Maximizing Efficiency with Dip Angle Belt Conveyor Design
The dip angle belt conveyor is a critical component in the design and operation of efficient conveyor systems. This angle, which refers to the inclination or decline of the conveyor belt, plays a pivotal role in determining the conveyor’s capability to transport materials effectively. Understanding the dip angle belt conveyor is essential for optimizing the conveyor’s performance, especially in terms of the angle of contact between the belt and pulley. This introduction delves into the nuances of the dip angle, exploring how it affects the overall functionality of the conveyor system. Additionally, it covers the importance of precision in tasks like cutting conveyor belts straight, which is vital for maintaining the desired dip angle and ensuring smooth operation.
Defining the Dip Angle Belt Conveyor
The Concept of the Dip Angle Belt Conveyor
The dip angle, also known as the incline or decline angle, is a crucial aspect in the design and operation of belt conveyors. It refers to the angle at which the conveyor operates relative to the horizontal plane. This angle is pivotal in determining the conveyor’s ability to transport materials effectively and efficiently.
Explanation of Dip Angle
- Definition: The dip angle of a belt conveyor is the angle formed between the horizontal plane and the line of the conveyor belt that transports the material.
- Measurement: It is typically measured in degrees, and its calculation is essential for the design and setup of the conveyor system.
Impact on Conveyor’s Material Transport Capability
- Incline Conveying: When transporting materials uphill, the dip angle affects how much material the conveyor can carry without spillage or slippage. A steeper angle may require specialized belt designs or modifications to maintain efficiency.
- Decline Conveying: For downhill transportation, the dip angle influences the speed and control of the material flow. Too steep an angle can lead to material roll-back or excessive speed, leading to potential system damage or safety hazards.
Factors Influencing Effective Dip Angles
- Material Characteristics: The type of material being conveyed (e.g., granular, sticky, or fine particles) significantly impacts the suitable dip angle. Different materials will behave differently at various inclines.
- Conveyor Belt Design: Features like belt width, texture, and the presence of cleats or sidewalls can affect the maximum effective dip angle.
- Operational Considerations: Factors such as the desired speed of material transport, the length of the conveyor, and the height difference between the start and end points play a role in determining the optimal dip angle.
The dip angle belt conveyor is a fundamental parameter that affects the conveyor’s design, efficiency, and safety. Understanding and correctly implementing the dip angle is essential for ensuring the conveyor system operates smoothly and effectively, meeting the specific material handling requirements.
The Angle of Contact Between Belt and Pulley in the Dip Angle Belt Conveyor
Exploring the Contact Angle in the Dip Angle Belt Conveyor
The angle of contact between the belt and pulley in a dip angle belt conveyor is a critical factor that influences the conveyor’s grip and efficiency. This section delves into the formula used to calculate this angle and discusses its impact on the conveyor system’s overall performance.
Formula for Calculating the Angle of Contact
- Basic Concept: The angle of contact, also known as the wrap angle, is the portion of the pulley over which the belt wraps or contacts.
- Calculation Formula: The angle of contact can be calculated using the formula: ( \text{Angle of Contact} = 180° + 2 \times \arccos\left(\frac{(D – d)}{2C}\right) ), where ( D ) is the diameter of the larger pulley, ( d ) is the diameter of the smaller pulley, and ( C ) is the center-to-center distance between the pulleys.
Impact of Contact Angle on Conveyor Grip and Efficiency
- Grip and Traction: A larger angle of contact increases the belt’s grip on the pulley, which is particularly important in dip angle belt conveyors where gravity affects the material’s movement.
- Power Transmission: The contact angle affects the efficiency of power transmission from the motor to the belt. A sufficient wrap angle ensures that the motor’s power is effectively transferred to the belt without slippage.
- Belt Tension: The angle of contact also influences the tension distribution across the belt. Proper tensioning is essential for the smooth operation of the conveyor and the prevention of belt slippage.
