Innovative Design of Curved Belt Conveyor Systems
In the realm of material handling and logistics, conveyor systems have long stood as the backbone of industrial efficiency, evolving significantly from their rudimentary beginnings to the sophisticated networks we see today. This evolution has been driven by an unyielding pursuit of flexibility and efficiency, leading to the advent of the curved belt conveyor system. Unlike their straight counterparts, these innovative systems are designed to navigate the complex layouts of modern facilities with ease, offering a seamless solution to the intricate challenges faced in logistics and manufacturing sectors. By integrating curved belt conveyor systems, industries can optimize space, enhance material flow, and adapt to the ever-changing demands of the market, marking a significant leap forward in the way we think about and implement conveyor technology.
What are Curved Belt Conveyor Systems
A curved belt conveyor system represents a significant advancement in the field of material handling, offering a dynamic solution where traditional straight conveyors fall short. Unlike their linear counterparts, curved belt conveyors are designed to follow the natural contours of a workspace, seamlessly integrating into environments where space is at a premium or where the material handling path is not strictly linear.Innovative curved belt conveyor systems optimize space, reduce handling time, and maintain product orientation for efficient transport.
Key Differences Between Curved and Straight Conveyors
- Path Flexibility: The most apparent difference is in the path flexibility; a curved belt conveyor system can navigate around obstacles and through tight spaces with ease, while straight conveyors are limited to linear movement.
- Space Optimization: Curved conveyors excel in optimizing space, as they can circumvent obstructions and utilize areas that would be inaccessible to straight conveyors.
- Design Complexity: The design of a curved belt conveyor system is inherently more complex, incorporating varying angles and radii to achieve the desired curvature, as opposed to the straightforward construction of straight conveyors.
- Load Transition: Curved conveyors are engineered to maintain the stability of loads as they transition through curves, a challenge not present in the linear movement of straight conveyors.
- Belt Design: The belts in curved conveyors are often specially designed with edges or guiding systems to keep the materials in place, contrasting with the simpler belt designs used in straight conveyors.
- Customization and Scalability: While both systems offer customization, curved conveyors often require more tailored solutions to fit specific layout needs, making them highly scalable but also more complex to design and implement.
Design and Functionality
The design of a curved belt conveyor system is a marvel of engineering, tailored to meet the specific needs of an operation. At its core, the system is built to navigate corners and curves with unparalleled efficiency, thanks to its unique construction. The conveyor belt itself is often fabricated with special materials and reinforced edges to withstand the forces exerted during turns. Additionally, the supporting structure and rollers are designed to ensure smooth and consistent belt movement, even at varying angles of curvature.
This ability to efficiently navigate curves opens up a plethora of possibilities in layout design, allowing facilities to maximize their operational space and streamline their material handling processes. Whether it’s maneuvering through the tight corners of a distribution center or wrapping around machinery in a manufacturing plant, the curved belt conveyor system proves to be an indispensable tool in the modern industrial landscape.
Key Features and Advantages of Curved Belt Conveyor Systems
The curved belt conveyor system stands out in the material handling industry for its unique features and numerous advantages. These systems are not just about navigating turns; they embody innovation, efficiency, and reliability.
Versatile Design and Space Optimization
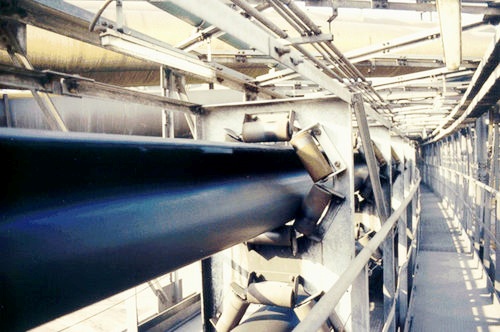
The space-saving design of curved belt conveyor systems is one of their most significant advantages. Their ability to adapt to various layouts without compromising efficiency or functionality is unparalleled. Here are four examples of design innovations that enhance the flexibility of these systems:
- Modular Construction: Many curved belt conveyor systems feature modular designs, allowing for easy expansion or reconfiguration as the needs of a facility change.
- Adjustable Radii: Some systems offer adjustable curve radii, enabling customization to fit specific space constraints and operational requirements.
