Cut Edge Conveyor Belt: Edge Types
Conveyor belts are indispensable components in the industrial world, seamlessly facilitating the transportation of materials across various sectors such as mining, manufacturing, and logistics. These belts are designed to withstand heavy loads, abrasive materials, and long operational hours, making them a critical element in the efficiency and productivity of industrial operations. Among the various features that differentiate conveyor belts, the type of edge finish—specifically, cut edge and moulded edge—plays a significant role in their performance and application. Cut edge conveyor belt is characterized by its raw, unsealed edges where the fabric layers are visible, offering a cost-effective solution with flexibility in width customization. In contrast, moulded edge conveyor belts feature sealed edges that protect the belt’s carcass, enhancing durability and resistance to wear. Understanding the distinctions between these two types of conveyor belt edges is crucial for selecting the right belt for specific industrial applications, ensuring optimal performance and longevity.
The Basics of Cut Edge Conveyor Belt
Cut edge conveyor belts are a fundamental component in the realm of industrial machinery, offering a versatile and cost-effective solution for the transportation of goods across various sectors. Unlike their moulded edge counterparts, cut edge conveyor belts feature edges that are directly cut from the fabric without any sealing or finishing. This results in a visible fabric or carcass layer along the belt’s edges, which can be an advantage or disadvantage depending on the application.
The primary distinction between cut edge and moulded edge conveyor belts lies in their edge finish. Moulded edge belts have their edges sealed, which protects the internal fabric from environmental elements and wear, potentially extending the belt’s lifespan. In contrast, cut edge conveyor belts are more susceptible to fraying and ingress of moisture or contaminants due to their exposed edges. However, they offer significant cost savings and flexibility, as they can be easily trimmed to the required width without the need for specialized equipment or processes.
To illustrate the differences more clearly, consider the following comparison table:
A diagram illustrating the structure of a cut edge conveyor belt would show the belt’s layers, including the top cover, carcass, and bottom cover, with the edges left raw and unsealed. This visual representation helps in understanding how the cut edge exposes the belt’s internal layers, offering insight into both the belt’s construction and the implications of choosing a cut edge design for specific applications.
Understanding the basics of cut edge conveyor belts, including their construction, advantages, and limitations, is crucial for making informed decisions when selecting a conveyor belt for industrial use. The choice between cut edge and moulded edge conveyor belts ultimately depends on the specific requirements of the application, including environmental conditions, operational demands, and budget constraints.
Types of EP Cut Edge Conveyor Belt
EP cut edge conveyor belts are classified based on various factors, including the number of fabric plies, the type of top and bottom cover materials, the belt’s strength, and specific applications. Below are the common types of EP cut edge conveyor belts:
1. Based on Ply Number:
- 2-Ply EP Conveyor Belt: Consists of two layers of polyester and nylon fabric. Suitable for light to medium-duty applications where moderate tensile strength is required.
- 3-Ply EP Conveyor Belt: Three layers of fabric provide higher tensile strength, making it suitable for medium-duty applications with heavier loads.
- 4-Ply EP Conveyor Belt: Four layers of fabric offer enhanced strength and durability, ideal for heavy-duty applications in mining, construction, and bulk material handling.
- 5-Ply EP Conveyor Belt: Five layers of fabric are used for extremely heavy-duty applications, where maximum strength and durability are required.
2. Based on Belt Strength (Rating):
- EP 100/150/200: These numbers refer to the tensile strength of the belt per millimeter of width, expressed in N/mm. For instance, an EP 200 belt has a tensile strength of 200 N/mm. Higher-rated belts are used for more demanding applications.
- EP 300/400/500 and above: These belts are used in very demanding environments where the belt needs to carry extremely heavy loads over long distances.
3. Based on Cover Material and Properties:
- General-Purpose EP Belt: Designed for standard material handling applications with moderate wear and tear.
- Heat-Resistant EP Belt: Equipped with heat-resistant covers, these belts can withstand high temperatures, making them suitable for conveying hot materials such as clinker in cement plants.
- Oil-Resistant EP Belt: Designed with oil-resistant covers, ideal for transporting materials with high oil content like grains or processed foods.
- Flame-Resistant EP Belt: These belts have flame-resistant covers, making them suitable for use in underground mining or other hazardous environments where fire safety is crucial.
