Innovations in Elevator Conveyor Belt Material Technology
Elevator conveyor belts play a crucial role in numerous industries, facilitating the vertical transportation of materials in bulk. This process is vital in sectors such as agriculture, mining, and construction, where efficiency and safety are paramount. The choice of elevator conveyor belt material directly impacts the operational efficiency and longevity of the system. Various materials are employed in the production of these belts, including rubber, fabric composites, and steel reinforcements. Each material is selected based on its durability, flexibility, and resistance to environmental factors, ensuring optimal performance tailored to specific industrial needs.
Types of Elevator Conveyor Belt Material
Elevator conveyor belts are critical components in many industrial sectors, enabling efficient vertical transportation of bulk materials. The choice of material for these belts depends on various factors including the weight of the materials, environmental conditions, and the specific needs of the industry. With advancements in material science, elevator conveyor belts are now more durable, efficient, and suitable for a wider range of applications than ever before. This section explores three primary types of elevator conveyor belt material, each catering to different industrial requirements and offering unique benefits.
Polyester/Polyamide (Polysur Belts)
Polyester and polyamide, commonly known as Polysur belts, are renowned for their strength and durability, making them ideal for a variety of industrial applications. Here are nine key aspects of these materials:
- Tensile Strength: Exceptionally high tensile strength to withstand significant operational loads without stretching or breaking.
- Chemical Resistance: Resistant to chemicals, making them suitable for industries dealing with corrosive materials.
- Low Elongation: Minimal elongation at working load, which ensures stable and precise lifting operations.
- Thermal Stability: Performs well in varying temperatures, maintaining integrity in both hot and cold environments.
- Wear Resistance: High wear resistance enhances longevity and reduces maintenance costs.
- Flexibility: Despite their strength, these belts remain flexible, facilitating smoother operations over pulleys and within confined spaces.
- Moisture Resistance: Resists moisture, preventing degradation and maintaining performance in damp or wet conditions.
- UV Resistance: The material is UV resistant, which is crucial for outdoor applications where UV exposure is frequent.
- Eco-Friendly Options: Some Polysur belts are made with eco-friendly materials, catering to industries aiming for sustainability.
Steel Fabric Reinforced Belts
Steel fabric reinforced belts are essential for heavy-duty applications and environments with high temperatures. Here are nine points detailing their importance:
- High Load Capacity: Designed to handle very high loads, ideal for heavy industrial use.
- Superior Durability: Steel reinforcement provides outstanding durability and longevity.
- Heat Resistance: Capable of withstanding high temperatures, suitable for industries like cement manufacturing and metal processing.
- Cut and Gouge Resistance: Highly resistant to cuts and gouges, protecting the belt from sharp materials.
- Low Stretch: Steel cords reduce belt stretch, essential for precise vertical movements.
- Impact Resistance: Excellent impact resistance helps in handling large, heavy materials without damage.
- Fire Resistance: Often designed to be fire-resistant, a necessary feature in industries with high fire risk.
- Corrosion Resistance: Coated steel materials prevent rust and corrosion, enhancing the belt’s lifespan.
- Energy Efficiency: Steel belts can be more energy-efficient due to their ability to carry more load with less belt material.
Rubber Types (NBR, SBR)
Rubber conveyor belts, particularly NBR (Nitrile Butadiene Rubber) and SBR (Styrene Butadiene Rubber), are chosen for their diverse qualities, including oil and fat resistance, which are beneficial in food processing and agricultural sectors. Here are nine detailed aspects:
- Oil Resistance: NBR belts are highly resistant to oils, fats, and greases, making them ideal for the food industry.
- Temperature Flexibility: SBR belts can operate effectively in temperatures ranging from -30°C to +70°C.
- Abrasion Resistance: Excellent abrasion resistance, prolonging the service life in rough industrial environments.
- Elasticity: Good elasticity helps in absorbing shocks and impacts during operations.
- Fat Resistance: Prevents degradation from animal fats and vegetable oils, essential in agri-food sectors.
- Hygienic Standards: Complies with food safety standards, ensuring that the belts do not contaminate food products.
- Customization: Available in various hardness and compound formulations to suit specific application needs.
- Cost-Effective: Generally more cost-effective than synthetic alternatives, providing a balance between performance and expense.
- Recyclability: Rubber belts can be recycled at the end of their lifecycle, supporting environmental sustainability efforts.
Each type of elevator conveyor belt material offers unique properties tailored to specific industrial needs, ensuring efficient and reliable vertical transportation of materials.