- Low-Profile Designs: The development of low-profile curved conveyors allows for installation in tight spaces where traditional conveyors might not fit, maximizing usable floor space.
- Retractable Features: Innovations include retractable curved sections that can be extended or retracted as needed, providing flexibility in dynamic operational environments.
Heavy-Duty Performance and Reliability
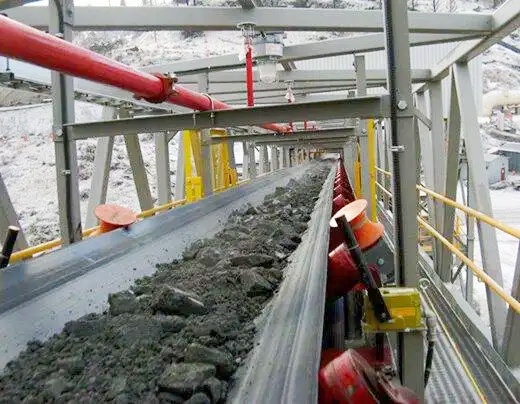
Curved belt conveyor systems are engineered for durability and reliability, even in the most demanding applications. The construction and materials used in these conveyors are selected for their ability to withstand heavy loads and continuous operation. Here are four industries where these conveyors excel:
- Airports: In baggage handling systems, curved belt conveyors efficiently transport luggage between terminals and aircraft, handling the heavy, continuous flow of bags with ease.
- Distribution Centers: These systems facilitate the smooth transition of goods through complex sorting and distribution processes, managing heavy loads and high throughput requirements.
- Manufacturing Plants: Curved conveyors are used to move raw materials and finished products around manufacturing facilities, accommodating heavy loads and varying production rates.
- Food Processing: In the food industry, specially designed curved conveyors handle bulk food products, ensuring heavy-duty performance while meeting hygiene standards.
Efficiency and Operational Benefits
The efficiency and operational benefits of curved belt conveyor systems are evident in their ability to maintain product alignment and ensure smooth transitions between conveyor sections. Here are seven roles that incline/decline belt conveyors play within a curved conveyor system:
- Seamless Integration: They integrate seamlessly with horizontal curved sections, providing a continuous flow of materials across different levels.
- Space Utilization: Incline/decline sections maximize vertical space, allowing for multi-level operations within a compact footprint.
- Product Handling: These conveyors gently handle products during elevation changes, reducing the risk of damage.
- Energy Efficiency: Advanced designs minimize energy consumption during elevation changes, contributing to overall operational efficiency.
- Speed Control: Variable speed settings allow for precise control of product flow, especially important during inclines and declines.
- Flexibility: The ability to adjust incline and decline angles provides flexibility to adapt to various product types and operational requirements.
- Safety Features: Built-in safety features ensure the secure transport of products, even at steep inclines or declines, enhancing overall system reliability.
The curved belt conveyor system is a testament to engineering ingenuity, offering versatile design options, heavy-duty performance, and significant efficiency benefits that make it a valuable asset in a wide range of industries.
DIY vs. Professional Curved Belt Conveyor Systems
When it comes to integrating a curved belt conveyor system into your operations, the decision between embarking on a DIY project or partnering with professional manufacturers is crucial. Each approach has its considerations and benefits, which we will explore in detail.
Considerations for DIY Curved Belt Conveyor Systems
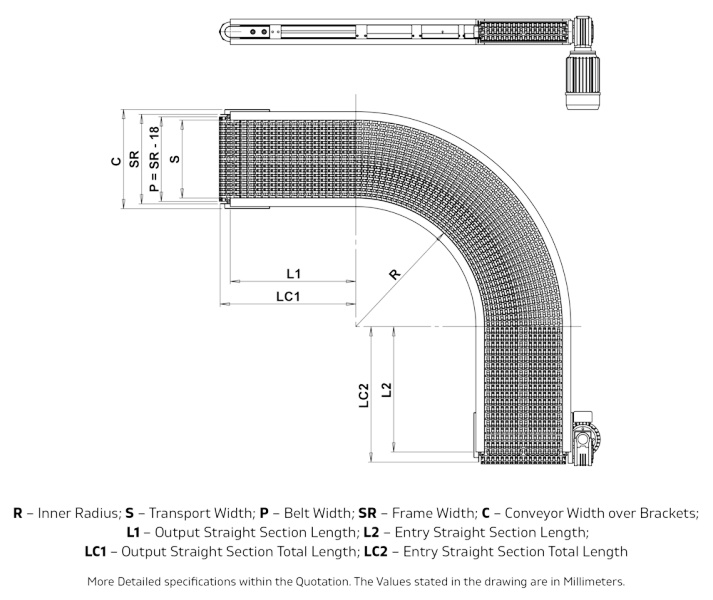
- Technical Expertise: Implementing a DIY curved belt conveyor system requires a significant level of technical knowledge, including understanding the mechanics of curved conveyance and material handling principles.
