Efficiency Showdown: Drag Conveyor vs Belt Conveyor in Industry
In the realm of material handling, conveyor systems stand as the backbone of numerous industries, streamlining the transportation of bulk materials and goods through complex manufacturing processes. Among the myriad of options available, the choice between a drag conveyor vs belt conveyor emerges as a critical decision that can significantly influence the operational efficiency and cost-effectiveness of a facility. This decision hinges not only on the nature of the materials being transported but also on the specific requirements of the operation, including space constraints, handling capacities, and environmental considerations. Selecting the appropriate conveyor system is paramount to optimizing workflow, minimizing downtime, and ensuring a seamless production line. As we delve deeper into the functionalities and advantages of these conveyor types, it becomes evident that understanding their distinct characteristics is essential for making an informed choice that aligns with the operational goals and budgetary constraints of a business.
Conveyor System Overview: Drag Conveyor vs Belt Conveyor Insights
Selecting the appropriate conveyor system is critical for optimizing operational efficiency and cost-effectiveness in material handling. The comparison among drag conveyors, belt conveyors, and chain conveyors highlights the importance of understanding each system’s unique capabilities and limitations. Here’s a detailed look into their applications and key considerations.
Drag Conveyors
Drag conveyors, or en-masse conveyors, utilize a chain mechanism to drag material through a closed trough. This type is favored for its ability to handle a variety of bulk materials, from grains to heavy ores, in a compact and controlled environment.
- General Applications:
- Ideal for handling abrasive materials like sand, metal chips, and coal, minimizing wear and tear.
- Used in the agricultural sector for grain and feed movement due to their gentle handling.
- Effective in waste management facilities for transporting solid waste materials.
- Suitable for chemical industries where contamination control is critical.
- Employed in biomass operations for moving wood chips and other biofuels.
- Key Points:
- High Efficiency: Optimizes space by moving materials in a compact, enclosed design.
- Dust Control: Enclosed system significantly reduces dust and contamination, improving air quality.
- Material Integrity: Gentle on materials, reducing breakage and degradation.
- Customization: Can be tailored with various flight designs to handle specific material types.
- Maintenance: Requires periodic inspection and maintenance of the chain and flight system to ensure longevity.
Belt Conveyors
Belt conveyors feature a continuous looped belt of various materials stretched between two pulleys. They are highly adaptable and can transport a wide range of materials over considerable distances.
- General Applications:
- Versatile in transporting a wide range of goods from bulk materials to individual products.
- Commonly used in the food industry for moving packaged items and raw materials.
- Integral to warehouse operations for sorting and distributing products.
- Utilized in mining for transporting ore over long distances from mines to processing plants.
- Essential in airports for baggage handling systems.
- Key Points:
- Adaptability: Can be equipped with various belt types (e.g., fabric, steel, modular plastic) to suit different applications.
- Long-Distance Capability: Efficiently moves materials over long stretches, including complex routes with inclines and declines.
- Speed Control: Speed can be adjusted according to the operational needs, enhancing process control.
- Ease of Maintenance: Modular design allows for easy replacement of parts and expansion of the system.
- Environmental Sensitivity: Open design may require additional measures for dust and environmental control.
Chain Conveyors
Chain conveyors utilize a series of chains to move materials, either on pallets or directly on the conveyor, making them ideal for heavy or bulky items.
- General Applications:
- Ideal for heavy-duty applications such as automotive assembly lines and heavy machinery manufacturing.
- Used in pallet handling operations for stable and secure transport.
- Suitable for high-temperature environments like foundries and steel mills.
- Employed in the beverage industry for moving large quantities of bottles or cans.
- Utilized in agricultural equipment manufacturing for moving large parts and assemblies.
- Key Points:
- Robust Design: Built to handle heavy loads and harsh conditions without significant wear.
- Stability: Provides a stable platform for goods, reducing the risk of damage during transport.
- Customization: Can be designed with various attachments and carriers to accommodate specific items.
- Operational Reliability: Less prone to slippage and misalignment compared to belt systems.
- Maintenance Considerations: Requires regular lubrication and inspection to maintain chain integrity and prevent failures.
Understanding these aspects of drag conveyors, belt conveyors, and chain conveyors is essential for making an informed decision that aligns with the specific needs of material handling operations, ensuring efficiency, safety, and cost-effectiveness.
Get expert advice on the best conveyor belts for your needs!
