Electric Conveyor Belt Cutter – Power Belt Cutters
Conveyor belts are indispensable in various industries, serving as the backbone for material handling in mining, manufacturing, logistics, and more. These belts facilitate the efficient movement of goods and raw materials, significantly enhancing productivity and operational efficiency. However, the continuous operation and varying loads can lead to wear and tear, necessitating regular maintenance and, at times, the precise cutting of belts for repairs or adjustments. This is where electric conveyor belt cutter comes into play, revolutionizing the way maintenance teams approach belt repairs. Unlike manual cutting tools, which can be laborious and less accurate, electric conveyor belt cutters offer a swift, clean, and precise cutting solution. They significantly reduce the effort and time required to cut through tough conveyor belt materials, ensuring that the belts are quickly returned to service with minimal downtime. The introduction of electric conveyor belt cutters has thus become a game-changer in maintaining the efficiency and longevity of conveyor systems across industries.
The Evolution of Belt Cutting Technology and the Rise of Electric Conveyor Belt Cutters
The journey from manual to mechanical and finally to electric conveyor belt cutter technologies marks a significant evolution in the maintenance of conveyor systems. Initially, the task of cut conveyor belts was performed manually, using basic tools like knives and cutters. This method, while straightforward, required considerable physical effort and often resulted in imprecise cuts, affecting the belt’s performance and longevity.
As industries grew and the demand for more efficient maintenance solutions became apparent, mechanical belt cutting tools were introduced. These tools, operated by hand or simple mechanical systems, offered improved precision and reduced the physical strain associated with manual cutting. However, they still fell short in terms of efficiency, safety, and the ability to consistently produce clean, straight cuts, especially on thicker or reinforced belts.
The introduction of the electric conveyor belt cutter represented a pivotal moment in this evolutionary timeline. These cutters combine the precision of mechanical tools with the power and consistency of electric operation, drastically improving the efficiency and safety of belt cutting operations. Electric conveyor belt cutters are designed to quickly and accurately cut through various conveyor belt materials, from rubber to fabric-reinforced and even steel-cord belts, with minimal effort from the operator.
To illustrate the advancements brought about by electric conveyor belt cutters, consider the following comparative data:
This table highlights the significant advantages of electric conveyor belt cutters over their manual and mechanical predecessors. Not only do they require less physical effort, but they also offer superior precision, safety, and efficiency across a wider range of belt types and conditions. The evolution to electric conveyor belt cutters has thus set a new standard in conveyor belt maintenance, ensuring that industries can keep their operations running smoothly with minimal downtime.
Key Features of Electric Conveyor Belt Cutters
The advent of the electric conveyor belt cutter has brought about a significant leap in the way conveyor belts are maintained and repaired. These cutters are engineered with a focus on safety, precision, and efficiency, making them indispensable tools in various industries. Below, we delve into the key features that set electric conveyor belt cutters apart from traditional cutting methods.
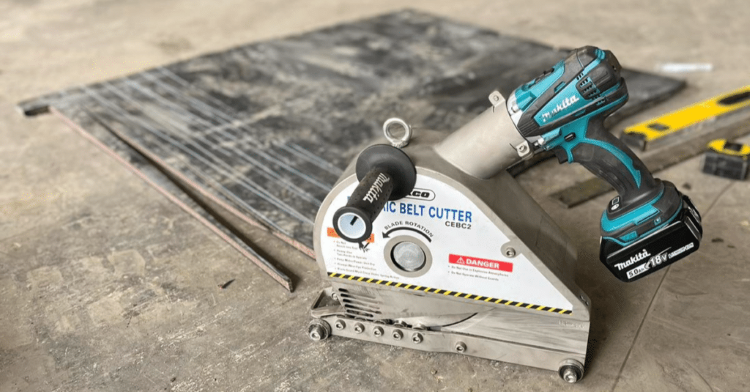
Safety Mechanisms and Ease of Use
One of the standout features of the electric conveyor belt cutter is its emphasis on operator safety. Equipped with safety guards and automatic shut-off features, these cutters minimize the risk of accidents during operation. The design often includes ergonomically placed controls that allow for easy operation without compromising on safety. This focus on safety is a significant advancement over manual cutters, which require more direct contact with the blade and, consequently, pose a higher risk of injury.
Precision and Efficiency in Cutting
Electric conveyor belt cutters are designed for precision and efficiency. They can quickly and accurately cut through various materials, including thick, reinforced rubber belts, without fraying or uneven edges. This precision is achieved through high-quality blades and powerful motors that ensure a clean cut in a fraction of the time it would take with manual or mechanical methods. The efficiency of electric cutters not only saves time but also reduces waste, as precise cuts ensure better fitting during belt splicing or repairs.
Portability and Versatility (Cordless Options)
Modern electric conveyor belt cutters are designed with portability and versatility in mind. Many models are cordless, powered by rechargeable batteries, making them easy to use in field conditions where access to power outlets may be limited. This portability allows maintenance teams to carry out repairs and adjustments directly on the conveyor line, regardless of its location. The versatility of these cutters is further enhanced by their ability to cut through a wide range of belt materials and thicknesses, making them suitable for a variety of industries and applications.
