Maximizing Efficiency with Deep Impact Rollers in Construction
A deep impact roller is a specialized piece of heavy machinery used predominantly in construction and ground compaction projects to significantly enhance soil stability and density. Unlike traditional compaction equipment, the deep impact roller is designed with a unique, non-cylindrical drum that delivers high-energy impacts deep into the soil layers. This method is particularly effective in densifying loose granular soils, making it an invaluable tool in preparing foundations, roadways, and other infrastructure projects. The use of a deep impact roller is crucial in various engineering applications, as it ensures a solid and stable base, reducing the risk of future settlement and structural issues. Its ability to reach deeper soil layers sets it apart from conventional compaction methods, highlighting its importance in modern construction practices.
Understand the Mechanical Principles of Deep Impact Rollers
Deep impact rollers are a groundbreaking technology in the field of ground compaction, offering a unique approach to soil densification and stabilization. These specialized pieces of equipment operate on mechanical principles distinct from traditional compaction methods, such as vibratory rollers. Understanding how deep impact rollers work, including the technology behind their non-cylindrical, polygonal geometry drums or modules, reveals why they are increasingly preferred for certain compaction tasks.
How Deep Impact Drums Work
The core of a deep impact roller’s functionality lies in its uniquely designed drum or module. Unlike the smooth, cylindrical drums found on traditional rollers, deep impact rollers feature a non-cylindrical, often polygonal drum. This design is pivotal to their operation and effectiveness:
- Non-Cylindrical Geometry: The polygonal geometry of the drum, typically with three to six sides, allows the roller to exert a high-energy impact on the soil surface. As the roller moves, each edge of the polygon acts as a pivot point, creating a lifting and dropping motion that delivers concentrated force to the ground below.
- Energy Transfer: When the edge of the drum lifts off the ground, it builds potential energy due to its height and mass. As it rotates and the next edge strikes the ground, this potential energy is converted into kinetic energy, delivering a powerful impact force deep into the soil layers. This process is repeated continuously as the roller advances, ensuring consistent and deep compaction.
- Depth of Influence: The unique design and operation of deep impact rollers allow them to affect soil layers at a much greater depth than traditional methods. The force of the impact is transmitted downward and outward, densifying soil to depths that can exceed several meters, depending on the soil type and the specific roller used.
Comparison with Traditional Compaction Methods
When compared to traditional compaction methods, such as vibratory rollers, deep impact rollers offer several unique advantages:
- Greater Depth of Compaction: The most significant advantage of deep impact rollers is their ability to compact soil at much greater depths. Vibratory rollers are generally effective for surface compaction and slightly below, but their influence diminishes rapidly with depth. In contrast, deep impact rollers can effectively densify soil layers several meters below the surface.
- Energy Efficiency: The mechanical operation of deep impact rollers, relying on gravity and the conversion of potential to kinetic energy, is inherently energy-efficient. There is no need for additional power to generate vibration, making deep impact rollers a more sustainable choice for large-scale compaction projects.
- Versatility in Soil Types: Deep impact rollers are particularly effective in granular soils, where their impact force can rearrange particles into a denser configuration. However, they are also capable of improving cohesionless soils and mixed soil conditions, offering a versatile solution for various ground engineering challenges.
- Reduced Vibrations: Unlike vibratory rollers that can cause significant vibrations affecting nearby structures, deep impact rollers concentrate their energy downward. This reduces the risk of vibration-induced damage, making them suitable for use near sensitive infrastructure.
The mechanical principles behind deep impact rollers, characterized by their non-cylindrical, polygonal geometry drums, set them apart from traditional compaction methods. These rollers offer unique advantages, including greater depth of compaction, energy efficiency, versatility across different soil types, and reduced vibrations, making them an invaluable tool in modern ground improvement projects.
Deep Impact Roller Manufacturers and Options
The market for deep impact rollers is served by a select group of manufacturers known for their engineering excellence and innovation in compaction technology. These leading deep impact roller manufacturers distinguish themselves through the robustness, efficiency, and technological advancements of their machinery. Each manufacturer brings a unique approach to design and functionality, catering to the diverse needs of construction and ground compaction projects.
When exploring the options for a deep impact roller, potential buyers will find a variety of models available for sale, each with its own set of specifications tailored to meet different project requirements. The range includes rollers with varying drum sizes, impact energy levels, and compaction depths, ensuring there is a suitable option for every type of soil condition and project scale. From compact models designed for smaller, more intricate spaces to larger units capable of delivering high-energy impacts for deep compaction, the selection is vast.
Manufacturers typically provide detailed specifications for each deep impact roller model, including the weight, dimensions, energy rating (measured in Kilojoules), and the maximum achievable depth of compaction. This information is crucial for contractors and project managers to match the roller’s capabilities with the specific needs of their projects, whether it’s for compacting sub-base layers for roadways, preparing sites for large structures, or enhancing ground stability for infrastructure projects.