- Design Challenges: Designing a system that efficiently navigates curves and maintains product integrity is complex and requires precise calculations and planning.
- Material Sourcing: Finding the right materials that can withstand the demands of your specific application can be challenging and time-consuming.
- Cost Overruns: Without the purchasing power of professional manufacturers, DIY projects can often end up being more expensive than anticipated.
- Time Investment: The time required to design, source materials, and build a curved belt conveyor system can be substantial, diverting resources from core business activities.
- Maintenance and Support: DIY systems may lack the ongoing support and maintenance services that come with professional solutions, potentially leading to longer downtimes.
- Compliance and Safety: Ensuring that your DIY system complies with industry standards and safety regulations requires thorough research and continuous monitoring.
- Scalability: As your business grows, scaling a DIY system to meet increased demands can be challenging without the modular options often provided by professional systems.
- Reliability: The reliability of a DIY system may not match that of professionally manufactured conveyors, potentially leading to more frequent breakdowns and disruptions.
- Resale Value: DIY systems typically have little to no resale value, whereas professional systems can be an asset if you choose to upgrade or reconfigure your operations.
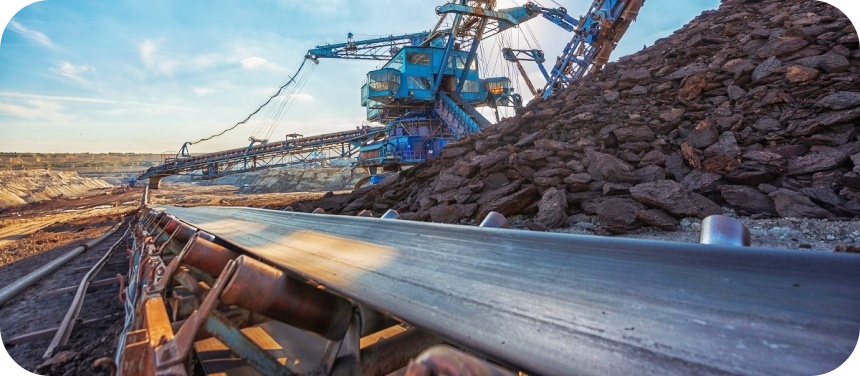
Benefits of Working with Professional Curved Belt Conveyor System Manufacturers
- Customized Solutions: Professional manufacturers can provide tailored solutions that perfectly fit your operational needs, space constraints, and material handling requirements.
- Engineering Expertise: Benefit from the extensive knowledge and experience of engineers who specialize in the design and implementation of curved belt conveyor systems.
- Quality and Durability: Professional systems are built with high-quality materials and components, ensuring durability and long-term reliability.
- After-Sales Support: Gain access to comprehensive after-sales support, including maintenance, repairs, and parts replacement, minimizing downtime and ensuring continuous operation.
- Compliance and Safety: Professional manufacturers ensure that their systems comply with all relevant industry standards and safety regulations, providing peace of mind and reducing liability risks.
- Scalability and Flexibility: Professional curved belt conveyor systems are designed with scalability in mind, allowing for easy expansion or reconfiguration as your business evolves.
Choosing between a DIY and a professional curved belt conveyor system involves weighing these considerations and benefits carefully. While a DIY project might seem appealing for its perceived cost savings and customization, the complexities and potential pitfalls often make partnering with professional manufacturers the more prudent and efficient choice for most businesses.
Innovative Technologies in Curved Conveyor Systems
The integration of innovative technologies into curved belt conveyor systems has revolutionized material handling, offering unprecedented flexibility, efficiency, and adaptability. These advancements cater to the dynamic needs of various industries, enhancing the functionality and capabilities of traditional conveyor systems.
