EP Conveyor Belt Safety and Standards Overview
EP conveyor belts, short for Polyester conveyor belts, are essential components in modern material handling sectors. They are designed with polyester fibers aligned lengthwise (warp) and polyamide (nylon) fibers crosswise (weft). This combination provides a robust structure that is crucial for the durability and functionality of the belts. EP conveyor belt is celebrated for their strength, resistance to stretching, and ability to handle a variety of materials across numerous industries. From mining and agriculture to packaging and logistics, these belts play a pivotal role in enhancing operational efficiency and productivity, ensuring that materials are transported smoothly and safely over distances within the operational infrastructure.
Detailed Specifications of EP Conveyor Belt
EP conveyor belts, commonly known as polyester conveyor belts, are essential in various industries for the efficient transportation of materials. These belts are favored for their durability, strength, and versatility, adapting to different environmental conditions and operational demands. The specifications of these belts are denoted by a series of numbers and letters that explain their structural composition and intended use. Here, we will delve into the common specifications, understand the significance of the specification numbers, and explore special types of EP belts, highlighting their unique features and advantages.
Common Specifications of EP Conveyor Belt
The specification of an EP conveyor belt helps users understand its suitability for certain applications based on the belt’s strength, ply configuration, and surface material. Common specifications include EP 400/3, EP 630/4, and EP 1000/4, each designed for specific stress and environmental conditions.
- EP 400/3: Commonly used in light to medium duty applications, offering sufficient strength for bulk material handling in sectors like manufacturing and agriculture.
- EP 630/4: Better suited for higher stress environments, such as mining and recycling plants, where additional strength is necessary to handle abrasive materials.
- EP 1000/4: Optimized for very high stress and heavy load applications, including heavy mining and minerals processing where superior strength and durability are crucial.
- Variety in Ply Configuration: Multiple layers increase structural integrity and ensure the belt can withstand various operational stresses without excessive stretch.
- Adaptability to Conditions: Tailored to perform under different environmental conditions, whether dealing with wet, dry, or highly abrasive materials.
- Custom Options: Many EP belts offer options for customization in terms of width, ply number, and even cover thickness to meet specific operational needs.
- Industrial Versatility: The range of specifications available makes EP belts suitable for virtually all industrial applications, from light conveyor systems to heavy-duty transport lines.
Specification Numbers
Specification numbers on EP conveyor belts are critical in identifying the belt’s design and capabilities, providing insights into the belt’s tensile strength, ply count, and overall durability.
- Tensile Strength Indication: The first number (e.g., 400 in EP 400/3) indicates the maximum tensile strength per ply, measured in N/mm, crucial for determining the belt’s load-bearing capacity.
- Ply Count Information: The subsequent number (e.g., 3 in EP 400/3) reveals the number of fabric layers, which helps assess the belt’s impact resistance and longevity.
- Significance of Material Blend: The polyester and polyamide blend provides a balance of strength and flexibility, crucial for various conveying needs.
- Impact on Operational Efficiency: Higher tensile strength and appropriate ply count contribute to reduced operational downtime and maintenance.
- Width and Length Customization: Belts are available in different widths and lengths, providing flexibility in system design and application.
- Load Distribution Capabilities: A higher ply count allows for better load distribution across the belt surface, enhancing the conveyor system’s efficiency.
- Performance Under Stress: These specifications dictate how well the belt will perform under dynamic and static loads, impacting overall system reliability.
Special Types and Their Significance
Special types of EP conveyor belts, such as Conveyor Belt EP 400/3 4+2, are designed with specific operational challenges in mind, providing additional protection and features to extend the belt’s service life under harsh conditions.
- Enhanced Cover Thickness: The “4+2” designation indicates additional thickness on the top and bottom covers, improving resistance to abrasion and puncture.
- Targeted Application Design: These belts are engineered for environments where sharp or highly abrasive materials are present.
- Extended Lifespan: Thicker covers significantly extend the belt’s lifespan by protecting the core material from external damages.
- Specialized Uses: Ideal for sectors like construction and heavy industry, where durability under rough handling is necessary.
- Improved Safety Features: Thicker covers also mean better resistance to ripping and tearing, enhancing operational safety.
- Energy Efficiency: The added thickness can help reduce the conveyor system’s energy consumption by minimizing belt slip and deformation under load.
- Customizable Features: Customers can specify additional features like anti-static properties, fire resistance, and low-noise materials depending on their specific needs.
These detailed insights into the specifications and features of EP conveyor belts provide a deeper understanding of their role and importance in modern industry, enabling users to make informed choices based on their specific material handling requirements.
