DIY Conveyor Belt Material: 7 Steps to Build Your Own
In recent years, the trend of constructing DIY conveyor belts has surged, particularly for home improvement and educational projects. Enthusiasts and students alike are embracing the challenge to create functional conveyor systems tailored to their specific needs. The appeal of using DIY conveyor belt material lies in its flexibility and adaptability, allowing for a high degree of customization. Whether it’s simplifying chores at home or facilitating learning in a classroom, building your own conveyor belt offers significant cost savings and the satisfaction of personal achievement. These projects not only enhance practical skills but also ignite creativity and innovation in problem-solving.
Types of DIY Conveyor Belt Materials
The variety of DIY conveyor belt materials available allows enthusiasts to tackle projects tailored to specific needs and environments. From moving garden dirt to managing small conveyor roller manufacturing processes at home, each type of DIY conveyor belt material offers unique benefits and challenges.
DIY Conveyor Belt for Dirt
For those needing to transport dirt or other heavy materials, selecting the right DIY conveyor belt material is crucial. Durable materials such as reinforced rubber belt or heavy-duty PVC can withstand the rigors of moving abrasive substances. The construction often involves a robust frame, possibly from metal or thick plastic, with a conveyor belt system designed to endure frequent use and outdoor conditions.
DIY Conveyor Belt from PVC
PVC is a popular choice for DIY conveyor belt material due to its affordability and versatility. A step-by-step guide to using PVC involves measuring and cutting the plastic to size, securing it around rollers, and installing a motor or manual crank. This type of conveyor belt is ideal for light to medium loads and can be easily customized to fit various lengths and widths.
DIY Conveyor Belt Kit
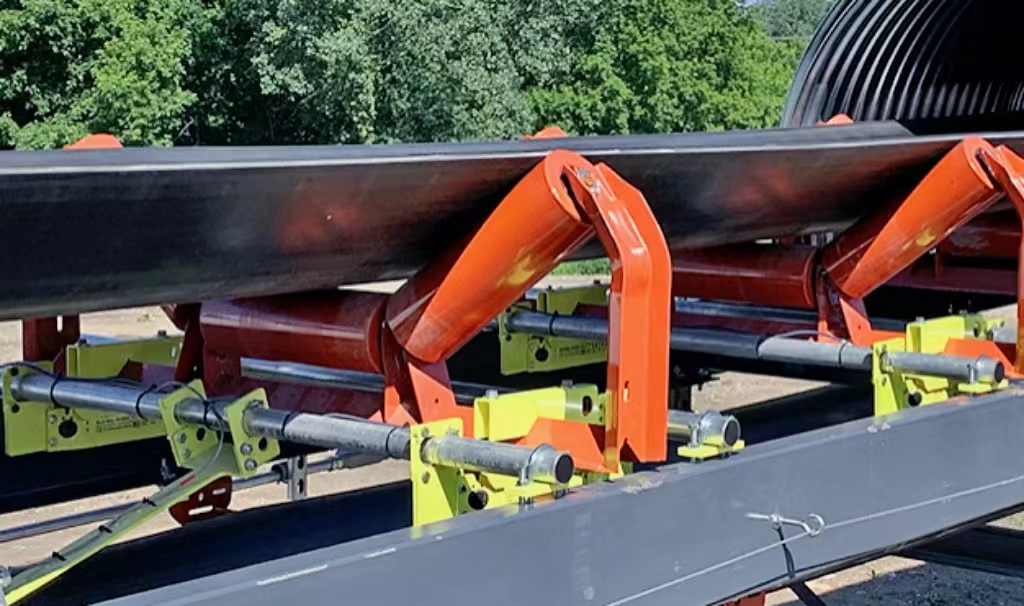
A DIY conveyor belt kit typically includes pre-cut materials, assembly instructions, and sometimes tools required for building. These kits simplify the construction process, making it accessible even to beginners. Kits vary in complexity and size, designed for different tasks—from simple educational models to more robust systems capable of handling heavier loads.
DIY Hand Crank Conveyor Belt
For educational purposes or light applications, a DIY hand crank conveyor belt is a great project. This manual system does not require electricity, making it safe and suitable for classroom settings. The construction involves attaching a belt to rollers that are turned by a hand crank, demonstrating basic mechanical principles and introducing students to practical engineering skills.
Each type of DIY conveyor belt material is designed to meet specific project requirements, providing a rewarding and practical experience in designing and building functional systems.
Planning Your DIY Conveyor Belt
DIY Conveyor Belt Material Plans
Planning your DIY conveyor belt is a crucial step in ensuring the success of your project. With careful consideration and preparation, you can create a functional and efficient conveyor system tailored to your specific needs. This section provides a comprehensive guide to planning your conveyor belt project, focusing on determining specifications, designing the layout, and compiling a materials list.
Determine Specifications
The first step in planning your DIY conveyor belt is to determine the key specifications, including the length, width, and load capacity of the belt. These factors will influence the choice of materials, the design of the frame, and the type of motor you will need.