Comparison with Traditional Cutting Methods
When compared to traditional cutting methods, electric conveyor belt cutters offer a host of advantages. Manual cutting tools, while simple, lack the precision and efficiency of electric cutters and pose greater safety risks. Mechanical cutters, on the other hand, offer more precision than manual tools but still fall short in terms of safety features and the ease of use provided by electric models. Furthermore, the portability and versatility of electric cutters, especially cordless models, are unmatched by traditional methods, making them the preferred choice for modern maintenance teams.
The key features of electric conveyor belt cutters—enhanced safety mechanisms, precision cutting, efficiency, and portability—make them essential tools in the maintenance and repair of conveyor belts. Their superiority over traditional cutting methods is clear, marking them as a significant advancement in conveyor belt maintenance technology.
Electric Conveyor Belt Cutters Primary Function
Electric conveyor belt cutters are specialized tools designed to cut through various types of conveyor belts quickly and efficiently. They are powered by electricity, which enhances their cutting capability and precision compared to manual cutters.
These cutters typically consist of a motor, a sharp blade, and a guiding mechanism to ensure straight and accurate cuts. Some models also include safety features such as blade guards and emergency stop buttons.
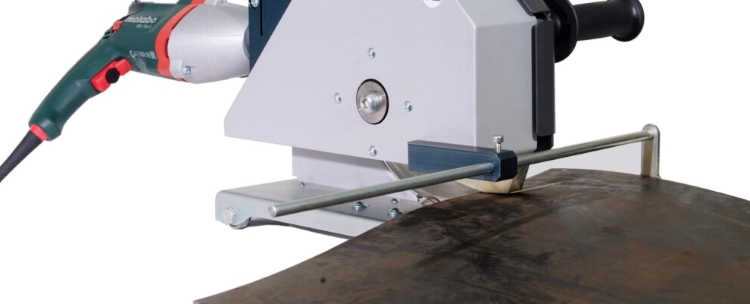
Primary Function of Electric Conveyor Belt Cutters
Power-Driven Cutting
Efficiency: The primary function of electric conveyor belt cutters is to leverage electric power to facilitate fast and efficient cutting of conveyor belts. The motor-driven blade can cut through thick and tough materials with minimal effort from the operator.
Consistency: Electric cutters provide consistent cutting performance, ensuring uniform cuts every time. This consistency is crucial in maintaining the quality and functionality of conveyor belts.
Precision and Accuracy
Guided Cutting Mechanism: Many electric cutters come with built-in guides or rails that help maintain a straight line while cutting. This precision ensures that the edges of the belt are clean and straight, which is important for the belt’s performance and longevity.
Adjustable Settings: Some models offer adjustable cutting depths and angles, allowing users to customize the cut to meet specific requirements. This flexibility is essential for different types of belts and applications.
Safety
Safety Features: Electric conveyor belt cutters are equipped with various safety features to protect the operator. These may include blade guards, safety switches, and emergency stop buttons. Such features minimize the risk of accidents during the cutting process.
Reduced Physical Strain: By using an electric cutter, the physical effort required from the operator is significantly reduced. This not only makes the cutting process safer but also lessens operator fatigue, contributing to a safer working environment.
Versatility
Wide Range of Materials: Electric conveyor belt cutters are designed to handle a variety of belt materials, from soft natural rubbers to the hardest constructed solid woven PVC and fabric-plied belts. This versatility makes them suitable for different industries and applications.
Multiple Applications: These cutters can be used for various purposes, such as trimming excess material, preparing belts for splicing, and making precise adjustments to belt width or length.
Applications of Electric Conveyor Belt Cutters:
Manufacturing: In manufacturing settings, electric conveyor belt cutters are used to prepare belts for assembly lines, ensuring that they fit the required specifications and maintain operational efficiency.
Mining and Quarrying: In these heavy-duty environments, the ability to quickly and accurately cut conveyor belts is essential for maintaining continuous operations and minimizing downtime.
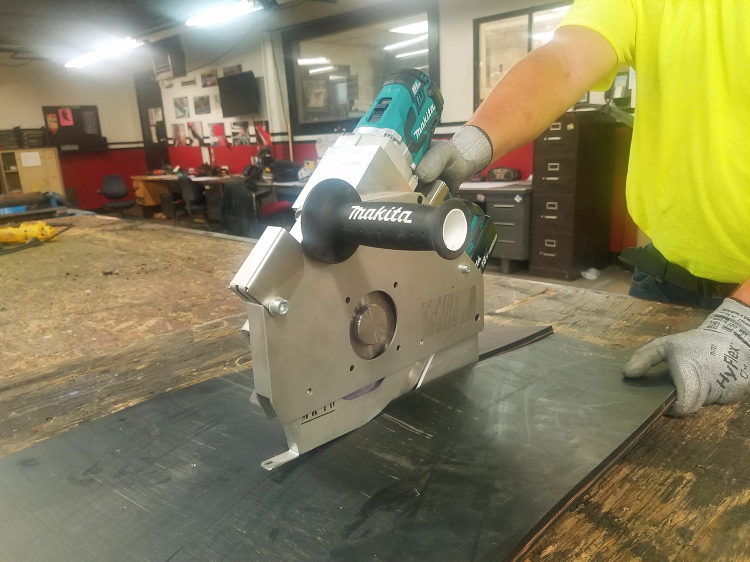
Maintenance and Repairs
On-Site Adjustments: Maintenance teams use electric conveyor belt cutters to make on-site adjustments and repairs to conveyor systems, ensuring that belts remain functional and efficient.
