Conveyor Training Idlers: Tracking And Trainer
Conveyor training idlers are essential components in the efficient operation of conveyor systems, playing a pivotal role in maintaining belt alignment, a crucial aspect of conveyor functionality. These specialized idlers are strategically positioned along the conveyor path to ensure the belt remains centered, thus preventing the common issues of belt wandering or mistracking. The unique design of conveyor training idlers allows them to pivot and guide the belt back to its optimal path whenever misalignment occurs. This not only enhances the longevity of the conveyor belt but also ensures smooth and uninterrupted material flow. By maintaining proper belt alignment, conveyor training idlers significantly reduce the risk of material spillage and equipment damage, thereby optimizing the overall efficiency and safety of the conveyor system.
The Purpose and Functionality of Conveyor Training Idlers
- Maintaining Belt Alignment: Conveyor training idlers are specifically engineered to keep the conveyor belt on track. Their primary function is to prevent the belt from drifting off its intended path, a common issue known as belt wandering or mistracking.
- Detecting and Correcting Misalignment: These idlers are equipped with rollers that can pivot in response to the belt’s movement. When the belt begins to drift sideways, the idlers detect this deviation and adjust their position accordingly. This self-correcting action gently steers the belt back towards the center line of the conveyor.
- Preventing Operational Inefficiencies: By ensuring that the belt remains aligned, conveyor training idlers play a crucial role in avoiding operational problems. Misaligned belts can lead to material spillage, uneven wear on the belt, and potential damage to the conveyor structure, all of which can cause significant downtime and repair costs.
- Enhancing Safety and Longevity: The functionality of conveyor training idlers is not just limited to maintaining efficiency; it also enhances the safety of the conveyor system. Proper belt alignment minimizes the risk of accidents and extends the lifespan of the conveyor belt and other components by reducing unnecessary stress and wear.
- Self-Adjusting Mechanism: The unique aspect of conveyor training idlers is their ability to self-adjust in real-time. This feature is crucial for continuous and unattended operations, where manual adjustments to the belt alignment are impractical.
- Addressing Belt Wandering Issues: Conveyor training idlers are particularly effective in addressing the challenges posed by belt wandering. This phenomenon, if left unchecked, can lead to operational disruptions and increased maintenance requirements.
- Optimizing Conveyor Efficiency: By maintaining proper belt alignment, conveyor training idlers ensure smooth and uninterrupted material flow. This optimization is key to maintaining the overall efficiency and productivity of the conveyor system.
- Versatility in Application: These idlers are versatile and can be used in various types of conveyor systems, making them an essential component across a wide range of industrial applications.
The Features of Training Idlers
Training idlers are specialized components used in conveyor systems, designed to stabilize the conveyor belt’s path and maintain its proper alignment. Here’s a detailed look at the features of training idlers:
- Adjustability: Training idlers are adjustable, allowing them to be precisely positioned to steer the conveyor belt towards the center of the conveyor frame. This adjustability is crucial for preventing the belt from wandering off its intended path, which can lead to uneven wear, spillage, and other operational issues.
- Self-correcting mechanism: Many training idlers are designed with a self-aligning feature that automatically corrects the belt’s position as it moves. This self-correcting mechanism can be based on the tilting action of the idler frame, which pivots in response to any misalignment of the belt.
- Variety of designs: Training idlers come in various designs to suit different types of conveyor systems and operational requirements. Common types include pivot and tilt idlers, which use a central pivot point to guide the belt, and troughing training idlers, which have multiple rolls set at angles to form a trough shape that helps center the belt.
- Durable construction: These idlers are built to withstand the harsh conditions of conveyor operations, including dust, moisture, and varying loads. Materials such as steel, reinforced polymers, and rubber coatings are commonly used to enhance durability and reduce wear.
- Ease of maintenance: Training idlers are designed for easy maintenance to minimize downtime. Many models feature easy-to-access components and require minimal tools for adjustment or replacement, ensuring that conveyor maintenance is efficient and straightforward.
- Impact resistance: Especially in applications where the conveyor belt carries heavy or abrasive materials, training idlers are designed to absorb impact and reduce the stress on the belt. This feature extends the life of both the belt and the idler.
