Custom Conveyor Rollers: Essential for Modern Industries
In today’s fast-paced industrial landscapes, the efficiency of conveyor systems is crucial, and custom conveyor rollers are at the heart of these solutions. These specialized rollers are designed to meet precise specifications and requirements, making them essential for a variety of industries, from manufacturing to distribution. As demands for more robust and adaptable systems increase, manufacturers of custom roller conveyor have stepped up to provide solutions that cater to specific needs. Whether it’s heavy-duty rollers for mining operations or rollers with unique diameters for packaging facilities, the ability to customize these components ensures optimal performance and longevity of conveyor systems. This adaptability not only supports diverse industrial activities but also drives innovation in material handling technologies.
What are Custom Conveyor Rollers
Custom conveyor rollers are tailored components designed to meet the unique needs of various conveyor systems. Unlike standard rollers, which come in fixed sizes and materials, custom conveyor rollers can be adapted to fit specific requirements, enhancing both functionality and efficiency in material handling. This customization is crucial in industries where standard rollers may not suffice due to unique operational conditions or specific performance requirements.
The flexibility in customizing custom conveyor rollers is evident in the choice of materials, sizes, and configurations. For instance, rollers can be made from ultra-durable materials like reinforced polymers for corrosive environments, or lightweight aluminum for applications requiring easy maneuverability. Sizes can vary dramatically, from small diameter rollers suitable for tight spaces to large, heavy-duty rollers designed for high-load applications.
- High-Temperature Rollers: For industries like steel manufacturing where temperatures can degrade typical rollers, custom rollers are made from heat-resistant materials.
- Grooved Rollers: Essential in the paper and printing industries, these rollers have grooves that guide and hold the paper in place as it moves through the machinery.
- Impact Rollers: Positioned at loading zones to absorb shocks and reduce damage to the conveyor belt, ideal for mining and quarrying operations.
- Non-Stick Coated Rollers: Used in the food processing industry, where preventing material buildup is crucial for maintaining hygiene and preventing contamination.
- Variable Diameter Rollers: These rollers are designed to accommodate uneven loads or varying widths of materials, ensuring stability across the conveyor belt.
By utilizing custom conveyor rollers, businesses can significantly enhance the performance and reliability of their conveyor systems, tailoring each component to their specific operational needs.
Benefits of Custom Conveyor Rollers
The advantages of custom conveyor rollers are multifaceted, significantly impacting operational efficiency, durability, and the ability to meet specific industrial requirements. By tailoring custom conveyor rollers to specific tasks, industries can achieve a higher level of productivity and reduce the risk of downtime caused by equipment failure.
Improved Efficiency
Custom conveyor rollers are designed to fit seamlessly into existing systems, ensuring that there is minimal resistance and wear. This precise fit not only reduces energy consumption but also increases the speed and smoothness of operations. For example, in distribution centers, rollers can be customized to handle different package sizes and weights, speeding up the sorting process and reducing bottlenecks.
Enhanced Durability
Each industry faces unique challenges, from abrasive materials in construction to corrosive substances in chemical processing. Custom conveyor rollers can be made from materials specifically chosen for their durability in these conditions. Stainless steel rollers might be used in wet environments to prevent rust, while hardened plastic rollers could be used in environments where metal contamination must be avoided, such as in food production.
Tailored to Specific Industrial Needs
The specificity of custom conveyor rollers allows for designs that address the precise needs of an industry. For instance, rollers with high load-bearing capacities are essential in heavy manufacturing environments to support the weight of raw materials like metal and stone without compromising system integrity.
Optimization for Unique Applications
Every application has its quirks and demands, and custom conveyor rollers can be optimized to handle these unique characteristics efficiently. In industries where precision is paramount, such as electronics manufacturing, rollers can be designed to handle delicate components without causing damage. Similarly, for applications involving extreme temperatures, rollers can be fitted with specialized bearings to withstand the conditions without faltering.
Custom conveyor rollers provide a robust solution tailored to enhance operational efficiencies, withstand harsh environments, and meet exact industry specifications. This customization leads to less wear and tear, lower maintenance costs, and a longer lifespan for the entire conveyor system.
Choosing the Right Manufacturer for Custom Conveyor Rollers
Selecting the right manufacturer for custom conveyor rollers is critical to ensuring that the end product meets your specific needs and standards. Here are key considerations to guide your decision when searching for a manufacturer capable of delivering high-quality custom roller conveyor:
Proximity
Choosing a manufacturer located near your operations can significantly enhance logistical efficiency and ease of communication. Local manufacturers can offer quicker turnaround times, reduced shipping costs, and the opportunity for better oversight during the production process. Proximity facilitates easier site visits, which are crucial for initial assessments and ongoing quality checks.