- Length: Measure the distance over which the conveyor belt will need to transport materials. Consider any turns or inclines the belt may need to navigate. Longer conveyors may require additional support and stronger motors.
- Width: The width of the conveyor belt should be sufficient to accommodate the items you plan to transport. Common widths for DIY conveyor belts range from 100mm to 600mm, but you can customize the width based on your specific requirements.
- Load Capacity: Determine the maximum weight the conveyor belt will need to carry. This includes the weight of the materials being transported as well as any additional weight from equipment or components placed on the belt. Ensure that the frame, belt material, and motor are capable of handling this load without excessive strain.
Design Layout
Once you have determined the specifications, the next step is to design the layout of your conveyor system. A well-thought-out design will ensure that your conveyor belt operates smoothly and efficiently.
- Sketch the Design: Begin by sketching a rough design of your conveyor system. Include all key components, such as the frame, rollers, motor, and belt. Indicate the dimensions of each part and their relative positions. This will help you visualize the final product and identify any potential issues before you begin construction.
- Frame Design: The frame of your conveyor belt should be sturdy and stable, capable of supporting the weight of the belt and the materials being transported. Common materials for the frame include steel, aluminum, and wood. Steel is highly durable and ideal for heavy-duty applications, while aluminum is lightweight and resistant to corrosion. Wood can be used for smaller, less demanding projects.
- Rollers and Pulleys: The rollers and pulleys are critical components that support and drive the conveyor belt. Ensure that the rollers are spaced evenly along the length of the frame to provide adequate support for the belt. The drive pulley, connected to the motor, should have a high friction surface to prevent slippage.
- Motor and Drive System: Choose a motor that provides sufficient power to move the conveyor belt and its load. The motor should be compatible with the drive pulley and capable of operating at the desired speed. Consider using a variable speed motor controller to adjust the speed of the conveyor as needed.
Materials List
With the specifications and design layout in hand, compile a comprehensive list of the materials and tools you will need to construct your DIY conveyor belt. This list will ensure that you have all the necessary components on hand before you begin the build.
- DIY Conveyor Belt Material: Choose the appropriate material for the belt itself. Common options include PVC, rubber, and fabric. PVC is a popular choice due to its durability and smooth surface, making it ideal for transporting various materials. Rubber belts are also durable and offer good traction, while fabric belts are flexible and lightweight.
- Frame Materials: Depending on your design, you may need steel bars, aluminum extrusions, or wooden planks. Ensure that the materials are of the appropriate size and strength to support your conveyor belt.
- Rollers and Bearings: Purchase rollers with appropriate diameters and lengths to fit your frame design. Bearings are essential for smooth roller operation and should be chosen based on the roller specifications.
- Motor and Controller: Select a motor with the necessary power rating and a compatible controller. Ensure that the motor mounting hardware is included.
- Fasteners and Hardware: Gather all necessary nuts, bolts, screws, and other fasteners needed to assemble the frame, attach the rollers, and secure the motor.
- Tools: Ensure you have the required tools for construction, such as a drill, saw, wrenches, screwdrivers, and measuring tape. Specialty tools, such as a PVC cutter or metal saw, may also be needed depending on the materials you are using.
By carefully planning your DIY conveyor belt project and gathering all necessary materials and tools, you can ensure a smooth construction process and a successful outcome. Whether you are building a conveyor for a workshop, garden, or educational project, following these steps will help you create a reliable and efficient conveyor system using DIY conveyor belt material.
Steps to Make a Manual Conveyor Belt
Creating a manually operated conveyor belt can be a rewarding DIY project that combines mechanical engineering with practical application. Below, you’ll find a detailed guide focusing on the necessary materials and components. By choosing the right DIY conveyor belt materials, you can ensure both functionality and durability.
DIY Conveyor Belt Materials and Components
- Frame Material: The structure of your conveyor belt needs to be sturdy. Aluminum profiles or steel channels are recommended for their strength and ease of assembly.
- Belt Material: For the belt itself, durability and flexibility are key. Rubber, leather, or PVC are excellent choices. Consider the items you plan to transport on the belt to choose the appropriate material.
- Pulleys: These are needed at both ends of your conveyor belt to guide and drive the belt. They should be made of a durable material like steel or heavy-duty plastic.
- Bearings: Bearings help reduce friction and wear at the points where the pulleys meet the frame. Quality ball bearings are essential for smooth operation.
- Motor (Optional for Manual Operation): If you want to add a motor later, a small electric motor can be used. For a fully manual system, you can exclude this or use a hand crank.
- Shaft: The shaft connects to the pulleys and can be turned manually or by a motor. A metal rod or a sturdy wooden dowel can work depending on the load.
- Drive Belt or Chain: This component is necessary if you are using a motor. A rubber belt or a metal chain can transfer power from the motor to the pulleys.
- Support Structure: This includes legs or a frame to hold your conveyor at the desired height. Materials like metal tubes or wooden beams can be used.