- Abrasion-Resistant EP Belt: With highly abrasion-resistant covers, these belts are designed to handle extremely abrasive materials like sharp rocks or slag.
- Chemical-Resistant EP Belt: These belts are made to resist the effects of chemicals, suitable for industries where exposure to chemicals is common.
4. Based on Surface Pattern:
- Plain Surface EP Belt: Standard flat surface, typically used for transporting materials without any significant incline.
- Chevron (Patterned) EP Belt: Features a V-shaped or other patterns on the surface, which helps in preventing materials from slipping off when the belt is used on an incline.
- Rough Top EP Belt: The rough texture on the surface provides better grip for transporting packaged materials or products on an incline.
5. Based on Application:
- Mining EP Conveyor Belt: Designed specifically for transporting heavy ores and minerals, with features such as high abrasion and tear resistance.
- Cement Plant EP Conveyor Belt: Customized for the specific needs of cement plants, including heat resistance and durability.
- Aggregate Handling EP Conveyor Belt: Used in construction and aggregate industries for transporting gravel, sand, and other bulk materials.
6. Based on Edge Reinforcement:
- Standard Cut Edge EP Belt: Standard cut edges without additional reinforcement, cost-effective but requires careful handling to prevent fraying.
- Reinforced Cut Edge EP Belt: Reinforced with additional materials to prevent edge fraying and enhance durability in demanding conditions.
Each type of EP cut edge conveyor belt is designed to meet specific operational requirements, providing a tailored solution for various industries and applications. The choice of belt type depends on factors such as the material being conveyed, operating environment, and specific industry needs.
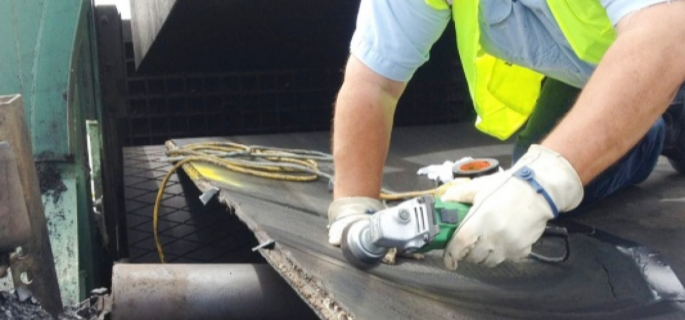
Cut Edge Conveyor Belt:Steel Cord Conveyor Belt
A Cut Edge Steel Cord Conveyor Belt is a type of conveyor belt that utilizes steel cords as the tension-bearing components. These belts are known for their high tensile strength, durability, and ability to handle extremely heavy loads over long distances. The “cut edge” refers to the edges of the belt being cut and left exposed during the manufacturing process, which is different from the molded edge type where the edges are sealed.
Key Features of Cut Edge Steel Cord Conveyor Belts
Construction:
- Steel Cords: The primary tensile members are steel cables embedded within the rubber matrix. These steel cords run longitudinally along the belt, providing superior strength and minimal elongation under load.
- Rubber Covers: The top and bottom covers are made of rubber or a similar compound, which provides resistance to wear, impact, and environmental factors.
High Tensile Strength:
- Steel cord conveyor belts are known for their exceptional tensile strength, making them suitable for carrying heavy materials over long distances. They are often used in industries where the belt must support high loads, such as mining and bulk material handling.
Low Elongation:
- The steel cords ensure that the belt exhibits very low elongation under load, which helps in maintaining precise tension and alignment on long conveyor systems. This characteristic is crucial in applications requiring stable operation and minimal maintenance.
Cut Edge Design:
- The cut edge design means that the edges of the belt are not sealed, leaving the steel cords exposed at the edges. While this reduces manufacturing costs, it requires careful handling and maintenance to prevent moisture ingress, corrosion, and fraying.
Abrasion and Impact Resistance:
- The rubber covers on cut edge steel cord belts are typically designed to resist abrasion and impact, making them suitable for harsh environments where the belt is exposed to sharp or heavy materials.
Flexibility:
- Despite the use of steel cords, these belts retain a degree of flexibility, allowing them to negotiate curves and bends in conveyor systems. However, they are generally stiffer than fabric-reinforced belts.
Applications of Cut Edge Steel Cord Conveyor Belts
- Mining: For transporting ores, coal, and other heavy minerals over long distances, especially in open-pit and underground mines.