In addition to the technical specifications, manufacturers often offer customization options and additional features, such as GPS tracking for compaction monitoring, variable frequency controls for impact energy, and adaptable drum configurations to tackle different soil types and compaction requirements. These options further enhance the versatility and effectiveness of deep impact rollers in a wide range of construction and engineering applications.
Choosing the right deep impact roller involves careful consideration of the project’s specific needs, soil conditions, and desired outcomes. Consulting with manufacturers or specialized dealers can provide valuable insights and recommendations, ensuring the selected roller delivers the optimal compaction performance for the task at hand.
Deep Impact Rollers Technology
Deep impact rolling technology represents a significant advancement in the field of ground compaction, offering a unique approach to soil stabilization and densification. This technology, centered around the use of a deep impact roller, distinguishes itself through its method of energy transfer and the depth of impact it achieves, setting it apart from traditional compaction methods. Understanding the intricacies of the impact roller process sheds light on its effectiveness and efficiency in various ground engineering applications.
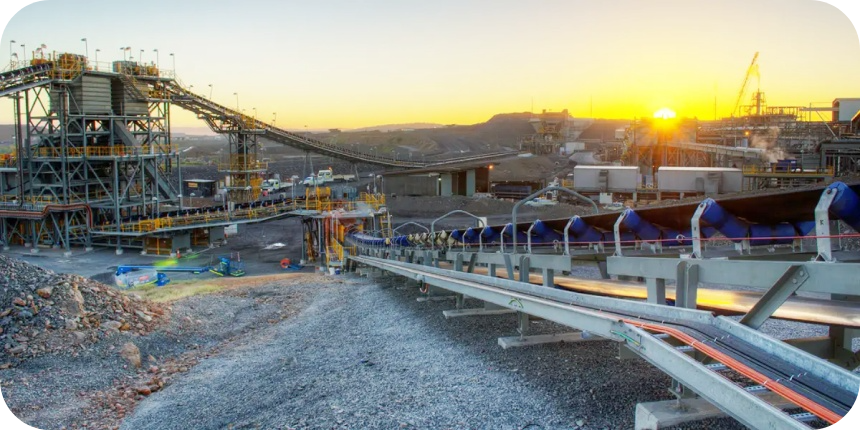
The Impact Roller Process
The operation of a deep impact roller is characterized by its innovative design and the dynamic process of energy transfer it employs:
- Non-Uniform Drum Design: Unlike conventional rollers, the deep impact roller features a non-uniform, often polygonal-shaped drum. This design is crucial for the roller’s unique compaction mechanism, where each edge of the polygon acts as a point of impact, delivering concentrated force into the soil.
- Energy Transfer Mechanism: As the roller moves forward, the polygonal drum rotates, lifting and then dropping each edge onto the soil surface. This action converts the potential energy of the raised drum into kinetic energy upon impact. The magnitude of energy transferred to the soil is significant, allowing for compaction at greater depths than achieved by traditional methods.
- Depth of Impact: The depth of impact achieved by a deep impact roller is a function of the drum’s weight, shape, and the height from which it falls. These factors combine to enable the roller to compact soil layers to depths that can exceed several meters, far surpassing the capabilities of conventional compaction equipment.

Comparison with Other Compaction Methods
To illustrate the advantages of deep impact rolling technology, a comparison with other common compaction methods, such as sheep’s foot rollers and vibratory rollers, is presented in the table below:
- Depth of Impact: Deep impact rollers achieve significantly greater depths of impact compared to sheep’s foot and vibratory rollers, making them ideal for projects requiring deep soil stabilization.
- Energy Efficiency: The gravitational energy conversion mechanism of deep impact rollers is inherently more efficient than the mechanically induced vibrations of vibratory rollers, leading to energy savings and reduced environmental impact.
- Soil Type Suitability: While sheep’s foot rollers are best suited for cohesive soils and vibratory rollers for granular and asphalt surfaces, deep impact rollers offer versatility, effectively compacting a wide range of soil types, including granular, cohesionless, and mixed soils.
- Vibrations to Surroundings: Unlike vibratory rollers, which can generate significant vibrations affecting nearby structures, deep impact rollers produce minimal vibrations, making them safer for use in sensitive areas.
Deep impact rolling technology, through its innovative design and energy transfer mechanism, offers a superior alternative to traditional compaction methods. The deep impact roller not only achieves greater depths of impact but also provides energy efficiency, versatility in soil type suitability, and minimal vibrations to surroundings. This technology represents a significant advancement in the field of ground compaction, offering effective solutions for a wide range of ground engineering challenges.
