Material Handling: Disadvantages of Belt Conveyor
Conveyor systems are integral to the operations of a myriad of industries, facilitating the efficient movement of materials and products through production lines and distribution centers. Among these systems, belt conveyors stand out for their versatility and widespread application across sectors such as manufacturing, mining, agriculture, and logistics. They are prized for their ability to transport a diverse range of goods over long distances, both horizontally and vertically, with simplicity and ease. However, despite their significant advantages and broad utility, the disadvantages of belt conveyor systems also merit attention. These drawbacks can impact their suitability for certain applications, influencing the choice of conveyor technology for specific industrial needs. As we delve deeper into the operational aspects of belt conveyors, understanding these limitations becomes crucial for optimizing material handling strategies and selecting the most appropriate conveying solutions.
Describe The Belt Conveyor in Detail
A belt conveyor is a pivotal material handling equipment used across various industries, particularly prevalent in mining, metallurgy, and coal sectors. It primarily consists of two or more pulleys (with at least one providing power) and a loop of carrying medium—the conveyor belt—that rotates around them. Materials are placed on this belt to be transported from one point to another with the aid of the rotating pulleys. Let’s delve into the definition, advantages, and applications of belt conveyors in detail.
Definition
A belt conveyor is a continuous transportation equipment that uses a belt—stretched across pulleys—to move materials. This system can transport materials horizontally, on an incline, or vertically, making it an excellent option for long-distance, high-volume, and continuous material transportation tasks.
Advantages
- Efficiency: Belt conveyors can transport materials continuously and are ideal for large-scale production demands.
- Versatility: They can adapt to various harsh environments, including high or low temperatures or dusty conditions.
- Low Energy Consumption: Compared to other types of transportation equipment, belt conveyors use less energy for the same amount of material transported.
- Safety: They are safe to operate, reducing labor intensity and improving working conditions.
- Long Transportation Distance: Belt conveyors can cover distances of several hundred meters to tens of kilometers.
- Ease of Maintenance: With a simple structure, maintenance is straightforward and quick.
Applications
- Mining Industry: For the transportation of ores, coal, and other extracted materials during the mining and processing stages.
- Metallurgy: Used in the iron and steel-making process for the transportation of raw materials, finished products, or semi-finished goods.
- Chemical and Pharmaceutical Industries: For the transportation of bulk chemicals, pharmaceuticals, etc.
- Grain Processing and Storage: In the handling and storage of grains.
- Airports: As part of the luggage handling systems.
- Postal and Courier Services: Used in parcel sorting centers for the efficient and effective sorting of packages.
- Manufacturing: For conveying components and finished products along production lines.
Operating Principle
The operating principle of belt conveyor systems is relatively straightforward but ingeniously effective, facilitating the movement of materials over long distances, across varying elevations, and at a controlled pace. At its core, a belt conveyor consists of a motor-driven pulley (the drive pulley) and one or more additional idler pulleys. The conveyor belt, a loop of flexible material, wraps around these pulleys. The drive pulley is powered, often by an electric motor, and it imparts motion to the belt, enabling the entire system to move materials from one point to another. Here’s a more detailed look at the operation principle of belt conveyors:
Components of a Belt Conveyor
- Conveyor Belt: This is the carrying medium of the belt conveyor system. It is made of various materials, such as rubber, PVC, or fabric, depending on the type of materials being transported.
- Drive Pulley: Connected to the motor, this pulley provides the force that drives the conveyor belt.
- Idler Pulleys: These pulleys support the conveyor belt and can adjust the belt’s tension and direction.
- Electric Motor: It powers the drive pulley and can be controlled to adjust the speed of the belt.
- Frame: The structure that supports the conveyor components and maintains their alignment.
Operation Principle
- Initiation: The process begins when the electric motor transfers power to the drive pulley. The interaction between the motor and the pulley is typically through a gearbox, which reduces the motor’s speed to the desired conveyor speed.