- Rollers: Rollers support the conveyor belt and help it to move smoothly. They can be made from metal or plastic and are spaced evenly along the length of the belt.
- Fasteners and Connectors: Bolts, nuts, and metal brackets are necessary to assemble and secure all parts of your conveyor belt system. Ensure they are compatible with the materials you have chosen.
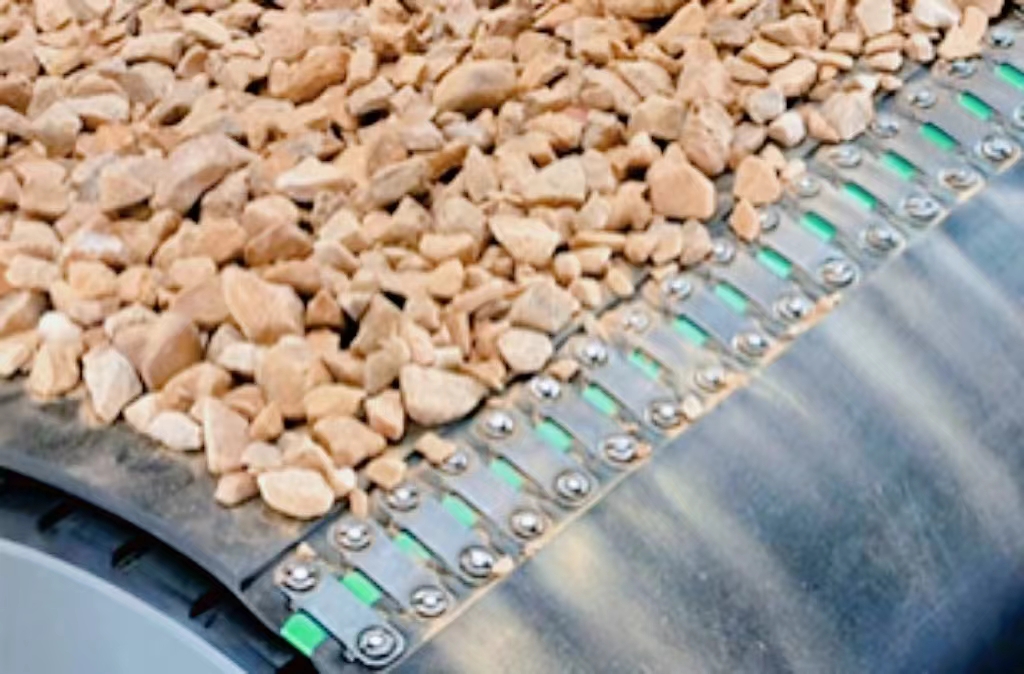
Assembly Tips
- Planning: Before assembling your DIY conveyor belt, plan the layout and dimensions based on the space and usage requirements.
- Safety: When cutting and assembling the materials, use appropriate safety gear like gloves, goggles, and ear protection.
- Testing: After assembly, test the conveyor with light loads to ensure everything is functioning smoothly before full usage.
By carefully selecting your DIY conveyor belt materials and meticulously assembling the components, you can build a robust manual conveyor belt suited for various tasks. This project not only provides a practical tool but also enhances your mechanical skills and understanding.
Building a Conveyor Belt with Cardboard Using DIY Conveyor Belt Material
Constructing a conveyor belt using cardboard can be a fun and educational project, especially for students and hobbyists looking to explore basic engineering concepts. This tutorial will guide you through the process of building a simple yet functional conveyor belt, focusing on using cardboard as the primary DIY conveyor belt material, which is ideal for light applications and school projects.
Materials and Tools
- Cardboard: Thick cardboard sheets will form the main structure of the conveyor belt. Ensure the cardboard is sturdy enough to hold the shape and bear light objects.
- Rubber Bands: These will serve as the conveyor belt itself, providing grip and flexibility. Choose wide, flat rubber conveyor belt bands for best results.
- Glue and Tape: Strong adhesive glue and duct tape will be needed to assemble and reinforce the cardboard parts.
- Pulleys: You can use cardboard tubes or spools (from thread or tape) as pulleys at each end of the conveyor belt.
- Skewers or Dowels: These will act as the axles for the pulleys, allowing them to rotate freely. Wooden skewers or small dowels work well for this purpose.
- Ruler, Pencil, and Scissors: For measuring, marking, and cutting the cardboard.
Steps to Assemble Your Cardboard Conveyor Belt
- Cut the Cardboard: Begin by cutting two long strips of cardboard for the base of the conveyor belt, and two smaller pieces to serve as supports for the pulleys.
- Assemble the Frame: Glue the support pieces perpendicularly to the base strips at each end. Reinforce these joints with tape for additional stability.
- Prepare the Pulleys: If using spools, ensure they are wide enough to stretch the rubber bands across. If using cardboard tubes, cut them to the appropriate width.
- Install the Axles: Pierce holes through the supports and insert the skewers or dowels. Place your pulleys (spools or tubes) on these axles.