Suppliers and Manufacturers of Elevator Conveyor Belt Material
The global market for elevator conveyor belt material is diverse, featuring several key players who specialize in the production and innovation of these essential components. This section highlights seven leading manufacturers of elevator conveyor belts, detailing what sets each apart in this competitive landscape.
Key Manufacturers
The manufacturing landscape of elevator conveyor belt material is diverse, comprising various companies that bring unique innovations and specialized products to the industry. These manufacturers not only supply the necessary materials for constructing elevator systems but also drive technological advancements and sustainability in their offerings. Below, we explore in detail some of the key players in the market, highlighting their unique contributions and specializations that set them apart in the field of elevator conveyor belts.
- Muller Beltex: Known for their Polysur® belts, Muller Beltex excels in providing highly durable belts that are tailor-made for specific industrial needs.
- Braime Elevator Buckets: A leader in bucket attachment technology, Braime also offers high-quality elevator belts that are compatible with their advanced bucket designs.
- ContiTech AG: This company offers a wide range of rubber and synthetic belts, known for their durability and adaptability to different environmental conditions.
- Fenner Dunlop: Specializing in heavyweight belting, Fenner Dunlop manufactures products that are ideal for mining and aggregates, ensuring high tensile strength and optimal abrasion resistance.
- Yokohama Rubber: They are pioneers in steel cord belts, which are crucial for high-capacity lifting and offer superior durability under strenuous conditions.
- Habasit: Habasit is renowned for their innovation in belt manufacturing, particularly in the food and packaging industries, where hygiene and precision are crucial.
- Derco Gypsum: This brand is a part of the Bridgestone Group and specializes in belts for building materials, providing unique solutions like fire-resistant and high-temperature belts.
Global Supply Chain Dynamics
The production and distribution of elevator conveyor belt material are influenced by several factors in the global supply chain:
- Raw Material Availability: Fluctuations in the availability of natural rubber or synthetic materials can significantly impact production rates and costs.
- Manufacturing Regulations: Changes in environmental and safety regulations in manufacturing countries can affect how belts are produced and what materials are permissible.
- Trade Policies: Tariffs and trade barriers can alter the cost structures, influencing how competitively companies can price their products internationally.
- Technological Advancements: Innovations in materials science often lead to improved product offerings, pushing companies to continuously adapt and innovate.
- Logistics and Transportation: The efficiency of global logistics networks affects the timely delivery of materials, impacting overall project timelines in industries reliant on these belts.
- Market Demand: Economic shifts in key industries like mining, agriculture, and construction can sway demand for elevator belts, prompting manufacturers to adjust production volumes.
- Sustainability Initiatives: Increasing emphasis on sustainability is driving manufacturers to invest in eco-friendly materials and processes, shaping the future landscape of the industry.
- Supplier Relationships: Long-term collaborations between belt manufacturers and raw material suppliers are crucial for maintaining quality and securing stable material supplies.
Understanding these dynamics is essential for stakeholders in the elevator conveyor belt material industry, as they navigate the complexities of global manufacturing and distribution to meet the evolving needs of their clients.
Specifications and Selection Criteria for Elevator Conveyor Belt Material
Selecting the right elevator conveyor belt material involves considering various specifications and factors that impact its performance and cost. This section explores the critical specifications and selection criteria for elevator belts, focusing on bucket elevator belt specifications, factors affecting elevator belt prices, and essential components of bucket elevator systems.
Bucket Elevator Belt Specification
When specifying elevator conveyor belt material, several key parameters must be considered to ensure optimal performance and durability:
- Tensile Strength: Measures the maximum load that a belt can handle without breaking; crucial for determining the belt’s capacity to carry heavy loads.
- Width: The belt width should be chosen based on the volume of material to be transported.
- Thickness: Thickness affects the durability and wear resistance of the belt.
- Belt Speed: Determines how fast materials are moved; needs to be compatible with system throughput requirements.
- Elongation: Minimal elongation is desirable to maintain stable bucket spacing and consistent elevator operation.
- Abrasion Resistance: High resistance helps to extend the lifespan of the belt, especially when transporting abrasive materials.
- Flexibility: A belt must be flexible enough to wrap around the system’s pulleys without excessive strain.
Elevator Belt Price Factors
The cost of elevator conveyor belt material can be influenced by multiple factors, each contributing to the overall investment and operational costs:
- Material Quality: Higher quality materials may cost more upfront but typically offer better durability and longer life.
- Customization: Specific features such as reinforced edges or custom widths and thicknesses can increase the price.
- Supply Chain Costs: Fluctuations in raw material availability and transportation costs can affect final pricing.
- Volume of Purchase: Buying in bulk often results in lower per unit costs due to economies of scale.