Flexible and Telescopic Conveyor Solutions
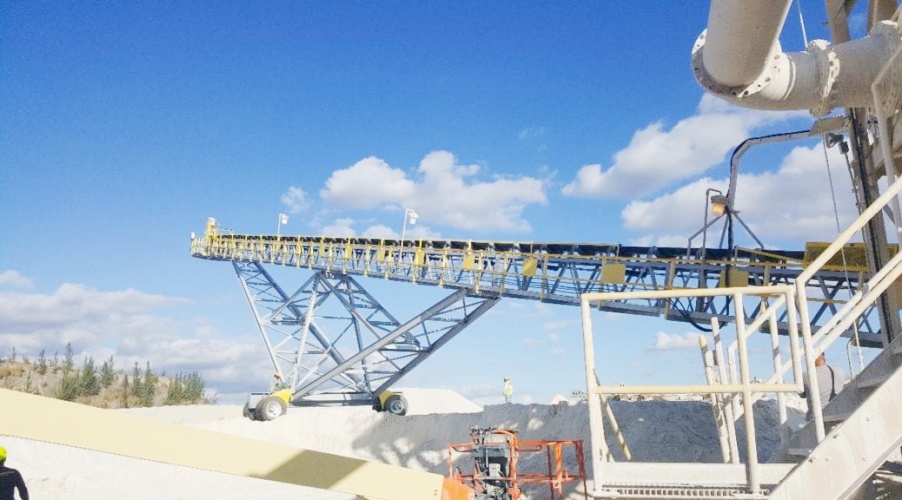
Flexible and telescopic conveyor solutions represent a significant leap forward in the design and functionality of curved belt conveyor systems. These technologies include:
- Segmented Belt Conveyors: These conveyors feature a segmented belt design that allows for greater flexibility in navigating tight curves and complex layouts, making them ideal for facilities with space constraints.
- Articulated Roller Conveyors: Employing rollers that can pivot, these conveyors smoothly guide products through turns, maintaining product orientation and spacing without the need for guide rails.
- Modular Plastic Belts: Made from interconnected plastic segments, these belts can easily navigate curves and inclines while providing a durable, easy-to-clean surface ideal for food processing applications.
- Retractable Conveyors: These systems can extend or retract as needed, offering flexibility in loading and unloading areas, particularly in dock operations.
- Telescopic Belt Conveyors: Specifically designed for efficient truck loading and unloading, these conveyors can extend into the cargo area, reducing manual handling and improving turnaround times.
- Variable Path Conveyors: Utilizing advanced control systems, these conveyors can change their path dynamically, allowing for real-time adjustments to production flows and reducing the need for fixed conveyor paths.
The impact of these technologies on logistics operations is profound:
- Increased Efficiency: By reducing manual handling and optimizing loading and unloading processes, these systems significantly enhance operational efficiency.
- Greater Adaptability: The ability to navigate tight spaces and adjust to varying operational needs makes these systems highly adaptable to changing business environments.
- Enhanced Product Handling: Improved control over product movement reduces the risk of damage, ensuring safer handling of delicate or high-value items.
- Space Optimization: The flexibility of these systems allows for more efficient use of available space, a critical factor in crowded industrial environments.
- Reduced Downtime: With features like retractability and variable paths, these systems can adapt to maintenance needs or operational changes without significant downtime.
- Improved Worker Safety: By automating loading and unloading tasks, these systems reduce the physical strain on workers, contributing to a safer workplace.
Smart Conveyor Features
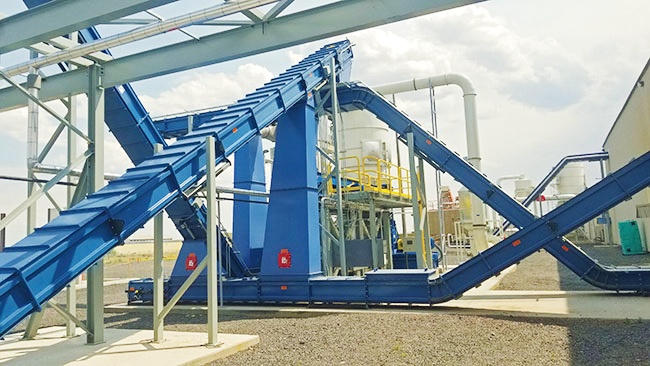
The advent of smart features in curved belt conveyor systems has brought about a new era of automation and efficiency. Key innovations include:
- Automation and Control Systems: Advanced control systems automate the operation of curved belt conveyors, optimizing speed and routing based on real-time demand and reducing the need for manual intervention.