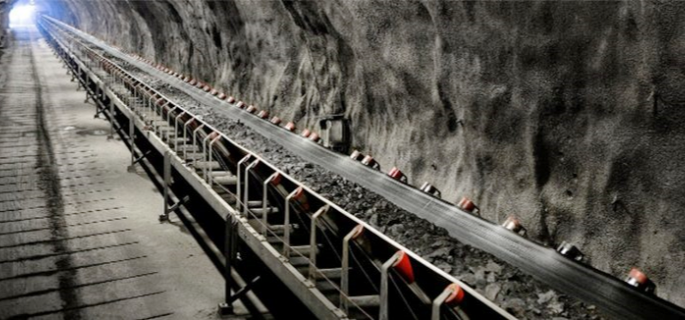
Drag Conveyor VS Belt Conveyor: Features and Components
Choosing between a drag conveyor and a belt conveyor depends on the material being handled, the required movement style, and the operational environment. Drag conveyors are more suited for heavy-duty applications and challenging materials, while belt conveyors offer versatility and efficiency in a wider range of industries. Drag conveyor vs belt conveyor: drag conveyors outperforming belt and screw conveyors in conveying efficiency and flexibility.
Drag Conveyor vs Belt Conveyor
The ongoing debate between drag conveyor vs belt conveyor systems is a focal point for industries seeking to enhance their material handling capabilities. Each system offers distinct operational mechanisms and advantages, tailored to meet specific requirements. Understanding the intricate differences in design, operation, applications, and the comprehensive pros and cons of each can significantly influence the decision-making process, impacting overall efficiency and cost-effectiveness.
Design and Operation
In the realm of material handling, the operational design of drag conveyors and belt conveyors presents a study in contrasts, each with its unique strengths and applications.
Drag Conveyors:
- Utilize a robust chain mechanism to pull materials through a closed trough, optimizing linear, direct paths.
- Feature an enclosed system that significantly reduces dust and contamination, ideal for sensitive environments.
- Are particularly effective in handling abrasive or hot materials without degradation, preserving product quality.
- Boast an energy-efficient design, leading to lower operational costs.
- Maintenance primarily focuses on the chain and flight system, ensuring durability and reliability.
- Offer limited flexibility for complex routing due to their straight-line operation.
Belt Conveyors:
- Employ a continuous belt moving over rollers or a flat surface, allowing for flexibility in material types and sizes handled.
- Provide unparalleled flexibility in conveyor layout, capable of accommodating inclines, declines, and turns.
- May require additional dust control measures due to their open design.
- Allow for easy adjustment of speed and throughput, tailoring operation to specific processing needs.
- Involve maintenance that typically includes belt alignment and tension adjustments, critical for smooth operation.
- Can handle a wide variety of material types and sizes, from fine powders to large, bulky items.
Applications
The applications of drag and belt conveyors highlight their suitability for different industrial scenarios, underscoring the importance of selecting the right system based on specific operational needs.
Drag Conveyors are particularly favored in:
- Industries where dust control is paramount, such as food processing and pharmaceuticals, benefiting from the enclosed design.
- The handling of abrasive materials like sand or coal, especially in mining and energy sectors, without wear and tear.
- Situations requiring the transport of hot materials in metal manufacturing, maintaining material integrity.
- Environments where material degradation needs to be minimized, ensuring product quality.
- Operations requiring vertical or steep incline material movement, utilizing space efficiently.
- Applications where the compact design of drag conveyors maximizes limited space.
Belt Conveyors excel in:
- Transporting goods over long distances, navigating complex routes efficiently in logistics and mining.
- Industries requiring gentle handling to prevent damage, such as agriculture.
- Scenarios needing operational flexibility, adapting easily to changing processes.
- Facilities handling diverse material types and sizes, from agriculture to manufacturing.
- Speed and efficiency-critical environments, like distribution centers.
- Integrating sorting and processing steps along the conveyor path, enhancing operational flow.
Pros and Cons
Before delving into the specific advantages and disadvantages of each system, it’s crucial to understand that the choice between drag conveyors and belt conveyors can significantly affect the operational dynamics of material handling.
Advantages of Drag Conveyors:
- Unmatched in handling abrasive and hot materials, maintaining operational integrity.
- Low maintenance due to their enclosed design, reducing downtime and operational costs.
- High material transport efficiency, utilizing less energy for movement.
- Superior dust control capabilities, essential for maintaining clean work environments.
- Preserves material integrity, crucial for quality-sensitive products.
- Compact design saves valuable facility space.
- Can be customized to handle various material types.
- Suitable for vertical and steep incline conveying.
Disadvantages of Drag Conveyors:
- Limited to relatively straight-line paths, reducing flexibility in system design.
- Not suitable for materials prone to sticking or clumping, which could hinder performance.
- The complexity of initial installation due to the enclosed design.
- Potential for more frequent maintenance in abrasive material applications.
- Higher initial costs compared to some belt conveyor configurations.
- Capacity may be limited in comparison to some belt conveyor systems.
Advantages of Belt Conveyors:
- Highly versatile, capable of transporting a wide range of materials.