Impact Rollers in Material Handling: Conveyor Systems
In the realm of material handling, especially within conveyor systems, the role of impact rollers is pivotal in ensuring the efficient and smooth transportation of goods. Specifically, in impact roller conveyors, these components are strategically placed at points where the conveyor belt is subjected to significant loading and impact forces, such as loading zones. The deep impact roller, with its robust design and ability to absorb shocks, plays a crucial role in extending the lifespan of the conveyor belt by distributing the force of falling materials across a wider surface area, thereby minimizing wear and tear.
Impact rollers are designed to withstand the high impact of various materials, ranging from mining ores to packages in a distribution warehouse. They are typically made from durable materials like rubber, which is mounted on the steel roller, to provide a cushioning effect. This design not only protects the conveyor belt from damage but also contributes to the stability of the conveyed materials, reducing spillage and enhancing overall system efficiency.
Complementing the impact rollers in a conveyor system are the load rollers and return rollers, which together ensure the seamless movement of the belt and materials. Load rollers, also known as carrying rollers, are positioned along the carrying side of the conveyor belt and support the weight of the material being transported. They are critical in maintaining the belt’s alignment and preventing sagging, which can lead to uneven wear or material spillage.
On the other hand, return rollers are located on the underside of the conveyor belt, on the return side. Their primary function is to support the belt as it loops back to the beginning of the conveyor system after offloading its cargo. Return rollers help maintain the belt’s tension and alignment, ensuring it runs smoothly and efficiently without slipping or tracking off-course.
Together, impact rollers, load rollers, and return rollers form an integrated system that ensures the conveyor operates smoothly, efficiently, and with minimal downtime. By absorbing the initial shock of loaded materials, deep impact rollers protect the belt and the system as a whole, while load and return rollers provide continuous support and alignment. This synergy is essential for the longevity and productivity of conveyor systems in various material handling applications, making each component indispensable in its own right.
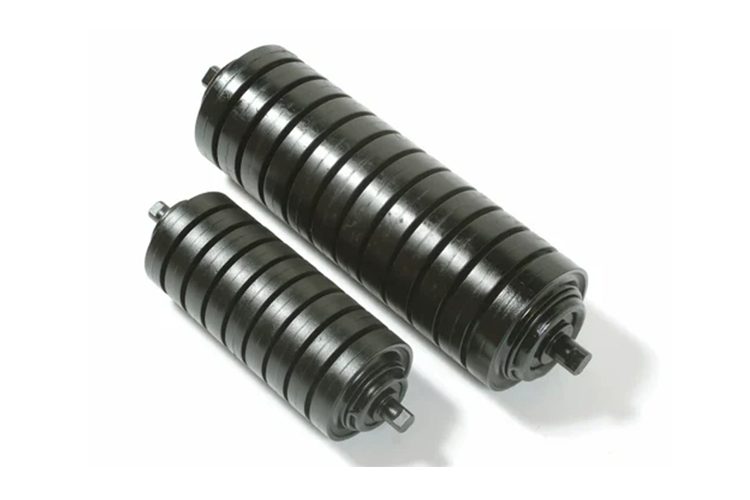
Maintenance and Operations Best Practices for Deep Impact Rollers
Maintaining and operating deep impact rollers effectively are crucial for achieving optimal performance and extending the service life of this sophisticated compaction equipment. By adhering to a set of best practices, operators can ensure that their deep impact roller continues to deliver efficient and effective soil compaction across various projects. Here, we explore essential maintenance tips and operational strategies for deep impact rollers.
Maintenance Tips for Optimal Performance
- Regular Inspection and Cleaning: Conduct thorough inspections of the deep impact roller before and after each use. Pay special attention to the drum and its components, looking for signs of wear or damage. Cleaning the roller after operation is essential to remove any debris that could affect its functionality or cause premature wear.
- Lubrication: Proper lubrication of moving parts is vital to reduce friction and prevent wear. Follow the manufacturer’s recommendations for lubrication intervals and types of lubricants to use. Special attention should be given to the drum rotation mechanism and any bearings or joints.
- Check Hydraulic Systems: Since deep impact rollers rely heavily on hydraulic systems for their operation, regularly check these systems for leaks, proper fluid levels, and pressure. Hydraulic fluid should be replaced according to the manufacturer’s schedule to ensure optimal performance.
- Tire and Pressure Maintenance: For deep impact rollers equipped with tires, maintaining the correct tire pressure is crucial for safe and effective operation. Regularly check and adjust the tire pressure to the manufacturer’s recommended levels.
- Component Replacement: Replace worn or damaged components promptly to prevent further damage and maintain the efficiency of the roller. This includes checking the condition of the polygonal drum edges and replacing them if they become too worn to provide effective compaction.
Best Practices for Operating Deep Impact Rollers
- Proper Training: Ensure that all operators are adequately trained on the specific model of deep impact roller being used. Understanding the unique features and operational techniques of the equipment is essential for achieving the best compaction results.