- Energy efficiency: Properly aligned conveyor systems are not only safer and more reliable but also more energy-efficient. Training idlers help reduce the energy consumption of the conveyor system by minimizing friction and resistance caused by misalignment.
These features make training idlers an essential part of modern conveyor systems, enhancing operational efficiency and safety while reducing maintenance costs and downtime.
Types of Conveyor Training Idlers
Conveyor training idlers come in various types, each designed to address specific needs within conveyor systems. The most common conveyor idler types include self-aligning carrying idlers, troughing idlers, impact idlers, and V-return idlers.
- Self-Aligning Carrying Idlers: These are designed to automatically adjust the belt alignment. They are particularly useful in situations where the conveyor belt tends to shift side to side. Their self-aligning feature ensures that the belt stays centered, thus reducing wear and tear.
- Troughing Idlers: Troughing idlers are used to shape the belt into a trough for carrying bulk materials. They consist of a center roller and two wing rollers at an angle, which helps in holding the material on the belt.
- Impact Idlers: Positioned at the loading points, impact idlers are designed to absorb the shock and impact of heavy materials falling onto the belt. They help in extending the lifespan of the conveyor belt by reducing the stress at these critical points.
- V-Return Idlers: These idlers roller are used on the return side of the conveyor. Their V-shaped design helps in maintaining belt tracking and preventing the belt from slipping off the rollers.

A notable example of an advanced training idler is the ASGCO Tru-Trainer. This idler stands out for its ability to provide continuous alignment, which is crucial in preventing misalignment-related issues. The Tru-Trainer is designed to react and compensate instantly to belt misalignment, ensuring that the belt remains centered. Its unique design allows it to be used in various applications, making it a versatile solution for conveyor belt alignment issues. The ASGCO Tru-Trainer represents a significant advancement in the technology of conveyor training idlers, offering enhanced reliability and efficiency.
Components and Working Principle of Conveyor Training Idlers
Conveyor training idlers consist of several key components that work together to maintain the alignment and efficiency of conveyor belts. The primary components include conveyor idler rollers and conveyor belt guide rollers.
Conveyor Idler Rollers: These are cylindrical rods that form the main part of the idler. They are designed to support the conveyor belt and the material being transported. The rollers are mounted on a frame and can rotate freely, which allows the belt to move smoothly over them.
Conveyor Belt Guide Rollers: These rollers are positioned on the sides of the conveyor belt and play a crucial role in guiding and aligning the belt. They prevent the belt from veering off its intended path and help to correct any misalignment that may occur during operation.
The working principle of self-aligning carrying idlers is centered around their ability to automatically adjust the position of the belt to ensure it remains aligned. These idlers are uniquely designed with a pivoting mechanism that responds to any misalignment of the belt. When the belt begins to drift off-center, the idler detects this movement and the rollers tilt slightly, guiding the belt back to its correct position. This self-adjusting action is crucial for maintaining the smooth operation of the conveyor system, reducing wear and tear on the belt, and preventing potential system failures or material spillage. The self-aligning carrying idlers are particularly beneficial in environments where the conveyor belt is subject to varying loads, directional changes, or other operational conditions that might lead to misalignment.

Installation and Location of Conveyor Training Idlers
The effective installation and strategic location of conveyor training idlers are crucial for the optimal performance of a conveyor system. Proper placement and installation not only enhance the functionality of the conveyor but also extend the lifespan of the conveyor belt.
1.Guidelines for Installation Location: Conveyor training idlers should be installed at specific points where misalignments are most likely to occur. These locations typically include the conveyor’s loading and unloading areas, where the belt is subjected to varying weights and directional changes. Additionally, placing them near the head and tail pulleys can be beneficial, as these are critical points where the belt changes direction.
2.Tips for Proper Installation: To ensure optimal performance, it is essential to follow these installation tips:
- Alignment: Ensure that the conveyor training idlers are perfectly aligned with the belt path. Misaligned idlers can cause more harm than good, leading to increased wear and tear.