Considerations for Optimizing Contact Angle
- Pulley Size and Spacing: Adjusting the size of the pulleys and their spacing can alter the contact angle, enhancing the conveyor’s grip and efficiency.
- Tensioning Devices: The use of tensioning devices like take-up units can help maintain an optimal contact angle, especially in varying load conditions.
- Belt Material and Texture: The material and texture of the conveyor belt can affect the required contact angle for efficient operation. Rough or textured belts may require a different angle compared to smooth belts.
The angle of contact between the belt and pulley in the dip angle belt conveyor is a vital aspect that dictates the system’s grip, power transmission efficiency, and overall performance. Accurate calculation and adjustment of this angle are crucial for the optimal functioning of the conveyor system.
Maximum Dip Angles for Different Conveyor Types
Analyzing Maximum Dip Angles in Various Conveyor Belt Systems
The maximum dip angle belt conveyor can effectively operate at varies significantly depending on the type of conveyor system and its design. This section provides an analysis of the maximum dip angles for various conveyor belt types, drawing parallels to Coveya’s approach, and considers factors like belt patterns and material types.
Different Conveyor Belt Types and Their Maximum Dip Angles
- Flat Belt Conveyors: Typically, these conveyors have a maximum dip angle of around 20°. Beyond this, material slippage becomes a concern.
- Chevron Pattern Belt Conveyors: With a 15mm chevron pattern, these conveyors can handle steeper inclines, up to about 32°, as the pattern provides additional grip.
- Troughed and Flighted Belt Conveyors: Designed for even steeper requirements, these can go up to 45° for ordinary excavated material, thanks to their unique shape and added flights.

Flat Belt Conveyors
Factors Influencing Maximum Dip Angles
- Belt Design: Features like sidewalls, cleats, and patterns (e.g., chevron) on the belt surface play a crucial role in determining the conveyor’s maximum dip angle.
- Material Characteristics: The type of material being conveyed (size, weight, texture) significantly impacts the maximum feasible dip angle. Heavier or more fluid materials may require a lesser incline to prevent rollback or spillage.
- Conveyor Length and Speed: Longer conveyors and those operating at higher speeds may have limitations on the maximum dip angle to ensure material control and safety.
Considerations for Specific Material Types
- Granular vs. Cohesive Materials: Granular materials like sand may be conveyed at steeper angles compared to more cohesive materials like wet clay, which require a shallower angle to prevent slippage.
- Impact of Material Size and Shape: Larger or irregularly shaped materials may necessitate a reduced dip angle to maintain stability and prevent dislodgement during transport.
The maximum dip angle belt conveyor is a critical factor that varies with the type of conveyor and the material being transported. Understanding these limitations and designing conveyor systems accordingly is essential for efficient and safe material handling operations.
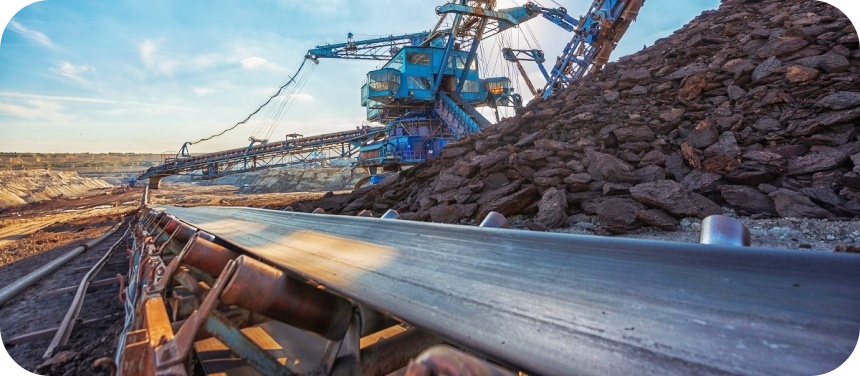
Anti-reversal Control Methods of Dip Angle Conveyor Belt
In conveyor systems with steep inclines, preventing the conveyor belt from reversing is crucial, especially during system stoppages or sudden halts. Reverse movement can lead to material loss, equipment damage, and safety hazards. Here are some anti-reversal control methods for dip angle conveyor belts:
Backstop (Anti-Reverse Device)
- Description: A mechanical device installed in the drive unit to prevent the conveyor belt from reversing.