- Attach the Conveyor Belt: Stretch rubber bands around the pulleys to form the moving conveyor belt. Ensure the bands are taut but not overly stretched to avoid snapping.
- Reinforce the Structure: Use extra cardboard and tape to reinforce any weak areas, ensuring the structure can hold small objects without bending.
- Test and Adjust: Place a lightweight object on the conveyor belt and manually rotate the pulleys to test the movement. Adjust the tightness and alignment of the rubber bands as necessary.
Additional Tips
- Decoration and Customization: Feel free to decorate the conveyor belt with paint, stickers, or markers to make the project more engaging.
- Enhancements: To increase the conveyor belt’s capabilities, consider adding side rails made of cardboard to prevent objects from falling off.
- Understanding Mechanisms: Use this project to discuss and explore simple machine concepts, such as pulleys and levers, with students or participants.
This project demonstrates how everyday materials like cardboard and rubber bands can be transformed into a functional machine, highlighting the versatility of DIY conveyor belt materials in educational and light-duty applications.
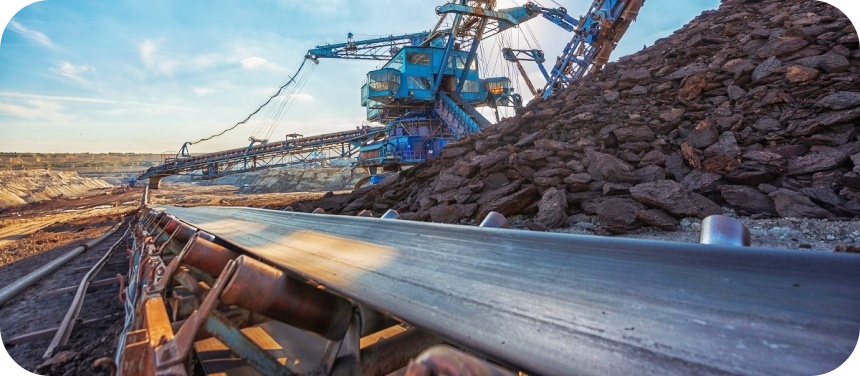
DIY Conveyor Belt Project for Students Using DIY Conveyor Belt Material
Engaging students in a hands-on project where they build a small conveyor belt can be a highly effective way to teach principles of engineering, physics, and material science. This guide outlines a project plan using DIY conveyor belt material, providing clear objectives, a list of required materials, and expected learning outcomes.
Project Objectives
- Understand Basic Mechanics: Students will learn how different components like pulleys, belts, and motors work together to create movement.
- Apply Engineering Principles: The project focuses on the design and assembly process, encouraging students to think critically about how to construct the conveyor belt efficiently.
- Develop Problem-Solving Skills: Students will identify and solve problems that arise during the construction process, such as alignment and tension issues.
Required Materials
To complete this project, students will need the following DIY conveyor belt materials:
- Cardboard or Foam Board: For the frame of the conveyor belt.
- Rubber Sheet or Fabric: As a flexible, durable surface that will act as the conveyor belt.
- Pulleys: Small spools or plastic discs can be used.
- Motor: A small DC motor will power the conveyor belt. This component is optional, depending on whether the conveyor is to be motorized or manual.
- Battery Pack: If a motor is used, a suitable battery pack is necessary.
- Adhesives: Tape and glue to assemble parts securely.
- Scissors and Cutting Tools: For shaping and cutting materials.
- Ruler and Marker: For accurate measurement and marking.
Learning Outcomes
Upon completion of the conveyor belt project, students will be able to demonstrate:
- Technical Knowledge: Understanding of how conveyor belts function and the roles of each component within the system.
- Construction Skills: Ability to follow a blueprint and assemble a working model using various materials and tools.
- Innovation and Creativity: Capacity to innovate with available resources and possibly improve the design.
- Teamwork and Collaboration: Experience working in a group setting, sharing tasks, and collaborating effectively to achieve a common goal.
Project Execution Steps
- Introduction to Basics: Start with a lesson on the mechanics of conveyor belts, including how pulleys, belts, and motors work.
- Design Phase: Students design their conveyor belt, deciding on dimensions and materials based on their specific project requirements.
- Assembly Workshop: Under supervision, students assemble their conveyor belts, using tools and materials provided.
- Testing and Refinement: Students test their conveyor belts and make necessary adjustments to improve functionality.
- Presentation: Each group presents their completed project, discussing the challenges they faced and how they overcame them.
Assessment Criteria
Students will be assessed on the following:
- Design Efficiency: How well does the conveyor belt perform the intended function?
- Creativity: How creative and effective were the solutions to the challenges faced during the project?
- Presentation: Clarity and thoroughness in explaining their project process and outcomes.
This DIY conveyor belt project offers a comprehensive educational experience, teaching students about the practical applications of DIY conveyor belt material and engineering principles. Through this project, they will gain valuable insights into the intersection of science, technology, and real-world applications.