- Technological Features: Advanced features like integrated sensors for monitoring wear and tear can add to the cost.
- Market Demand: High demand for certain types of belts can drive up prices temporarily.
- Regulatory Compliance: Belts that need to meet specific regulatory standards for safety and environmental impact may cost more.
- Economic Conditions: General economic conditions can affect material costs and manufacturing expenses.
Bucket Elevator Parts
Essential components of a bucket elevator system include several critical parts that ensure efficient and safe operation:
- Buckets: Attach directly to the belt to carry the material; must be matched to the belt in terms of size and weight capacity.
- Head and Boot Pulley: These are key to driving the belt and controlling its tension.
- Drive System: Includes motors and gear reducers that provide the necessary power to move the belt.
- Bearing Assemblies: Ensure smooth operation of the pulleys and drive system.
- Inspection Doors: Allow for easy access to internal components for maintenance and troubleshooting.
- Casing: Provides a protective enclosure for the moving belt and material, enhancing safety and containing dust.
- Spouting: Directs the flow of discharged material to specific locations.
- Backstops: Prevent the belt from running backwards in the event of a power failure.
Each of these components plays a vital role in the operation of an elevator conveyor belt material system, contributing to its efficiency, safety, and longevity.
Purchasing and Using Recycled Elevator Conveyor Belt Material
Recycling and repurposing elevator conveyor belt material are becoming increasingly important in sustainable industrial practices. This section details how used materials contribute to environmental sustainability and how companies can achieve cost efficiency through refurbishment and repurposing strategies.
The Role of Used Elevator Conveyor Belt Materials in Sustainable Practices
Utilizing used elevator conveyor belt material in sustainable practices is an impactful way to address environmental concerns within the industry. Repurposing these materials not only mitigates waste but also reduces the demand for virgin resources, supporting a more sustainable production cycle. Here, we explore in-depth how these practices contribute to environmental conservation and support a green business ethos.
- Reducing Waste: By reusing materials, industries reduce the volume of waste sent to landfills.
- Lowering Carbon Footprint: Repurposing belts minimizes the carbon emissions associated with producing new materials from scratch.
- Conserving Resources: Recycling conserves raw materials such as rubber, steel, and polyester, which are finite and require significant energy to process.
- Energy Efficiency: It requires less energy to refurbish and reuse conveyor materials than to manufacture new ones, leading to energy savings.
- Supporting Circular Economy: Utilizing used belts promotes a circular economy, where materials are kept in use for as long as possible.
- Enhancing Corporate Responsibility: Companies adopting recycling practices improve their corporate social responsibility (CSR) profiles, appealing to eco-conscious consumers and stakeholders.
- Reducing Manufacturing Costs: Lower raw material costs through recycling can reduce overall manufacturing expenses.
- Innovating New Products: Recycled elevator conveyor belt material can be transformed into innovative products, creating new business opportunities within and beyond the original industry.
How Companies Refurbish or Repurpose Used Materials for Cost Efficiency
Companies are increasingly finding innovative ways to refurbish and repurpose used elevator conveyor belt material, achieving significant cost savings while maintaining operational efficiency. This section details the processes and strategies that enhance the lifecycle of these materials and reduce overall expenses.
- Inspection and Sorting: Used belts are thoroughly inspected and sorted based on their condition and potential for reuse.
- Cleaning Processes: Belts are cleaned to remove debris and contaminants that could compromise their quality and functionality.
- Repair Techniques: Damaged sections of belts can be repaired using specialized patching methods, ensuring they meet safety and performance standards.
- Recoating: Belts that have worn surfaces can be recoated with rubber or other materials to restore their grip and protective qualities.
- Cutting to Size: Materials can be cut into smaller sizes for different uses, such as protective mats or parts for smaller machinery.
- Integration into New Products: Repurposed elevator conveyor belt material can be integrated into new products, such as flooring or vehicle mud flaps, adding value to the waste.
- Selling Refurbished Belts: Refurbished belts can be sold at a lower cost to industries not requiring top-grade materials, such as agriculture or construction.
- Collaborative Exchange Programs: Companies can establish exchange programs where used belts can be returned, refurbished, and resold, creating a continuous cycle of use.
By adopting these strategies, companies not only enhance their operational cost efficiency but also contribute significantly to environmental conservation. The repurposing of elevator conveyor belt material embodies a commitment to sustainable practices that benefit both the planet and the bottom line.
Customization and Innovation in Elevator Conveyor Belt Material
The elevator conveyor belt material industry continually evolves, driven by customization and technological innovations that enhance performance and adaptability to diverse industrial needs. This section explores the unique custom features that manufacturers offer and the advances in material technology that significantly improve the functionality and efficiency of elevator belts.