- Spacing: The spacing between each idler should be consistent and in accordance with the manufacturer’s recommendations. Incorrect spacing can lead to uneven belt wear and reduced efficiency.
- Secure Mounting: Idlers must be securely mounted to prevent any wobbling or shifting during operation. A stable idler is crucial for consistent performance.
- Adjustability: Some conveyor training idlers come with adjustable features. Utilize these to fine-tune the idler’s position for precise belt alignment.
- Regular Inspection: After installation, regular inspections are necessary to ensure that the idlers are functioning correctly and to make any needed adjustments or replacements.
By adhering to these guidelines and tips, the conveyor training idlers can be installed effectively, ensuring that the conveyor system operates smoothly and efficiently, with minimal downtime and maintenance requirements.
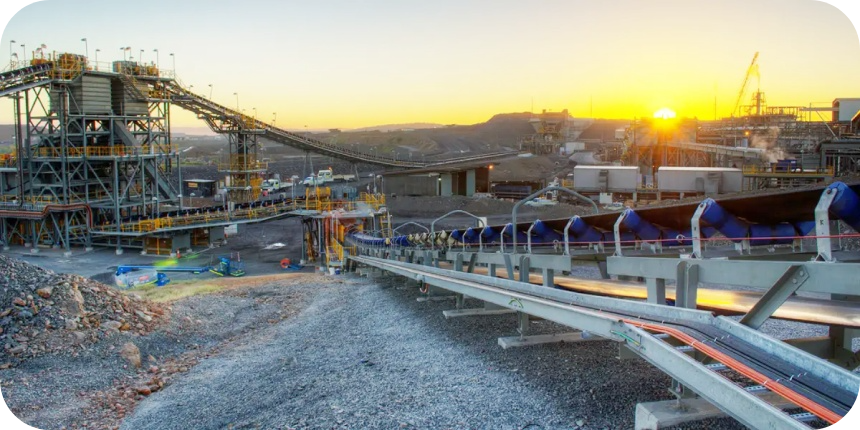
Precautions for installation of conveyor training rollers
Installing conveyor training rollers (also known as training idlers) requires careful attention to detail to ensure proper alignment and function of the conveyor belt. Here are some key precautions to consider during the installation process:
- Read Manufacturer’s Instructions: Before installation begins, thoroughly read and understand the manufacturer’s instructions. Different types of training rollers may have specific requirements or recommendations for installation.
- Check Conveyor Alignment: Before installing the training rollers, ensure the conveyor framework is correctly aligned. Misalignment of the structure can lead to uneven loading on the belt and premature wear or failure of the rollers.
- Proper Placement: Training rollers should be placed strategically along the conveyor belt path. Typically, they are installed where misalignments are most likely to occur, such as loading and unloading points. The correct placement helps in effectively steering the belt back to its central path.
- Secure Mounting: Ensure that all mounting brackets and hardware are tightly secured. Loose components can lead to ineffective training of the belt and may cause damage to the belt and the rollers.
- Adjustable Installation: Install the training rollers so they are easily adjustable. As the conveyor belt operates, it might require re-adjustment to maintain proper alignment. The ability to easily adjust the rollers is critical for ongoing maintenance and efficiency.
- Test for Free Movement: After installation, check that the rollers can rotate freely without any hindrance. Any resistance in rotation could indicate improper installation or misalignment, which needs correction before full operation.
- Initial Testing: Conduct initial testing with the conveyor running empty. Observe the behavior of the belt and the training rollers to ensure that they are functioning as intended. Look for smooth operation and effective realignment of the belt.
- Load Testing: After successful empty testing, run the conveyor with a load. This helps to see how the belt and rollers perform under operational conditions. Monitor for any shifts in the belt path and make adjustments as necessary.
- Regular Inspection: After installation, schedule regular inspections to monitor the condition and effectiveness of the training rollers. Adjust, repair, or replace parts as needed based on these inspections to maintain optimal performance.
- Safety Precautions: Always follow safety guidelines during installation. Ensure that the conveyor system is locked out and tagged out during the installation process to prevent accidental activation. Use appropriate personal protective equipment (PPE) to safeguard against potential hazards.