Routine Maintenance: Regular maintenance tasks often require the cutting and splicing of conveyor belts. Electric cutters streamline these tasks, making them quicker and more reliable.
Customization
Custom Belt Fabrication: For applications that require custom-sized belts, electric cutters allow for precise fabrication, ensuring that the belts meet specific requirements and dimensions.
Benefits of Using Electric Conveyor Belt Cutters
Increased Efficiency
Time-Saving: The use of electric power significantly reduces the time required to cut through conveyor belts, compared to manual cutting methods. This efficiency is particularly beneficial in high-volume industrial environments.
Reduced Downtime: By enabling quick and accurate cuts, electric cutters help minimize downtime during maintenance or repair tasks, keeping production lines running smoothly.
Enhanced Precision:
High-Quality Cuts: The precision offered by electric cutters ensures that the edges of the conveyor belts are clean and even, which is critical for the proper functioning of the belts and their integration into conveyor systems.
Reduced Waste: Accurate cutting minimizes material waste, as the belts can be cut to exact specifications without excess material needing to be trimmed or discarded.
Improved Safety
Operator Safety: The safety features built into electric conveyor belt cutters protect operators from potential injuries, making the cutting process safer overall.
Ergonomic Benefits: The reduced physical effort required to operate electric cutters lessens the strain on workers, contributing to a safer and more comfortable working environment.
By addressing these key points, the detailed outline provides a comprehensive explanation of the primary function of electric conveyor belt cutters, emphasizing their efficiency, precision, versatility, and safety in various industrial applications.
Types of Electric Conveyor Belt Cutters
Cordless Conveyor Belt Cutter
Cordless conveyor belt cutters are battery-operated tools designed to cut conveyor belts without the need for a direct power connection. This design offers the freedom to operate the cutter in various locations without being tethered to an electrical outlet.
- Battery Pack: Equipped with rechargeable battery packs, these cutters provide mobility and convenience. The battery pack typically offers sufficient power to handle multiple cuts on a single charge, depending on the thickness and material of the belt.
- Motor and Blade: Similar to corded models, cordless cutters have a motor and a sharp blade designed to slice through various types of conveyor belts efficiently. The motor’s power is calibrated to work effectively with the battery’s output.
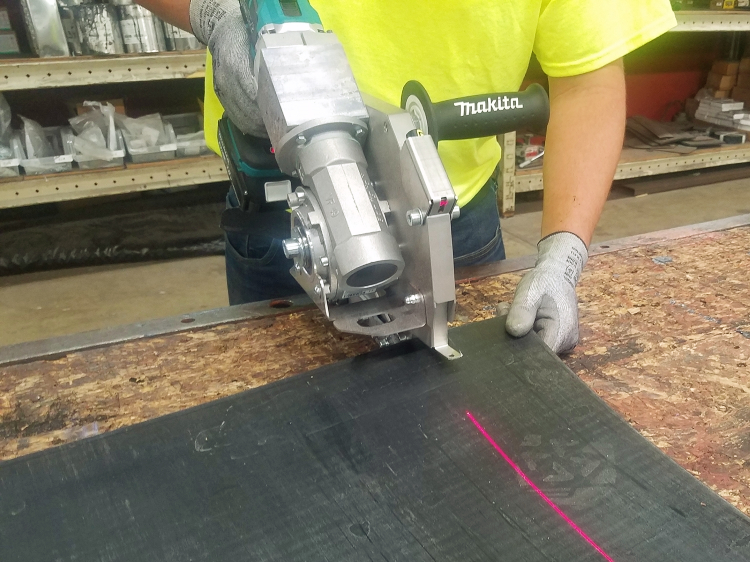
Advantages of Cordless Conveyor Belt Cutters
Mobility and Flexibility:
- Portability: The primary advantage of cordless conveyor belt cutters is their portability. Without the need for an electrical outlet, these cutters can be used in remote or hard-to-reach areas, making them ideal for fieldwork or on-site maintenance tasks.
- Ease of Use: The absence of cords reduces the risk of tripping hazards and allows for greater freedom of movement. This makes the cutting process smoother and safer for the operator.
Versatility:
- Multiple Environments: Cordless cutters can be used in various environments, from indoor factory floors to outdoor mining sites. This versatility ensures that they can handle diverse cutting needs across different industries.
- Different Materials: These cutters are designed to handle a wide range of belt materials, including rubber, PVC, and fabric-plied belts. Their adaptability makes them suitable for various applications, regardless of the belt type.
Efficiency:
- Quick Setup: Cordless models are easy to set up and use, reducing downtime. Operators can quickly grab the tool and start cutting without having to worry about finding a power source or dealing with extension cords.
- Time-Saving: The efficient cutting capability of cordless cutters, combined with their mobility, helps save time during maintenance and repair tasks. This efficiency translates to reduced operational disruptions and higher productivity.
Ideal Use Cases for Cordless Cutters
Field Maintenance and Repairs:
- Remote Locations: In remote locations where power sources are scarce or unavailable, cordless conveyor belt cutters are indispensable. They allow maintenance teams to perform essential cutting tasks without the need for generators or long extension cords.