Homemade Conveyor Belt for Wood Using DIY Conveyor Belt Material
Crafting a homemade conveyor belt for wood requires careful consideration of the materials and design to ensure strength and durability. This guide provides instructions for building a DIY conveyor belt using robust DIY conveyor belt materials, specifically designed to handle the rigors of transporting wood. Below, we discuss six key considerations to ensure your conveyor belt is both effective and long-lasting.
Key Considerations for Building a Wood Conveyor Belt
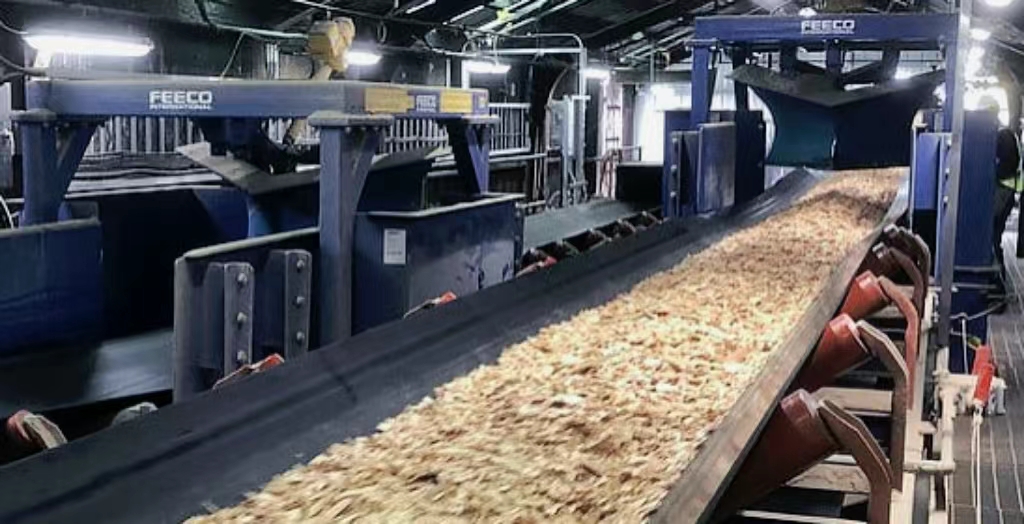
- Belt Material: The choice of belt material is crucial as it needs to withstand the weight and abrasiveness of wood. A thick rubber or heavy-duty PVC belt is ideal, as these materials offer durability and resistance to wear and tear.
- Frame Construction: The frame should be constructed from materials capable of supporting heavy loads without bending. Steel or heavy aluminum are preferred for their strength and rigidity. Ensure all joints are securely welded or bolted together.
- Motor and Gearbox: Opt for a motor with sufficient torque to move heavy loads of wood, especially if the conveyor belt will be used uphill. A gearbox may be necessary to adjust the speed and torque according to your needs.
- Pulley and Bearings: Use steel pulleys and high-quality bearings to support the conveyor belt. Bearings should be sealed against dust and debris to prolong their life and maintain smooth operation.
- Support Rollers: To prevent the conveyor belt from sagging under the weight of the wood, install support rollers along the length of the conveyor. These rollers should be spaced evenly and be capable of rotating under load without significant resistance.
- Safety Features: Since wood can be a cumbersome and potentially hazardous material to transport, incorporate safety features such as emergency stop buttons, guards around moving parts, and a reliable method for quickly disengaging the motor.
Step-by-Step Instructions for Assembly
- Design the Conveyor Layout: Sketch the design of your conveyor belt, including length, width, and load capacity. Determine the positioning of the motor, pulleys, and support structures.
- Construct the Frame: Cut and assemble the steel or aluminum frame based on your design. Ensure all connections are secure and check for structural integrity.
- Install the Pulleys and Motor: Attach the pulleys at each end of the frame and mount the motor. Ensure the motor is aligned correctly to avoid undue strain on the belt.
- Lay the Conveyor Belt: Place the chosen belt material over the pulleys. Adjust the tension to ensure the belt is tight but not overstretched. Secure the belt to the pulleys if necessary.
- Add Support Rollers: Install the support rollers beneath the belt. Make sure they are aligned and level to provide consistent support.
- Implement Safety Features: Install guards and emergency stop mechanisms. Test these features to ensure they function correctly before full operation.
- Test the Conveyor: Run the conveyor belt empty to check for smooth operation and correct any issues. Gradually add weight to test the load capacity and make adjustments as needed.
By following these instructions and focusing on the use of sturdy DIY conveyor belt materials, you can create a reliable and durable conveyor system that will effectively transport wood and other heavy materials. This project not only serves a practical purpose but also enhances your understanding of mechanical systems and materials engineering.
Optimizing Your DIY Conveyor Belt with DIY Conveyor Belt Material
To ensure that your DIY conveyor belt performs optimally and lasts long, careful attention must be given to both the construction and maintenance of the system. Using appropriate DIY conveyor belt materials and following best practices for maintenance can significantly enhance both the performance and longevity of your conveyor belt. Here are 12 tips and tricks to help you optimize your DIY conveyor belt.