- Working Principle:
- During normal operation, the backstop rotates freely.
- When the conveyor belt attempts to reverse, wedges or rollers inside the backstop lock the shaft, preventing backward movement.
- Advantages:
- Effectively prevents belt reversal, especially in high-incline conveyor belts.
- Installed on the drive motor, gearbox, or sprocket.
Electromagnetic Brakes
- Description: Use electromagnetic force to generate braking power, controlling the stopping and starting of the conveyor belt.
- Working Principle:
- When energized, the brake releases, allowing free movement.
- When de-energized, it applies braking force to prevent reverse movement.
- Advantages:
- Precise stopping position control of the conveyor belt.
- Remote control and automation operation.
- Especially suitable for conveyor systems with frequent start-stop operations.
Hydraulic Brakes
- Description: Use hydraulic systems to generate braking force, controlling the movement of the conveyor belt.
- Working Principle:
- The hydraulic brake uses hydraulic oil pressure to generate braking force, preventing the belt from reversing.
- Advantages:
- Provides strong and adjustable braking force.
- Performs well under heavy load conditions.

Hydraulic Brakes
Holdbacks
- Description: Installed on the conveyor pulley to prevent belt reversal during sudden stops or power failures.
- Working Principle:
- Usually, a mechanical pawl or ratchet device locks the pulley shaft, preventing the conveyor belt from reversing.
- Advantages:
- Simple and economical operation.
- Particularly suitable for long-distance, heavy-load, or high-incline conveyor systems.
Centrifugal Brakes
- Description: Devices that use centrifugal force to generate braking power.
- Working Principle:
- When the conveyor belt reverses, centrifugal force causes friction plates or blocks inside the brake to contact and generate braking force.
- Advantages:
- High degree of automation and excellent anti-reversal effects.
- Suitable for medium to high-incline conveyor belts.
Safety Control Systems
- Description: Combine sensors and control logic to monitor conveyor belt operation and prevent reversal.
- Working Principle:
- Sensors: Speed sensors monitor conveyor belt speed. If an abnormal reversal trend is detected, they send a signal to the control system.
- Control Logic: Upon receiving the signal from the sensors, the control system automatically activates braking devices to prevent belt reversal.
- Advantages:
- Enables automated control, reducing manual intervention.
- Reliable system suitable for various conveyor belt systems.
Several anti-reversal control methods are available for inclined conveyor belts. Selection and combination depend on specific conveyor conditions, environmental factors, and load requirements. Effective anti-reversal control ensures safe conveyor belt operation, prevents material loss, reduces downtime, and improves productivity.
Material Size, Shape, and Conveyor Efficiency in the Dip Angle Belt Conveyor
Impact of Material Characteristics on Conveyor Efficiency
The efficiency of a dip angle belt conveyor is significantly influenced by the size and shape of the materials it transports. This section discusses how these material characteristics affect the suitable dip angle and offers tips for optimizing conveyor efficiency based on these factors.
Influence of Material Size on Conveyor Dip Angle
- Large vs. Small Materials: Larger, bulkier materials may require a shallower dip angle to prevent them from rolling or sliding back, especially on steeper inclines. Conversely, smaller materials can be transported at steeper angles without significant risk of displacement.
- Material Weight Considerations: Heavier materials exert more force on the conveyor belt, potentially leading to slippage at steeper angles. Adjusting the dip angle based on material weight is crucial for maintaining efficiency.
Role of Material Shape in Determining Dip Angle
- Irregular Shapes: Materials with irregular shapes, such as large rocks or uneven debris, can destabilize at steep angles, necessitating a more gradual incline.