- Cement Industry: Used for conveying raw materials like limestone, clay, and cement clinker.
- Port Facilities: Handling bulk materials such as iron ore, coal, and grain in ports and harbors.
- Power Plants: Moving coal or ash in thermal power plants.
- Quarries: Transporting aggregates and heavy rocks in quarries.
Advantages of Cut Edge Steel Cord Conveyor Belts
- Superior Strength: Capable of carrying extremely heavy loads with minimal elongation.
- Durability: Long service life due to resistance to wear and impact.
- Stable Operation: Low elongation ensures consistent belt tension and tracking.
- Cost-Effective: Cut edges can reduce initial manufacturing costs compared to molded edge belts.
Disadvantages
- Susceptibility to Edge Wear: The exposed steel cords can be vulnerable to moisture ingress, leading to potential corrosion and fraying over time.
- Maintenance Requirements: Regular inspections are needed to monitor the condition of the exposed edges, and preventative maintenance is essential to extend the belt’s lifespan.
- Not Ideal for Wet Conditions: Cut edges can absorb moisture, leading to potential issues with corrosion and weakening of the steel cords.
Selection Considerations
Operating Environment:
- In dry conditions with minimal exposure to moisture, cut edge steel cord belts can be highly effective.
- For wet or corrosive environments, additional protective measures or molded edge belts may be preferable.
Load Requirements:
- These belts are ideal for applications requiring the transportation of heavy and abrasive materials over long distances.
Maintenance Capabilities:
- If regular maintenance can be ensured, cut edge steel cord belts offer a cost-effective solution with high performance. However, where maintenance is limited, the risks associated with edge exposure should be carefully considered.
Cut edge steel cord conveyor belts are a robust and cost-effective solution for demanding applications in heavy industries. They offer excellent tensile strength and durability but require careful maintenance to prevent issues related to the exposed edges. When selecting these belts, consider the environmental conditions, load requirements, and maintenance capabilities to ensure optimal performance and longevity.
Cut Edge Conveyor Belt Used in Rubber Conveyor Belt
When discussing cut edge conveyor belts within the context of rubber conveyor belts, the term refers to belts where the edges of the belt have been cut and left exposed, rather than being sealed or molded. These belts are commonly used across various industries due to their cost-effectiveness and versatility, particularly when made with rubber materials. Here’s an overview of how cut edge conveyor belts are utilized in rubber conveyor belts:
Cut edge rubber conveyor belts are a type of conveyor belt where the edges of the rubber belt are cut during the manufacturing process. These edges are not sealed, meaning the internal fabric or reinforcement materials are exposed. This design is typical for belts where cost savings and flexibility in width are important.
Features of Cut Edge Rubber Conveyor Belts
Material Composition:
- Rubber Covers: The belt is covered with layers of rubber on both the top and bottom surfaces. The rubber provides the belt with resistance to abrasion, impacts, and environmental factors such as heat and chemicals.
- Reinforcement Materials: Inside the rubber, layers of fabric or steel cords are used to reinforce the belt, providing the necessary tensile strength. These can include materials like polyester, nylon, or steel cords.
Edge Design:
- Exposed Edges: The cut edge design leaves the reinforcement layers (such as fabric plies or steel cords) exposed at the edges, which can make the belt more susceptible to wear and environmental damage if not properly maintained.
Flexibility:
- Cut edge rubber belts can be easily cut to specific widths on-site, offering flexibility in installation and customization.
Cost-Effective:
- These belts are typically less expensive to manufacture compared to molded edge belts, making them a cost-effective option for many industrial applications.
Applications of Cut Edge Rubber Conveyor Belts
General Material Handling:
- Used in industries like manufacturing, warehousing, and logistics for the transportation of various materials, including packaged goods, bulk materials, and components.
Mining and Quarrying:
- Commonly used to transport ores, rocks, and other heavy materials in mining operations. The rubber provides good resistance to abrasion from rough materials.
Construction:
- Ideal for conveying building materials such as sand, gravel, and cement in construction sites and related industries.
Agriculture:
- Employed in the transportation of agricultural products like grains, seeds, and fertilizers, where the belt needs to handle various types of loads.
Recycling and Waste Management:
- Used in recycling plants and waste management facilities to convey waste materials, including metals, plastics, and other recyclables.