Experience and Specialty
It is essential to select manufacturers that have a proven track record and specialized experience in producing custom conveyor rollers suited to your industry’s specific demands. For example, if your operation requires heavy-duty rollers for mining or quarrying, a manufacturer with expertise in crafting durable, robust rollers would be ideal. Similarly, for precise applications like small component assembly, a manufacturer skilled in producing small diameter rollers, such as 4-inch options, should be considered.
Quality Assurance Processes
Evaluate the quality control measures the manufacturer has in place. A good manufacturer should have rigorous testing and quality assurance processes to ensure that the custom conveyor rollers meet industry standards and are free from defects. This is particularly crucial when rollers are intended for critical applications where failure could lead to significant downtime or safety hazards.
Customization Capabilities
The ability to fully customize rollers according to specific requirements is a core consideration. Assess whether the manufacturer can provide a range of materials, sizes, and configurations. This includes options for various bearing types, surface treatments, and material properties designed to withstand different environmental conditions and operational stresses.
Customer Support and Service
After-sales support is as important as the quality of the custom conveyor rollers themselves. Reliable customer service ensures that you can access prompt assistance with installation, troubleshooting, and any maintenance issues that may arise. It also helps in ensuring the longevity and efficiency of the rollers in your conveyor system.
By carefully evaluating these factors, you can choose a manufacturer that will not only deliver high-quality custom conveyor rollers but also support your operational goals effectively.
Types of Custom Conveyor Rollers
Custom conveyor rollers are essential components in modern material handling systems, tailored to meet diverse industrial requirements. Below, we delve into some specific types of custom conveyor rollers that cater to various needs and applications.
Heavy Duty Conveyor Rollers
Heavy duty custom conveyor rollers are designed to withstand extreme conditions and heavy loads, making them ideal for industries such as mining, steel manufacturing, and bulk material handling. These rollers are built with robust materials to endure abrasive and harsh environments.
- Steel Reinforced Rollers: Perfect for handling sharp or hot materials that could damage standard rollers.
- Impact Resistant Rollers: Designed to absorb shocks and reduce vibration, ensuring stability under heavy loads.
- Large Diameter Rollers: Suitable for supporting and moving large volumes of materials, reducing the number of rollers needed.
- High Load Rollers: Engineered to carry more weight than typical rollers, ideal for heavy assembly lines.
- Sealed Bearing Rollers: Provides extra protection against dust and particles, prolonging the lifespan of the roller in dirty conditions.
Omni Conveyor Rollers
Omni custom conveyor rollers are engineered for versatility, allowing directional movement that facilitates complex routing in distribution centers and warehouses. These rollers are particularly beneficial in systems requiring multi-directional sorting and transferring. They help in seamlessly directing packages and products between different conveyor belts without manual intervention, enhancing efficiency and reducing handling time.
Small & Specific Diameter Rollers
Small and specific diameter custom conveyor rollers are crucial for applications where precision is key. These rollers are often found in industries like electronics manufacturing, where they handle delicate components, or in pharmaceuticals, where small batches of products are processed. A typical example includes 4-inch diameter rollers, which are excellent for:
- Handling small or lightweight items with care.
- Operating in limited space environments.
- Ensuring precise movement and positioning.
Grooved Conveyor Rollers
Grooved custom conveyor rollers are specialized for tasks where materials need to be aligned or securely positioned during transport. These rollers have grooves that can help stabilize and guide flat or uneven products.
- Cable Manufacturing: Keeps wires and cables in place during production.
- Printing and Paper Industries: Ensures paper travels straight and does not skew.
- Packaging Lines: Aligns boxes for accurate labeling or sealing.
- Textile Manufacturing: Guides fabrics smoothly through the process.
- Food Processing: Helps in proper alignment of containers or packages for filling or sealing.
Each type of custom conveyor roller is designed to optimize specific aspects of conveyor systems, from improving load-bearing capacity and operational flexibility to ensuring precision and alignment in specialized applications. These customizations enable industries to enhance efficiency, reduce downtime, and achieve higher productivity.
Features to Consider for Custom Conveyor Rollers
When designing or selecting custom conveyor rollers, it is crucial to consider various features that contribute to the performance and longevity of the rollers. Each component plays a specific role, impacting the overall efficiency of the conveyor system.
Tube Material
The choice of tube material is pivotal in determining the suitability and durability of custom conveyor rollers. Each material offers distinct advantages depending on the environment and load requirements. Examples of commonly used materials include:
- PVC: Lightweight and resistant to corrosion and chemicals, ideal for food processing or pharmaceutical environments.
- Steel: Offers high strength and durability, suitable for heavy-duty applications in industries like mining and construction.
- Stainless Steel: Combines strength with corrosion resistance, perfect for moist or corrosive environments such as chemical processing or outdoor use.