- Real-Time Tracking: RFID tags and sensors enable the real-time tracking of items on the conveyor, providing valuable data for inventory management, process optimization, and quality control.
- Predictive Maintenance: IoT sensors monitor the health of conveyor components, predicting maintenance needs before failures occur, thereby reducing unplanned downtime and extending equipment life.
- Energy Efficiency: Smart conveyors can adjust their operation based on the current load and operational needs, minimizing energy consumption and operational costs.
- Integration Capabilities: Modern curved belt conveyor systems can seamlessly integrate with warehouse management systems (WMS) and enterprise resource planning (ERP) systems, enhancing data flow and decision-making processes.
These smart features not only enhance the operational capabilities of curved belt conveyor systems but also provide businesses with valuable insights, enabling more informed decision-making and strategic planning. The integration of these technologies represents a significant step forward in the pursuit of more efficient, adaptable, and intelligent material handling solutions.
Choosing the Best Curved Belt Conveyor System
Selecting the right curved belt conveyor system is crucial for optimizing your material handling processes. The decision involves considering various factors to ensure the system meets your operational needs effectively.
Factors to Consider
Here are eight essential factors to keep in mind:
- Load Capacity: Assess the maximum weight the conveyor will need to handle. Ensure the curved belt conveyor system is designed to support your typical load without compromising efficiency or safety.
- Conveyor Speed: The speed of the conveyor should align with your operational tempo. Too fast could lead to product damage, while too slow might bottleneck your processes.
- System Compatibility: The new curved belt conveyor system should integrate seamlessly with your existing conveyor systems and material handling equipment, ensuring a smooth and efficient workflow.
- Operational Flexibility: Consider the system’s ability to adapt to future changes in your operations, such as expansions or alterations in product lines.
- Durability and Maintenance: Look for systems known for their durability and ease of maintenance. A robust system with accessible parts can significantly reduce downtime and maintenance costs.
- Safety Features: Safety should never be compromised. Ensure the system includes all necessary safety features to protect your workers and products.
- Energy Efficiency: An energy-efficient system can reduce operational costs over time. Consider the energy consumption of the system under typical loads.
- Vendor Support: Post-installation support is crucial. Ensure the manufacturer offers comprehensive support, including maintenance, repairs, and parts replacement.
Tips to Guide Your Selection
When it comes to identifying the best curved belt conveyor system manufacturers and products, here are ten tips to guide your selection:
- Reputation: Research manufacturers with a solid reputation in the industry for quality and reliability.
- Experience: Look for companies with extensive experience in designing and installing curved belt conveyor systems.
- Customization Options: The best manufacturers offer customization options to tailor the system to your specific needs.
- Client Testimonials: Seek feedback from current and past clients to gauge their satisfaction with the manufacturer’s products and services.
- Technical Support: Ensure the manufacturer provides excellent technical support, both during and after installation.
- Warranty: A comprehensive warranty can provide peace of mind and protection against unforeseen issues.
- Innovation: Choose manufacturers that invest in research and development to stay at the forefront of conveyor technology.
- Material Quality: The quality of materials used in the conveyor system affects its durability and performance. Insist on high-quality materials.
- Cost-Effectiveness: While cost shouldn’t be the sole deciding factor, it’s important to ensure you’re getting value for your investment.
- Compliance: Ensure the manufacturer’s products comply with industry standards and regulations.
By carefully considering these factors and tips, you can make an informed decision when selecting the best curved belt conveyor system for your operations, ensuring it meets your requirements for efficiency, reliability, and safety.
Applications of Curved Belt Conveyor Systems
Industry Applications
Curved belt conveyor systems are versatile solutions used across a wide range of industries to improve efficiency, optimize space, and streamline material handling processes. They are particularly beneficial in the following sectors:
- Warehouses:
- Space Optimization: Curved belt conveyors are ideal for navigating tight spaces and maximizing the use of available floor space. They allow for smooth directional changes, which is crucial in warehouse environments where space is often limited.