- Emergency Repairs: Cordless cutters are ideal for emergency repairs where quick response times are crucial. Their portability ensures that maintenance teams can address issues promptly, minimizing downtime and production losses.
Mining and Quarrying:
- Harsh Environments: The rugged design of cordless conveyor belt cutters makes them suitable for use in harsh environments such as mines and quarries. These settings often lack easy access to power, making cordless tools a practical choice.
- On-the-Go Flexibility: The mobility offered by cordless cutters is particularly beneficial in large mining sites where belts need to be cut at different locations. Workers can move freely and make cuts as needed without being constrained by power cords.
Construction Sites:
- Versatile Application: Construction sites frequently require the cutting of conveyor belts for various applications, such as temporary conveyor setups for material handling. Cordless cutters provide the flexibility needed to perform these tasks efficiently.
- Safety and Convenience: The cordless design reduces the risk of tripping over cords and allows workers to navigate busy construction sites more safely and conveniently.
Industrial Plants:
- Routine Maintenance: In industrial plants, routine maintenance tasks often involve cutting conveyor belts. Cordless cutters streamline these tasks by eliminating the need for power outlets and extension cords, making the process more efficient.
- Space Constraints: In plants with limited space or complex layouts, cordless cutters offer the advantage of maneuverability, allowing workers to reach and cut belts in tight or confined spaces.
By addressing these key points, the detailed outline provides a comprehensive explanation of cordless conveyor belt cutters, highlighting their advantages and ideal use cases. This approach ensures a clear understanding of the benefits and applications of cordless models in various industrial settings.
Popular Models and Brands of Electric Conveyor Belt Cutters
In the realm of maintenance and repair for conveyor systems, electric conveyor belt cutters stand out for their efficiency, precision, and safety. Among the plethora of options available, two models have garnered attention for setting industry standards: the Flexco Belt Cutter and the Milwaukee Conveyor Belt Cutter. These models are celebrated for their innovative design, reliability, and ease of use, making them indispensable tools for professionals. Let’s delve into the unique features and advantages of each model and provide a comparative overview.
Flexco Belt Cutter
The Flexco Belt Cutter is renowned for its precision and durability, designed to handle the toughest conveyor belt materials with ease. It features a robust design that ensures straight, clean cuts, thereby reducing downtime and improving the efficiency of maintenance operations. Its safety features, including a guarded blade and an ergonomic design, minimize the risk of accidents during operation. The Flexco model is particularly favored in industries where conveyor belt integrity is critical to operational success.
Milwaukee Conveyor Belt Cutter
The Milwaukee Conveyor Belt Cutter is celebrated for its portability and power. As a cordless model, it offers unparalleled flexibility, allowing users to perform cuts in various locations without the need for a nearby power source. Its high-torque motor ensures quick and efficient cuts through even the most resilient materials. Safety is also a key feature of the Milwaukee cutter, with a well-designed safety mechanism to protect the user during operation.
Comparative Overview
To provide a clearer comparison between these two leading electric conveyor belt cutter models, the following table summarizes their key features and advantages:
This comparative data highlights the strengths of each electric conveyor belt cutter model, with the Flexco Belt Cutter excelling in precision and safety for critical applications, and the Milwaukee Conveyor Belt Cutter offering unmatched portability and power for a wide range of maintenance tasks. Both models embody the key features that professionals seek in electric conveyor belt cutters, making them top choices in their field.
Flexco Belt Cutter: A Closer Look at This Electric Conveyor Belt Cutter
The Flexco Belt Cutter is a standout in the realm of electric conveyor belt cutters, offering a blend of precision, durability, and safety that sets it apart from competitors. This detailed examination will delve into the specific design features and specifications that make the Flexco Belt Cutter a preferred choice for professionals, followed by an analysis of its price and overall value.
Design Features and Specifications
- Ergonomic Design: The Flexco conveyor belt engineering with the user’s comfort and safety in mind. Its ergonomic design reduces user fatigue and increases the safety of operations, making it suitable for extended use without compromising on performance.
- Precision Cutting Blade: Equipped with a high-grade, sharpenable blade, this cutter delivers clean and straight cuts across various diy conveyor belt material, ensuring a perfect edge for splicing. The blade is made from hardened steel rollers, offering durability and longevity.
- Adjustable Blade Depth: A key feature of the Flexco model is its adjustable blade depth, allowing users to set the cutting depth according to the belt thickness. This flexibility ensures that the cutter can be used across a wide range of belt types and thicknesses, from thin fabric belts to thick, reinforced rubber belting.
- Safety Guard: Safety is paramount with the Flexco Belt Cutter. It includes a robust safety guard that protects the user from the cutting blade during operation. This feature significantly reduces the risk of accidents, making it a safe choice for any environment.
- Portable and Durable Construction: The cutter’s construction features lightweight, high-strength materials that offer both portability and durability. This makes it easy to transport to various job sites while ensuring it can withstand the rigors of heavy-duty use.