Material Selection and Construction Tips
- Choose High-Quality Belt Material: Opt for materials that are robust and appropriate for the type of load you will transport. Heavy-duty rubber or reinforced PVC are excellent choices for durability and resistance to wear.
- Use Suitable Frame Materials: A strong frame made from steel or aluminum can provide the necessary support and stability for your conveyor belt, especially under heavy loads.
- Correct Pulley Selection: Ensure that pulleys are made of materials that can withstand the belt tension and load. Steel pulleys are ideal for high-load scenarios.
- Bearing Quality: High-quality bearings not only reduce maintenance needs but also increase the efficiency of your conveyor by reducing friction.
- Appropriate Motor Selection: Choose a motor with enough power to handle the conveyor’s operational load but avoid over-sizing, which can be inefficient and costly.
- Proper Tensioning: Too much tension can lead to premature wear, while too little can cause slippage. Adjust tension carefully to find a balance.
Maintenance and Performance Enhancement Tips
- Regular Inspection: Schedule regular inspections of the entire conveyor system to check for wear and tear, especially on the belt and joints.
- Lubrication: Keep all moving parts, especially bearings and pulleys, well-lubricated to reduce wear and save energy.
- Keep It Clean: Debris on the conveyor belt can cause premature wear and potential damage. Clean your conveyor regularly to prevent build-up.
- Monitor Belt Alignment: A misaligned belt can cause uneven wear and potential system failures. Regularly check and adjust the alignment of your belt.
- Replace Worn Parts Promptly: Do not wait for a failure to replace worn out parts. Proactive replacement helps avoid downtime and possible damage to other components.
- Optimize Speed Settings: Adjust the speed of the conveyor to match the type and weight of the material being transported. Optimizing speed can enhance efficiency and reduce strain on the conveyor.
Additional Considerations
- Temperature and Environmental Conditions: Be aware of the operating environment. Extreme temperatures and exposure to harsh chemicals can degrade DIY conveyor belt materials faster than normal.
- Customization for Specific Loads: Customize your conveyor system to suit the specific types of materials you plan to transport. This might mean adjusting the spacing of rollers or the type of belt surface texture.
By focusing on these tips and choosing the right DIY conveyor belt materials, you can significantly enhance the performance and extend the lifespan of your DIY conveyor belt. Regular maintenance, proper assembly, and thoughtful material choice are key to optimizing your conveyor system for any application.
Case Studies and Success Stories: DIY Conveyor Belt Material
Real-Life Examples
The use of DIY conveyor belt material has enabled countless individuals and organizations to create functional, cost-effective conveyor systems tailored to their specific needs. These case studies and success stories highlight the diverse applications and innovative approaches taken by hobbyists, students, and professionals.
Hobbyist Projects
John’s Workshop Conveyor
John, a woodworking enthusiast, needed a way to efficiently move wood pieces across his workshop. Using DIY conveyor belt material, he built a conveyor belt system that significantly improved his workflow. John chose PVC for the belt due to its smooth surface and durability, ensuring that his wood pieces moved without getting scratched.
- Materials Used: PVC belt, steel frame, roller bearings, and a small motor.
- Challenges: Ensuring the belt was strong enough to carry heavy wood pieces and aligning the rollers properly.
- Outcome: John’s DIY conveyor belt now helps him transport wood effortlessly, increasing his productivity and making his workshop safer by reducing manual lifting.
Sarah’s Garden Conveyor
Sarah, an avid gardener, built a conveyor belt to help move soil and compost. Using recycled materials, including an old treadmill belt, she created a durable conveyor system perfect for her gardening needs.
- Materials Used: Recycled treadmill belt, wooden frame, PVC rollers, and an old washing machine motor.
- Challenges: Integrating the motor and ensuring it had enough power to move heavy loads.
- Outcome: Sarah’s DIY conveyor belt efficiently moves soil and compost, saving her time and physical effort, and proving that repurposed materials can be both functional and sustainable.
Student Projects
High School Engineering Project
A group of high school students designed and built a conveyor belt for their engineering class. Their project aimed to demonstrate principles of mechanics and automation using DIY conveyor belt material.
- Materials Used: Rubber belt, aluminum frame, 3D-printed rollers, and a programmable motor controller.
- Challenges: Learning to program the motor controller and ensuring precise belt tension.
- Outcome: The students successfully built a working conveyor belt, which they used to transport small objects during a school exhibition. This project earned them top marks and sparked interest in further engineering studies.
University Research Conveyor
In a university research lab, students built a conveyor belt to study material handling and automation. They selected DIY conveyor belt material that could withstand various weights and types of materials used in their experiments.
- Materials Used: Fabric-reinforced rubber belt, stainless steel frame, idler rollers, and a stepper motor with a microcontroller.
- Challenges: Calibrating the stepper motor for precise control and ensuring the belt could handle different experimental materials.
- Outcome: The conveyor belt became an integral part of their research, enabling precise control over material movement and enhancing the accuracy of their experiments.
