Safety Risks Disadvantages of Belt Conveyor System
Conveyor systems are integral to modern industrial applications, facilitating the efficient movement of materials across various sectors, from manufacturing to distribution. As prevalent as these systems are, belt conveyors particularly stand out due to their versatility and widespread use. However, this blog post aims to shed light on the disadvantages of belt conveyor systems, providing a balanced perspective against the commonly noted advantages. By focusing on these disadvantages, we aim to offer valuable insights for businesses evaluating conveyor solutions, ensuring they are aware of potential challenges that could impact their operations. This discussion is crucial for informed decision-making in the deployment and use of belt conveyor systems in any industry.
Dissecting the Disadvantages of Belt Conveyor Systems
Disadvantages of belt conveyor system are costly to contain, hard to clean, lack agility for changing needs, and are non-portable.
Belt conveyors are fundamental components in countless industrial scenarios, defined by their continuous, flat or troughed belts driven by pulleys and powered by motors. These systems operate on a simple principle: a belt made from various materials, like rubber or synthetic fabrics, moves over rollers positioned at either end of the system to transport goods from one point to another. This movement can be continuous or controlled at varying speeds, which makes belt conveyors highly adaptable to different operational requirements.
The versatility of belt conveyors allows them to be used across a wide range of industries. In manufacturing, they are essential for assembly lines, moving components through different stages of production. The mining industry relies on them to transport raw extracted materials over long distances, often from deep underground to surface level. Agriculture uses belt conveyors to handle grains and other bulk materials, reducing labor costs and increasing efficiency. Even the food industry employs these conveyors for the careful and hygienic transport of food products. Despite their widespread advantages and applications, it’s also critical to discuss the disadvantages of belt conveyor system to give a complete picture of their functionality and limitations in various industrial contexts.
Advantages of Belt Conveyor Systems
While exploring the disadvantages of belt conveyor system is crucial for a balanced understanding, it’s equally important to acknowledge the significant advantages that make belt conveyors a preferred choice in many industries. Here’s a closer look at some of the key benefits:
Cost-effectiveness for Long Distances
One of the most significant advantages of belt conveyors is their ability to transport materials over long distances at a relatively low cost. Unlike trucks or rail, conveyors do not require frequent starts and stops, which conserves energy and reduces wear and tear. This makes them an economically viable option for moving large quantities of materials across expansive industrial facilities or between processing stages.
Minimal Product Degradation
Belt conveyors are designed to handle materials gently, reducing the chances of material degradation during transport. This is particularly beneficial in industries such as food processing or pharmaceuticals, where maintaining the integrity of the product is crucial. The smooth and steady movement of the conveyor belt ensures that products arrive at their destination in the same condition as they were loaded.
Flexibility in Elevation Changes and Loading Points
Belt conveyors can be designed to accommodate changes in elevation, allowing them to ascend or descend between different levels within a facility. This flexibility is enhanced by the ability to incorporate multiple loading and unloading points along the conveyor’s path. This adaptability makes belt conveyors ideal for complex industrial landscapes where materials need to be moved efficiently over varying heights and distances.
Optimize your operations with high-quality conveyor belts. Inquire today!
Comprehensive Look at the Disadvantages of Belt Conveyor Systems
Despite the many advantages, there are significant disadvantages of belt conveyor system that need careful consideration when deciding on a conveyor solution for industrial applications. Here’s an in-depth look at some of the key drawbacks:
Maintenance Requirements
- Frequent Inspections and Repairs: Belt conveyors require regular inspections to ensure they are functioning correctly. This includes checking for wear and tear, misalignment, and other issues that can lead to system failures.
- Component Replacement: The belts and other components like pulleys and rollers often need replacement due to wear, especially in harsh operating conditions.
Material Spillage and Dust
- Spillage: Materials can spill over the sides of the belt, leading to loss of material and potential safety hazards.
- Dust Generation: Dust can be a significant issue, especially when handling fine or powdery materials. This not only creates a health hazard for workers but also requires additional cleanup and maintenance.
Limited Flexibility
- Fixed Path: Belt conveyors are typically designed for a fixed path, making it difficult to change the layout or adapt to new production requirements without significant modifications.
- Limited Incline Capability: Belt conveyors are not suitable for steep inclines. When transporting materials up or down slopes, the angle is generally limited to prevent material rollback or slippage.
