Guide to Dewatering Conveyor Belt Material Selection
Conveyor belts are essential components in various industries, facilitating the transport and handling of materials over short and long distances. These belts come in different types, each designed for specific tasks and environments. Among these, dewatering conveyor belts stand out for their unique ability to remove water from materials as they are conveyed. This blog focuses on the dewatering conveyor belt material, which is crucial for effective moisture removal. Such materials are specifically engineered to withstand the rigors of removing water, making them indispensable in industries like mining, agriculture, and waste management. This introduction will explore the characteristics and applications of dewatering conveyor belt materials, underscoring their importance in industrial operations.
What is a Dewatering Conveyor Belt?
A dewatering conveyor belt is a specialized type of conveyor belt designed for the specific purpose of removing water from materials as they are transported from one point to another. This type of conveyor belt is typically used in industries such as mining, agriculture, and food processing where the reduction of moisture in bulk materials is crucial for the subsequent processing or handling stages.
Dewatering Conveyor Belt Material
The material used in dewatering conveyor belts is critical as it needs to possess certain qualities to effectively reduce moisture content. The dewatering conveyor belt material is usually made from a mesh or woven fabric that allows water to escape while retaining the solid particles. Materials such as polyester, polyethylene, or coated stainless steel are commonly used due to their strength, durability, and resistance to moisture, chemicals, and abrasion.
Key Features of Dewatering Conveyor Belts
- Permeable Surface: The surface of the belt is designed to be permeable to allow water to pass through but keep the solid material intact.
- Vibration Mechanisms: These are often integrated to shake off excess water from the material.
- Inclined Design: Many dewatering belts are positioned at an angle to use gravity to assist in the drainage process.
- High Tensile Strength: The belts are engineered to handle the weight of wet materials, which can be significantly heavy.
- Chemical Resistance: Materials used in dewatering belts resist corrosion from various chemicals present in the materials being processed.
- Temperature Resistance: The belts can withstand high temperatures, often necessary when drying materials or working in harsh environments.
- Easy to Clean: Hygiene and maintenance are facilitated by materials that prevent adhesion of particles and are easy to wash.
- Durability: These belts are built to last and withstand continuous operation under wet conditions.
Functionalities of Dewatering Conveyor Belts
- Moisture Reduction: Their primary function is to effectively reduce the moisture content of the bulk material.
- Increased Efficiency in Material Handling: By reducing moisture, the material becomes lighter and easier to manage and transport.
- Preparation for Further Processing: Lowering the moisture content is often a prerequisite for processes such as milling, storage, or packaging.
- Waste Management: In industries like mining, dewatering conveyor belts help in managing and disposing of slurry by separating the water component.
- Product Quality Improvement: For agricultural products and food, moisture reduction can improve the quality and shelf life of the product.
- Energy Savings: Reducing moisture can decrease the energy required for subsequent drying processes.
- Environmental Impact: Efficient dewatering reduces the volume of waste and potentially lowers environmental contamination.
- Cost Reduction: By optimizing material handling and processing, these belts can lead to significant cost savings in operation and maintenance.
Dewatering conveyor belts, by virtue of their design and material, offer a unique solution in numerous industrial applications where moisture reduction is essential for efficient and effective material handling.
Materials Used in Dewatering Conveyor Belt Material
The selection of materials for dewatering conveyor belts is crucial as they must not only support the weight and abrasiveness of the materials being transported but also facilitate the dewatering process. The dewatering conveyor belt material is typically chosen based on its ability to allow water to pass through while ensuring the retention and stability of the conveyed materials. Here we discuss six common materials used in the manufacturing of these belts and the properties that make them suitable for dewatering applications.
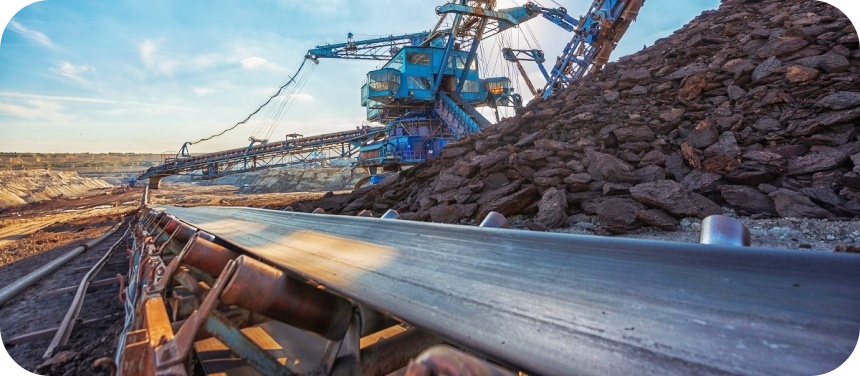
Common Materials Used
- Rubber Composites: Rubber is often used in the form of composites that include fabrics like polyester or nylon to enhance tensile strength. These composites are excellent for heavy-duty applications due to their high durability and resistance to tearing.