Advantages of Cut Edge Rubber Conveyor Belts
- Cost-Effective: Lower initial costs compared to molded edge belts.
- Easy to Customize: Can be cut to specific widths and lengths on-site, allowing for flexibility in installation.
- Good Abrasion Resistance: The rubber covers provide excellent resistance to wear and tear, making these belts suitable for abrasive materials.
Disadvantages:
- Vulnerability to Edge Wear: The exposed edges can fray or wear out faster, particularly in harsh environments.
- Higher Maintenance Requirements: Regular inspections and maintenance are needed to monitor the condition of the edges and prevent issues like fraying or delamination.
- Not Ideal for Wet Conditions: Cut edges can absorb moisture, leading to potential degradation of the internal reinforcement materials.
Selection Considerations:
Environmental Conditions:
- In dry, non-corrosive environments, cut edge rubber belts can be very effective.
- For wet or chemically aggressive environments, additional protection or alternative edge designs might be needed.
Material Handling Requirements:
- These belts are well-suited for general-purpose material handling where cost and flexibility are prioritized.
- For heavy-duty or abrasive material handling, ensure the rubber cover thickness and quality are adequate to handle the demands.
Maintenance Practices:
- Ensure that regular maintenance is part of the operation to extend the belt’s lifespan and avoid premature wear due to exposed edges.
Cut edge rubber conveyor belts are a versatile and cost-effective option for a wide range of industrial applications. They are particularly useful in situations where the belt needs to be customized or where initial costs are a concern. However, they require regular maintenance to ensure longevity, especially in harsh operating environments where the exposed edges might be more vulnerable to wear.
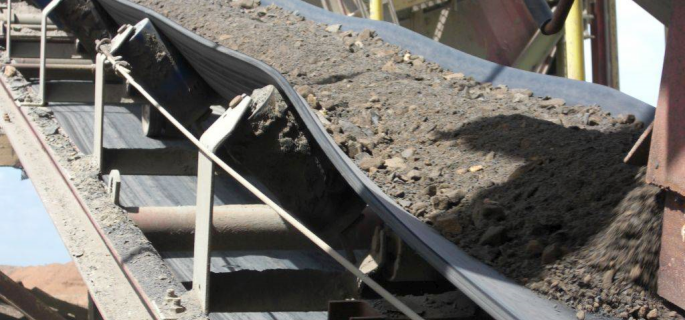
Advantages of Cut Edge Conveyor Belt
Cut edge conveyor belts offer a range of benefits that make them a preferred choice in various industrial applications. Their unique features provide cost-effectiveness, flexibility in sizing, and advantages in inventory management that are particularly appealing for operations looking to optimize efficiency and reduce expenses.
Cost-Effectiveness
The cost-effectiveness of cut edge conveyor belts is one of their most significant advantages over moulded edge belts. Here are five reasons why:
- Simplified Manufacturing Process: The production of cut edge conveyor belts involves a simpler process since it eliminates the need for edge sealing. This reduction in manufacturing complexity directly translates to lower production costs.
- Material Savings: Without the need to seal the edges, there’s less material waste during the production of cut edge conveyor belts. This efficient use of materials further reduces the overall cost.
- Lower Repair Costs: Cut edge conveyor belts can be more easily repaired or resized on-site without specialized equipment, reducing maintenance and repair expenses.
- Economical Customization: The ability to cut the belt to specific widths after manufacturing allows for economical customization to meet precise operational requirements.
- Reduced Shipping Costs: Generally lighter due to the absence of additional edge material, cut edge conveyor belts can be cheaper to transport, contributing to overall cost savings.
Flexibility in Sizing
Cut edge conveyor belts provide unparalleled flexibility in sizing, which is beneficial in several ways:
- Custom Width Adjustment: They can be trimmed to the exact width required for specific applications, ensuring a perfect fit and optimal performance.
- On-Site Customization: The ability to adjust the belt size on-site allows for rapid modifications and adaptations to changing operational needs.
- Reduced Need for Multiple Belt Sizes: Facilities can maintain fewer belt sizes in inventory, as cut edge belts can be customized as needed.
- Efficient Use of Space: By stocking wider belts and cutting them to size as required, companies can make more efficient use of storage space, reducing the need for extensive inventory.