- Can cover long distances, including complex routes with inclines and declines.
- Adjustable speed and throughput for operational flexibility.
- Gentle on materials, reducing potential damage during transport.
- Open design allows for easy inspection and maintenance.
- Can be equipped with various accessories for sorting and processing.
- Suitable for both heavy-duty and light applications.
- Relatively low operating costs.
- Easily integrated into existing material handling systems.
Disadvantages of Belt Conveyors:
- Require more space due to their layout and operation.
- Sensitive to environmental conditions, such as wind and moisture.
- May require additional dust control systems.
- Potential for material spillage and loss.
- Regular maintenance needed for belt alignment and tension.
- Can be more challenging to seal completely for dust control.
- Material can stick to belts, requiring regular cleaning.
- Higher energy consumption for long-distance transport.
In transitioning between the strengths and weaknesses of drag conveyors and belt conveyors, it’s evident that the choice between these systems hinges on the specific requirements of the material handling operation. Factors such as the type of materials, the desired path of conveyance, environmental considerations, and cost must all be carefully weighed. A thorough understanding of these aspects is indispensable for selecting a system that not only enhances operational efficiency but also aligns with strategic organizational goals.
It seems there was a slight misunderstanding in the instructions regarding the comparison focus. The initial request mentioned a comparison between drag conveyors and belt conveyors, but the follow-up request shifts the comparison to drag conveyors and chain conveyors. For clarity and to adhere to the instructions, I’ll proceed with the comparison between drag conveyors and chain conveyors, incorporating the essential keyword focus from the initial request where applicable.
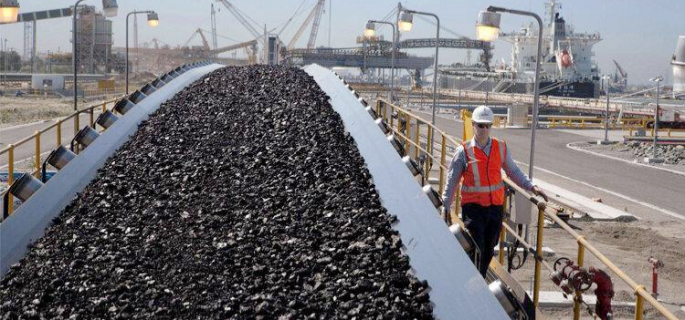
Drag Conveyor VS Belt Conveyor VS Tubular Drag Conveyors
Here’s a comparison table for Drag Conveyor, Belt Conveyor, and Tubular Drag Conveyors based on their features and components:
Here’s a comparison table for Drag Conveyor, Belt Conveyor, and Tubular Drag Conveyors based on their features and components:
Drag Conveyor vs. Chain Conveyor
The comparison between drag conveyors and chain conveyors is essential for industries that rely heavily on efficient material handling systems. While both types serve the purpose of transporting materials from one point to another, their operational mechanisms, design, and suitability for specific applications vary significantly. Understanding these differences is crucial for selecting the most appropriate conveyor system that aligns with operational needs and enhances productivity.
Differences
When examining drag conveyor vs chain conveyor systems, several key differences emerge, each influencing their performance and suitability for various material handling tasks:
- Operational Mechanism: Drag conveyors use a chain mechanism with attached paddles to pull material through a trough or tube, whereas chain conveyors typically use one or more chains to move materials directly on the conveyor’s pathway.
- Enclosure: Drag conveyors are often fully enclosed, reducing dust and contamination, which contrasts with many chain conveyor designs that are open and may expose materials to the environment.
- Material Handling: Drag conveyors are particularly effective for fine, granular, or abrasive materials, while chain conveyors excel in moving larger, heavier loads.
- Flexibility in Routing: Chain conveyors offer more flexibility in routing, with the ability to handle vertical and horizontal curves, unlike drag conveyors, which are more limited to straight paths or gentle inclines.
- Maintenance Requirements: Drag conveyors typically require less maintenance due to their enclosed design and fewer moving parts, whereas chain conveyors may require more frequent maintenance checks for the chains and sprockets.
- Energy Efficiency: Drag conveyors are generally more energy-efficient, as their design allows for material to be moved with less friction and resistance.
- Installation Complexity: The enclosed nature of drag conveyors can lead to more complex installations compared to the more straightforward setup of many chain conveyors.
- Material Degradation: Drag conveyors tend to be gentler on materials, minimizing degradation, which is an important consideration for sensitive materials. In contrast, chain conveyors, depending on their design, can sometimes cause more material breakage.
- Cost Implications: Initial costs for drag conveyors can be higher due to their enclosed design and material handling capabilities, whereas chain conveyors might offer a more cost-effective solution for simple, heavy-duty applications.