Flexco Belt Cutter Price and Value Analysis
The price of the Flexco Belt Cutter varies depending on the model and specifications required for specific applications. Generally, it is positioned as a premium product within the electric conveyor belt cutter market. However, its price is justified by the value it offers in terms of efficiency, safety, and precision. The initial investment in a Flexco Belt Cutter can lead to significant savings over time, thanks to reduced downtime, fewer accidents, and the longevity of the cutter itself. Moreover, the precision cuts provided by the Flexco model can extend the life of conveyor belts by ensuring proper alignment and tension, further enhancing its overall value proposition.
The Flexco Belt Cutter stands out as a top-tier electric conveyor belt cutter, offering a combination of design features and specifications that cater to the needs of professionals seeking efficiency, safety, and precision. While its price point may be higher than some alternatives, the value it delivers through its performance and durability makes it a wise investment for those who prioritize quality and safety in their conveyor belt maintenance operations.
Pricing and Availability of Electric Conveyor Belt Cutters
The market for electric conveyor belt cutters offers a variety of options catering to different needs and budgets. Understanding the general price range, the cost difference between new and used models, and where to find these essential tools for sale is crucial for making an informed purchase decision.
General Price Range
The price of electric conveyor belt cutters can vary widely based on factors such as brand, model, features, and cutting capacity. Generally, prices can range from a few hundred dollars for basic models to several thousand dollars for high-end, industrial-grade cutters. Premium models like the Flexco Belt Cutter or the Milwaukee Conveyor Belt Cutter, known for their advanced safety features, precision, and durability, tend to be at the higher end of the price spectrum.
New vs. Used Electric Conveyor Belt Cutter Prices
Purchasing a used electric conveyor belt cutter can be a cost-effective option for businesses on a tight budget. Used cutters can be found at prices significantly lower than their new counterparts, sometimes saving buyers up to 50% of the cost. However, it’s important to carefully assess the condition of a used cutter, including its blades, safety features, and overall wear and tear, to ensure it meets your needs and safety standards.
Tips on Where to Find Electric Conveyor Belt Cutters for Sale
- Manufacturer Websites: Directly purchasing from manufacturers like Flexco or Milwaukee ensures you’re getting a genuine product with a warranty. Their websites often list authorized dealers and current models available.
- Industrial Supply Stores: Retailers specializing in industrial equipment typically carry a range of electric conveyor belt cutters. Stores such as Grainger, MSC Industrial Supply, and Fastenal offer both in-person and online shopping options.
- Online Marketplaces: Websites like eBay, Amazon, and Alibaba feature both new and used electric conveyor belt cutters. They provide a broad selection from various sellers, allowing for price comparison and access to customer reviews.
- Auctions and Liquidation Sales: Industrial auctions and liquidation sales can be excellent sources for finding high-quality, used electric conveyor belt cutters at reduced prices. Websites like Ritchie Bros. Auctioneers and Industrial Auctions often list such equipment.
- Trade Shows and Conferences: Attending industry-specific trade shows and conferences can provide opportunities to see the latest electric conveyor belt cutter models in action, negotiate deals, and even purchase models at discounted show prices.
The pricing and availability of electric conveyor belt cutters vary widely, with options suitable for every budget and need. Whether opting for a new, high-end model for its reliability and warranty or a used cutter for its cost savings, numerous avenues are available for purchasing these essential maintenance tools.
Choosing the Best Electric Conveyor Belt Cutter
Selecting the right electric conveyor belt cutter is crucial for ensuring efficient, safe, and precise cuts, which directly impact the operational efficiency and longevity of conveyor systems. When in the market for an electric belt cutter, several factors should guide your decision to ensure that the tool meets your specific needs. Here are five critical considerations:
- Type of Belts to Be Cut: The material composition and conveyor belt thickness are paramount considerations. Whether you’re cutting rubber conveyor belts, fabric-reinforced belts, or steel-cord belts, the cutter you choose must be capable of handling the specific material without compromising on cut quality. Some cutters are specifically designed for tougher materials, offering higher torque and specialized blades.
- Frequency of Use and Durability Requirements: Assess how often the cutter will be used. For high-volume operations requiring frequent cuts, a cutter designed for heavy-duty use with robust construction and long-lasting blades is essential. Durability ensures the cutter can withstand the rigors of frequent use, reducing the need for replacements and repairs.
- Budget and Cost-Effectiveness: While budget constraints are a reality for many operations, investing in a high-quality electric conveyor belt cutter can be more cost-effective in the long run. Cheaper models may save upfront costs but can lead to higher expenses over time due to replacements, repairs, and inefficient operation. Consider the total cost of ownership, including maintenance and operational efficiency, when making your decision.
- Safety Features: Operator safety should never be compromised. Look for cutters with built-in safety features such as blade guards, emergency stop functions, and ergonomic designs that minimize the risk of accidents during operation. A safe working environment is paramount, and the right equipment plays a crucial role in ensuring it.
- Portability and Ease of Use: In many cases, conveyor belt maintenance needs to be performed in situ, making portability a valuable feature. Cordless models offer the flexibility to work in various locations without worrying about power sources. Additionally, cutters that are easy to set up and operate can significantly reduce downtime and increase productivity.
Recommendations for the Best Electric Conveyor Belt Cutter Based on Use Case
- For Heavy-Duty, Frequent Use: Opt for a model like the Flexco Belt Cutter, known for its durability and ability to handle a wide range of belt materials and thicknesses. Its robust design and precision cutting capabilities make it ideal for operations that require frequent, high-volume cutting.