- Fabric Belts: Fabrics such as polyester, nylon, and polypropylene are widely used in dewatering conveyor belts. These materials are chosen for their light weight, flexibility, and good water permeability.
- Polyvinyl Chloride (PVC): PVC is valued in dewatering conveyor belt material for its chemical resistance and ability to form a solid, non-porous barrier that can still incorporate perforations for water drainage.
- Polyurethane: Known for its exceptional wear resistance and ability to resist water, oils, and some solvents, polyurethane is often used in environments where durability and hygiene are paramount.
- Stainless Steel Mesh: For applications requiring high levels of hygiene and resistance to high temperatures, stainless steel mesh belts are used. They are especially prevalent in food processing and mining industries.
- Specially Treated Materials: These include materials treated with coatings or processes to enhance specific properties like UV resistance, antimicrobial properties, or increased abrasion resistance, making them ideal for specific industrial environments.
Advantageous Material Properties
- Water Resistance: Materials used in dewatering conveyor belts must be able to resist water to prevent degradation and maintain integrity over long periods.
- Durability: Given the rough industrial environments, the materials need to withstand continuous abrasion, heavy loads, and potentially corrosive substances.
- Mesh Design: The mesh or weave of the material is critical as it determines the efficiency of the water drainage. The size and shape of the mesh holes are designed to maximize water removal while minimizing the loss of solid materials.
- Hygienic Properties: For industries such as food processing, materials that are easy to clean and resistant to bacteria buildup are essential.
- Flexibility and Strength: The materials must be flexible enough to handle the mechanical forces of the conveyor system but strong enough to carry heavy loads without stretching or breaking.
- Chemical and Heat Resistance: Some dewatering processes involve exposure to chemicals and high temperatures, requiring materials that can maintain performance without degrading under such conditions.
By carefully selecting the dewatering conveyor belt material, manufacturers ensure that the belts not only perform their primary function of moisture removal efficiently but also meet the operational demands of different industries, thereby enhancing the overall efficiency of the material handling and processing systems.
Manufacturers of Dewatering Conveyor Belt Materials
The market for dewatering conveyor belt materials is served by a range of manufacturers who specialize in producing materials that are essential for effective water removal in various industries. These manufacturers often provide customized solutions to meet the specific needs of their clients, ensuring that the conveyor belts offer maximum performance in dewatering applications.
Key Manufacturers
Here is a list of nine key manufacturers known for their expertise in producing high-quality dewatering conveyor belt materials:
- ContiTech AG: A leading player in rubber and plastics technology worldwide, known for their durable and high-performance conveyor belts.
- Bridgestone Corporation: Recognized for their technologically advanced rubber products and conveyor belts that are used globally.
- Fenner Group: Specializes in reinforced polymer technology with a strong focus on producing robust conveyor belts for mining and industrial applications.
- Habasit: Known for their comprehensive range of fabric-based conveyor belts and related accessories.
- Ammeraal Beltech: Offers a wide range of belts including those specifically designed for dewatering processes in various industries.
- Intralox: Provides innovative conveyor solutions with a focus on modular plastic conveyor belts.
- Wire Belt Company: Specializes in stainless steel mesh belts that are ideal for dewatering applications requiring high hygiene standards.
- Esbelt: Offers thermoplastic conveyor belts, including those with properties suited for dewatering and other specialized industrial uses.
- Forbo Siegling: Well-regarded for their comprehensive line of conveyor and processing belts, including those used in dewatering.
What to Look for When Selecting a Manufacturer
When choosing a manufacturer for dewatering conveyor belt materials, consider the following eight criteria to ensure you select a reliable and effective provider:
- Material Quality: The durability and performance of the conveyor belt depend largely on the quality of the materials used.
- Industry Experience: Look for manufacturers with specific experience and a proven track record in your industry.
- Customization Options: The ability to tailor the conveyor belt to specific operational needs is crucial.
- Technological Innovation: Manufacturers who invest in research and development tend to offer more advanced and efficient solutions.
