Maximizing Efficiency with Crusher Conveyor Rollers
Crusher conveyor rollers are essential components in the bulk material handling industry, playing a pivotal role in the efficient operation of conveyor systems. These rollers are specifically designed to facilitate the smooth transportation of materials through crushing machines, which is crucial in sectors like mining, construction, and aggregate production. The functionality of crusher conveyor rollers directly impacts the effectiveness and productivity of these sectors by ensuring continuous, reliable movement of crushed materials. This introduction explores not only what crusher conveyor rollers are, but also their significance in maintaining the flow and quality of operations in various heavy industries. Understanding these roles highlights the importance of selecting, maintaining, and optimizing the right types of rollers for different applications.
The Critical Role of Crusher Conveyor Rollers in Crushing Processes
Crusher conveyor rollers are instrumental in the crushing industry, serving as the backbone for material handling systems. Their primary function is to support and propel conveyor belts loaded with raw materials through the crushing apparatus. The effectiveness of these rollers directly influences the efficiency and throughput of the entire crushing process.
- Consistent Material Feed: Crusher conveyor rollers ensure a steady and consistent feed of materials into the crusher, which is crucial for maintaining the efficiency of the crushing process. Irregular feeds can lead to operational disruptions and increased wear on machinery.
- Reduction in Downtime: Well-maintained crusher conveyor rollers minimize unexpected downtime by reducing the risk of belt slippage and misalignment, which are common causes of operational delays in the crushing process.
- Energy Efficiency: Efficient crusher conveyor rollers help in reducing the energy consumption of the motor driving the belts. A smoother roller operation requires less power to move heavy loads, which contributes to overall energy savings.
- Extended Equipment Lifespan: By reducing the stress and strain on the conveyor belts and the crusher itself, high-quality crusher conveyor rollers extend the lifespan of the entire system. This minimizes the frequency and cost of repairs and replacements.
- Enhanced Safety: Properly functioning crusher conveyor rollers contribute to safer workplace environments by preventing accidents associated with equipment malfunction, such as belt derailments or blockages.
Understanding how crusher conveyor rollers work and their impact on operations can significantly enhance operational efficiency. These rollers bear the weight of loaded belts, facilitating the smooth and uninterrupted flow of materials. The role of these rollers extends beyond mere support—they condition the belt to appropriately release the material into the crushing mechanism, ensuring uniformity in size after processing. This consistency is critical for the quality control of output materials and impacts subsequent processes and product quality. Therefore, the reliability and performance of crusher conveyor rollers are key to the overall productivity and profitability of crushing operations.
What is the Variety of Crusher Conveyor Rollers
Crusher conveyor rollers come in various types, each designed to meet specific operational needs within crushing and processing environments. Understanding the differences among these rollers can guide users in selecting the right type for their system, thereby enhancing performance and durability.
- Beater Rollers: These crusher conveyor rollers are utilized primarily to clean the conveyor belt and ensure material is evenly distributed across the belt’s surface. Their robust construction helps in breaking up clumps of material, facilitating smoother processing.
- Center and Return Rollers: These are essential components of the conveyor system, used to support the return side of the conveyor belt. Efficient center and return rollers ensure that the belt travels smoothly and stays aligned, which is crucial for optimal operation and minimal wear.
- Disc Rollers: Disc rollers are designed with a series of discs that extend the life of the belt by reducing the build-up of materials on the roller, which is particularly useful in handling sticky or wet materials.
- Impact Rollers: Placed at the loading points, impact rollers absorb the shock and impact of falling materials, protecting the belt and system from damage. These are critical in heavy-duty operations where large quantities of material are dumped onto the conveyors.
- Spiral Rollers: Designed to combat material build-up, spiral rollers have a unique configuration that helps to clean the belt while maintaining contact. They are particularly effective in environments where traditional rollers suffer from excessive material accumulation.
Roller Conveyor Systems: Roller conveyors are versatile systems used to move materials through manufacturing or processing facilities. They are beneficial for their ability to handle a wide range of materials, reduce labor costs, increase safety, speed up workflow, and enhance material handling efficiency.
- Durability: Strong construction materials ensure that roller conveyors can handle heavy loads without significant wear, leading to longer service lives.
- Flexibility: Modular designs make roller conveyors adaptable to various tasks and space configurations in industrial settings.
- Safety: With fewer moving parts compared to other types of conveyors, roller conveyors are generally safer for workers.
- Efficiency: Roller conveyors facilitate the quick and easy transport of goods across different sections of a production facility, improving overall operational efficiency.
- Scalability: Easy to scale up or modify as production needs change, making them suitable for growing businesses.
For those seeking to purchase crusher conveyor rollers, options vary from online industrial equipment retailers to local manufacturers. Online platforms often provide a broader selection of models and competitive prices, whereas local suppliers offer the advantage of direct support and quicker access to replacement parts. Businesses should consider factors such as delivery times, cost, and after-sales support when deciding where to purchase their conveyor rollers.