Chain Conveyor Advantages and Disadvantages
Advantages:
- Handling Heavy Loads: Chain conveyors are robust and ideal for transporting heavy or bulky materials efficiently.
- Durability: Designed for durability, they can withstand harsh industrial environments and heavy use.
- Routing Flexibility: Capable of accommodating complex routing, including vertical and horizontal curves.
- Variety of Materials: Suitable for a wide range of material types, including pallets, large containers, and heavy manufacturing components.
- Customization Options: Chain conveyors can be customized with various attachments to handle different loads and applications.
- Low Material Degradation: For certain designs, chain conveyors can transport goods with minimal degradation.
- Operational Reliability: Offers reliable operation with the proper maintenance schedule.
- Ease of Integration: Can be easily integrated into existing material handling systems, enhancing operational flow.
Disadvantages:
- Cost: The initial investment and maintenance costs can be higher, especially for complex systems.
- Complexity of Maintenance: Requires regular lubrication and tension adjustments to prevent wear and ensure smooth operation.
- Noise Levels: Can generate more noise during operation, which may require mitigation measures.
- Limited Enclosure Options: The open design may not be suitable for materials that require protection from environmental contaminants.
- Space Requirements: Depending on the design, chain conveyors may require more space, particularly for complex routing.
- Energy Consumption: Can consume more energy, especially for systems designed to move very heavy loads.
- Material Handling Limitations: Not as effective for fine, powdery materials that could fall between components.
- Operational Speed: Generally operates at lower speeds compared to some drag conveyor designs, which might limit throughput for certain applications.
In transitioning from the operational and design differences to the specific advantages and disadvantages of chain conveyors, it’s evident that the choice between a drag conveyor vs chain conveyor (and implicitly considering drag conveyor vs belt conveyor for broader context) hinges on the unique requirements of the material handling operation. Factors such as the type of materials to be transported, the environmental considerations, the complexity of the installation space, and cost implications play critical roles in this decision. A comprehensive understanding of these aspects is indispensable for selecting a system that not only meets the immediate operational needs but also aligns with long-term strategic objectives, ensuring efficiency, safety, and cost-effectiveness.
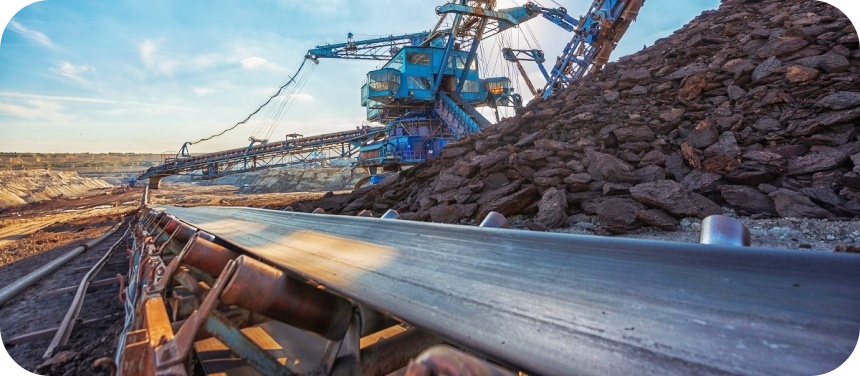
Cost Comparison: Drag Conveyor vs Belt Conveyor
In evaluating the financial implications of integrating a conveyor system into material handling operations, a thorough cost comparison between drag conveyor vs belt conveyor is indispensable. This analysis extends beyond the initial capital outlay to encompass a broad spectrum of operational costs, including energy efficiency, maintenance expenses, and considerations regarding the lifespan of the system. Such a comprehensive review aids in making an informed decision that not only meets the immediate financial requirements but also aligns with long-term operational efficiency and sustainability goals.
Initial Investment
The initial investment required for implementing drag conveyors, belt conveyors, and chain conveyors varies significantly, influenced by factors such as design complexity, capacity needs, and the degree of customization required.
- Drag Conveyors: Typically, drag conveyors demand a higher initial investment compared to belt conveyors. This is attributed to their robust construction and the enclosed system, which is engineered to minimize dust and contamination. Although this design entails a higher upfront cost, it offers substantial benefits for handling abrasive or sensitive materials, potentially justifying the investment in scenarios where material integrity is paramount.
- Belt Conveyors: Belt conveyors generally present a lower initial cost, making them an attractive option for standard applications. The simplicity of their design and the open system contribute to cost-effectiveness. However, for specialized applications requiring custom features or for systems designed to navigate complex routes, the investment can escalate.
- Chain Conveyors: Chain conveyors fall somewhere between drag and belt conveyors in terms of initial investment. Their cost is influenced by the heavy-duty design and the customization required to handle specific materials or operational conditions. For applications involving heavy loads or requiring high durability, chain conveyors may offer a balanced initial cost proposition.