- Motion Transmission: The drive pulley, receiving rotational power from the motor, rotates on its axis. This rotation, due to the friction between the pulley surface and the conveyor belt, propels the belt forward.
- Material Movement: Materials placed on the conveyor belt are carried forward as the belt moves. The belt’s surface can be customized (e.g., textured, ridged) to transport various materials efficiently, whether they are bulk materials like grains or individual items like packages.
- Direction and Speed Control: The system’s design allows for control over the direction and speed of material transport. This is achieved by adjusting the motor’s operation and, if necessary, using additional conveyors in series or parallel arrangements to direct materials to different locations.
- Support and Tension: Idler pulleys are spaced along the conveyor to support the belt and materials. They also help in maintaining the correct tension in the belt, ensuring smooth operation and preventing slippage or sagging.
- End of Line: At the conveyor’s end, materials are off-loaded, either manually, through automated systems like robotic arms, or by gravity (down chutes).
Versatility
Belt conveyors operate on a simple mechanism: a powered pulley, known as the drive pulley, moves a continuous loop of material—the conveyor belt—along a fixed path. The non-powered pulley, or idler, provides tension and support. This system offers several advantages:
- Adaptability: Can be designed to transport materials horizontally, inclined, or even vertically.
- Customization: Available in various sizes and configurations to handle different types of materials.
- Control: Speed and direction of the belt can be easily adjusted to suit operational needs.
- Efficiency: Ideal for transporting large volumes of materials consistently and with minimal labor.
Belt conveyors, with their efficiency, versatility, and low energy consumption, play a crucial role across various fields. From simple material handling tasks to complex production line arrangements, belt conveyors are an indispensable component, demonstrating their importance and utility in modern industry.Despite these benefits, belt conveyors are not without their limitations.
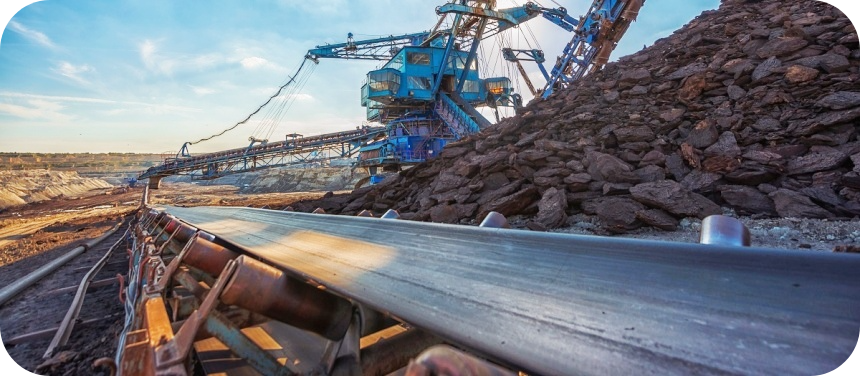
Examining the Disadvantages of Belt Conveyor Systems in Material Handling
While belt conveyors are a staple in many industries due to their ability to efficiently transport materials over both short and long distances, come with certain disadvantages that can impact their suitability and efficiency in some scenarios. This section delves into their versatility across various sectors, and the specific drawbacks that users may encounter.
Limited Material Types
Belt conveyors are not universally adaptable to all types of materials. Their design and material composition make them less suitable for:
- Very Hot Materials: The heat can warp or melt the conveyor belt, causing operational failures and necessitating frequent replacements.
- Sharp Objects: Sharp materials can cut or puncture the belt, leading to potential hazards and system downtime for repairs.
- Sticky Materials: Certain substances can adhere to the belt, disrupting the smooth flow of materials and complicating cleaning processes.
- Abrasive Materials: Over time, abrasive materials can wear down the belt surface, diminishing its durability and effectiveness.
- Heavy Loads: Excessive weight can strain the belt, pulleys, and motors, increasing the risk of breakdowns.
- Chemically Reactive Materials: Some materials may react with the belt material, leading to degradation and the need for specific belt compositions, which can be costly.