- Efficiency: These conveyors enhance the efficiency of material handling operations by reducing the need for manual handling and minimizing the time required to move goods from one area to another.
- Distribution Centers:
- High Throughput: Curved belt conveyors facilitate high-speed sorting and distribution of packages, ensuring that items reach their destinations quickly and accurately.
- Integration with Sorting Systems: They can be seamlessly integrated with automated sorting systems, enabling efficient handling of a large volume of parcels and packages with minimal manual intervention.
- Manufacturing:
- Production Line Flexibility: In manufacturing plants, curved belt conveyors are used to connect different stages of the production process, allowing for flexible layout designs that can accommodate changes in production needs.
- Handling Various Products: They are suitable for transporting a wide range of products, from small components to large assemblies, ensuring smooth and continuous production flow.
- Packaging Facilities:
- Customized Solutions: Curved belt conveyors can be tailored to handle specific packaging requirements, including the transport of delicate items that need careful handling.
- Streamlining Operations: They help streamline packaging operations by efficiently moving products through different stages, such as labeling, sealing, and boxing.
- Airports:
- Baggage Handling: These conveyors are commonly used in baggage handling systems to route luggage through security checks, sorting areas, and onto the appropriate flights.
- Passenger Convenience: They enhance passenger convenience by ensuring quick and reliable movement of luggage, reducing wait times and improving overall airport efficiency.
- Food Industry:
- Sanitary Design: Curved belt conveyors in the food industry are designed with sanitary features, such as easy-to-clean surfaces and food-grade materials, to meet stringent hygiene standards.
- Versatile Use: They are used for various applications, including processing, packaging, and distribution of food products, ensuring that items are transported safely and efficiently.
Need conveyor belts? Reach out for expert assistance.
Specific Use Cases
Curved belt conveyor systems are engineered to handle a variety of specific use cases, providing reliable and efficient solutions for diverse material handling needs.
- Transport of Bins, Cardboard Boxes, and Parcels:
- Smooth Movement: These conveyors are ideal for moving bins, cardboard boxes, and parcels around corners without causing damage or shifting the contents. The smooth transition around curves ensures that items are transported safely and securely.
- Flexible Layouts: They allow for flexible conveyor layouts, accommodating different sizes and shapes of packages while maintaining consistent movement and alignment.
- Heavy-Duty Loads:
- Robust Construction: Curved belt conveyors designed for heavy-duty applications are built with strong materials and components to handle large and heavy loads, such as machinery parts, building materials, and other industrial products.
- Enhanced Capacity: The robust design ensures that the conveyor can support and transport heavy items efficiently, reducing the need for multiple handling stages and improving overall throughput.
- Changes in Elevation:
- Incline and Decline Handling: Curved belt conveyors can be configured to handle changes in elevation, making them suitable for applications that require moving products between different levels within a facility.
- Space-Saving Solutions: By incorporating curves with inclines or declines, these conveyors optimize vertical space, enabling efficient use of the available area and reducing the footprint of the conveyor system.
- Handling of Irregular Loads:
- Custom Adaptations: For irregularly shaped or fragile items, curved belt conveyors can be customized with specific features, such as padded surfaces or gentle guiding mechanisms, to ensure safe and stable transport.
- Versatile Applications: They are used in industries where products do not have uniform shapes or sizes, such as recycling centers, automotive parts manufacturing, and furniture production, ensuring that even the most challenging loads are conveyed reliably.
FAQs about Curved Belt Conveyor System
Curved conveyor belts are ingeniously designed to navigate corners and turns within various industrial and commercial environments, enabling the continuous movement of goods in directions other than straight lines. Unlike traditional straight conveyors, curved conveyors incorporate specially engineered belts and structural components that maintain the stability and orientation of products as they move along the curve. The belts on these conveyors are often constructed with unique features, such as tapered rollers or guiding mechanisms, to ensure that items remain securely on the conveyor through the curve. This capability is particularly beneficial in facilities where space constraints require efficient use of the available area, allowing conveyor paths to weave around obstacles and utilize space that would otherwise be inaccessible. The seamless integration of curved sections with straight conveyor segments creates a versatile and efficient material handling system, optimizing the flow of goods and enhancing operational efficiency across various industries, from manufacturing and packaging to distribution and logistics.