By following these precautions, you can help ensure that your conveyor training rollers are installed correctly and function eff
Selecting the Best Conveyor Training Idlers
Choosing the best conveyor training idlers is pivotal for ensuring the optimal performance and longevity of conveyor systems. The selection process involves considering various criteria and understanding the features that distinguish high-quality idlers.
Criteria for Choosing the Best Idlers:
- Application Specifics: Understand the specific requirements of your conveyor system. Factors like the type of material being conveyed, the load weight, and the conveyor speed influence the choice of idlers.
- Environmental Conditions: Consider the operating environment. Idlers used in harsh conditions, such as extreme temperatures or corrosive environments, require more robust construction.
- Compatibility: Ensure that the idlers are compatible with your conveyor system in terms of size, belt width, and design.
- Adjustability and Flexibility: Look for idlers that offer adjustability for precise alignment and flexibility to accommodate various operational conditions.
Features That Make Idlers Stand Out:
- Durability: High-quality conveyor training idlers are made from materials that can withstand wear and tear, ensuring a longer lifespan.
- Efficiency: Efficient idlers contribute to lower energy consumption of the conveyor system by reducing friction and resistance.
- Ease of Maintenance: Idlers that are easy to install, adjust, and replace can significantly reduce downtime and maintenance costs.
- Innovative Design: Some idlers come with advanced features like self-cleaning mechanisms or shock-absorbing capabilities, which can be particularly beneficial in specific applications.
Selecting the best conveyor training idlers requires a thorough understanding of your conveyor system’s needs and an evaluation of the idlers’ features. The right choice not only enhances the efficiency and reliability of the conveyor but also contributes to reduced operational costs and increased productivity.

How to Select the Best Conveyor Training Idlers
Selecting the best conveyor training idlers involves considering various factors to ensure that the conveyor system operates efficiently and with minimal maintenance. Here are key steps and considerations to guide you in selecting the right training idlers:
Assess Belt Requirements:
- Belt Width: Choose idlers that are compatible with the width of your conveyor belt to ensure effective support and guidance.
- Material Handled: Consider the type of materials the conveyor will carry. Heavier and more abrasive materials require more robust and durable idlers.
Choose the Right Type:
- Troughing vs. Return Idlers: Troughing idlers are used on the carrying side of the belt, while return idlers support the return side. Decide based on which section of the belt requires training.
- Self-aligning Idlers: These idlers automatically adjust the belt alignment, making them suitable for longer and more critical conveyor systems where misalignment issues are frequent.
Look for Quality and Durability:
- Material Construction: Ensure the idlers are made from high-quality materials that can withstand wear and tear, such as steel with corrosion-resistant coatings or heavy-duty polymers.
- Design Features: Look for features that enhance durability, such as sealed bearings and dust-proof covers.
Consider the Operating Environment:
- Environmental Conditions: If the conveyor operates in a harsh environment (e.g., extreme temperatures, corrosive environments), select idlers designed to withstand these conditions.
- Safety and Compliance: Ensure the idlers comply with industry safety standards and regulations.
Evaluate Manufacturer and Supplier:
- Reputation and Experience: Choose a manufacturer with a proven track record in the industry. Experienced suppliers are more likely to provide reliable and high-quality products.
- Support and Service: Consider the level of support the supplier offers, including availability of spare parts and their capability to provide maintenance services.
Cost-Effectiveness:
- Initial Cost vs. Long-Term Savings: While higher-quality idlers may be more expensive initially, they can offer greater long-term savings due to reduced maintenance costs and downtime.
- Energy Efficiency: Efficient idlers reduce the power consumption of the conveyor system, saving on energy costs.
Customization Options:
- Adjustability: Some idlers offer adjustable features to fine-tune the conveyor alignment based on specific operational needs.
- Custom Designs: Depending on your conveyor’s specific requirements, you might need custom-designed idlers to meet unique operational challenges.
By carefully considering these factors, you can select the best conveyor training idlers that will enhance the efficiency and reliability of your conveyor system while minimizing maintenance and operational costs.
Pricing and Budget Considerations for Conveyor Training Idlers
Understanding the pricing of conveyor training idlers is crucial for effective budgeting and ensuring that you get the best value for your investment. The price of conveyor training idlers can vary significantly based on several factors.