How to Choose the Right Crusher Conveyor Rollers
Selecting the right crusher conveyor rollers is vital for ensuring operational efficiency and longevity of the conveyor system. Several factors must be considered to make an informed decision, ensuring that the rollers are not only effective but also cost-efficient over their lifespan.
- Material Composition: The material of the crusher conveyor rollers should be chosen based on the type of material they will carry. Rollers made from reinforced materials such as steel are suitable for heavy-duty applications where durability is critical. Alternatively, plastic rollers might be appropriate for lighter loads and less abrasive materials.
- Load Capacity: It’s crucial to select rollers that can handle the weight and volume of material they will transport. Overloading rollers can lead to premature wear and failure, so ensuring they are matched to the conveyor’s capacity is essential.
- Operating Environment: The environment in which the rollers will operate can significantly affect their lifespan and effectiveness. For example, rollers used in damp or corrosive environments should have appropriate protective coatings or be made from corrosion-resistant materials.
- Size and Fit: Proper sizing of the crusher conveyor rollers is critical to maintain the alignment and tension of the conveyor belt. Incorrectly sized rollers can cause the belt to slip or misalign, leading to increased wear and potential system failures.
- Maintenance Requirements: Consider the ease of maintenance and the availability of replacement parts. Rollers that are easy to install, replace, and maintain can significantly reduce downtime and maintenance costs.
Importance of Specific Features:
- Weight of the Roller: The weight of the crusher conveyor rollers affects the inertia of the conveyor system; heavier rollers may require more energy to move but could offer more stable operation.
- Material Durability: Durability is essential as it determines how well the rollers will stand up to the operational stresses and environmental conditions they will be exposed to. Choosing rollers made from materials that resist wear and tear is crucial in reducing the frequency of replacements.
- Design Features: Features such as sealing and shielding are important in environments where dust, water, or other contaminants are present. Such features protect the bearings and other critical parts of the roller, thereby extending the operational life of the crusher conveyor rollers.
When shopping for crusher conveyor rollers, it is essential to assess the full scope of operational requirements and environmental conditions. This holistic approach ensures that the selected rollers enhance the efficiency of the conveyor system, support continuous operations, and minimize maintenance costs.
The Price of Crusher Conveyor Rollers
The cost of crusher conveyor rollers can vary widely depending on several factors including material, size, design, and the specific needs of the application. In this section, we will explore the price range for different types of crusher conveyor rollers and discuss how these costs can impact the overall expenses of the crushing machinery.
- Standard Steel Rollers: These are the most common types of rollers used in crusher conveyor systems. Prices for standard steel rollers can range from $30 to $100 each, depending on size and specifications.
- Impact Rollers: Designed to absorb the shock and impact at loading points, impact rollers are generally more expensive than standard rollers. Prices can range from $50 to $200 per roller, reflecting their enhanced durability and specialized design.
- Polyurethane-Coated Rollers: These rollers, known for their durability and resistance to wear, are suitable for handling abrasive materials. They are typically priced between $100 and $300 per roller.
- Stainless Steel Rollers: Best suited for corrosive environments, stainless steel rollers are on the higher end of the price spectrum. Costs can range from $200 to $500 per roller, depending on the exact grade of stainless steel.
- Custom-Designed Rollers: Prices for custom-designed crusher conveyor rollers vary greatly based on the complexity of the design and the materials used. These can cost anywhere from $150 to over $500 each.
Impact on Overall Costs:
The initial purchase price of crusher conveyor rollers is just one aspect of the cost to consider. The type of rollers selected can significantly influence the operational costs of the crushing machine over time. For instance, opting for cheaper rollers might reduce initial expenses but could lead to higher maintenance costs and more frequent replacements if they fail to hold up under the operational demands. Conversely, investing in higher quality, more durable rollers can offer better long-term value through reduced downtime and maintenance needs.
Moreover, the efficiency of the conveyor system, driven by the choice of rollers, directly affects the energy consumption and operational efficiency of the crushing plant. Choosing the right rollers can lead to energy savings and improved productivity, which can offset the higher initial cost of premium models.
When considering the price of crusher conveyor rollers, it’s crucial to evaluate not only the upfront cost but also how these components will impact the overall operational efficiency and maintenance expenses of the crushing machinery. This holistic view helps in making a more cost-effective decision that can enhance performance and reduce long-term costs.
Maintenance of Crusher Conveyor Rollers
Proper maintenance of crusher conveyor rollers is essential for ensuring their longevity and efficiency. This section provides practical tips and techniques for maintaining these critical components, as well as discussing the importance of timely replacements.
- Regular Inspection: Conduct regular inspections of crusher conveyor rollers to identify wear and damage early. This should include checking for signs of misalignment, unusual noise, and wear patterns on the rollers and the conveyor belt.
- Lubrication: Adequate lubrication of the bearings in the crusher conveyor rollers is crucial. Use the correct grade and type of lubricant as specified by the manufacturer, and apply it at intervals recommended to keep the rollers running smoothly.