Custom Features Offered by Manufacturers
Manufacturers of elevator conveyor belt material provide a variety of custom options that enable precise adaptation to specific operational requirements:
- Bolt Holes for Buckets: Precisely drilled bolt holes ensure secure attachment of buckets to the belt, tailored to specific spacing and alignment requirements.
- Special Coatings: Coatings such as abrasion-resistant and anti-static materials enhance belt longevity and safety.
- Edge Reinforcements: Added reinforcements along the edges of the belts prevent fraying and damage under heavy use.
- Cleats and Guides: Integrated cleats and guides help maintain material stability on the belt, preventing slippage and aiding in inclined or vertical transport.
- Variable Belt Widths and Thicknesses: Custom belt sizes are available to accommodate different volumes and weights of materials being transported.
- Antimicrobial and Food-Grade Coatings: For belts used in the food processing industry, coatings that resist bacterial growth and comply with health standards are essential.
- Temperature-Resistant Materials: Belts designed to withstand extreme temperatures, suitable for applications in high-heat environments such as foundries or cold storage facilities.
- Impact Zones: Specialized materials in areas of high impact improve durability where the belt interfaces with loading zones.
Advances in Material Technology and Performance Enhancement
Technological advances in elevator conveyor belt material have led to significant improvements in belt performance across various metrics:
- High-Tensile Materials: Development of materials with higher tensile strength allows belts to handle greater loads without stretching or breaking.
- Wear-Resistant Technologies: New compounds and weaving techniques have increased the abrasion resistance of belts, extending their operational life.
- Energy Efficiency: Innovations in belt design reduce the energy consumption of conveyor systems by minimizing friction and improving load distribution.
- Environmental Resistance: Advances in chemical engineering have resulted in materials that are more resistant to oils, chemicals, and other corrosive substances.
- Reduced Maintenance Needs: New materials and intelligent designs decrease the need for frequent maintenance, lowering operational costs.
- Smart Belting Technologies: Integration of sensors and IoT technologies into belt systems allows for real-time monitoring of wear and operational conditions, facilitating predictive maintenance.
- Improved Safety Features: Enhanced safety measures, such as fire-retardant and anti-static properties, increase the safety of operations, particularly in hazardous environments.
- Lightweight Materials: The development of lighter materials that maintain strength and durability helps to reduce the load on conveyor systems and increase efficiency.
These innovations and custom features in elevator conveyor belt material design and manufacturing not only enhance the operational capabilities of conveyor systems but also contribute to broader goals of safety, efficiency, and sustainability in material handling.
Case Studies and Applications of Elevator Conveyor Belt Material
The use of elevator conveyor belt material plays a pivotal role in enhancing operational efficiency and safety across various industries. This section delves into several real-world case studies where innovative materials have significantly improved performance and explores the diverse industries that benefit from these advancements.
Real-World Case Studies
The deployment of elevator conveyor belt material in various industries provides a wealth of real-world applications that showcase significant enhancements in efficiency and safety. By examining specific case studies, we gain insights into how different materials and technologies are tailored to meet unique industry challenges and improve operational outcomes. These studies not only demonstrate the versatility of elevator belts but also highlight their impact on reducing costs and increasing productivity in challenging environments.
- Mining Operations in South Africa: A case study involving the use of steel cord belts in a deep mine that improved load capacity by 20% while reducing maintenance costs by 30%, enhancing both efficiency and safety.
- Agricultural Product Handling in the USA: Polysur polyester belts were implemented to handle grains, resulting in a 50% reduction in belt slippage and a 25% increase in conveyor uptime.
- Pharmaceutical Production in Germany: Introduction of antimicrobial belts in the production line reduced contamination risks and increased compliance with stringent health standards.
- Cement Manufacturing in India: Heat-resistant belts were used to manage clinker handling, withstanding temperatures over 200°C, which extended belt life and reduced fire hazards.
- Food Processing in Brazil: Food-grade belts with FDA-approved coatings improved hygiene and product safety in a meat processing plant, reducing cross-contamination incidents.
- Recycling Facility in Japan: Implementation of high-abrasion-resistant rubber belts allowed for more efficient recycling processes, with a notable decrease in operational downtime.
- Logistics and Warehousing in the Netherlands: Use of energy-efficient flat belts in automated sorting systems increased throughput by 15% and reduced energy consumption by 10%.