- For Varied Material Types: If you’re dealing with different types of conveyor belts, a versatile cutter like the Milwaukee Conveyor Belt Cutter offers the flexibility to adjust to various materials and thicknesses, ensuring clean and precise cuts across the board.
- For Budget-Conscious Operations: For those who need quality and efficiency without the high price tag, consider models that offer a good balance between cost and functionality. Look for cutters with solid construction and essential safety features that don’t compromise on performance.
Choosing the best electric conveyor cutter involves balancing these considerations to find a model that meets your operational needs, safety standards, and budget. By focusing on these key factors, you can ensure that your investment enhances your maintenance capabilities and contributes to the overall efficiency and safety of your conveyor system operations.
Industrial Applications and User Experiences – Electric Conveyor Belt Cutter
Electric conveyor belt cutters have become an indispensable conveyor belt cutter tool in various industries due to their efficiency, precision, and ease of use. Here are five specific examples of industries that greatly benefit from the use of electric conveyor belt cutters:
- Mining Industry: In the mining industry, electric conveyor belt cutters are widely used for accurately and quickly cutting conveyor belts to the desired length. This helps in the seamless operation of conveyor systems, optimizing the transportation of materials and increasing overall productivity.
- Manufacturing Industry: Electric conveyor belt cutters find extensive applications in the manufacturing industry, where conveyor belts are commonly used for material handling. These cutters enable precise cutting of belts for conveyor system maintenance, minimizing downtime and ensuring smooth operations.
- Logistics and Warehousing: Electric conveyor belt cutters are essential in logistics and warehousing industries to handle and maintain conveyor systems. They facilitate the cutting and splicing of conveyor belts, allowing for seamless material flow, preventing disruptions, and ensuring efficient operations.
- Packaging Industry: The packaging industry heavily relies on conveyor belts to transport packages efficiently. Electric conveyor belt cutters play a crucial role in this sector by assisting in the precise cutting of belts needed for packaging line maintenance and optimization. This ensures a streamlined production process and high-quality packaging.
- Agriculture Industry: Electric conveyor belt cutters also find applications in the agriculture industry, primarily in agricultural processing plants. These cutters help in maintaining and repairing conveyor belts used for crops, facilitating smooth transportation and processing of agricultural produce.
Aside from the industrial applications, let’s take a look at some user testimonials and feedback on specific models of electric conveyor belt cutters:
- Flexco Electric Belt Cutter: “The Flexco electric conveyor belt cutter has been a game-changer for our mining operations. It provides precise and effortless cutting, saving us significant time and improving our overall efficiency.” – John, Mining Industry.
- Milwaukee Electric Belt Cutter: “We have been using the Milwaukee electric conveyor belt cutter in our manufacturing facility for the past year, and it has surpassed our expectations. The cutter is user-friendly and has greatly increased our productivity.” – Sarah, Manufacturing Industry.
- Flexco Electric Belt Cutter: “We rely on the Flexco electric conveyor belt cutter in our logistics and warehousing operations. Its accuracy and durability have helped us maintain the conveyor systems effectively, ensuring uninterrupted material flow.” – Mark, Logistics Industry.
- Milwaukee Electric Belt Cutter: “The Milwaukee electric conveyor belt cutter has been a valuable addition to our packaging line. It enables us to swiftly cut and maintain conveyor belts, ensuring smooth operations and minimal downtime.” – Rachel, Packaging Industry.
- Flexco Electric Belt Cutter: “We utilize the Flexco electric conveyor belt cutter in our agricultural processing plant. It has significantly improved our workflow, allowing us to easily cut and repair belts, optimizing our agricultural production process.” – Andrew, Agriculture Industry.
Electric Conveyor Belt Cutter Maintenance and Safety Tips
Importance of Regular Maintenance to Ensure Longevity and Performance:
- Prolonged Lifespan: Regular maintenance of electric conveyor belt cutters is crucial to extend their lifespan. Proper care and timely servicing prevent wear and tear, ensuring that the conveyor belt cutting tool remains functional and reliable for a longer period.
- Consistent Performance: Maintenance ensures that the cutter operates at peak efficiency. Well-maintained cutters provide precise and clean cuts, which is essential for maintaining the quality of the conveyor belts and the overall system performance.
- Preventive Care: Routine maintenance helps identify potential issues before they become major problems. This proactive approach minimizes the risk of unexpected breakdowns and costly repairs.
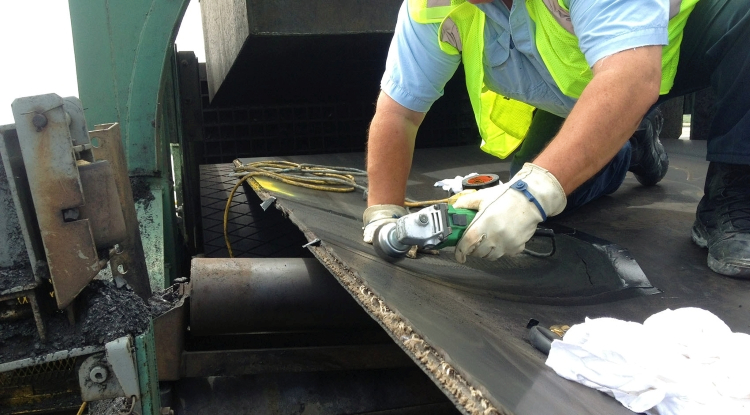
Tips for Maintaining Electric Conveyor Belt Cutters
Regular Cleaning:
- Remove Debris: After each use, clean the cutter to remove any debris, dust, or residue from the blade and motor housing. Accumulated debris can hinder the cutter’s performance and cause damage over time.