- Spherical or Rounded Materials: These shapes pose a unique challenge as they can roll easily. Conveyors handling such materials might require specialized belt designs or reduced dip angles to ensure stability.
Tips for Optimizing Conveyor Efficiency
- Belt Design Adaptations: Utilizing belts with features like cleats, sidewalls, or textured surfaces can enhance grip and stability for various material types.
- Adjustable Dip Angles: Implementing conveyors with adjustable inclines can offer flexibility to accommodate different material sizes and shapes.
- Regular Material Assessment: Continuously assessing the material characteristics and adjusting the conveyor settings accordingly can optimize efficiency and prevent operational issues.
Safety and Handling Considerations
- Preventing Spillage: For materials prone to spillage, a shallower dip angle or containment measures like side guards can be effective.
- Load Distribution: Ensuring even distribution of materials across the belt width can prevent imbalances and maintain optimal conveyor function.
The size and shape of materials being conveyed are critical factors in determining the suitable dip angle for belt conveyors. By understanding and adapting to these characteristics, conveyor efficiency can be optimized, ensuring smooth and effective material handling operations.

Motor Size Considerations for Steeper Angles in the Dip Angle Belt Conveyor
Evaluating Motor Requirements for Steep Incline Conveyors
When designing dip angle belt conveyors, especially those operating at steeper angles, the size and power of the motor become critical factors. This section delves into how increased dip angles may necessitate more powerful motors and the factors to consider when sizing these motors.
Impact of Steeper Angles on Motor Sizing
- Increased Load on the Motor: Steeper inclines in belt conveyors require the motor to work harder to move materials uphill, thereby increasing the load and power requirements.
- Gravity and Material Weight: As the dip angle increases, the effect of gravity on the conveyed material becomes more pronounced, requiring additional motor power to maintain consistent movement and prevent backsliding.
Factors Influencing Motor Size for Steep Conveyors
- Conveyor Length and Incline Degree: Longer conveyors with higher incline angles demand more power to transport materials efficiently.
- Material Characteristics: The weight, size, and type of material being conveyed influence the motor’s power requirements. Heavier and bulkier materials require stronger motors.
- Belt Speed and Capacity: Desired belt speed and the capacity of the conveyor also play a role in determining the appropriate motor size.
Calculating Motor Power for Steep Dip Angle Conveyors
- Power Calculation Formulas: Engineers use specific formulas to calculate the required motor power, taking into account factors like belt speed, conveyor length, incline angle, and material weight.
- Consultation with Manufacturers: It’s often advisable to consult with conveyor manufacturers or specialists to accurately determine the motor size needed for a specific application.
Ensuring Motor Efficiency and Reliability
- Safety Margins: Incorporating safety margins in motor power calculations can account for potential variations in material load and operational conditions.
- Quality Motors: Choosing high-quality, reliable motors can enhance the efficiency and longevity of the conveyor system.
- Regular Maintenance: Routine maintenance of the motor and conveyor system ensures optimal performance and prevents unexpected breakdowns.
Motor size is a critical consideration in the design of the dip angle belt conveyor, particularly for steep inclines. Proper sizing and selection of the motor ensure the conveyor operates efficiently, handles the required material load, and maintains consistent performance over time.
Techniques for Cutting Conveyor Belts Straight in the Dip Angle Belt Conveyor
Ensuring Precise Belt Cutting for Optimal Conveyor Performance
In dip angle belt conveyors, cutting the conveyor belt straight is crucial for maintaining proper alignment and efficiency. This section provides a step-by-step guide on how to accurately cut conveyor belts, ensuring optimal alignment and efficiency, and highlights the importance of precision in belt cutting for maintaining the desired dip angle.
Step-by-Step Guide to Cutting Conveyor Belts Straight
- Measuring and Marking: Begin by accurately measuring the required length of the belt. Use a chalk line or marker to create a straight line across the width of the belt.
- Using the Right Tools: Employ a straight edge or a carpenter’s square along with a sharp cutting tool, such as a utility knife or a specialized belt cutter, to ensure a clean, straight cut.