Maintenance and Durability Concerns
The maintenance and durability of belt conveyors present several challenges:
- Regular Inspections: To prevent failures, belt conveyors require frequent inspections to check for wear, alignment, and tension.
- Belt Alignment Issues: Misalignment can cause uneven wear and tear, necessitating adjustments and repairs to avoid more significant damage.
- Wear and Tear: Continuous operation leads to inevitable wear, impacting the belt, rollers, and pulleys, and requiring periodic replacement.
- Cleaning Requirements: Accumulation of debris and materials necessitates regular cleaning to maintain operational efficiency and prevent damage.
- Lubrication Needs: Moving parts require lubrication, adding to maintenance tasks and costs.
- Vulnerability to Environmental Conditions: Exposure to moisture, temperature extremes, and contaminants can accelerate wear and necessitate additional maintenance.
- Complexity of Repairs: Repairing or replacing parts of a belt conveyor can be time-consuming and may require specialized skills.
- Downtime: Maintenance and repairs can lead to operational downtime, affecting productivity.
- Costs: The cumulative effect of maintenance requirements can lead to significant costs in terms of parts, labor, and lost productivity.
Efficiency and Speed Limitations
While belt conveyors are a popular choice for many material handling applications due to their simplicity and effectiveness, they exhibit certain limitations in terms of efficiency and speed that can affect their overall performance:
- Speed Constraints: Belt conveyors generally offer lower speeds compared to automated systems like pneumatic conveyors, which can rapidly transport materials across various distances. This limitation can reduce throughput in high-volume or fast-paced operations.
- Efficiency Issues: The mechanical nature of belt conveyors means they may not always provide the most energy-efficient means of transportation, especially over short distances where the startup and shutdown processes consume a disproportionate amount of energy.
- Limited Agility: Belt conveyors lack the agility to quickly adapt to changing operational needs, such as varying speeds for different products or operational phases, without manual intervention or complex control systems.
- Productivity Bottlenecks: In systems requiring high throughput, the inherent speed limitations of belt conveyors can become a bottleneck, reducing overall productivity and efficiency.
- Energy Use at Scale: For large-scale operations, the continuous operation of belt conveyors, especially over long distances, can lead to significant energy consumption, impacting operational costs and sustainability goals.
- Material Handling Restrictions: The effectiveness and speed of belt conveyors can be compromised when handling bulky, irregularly shaped, or very heavy materials, requiring slower speeds or additional equipment to ensure safe transport.
Environmental Impact
The environmental footprint of belt conveyor systems, while often overlooked, includes several aspects that can have significant implications:
- High Energy Consumption: The continuous operation of belt conveyors, particularly in large facilities, contributes to high energy usage, which can be a concern for operations aiming to reduce their carbon footprint.
- Use of Lubricants: The maintenance of belt conveyors involves the use of lubricants and greases, which, if not properly managed, can lead to environmental contamination and pose challenges in terms of disposal and recycling.
- Noise Emissions: The operation of belt conveyors can generate noise pollution, particularly in large distribution centers or open mining operations, potentially impacting local wildlife and communities.
- Dust and Particulate Matter: The movement of materials, especially in industries like mining and agriculture, can generate dust and particulate emissions, contributing to air quality concerns and requiring additional mitigation measures.
- Resource Intensive: The production and maintenance of belt conveyors involve the use of significant amounts of metal and synthetic materials, which have their own environmental impacts in terms of resource extraction, manufacturing, and eventual disposal or recycling.
- Heat Generation: In some cases, the operation of belt conveyors can generate heat, contributing to thermal pollution and affecting the microclimate in enclosed spaces, which may require additional ventilation or cooling solutions.
- Water Usage: Cleaning and maintenance of belt conveyors, particularly in food processing or pharmaceutical applications, can consume substantial amounts of water, impacting the overall sustainability of operations.
