Investing in Diamond Top Conveyor Belts: A Smart Choice
Diamond top conveyor belting stands out in the material handling industry for its unique design and exceptional grip. Characterized by its distinctive diamond-patterned surface, this type of belting offers unparalleled traction, making it an ideal choice for conveying goods on steep inclines. The raised diamond profile ensures a secure hold on items, minimizing slippage and enhancing overall transport stability. This introduction delves into the design intricacies and functional benefits of diamond top conveyor belting, setting the stage for a deeper exploration of its cost-effectiveness and practical applications in various industries.
The Cost-Effectiveness of Diamond Top Conveyor Belting
Diamond Top Conveyor Belting: A Comprehensive Analysis of Cost and Efficiency
In the intricate world of material handling and logistics, the choice of conveyor belting is not just a matter of functionality but also a significant financial decision. Diamond top conveyor belting, with its distinctive textured surface, offers a unique combination of durability, grip, and operational efficiency, making it a preferred choice in various industries. However, the true measure of its value lies in understanding its cost-effectiveness, which involves an in-depth analysis of various cost factors, including material, manufacturing, and installation, as well as a comparison with traditional conveyor belts.
1. Material Costs: The Foundation of Quality and Durability
The material used in diamond top conveyor belting is a key factor in its overall cost. Unlike standard flat belts, the diamond top belts are constructed with high-grade materials designed to withstand harsh conditions, including abrasive materials and steep incline transfers. The cost of these materials is inherently higher due to their superior quality and durability. However, this initial cost is offset by the belt’s longevity and reduced need for frequent replacements, translating into long-term savings.
2. Manufacturing Complexity: Precision and Expertise
The manufacturing process of diamond top conveyor belting is more complex than that of standard belts. The creation of the diamond-patterned top involves precise engineering and state-of-the-art machinery to ensure that each belt meets stringent quality standards. This complexity adds to the manufacturing cost. However, the precision in manufacturing ensures a high-performance belt that delivers in terms of efficiency and reliability, justifying the higher production cost.
3. Installation and Maintenance: Ensuring Long-Term Performance
Installation of diamond top conveyor belting may require specialized knowledge and equipment, especially in systems with steep inclines or specific material handling requirements. While this might increase the initial setup cost, proper installation ensures optimal performance and longevity of the belt, reducing the need for frequent maintenance and potential downtimes, which can be costly in terms of both repairs and lost productivity.
4. Operational Efficiency: Maximizing ROI
The true cost-effectiveness of diamond top conveyor belting is most evident when considering its operational efficiency. The unique diamond pattern provides superior grip, reducing slippage and material spillage, especially in steep incline applications. This efficiency translates into faster, more reliable material handling, minimizing waste and maximizing throughput. When compared to traditional conveyor belts, the increased efficiency can lead to significant cost savings over time, offering a higher return on investment.
5. Comparative Analysis with Traditional Belts
When compared to traditional flat or smooth conveyor belts, diamond top conveyor belting offers distinct advantages. Traditional belts often struggle with material slippage, especially in incline applications, leading to material loss and potential damage to the belt itself. The maintenance and replacement costs, coupled with the potential operational downtimes, can add significant expenses in the long run. In contrast, diamond top conveyor belting, with its enhanced grip and durability, provides a more stable and reliable solution, reducing the frequency of these costly issues.
While the initial cost of diamond top conveyor belting may be higher than that of traditional belts, its durability, manufacturing quality, operational efficiency, and reduced maintenance needs make it a cost-effective solution in the long term. Businesses looking to optimize their material handling processes and maximize their return on investment would do well to consider the long-term benefits and savings offered by diamond top conveyor belting.
Locating Diamond Top Conveyor Belting Near You
Diamond Top Conveyor Belting: Strategies for Finding the Best Suppliers and Manufacturers
Finding the right supplier or manufacturer for diamond top conveyor belting is crucial for ensuring the quality and reliability of your material handling system. The market is vast, with numerous providers offering a range of products and services. However, not all suppliers are created equal, and choosing the right one can be the difference between a system that enhances your operational efficiency and one that becomes a source of constant issues and expenses. This section provides a comprehensive guide on how to locate and evaluate suppliers and manufacturers of diamond top conveyor belting in your area.