- Cutting Technique: Place the straight edge along the marked line. Apply steady pressure with the cutting tool, ensuring that the cut is perpendicular to the belt edges.
- Double-Checking the Cut: After cutting, verify the straightness of the cut using a measuring tape or square. Any deviations can affect the belt’s tracking and efficiency.
Importance of Precision in Belt Cutting
- Alignment and Tracking: A straight cut is essential for proper belt alignment. Misaligned cuts can lead to tracking issues, causing uneven wear and potential system malfunctions.
- Maintaining Dip Angle Integrity: Precise cutting is crucial for maintaining the conveyor’s designed dip angle. Inaccurate cuts can alter the belt’s path, affecting the conveyor’s ability to transport materials efficiently at the intended angle.
- Joint Quality: For spliced belts, a straight cut ensures a better joint quality, which is vital for the belt’s strength and longevity.
Looking for durable and efficient conveyor belts? Inquire here!
Tips for Maintaining Cutting Precision
- Regular Tool Maintenance: Keep cutting tools sharp and well-maintained to ensure clean and straight cuts.
- Training and Skill Development: Operators should be trained in proper cutting techniques and understand the importance of precision in this process.
- Quality Control Checks: Implement regular quality control checks to ensure that the belt cuts meet the required standards.
Cutting conveyor belts straight is a critical aspect of conveyor belt maintenance, especially for the dip angle belt conveyor. Precision in this process ensures proper belt alignment, maintains the conveyor’s efficiency, and contributes to the overall reliability of the conveyor system.
The Important Role of With Dip Angle Belt Conveyor in Industry
The Important Role of Dip Angle Belt Conveyor in Industry
A belt conveyor with a dip angle, often referred to as a steep angle or high-incline belt conveyor, plays a crucial role in various industries. It allows the efficient transportation of materials over steep inclines, providing numerous benefits in terms of space optimization, cost savings, and operational efficiency. Here’s a detailed exploration of its significant role in industry:
Efficient Space Utilization
- Steep Incline Capability:
- Dip angle belt conveyors are capable of handling gradients up to 90 degrees, enabling vertical lifting of materials.
- This unique capability drastically reduces the footprint of the conveyor system, which is essential for facilities with limited space.
- Shorter Conveyor Length:
- The ability to lift materials at steep angles minimizes the conveyor length required to transport materials between different elevations.
- This feature optimizes the use of floor space, allowing more equipment or production lines to be accommodated.
Reduced Operational Costs
- Infrastructure Savings:
- The compact design requires fewer structural frameworks due to the minimized conveyor path.
- The reduced number of transfer points results in lower spillage, less wear and tear, and subsequently lower maintenance costs.
- Maintenance Efficiency:
- Fewer transfer points also translate to reduced maintenance efforts and costs compared to conventional conveyor systems.
- A well-maintained dip angle belt conveyor can significantly reduce unplanned downtime.
Versatile Material Handling
- Diverse Material Compatibility:
- Suitable for handling a wide range of materials, including granular, powdery, and lump materials.
- Effective for transporting wet or dry materials, abrasive substances, and sticky products.
- Application Versatility:
- Ideal for industries like mining, coal processing, cement production, agriculture, and more, where steep incline conveying is beneficial.
Minimized Material Spillage
- Sidewalls and Cleats:
- The use of sidewalls and transverse cleats keeps the materials contained within the belt.
- This design ensures that materials do not spill even at steep angles, making it suitable for high-capacity conveying.
- Cleaner Work Environment:
- Reduced spillage ensures a cleaner work environment, enhancing workplace safety and productivity.
High Conveying Efficiency
- Continuous Flow:
- Dip angle belt conveyors provide continuous material flow over steep inclines, improving overall throughput.
- This continuous flow reduces the need for intermediate storage and additional handling equipment.
- Fast Installation:
- The modular design allows for quick installation, reducing downtime and improving production efficiency.