Inventory Management
For distributors and facilities, the advantages of cut edge conveyor belts extend into inventory management:
- Versatility in Stock: Distributors can stock wider belts and cut them to the required widths, allowing them to meet customer demands quickly without the need for a large variety of pre-sized belts.
- Reduced Inventory Costs: By minimizing the number of different belt sizes needed in stock, distributors can significantly reduce inventory costs.
- Faster Response to Customer Needs: The ability to cut belts to size on demand means distributors can offer faster delivery times, improving customer satisfaction.
- Optimized Inventory Space: Storing fewer, wider belts maximizes the use of warehouse space, allowing for a more organized and efficient inventory management system.
Cut edge conveyor belts provide significant advantages in terms of cost savings, flexibility, and inventory management. These benefits make them an attractive option for a wide range of industrial applications, where efficiency and adaptability are key to operational success.
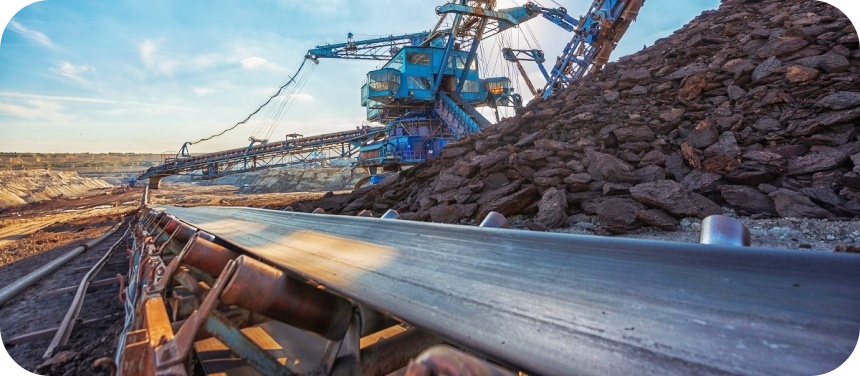
Applications and Considerations for Cut Edge Conveyor Belts
Cut edge conveyor belts are a versatile and cost-effective solution for a wide range of industrial applications. Their design and construction make them particularly suitable for certain industries, though there are environmental and durability considerations that need to be taken into account when choosing between cut edge and moulded edge conveyor belts.
Suitable Industries
Cut edge conveyor belts are commonly used in several key industries due to their flexibility and cost-effectiveness:
- Mining and Quarrying: In these industries, cut edge conveyor belts are favored for their ability to handle rough and abrasive materials, as well as their ease of repair and maintenance in challenging working conditions.
- Agriculture: The agricultural sector benefits from the versatility of cut edge conveyor belts, especially for processing and transporting grains, feeds, and other bulk materials.
- Manufacturing: Various manufacturing processes, from automotive to electronics, utilize cut edge conveyor belts for their adaptability and the straightforward customization they offer for different production lines.
- Recycling Plants: Recycling operations value cut edge conveyor belts for their durability and the economic advantages they provide, especially when handling a wide variety of materials.
Environmental Considerations
The choice between cut edge and moulded edge conveyor belts can be influenced by environmental factors, as outlined in the table below:
Durability Concerns
While cut edge conveyor belts offer significant advantages, there are durability concerns that should be considered:
- Fraying Edges: The exposed fabric or carcass at the edges can fray over time, potentially leading to reduced belt life.
- Moisture Ingress: Without sealed edges, moisture can penetrate the belt, accelerating wear and potentially leading to delamination.
- Contaminant Exposure: Cut edge belts are more vulnerable to contaminants, which can affect the integrity of the belt’s fabric and overall durability.
- Wear and Tear: In harsh industrial environments, the lack of edge protection can result in quicker wear and tear, necessitating more frequent inspections and replacements.
Cut edge conveyor belts are a valuable option for many industries, offering cost savings and flexibility. However, when selecting a conveyor belt, it’s important to consider the specific environmental conditions and potential durability issues associated with cut edge designs. These considerations will help ensure that the chosen conveyor belt meets the operational needs and longevity requirements of the application.
How to Cut Edge Conveyor Belt Safely and Efficiently
Cutting a cut edge conveyor belt to the correct size and specification is a critical process in ensuring the efficient operation of conveyor systems. It requires precision, the right tools, and adherence to safety protocols to prevent accidents and ensure the longevity of the belt.