Installation Space
- Large Footprint: Belt conveyors often require a significant amount of space for installation due to their linear design and the need to accommodate long distances. This can be a major limitation in facilities where space is constrained or in environments where the layout must be optimized for multiple processes.
- Inflexible Layout: The requirement for a predefined, linear path limits the ability to easily modify the facility layout without substantial changes or reinstallation of the conveyor system. This can lead to inefficiencies or require additional investment in space reconfiguration should operational needs change.
Cost
- High Initial Investment: The upfront cost of belt conveyor systems can be quite high. This includes the expenses for purchasing all necessary components—conveyor belt, motors, pulleys, support structure—and the cost of installation. The total investment can be a significant consideration for small or medium-sized operations.
- Maintenance and Operational Expenses: Beyond the initial investment, belt conveyors incur ongoing maintenance and operational costs. Regular maintenance is required to ensure smooth operation, and parts like the belt itself may need periodic replacement due to wear and tear. Additionally, the energy costs associated with running the conveyor system can add up, especially for systems that operate continuously over long periods.
- Specialized Requirements: Depending on the application, specialized conveyor belts that can handle extreme temperatures, abrasive materials, or specific hygiene standards may be required, further driving up costs.
Flexibility Limitations
- Adaptability to Change: Belt conveyors are designed for a specific path and operation. Making changes to the system, whether to alter its path, length, or to accommodate different materials, can be challenging and costly. This lack of flexibility makes it difficult to adapt the system to evolving operational needs without significant modifications.
- Handling Varied Materials: While belt conveyors can transport a wide range of materials, they may not be the best choice for all types of cargo. For example, very fine materials can slip through gaps in the conveyor, and very bulky or irregularly shaped items may not transport smoothly. This limitation necessitates careful consideration of the materials to be moved before implementing a belt conveyor system.
- System Complexity: Increasing the system’s flexibility often requires additional components like switches, turntables, or elevators, which can complicate the conveyor system. Each additional component not only increases the initial cost but also the maintenance requirements and potential points of failure within the system.
While belt conveyors offer significant advantages in terms of efficiency and capability for continuous, long-distance material transport, their disadvantages in terms of limited material types ,maintenance and durability concerns,efficiency and speed limitations,environmental impact,installation space requirements, cost implications, and flexibility limitations must be carefully considered. These factors can significantly impact the overall effectiveness and suitability of belt conveyor systems for specific applications, influencing both short-term operations and long-term strategic planning.
When evaluating the disadvantages of belt conveyor systems, it’s beneficial to compare them with other types of conveyor systems, such as chain and screw conveyors, as well as to consider the advantages of alternative systems like bucket conveyors. This comparison can help in selecting the most suitable conveyor system for specific material handling needs.
Disadvantages of Belt Conveyors:Other Conveyors
The Difference Between Conveyor Belts and Chain Conveyors
Conveyor belts and chain conveyors are both integral components of material handling systems, each offering unique features and benefits. Understanding the differences between them is crucial for selecting the most appropriate system for a given application. Here’s a detailed comparison:
Conveyor Belts
Definition and Mechanism:
- A conveyor belt consists of a continuous loop of material that rotates around two or more pulleys. It operates on the principle of friction between the belt and pulleys to move materials along the belt’s surface.
Advantages:
- Versatility: Conveyor belts can transport a wide variety of materials, including those with irregular shapes or sizes.
- Gentle Handling: They offer smooth and continuous motion, which is ideal for fragile or delicate items.
- Speed and Efficiency: Belt conveyors can move materials quickly and continuously, improving efficiency in production lines and material handling tasks.
Disadvantages:
- Limitations with Vertical Transport: While inclined belts can handle some elevation changes, steep or vertical transport is generally not feasible.
- Maintenance: The belt itself may require regular maintenance, cleaning, or replacement due to wear and tear or material spillage.
Chain Conveyors
Definition and Mechanism:
- Chain conveyors utilize a series of chains or a chain loop to transport materials. They can be designed with single or multiple chains and might include attachments or carriers for specific materials.