Factors Affecting Conveyor Training Idlers Price
- Material Quality: High-grade materials typically command a higher price due to their durability and longevity.
- Design Complexity: Advanced features like self-cleaning mechanisms or shock-absorbing capabilities can add to the cost.
- Brand and Manufacturer: Established brands with a reputation for quality may offer their products at a premium.
- Size and Customization: Larger idlers or those requiring customization to fit specific conveyor systems can be more expensive.
- Operational Environment: Idlers designed for harsh or specialized environments may have additional cost implications.
Tips for Budgeting and Finding Cost-Effective Solutions
- Assess Total Cost of Ownership: Consider not just the initial purchase price but also long-term costs like maintenance, replacement, and operational efficiency.
- Compare Different Suppliers: Research and compare prices from various suppliers to find the best deal.
- Don’t Compromise on Quality: Investing in high-quality idlers can be more cost-effective in the long run due to lower maintenance costs and longer service life.
- Bulk Purchases: If possible, buy in bulk to benefit from volume discounts.
- Look for Warranties and Support: Products with warranties or those from suppliers offering good customer support can offer more value for your investment.
By carefully considering these factors and tips, you can make informed decisions that balance cost with quality, ensuring that your conveyor system operates efficiently without exceeding your budget.
Maintenance and Troubleshooting of Conveyor Training Idlers
Regular maintenance and effective troubleshooting are key to ensuring the longevity and efficiency of conveyor training idlers. Proper care not only extends the life of these components but also maintains the overall health of the conveyor system.
Regular Maintenance Practices:
- Routine Inspections: Conduct regular inspections of conveyor training idlers for signs of wear, damage, or misalignment. This should include checking for smooth roller rotation and proper alignment.
- Lubrication: Ensure that idlers are adequately lubricated. This is crucial for idlers with moving parts to prevent friction and wear.
- Cleaning: Keep the idlers clean from debris and material build-up, which can cause the rollers to stick or malfunction.
- Adjustments: Periodically check and adjust the alignment of the training idlers to ensure they are effectively guiding the conveyor belt.
- Replacement Schedule: Follow a scheduled replacement plan based on the manufacturer’s recommendations and the operational conditions of the conveyor.
Common Issues and Troubleshooting Tips:
- Belt Misalignment: If the belt is not tracking properly, check if the training idlers are correctly aligned and functioning. Misaligned or stuck idlers can cause the belt to drift.
- Excessive Noise or Vibration: Unusual noise or vibration can indicate worn-out bearings or rollers. Inspect and replace any faulty components.
- Roller Sticking or Not Turning: This can be caused by material build-up or lack of lubrication. Clean and lubricate the rollers to ensure they move freely.
- Rapid Wear: If idlers are wearing out faster than usual, check for improper loading of the belt or misalignment. Ensure that the load is evenly distributed and the belt is properly aligned.
By adhering to these maintenance and troubleshooting guidelines, the performance and lifespan of conveyor training idlers can be maximized, contributing to the overall efficiency and reliability of the conveyor system. Regular upkeep not only prevents downtime but also ensures safe and smooth operation.
The integration of the right conveyor training idlers is paramount in ensuring the efficiency, safety, and longevity of conveyor systems. These idlers play a critical role in maintaining belt alignment, preventing mishaps like belt wandering and material spillage, and reducing wear and tear on the conveyor belt. The selection of appropriate conveyor training idlers, considering factors such as the operational environment, load characteristics, and specific conveyor requirements, is essential. High-quality idlers, characterized by durability and efficiency, not only enhance the performance of the conveyor system but also contribute to significant cost savings in the long run through reduced maintenance and downtime.
We encourage readers to assess their current conveyor systems and consider the potential benefits of upgrading to suitable conveyor training idlers. Whether it’s for a new installation or an existing system, the right choice of idlers can lead to improved operational efficiency, reduced maintenance costs, and a safer working environment. Remember, the investment in quality conveyor training idlers is an investment in the productivity and longevity of your conveyor system. By prioritizing the health and efficiency of your conveyor system with the right components, you ensure its optimal performance and contribute to the overall success of your operations.