Standards and Safety in EP Conveyor Belt Specifications
Adhering to robust standards and integrating sufficient safety factors are foundational to the design and usage of EP conveyor belts. These standards not only govern the physical and mechanical properties of the belts but also ensure they are safe and reliable across various industries. This section details the prevalent standards, explains the significance of safety factors in belt design, and elucidates key terminologies like PIW and Class, which are essential for understanding and selecting the right conveyor belt.
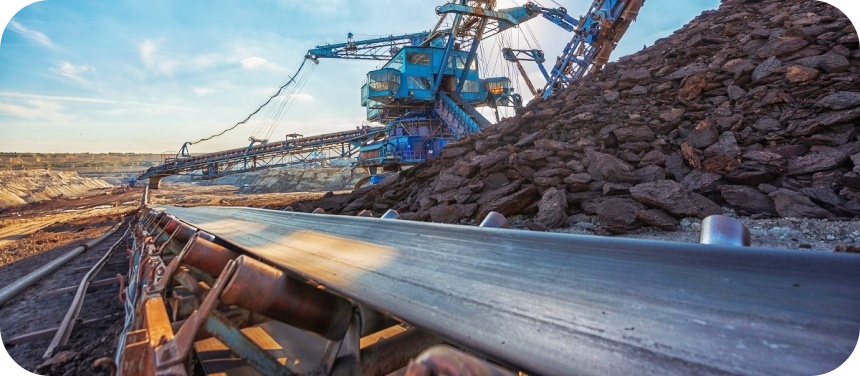
Overview of Conveyor Belt Specification Standards
Conveyor belt standards are crucial as they define the quality, safety, and performance expectations for belts used in different industrial applications. These standards are developed and maintained by various international and national bodies.
- DIN (Deutsches Institut für Normung): Focuses on ensuring that conveyor belts meet German engineering standards, renowned for their precision and reliability in industrial applications.
- ISO (International Organization for Standardization): Sets global standards to ensure consistency and safety across all countries, facilitating international trade and cooperation in conveyor belt manufacturing.
- RMA (Rubber Manufacturers Association): American standards that specify the quality and types of materials used, ensuring that the belts are durable and safe for use in a variety of American industries.
- AS (Australian Standards): Tailored to meet the rugged conditions of the Australian landscape, these standards ensure that conveyor belts can withstand harsh environments typical of the mining and agricultural sectors.
- BS (British Standards): These standards focus on safety, efficiency, and sustainability, crucial for maintaining the UK’s strict industrial safety regulations.
- JIS (Japanese Industrial Standards): Provide guidelines that ensure the high quality and durability required in Japan’s advanced manufacturing and technology sectors.
- SANS (South African National Standards): Specific to South Africa’s extensive mining and industrial sector, focusing on high performance and safety under extreme conditions.
Importance of Safety Factors in EP Conveyor Belt Design
Safety factors in conveyor belt design are critical for ensuring the belt can handle expected and unexpected stresses throughout its operational life.
- Design Margin: Safety factors provide a design margin that accounts for possible miscalculations or unexpected operational conditions, ensuring the belt remains functional and safe under various loads.
- Risk Management: Incorporating adequate safety factors helps in managing risks associated with belt failure, which can lead to operational downtime and hazardous situations.
- Durability Enhancement: By considering higher safety factors, manufacturers ensure that the belt can withstand wear and tear for longer periods, enhancing its durability and reliability.
- Environmental Adaptability: Safety factors allow belts to perform reliably in different environmental conditions, whether they are exposed to extreme temperatures, moisture, or abrasive materials.
- Regulatory Compliance: Adhering to the safety factors recommended by various standards helps companies meet legal safety requirements, avoiding penalties and ensuring worker safety.
- Economic Impact: While higher safety factors may increase initial costs, they significantly reduce long-term expenses related to maintenance, replacements, and potential accidents.
Explanation of Terms like Conveyor Belt PIW and Class
Terms such as PIW (Pounds per Inch of Width) and Class are integral to understanding the technical specifications and capabilities of EP conveyor belts. These terms help in assessing the suitability of a belt for specific applications.
- PIW – Pounds per Inch of Width: Indicates the maximum load that the belt can support per inch of its width, crucial for sizing and strength considerations.
- Class of Belt: Refers to specific categories of belts that are designed for particular environments or materials, such as heat-resistant or oil-resistant.
- Tension Rating: Expressed alongside PIW to indicate how much tension the belt can handle without compromising its structural integrity.
- Application Suitability: Understanding PIW and belt class helps in choosing the right belt for specific applications, ensuring it can handle the intended loads and operational conditions.
- Selection Criteria: Manufacturers and engineers use PIW and Class as selection criteria to match conveyor belts with the mechanical demands of the conveying system.
- Safety Implications: The correct understanding and application of these terms ensure that the conveyor system operates within safe limits, preventing overloading and reducing the risk of failures.
By thoroughly understanding these standards, safety factors, and key terms, stakeholders can ensure that EP conveyor belts are selected and used correctly, enhancing operational efficiency and safety.