- Blade Maintenance: Ensure that the blade is clean and sharp. Dull blades require more force to cut and can result in uneven or jagged edges. Regularly inspect the blade for sharpness and replace it if necessary.
Lubrication:
- Moving Parts: Lubricate the moving parts of the cutter, such as the blade mechanism and motor bearings, to reduce friction and wear. Use manufacturer-recommended lubricants to ensure compatibility and effectiveness.
Battery Care (For Cordless Models):
- Charge Management: Follow proper charging practices to maintain battery health. Avoid overcharging and deep discharging to prolong battery life. Store batteries in a cool, dry place when not in use.
- Inspection: Regularly inspect the battery for any signs of damage or wear. Replace the battery if it shows signs of swelling, leakage, or reduced performance.
Electrical Components:
- Check Connections: Periodically check the electrical connections and wiring for any signs of damage or looseness. Secure any loose connections and replace damaged wires to ensure safe operation.
- Motor Maintenance: Inspect the motor for signs of overheating or unusual noises. If the motor shows signs of malfunction, consult the manufacturer or a qualified technician for servicing.
Safety Precautions:
- Essential Safety Measures to Follow When Using Electric Cutters:
Personal Protective Equipment (PPE):
- Safety Glasses: Always wear safety glasses to protect your eyes from flying debris or sparks during cutting.
- Gloves: Use cut-resistant gloves to protect your hands from sharp edges and accidental contact with the blade.
- Hearing Protection: If the cutter produces significant noise, wear hearing protection to prevent hearing damage.
Proper Workspace:
- Clear Area: Ensure that the cutting area is clear of obstructions and debris. A clutter-free workspace reduces the risk of accidents and allows for safe maneuvering of the cutter.
- Stable Surface: Perform cutting tasks on a stable, flat surface to prevent the cutter from slipping or tipping over.
Tool Handling:
- Firm Grip: Maintain a firm grip on the cutter at all times to ensure control and prevent accidental slips.
- Controlled Cutting: Use controlled and steady movements when operating the cutter. Avoid applying excessive force, which can lead to loss of control and potential injury.
Proper Handling and Storage to Prevent Accidents:
Blade Safety:
- Blade Guard: Always use the blade guard when the cutter is not in use to protect the blade and prevent accidental contact.
- Blade Replacement: Follow the manufacturer’s instructions for safe blade replacement. Ensure that the cutter is powered off and unplugged (or the battery removed) before changing the blade.
Storage:
- Dry Environment: Store the cutter in a dry, cool place to prevent moisture damage to electrical components and the blade.
- Secure Location: Keep the cutter in a secure location, away from children and unauthorized personnel. Use a lockable cabinet or toolbox if available.
Transporting the Cutter:
- Protective Case: Use a protective case or sheath when transporting the cutter to prevent damage to the blade and motor. This also reduces the risk of accidental injury during transport.
- Battery Handling: For cordless conveyor belt cutter models, remove the battery during transport to prevent accidental activation and potential damage.
By addressing these key points, the detailed outline provides comprehensive guidance on the routine maintenance and safety precautions necessary for using electric conveyor belt cutters. This ensures that the cutters remain in optimal condition, perform efficiently, and are used safely in various industrial settings.
FAQs About Electric Conveyor Belt Cutter
When it comes to cutting conveyor belts, the choice of tool depends on the type of belt material, the precision required, and safety considerations. Electric conveyor belt cutters are widely regarded as the best tool for this task due to their efficiency, precision, and ease of use. These cutters are designed to handle various belt materials, including rubber, fabric-reinforced belts, and even steel-cord belts. Electric cutters like the Flexco Belt Cutter or the Magnum Rubber Conveyor Belt Cutter offer features such as quick and straight cuts, safety guards to protect the operator, and portability for on-site repairs. Unlike manual cutting tools, which can be labor-intensive and less accurate, electric belt cutters provide a clean, straight edge, which is crucial for the proper alignment and splicing of the belt. Additionally, the reduced physical effort and time savings make electric cutters a valuable investment for maintenance teams.
Cutting a hole in a conveyor belt requires precision to ensure the integrity and functionality of the belt are maintained. The process typically involves marking the belt where the hole is needed, using a punch or drill designed for belt material. For small holes, a heavy-duty punch can be effective, especially for fabric-reinforced belts. For larger holes or for belts with harder materials, a drill with a suitable bit or a specialized belt hole cutter may be necessary. It’s important to choose the right tool based on the belt’s material and thickness to prevent damage. After marking the center point of the hole, secure the belt to prevent movement and carefully begin the cutting process. If using a drill, proceed slowly to ensure a clean cut. Always wear appropriate safety gear, such as gloves and eye protection, to avoid injuries from sharp tools or flying debris.