Operational Costs
When considering operational costs, several key factors come into play, including energy efficiency, maintenance expenses, and the overall lifespan of the conveyor system.
- Energy Efficiency: Drag conveyors are often more energy-efficient than belt conveyors due to their enclosed design and the direct transfer method, which reduces friction and energy loss. Belt conveyors, while versatile, may consume more energy, especially over long distances or when handling heavy loads.
- Maintenance Costs: Maintenance expenses can vary widely. Drag conveyors, with their enclosed design, tend to have higher maintenance costs due to the complexity of accessing the internal components. Belt conveyors, in contrast, may require less frequent maintenance, but the open design exposes them to wear and environmental factors that can increase maintenance needs over time.
- Lifespan Considerations: The lifespan of a conveyor system is crucial in evaluating its cost-effectiveness. Drag conveyors, built for durability and to handle abrasive materials, often have a longer lifespan, potentially offering better long-term value. Belt conveyors, depending on the application and maintenance practices, can also offer significant operational life but may require more frequent belt replacements or adjustments.
- System Efficiency and Productivity: The efficiency of a conveyor system directly impacts its productivity and, consequently, operational costs. Drag conveyors typically offer a consistent material flow rate, which can lead to more predictable processing times and reduced bottlenecks in production. Belt conveyors, with their ability to be easily adjusted for speed, offer flexibility in managing varying production demands, potentially increasing overall system productivity.
- Repair and Replacement Costs: Beyond regular maintenance, the costs associated with repairing or replacing parts of the conveyor system can significantly affect its overall cost-effectiveness. Drag conveyors, while generally robust, may incur higher costs for repairing or replacing the chain or flights due to wear or damage. Belt conveyors, on the other hand, may see more frequent needs for belt replacement or repair, especially in applications involving sharp or hot materials that can compromise belt integrity.
- Operational Noise and Worker Safety: The operational noise level of conveyor systems can impact worker safety and may require additional investments in noise reduction measures. Drag conveyors typically operate with lower noise levels due to their enclosed design, potentially reducing the need for costly noise mitigation strategies. Belt conveyors, depending on the material being transported and the speed of operation, can generate higher levels of noise, which might necessitate additional safety measures or protective equipment for workers.
- Material Compatibility and Handling Efficiency: The compatibility of the conveyor system with the materials being transported plays a crucial role in operational efficiency and costs. Drag conveyors are particularly suited for handling abrasive, hot, or sticky materials with minimal loss or degradation, which can lead to cost savings by reducing waste and improving material quality. Belt conveyors, while versatile, may require special belt materials or treatments to handle certain types of materials effectively, potentially increasing operational costs.
Additional Considerations
- System Flexibility: The ability to adapt to changing operational needs without significant additional investment is crucial. Belt conveyors offer greater flexibility in routing and modifications, which can be a cost-saving feature in dynamic operational environments.
- Installation Complexity: The complexity of installing the conveyor system can impact initial costs. Drag conveyors may require more extensive installation efforts, especially in confined spaces, compared to the relatively straightforward installation of belt conveyors.
- Material Handling Capabilities: The type of materials being handled can influence operational costs. Drag conveyors are suited for abrasive or fine materials, potentially reducing waste and associated costs.
- Environmental Impact: Considerations around dust control and material spillage can affect operational costs. Drag conveyors offer superior control in this regard, potentially reducing cleanup and environmental mitigation expenses.
The decision between a drag conveyor vs belt conveyor involves a nuanced analysis of both upfront and ongoing costs, balanced against the specific operational requirements and long-term efficiency goals of the material handling operation. Understanding these cost dynamics is essential for selecting a conveyor system that not only fits the budget but also enhances operational productivity and sustainability.
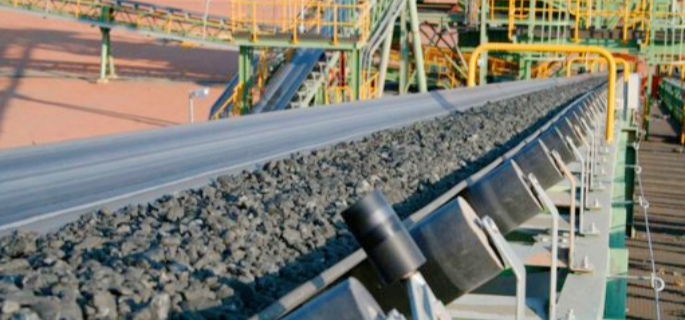
Additional Conveyor Types Overview: Beyond Drag Conveyor vs Belt Conveyor
While the comparison between drag conveyor vs belt conveyor systems is crucial for determining the most suitable conveyor for specific material handling needs, understanding the broader landscape of conveyor technology is essential. Other conveyor types, each with unique advantages and applications, play pivotal roles in various industries. Here’s an overview of some additional conveyor types, providing context to the diverse options available.