Advantages and Features of EP Conveyor Belts
EP conveyor belts, consisting of polyester in the warp and polyamide in the weft, are designed to meet the rigorous demands of various industrial environments. These belts provide a combination of exceptional strength, durability, and operational flexibility, making them suitable for a wide range of applications. Here we explore at least ten distinct advantages and features of EP conveyor belts, emphasizing their utility in different industrial settings.
- Lower Longitudinal Elongation: EP conveyor belts exhibit minimal elongation under tension, which helps maintain the belt’s length and stability during operations, reducing the need for frequent adjustments and maintenance.
- Excellent Durability: The robust construction of EP conveyor belt ensures a longer operational life even under harsh conditions, which is crucial for industries such as mining and construction where the belts are subjected to extreme stress.
- Resistance to Mildew, Moisture, and Rotting: These belts are specially treated to resist environmental factors like mildew and moisture, which can degrade materials over time. This feature is particularly beneficial in agricultural applications where exposure to the elements is frequent.
- High Tensile Strength: The polyester fabric used in the warp direction gives these belts high tensile strength, allowing them to handle heavy loads without stretching excessively.
- Good Flexibility and Troughability: Despite their strength, EP conveyor belts are sufficiently flexible to form troughs easily, efficiently containing materials and reducing spillage during transport.
- Energy Efficiency: Due to their low elongation, EP conveyor belts require less energy to move and maintain tension, which can significantly reduce operational costs.
- Heat Resistance: With the appropriate choice of compounds, EP conveyor belts can withstand higher temperatures, making them suitable for industries like cement manufacturing and steel processing.
- Chemical Resistance: These belts can be formulated to resist various chemicals, making them ideal for use in chemical processing plants or places where belts are exposed to harsh substances.
- High Impact Resistance: The multi-ply construction typically used in EP conveyor belt provides enhanced resistance to impacts and punctures, which is essential in heavy-duty applications.
- Versatility Across Industries: EP conveyor belts are versatile enough to be used in diverse industries, from light agricultural conveyors to heavy-duty mining and construction sites, due to their balanced properties of durability, flexibility, and load-bearing capacity.
These features collectively make EP conveyor belts a preferred choice in a myriad of operational settings, providing a reliable and efficient means of material transport across different sectors. The extensive range of advantages ensures that these belts meet the specific requirements of various applications, enhancing productivity and safety in industrial operations.
Applications of EP Conveyor Belt in Industry
EP conveyor belts, characterized by their robust and durable design, serve a crucial role across a variety of industries. These belts are engineered to handle a wide range of materials, from the lightest grains to the heaviest stones, adapting to different environmental and operational demands. This section explores the specific applications of EP conveyor belt, illustrating their effectiveness in diverse industry settings.
Diverse Applications of EP Conveyor Belt
- Mining Operations: EP conveyor belts are indispensable in the mining industry, transporting materials such as coal, ores, and aggregates. These belts are designed to withstand the harsh mining environment, managing heavy loads over long distances without extensive wear.
- Agricultural Sector: In agriculture, these belts facilitate the efficient transfer of grains and other bulk products from silos to processing areas or directly into trucks for market distribution, helping maintain the quality and integrity of agricultural products.
- Cement Manufacturing: Utilized in the cement industry, EP conveyor belts transport raw materials like limestone from quarries to processing plants, and move clinker to the grinding area, handling the high temperatures and abrasive nature of these materials.
- Chemical Plants: In chemical processing, these belts convey raw chemicals, finished products, and by-products, featuring special coatings or treatments to resist chemical corrosion and ensure safe handling of potentially hazardous materials.
- Recycling Operations: EP conveyor belts are used in recycling facilities to sort and convey recyclable materials through the plant, supporting environmental sustainability by efficiently managing various types of waste products.
- Packaging and Distribution: These belts streamline operations in packaging plants by transporting goods between production, packaging, and shipping areas, enhancing speed and efficiency in the logistics chain.
Role of EP Belts in Improving Operational Efficiency and Safety
The efficiency and safety of industrial operations heavily rely on the quality and performance of conveyor systems. EP conveyor belts, with their advanced design and material properties, contribute significantly to operational excellence and safety in workplaces. This section highlights how these belts improve efficiency and safety across various industries.
- Enhanced Productivity: The strength and durability of EP conveyor belts allow them to handle larger volumes of materials at higher speeds, effectively increasing productivity and reducing cycle times in industrial operations.
- Minimized Operational Downtime: The robust construction of EP conveyor belts reduces the frequency of maintenance and replacement, thereby minimizing downtime and ensuring continuous production flows.
- Safety Enhancements: By maintaining their integrity under extreme conditions, EP conveyor belts reduce the risks of belt-related failures and accidents, ensuring a safer working environment for employees.
