: Implementing a color-coding system for snub rollers can facilitate maintenance schedules and ensure timely
Choosing the right conveyor snub roller involves considering a combination of load requirements, environmental conditions, and operational demands. By tailoring the selection and customization of snub rollers, conveyor systems can achieve improved efficiency, reduced maintenance, and longer service life, contributing significantly to the overall productivity and safety of the operation.
Market Options for Conveyor Snub Roller
Choosing the right conveyor snub roller involves navigating through various market options, especially when considering used components. Understanding where to find used conveyor snub rollers and ensuring their quality and compatibility with your existing system is crucial. This guide will offer structured advice on both finding used snub rollers and ensuring they meet your needs.
Information on Finding and Choosing Used Conveyor Snub Roller
The market for used conveyor snub rollers offers significant cost savings, but it also requires careful scrutiny to ensure you are getting a component that will function reliably in your conveyor system. Here are the detailed points to guide you through this process:
- Online Industrial Marketplaces: Websites like eBay, Amazon, and specialized industrial platforms can be excellent sources for used snub roller conveyor. Use specific search terms related to your needs, and filter results by condition, location, and price to narrow down suitable options.
- Surplus and Refurbished Equipment Dealers: These dealers often have a good selection of used or refurbished conveyor snub roller. They usually provide some form of guarantee or certification of the equipment’s condition, which can offer peace of mind.
- Direct Purchases from Manufacturing Facilities: Some manufacturing companies sell their surplus or replaced components directly. Contacting local manufacturers might lead to finding high-quality used snub rollers that are no longer needed due to system upgrades or changes.
- Industrial Auctions: Industrial auctions, both online and offline, frequently feature conveyor components. These can be a goldmine for finding robust equipment at lower prices, but you must be prepared to inspect the rollers personally or understand the auction’s terms for equipment sales.
- Networking in Industry Forums and Trade Groups: Engaging with peers in conveyor-related industries can lead to tips on where to find used snub rollers. Networking can often open up opportunities that are not advertised publicly.
- Specialized Conveyor System Consultants: These professionals can offer guidance and potentially direct you to sources of used conveyor components. They typically have extensive networks and knowledge about where to find specific items.
- Trade Shows and Industrial Fairs: Attending industry-specific trade shows can connect you with sellers and manufacturers who have used snub rollers on offer. These events also allow for direct negotiation and inspection of the goods.
- Equipment Rental Outlets: Some companies that rent out conveyor systems may also offer used components for sale. Since these outlets regularly maintain and replace their inventory, they often have used snub rollers in good condition.
- Local and Online Classified Ads: Keep an eye on classified sections in industry magazines or websites where businesses often advertise surplus machinery and components for sale.
- Reclamation Centers and Demolition Sites: Industrial reclamation centers and sites where facilities are being demolished can sometimes yield used conveyor components. This requires visiting the site to inspect and potentially remove the rollers.
Tips on Where to Find Snub Rollers for Sale and How to Ensure Quality and Compatibility
Once you know where to look for snub rollers, the next step is ensuring that what you find will serve your needs without causing additional issues. These tips will help you assess the quality and compatibility of conveyor snub roller before making a purchase.
- Detailed Inspection: Examine used conveyor snub roller for signs of wear and damage, such as cracks, excessive wear on bearings, or deformation. If possible, see the rollers in operation or request a video if buying remotely.
- Manufacturer’s Specifications: Always compare the specifications from the manufacturer with the requirements of your conveyor system. This includes checking the load capacity, size, material, and suitability for the environment (e.g., wet, corrosive).
- Seek Seller Guarantees: Ask for some form of guarantee or return policy from the seller. This can provide recourse if the purchased snub rollers fail to meet expected standards or performance levels.
- Professional Evaluation: If you’re not sure about the technical aspects, consider hiring an expert to assess the rollers. This can be particularly important for high-value purchases or when the rollers are critical to your operation’s uptime.
- Compatibility Testing: Ensure that the snub rollers will integrate smoothly with your existing system. This might involve checking the fitting, attachment points, and interaction with the conveyor belt.
- References and Reviews: Check references or reviews for the sellers to gauge their reliability and the quality of their equipment. Previous customer experiences can provide insights into what you can expect.
- Negotiation Based on Condition: Use the condition of the snub rollers as a leverage point in negotiations. Better understanding the condition can give you an upper hand in negotiating prices.