Professional Projects
Small Manufacturing Business
A small manufacturing business needed an affordable conveyor system to transport products between workstations. By using DIY conveyor belt material, they designed a cost-effective solution that met their needs without compromising quality.
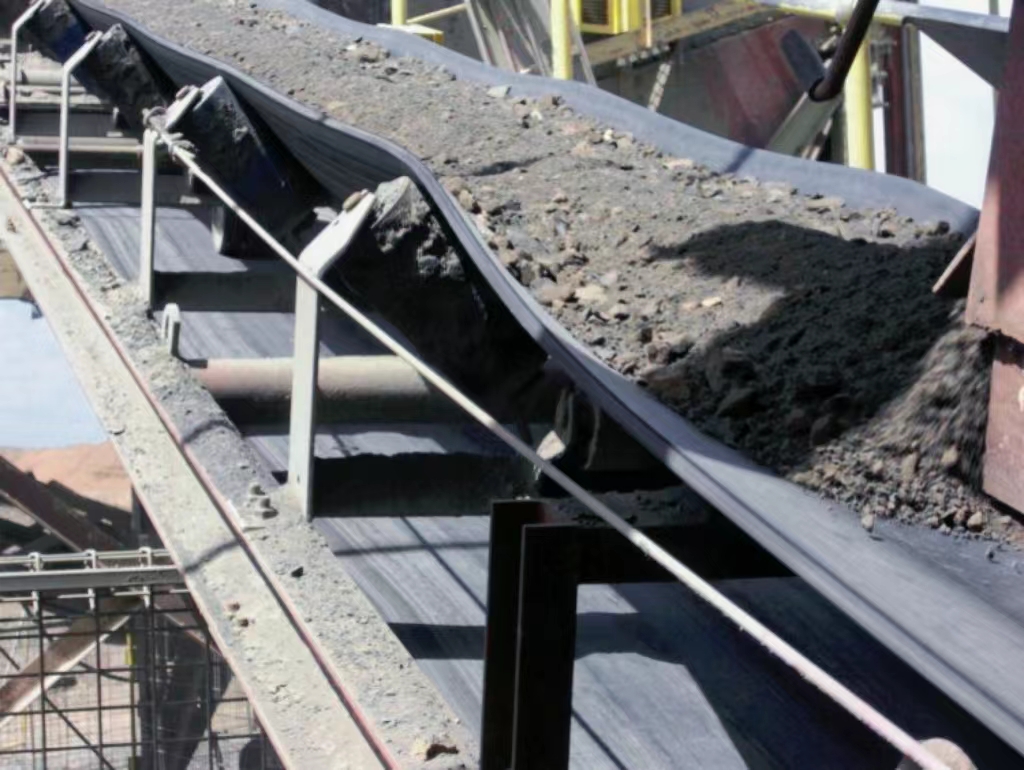
- Materials Used: Heavy-duty rubber belt, galvanized steel frame, industrial-grade bearings, and a powerful motor.
- Challenges: Ensuring the system could handle continuous operation and heavy loads.
- Outcome: The DIY conveyor belt significantly improved workflow efficiency, reducing manual handling and increasing production speed. This system allowed the business to expand its operations without a substantial investment in commercial conveyor systems.
Agricultural Application
Farmers used DIY conveyor belt material to build a conveyor system for moving harvested crops. This system needed to be robust, durable, and capable of handling large volumes of produce.
- Materials Used: Modular plastic belt, treated wood frame, high-torque motor, and weather-resistant components.
- Challenges: Creating a system that could operate in outdoor conditions and handle bulky loads.
- Outcome: The conveyor belt system proved highly effective, reducing the time and labor required for moving crops. It also minimized damage to the produce, enhancing overall efficiency and yield.
Connect with us for superior conveyor belt options.
Photos and Videos
Visual documentation plays a crucial role in showcasing the diversity and functionality of projects utilizing DIY conveyor belt material. Photos and videos of these projects not only highlight the technical aspects but also provide inspiration for others looking to embark on similar DIY endeavors.
- John’s Workshop Conveyor: Photos of the completed conveyor system in operation, moving large wood pieces smoothly.
- Sarah’s Garden Conveyor: Videos showing the conveyor belt moving soil and compost effortlessly in her garden.
- High School Engineering Project: Clips from the school exhibition demonstrating the conveyor belt transporting small objects.
- University Research Conveyor: Photos of the conveyor belt integrated into the research lab, handling various experimental materials.
- Small Manufacturing Business: Videos of the conveyor belt streamlining the production process in the manufacturing facility.
- Agricultural Application: Images showing the conveyor belt in the field, moving large volumes of harvested crops efficiently.
These case studies and success stories illustrate the versatility and practicality of using DIY conveyor belt material across different fields, showcasing how innovative solutions can be achieved with accessible materials and a bit of creativity.