- Compliance and Certifications: Ensure that the manufacturer meets all relevant industry standards and certifications.
- Customer Service: Reliable customer support for maintenance, troubleshooting, and advice can significantly impact the effectiveness of your conveyor system.
- Global Reach and Availability: Consider whether the manufacturer can provide products and services in all your operational areas.
- Environmental Standards: Manufacturers that adhere to environmental regulations and strive for sustainability in their production processes are preferable.
Selecting the right manufacturer for your dewatering conveyor belt material is critical. It ensures not only the efficiency of your dewatering process but also the reliability and longevity of the conveyor system itself. Each of these manufacturers brings different strengths to the table, and the best choice will depend on your specific needs and application requirements.
Applications of Dewatering Conveyor Belt Material
Dewatering conveyor belts, utilizing specific dewatering conveyor belt material, are critical components in various industrial processes where the removal of water from materials is necessary to enhance productivity and operational efficiency. These belts are designed to facilitate the quick and effective drying or draining of moisture from products and raw materials. Below are seven detailed examples of industries and scenarios in which these conveyor belts are essential, along with descriptions of how they contribute to the efficiency and effectiveness of operations.
Key Industries and Scenarios
- Mining and Quarrying: In the mining industry, dewatering conveyor belts are used to separate water from minerals. These belts help in the processing of ores after washing to reduce moisture content, which minimizes shipping weight and enhances the efficiency of smelting processes.
- Agriculture: During the harvesting of crops, especially those that are washed before packaging, dewatering belts are used to remove excess water. This not only reduces transport costs but also prevents spoilage during storage.
- Wastewater Treatment: In wastewater treatment facilities, dewatering conveyor belts are essential for the dehydration of sludge. The belts filter and press sludge to extract water, which facilitates more cost-effective disposal and reduces the volume of waste.
- Food Processing: The food industry uses these belts for many applications, including the drying of washed fruits, vegetables, and meats. By removing excess water, the belts help in preserving the quality and extending the shelf life of food products.
- Paper and Pulp Industry: Dewatering belts play a crucial role in the paper manufacturing process where they are used to drain water from pulp slurry before the drying process. This is vital for improving the quality and strength of the paper.
- Chemical Industry: Chemical manufacturers utilize dewatering belts to dry wet chemical compounds. This process ensures that the final products are not only dry but also free from impurities that could be trapped in the water.
- Fisheries and Seafood Processing: In seafood processing, removing excess water from seafood products before freezing or packaging is critical. Dewatering belts help in achieving this by efficiently removing water, thereby enhancing product quality and reducing freezer burn.
Contribution to Efficiency and Effectiveness
In each of these industries, dewatering conveyor belts enhance operational efficiencies by reducing handling difficulties and preparing materials for the next stage of manufacturing or processing. For instance, in mining, reducing the moisture content of ore concentrates aids in reducing transportation costs and improving the ease of handling and processing at smelters. In wastewater treatment, the reduction of sludge volume through effective dewatering cuts down on disposal costs and helps in managing environmental impacts.
Furthermore, the use of specific dewatering conveyor belt materials ensures that these systems can handle the rigorous conditions of different industrial environments, including exposure to chemicals, heavy loads, and abrasive materials. The durability and reliability of these materials help in prolonging the life of conveyor belts and reducing maintenance costs, thereby ensuring continuous production processes without significant downtime.
Dewatering conveyor belts are indispensable in industries where moisture reduction is critical to the product’s quality, handling, and cost-effectiveness, proving their worth as essential components in various industrial operations.
Safety and Maintenance Concerns with Dewatering Conveyor Belt Material
Dewatering conveyor belts, like all industrial machinery, pose certain safety risks if not properly operated and maintained. Understanding these risks and adhering to best practices for safety and maintenance can significantly minimize accidents and ensure efficient operation. Below is an overview of potential dangers specifically associated with dewatering conveyor belts, followed by tips and best practices for their safe operation and maintenance.
Potential Dangers
- Slip and Fall Hazards: The presence of water and moisture makes slip and fall hazards a primary concern around dewatering conveyor belts.
- Entanglement and Pinch Points: Due to the moving parts, there is a risk of entanglement or getting caught in pinch points, which can cause severe injuries.
- Electrical Hazards: The combination of electricity and water can lead to electrical hazards if the equipment is not properly maintained.
- Chemical Exposure: In some industries, dewatering conveyor belts are used to transport chemically treated materials, which can pose risks of exposure.