- Warranty and Support: Prefer sellers who offer after-sales support or a warranty period. This support can be invaluable in addressing any issues that arise shortly after installation.
By carefully considering where to find and how to assess used conveyor snub roller, you can make informed decisions that contribute to the efficiency and cost-effectiveness of your conveyor.
Get expert advice on choosing the best conveyor rollers.
FAQs about Conveyor Snub Roller
A snub roller is an essential component of a conveyor system that plays a critical role in enhancing the performance and efficiency of the conveyor belt. Positioned closely to the drive rollers, snub rollers increase the belt’s contact area with the drive, which improves the traction and enables the belt to carry heavier loads more effectively. Additionally, snub rollers are instrumental in maintaining the proper tension and alignment of the conveyor belt. By adjusting the position of the snub rollers, operators can fine-tune the belt’s tension to prevent slippage and misalignment. This not only helps in ensuring smooth operations but also extends the life of the belt by distributing the load evenly and reducing wear. Overall, snub rollers are pivotal in the preventive maintenance and energy efficiency of conveyor systems, dynamically responding to varying conditions and operational demands.
The rollers on a conveyor are generally called conveyor rollers. These rollers are cylindrical components that rotate to move the conveyor belt along the desired path. Conveyor rollers are crucial in supporting the conveyor belt and the material being transported. They vary in type and size depending on their function within the conveyor system. The main types include drive rollers, which power the belt’s movement; idler rollers, which provide support and maintain the path of the belt; and snub rollers, which increase the belt’s tension and contact with drive rollers. Each type of roller is specifically designed to fulfill a particular role, contributing to the efficiency and effectiveness of the conveyor system.
Roller conveyors are versatile systems used to transport a variety of materials across different industries. They are classified based on the mechanism of operation and the type of loads they handle. The primary types of roller conveyors include:
Gravity Roller Conveyors: These use the force of gravity to move items across a downward-sloping path. They are ideal for moving items with a flat base and are commonly used in picking and packing facilities.
Powered Roller Conveyors: These conveyors use powered rollers to move items along the conveyor path. They can be powered by belts, chains, or motors and are suitable for handling heavy loads.
Live Roller Conveyors: A subtype of powered conveyors, live roller conveyors use rollers that are directly powered by motors, which allows for control of the speed and movement of the conveyor belt.
Flexible Roller Conveyors: These are designed to be flexible and can be adjusted to various shapes (like curves) to fit different spaces and needs. They can be either gravity or powered and are ideal for loading docks and other areas where space is a constraint.
Each type of roller conveyor has distinct advantages and is selected based on the specific needs of the operation, including the type of materials handled, the required speed of transport, and the layout of the installation space.
Conveyors feature several types of rollers, each serving a specific function in the conveyor system:
Drive Rollers: These are the primary powered rollers that drive the conveyor belt’s movement. They are typically coated with rubber or another material to increase friction for better traction.
Idler Rollers: These rollers provide passive support to the conveyor belt and are positioned along the conveying path to hold the belt up and ensure it maintains a consistent path.
Snub Rollers: Positioned close to the drive rollers, snub rollers increase the belt’s contact with the drive rollers, enhancing traction and allowing for better belt tension adjustment.
Impact Rollers: Installed at points where material is dropped onto the belt, impact rollers help absorb the shock and distribute the load, preventing damage to the conveyor belt.
Understanding the specific roles and types of rollers can help in designing an efficient conveyor system tailored to an operation’s specific needs.
Last Updated on July 18, 2024 by Jordan Smith
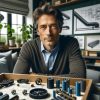
Jordan Smith, a seasoned professional with over 20 years of experience in the conveyor system industry. Jordan’s expertise lies in providing comprehensive solutions for conveyor rollers, belts, and accessories, catering to a wide range of industrial needs. From initial design and configuration to installation and meticulous troubleshooting, Jordan is adept at handling all aspects of conveyor system management. Whether you’re looking to upgrade your production line with efficient conveyor belts, require custom conveyor rollers for specific operations, or need expert advice on selecting the right conveyor accessories for your facility, Jordan is your reliable consultant. For any inquiries or assistance with conveyor system optimization, Jordan is available to share his wealth of knowledge and experience. Feel free to reach out at any time for professional guidance on all matters related to conveyor rollers, belts, and accessories.