Tools Required
Several tools can be used to cut a cut edge conveyor belt, each with its advantages in terms of ease of use and safety:
- Utility Knife: Ideal for thinner belts, a sharp utility knife can make precise cuts. Ensure the blade is fresh to reduce effort and increase safety.
- Electric Belt Cutter: Designed for cutting conveyor belts, electric cutters provide a quick and clean cut through thicker belts.
- Heavy-Duty Scissors: For light-duty belts, heavy-duty scissors might be sufficient and offer control over the cut.
- Circular Saw with a Fine-Tooth Blade: For a straight and efficient cut on thicker belts, a circular saw can be used, though it requires more skill and safety precautions.
Step-by-Step Guide
Cutting a cut edge conveyor belt safely and efficiently involves several steps:
- Measure and Mark: Accurately measure the length and width where the belt needs to be cut. Use a chalk line or marker to create a visible cut line.
- Secure the Belt: Clamp the belt down to a stable surface to prevent it from moving while cutting. This ensures both safety and precision.
- Choose the Right Tool: Based on the belt’s thickness and material, select the most appropriate tool for the job.
- Make the Cut: Follow the marked line, using steady pressure to cut through the belt. For thicker belts, multiple passes may be necessary.
- Check the Edges: After cutting, inspect the edges for any fraying or irregularities. Clean up any rough spots to prevent future wear.
Safety Measures
When cutting a cut edge conveyor belt, prioritizing safety is crucial. Here are six important safety measures:
- Wear PPE: Always wear personal protective equipment, including gloves, eye protection, and, if necessary, hearing protection.
- Check the Tools: Ensure all cutting tools are in good condition, with sharp blades to reduce the risk of accidents.
- Work in a Well-Lit Area: Good lighting is essential for precision and safety.
- Keep Your Hands Clear: Always keep your hands and fingers away from the cutting path.
- Secure the Belt: A securely clamped belt won’t slip, reducing the risk of accidents.
- Dispose of Blades Properly: Used blades can be a hazard; dispose of them in a safe container.
Following these guidelines for cutting a cut edge conveyor belt not only ensures the safety of the operator but also contributes to the efficiency and effectiveness of the conveyor system by ensuring the belt is cut to the precise specifications required for optimal operation.
Cut Edge Conveyor Belt: Edge Types Selecting
Selecting the appropriate conveyor belt edge type is crucial for ensuring the belt’s performance, longevity, and suitability for the application. There are primarily two types of conveyor belt edges: cut edge and molded edge. The selection between these types depends on various factors, including the application, environmental conditions, maintenance practices, and cost considerations. Here’s a detailed guide to help in selecting the right edge type:
1. Cut Edge Conveyor Belts
Description:
- The fabric plies of the conveyor belt are cut and left exposed.
- Cut edge conveyor belt the edges are not sealed, meaning the fibers are visible and can be more susceptible to wear.
Advantages:
- Cost-Effective: Cut edge belts are generally less expensive to manufacture, making them more economical.
- Easier to Splice: The absence of a sealed edge can make splicing and joining the belt easier on-site.
- Customizable Width: Easier to cut and customize to specific widths during installation or as per requirement.
Disadvantages:
- Susceptible to Fraying: The exposed fabric can fray over time, especially in harsh environments, which might reduce the belt’s lifespan.
- Maintenance-Intensive: Requires more frequent inspections and maintenance to prevent and address fraying or delamination issues.
- Not Suitable for Wet Environments: Cut edges can absorb moisture, leading to potential weakening and faster degradation of the belt.
Best for:
- Applications where cost is a primary concern.
- Situations where the belt will be frequently spliced or resized.
- Dry environments where the risk of fraying is minimal.
2. Molded Edge Conveyor Belts
Description:
- The edges are sealed during the manufacturing process, often by applying an additional layer of rubber or other protective material.
- The edge is continuous and encapsulated, providing a smooth finish without exposed fibers.
Advantages:
- Better Protection Against Fraying: The sealed edges protect the fabric from fraying, increasing the belt’s lifespan.
- Improved Durability in Wet Environments: Molded edges prevent moisture ingress, making the belt more durable in humid or wet conditions.
- Enhanced Safety: Molded edges reduce the risk of injury during installation and operation, as there are no exposed fibers or sharp edges.
Disadvantages:
- Higher Cost: Molded edge belts are generally more expensive due to the additional manufacturing process.