Advantages:
- Durability and Strength: Chain conveyors are typically more robust and can carry heavier loads, including pallets and large containers, making them suitable for industrial environments.
- Versatility in Direction: They can easily accommodate vertical, horizontal, and curved paths, providing flexibility in configuring production lines or material handling systems.
- Low Maintenance: The chains are generally durable and require less frequent maintenance compared to conveyor belts.
Disadvantages:
- Noise and Wear: Chain conveyors can be noisier during operation and may produce more wear and tear on transported materials, which might not be ideal for fragile items.
- Cost: The initial installation and setup costs can be higher for chain conveyors, especially for complex configurations or heavy-duty applications.
Key Differences
- Material Handling Capabilities: Conveyor belts are more suited for handling a wide range of materials, including fine, granular, or delicate items. Chain conveyors, on the other hand, are better for heavy or bulky materials that require more support and strength during transport.
- Path Flexibility: Chain conveyors offer more flexibility in terms of the path, able to move materials vertically and around corners more effectively than conveyor belts.
- Operational Environment: Conveyor belts provide a smoother operation suitable for environments where noise reduction is important, whereas chain conveyors are preferred in industrial settings where durability and load capacity are prioritized.
- Maintenance and Durability: While both systems require maintenance, the nature and frequency can differ. Conveyor belts often need attention to ensure the belt remains intact and clean, whereas chain conveyors might require lubrication and inspection of links and attachments.
Selecting between a conveyor belt and a chain conveyor depends on the specific needs of the application, including the types of materials being transported, the required direction and path of transport, operational environment considerations, and budget constraints.
Disadvantages of Chain and Screw Conveyors
Chain and screw conveyors are commonly used in various industries for material handling tasks. Here’s a brief comparison highlighting their advantages and disadvantages in contrast to belt conveyors:
Advantages of Bucket Conveyors
Bucket conveyors offer several advantages over belt conveyors, especially in specific applications where precision and vertical transport are crucial. Here are at least eight advantages of bucket conveyors:
- Vertical Transport: Bucket conveyors excel in vertical material handling, offering efficient elevation of materials without the need for inclined configurations.
- Handling of Fragile Materials: The bucket design minimizes material damage, making it ideal for fragile goods.
- Precision Loading and Unloading: Buckets allow for precise control over the loading and unloading points, reducing spillage.
- High Capacity: Designed for high-capacity transport, bucket conveyors can handle large volumes of material efficiently.
- Compact Footprint: Vertical design saves valuable floor space in facilities.
- Versatility: Can handle a wide range of material types, including powdery, granular, and small-sized goods.
- Reduced Maintenance: Compared to belt conveyors, bucket conveyors often require less maintenance as they have fewer moving parts in contact with the material.
- Environmental Considerations: Bucket conveyors can be enclosed to prevent dust and spillage, improving the working environment and reducing waste.
While belt conveyors are versatile and widely used, understanding their disadvantages in comparison to other conveyor systems like chain, screw, and bucket conveyors is crucial. This knowledge aids in selecting the most appropriate system based on the specific requirements of material type, operational efficiency, space constraints, and environmental impact.

Applications Where Belt Conveyors Fall Short: Disadvantages of Belt Conveyor Systems
Application Status of Belt Conveyors
Belt conveyors are a cornerstone in the material handling sector, with their application spanning multiple industries due to their efficiency and versatility. The application status of belt conveyors showcases their pivotal role in automating processes, enhancing productivity, and optimizing logistics. Here’s a detailed exploration of their application across various sectors:
Mining and Quarrying
- Bulk Material Transport: Belt conveyors are extensively used in the mining industry to transport bulk materials such as coal, ore, and gravel over long distances, from the mining site to processing facilities or loading docks.
- Safety and Efficiency: Their use significantly reduces the reliance on heavy truck haulage, thereby lowering operational costs, reducing emissions, and enhancing safety within mines.