- Energy Cost Savings: The low elongation properties of EP belts mean less energy is required for tensioning and movement, leading to significant savings in energy costs over time.
- Operational Versatility: Their ability to perform under varying environmental conditions makes EP conveyor belts suitable for a wide range of applications, from indoor facilities to outdoor industrial settings, adapting to different operational needs without compromising performance.
- Reduced Material Loss: Good troughability of EP belts prevents material spillage during transport, which not only enhances safety by keeping walkways clear but also reduces waste and increases material handling efficiency.
Through these capabilities, EP conveyor belt plays a pivotal role in optimizing industrial operations, making them a valuable asset in enhancing both efficiency and safety in diverse industrial landscapes.
Fill out the form for a prompt quote and more information about our EP conveyor belts.
FAQs about EP Conveyor Belt
EP in belt conveyors stands for “Polyester-Polyamide,” specifically referring to the type of fabrics used in the construction of the conveyor belt. EP belts are constructed with multiple layers of polyester (E) in the warp direction (lengthwise) and polyamide (nylon, N) in the weft direction (widthwise). This combination of materials provides the belt with exceptional strength and resistance to stretching, which is essential for the dynamic conditions under which conveyor belts operate. The polyester provides high strength, rigidity, and low stretch properties, while the nylon offers flexibility, excellent troughability, and shock absorption. These characteristics make EP conveyor belts particularly suitable for long-distance, high-load, and high-speed applications in various industrial environments, including mining, construction, and aggregate industries.
The main difference between EP (Polyester-Polyamide) and NN (Nylon-Nylon) belts lies in the material composition used in their fabric layers. EP belts are made with polyester in the warp direction and polyamide (nylon) in the weft direction, while NN belts are constructed entirely from nylon both in the warp and the weft. This difference in material construction gives EP belts a higher tensile strength, lower elongation, and better resistance to mechanical damage and moisture compared to NN belts. On the other hand, NN belts typically exhibit better flexibility and are more shock absorbent due to the nylon’s inherent properties. The choice between EP and NN belts depends on specific operational requirements such as load, speed, and the type of materials being transported. EP belts are generally favored for their strength and durability in harsher environments, while NN belts might be preferred in applications requiring greater flexibility and shock absorption.
Elongation of an EP belt refers to the stretch that occurs under tensile load, expressed as a percentage of the belt’s original length. Generally, EP conveyor belts are designed to have lower elongation rates compared to other types of belts, which is a crucial characteristic for maintaining stable belt tension and operational efficiency over long distances. The typical elongation for EP belts is usually around 1.5% to 2% at 10% of the belt’s breaking strength. This low elongation helps prevent the belt from stretching excessively under load, which in turn reduces the need for frequent re-tensioning and maintenance. It also enhances the belt’s ability to handle high loads and speeds, making EP belts a reliable choice for critical and heavy-duty applications in industries such as mining, bulk material handling, and large-scale manufacturing.
Conveyor belts can be categorized based on their construction material, design, and application. The most common types include:
Flat Belt Conveyors: These are primarily used in material handling, packaging, and parts transferring processes. They are versatile and can be used in a range of industries.
Modular Belt Conveyors: Made from plastic composite materials, these belts are suitable for applications requiring high standards of cleanliness and low maintenance.
Cleated Belt Conveyors: These belts are equipped with vertical cleats to prevent slippage of materials. They are ideal for moving loose materials uphill or vertically.
Curved Belt Conveyors: These can navigate turns and obstacles, making them suitable for complex layouts where space is limited.
Steel Belt Conveyors: These are designed for heavy-duty applications and are predominantly used in metal scrap handling and recycling.
Specialty Conveyor Belts: This category includes belts designed for specific conditions and materials, such as heat-resistant, oil-resistant, and flame-retardant conveyor belts.
Each type of conveyor belt is designed to meet specific operational needs and to work within particular environments. Choosing the right type of conveyor belt is crucial for efficient, safe, and cost-effective operations.
Last Updated on July 31, 2024 by Jordan Smith
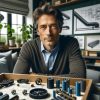
Jordan Smith, a seasoned professional with over 20 years of experience in the conveyor system industry. Jordan’s expertise lies in providing comprehensive solutions for conveyor rollers, belts, and accessories, catering to a wide range of industrial needs. From initial design and configuration to installation and meticulous troubleshooting, Jordan is adept at handling all aspects of conveyor system management. Whether you’re looking to upgrade your production line with efficient conveyor belts, require custom conveyor rollers for specific operations, or need expert advice on selecting the right conveyor accessories for your facility, Jordan is your reliable consultant. For any inquiries or assistance with conveyor system optimization, Jordan is available to share his wealth of knowledge and experience. Feel free to reach out at any time for professional guidance on all matters related to conveyor rollers, belts, and accessories.