1. Leveraging Online Resources
The internet is a powerful tool for locating suppliers of diamond top conveyor belting. A simple search can yield a list of potential suppliers, complete with websites, product catalogs, and contact information. Many suppliers also offer online quote systems, allowing you to get a sense of pricing and availability quickly. Additionally, online trade directories and industry forums can provide valuable insights into the reputation and reliability of different suppliers.
2. Industry Networks and Recommendations
Tapping into your industry network can provide valuable leads on where to find quality diamond top conveyor belting. Recommendations from peers, industry associations, or trade groups can be particularly trustworthy, as they come from individuals and organizations with firsthand experience with various suppliers.
3. Evaluating Local Suppliers
Once you have a list of potential suppliers, evaluating them based on certain criteria can help you make an informed decision. Key factors to consider include:
- Product Range: Does the supplier offer a wide range of conveyor belting options, including the specific type and specifications you need?
- Customization Options: Can the supplier provide custom-sized belts or specific features to meet your unique operational requirements?
- Quality and Reliability: What is the supplier’s reputation for product quality and reliability? Look for certifications, customer testimonials, and case studies.
- Customer Service: Does the supplier offer comprehensive customer support, including consultation, installation, and after-sales service?
- Pricing: While not the only factor, pricing is important. Ensure that the cost aligns with the quality and service offered.
4. Visiting Facilities and Meeting with Suppliers
If possible, visiting the supplier’s facility can provide valuable insights into their operations, quality control processes, and company culture. Meeting with the supplier’s team can also help establish a strong business relationship and ensure that they understand your specific needs and expectations.
Finding the right supplier for diamond top conveyor belting requires a combination of online research, leveraging industry networks, thorough evaluation of potential suppliers, and, if possible, personal visits and meetings. By taking these steps, you can ensure that you partner with a supplier that offers high-quality products, reliable service, and a commitment to meeting your specific material handling needs.
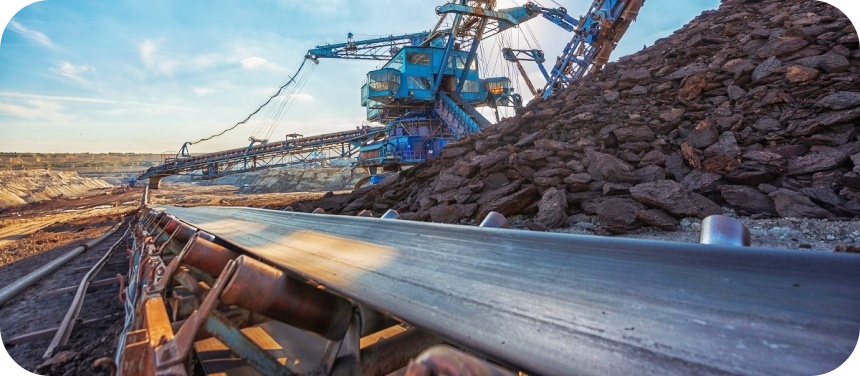
What is the Investment: Cost of Belt Conveyor Systems
Evaluating the Financial Implications of Diamond Top Conveyor Belting
Investing in a diamond top conveyor belt system involves a comprehensive understanding of both the initial costs and the long-term financial benefits. This section delves into the various aspects of this investment.
Initial Investment Costs
- Purchase Price: The cost of a diamond top conveyor belt varies based on size, length, and specific design features. These belts are typically more expensive than standard flat belts due to their specialized design and material.
- Installation Expenses: Installation costs can be significant, especially for complex systems. This includes labor, integration into existing systems, and potential modifications to the facility.
- Customization and Additional Features: Customized features, such as specific belt widths, lengths, or unique diamond patterns, can add to the initial cost.