Manufacturing
- Assembly Lines: In the manufacturing sector, belt conveyors serve as the backbone of assembly lines, moving parts and products through various stages of production and assembly with precision and efficiency.
- Versatility: They handle a wide range of materials, from small electronic components to large automotive parts, accommodating different weights and sizes with adjustable speeds and capacities.
Agriculture and Food Processing
- Crop Handling: Belt conveyors play a crucial role in agriculture, used for the handling and processing of crops, from gentle handling of delicate fruits to the transport of grains and vegetables.
- Hygiene and Speed: In food processing, conveyors are designed to meet hygiene standards, facilitating the quick and efficient movement of food products through cleaning, processing, and packaging stages.
Logistics and Warehousing
- Sorting and Distribution: In the logistics industry, belt conveyors are integral to sorting systems, efficiently moving packages and goods for distribution. They optimize the flow of items in warehouses and distribution centers, enhancing order fulfillment processes.
- Adaptability: The adaptability of belt conveyors to different layouts and their ability to transport a variety of package sizes and weights make them indispensable in modern logistics operations.
Airports
- Baggage Handling: Belt conveyors are essential for the smooth operation of airport baggage handling systems, transporting luggage between check-in, sorting areas, and aircraft, as well as facilitating baggage claim processes.
- Reliability and Safety: Their reliability and ability to handle high volumes of luggage safely and efficiently are crucial for maintaining flight schedules and passenger satisfaction.
Recycling and Waste Management
- Material Sorting and Handling: In recycling plants, belt conveyors are used to transport and sort various types of waste materials, contributing to efficient recycling processes.
- Durability: These conveyors are often designed to withstand harsh conditions, including the handling of abrasive, heavy, or potentially damaging materials.
Construction
- Material Movement: Belt conveyors are used on construction sites to move materials over difficult terrain and to locations that are not easily accessible by other means, such as high-rise buildings.
- Cost-Effectiveness: They provide a cost-effective solution for transporting large volumes of materials like dirt, rubble, and cement, reducing the need for manual labor.
Experience top performance with our premium belt conveyors! Contact us now!
Challenges and Innovations
While belt conveyors are widely used across industries, their application is not without challenges, including maintenance requirements, energy consumption, and environmental impact. However, ongoing innovations in conveyor technology, such as the development of more durable materials, energy-efficient motors, and advanced control systems, continue to enhance their efficiency, sustainability, and application scope.
The application status of belt conveyors across diverse industries underscores their importance in modern industrial operations, offering a combination of efficiency, versatility, and reliability that is hard to match with other material handling solutions.

Existing Problems of Belt Conveyors
Despite the widespread use of belt conveyors in various industries, there are specific applications where the disadvantages of conveyor belt systems become apparent, making them less than ideal for certain tasks. Here, we explore seven detailed examples of such applications, highlighting why belt conveyors may not be the best choice and suggesting alternative conveying solutions.
- High-Temperature Materials Handling: Belt conveyors are not suited for transporting materials at high temperatures, as the heat can damage the conveyor belt. Alternative: Slag and foundry operations can benefit from using steel apron conveyors, which can withstand extreme temperatures.
- Sharp or Jagged Material Transport: The risk of puncturing or tearing the conveyor belt with sharp or jagged materials is a significant disadvantage. Alternative: Vibratory conveyors or steel apron conveyors are better suited for handling such materials without the risk of damage.
- Sticky or Wet Material Conveyance: Sticky or wet materials can adhere to the belt, causing cleaning and maintenance challenges. Alternative: Screw conveyors are effective in moving these types of materials while minimizing cleanup efforts.
- Abrasive Material Handling: The wear and tear on belt conveyors from abrasive materials can lead to frequent belt replacements. Alternative: Drag chain conveyors are more durable and resistant to abrasive materials, reducing maintenance needs.
- Vertical or High-Incline Transport: Belt conveyors have limitations in vertical or steep incline applications due to slippage and material rollback. Alternative: Bucket elevators or vertical screw conveyors offer efficient solutions for vertical transport without these drawbacks.