Conveyors are essential components in material handling and logistics, designed to transport goods efficiently across short and long distances. The three primary types of conveyors are:
Belt Conveyors: These are the most common type, consisting of a continuous belt that rotates around two or more pulleys. Belt conveyors are versatile and can transport a wide range of materials, from small, lightweight items to large, bulky goods. They are used in various industries, including manufacturing, warehousing, and retail.
Roller Conveyors: These conveyors use a series of rollers to move goods along the conveyor path. Roller conveyors are ideal for transporting items with a flat bottom and are commonly used in sorting, assembly, and packaging operations. They can be powered or gravity-fed, depending on the application’s requirements.
Chain Conveyors: Chain conveyors consist of a series of chain links or segments that transport goods along the conveyor path. They are particularly suited for heavy-duty applications, such as moving large or heavy items in manufacturing plants or automotive assembly lines. Chain conveyors can be designed to handle a wide range of load sizes and shapes.
Each conveyor type offers unique advantages and is suited to specific applications and material handling needs, making it crucial to select the right conveyor type based on the operational requirements and the nature of the goods being transported.
A curve belt refers to the specialized conveyor belt used in curved conveyor systems, designed to facilitate the smooth and efficient transport of goods around bends and corners within a conveyor system. Unlike standard straight conveyor belts, curve belts are engineered to handle the additional stresses and strains encountered as the belt navigates through curved sections.
These belts may feature unique designs, such as tapered edges or reinforced structures, to maintain product stability and alignment during transit through the curve. Curve belts are an integral component of curved conveyor systems, enabling the seamless integration of curved paths within a material handling setup, thereby optimizing space utilization and improving the overall efficiency of the conveyor system. They are widely used in various industries, including logistics, manufacturing, and packaging, where the layout requires conveyor paths to navigate around obstacles or to maximize the use of available space.
Measuring a curved conveyor belt involves several key steps to ensure accurate dimensions for replacement or system design purposes. The process typically includes:
Radius Measurement: Determine the radius of the curve by measuring from the center point of the curve to the edge of the conveyor belt. This measurement is crucial for understanding the belt’s curvature.
Arc Length: Measure the length of the arc, which is the curved section of the belt. This can be done by using a flexible measuring tape along the path of the belt’s curve.
Belt Width: Measure the width of the conveyor belt from edge to edge. In curved conveyor belts, the width may vary across the belt’s length, especially if the belt is designed with tapered edges to accommodate the curve.
Belt Thickness: Use a caliper to measure the thickness of the conveyor belt, which can impact the belt’s ability to navigate the curve and affect the overall system performance.
The angle of the Curve: Determine the angle of the curve by measuring the degree of the turn that the conveyor belt makes. This is particularly important for precise engineering and design purposes.
Accurate measurements are essential for ensuring the proper fit and function of the curved conveyor belt within the system, contributing to the efficient and reliable operation of the conveyor.
Flat Belt Conveyors: Used for general material handling.
Modular Belt Conveyors: Made of interlocking plastic pieces, suitable for food processing.
Cleated Belt Conveyors: Have raised sections to prevent material rollback on inclines.
Curved Belt Conveyors: Designed to navigate turns and changes in direction.
Incline/Decline Belt Conveyors: Used for moving materials between different heights.
Timing Belt Conveyors: Provide precise product placement and synchronization.
Wire Mesh Belt Conveyors: Used for high-temperature applications and heavy loads.
Specialty Belt Conveyors: Custom-designed for specific applications, such as heavy-duty or hygienic environments.
Last Updated on June 21, 2024 by Jordan Smith
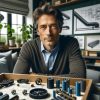
Jordan Smith, a seasoned professional with over 20 years of experience in the conveyor system industry. Jordan’s expertise lies in providing comprehensive solutions for conveyor rollers, belts, and accessories, catering to a wide range of industrial needs. From initial design and configuration to installation and meticulous troubleshooting, Jordan is adept at handling all aspects of conveyor system management. Whether you’re looking to upgrade your production line with efficient conveyor belts, require custom conveyor rollers for specific operations, or need expert advice on selecting the right conveyor accessories for your facility, Jordan is your reliable consultant. For any inquiries or assistance with conveyor system optimization, Jordan is available to share his wealth of knowledge and experience. Feel free to reach out at any time for professional guidance on all matters related to conveyor rollers, belts, and accessories.