This table provides a snapshot of the diverse conveyor technologies available beyond the drag conveyor vs belt conveyor comparison, highlighting their roles, advantages, suitability for different operations, and inherent limitations. Each conveyor type offers unique benefits tailored to specific material handling requirements, underscoring the importance of selecting the right conveyor system based on the operational context and specific needs.
Find the perfect conveyor belts for your applications. Inquire today!
Drag Conveyor VS Belt Conveyor: What Are the Different Types of Conveyor Systems
Conveyor systems are mechanical devices used to transport materials from one place to another, and they come in various types tailored for different applications and industries. Here are the different types of conveyor systems:
1. Belt Conveyors
- Description: Use a continuous belt to move materials.
- Applications: Common in industries like mining, food processing, and manufacturing. Ideal for moving large volumes of materials over long distances.
- Types:
- Flat Belt Conveyors: Standard for transporting items.
- Cleated Belt Conveyors: Have cleats for moving items up an incline.
- Modular Belt Conveyors: Made of interlocking plastic pieces, allowing for easy customization.
2. Roller Conveyors
- Description: Use rollers to move items, which can be powered or unpowered (gravity).
- Applications: Ideal for moving heavy or bulky items in distribution centers and manufacturing plants.
- Types:
- Gravity Roller Conveyors: Use gravity for movement, no motor needed.
- Powered Roller Conveyors: Use a motor to drive the rollers.
- Lineshaft Roller Conveyors: Powered by a shaft beneath the rollers.
3. Chain Conveyors
- Description: Use chains to move heavy items or materials.
- Applications: Common in automotive and heavy manufacturing industries where heavy loads need to be moved.
- Types:
- Drag Chain Conveyors: Use a chain to drag materials along a path.
- Apron Conveyors: Use a chain to move a series of overlapping metal plates.
- Slat Conveyors: Use slats attached to a chain, typically used for moving large, heavy items.
4. Screw Conveyors
- Description: Use a rotating helical screw inside a tube to move materials.
- Applications: Often used in food processing, agriculture, and waste management.
- Types:
- Horizontal Screw Conveyors: Move materials in a straight horizontal line.
- Inclined Screw Conveyors: Move materials up or down an incline.
- Vertical Screw Conveyors: Lift materials vertically.
5. Pneumatic Conveyors
- Description: Use air pressure or vacuum to move bulk materials through enclosed pipes.
- Applications: Common in industries like food processing, pharmaceuticals, and chemicals, where dust-free and contamination-free transportation is crucial.
- Types:
- Dilute Phase Conveyors: Move materials at high speed in an air stream.
- Dense Phase Conveyors: Move materials at a slower speed in a more concentrated manner.
6. Bucket Elevators
- Description: Use buckets attached to a belt or chain to vertically lift materials.
- Applications: Ideal for moving bulk materials vertically, such as grains, minerals, or fertilizers.
- Types:
- Centrifugal Bucket Elevators: Use centrifugal force to discharge materials.
- Continuous Bucket Elevators: Gently discharge materials without the use of centrifugal force.
7. Drag Chain Conveyors
- Description: Use a chain to drag bulk materials through a trough.
- Applications: Used in heavy-duty applications like mining, grain handling, and material recycling.
- Types:
- En-Masse Conveyors: Move bulk materials at low speed and high volume.
- Tubular Drag Conveyors: Move materials in a fully enclosed tube using discs attached to the chain.
8. Slat Conveyors
- Description: Use slats attached to a chain to move materials along a fixed path.
- Applications: Commonly used in automotive assembly lines and heavy equipment manufacturing.
9. Overhead Conveyors
- Description: Use trolleys suspended from an overhead track to move materials.
- Applications: Frequently used in automotive, painting, and garment industries where floor space is limited.
- Types:
- Power and Free Conveyors: Allow for materials to be stopped and started at different points.
- Monorail Conveyors: Use a single track to move materials in a continuous loop.
10. Vibrating Conveyors
- Description: Use vibration to move materials along a trough.
- Applications: Often used in the food industry and for moving bulk materials like sand or gravel.
- Types:
- Natural Frequency Conveyors: Use the natural frequency of the system to move materials.
- Tuned Coil Vibrating Conveyors: Use electromagnets to create vibrations.
11. Flexible Conveyors
- Description: Use a flexible system that can expand, contract, and curve.
- Applications: Ideal for loading and unloading trucks, moving items in temporary or variable layouts.
- Types:
- Flexible Roller Conveyors: Use rollers to move items in a flexible system.