Operational Costs
- Energy Consumption: Diamond top conveyor belts are designed for efficiency, but the energy cost for operation should be considered, especially for large-scale systems.
- Maintenance and Repairs: Regular maintenance is essential to keep the system running smoothly. Budgeting for routine checks, repairs, and potential belt replacements is crucial.
Long-Term Benefits and ROI
- Increased Productivity: The unique design of diamond top conveyor belts allows for efficient handling of materials, particularly in incline/decline applications, leading to increased productivity.
- Durability and Longevity: High-quality diamond top conveyor belts are more durable, reducing the frequency of replacements and maintenance costs over time.
- Safety and Reduced Downtime: The enhanced grip of diamond top belts can lead to fewer accidents and material spillage, reducing downtime and potential liability costs.
- Energy Efficiency: Modern diamond top conveyor belts are designed to be energy efficient, which can lead to cost savings in the long run.
- ROI Calculation: When calculating ROI, consider the increased efficiency, reduced downtime, and potential increase in production capacity.
Maximizing Efficiency: Maximum Angle of Belt Conveyor
Exploring the Incline Capabilities of Diamond Top Conveyor Belting
Diamond top conveyor belts are renowned for their ability to handle steep inclines, a feature that sets them apart from other conveyor belt types. This section explores their maximum angle capabilities and operational advantages.
Maximum Angle of Incline
- Comparative Analysis: Diamond top conveyor belts can handle steeper inclines compared to flat or smooth belts due to their enhanced grip and stability.
- Angle Limitations: The maximum angle of incline for a diamond top conveyor belt depends on factors like belt width, material weight, and the nature of the material being conveyed.
Case Studies and Operational Advantages
- Industrial Applications: Case studies in industries like mining, agriculture, and manufacturing, where diamond top belts have successfully transported materials on steep inclines.
- Efficiency in Material Handling: Examples showcasing how these belts have improved efficiency by reducing the need for additional material handling equipment.
- Comparative Performance: Analysis of scenarios where diamond top belts outperform other types in terms of handling steep inclines.
Maintenance and Optimization: Diamond Top Conveyor Belting Tips
Ensuring Longevity and Performance of Diamond Top Conveyor Belts
Proper maintenance and optimization are key to maximizing the lifespan and efficiency of diamond top conveyor belts. This section provides best practices and tips for maintaining these specialized belts.
Maintenance Best Practices
- Regular Inspections: Routine checks for wear and tear, alignment issues, and damage to the diamond pattern.
- Cleaning Protocols: Guidelines for cleaning the belt to prevent material buildup, which can affect grip and efficiency.
- Lubrication and Adjustments: Tips on lubricating moving parts and making necessary adjustments to maintain belt tension and alignment.
Five Tips for Preventing Common Issues
- Avoid Overloading: Ensuring the belt is not overloaded, which can lead to premature wear and potential damage.
- Proper Material Handling: Tips on optimizing material loading to prevent uneven wear and extend belt life.
- Environmental Considerations: Advice on protecting the belt from harsh environmental conditions that can accelerate wear.
- Training for Operators: Importance of training personnel on proper operation and maintenance of the conveyor system.
- Scheduled Downtime for Maintenance: Planning for regular downtime to perform comprehensive maintenance checks and repairs.
By following these maintenance and optimization strategies, operators can significantly enhance the performance and extend the lifespan of their diamond top conveyor belting, ensuring continued operational efficiency and reliability.
Innovative Applications of Diamond Top Conveyor Belting
Diamond Top Conveyor Belting: Pioneering Solutions in Material Handling
In the dynamic landscape of industrial operations, diamond top conveyor belting has emerged not just as a tool for material conveyance but as a pivotal component in innovative solutions across various sectors. The unique properties of diamond top conveyor belting, such as its high friction surface and durability, have been ingeniously leveraged to address complex material handling challenges, leading to operational transformations and efficiency enhancements. This section delves into the unique and innovative applications of diamond top conveyor belting in different industries and presents case studies that highlight how businesses have capitalized on these properties to solve intricate material handling problems.