Measuring and cutting a conveyor belt accurately is crucial for the belt’s performance and longevity. To measure a conveyor belt, first, determine the length required based on the conveyor’s specifications or the damaged section that needs replacement. Use a flexible measuring tape to measure the distance accurately, considering any belt tension adjustments that may affect the length. Mark the cutting line clearly on the belt using a straight edge to ensure the cut will be straight, as an uneven cut can lead to tracking problems and premature wear.
For cutting, an electric conveyor belt cutter is recommended for its precision and ease of use. Before cutting, ensure the belt is tensioned correctly and supported to prevent it from moving. Align the cutter along the marked line, and proceed with the cut, ensuring your hands and any loose clothing are clear of the cutting blade. After cutting, inspect the edge to ensure it is straight and smooth, ready for splicing or installation.
Rolling a conveyor belt by hand is a manual process that requires careful handling to avoid damage to the belt and ensure it can be stored or transported safely. Start by laying the belt flat on the ground or a large working surface. If the belt is long, you may need assistance to handle it properly. Begin at one end of the belt, folding it over in small sections, approximately 1 to 2 feet wide, depending on the belt’s thickness and rigidity. Continue folding the belt onto itself, applying even pressure to avoid twisting or pinching the material.
For longer belts, it may be helpful to walk backwards as you roll, guiding the belt into a tight roll. Secure the rolled belt with straps or ropes to keep it from unrolling during storage or transport. It’s important to handle the belt gently throughout the process to prevent creases or damage, especially to the edges, which could affect the belt’s performance when unrolled and installed.
The best way to cut a conveyor belt involves using the right tools and following specific procedures to ensure precision, safety, and efficiency. For most applications, an electric conveyor belt cutter is highly recommended due to its power and precision. Here are the steps to effectively cut a conveyor belt:
Measure and Mark: Accurately measure and mark the area where the cut is to be made using a measuring tape and a marker. Ensuring precise measurements is crucial for the belt’s performance and fit.
Secure the Belt: Place the belt on a stable surface and secure it to prevent movement during cutting. This can be done using clamps.
Select the Right Cutter: An electric cutter is preferred for its ease of use and efficiency. Cordless models provide mobility, while corded models are suitable for stationary tasks.
Set the Cutter: Adjust the blade depth and angle according to the thickness and type of the conveyor belt. Ensure the blade is sharp and properly installed.
Cut with Control: Power on the cutter and make a steady, controlled cut along the marked line. Use a guide rail if necessary to maintain a straight line.
Inspect the Cut: Check the cut edges for smoothness and uniformity. Clean any debris or rough edges with a trimming tool if needed.
Safety Measures: Always wear appropriate personal protective equipment (PPE), such as safety glasses and cut-resistant gloves, to protect against injuries during the cutting process.
Using these steps ensures a clean, precise cut, maintaining the integrity of the conveyor belt and enhancing its operational efficiency.
Yes, I have extensive knowledge of conveyor belts, which are crucial components in various industries for material handling and transport. Conveyor belts are continuous loops made of flexible material that move materials from one point to another. Here are some key points about conveyor belts:
Flat Belts: Commonly used in manufacturing and warehousing, flat belts are simple, efficient, and ideal for transporting items on a flat surface.
Modular Belts: Made from interlocking plastic pieces, these belts are versatile and can be customized for specific needs, such as curved paths or easy cleaning.
Cleated Belts: Equipped with raised sections (cleats) to prevent material from sliding off, these belts are ideal for transporting items up steep inclines.
Rubber: Durable and flexible, rubber belts are suitable for heavy-duty applications and can handle abrasive materials.
PVC: Lightweight and resistant to chemicals, PVC belts are often used in food processing and packaging industries.
Fabric Ply: These belts consist of multiple layers of fabric for added strength and flexibility, commonly used in mining and bulk material handling.
Manufacturing: Conveyor belts streamline assembly lines and automate material handling, increasing productivity and efficiency.
Mining: Heavy-duty belts transport raw materials such as coal and ores from mines to processing facilities.
Food Processing: Hygienic belts, resistant to oils and fats, are essential for safe and efficient food handling.
Regular Inspection: Routine checks for wear, tear, and misalignment ensure the belt runs smoothly and reduces downtime.
Proper Tensioning: Maintaining the correct tension prevents slippage and prolongs the belt’s lifespan.
Cleaning: Regular cleaning prevents contamination and buildup of materials, which can cause operational issues.
Conveyor belts are integral to efficient material handling systems, and understanding their types, applications, and maintenance can significantly enhance their performance and longevity in various industrial settings.
Last Updated on May 29, 2024 by Jordan Smith
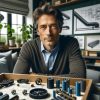
Jordan Smith, a seasoned professional with over 20 years of experience in the conveyor system industry. Jordan’s expertise lies in providing comprehensive solutions for conveyor rollers, belts, and accessories, catering to a wide range of industrial needs. From initial design and configuration to installation and meticulous troubleshooting, Jordan is adept at handling all aspects of conveyor system management. Whether you’re looking to upgrade your production line with efficient conveyor belts, require custom conveyor rollers for specific operations, or need expert advice on selecting the right conveyor accessories for your facility, Jordan is your reliable consultant. For any inquiries or assistance with conveyor system optimization, Jordan is available to share his wealth of knowledge and experience. Feel free to reach out at any time for professional guidance on all matters related to conveyor rollers, belts, and accessories.