FAQs about DIY Conveyor Belt Material
To construct a conveyor belt, several materials are essential, each selected based on the belt’s intended use and operating environment. The primary materials include:
Rubber: Often used for the belt’s body, rubber provides flexibility and durability. Natural rubber or synthetic forms such as styrene-butadiene rubber are common.
Fabric: Materials like polyester, nylon, or cotton are used as reinforcement layers within the belts to provide strength and shape retention.
Steel: In belts that require high strength, steel wires or mesh are incorporated as reinforcement to withstand heavy loads.
PVC: Polyvinyl chloride is used in lighter conveyor belts and is valued for its resistance to chemicals and abrasion.
Silicone: Used in high-temperature environments due to its heat resistance.
Urethane: Known for its wear resistance and used in applications where abrasion is a concern.
Each material is chosen to suit the specific mechanical demands of the conveyor system, including load weight, speed, and environmental factors such as exposure to chemicals, temperatures, and moisture.
The material used for conveyor belts depends largely on the belt’s specific application. Common materials include:
Rubber: Versatile and resilient, rubber is widely used for general purpose belts, especially in the mining and milling industries.
PVC: Preferred for its light weight and resistance to corrosion, PVC belts are common in food processing and pharmaceutical industries.
Polyurethane: Known for its hygienic properties, making it suitable for food processing industries.
Metal: Steel or mesh belts are used in situations requiring high strength, thermal resistance, or exposure to harsh environments.
The choice of material impacts the belt’s performance, longevity, and suitability for specific tasks, making it crucial to select based on the operational requirements.
The best material for a conveyor system depends on the specific requirements of the operation including the type of goods being transported, the environmental conditions, and the necessary speed and efficiency of the system:
Rubber: Excellent for heavy-load industries due to its durability and elastic nature.
PVC: Ideal for food processing or pharmaceuticals due to easy cleaning and resistance to chemicals.
Metal: Best for high-temperature applications or those involving sharp or hot objects.
Urethane: Used in applications where materials with good wear resistance are needed.
Ultimately, there is no one-size-fits-all answer, and the best material should align with operational demands to ensure optimal function and efficiency of the conveyor system.
The ingredients, or components, of conveyor belts can vary widely based on the type and purpose of the belt. Here are some common ingredients:
Base Material: Rubber, PVC, or fabric are typical base materials providing the structural foundation of the belt.
Reinforcement Layers: Steel, nylon, or polyester layers are added to enhance strength and ensure the belt can handle the tension during operation.
Top Coating: Materials like urethane may be used as a top coating to provide a durable surface resistant to wear and abrasion.
Additives: Components like antioxidants, antistatic agents, and fire retardants may be incorporated to improve the belt’s functionality and safety properties.
These ingredients are combined to create conveyor belts tailored to specific industrial needs, balancing factors like strength, durability, and resistance to environmental challenges.
To make a DIY conveyor belt, gather materials like rubber for the belt, sturdy fabric, or modular plastic components. Follow these steps:
Design your conveyor layout.
Assemble the frame using metal or wood.
Attach the rollers and drive pulleys.
Install the motor and drive system.
Secure the belt material onto the rollers.
Test and adjust for proper alignment and tension.
Add any additional features or safety measures as needed.
The most common material for conveyor belts is rubber, known for its durability and flexibility. Other materials include sturdy fabric and modular plastic components, each offering specific properties like corrosion resistance and wear resistance.
Fabricating a belt conveyor involves several steps:
Design the Conveyor: Create a detailed plan, including dimensions and component placement.
Gather Materials: Use materials like metal for the frame, rubber or plastic for the belt, and metal or plastic for rollers and pulleys.
Build the Frame: Assemble the frame according to your design, ensuring it is sturdy and level.
Install Rollers and Pulleys: Attach rollers and drive pulleys at designated points.
Set Up the Drive System: Connect the motor and drive mechanism, ensuring it aligns with the drive pulley.
Attach the Belt: Secure the conveyor belt material onto the rollers and pulleys, adjusting tension as needed.
Test and Adjust: Run the conveyor to check for alignment, tension, and proper operation. Make necessary adjustments to ensure smooth functioning.
These FAQs cover the basics of making, using, and understanding the materials for DIY conveyor belts, providing a comprehensive guide for enthusiasts and beginners.
Last Updated on June 21, 2024 by Jordan Smith
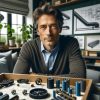
Jordan Smith, a seasoned professional with over 20 years of experience in the conveyor system industry. Jordan’s expertise lies in providing comprehensive solutions for conveyor rollers, belts, and accessories, catering to a wide range of industrial needs. From initial design and configuration to installation and meticulous troubleshooting, Jordan is adept at handling all aspects of conveyor system management. Whether you’re looking to upgrade your production line with efficient conveyor belts, require custom conveyor rollers for specific operations, or need expert advice on selecting the right conveyor accessories for your facility, Jordan is your reliable consultant. For any inquiries or assistance with conveyor system optimization, Jordan is available to share his wealth of knowledge and experience. Feel free to reach out at any time for professional guidance on all matters related to conveyor rollers, belts, and accessories.