- Flexible Belt Conveyors: Use belts in a system that can change shape.
12. Magnetic Conveyors
- Description: Use magnets to move ferrous materials along a path.
- Applications: Common in metalworking and recycling industries.
- Types:
- Permanent Magnetic Conveyors: Use permanent magnets to move materials.
- Electromagnetic Conveyors: Use electromagnets that can be turned on and off.
13. Spiral Conveyors
- Description: Use a spiral or helical structure to move materials vertically.
- Applications: Often used in food processing, packaging, and warehousing where vertical space is utilized.
- Types:
- Gravity Spiral Conveyors: Use gravity to move items downwards.
- Powered Spiral Conveyors: Use a motor to move items upwards.
Each conveyor system type has its specific advantages and is selected based on the material to be moved, the distance, the direction of movement, and the environmental conditions.
How to Choose the Right Conveyor: Drag Conveyor vs Belt Conveyor
Selecting the appropriate conveyor system—whether a drag conveyor vs belt conveyor or another type—requires careful consideration of various factors. The decision impacts not only the efficiency and productivity of your operations but also long-term costs and maintenance requirements. Here are nine critical factors to consider when choosing between a drag conveyor, belt conveyor, and other conveyor types, ensuring the selection aligns with your operational needs and goals.
- Material Type: The nature of the materials being handled is paramount. Abrasive, fine, or hazardous materials may be better suited to drag conveyors, which minimize exposure and contamination. Belt conveyors offer versatility for handling a wide range of materials, including bulky items.
- Facility Space: The available space within your facility can dictate the type of conveyor that can be accommodated. Drag conveyors, often enclosed, might require more vertical space, whereas belt conveyors might sprawl over larger horizontal areas but can be more easily routed around existing structures.
- Budget: Initial capital outlay and long-term operational costs, including energy consumption and maintenance, will significantly influence the choice. While belt conveyors might offer a lower initial investment, drag conveyors could provide savings in maintenance and energy efficiency over time.
- Maintenance Capabilities: The ability to perform regular maintenance and repairs in-house can affect the choice. Drag conveyors might require specialized maintenance due to their enclosed design, whereas belt conveyors often allow for easier access and simpler maintenance procedures.
- Operational Efficiency: Consider how the conveyor will integrate into your existing operations. This includes the speed of material transport, ease of loading and unloading, and compatibility with other equipment.
- Energy Efficiency: The energy requirements of the conveyor system should align with your operational sustainability goals and cost considerations. Drag conveyors are generally more energy-efficient, especially for materials that require gentle handling.
- Durability and Lifespan: Assess the expected lifespan of the conveyor system and its components. Systems that are built to last longer may offer better value over time, despite a higher initial investment.
- Safety and Compliance: Ensure the conveyor system meets industry standards and safety regulations, especially when handling hazardous materials. Enclosed systems like drag conveyors can offer enhanced safety features.
- Scalability: The ability to scale the conveyor system as your operations grow is crucial. Consider whether the system can be easily expanded or reconfigured without significant downtime or additional expense.
The Importance of Consulting with Manufacturers for Tailored Solutions
Consulting with conveyor manufacturers is critical for tailoring a solution that meets your specific needs. Here are eight points highlighting the importance of this collaboration:
- Expertise: Manufacturers possess deep knowledge of their systems and can offer insights into the most efficient and cost-effective solutions.
- Customization: They can customize conveyors to handle specific material types, weights, and operational requirements, ensuring optimal performance.
- Integration: Manufacturers can advise on integrating the new conveyor system with existing processes and equipment for seamless operation.
- Compliance: They ensure the conveyor system complies with all relevant industry standards and safety regulations.
- Innovation: Manufacturers often incorporate the latest technology and innovations into their systems, offering you the best possible solution.
- Support: Ongoing support, including maintenance and repair services, ensures your conveyor system continues to operate efficiently.
- Training: They can provide training for your staff on the proper operation and maintenance of the conveyor system.
- Future-proofing: Manufacturers can help design a system that not only meets current needs but also accommodates future expansion and technological upgrades.
Choosing the right conveyor system, whether a drag conveyor vs belt conveyor or another type, is a complex decision that impacts many aspects of your operation. By carefully considering the key factors and consulting with manufacturers, you can ensure that you select a system that meets your needs today and can grow with your business in the future.
FAQs about Drag Conveyor vs Belt Conveyor
Drag conveyors, also known as drag chain conveyors, are designed for moving bulk materials, particularly those that are abrasive, granular, or powdery, across a relatively short distance. They are highly effective in industries where material integrity and minimizing exposure to the external environment are crucial. This includes applications in the agricultural sector for grain handling, in the mining industry for transporting coal or minerals, and in the chemical manufacturing sector where preventing contamination is essential. Drag conveyors operate by dragging material along a trough or tube, which is enclosed to protect the material from outside contaminants and to prevent material loss, making them an ideal choice for handling hazardous or sensitive materials safely and efficiently.