- Cleaning: Keep the rollers and the entire conveyor system clean from dust, dirt, and debris that can accumulate and cause the system to work harder, leading to premature wear. Cleaning should be part of the routine maintenance schedule.
- Alignment and Tension Adjustment: Misalignment and improper tension are common issues that can cause significant damage to crusher conveyor rollers. Regularly check and adjust the alignment and tension of the rollers to ensure optimal performance and reduce stress on the system.
- Replacement of Worn Parts: Replace worn or damaged rollers promptly to prevent further damage to the conveyor system. Regular replacement of parts as needed helps maintain the integrity of the system and ensures continuous operation.
Impact of Replacement Parts on System Functionality:
Replacement parts play a vital role in the maintenance strategy for crusher conveyor rollers. High-quality replacement parts ensure that the entire conveyor system operates at peak efficiency. The use of OEM (Original Equipment Manufacturer) parts, although sometimes more expensive, often provides better performance and longevity compared to aftermarket alternatives. Replacing worn or faulty rollers not only prevents breakdowns but also:
- Enhances System Reliability: New rollers can help maintain the conveyor belt’s tension and alignment, which are crucial for the consistent flow of materials.
- Reduces Downtime: By preventing unexpected failures, timely replacement of rollers minimizes downtime and maintains productivity.
- Improves Safety: Regular maintenance and replacement of critical parts reduce the risk of accidents and injuries related to equipment malfunction.
- Saves Money: Although replacements incur costs, they are often less expensive than the costs associated with a system failure, including lost production and more extensive repairs.
Maintaining crusher conveyor rollers through regular inspections, proper lubrication, timely cleaning, and alignment checks, along with the strategic replacement of worn parts, is essential for the efficient and safe operation of any material handling system. This proactive approach to maintenance ensures the longevity of the rollers and the overall health of the conveyor system.
FAQs About Crusher Conveyor Rollers
Conveyor rollers are cylindrical components that facilitate the movement of materials along conveyor belts. They are crucial in a variety of industrial, commercial, and retail operations. The most common materials used for these rollers include steel, stainless steel, and plastic, each chosen based on the specific needs of the environment and the materials being transported. Steel rollers are favored for their strength and durability, making them suitable for heavy-duty applications. Stainless steel rollers offer corrosion resistance, ideal for use in wet or chemically aggressive environments. Plastic rollers are lighter and quieter than metal rollers and are used in applications requiring low noise or where lighter loads are transported. Each type contributes uniquely to the conveyor system’s efficiency, cost-effectiveness, and maintenance needs.
Roller conveyors can be categorized into several types based on their functionality and the applications they serve. The primary types include gravity roller conveyors, driven roller conveyors, and motorized roller conveyors. Gravity roller conveyors use the force of gravity to move items across the horizontal or slightly inclined tracks and are often used in picking and assembly operations. Driven roller conveyors, powered by belts or chains, are used where controlled movement of goods is necessary. Motorized roller conveyors feature rollers that are individually powered by an internal motor, offering precise control over product movement, suitable for delicate or variable speed operations. Each type provides different benefits and is chosen based on the specific requirements of the transport and handling needs.
Conveyor rollers support and move the conveyor belt or directly move goods placed on rollers, reducing friction and allowing for smooth and efficient transport of items across a designated path. In a typical setup, rollers are mounted in a frame and spaced at regular intervals. They can be powered by motors, or they can be gravity-fed in non-powered applications. The rollers rotate when an external force—either from a motor or from the manual pushing of materials—is applied. This rotation reduces the overall friction between the surface of the roller and the items being moved, making it easier to transport heavy or large items across warehouses, production floors, or assembly areas.
Conveyor rollers are measured by their diameter, length, and the type of bearings they use. The diameter of the rollers is chosen based on the size and weight of the items to be conveyed. Larger diameter rollers are capable of handling heavier loads. The length of the rollers must be appropriate for the width of the materials or products they are intended to carry, ensuring stability and balance during operation. Measurement of length is typically from bearing to bearing, accounting for the entire span that supports the conveyor belt or materials. Additionally, the choice of bearing type is important for the application’s load-bearing capacity and operational speed. Accurate measurement and selection of conveyor rollers ensure optimal performance, reduce wear and tear, and extend the lifespan of the conveyor system.
Last Updated on April 15, 2024 by Jordan Smith
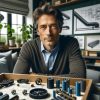
Jordan Smith, a seasoned professional with over 20 years of experience in the conveyor system industry. Jordan’s expertise lies in providing comprehensive solutions for conveyor rollers, belts, and accessories, catering to a wide range of industrial needs. From initial design and configuration to installation and meticulous troubleshooting, Jordan is adept at handling all aspects of conveyor system management. Whether you’re looking to upgrade your production line with efficient conveyor belts, require custom conveyor rollers for specific operations, or need expert advice on selecting the right conveyor accessories for your facility, Jordan is your reliable consultant. For any inquiries or assistance with conveyor system optimization, Jordan is available to share his wealth of knowledge and experience. Feel free to reach out at any time for professional guidance on all matters related to conveyor rollers, belts, and accessories.