- Less Flexibility in Width Customization: Cutting the belt to a specific width is more challenging and may require special equipment.
- Potential Issues with Splicing: Molded edges can make splicing more complex and may require specialized techniques or tools.
Best for:
- Applications in wet or humid environments, such as food processing, water treatment, or marine applications.
- Situations where durability and long-term performance are critical.
- Heavy-duty applications where the belt is subjected to significant wear and tear.
Factors to Consider When Selecting Conveyor Belt Edge Types:
Application Environment:
- Dry, Low-Abrasion: Cut edge belts may be sufficient.
- Wet, High-Abrasion: Molded edge belts are recommended.
Material Being Conveyed:
- If the material is abrasive or has sharp edges, a molded edge may offer better protection.
- For non-abrasive materials, a cut edge could be more economical.
Maintenance Capability:
- If regular maintenance is feasible and costs are a concern, a cut edge belt could be considered.
- For low-maintenance operations, molded edge belts are more suitable.
Cost Considerations:
- Cut edge belts are cheaper but may incur higher maintenance costs.
- Molded edge belts have a higher upfront cost but potentially lower long-term maintenance costs.
Belt Width Requirements:
- If the belt needs frequent customization in width, cut edges offer greater flexibility.
- For standard applications with fixed widths, molded edges provide better protection.
The choice between cut edge and molded edge conveyor belts largely depends on the specific operational needs and conditions. For most heavy-duty and wet applications, molded edges are preferable due to their durability and resistance to environmental factors. However, for less demanding applications or where cost is a significant concern, cut edge belts can be a more economical choice, provided that proper maintenance is performed regularly.
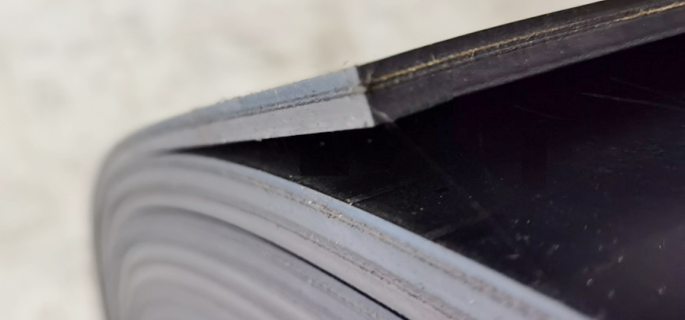
Cost Analysis: Cut Edge vs. Moulded Edge Conveyor Belts
When selecting a conveyor belt for industrial applications, one of the key considerations is cost. This includes not only the initial purchase price but also long-term savings and potential costs associated with durability and maintenance. A comparison between cut edge conveyor belt and moulded edge conveyor belts reveals significant differences in both upfront costs and long-term investment.
Price Comparison
The initial purchase price is a critical factor for many businesses when choosing between cut edge and moulded edge conveyor belts. Generally, cut edge conveyor belts are less expensive than their moulded edge counterparts due to the simpler manufacturing process, which does not require the edges to be sealed. Below is a table comparing the price aspects of both types of belts:
Long-Term Savings
While cut edge conveyor belts offer initial cost savings, it’s essential to consider the long-term implications of choosing them over moulded edge belts. The key factors affecting long-term savings include:
- Durability: Moulded edge belts typically exhibit greater durability due to their protected edges, which can lead to lower replacement costs over time.
- Maintenance: Cut edge belts may require more frequent maintenance or replacement in harsh environments, where the exposed edges are more susceptible to wear and tear.
- Operational Efficiency: Frequent downtime for belt maintenance or replacement can affect operational efficiency, potentially offsetting the initial savings of cut edge belts.
The decision between a cut edge conveyor belt and a moulded edge conveyor belt should be based on a comprehensive cost-benefit analysis. While cut edge belts may offer upfront cost savings, moulded edge belts could provide better value in the long run, especially in applications where the belt is exposed to harsh conditions that could accelerate wear. Factors such as the specific operational environment, maintenance capabilities, and the expected lifespan of the belt should all be considered to make the most cost-effective choice.
Fill out this form to get pricing and availability information for our Cut edge conveyor belt.