- Aluminum: Lightweight yet strong, suitable for applications where weight reduction is crucial without compromising load capacity.
- Composite Materials: Such as fiberglass or reinforced plastics, used for their unique properties like non-magnetic or non-sparking characteristics, suitable for explosive environments or MRI facilities.
Bearings
Bearings are critical components in custom conveyor rollers, as they directly influence the roller’s performance and longevity. Different types of bearings are designed to handle various operational stresses:
- Polyhoused Precision ABEC Bearings: Provide high precision and low friction, perfect for applications requiring high-speed and low-noise operation.
- Stainless Steel Bearings: Ideal for environments prone to moisture or corrosive substances, ensuring durability and resistance to rust.
- Sealed Bearings: Offer protection against dust and debris, crucial for maintaining performance in dirty or gritty environments.
- Tapered Roller Bearings: Used for heavy load applications, capable of handling both radial and axial forces efficiently.
- Spherical Roller Bearings: Excellent for applications where misalignment might occur, providing flexibility and load capacity.
Axle
The axle of a custom conveyor roller is another fundamental component, often overlooked, but it holds the roller together and ensures smooth operation.
- Fixed Axle: Typically used where the roller needs to be secured to the frame, providing stability and alignment.
- Spring Loaded Axle: Allows for easy installation and removal, ideal for systems requiring frequent maintenance or adjustments.
- Threaded Axle: Provides the ability to adjust the tension or clearance, enhancing the customizability for specific applications.
- Stainless Steel Axle: Offers corrosion resistance, essential for harsh environments like chemical processing or marine applications.
- Hollow Axle: Reduces weight without sacrificing strength, suitable for applications where overall conveyor weight is a concern.
Each of these features — from the material of the tube and the type of bearings to the design of the axle — plays a crucial role in the functionality and durability of custom conveyor rollers. Proper consideration and selection of these features ensure that the conveyor system operates efficiently, meets the required specifications, and withstands the operational demands of its intended environment.
Replacement and Maintenance of Custom Conveyor Rollers
Proper maintenance and timely replacement of custom conveyor rollers are essential to ensure the longevity and efficiency of a conveyor system. Here are detailed strategies and tips for maintaining and replacing custom conveyor rollers.
Tips on Conveyor Roller Replacement
Knowing when and how to replace custom conveyor rollers can significantly reduce downtime and increase productivity.
- Regular Inspection: Schedule regular inspections to assess the wear and tear on rollers. Replace any roller showing signs of significant wear, such as cracks, deformations, or severe corrosion.
- Listen for Noise: Unusual noises, such as grinding or squeaking, are often the first indicator of bearing failure. Such noises can prompt a closer inspection and possible replacement of the affected rollers.
- Monitor Movement: Rollers that stick or do not turn smoothly can cause conveyor belts to slip or misalign. Replacing these rollers promptly avoids further damage and potential operational disruptions.
- Check for Material Build-up: Rollers that accumulate material can become unbalanced, leading to premature wear. If cleaning does not restore normal operation, replacement might be necessary.
- Upgrade as Needed: When upgrading other parts of the conveyor system, consider whether existing rollers are suitable for new operational demands. Replace rollers that are not compatible with increased loads or speeds.
Maintenance Advice for Custom Conveyor Rollers
Effective maintenance extends the life of custom conveyor rollers and ensures their continual efficiency. Here are key practices to maintain the performance of your rollers:
- Lubrication: Regularly lubricate bearings according to the manufacturer’s recommendations. Proper lubrication reduces friction and wear, thereby extending the life of the rollers.
- Cleaning: Keep the rollers and the conveyor environment clean. Dirt, debris, and corrosive substances can damage rollers and degrade their performance.
- Alignment Checks: Ensure that the conveyor framework and rollers are properly aligned. Misalignment can lead to uneven wear and tear, reducing the effectiveness and lifespan of rollers.
- Load Monitoring: Avoid overloading the conveyor system. Consistently exceeding the recommended load capacity can strain rollers, leading to faster deterioration.
- Record Keeping: Maintain records of maintenance activities, replacements, and any issues encountered with the rollers. This documentation helps in planning future maintenance and identifying recurring problems.
By adhering to these replacement and maintenance tips, businesses can ensure that their custom conveyor rollers remain in optimal condition, supporting efficient and reliable operation of the conveyor system. This proactive approach minimizes downtime and maximizes the return on investment in these crucial components.
Case Studies & Examples of Custom Conveyor Rollers
The use of custom conveyor rollers has significantly impacted various industries by enhancing operational efficiency, reducing maintenance costs, and solving unique material handling challenges. Below are five real-world examples of businesses that have seen substantial benefits from integrating custom conveyor rollers into their systems, as well as an overview of how different sectors utilize these specialized components.