Space Requirements
- Large Footprint: Belt conveyor systems can take up a considerable amount of space, which can be a disadvantage in facilities with limited floor space.
Energy Consumption
- High Power Usage: Operating belt conveyors, especially over long distances or with heavy loads, can result in significant energy consumption, leading to higher operational costs.
Initial Installation Costs
- Capital Investment: The initial cost of purchasing and installing a belt conveyor system can be high, which may be a barrier for some businesses.
Potential for Belt Slippage
- Loss of Efficiency: Under certain conditions, such as when handling wet or oily materials, there is a risk of belt slippage, which can reduce efficiency and increase the likelihood of damage to the conveyor system.
Safety Concerns
- Risk of Injuries: Belt conveyors can pose a risk of injuries to workers, especially if proper safety protocols are not followed. Moving parts can cause accidents if workers’ clothing or limbs get caught.
Open Design Limitations
Belt conveyors typically feature an open design that, while facilitating easy access and monitoring of the material in transit, also poses challenges in containing the products. This openness can lead to material losses during transport, especially in windy or outdoor conditions, and may expose materials to environmental contaminants. Covering the conveyor to mitigate these issues can be costly and complex, adding to the overhead.
Cleaning Challenges
Maintaining the cleanliness of belt conveyors can be particularly challenging. The nature of the conveyor belt surfaces makes them prone to accumulating dirt and debris, and they can be difficult to clean, especially when dealing with sticky or finely granulated materials. This not only leads to downtime but also increases maintenance costs as more resources are needed to ensure cleanliness and prevent contamination of conveyed products.
Material Carryover
Another disadvantage of belt conveyor system is the issue of material carryover. Materials can stick to the conveyor belt and get carried over to the return side of the system. This not only wastes materials but also can lead to damage and increased wear on the conveyor’s rolls, idlers, and pulleys. Such issues necessitate frequent cleaning and can cause significant operational disruptions.
Maintenance and Operational Challenges
Belt conveyors require regular maintenance to ensure they operate efficiently. One common issue is the need for ongoing alignment and tracking of the conveyor belt, which if not properly maintained, can lead to uneven wear, belt slippage, and reduced operational efficiency. Additionally, managing odors can be particularly challenging in industries such as food processing or chemicals, where odors from products can become trapped in the conveyor system and are difficult to eliminate.
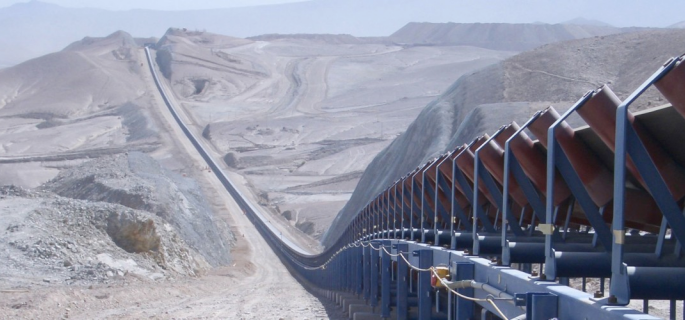
Disadvantages of Belt Conveyor Systems in Comparison with Other Conveying Methods
While examining the disadvantages of belt conveyor system, it’s useful to compare belt conveyors with other types of conveyor systems to better understand their relative pros and cons. Below is a detailed comparison outlined in a table format, highlighting how belt conveyors stack up against chain conveyors, screw conveyors, and bucket conveyors:
The Difference Between Belts Conveyor and Chain Conveyors
Conveyor belts and chain conveyors are both widely used in material handling, but they have distinct differences in design, functionality, and applications. Here are the key differences between the two:
Design and Structure
Conveyor Belts:
- Material: Made of continuous looped materials such as rubber, PVC, fabric, or metal.
- Surface: A flat, smooth surface that transports materials.
- Drive Mechanism: Typically driven by a motorized pulley system.
- Support: Supported by rollers or a flat slider bed.
Chain Conveyors:
- Material: Constructed from chains made of metal or plastic links.
- Surface: Consists of linked chains that form a moving track.
- Drive Mechanism: Powered by a series of sprockets driven by a motor.
- Support: Supported by a series of rollers or a framework that guides the chains.