FAQs About Cut Edge Conveyor Belt
Cutting a conveyor belt requires precision and the right tools to ensure a clean, straight cut without damaging the belt’s integrity. Start by measuring and marking the area where the cut will be made, using a straight edge to ensure accuracy. A utility knife or a sharp, heavy-duty cutter is commonly used for thinner belts. For safety, wear appropriate personal protective equipment (PPE), such as gloves and eye protection. Make several gentle passes with the knife instead of trying to cut through all at once, to maintain control and precision. This method helps prevent accidents and ensures a straight, clean cut.
Thick conveyor belts pose a greater challenge due to their durability and the materials they are made from. For these, an electric belt cutter is the most efficient tool. Electric belt cutters are designed to handle the thickness and toughness of industrial conveyor belts, cutting through them with precision and ease. Before cutting, secure the belt to prevent it from moving. Mark your cutting line clearly and ensure the electric cutter’s blade is sharp and in good condition. Always follow the manufacturer’s safety instructions when operating the cutter to avoid injuries.
Cutting a conveyor belt straight requires careful measurement and preparation. Use a chalk line or a long straight edge to mark a straight line across the belt where you intend to cut. A reliable method is to clamp a straight edge along the line to guide your cutting tool, ensuring it doesn’t deviate. Whether using a utility knife for thinner belts or an electric cutter for thicker ones, the key is to make slow, controlled cuts, following the guide closely. This method minimizes the risk of the tool slipping and ensures a straight cut.
A cut edge in a conveyor belt refers to the edge finish where the belt’s layers are cut at the end, leaving the fabric or carcass of the belt exposed. This is in contrast to moulded edges, where the belt’s edges are sealed or finished to prevent fraying and exposure of the inner layers. Cut edge belts are often more economical and can be easily customized in width. However, they may be more susceptible to wear and environmental damage due to the exposed edges.
For cutting a conveyor belt, you can use a utility knife for thinner belts or an electric belt cutter for thicker, more durable belts. Utility knives are suitable for small adjustments or light-duty belts, requiring multiple passes to complete the cut. Electric belt cutters offer a more powerful solution, capable of slicing through thick belts with precision and ease. Always ensure the cutting tool is sharp and in good condition to achieve a clean cut and reduce the risk of accidents.
The cut edge of a conveyor belt refers to the exposed sides of the belt material after it has been cut to the desired width during manufacturing. This edge can be treated (sealed) or untreated (left raw) depending on the type of belt and its intended application. The treatment helps to prevent fraying, water ingress, and other forms of deterioration that could affect the belt’s performance and longevity.
There are primarily two types of conveyor belt edges:
Cut Edge: This type of edge is simply the raw, exposed edge of the belt material after it has been cut to width. Cut edges are common in belts with synthetic carcasses and can be treated or untreated.
Molded (or Sealed) Edge: A molded or sealed edge is created during the manufacturing process by folding or molding the outer layer of the belt over the carcass. This type of edge offers better protection against fraying, moisture, and contaminants, making it more durable in harsh environments.
The best way to cut a conveyor belt depends on the material and thickness of the belt. For most standard rubber or fabric belts:
Use a Sharp Utility Knife: Score the belt deeply on both sides and then cut through it with steady pressure. For thicker belts, you may need to use multiple passes.
Heat Cutting: For certain synthetic belts, a hot knife can be used to cut and simultaneously seal the edges, reducing fraying.
Mechanical Cutting Tools: In industrial settings, specialized belt cutting machines or band saws may be used for precise and clean cuts.
Always ensure the belt is secured and supported while cutting, and take proper safety precautions, including wearing gloves and eye protection.
Last Updated on August 12, 2024 by Jordan Smith
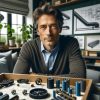
Jordan Smith, a seasoned professional with over 20 years of experience in the conveyor system industry. Jordan’s expertise lies in providing comprehensive solutions for conveyor rollers, belts, and accessories, catering to a wide range of industrial needs. From initial design and configuration to installation and meticulous troubleshooting, Jordan is adept at handling all aspects of conveyor system management. Whether you’re looking to upgrade your production line with efficient conveyor belts, require custom conveyor rollers for specific operations, or need expert advice on selecting the right conveyor accessories for your facility, Jordan is your reliable consultant. For any inquiries or assistance with conveyor system optimization, Jordan is available to share his wealth of knowledge and experience. Feel free to reach out at any time for professional guidance on all matters related to conveyor rollers, belts, and accessories.