Adaptability to Challenging Terrains
- Overcoming Obstacles:
- Dip angle belt conveyors can efficiently transport materials over rugged terrains, such as hills and valleys.
- Mining Applications:
- Effective for both underground mining (vertical shafts) and open-pit mining, where space constraints require compact solutions.
Applications Across Various Industries
- Mining and Quarrying:
- Transporting ore, coal, and other minerals from underground or open-pit mines to processing plants.
- Cement Industry:
- Conveying limestone, clay, and other raw materials to kilns or storage facilities.
- Agriculture:
- Moving grains and seeds to silos or processing plants.
- Food Processing:
- Efficiently transporting granular food products or packaged goods.
- Chemical and Fertilizer Production:
- Conveying chemical powders, granules, and fertilizers vertically.
- Power Plants:
- Moving coal and other fuels to boilers.
- Waste Management and Recycling:
- Conveying recyclables or waste materials to sorting or processing units.
Design Considerations and Challenges
- Material Characteristics:
- The choice of belt and cleat materials depends on the type of material being transported.
- Abrasive materials require wear-resistant belts and components.
- Capacity and Speed:
- Capacity and speed must be balanced to achieve the desired throughput while preventing material spillage.
- Belt Tension:
- Proper tension is required to prevent slippage or excessive wear due to high inclines.
- Maintenance:
- Regular inspection and maintenance of cleats, sidewalls, and belt tension are crucial for optimal performance.
With its ability to convey materials over steep inclines, the dip angle belt conveyor plays a pivotal role in improving efficiency and optimizing space in various industries. By offering a compact design, high versatility, and minimized spillage, it helps industries reduce operational costs and streamline material handling operations, making it an invaluable component in many production and processing environments.
FAQs about Dip Angle Belt Conveyor
The angle of a belt conveyor, often referred to as the conveyor’s incline or decline angle, is the angle at which the conveyor is tilted relative to the horizontal plane. This angle can vary widely depending on the application and the type of material being transported. For flat conveyors, this angle is typically zero, but for inclined or declined conveyors, it can range from a few degrees to a steep slope.
The maximum angle for a conveyor belt varies depending on the material being conveyed and the type of conveyor belt used. Generally, the maximum incline angle for a troughed belt conveyor handling dry, free-flowing material ranges from 15 to 20 degrees. However, using specialized belts and cleats, inclines of up to 30 degrees or more can be achieved for certain materials.
The belt conveyor surcharge angle refers to the angle formed between the horizontal plane and a line drawn from the edge of the load carried by the conveyor belt to the center of the maximum cross-sectional area of the load. This angle is significant because it helps determine the carrying capacity of the conveyor and affects the conveyor belt’s selection and design. The surcharge angle is influenced by the properties of the material being transported, such as its size, shape, and moisture content.
The inclination angle for coal on a belt conveyor typically depends on the type of coal, its size, and moisture content, as well as the design of the conveyor belt. For most coal applications, the inclination angle can range from 0 to 20 degrees. For steeper inclines, specially designed belts with higher friction and sidewalls or cleats might be used to prevent slippage and roll-back of the coal.
Last Updated on June 14, 2024 by Jordan Smith
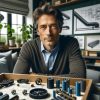
Jordan Smith, a seasoned professional with over 20 years of experience in the conveyor system industry. Jordan’s expertise lies in providing comprehensive solutions for conveyor rollers, belts, and accessories, catering to a wide range of industrial needs. From initial design and configuration to installation and meticulous troubleshooting, Jordan is adept at handling all aspects of conveyor system management. Whether you’re looking to upgrade your production line with efficient conveyor belts, require custom conveyor rollers for specific operations, or need expert advice on selecting the right conveyor accessories for your facility, Jordan is your reliable consultant. For any inquiries or assistance with conveyor system optimization, Jordan is available to share his wealth of knowledge and experience. Feel free to reach out at any time for professional guidance on all matters related to conveyor rollers, belts, and accessories.