- Heavy Load Accidents: The weight of wet materials can lead to structural failures if the belts are not adequately supported.
- Bacterial and Mold Growth: Due to the constant presence of moisture, there is a risk of bacterial and mold growth on the conveyor, which can be a health hazard.
Tips for Safe Operation
- Regular Inspections: Conduct regular inspections of the conveyor belt’s integrity and the mechanical parts to ensure everything is in working order.
- Proper Training: Ensure all operators are properly trained on the safe operation of the equipment.
- Use of Safety Guards: Install safety guards at necessary points to prevent accidents.
- Maintain Cleanliness: Regular cleaning of the belt and surrounding area to prevent slips and bacterial growth.
- Emergency Stop Mechanisms: Ensure that emergency stop mechanisms are accessible and functional.
- Adequate Lighting: Provide adequate lighting around the conveyor area to ensure safe operation.
- Proper Signage: Display safety signs clearly around the conveyor area to warn of potential hazards.
- Anti-Slip Flooring: Install anti-slip flooring around the area where the conveyor is operated.
- Chemical Safety Equipment: Provide appropriate personal protective equipment when handling chemically treated materials.
- Routine Maintenance: Follow a routine maintenance schedule to replace worn parts and lubricate moving components.
- Electrical Safety Checks: Regularly check electrical components for signs of damage or exposure to moisture.
- Moisture Control: Implement measures to control moisture accumulation on and around the conveyor.
Best Practices for Maintenance
- Documentation: Keep detailed records of all maintenance activities and safety checks to track the condition of the conveyor belt over time.
- Manufacturer’s Guidelines: Adhere strictly to the manufacturer’s guidelines for maintenance and operation.
- Regular Training Updates: Regularly update training procedures to include new safety practices and operational techniques.
- Monitor Load Capacities: Regularly check that the load capacities are within safe limits to prevent overloading.
- Environmental Controls: Use environmental controls to manage humidity and temperature in the conveyor area to prevent degradation of the belt material.
- Feedback System: Implement a feedback system for operators to report potential issues or suggestions for improvements in safety and operation.
Adhering to these tips and best practices not only helps in maintaining the longevity and efficiency of dewatering conveyor belts but also ensures a safer working environment, minimizing the risk of accidents and health hazards associated with the operation of these essential industrial tools.
Find out more about our Dewatering Conveyor Belt range by filling out the form.
Purchasing Dewatering Conveyor Belt Material
When it comes to purchasing dewatering conveyor belts, selecting the right dewatering conveyor belt material is crucial for ensuring optimal performance and durability. Potential buyers need to consider various factors that affect both the functionality and cost-effectiveness of these belts. Here are ten pieces of advice on what to consider when looking for dewatering conveyor belt material for sale, followed by eight factors that influence their cost and performance.
Advice for Potential Buyers
- Material Suitability: Ensure the material is suitable for the specific type of substances it will convey and the environmental conditions of the operation (e.g., temperature, chemical exposure).
- Water Permeability: The material must have adequate permeability to effectively remove water while retaining solids.
- Durability: Look for materials that are durable and can withstand continuous use under wet conditions without degrading.
- Strength and Load Capacity: The belt should have high tensile strength and be able to handle the expected load without stretching or breaking.
- Maintenance Requirements: Consider the ease of maintenance and cleaning of the conveyor belt material. Materials that are easier to clean and maintain can reduce long-term costs.
- Vendor Reputation: Choose suppliers with good reputations for quality and service to ensure reliability and support after purchase.
- Cost-Effectiveness: Evaluate the cost relative to the performance capabilities and lifespan of the belt.
- Customization Options: Some applications may require custom dimensions or features. Check if the manufacturer offers customization and at what cost.
- Certifications and Standards: Verify that the material meets industry standards and certifications applicable to your industry, ensuring safety and compliance.
- Environmental Impact: Consider the environmental impact of the material, including whether it is recyclable or made from sustainable resources.
Factors Influencing Cost and Performance
- Quality of Material: Higher quality materials might be more expensive but can offer better durability and efficiency, reducing replacement costs.
- Complexity of Design: Custom features such as integrated cleats or sidewalls can add to the cost but improve the belt’s functionality.
- Manufacturer’s Expertise: Experienced manufacturers might charge more but typically deliver superior products and better customer support.
- Supply Chain and Availability: The availability of the material and the length of the supply chain can significantly affect the cost.
- Market Demand: Fluctuations in market demand can influence the prices of raw materials and the final cost of the conveyor belts.