High-performance conveyor idlers tailored to meet your specific needs!
FAQs about Conveyor Training Idlers
A training idler is a specialized type of idler used in conveyor systems to ensure that the conveyor belt remains aligned on its path. It plays a crucial role in preventing the belt from drifting sideways, which can lead to operational inefficiencies, increased wear and tear, and potential safety hazards. The training idler is designed to pivot and guide the belt back towards the center if it starts to drift off to one side. This is achieved through a self-adjusting mechanism that responds to the belt’s movement. By maintaining proper belt alignment, training idlers help in reducing material spillage, minimizing the risk of damage to the conveyor belt, and ensuring smooth and uninterrupted material flow. Their use is essential in maintaining the longevity and efficiency of conveyor systems.
A self-training idler is used in conveyor systems to automatically correct any misalignment of the conveyor belt. Its primary function is to prevent the belt from wandering or mistracking, which can cause several operational problems. The self-training idler is equipped with a mechanism that allows it to pivot in response to the belt’s movement, guiding the belt back to its proper path. This feature is particularly beneficial in environments where the conveyor belt is subject to varying loads, directional changes, or other operational conditions that might lead to misalignment. By ensuring that the belt remains centered, self-training idlers play a vital role in reducing wear and tear on the belt, preventing material spillage, and maintaining the overall efficiency and safety of the conveyor system.
Training a conveyor belt involves adjusting the belt and the conveyor system to ensure that the belt runs straight and true. This process typically includes several steps:
1. Inspect the Conveyor: Check the entire conveyor structure for any misalignments or damage that could affect the belt’s path.
2. Adjust the Idlers: Conveyor training idlers can be adjusted to guide the belt back to the center. This is done by tilting the idlers in the direction where the belt needs to be guided.
3. Check the Belt Tension: Ensure that the belt is correctly tensioned. An overly tight or loose belt can cause misalignment.
4. Test and Observe: Run the conveyor and observe the belt’s movement. Make incremental adjustments to the idlers and tension as needed until the belt runs centrally.
5. Regular Maintenance: Regularly inspect and maintain the conveyor and its components to prevent future misalignments.
An example of an idler in a conveyor system is a flat return idler. This type of idler consists of a single horizontal roller that supports the return side of the conveyor belt. Flat return idlers are used to support the belt as it cycles back to the beginning of the conveyor system after unloading its cargo. They are essential in maintaining the structural integrity of the belt and ensuring smooth operation. Flat return idlers are typically spaced further apart than carrying idlers since the return side of the belt does not carry a load.
Several types of idlers are used in belt conveyor systems, each serving a specific purpose:
1. Carrying Idlers: These support the loaded side of the belt and are usually arranged in a trough shape to hold the material on the belt.
2. Impact Idlers: Located at the loading point, these idlers are designed to absorb the impact of material falling onto the belt, thereby protecting the belt from damage.
3. Return Idlers: These support the return side of the belt and are usually flat and spaced further apart.
4. Self-Aligning Idlers: These are used to automatically correct any misalignment of the belt.
5. Troughing Idlers: These form the belt into a trough shape, ideal for transporting bulk materials.
Each type of idler plays a vital role in the efficiency and longevity of a conveyor system.
Last Updated on August 19, 2024 by Jordan Smith
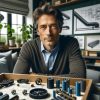
Jordan Smith, a seasoned professional with over 20 years of experience in the conveyor system industry. Jordan’s expertise lies in providing comprehensive solutions for conveyor rollers, belts, and accessories, catering to a wide range of industrial needs. From initial design and configuration to installation and meticulous troubleshooting, Jordan is adept at handling all aspects of conveyor system management. Whether you’re looking to upgrade your production line with efficient conveyor belts, require custom conveyor rollers for specific operations, or need expert advice on selecting the right conveyor accessories for your facility, Jordan is your reliable consultant. For any inquiries or assistance with conveyor system optimization, Jordan is available to share his wealth of knowledge and experience. Feel free to reach out at any time for professional guidance on all matters related to conveyor rollers, belts, and accessories.