- Heavy-Duty Material Transportation: The structural limitations of belt conveyors can be a disadvantage when transporting very heavy loads. Alternative: Chain conveyors, with their robust design, are better equipped to handle heavy-duty applications.
- Chemically Reactive Material Handling: Materials that can react chemically with the rubber or plastic components of a belt conveyor pose a risk of degradation. Alternative: Stainless steel screw conveyors or pneumatic conveying systems, which can be made from materials resistant to chemical reactions, offer a safer alternative.
In each of these scenarios, the disadvantages of belt conveyor systems—ranging from material incompatibility and maintenance challenges to efficiency limitations in specific conditions—underscore the importance of selecting the right type of conveyor. By considering the specific needs of the application and the materials to be handled, businesses can choose conveying solutions that not only avoid the pitfalls associated with belt conveyors but also enhance operational efficiency, safety, and reliability.

FAQs about Disadvantages of Belt Conveyor
Belt conveyors are among the most efficient and versatile systems for transporting materials across various distances and terrains. Their advantages are numerous, making them a preferred choice in a wide range of industries. Firstly, belt conveyors offer significant cost efficiency, both in terms of initial investment and operational costs. They are designed to handle large volumes of materials, which can significantly reduce labor costs and enhance productivity. Additionally, belt conveyors are highly adaptable; they can be customized to transport different types of materials, including those that are fragile or sensitive to damage.
The operational flexibility of belt conveyors is another major advantage. They can be installed in almost any type of environment, whether indoor or outdoor, and can be designed to fit specific space constraints, including curved, inclined, or straight paths. This adaptability extends to their capability to transport materials over long distances, seamlessly integrating with existing production or warehousing setups.
Safety and reliability are also key benefits of using belt conveyors. They provide a stable and continuous flow of materials, minimizing the risk of accidents and ensuring consistent productivity. Moreover, belt conveyors are known for their low maintenance requirements. Designed with durability in mind, they can operate under harsh conditions with minimal downtime, ensuring a long service life and a high return on investment.
Conveyor accumulators, designed to collect and store materials temporarily during production processes, come with certain disadvantages. One of the primary concerns is the complexity of integrating accumulators into existing conveyor systems. This can require significant modifications, leading to increased costs and potential disruptions in production. Additionally, accumulators can become points of congestion, especially in high-volume operations, where the continuous flow of materials is critical. This can lead to bottlenecks, affecting overall efficiency and productivity.
Maintenance and operational challenges also pose significant disadvantages. Accumulators require regular maintenance to ensure optimal performance, which can increase operational costs. The risk of material damage or loss is another concern, particularly for sensitive or fragile materials that may not withstand the accumulation process without degradation.
Space constraints are another issue, as accumulators can occupy a considerable amount of floor space. This can be a significant drawback in facilities where space is limited. Moreover, the complexity of managing the infeed and outfeed of materials from accumulators can require sophisticated control systems, adding to the overall cost and complexity of the conveyor system.
Vertical conveyors, while efficient for transporting materials between different levels, have specific disadvantages. One of the main drawbacks is the limitation on the types of materials they can handle effectively. Certain materials may not be suitable for vertical conveyance due to their weight, size, or shape, limiting the applicability of vertical conveyors in diverse industrial settings.
Installation and operational costs are also higher for vertical conveyors compared to other types of conveying systems. The need for specialized equipment, structural modifications, and safety measures can significantly increase the initial investment. Additionally, vertical conveyors often require more maintenance due to the complexity of their design and the stress placed on components by vertical movement, leading to higher long-term operational costs.
Space requirements can also be a disadvantage, as vertical conveyors may require significant vertical clearance, which may not be available in all facilities. Furthermore, the efficiency of vertical conveyors can be affected by the speed of operation, which is generally lower compared to horizontal systems, potentially impacting overall productivity.