Functionality
Conveyor Belts:
- Load Capacity: Suitable for transporting lighter to moderate loads.
- Speed: Typically operates at higher speeds.
- Material Handling: Ideal for bulk materials and items with flat bottoms.
- Incline: Limited incline capability due to potential material slippage.
Chain Conveyors:
- Load Capacity: Designed to handle heavier loads and harsh environments.
- Speed: Generally operates at slower speeds due to the nature of heavy-duty applications.
- Material Handling: Suitable for irregularly shaped items, pallets, or heavy containers.
- Incline: Can handle steeper inclines and declines, as the chains provide better grip.
Applications
Conveyor Belts:
- Industries: Commonly used in food processing, packaging, mining, and manufacturing.
- Products: Efficient for transporting fine, small, or lightweight products such as grains, sand, and small parts.
Chain Conveyors:
- Industries: Widely used in automotive, heavy manufacturing, warehousing, and material handling.
- Products: Ideal for moving heavy items like automotive components, pallets, and large containers.
Maintenance and Durability
Conveyor Belts:
- Wear and Tear: Subject to wear, requiring regular inspections and potential replacements.
- Maintenance: Requires maintenance of the belt, rollers, and pulleys.
- Durability: Generally less durable under heavy load and abrasive conditions.
Chain Conveyors:
- Wear and Tear: More robust and durable, designed for heavy-duty applications.
- Maintenance: Requires maintenance of chains, sprockets, and support structures.
- Durability: Highly durable and capable of withstanding harsh conditions and heavy loads.
Cost
Conveyor Belts:
- Initial Cost: Typically lower initial cost compared to chain conveyors.
- Operational Cost: Potentially higher operational costs due to regular maintenance and part replacements.
Chain Conveyors:
- Initial Cost: Higher initial cost due to robust construction and materials.
- Operational Cost: Lower operational costs over time, as they are designed for durability and less frequent maintenance.
Conveyor belts are ideal for lighter, faster material handling tasks with smooth surfaces, while chain conveyors excel in handling heavy, irregularly shaped items in demanding environments. The choice between the two depends on the specific requirements of the application, including load capacity, speed, material type, and operating conditions.
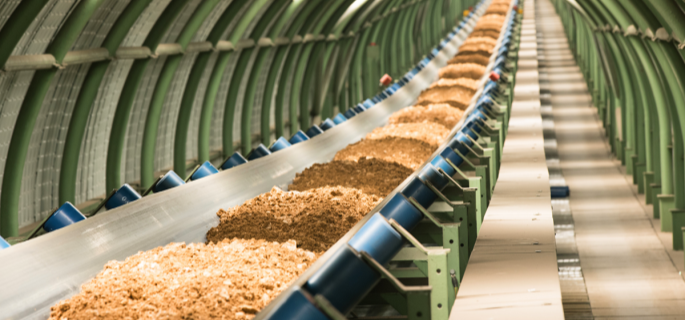
Seeking Alternatives of Disadvantages of Belt Conveyor Systems
In light of the disadvantages of belt conveyor system, it is important for industries to consider alternative conveying solutions that might better meet specific operational needs. Here we explore some of the key alternatives to belt conveyors, each offering unique benefits for different types of material handling:
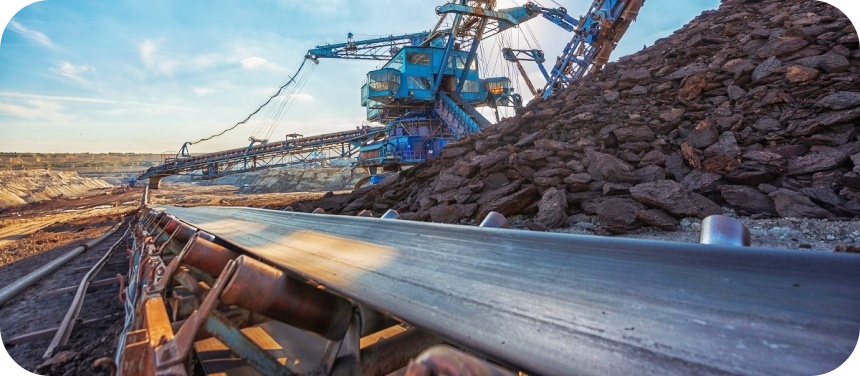
Aerial Conveyors
Aerial conveyors, also known as overhead conveyors, provide a solution that utilizes space above the work areas, avoiding interference with ground-level operations. These systems are particularly useful in facilities where floor space is a premium. They are ideal for transporting goods across large facilities, often seen in automotive and manufacturing environments. Overhead conveyors can significantly reduce floor congestion and are highly effective in environments requiring a clean floor policy.