1. Revolutionizing the Packaging Industry
In the packaging industry, precision and speed are paramount. Diamond top conveyor belting has been instrumental in ensuring the rapid and secure movement of packaged goods, especially in facilities with steep incline conveyors. The high-grip surface minimizes slippage, ensuring that products, regardless of their packaging material, are transported efficiently without the risk of falls or disturbances. Case studies from leading packaging facilities demonstrate how integrating diamond top conveyor belting has streamlined operations, reduced product damage, and enhanced overall productivity.
2. Transforming Agricultural Operations
Agriculture is an industry where the handling of diverse materials, from grains to fertilizers, is routine. The versatility of diamond top conveyor belting has been a game-changer in this sector. Its ability to securely transport materials of varying granularities and weights has led to significant improvements in the handling and distribution processes. For instance, a case study from a large-scale grain processing plant illustrates how diamond top conveyor belting facilitated the smooth and spill-free transfer of grains, thereby reducing waste and improving operational efficiency.
3. Innovations in Recycling Facilities
Recycling facilities often deal with a mix of materials that need to be sorted and processed. The robustness of diamond top conveyor belting, coupled with its high friction surface, has made it an invaluable asset in these facilities. It ensures the steady movement of recycled materials up steep conveyors for sorting and processing. A detailed case study from a recycling plant shows how the adoption of diamond top conveyor belting significantly reduced material spillage and contributed to a more streamlined and environmentally friendly operation.
4. Enhancements in Manufacturing Units
In manufacturing units, especially those dealing with heavy or bulky items, the strength and grip offered by diamond top conveyor belting have led to safer and more reliable material handling solutions. For instance, in the automotive industry, where components need to be moved swiftly and securely, diamond top conveyor belts have provided a solution that combines speed with stability, as evidenced by multiple case studies from leading automotive manufacturers.
Diamond top conveyor belting has transcended its traditional role, becoming a catalyst for innovation in various industries. Through its unique properties, it has provided solutions to longstanding challenges in material handling, leading to operational efficiencies, cost savings, and enhanced safety. The case studies presented in this section are a testament to the versatility and transformative potential of diamond top conveyor belting.
Safety and Compliance in Diamond Top Conveyor Belting
Diamond Top Conveyor Belting: Ensuring Safety and Adherence to Standards
Safety and compliance are paramount in any industrial operation, and conveyor systems are no exception. Diamond top conveyor belting, with its unique design and material properties, brings forth inherent safety features that are crucial in minimizing workplace accidents and ensuring smooth operations. Moreover, adherence to industry standards and compliance requirements is essential to maintain operational integrity and avoid legal complications. This section discusses the safety features inherent to diamond top conveyor belting and provides an overview of the industry standards and compliance requirements relevant to this type of belting.
1. Inherent Safety Features of Diamond Top Conveyor Belting
The design of diamond top conveyor belting inherently enhances safety in material handling operations. The high coefficient of friction provided by the diamond-patterned surface significantly reduces the risk of slippage, a common cause of accidents in conveyor operations. This feature is particularly beneficial in industries where conveyor belts are inclined or where the materials being transported are prone to shifting. Additionally, the robust construction of diamond top conveyor belts ensures that they can withstand heavy loads and harsh conditions without compromising the safety or integrity of the materials being transported.
2. Compliance with Industry Standards
Adherence to industry standards is critical in ensuring the safety and reliability of conveyor belting systems. Diamond top conveyor belting is designed and manufactured in compliance with stringent industry standards, which cover aspects such as material quality, belt strength, and durability. These standards ensure that the belting systems are capable of handling the operational demands without posing risks to workers or the materials being transported.
3. Meeting Regulatory Requirements
Beyond industry standards, diamond top conveyor belting is also subject to various regulatory requirements, which may vary depending on the region and the specific application of the belting system. These regulations often pertain to safety, environmental impact, and operational efficiency. Manufacturers and users of diamond top conveyor belting must be well-informed about these requirements and ensure that their operations are in full compliance to avoid penalties and ensure uninterrupted operations.