Conveyor belts offer substantial advantages in mining operations, providing a highly efficient, cost-effective, and safe method for transporting materials from the mining site to processing facilities or storage areas. One of the primary advantages is the ability to move large volumes of material over long distances continuously, which significantly reduces the need for truck haulage, lowering fuel costs and emissions, and minimizing the environmental impact.
The safety of operations is greatly enhanced by using conveyor belts, as they reduce the need for manual handling of materials, thereby decreasing the risk of accidents and injuries. Conveyor belts also contribute to increased productivity, as they can operate continuously, 24/7, without the need for breaks or shifts changes, ensuring a steady flow of materials.
Moreover, conveyor belts in mining are designed to withstand harsh conditions, including abrasive materials, heavy loads, and extreme weather, ensuring reliability and durability. They can be customized with features such as covers to protect materials from environmental factors, further enhancing operational efficiency. The adaptability of conveyor belts to various terrains and their ability to be installed at different angles provide additional flexibility in mine planning and operations, making them an indispensable tool in modern mining.
Advantages of Using an Electric Motor for a Conveyor Belt:
Energy Efficiency: Electric motors are highly efficient, converting a large portion of electrical energy into mechanical energy. This efficiency can lead to reduced operational costs over time.
Control and Precision: Electric motors provide precise control over the speed and torque of the conveyor belt, allowing for smooth operation and the ability to adjust the conveyor’s performance based on the specific needs of the material being transported.
Low Maintenance: Compared to other types of power sources, electric motors generally require less maintenance. They have fewer moving parts, which reduces the likelihood of mechanical failure and extends the lifespan of the conveyor system.
Environmental Friendliness: Electric motors produce no direct emissions, making them a cleaner option that can help reduce the environmental footprint of industrial operations.
Quiet Operation: Operating more quietly than combustion engines, electric motors can help to lower noise pollution in the workplace, contributing to a better working environment.
Easy Integration: They can be easily integrated into existing systems and are compatible with a wide range of industrial applications, making them a versatile choice for conveyor belt operations.
Disadvantages of Using an Electric Motor for a Conveyor Belt:
Initial Cost: The upfront cost of electric motor systems can be higher than other types, especially when considering the need for electrical infrastructure and control systems to manage the motor.
Dependence on Electricity: Electric motors rely on a continuous supply of electricity. Power outages or fluctuations in the power supply can disrupt conveyor belt operations, leading to potential downtime and productivity losses.
Complexity in Installation and Repair: Setting up an electric motor-driven conveyor system can be complex, requiring specialized knowledge for installation, calibration, and repair. This complexity might increase the time and cost involved in maintenance and troubleshooting.
Overheating Risks: Electric motors can overheat if overworked or if not properly sized for the application, potentially leading to motor damage or failure and posing safety risks.
Limited by Electrical Infrastructure: In areas with limited or unreliable electrical infrastructure, using an electric motor might not be feasible, limiting the applicability of conveyor systems in remote or undeveloped regions.
Electromagnetic Interference (EMI): Electric motors can generate EMI, which could interfere with nearby electronic equipment, necessitating careful planning and shielding in sensitive environments.
Last Updated on June 5, 2024 by Jordan Smith
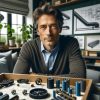
Jordan Smith, a seasoned professional with over 20 years of experience in the conveyor system industry. Jordan’s expertise lies in providing comprehensive solutions for conveyor rollers, belts, and accessories, catering to a wide range of industrial needs. From initial design and configuration to installation and meticulous troubleshooting, Jordan is adept at handling all aspects of conveyor system management. Whether you’re looking to upgrade your production line with efficient conveyor belts, require custom conveyor rollers for specific operations, or need expert advice on selecting the right conveyor accessories for your facility, Jordan is your reliable consultant. For any inquiries or assistance with conveyor system optimization, Jordan is available to share his wealth of knowledge and experience. Feel free to reach out at any time for professional guidance on all matters related to conveyor rollers, belts, and accessories.