Roller Conveyors
Roller conveyors are suitable for simpler, gravity-based transport of items, primarily used where items are solid and have a rigid base. This type of conveyor is less expensive to install and maintain compared to belt conveyors and uses gravity (if inclined) or manual force to move items along rollers. They are highly effective in distribution centers, packaging lines, and assembly areas where items can be easily moved over short distances without the need for powered assistance.
Pneumatic and Vacuum Conveyors
For handling light, dry materials over short distances, pneumatic and vacuum conveyors offer a completely enclosed system, which prevents any contamination of the materials during transport. These systems are particularly advantageous in industries such as pharmaceuticals, food processing, and chemical manufacturing, where maintaining the purity of materials is critical. Pneumatic conveyors use air pressure to transport materials through tubes, making them suitable for fine or granular materials like powders and grains.
FAQS About Disadvantages Of Belt Conveyor System
1. Noise Levels: Drag chain conveyors can be quite noisy due to the metal-on-metal contact, which may not be suitable for all work environments.
2. Maintenance Requirements: They typically require more maintenance than other types of conveyors because the chains need regular lubrication and tension adjustments to avoid wear and tear.
3. Material Suitability: Drag chains are not suitable for all types of materials; they are best used with large, non-fragile materials as smaller or delicate items may suffer damage or degradation during transport.
4. Cost and Energy Consumption: The initial installation cost can be higher compared to other conveyor systems, and they consume a significant amount of energy, especially when transporting heavy loads over long distances.
1. Safety Concerns: Major safety risks include injuries from entanglements, pinches, and crush points, particularly when safety guards are not properly installed or maintained.
2. Electrical and Fire Hazards: Electrical hazards and fire risks due to the accumulation of dust and debris around the conveyor’s mechanical parts.
3. Operational Risks: Risk of breakdowns which can disrupt production schedules and lead to costly downtime. Material spillage and wear and tear of mechanical parts also pose efficiency and longevity risks.
1. Material Limitations: Belt dryers have limitations in the variety of materials that can be processed, especially those that are heat sensitive or require lower temperatures.
2. Uneven Drying: There is potential for uneven drying as the material’s exposure to the heat source can vary depending on its position on the belt.
3. Space Requirements: Belt dryers typically require a large footprint in industrial settings, which may not be feasible for all facilities.
4. Operational Costs: High operational costs including energy consumption and maintenance, as continuous monitoring and adjustments may be necessary to ensure optimal drying conditions.
1. Efficiency and Versatility: Belt conveyors are highly efficient for transporting a wide range of materials over both short and long distances. They can handle large volumes of materials at a fast pace.
2. Customization and Control: Capable of controlled speeds and can be customized with different belt types and configurations to suit specific needs and applications.
3. Safety Features: Generally safer than other types of conveyors due to fewer moving external parts and the availability of safety guards and emergency stops.
4. Cost-Effectiveness: Lower maintenance and operational costs compared to other mechanical conveying systems.
Last Updated on July 12, 2024 by Jordan Smith
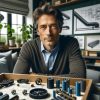
Jordan Smith, a seasoned professional with over 20 years of experience in the conveyor system industry. Jordan’s expertise lies in providing comprehensive solutions for conveyor rollers, belts, and accessories, catering to a wide range of industrial needs. From initial design and configuration to installation and meticulous troubleshooting, Jordan is adept at handling all aspects of conveyor system management. Whether you’re looking to upgrade your production line with efficient conveyor belts, require custom conveyor rollers for specific operations, or need expert advice on selecting the right conveyor accessories for your facility, Jordan is your reliable consultant. For any inquiries or assistance with conveyor system optimization, Jordan is available to share his wealth of knowledge and experience. Feel free to reach out at any time for professional guidance on all matters related to conveyor rollers, belts, and accessories.