Real-World Business Examples
- Automotive Assembly Plant: An automotive manufacturer redesigned their assembly line using custom conveyor rollers capable of handling the heavy weight of car frames and components. This adjustment allowed for smoother operations and a reduced rate of roller replacements, significantly cutting downtime.
- E-commerce Fulfillment Center: By implementing grooved and omni-directional custom conveyor rollers, a large e-commerce company optimized their package sorting process. The customized rollers improved the directional movement of packages, enhancing sorting accuracy and speed, which was crucial during peak shopping seasons.
- Pharmaceutical Production: A pharmaceutical company utilized small-diameter, stainless steel custom conveyor rollers in their production lines to handle sensitive materials in a clean environment. These rollers were specifically designed to be easy to clean and resistant to chemical corrosion, ensuring compliance with stringent industry regulations.
- Food Processing Facility: A food processing plant employed non-stick coated and PVC custom conveyor rollers to prevent contamination and build-up of food products. This customization not only met health and safety standards but also reduced cleaning times between batches.
- Heavy Machinery Manufacturer: This company used ultra-heavy-duty steel custom conveyor rollers for moving large machinery parts through the assembly line. The robust design of these rollers ensured they could withstand the substantial weight and abrasion without frequent replacements.
Industries Utilizing Custom Rollers
- Distribution Warehouses: These facilities often use customized rollers to improve the efficiency of sorting and handling diverse merchandise. Customization can include anything from the roller size to specific features like shock absorbers to handle fragile goods.
- Food and Beverage: In this industry, rollers may be customized for hygiene, with materials that are easy to clean and resistant to the acidic or sugary substances found in food and beverage products.
- Manufacturing: Diverse manufacturing environments benefit from rollers designed to withstand the specific conditions of their production processes, whether it’s high temperatures in metalworking or clean-room standards in electronics manufacturing.
Through these case studies and industry examples, it is evident that custom conveyor rollers play a pivotal role in optimizing productivity and addressing specific operational needs across various sectors. This customization leads to tangible improvements in efficiency, safety, and overall operational effectiveness.
FAQs About Custom Conveyor Rollers
Conveyor rollers are manufactured by a variety of companies specializing in material handling equipment. These manufacturers range from large multinational corporations to smaller, specialized engineering firms. The production of conveyor rollers is a detailed process that involves precision engineering to ensure that each roller meets specific operational requirements. Companies that make these rollers typically also offer customization options to cater to unique industrial needs, such as varying load capacities, sizes, and materials suited for different environments. When choosing a manufacturer, it’s important to consider factors like their reputation, production capabilities, quality assurance processes, and the ability to provide tailored solutions. Experienced manufacturers will often have a portfolio of successful installations and client testimonials that can provide insights into their expertise and reliability.
Conveyor rollers come in various types to suit different industrial applications and operational needs. The primary types include gravity rollers, which move items through manual force or natural gravity; driven rollers, which are powered by belts or chains; and impact rollers, placed at points where items are loaded onto conveyors to absorb shock and reduce damage to both the conveyor belt and the items. Other specialized types include tapered rollers for curves and corners, grooved rollers for sorting and moving specific types of items, and polyurethane coated rollers for quieter operation and reduced wear. Each type serves a unique purpose, enhancing the efficiency and functionality of conveyor systems across various sectors like manufacturing, distribution, and packaging.
Manufacturing a conveyor roller involves several key steps. First, the design process defines the specifications based on the intended load, speed, and environmental conditions. Materials are then selected, such as steel, aluminum, or plastic, depending on the requirements for strength, durability, and corrosion resistance. The manufacturing process may involve machining operations to shape the roller tubes and ends, followed by assembly where bearings are inserted and sealed. Additional features like coatings or grooves are applied as per the custom requirements. Quality control is crucial throughout the manufacturing process, including testing for dimensional accuracy, load capacity, and performance under simulated conditions to ensure that each roller meets the specified standards and functions reliably in its intended application.
Last Updated on April 16, 2024 by Jordan Smith
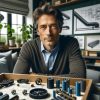
Jordan Smith, a seasoned professional with over 20 years of experience in the conveyor system industry. Jordan’s expertise lies in providing comprehensive solutions for conveyor rollers, belts, and accessories, catering to a wide range of industrial needs. From initial design and configuration to installation and meticulous troubleshooting, Jordan is adept at handling all aspects of conveyor system management. Whether you’re looking to upgrade your production line with efficient conveyor belts, require custom conveyor rollers for specific operations, or need expert advice on selecting the right conveyor accessories for your facility, Jordan is your reliable consultant. For any inquiries or assistance with conveyor system optimization, Jordan is available to share his wealth of knowledge and experience. Feel free to reach out at any time for professional guidance on all matters related to conveyor rollers, belts, and accessories.