Industries Relying on Elevator Conveyor Belt Material
Elevator conveyor belt material is integral to the functioning of multiple sectors, each with distinct requirements and challenges. The following outlines the critical roles these materials play across diverse industries, underscoring their importance in supporting global industrial operations.
- Mining: Belts designed for high tensile strength and abrasion resistance to carry ores from deep underground to the surface.
- Agriculture: Belts that handle large volumes of agricultural products, often designed to resist moisture and minimize spoilage.
- Manufacturing: Diverse applications from automotive to electronics, where precision and durability of belts are crucial for assembly lines.
- Construction: Heavy-duty belts used for moving large quantities of materials like sand, gravel, and cement on construction sites.
- Food Processing: Belts that comply with food safety standards to prevent contamination and ensure the integrity of food products.
- Pharmaceuticals: Highly regulated belts that are easy to clean and resist chemical corrosion for sensitive drug manufacturing processes.
- Recycling: Durable belts capable of handling sharp and rough recycled materials without extensive wear.
- Packaging: Belts that support high-speed and precise movements needed in packaging facilities to enhance efficiency and reduce packaging time.
Each of these case studies and industry applications highlights the critical role of elevator conveyor belt material in not only improving efficiency and safety but also in contributing to cost savings and environmental sustainability through enhanced material handling solutions.
FAQs about Elevator Conveyor Belt Material
Elevator belts, a key component in the vertical transportation of materials, are typically made from robust materials that can withstand significant wear and tear. The most common material used for elevator belts is rubber because of its flexibility, durability, and ability to handle various environmental conditions. Rubber may be reinforced with fabrics such as polyester or nylon to enhance strength and stability. For more demanding applications, especially where high tensile strength is required, belts may incorporate steel cords. Steel reinforced belts are particularly suited for applications involving high lift heights and heavy loads. Other materials such as PVC and polyurethane are also used depending on the specific requirements of the operation, including food-grade belts that meet regulatory standards for cleanliness and non-contamination.
Conveyor belts are crafted from multiple layers of different materials, depending on their intended function. The core material is usually a fabric like polyester, nylon, or cotton, providing structural integrity and shape. This core is often coated or covered with rubber, PVC, or polyurethane to protect against environmental factors such as abrasion, chemicals, and temperature extremes. Rubber belts are common in general use due to their durability and flexibility, whereas PVC conveyor belts are favored in industries requiring a high degree of hygiene, like food processing. Polyurethane belts are used when excellent chemical resistance and cleanliness are necessary. High-performance applications might use specialized materials like Kevlar or other aramid fibers for enhanced strength and heat resistance.
Conveyors employ a variety of materials tailored to their specific usage and the conditions under which they operate. Common materials include rubber, PVC, polyurethane, and metals such as steel or stainless steel. Rubber is widely used for general purpose belts due to its resilience and flexibility. PVC offers excellent resistance to chemicals, oils, and weather, making it suitable for both indoor and outdoor applications. Polyurethane is prized for its hygienic qualities, making it a common choice in the food and pharmaceutical industries. For the structure of conveyors, metals such as steel provide the necessary durability and strength, especially in heavy-duty applications. Each material is selected based on factors like load capacity, operational environment, cost, and the specific properties needed for the conveyor’s function.
Metal is frequently used in conveyor belts, either as a reinforcing material or as the primary substance in metal belts. Steel is the most common metal used due to its high tensile strength, durability, and resistance to tearing and deformation. Steel can be used in the form of cords that reinforce rubber or fabric belts, or as complete metal belts made of linked steel plates or mesh. Stainless steel is often used in environments that require resistance to rust and corrosion, such as in food processing or chemical industries. Other metals like aluminum are used for their lightweight properties in applications where reducing the conveyor’s overall weight is beneficial. Metal belts are particularly valued in applications requiring heat resistance, cleanability, and a high degree of precision.
Last Updated on August 16, 2024 by Jordan Smith
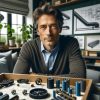
Jordan Smith, a seasoned professional with over 20 years of experience in the conveyor system industry. Jordan’s expertise lies in providing comprehensive solutions for conveyor rollers, belts, and accessories, catering to a wide range of industrial needs. From initial design and configuration to installation and meticulous troubleshooting, Jordan is adept at handling all aspects of conveyor system management. Whether you’re looking to upgrade your production line with efficient conveyor belts, require custom conveyor rollers for specific operations, or need expert advice on selecting the right conveyor accessories for your facility, Jordan is your reliable consultant. For any inquiries or assistance with conveyor system optimization, Jordan is available to share his wealth of knowledge and experience. Feel free to reach out at any time for professional guidance on all matters related to conveyor rollers, belts, and accessories.