- Optimal Speed and Pattern: Follow the manufacturer’s guidelines for the optimal speed and pattern of passes to achieve effective soil compaction. The unique lifting and dropping action of the deep impact roller requires careful consideration of travel speed to ensure that energy is efficiently transferred to the soil.
- Soil Condition Assessment: Before compaction, assess the soil conditions to determine the most effective compaction strategy. The effectiveness of deep impact rollers can vary depending on soil type, moisture content, and other factors. Adjusting the compaction approach based on these conditions can lead to better outcomes.
- Monitoring Compaction Progress: Use appropriate methods to monitor the progress of soil compaction, such as compaction meters or post-compaction testing. This will help in determining when the desired soil density has been achieved and prevent over-compaction.
- Safety Precautions: Always adhere to safety protocols when operating deep impact rollers. This includes wearing appropriate personal protective equipment, securing the work area, and being mindful of the roller’s operation, especially the high-energy impacts it delivers.
By following these maintenance and operational best practices, users of deep impact rollers can ensure that their equipment remains reliable, efficient, and capable of delivering superior soil compaction performance. Proper care and skilled operation are the keys to maximizing the benefits of deep impact rolling technology in ground improvement projects.
Submit your deep impact roller specifications and get a fast response.
FAQs about Deep Impact Roller
An impact roller, also known as a dynamic compaction roller, is a specialized piece of heavy construction equipment used primarily for soil compaction in various construction and ground improvement projects. Unlike traditional rollers, an impact roller does not rely on static weight or vibration to compact soil. Instead, it utilizes a unique drum design, often polygonal, which lifts and then forcefully drops onto the soil surface. This action delivers high-energy impacts, mimicking the effects of dynamic compaction but in a continuous and controlled manner.
The design of the impact roller allows it to achieve deep compaction, affecting soil layers several meters below the surface. This capability makes it particularly effective for preparing ground for large-scale construction projects, such as roads, airports, and building foundations, where deep and uniform soil compaction is critical. The roller’s operation involves converting the potential energy of the raised drum into kinetic energy upon impact, efficiently transferring force deep into the ground to densify the soil, reduce air voids, and increase stability.
Impact rollers are versatile and can be used on a variety of soil types, though they are most effective on granular soils. Their ability to achieve deep compaction makes them a valuable tool in ground improvement strategies, offering a solution to soil settlement issues and enhancing the load-bearing capacity of the ground.
The primary difference between an impact roller and a vibratory roller lies in their mechanisms of soil compaction and the depth of impact they can achieve. While both are used for soil compaction, their methodologies and applications vary significantly, catering to different project needs.
Mechanism of Action: Impact rollers utilize a high-energy impact mechanism, where a uniquely designed, often polygonal, drum lifts and forcefully drops onto the soil surface, delivering concentrated impacts. This action allows for deep compaction of the soil. In contrast, vibratory rollers use a combination of weight and rapid vibratory forces to compact the soil. The vibration encourages particle rearrangement and densification but primarily affects the surface and near-surface layers.
Depth of Compaction: One of the most significant differences is the depth of soil compaction achievable. Impact rollers are capable of compacting soil to depths of several meters, making them suitable for projects requiring deep ground stabilization. Vibratory rollers, however, are more effective for surface compaction and are generally used for asphalt compaction or shallow soil compaction, with their effectiveness diminishing with depth.
Soil Type Suitability: Impact rollers are particularly effective on granular, non-cohesive soils, where the impact can efficiently rearrange soil particles for densification. Vibratory rollers, on the other hand, are versatile and can be used on both cohesive and non-cohesive soils but are especially effective on granular materials.
Application: The choice between an impact roller and a vibratory roller often depends on the project requirements. Impact rollers are preferred for large-scale projects needing deep compaction, such as foundation preparation for buildings, roads, and airports. Vibratory rollers are commonly used for road construction, asphalt laying, and shallow soil compaction tasks.
Last Updated on August 5, 2024 by Jordan Smith
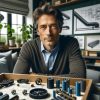
Jordan Smith, a seasoned professional with over 20 years of experience in the conveyor system industry. Jordan’s expertise lies in providing comprehensive solutions for conveyor rollers, belts, and accessories, catering to a wide range of industrial needs. From initial design and configuration to installation and meticulous troubleshooting, Jordan is adept at handling all aspects of conveyor system management. Whether you’re looking to upgrade your production line with efficient conveyor belts, require custom conveyor rollers for specific operations, or need expert advice on selecting the right conveyor accessories for your facility, Jordan is your reliable consultant. For any inquiries or assistance with conveyor system optimization, Jordan is available to share his wealth of knowledge and experience. Feel free to reach out at any time for professional guidance on all matters related to conveyor rollers, belts, and accessories.