- Technological Enhancements: Advanced technologies for improved performance, such as reinforced edges or specialized coatings, can increase the cost.
- Installation Requirements: Belts that are easier to install and integrate into existing systems may lead to lower overall costs in terms of labor and downtime.
- Operational Costs: Consider the energy efficiency and operational costs associated with the conveyor belt, as some materials may require less power to move or can reduce the load through better water removal.
By taking these factors into consideration, buyers can make informed decisions that balance cost with performance, ensuring that the dewatering conveyor belt they choose will meet their specific needs and provide long-term value in their operations.
FAQs about Dewatering Conveyor Belt Material
Conveyor belts are made from a diverse array of materials, each chosen for its specific properties and suitability for different applications. The most common material is rubber or a rubber composite, which is prized for its durability, flexibility, and ability to handle a variety of loads and environmental conditions. Rubber conveyor belts may also include layers of fabric to increase strength and reduce stretch. Other materials include PVC (Polyvinyl Chloride), which offers excellent resistance to chemicals and abrasion, and thermoplastics like polyurethane, known for their high wear resistance and smooth operation. For applications requiring high strength and durability, belts made from metal meshes or chains are used. Each material offers unique benefits, ranging from grip and resistance to temperatures and chemicals, to the ability to conform to complex paths and handle heavy loads.
Creating a conveyor belt involves several materials, the choice of which depends on the intended use of the belt itself. For general-purpose conveyor belts, materials such as rubber or synthetic fabrics like polyester, nylon, or cotton are common for the belt’s body. For heavy-duty applications, stronger materials like steel cables or woven wire mesh can be employed as the core. The outer layers or coverings of the belts can be made from various grades of rubber, PVC, or thermoplastic material, tailored to withstand wear, abrasion, chemicals, or heat as required by their operating environment. Additional components such as coatings or toppings might be added to enhance properties like friction, anti-static behavior, or resistance to specific chemicals. Understanding the operational demands of the conveyor system is crucial in selecting the appropriate materials to ensure longevity and efficiency.
The “best” material for a conveyor system highly depends on the specific requirements of the operation where it will be used. Polyvinyl Chloride (PVC) belts are favored for general light to medium applications due to their durability and resistance to chemicals and abrasion. For more demanding tasks, especially where higher temperatures, sharp objects, or heavy loads are involved, rubber or metal belts are preferred. Rubber belts are versatile and can be reinforced with fabric or steel cables for added strength. Metal belts, often made of stainless steel or aluminum, excel in environments requiring high strength, durability, and resistance to extreme temperatures or corrosive materials. Polyurethane is another excellent choice, particularly in food processing or pharmaceutical industries, due to its non-toxic and hygienic properties. Ultimately, the best material is one that aligns with the conveyor system’s intended use, taking into account factors like load type, environmental conditions, and wear resistance.
Metals commonly used in conveyor belts include stainless steel, carbon steel, and aluminum, each selected based on the application’s specific needs. Stainless steel is the most popular due to its excellent corrosion resistance, making it ideal for use in the food processing, pharmaceutical, and chemical industries. It can withstand harsh cleaning agents and high temperatures, making it suitable for sterilization processes. Carbon steel is often used in heavy industrial applications due to its high strength and durability; however, it lacks the corrosion resistance of stainless steel and is prone to rust in humid or wet environments unless properly treated or coated. Aluminum, being lightweight, is chosen for applications where reducing the conveyor system’s weight is critical. It’s preferred in situations that require ease of handling and mobility, though it doesn’t offer the same strength or durability as steel. The choice of metal largely depends on a balance between environmental conditions, load requirements, and the need for corrosion resistance.
Last Updated on August 16, 2024 by Jordan Smith
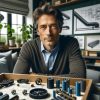
Jordan Smith, a seasoned professional with over 20 years of experience in the conveyor system industry. Jordan’s expertise lies in providing comprehensive solutions for conveyor rollers, belts, and accessories, catering to a wide range of industrial needs. From initial design and configuration to installation and meticulous troubleshooting, Jordan is adept at handling all aspects of conveyor system management. Whether you’re looking to upgrade your production line with efficient conveyor belts, require custom conveyor rollers for specific operations, or need expert advice on selecting the right conveyor accessories for your facility, Jordan is your reliable consultant. For any inquiries or assistance with conveyor system optimization, Jordan is available to share his wealth of knowledge and experience. Feel free to reach out at any time for professional guidance on all matters related to conveyor rollers, belts, and accessories.