The term “conveyor” refers to a broad category of material handling equipment designed to move items from one location to another. Conveyors can come in various forms, utilizing different mechanisms to transport materials, such as belts, chains, rollers, or screws. A “conveyor belt,” on the other hand, is a specific type of conveyor that uses a continuous belt of fabric, metal, or other materials to transport items along a set path. Conveyor belts are versatile and can handle a wide range of materials, from small, lightweight items to large, bulky goods. The main difference lies in the mechanism of transport; while conveyors can employ various systems to move materials, conveyor belts specifically use a belt mechanism.
Three common types of conveyors used in various industries for material handling are belt conveyors, roller conveyors, and chain conveyors.
Belt Conveyors: Utilize a continuous belt that moves over pulleys or rollers to transport materials along a fixed path. They are versatile and can handle a variety of material types and sizes, making them suitable for many industries.
Roller Conveyors: Comprise a series of rollers over which materials are moved by gravity or manual force, or the rollers themselves can be powered. They are ideal for moving solid, stable items and are commonly used in warehousing and distribution.
Chain Conveyors: Use a chain or multiple chains to move pallets, large containers, or other heavy materials. They are particularly useful for heavy-duty applications where durability and the ability to handle large loads are required.
Each type offers distinct advantages and is suited for different applications based on the material characteristics, required transport distance, and specific operational needs.
Belt conveyors and slat conveyors are both used to transport materials across various distances, but they differ significantly in design and application.
Belt Conveyors: Feature a continuous loop of flexible material, such as fabric, rubber, or metal, that rotates over two or more pulleys. They are suited for transporting a wide range of materials, including small or irregularly shaped items, across long distances. Belt conveyors are versatile, allowing for horizontal, inclined, or declined movement, and can be customized with sidewalls or cleats for specific applications.
Slat Conveyors: Consist of a series of metal or wooden slats attached to a chain, creating a flat, rigid surface for material transport. Slat conveyors are designed to handle heavier, more stable items, such as pallets, containers, or in assembly line operations where materials need to be moved at a steady pace. They offer durability and the ability to operate in harsh environments, but are generally less flexible than belt conveyors in terms of route and material type.
The primary difference lies in their construction and suitability for specific tasks; belt conveyors offer greater flexibility and are ideal for a wide range of materials, while slat conveyors provide a more robust solution for heavy-duty applications.
A drag conveyor and an auger (or screw conveyor) are both used in heavy industries like mining for material handling, but they operate differently and are suited to different tasks.
Drag Conveyor: This conveyor uses a series of flights (attachments) that are dragged through a trough, moving bulk materials such as coal, minerals, or aggregates. The material is conveyed by the dragging action of the flights along the trough, typically resulting in low material degradation. Drag conveyors are well-suited for moving large volumes of material over long distances with minimal spillage.
Auger (Screw Conveyor): An auger consists of a helical screw blade (flight) rotating within a tube or trough to move materials. This method is ideal for handling materials like grains, cement, or small aggregates but tends to cause more material degradation due to the shearing action of the screw. Augers are typically used for shorter distances or vertical transport, where precision and consistency in material feed are more critical.
A drag conveyor operates by using a chain or cable with attached flights that move within a trough or channel. The flights drag the bulk material along the bottom of the trough, propelling it forward. The design of the trough and the close spacing of the flights ensure that the material moves smoothly and steadily, even over long distances or in vertical or inclined configurations.
In heavy industries like mining, drag conveyors are particularly valuable because they can handle a wide range of bulk materials, from fine particles to large lumps, with minimal wear and tear on the equipment. The enclosed design of a drag conveyor also helps to reduce dust and spillage, making it ideal for transporting potentially hazardous or valuable materials safely and efficiently.
Last Updated on August 13, 2024 by Jordan Smith
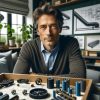
Jordan Smith, a seasoned professional with over 20 years of experience in the conveyor system industry. Jordan’s expertise lies in providing comprehensive solutions for conveyor rollers, belts, and accessories, catering to a wide range of industrial needs. From initial design and configuration to installation and meticulous troubleshooting, Jordan is adept at handling all aspects of conveyor system management. Whether you’re looking to upgrade your production line with efficient conveyor belts, require custom conveyor rollers for specific operations, or need expert advice on selecting the right conveyor accessories for your facility, Jordan is your reliable consultant. For any inquiries or assistance with conveyor system optimization, Jordan is available to share his wealth of knowledge and experience. Feel free to reach out at any time for professional guidance on all matters related to conveyor rollers, belts, and accessories.