4. Case Studies: Safety and Compliance in Action
Real-world case studies illustrate how diamond top conveyor belting has been implemented in a manner that prioritizes safety and compliance. For instance, in the food processing industry, where hygiene and safety are of utmost importance, diamond top conveyor belting has been used to ensure the safe and contamination-free transport of food products, while adhering to strict food safety regulations. Similarly, in industries such as mining and construction, where the risk of accidents is higher, the implementation of diamond top conveyor belting has led to a noticeable reduction in workplace incidents, demonstrating the belt’s contribution to a safer working environment.
Diamond top conveyor belting not only enhances the efficiency and reliability of material handling operations but also contributes significantly to the safety and compliance aspects of industrial operations. Its unique design features, coupled with a strong commitment to adhering to industry standards and regulatory requirements, make it an exemplary solution in the pursuit of safe, compliant, and efficient material handling solutions. The case studies presented in this section underscore the importance of integrating safety and compliance into every aspect of conveyor belt design and operation.
Learn more about our high-performance conveyor belt options.
FAQs about Diamond Top Conveyor Belting
Flat Belt Conveyors: These are the most common type of conveyor belts, used in a variety of industries. They consist of a flat belt surface that moves over rollers or a flat pan. Flat belt conveyors are versatile and can transport a range of items, from small components to large boxes.
Modular Belt Conveyors: Made of individual, interlocked segments, usually of hard plastic, modular belt conveyors are durable and easy to clean. They are suitable for applications that require the transport of heavy loads or exposure to harsh conditions, such as in food processing.
Cleated Belt Conveyors: These conveyors have vertical cleats or barriers on their surface, which are useful for preventing slippage or controlling the position of items on the belt. They are ideal for incline or decline applications, or when moving products that need to be kept in a specific orientation.
The “best” conveyor belt depends on the specific requirements of the application, including the type of materials being transported, the environment in which the conveyor operates, and the required speed and efficiency. Here are some considerations:
For General Use: PVC conveyor belts are popular for general applications due to their durability and versatility.
For Heavy-Duty Applications: Rubber conveyor belts are preferred for their strength and resilience.
For Food Industry: Food-grade conveyor belts made of materials like polyurethane are best as they meet health and safety standards.
For High-Temperature Environments: Heat-resistant conveyor belts are necessary to withstand high temperatures.
The ISO standard for conveyor belting is ISO 14890. This standard specifies requirements for rubber or plastic-covered conveyor belting of textile construction for general surface use on flat or troughed idlers. It includes mechanical and physical properties, methods of test, and marking requirements. This standard helps ensure quality, safety, and efficiency in conveyor belt manufacturing and use.
A rough top conveyor belt is a type of belt that has a textured surface pattern to increase friction between the belt and the items being conveyed. This texture often resembles small raised bumps or ridges, providing a “grippy” surface. Rough top conveyor belts are commonly used in applications where items need to be transported at an incline or decline, as the increased friction helps prevent slippage of items. They are ideal for moving boxes, packages, or other materials that require stability during transport. These belts are also used in applications where shock absorption is beneficial, such as in sorting systems.
Last Updated on July 18, 2024 by Jordan Smith
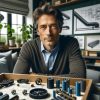
Jordan Smith, a seasoned professional with over 20 years of experience in the conveyor system industry. Jordan’s expertise lies in providing comprehensive solutions for conveyor rollers, belts, and accessories, catering to a wide range of industrial needs. From initial design and configuration to installation and meticulous troubleshooting, Jordan is adept at handling all aspects of conveyor system management. Whether you’re looking to upgrade your production line with efficient conveyor belts, require custom conveyor rollers for specific operations, or need expert advice on selecting the right conveyor accessories for your facility, Jordan is your reliable consultant. For any inquiries or assistance with conveyor system optimization, Jordan is available to share his wealth of knowledge and experience. Feel free to reach out at any time for professional guidance on all matters related to conveyor rollers, belts, and accessories.