Choosing EP Conveyor Belt Specification
EP conveyor belts, known for their robust construction using Polyester in the warp and Polyamide in the weft, are essential in industries like mining, agriculture, and construction due to their durability and efficiency in handling diverse materials under various environmental conditions. Understanding EP conveyor belt specification:known for strength and durability, transport bulk materials like ore, sand, and chemicals.The importance of understanding detailed EP conveyor belt specification cannot be overstated, as it ensures the selection of the right belt type that can handle specific operational demands effectively. By delving into these specifications, industries can optimize both the performance and lifespan of their conveyor systems, leading to improved productivity and reduced downtime.
What is EP in EP Conveyor Belt Specification
The designation “EP” in conveyor belts stands for the combination of Polyester in the warp (longitudinal direction) and Polyamide in the weft (transverse direction). This specific composition of materials in the EP conveyor belt specification offers a distinct set of properties that enhances the performance and durability of the belts. Here’s a detailed look at the characteristics of EP, explaining its significance in conveyor belt technology:
- Composition: Polyester in the warp offers high tensile strength, essential for the belt’s structural integrity and resistance to elongation.
- Flexibility: Incorporating Polyamide in the weft adds flexibility to the belt, which helps it to absorb shocks and impacts more effectively during operation.
- Low Elongation: Polyester’s inherent low elongation helps the belt maintain its form under thermal and mechanical stresses, ensuring consistent performance.
- Moisture Resistance: Polyamide enhances the belt’s ability to resist moisture, preventing degradation in humid or wet conditions.
- Troughability: The unique weave of Polyester and Polyamide ensures excellent troughability, allowing the belt to carry a variety of materials securely.
- Chemical Resistance: The chemical resistance of EP belts makes them suitable for environments where corrosive materials are handled.
- Heat Resistance: Polyester’s high melting point allows the belt to perform under higher temperatures without losing its dimensional stability.
- Dimensional Stability: Together, Polyester and Polyamide provide a balance of strength and flexibility, maintaining the belt’s shape under loads.
EP Conveyor Belt Construction
EP conveyor belts, also known as polyester-nylon conveyor belts, are constructed using several key components that provide their strength, durability, and versatility. Here’s a detailed breakdown of their construction:
1. Carcass
- Fabric Layers: The carcass is made up of multiple layers of fabric, typically consisting of polyester (E) in the warp direction and polyamide (nylon) (P) in the weft direction.
- Layer Configuration: The number of fabric layers can vary depending on the required strength and application. Common configurations include 2-ply, 3-ply, or more layers.
- Properties: Polyester provides low elongation and high tensile strength, while polyamide offers excellent flexibility and impact resistance.
2. Top Cover
- Rubber Compound: The top cover is made from a high-quality rubber compound designed to protect the belt from wear, abrasion, and impact.
- Thickness: The thickness of the top cover can vary depending on the application, typically ranging from 3 mm to 10 mm or more.
- Special Properties: Depending on the application, the top cover can be formulated to have special properties such as heat resistance, oil resistance, or flame retardancy.
3. Bottom Cover
- Rubber Compound: Similar to the top cover, the bottom cover is also made from a rubber compound, though it is typically thinner than the top cover.
- Thickness: The thickness usually ranges from 1 mm to 4 mm.
- Function: The bottom cover provides additional protection to the carcass and ensures smooth movement over conveyor idlers and pulleys.
4. Adhesive Layers
- Bonding Layers: Between the fabric plies and the rubber covers, adhesive layers are used to bond the components together.
- Adhesive Properties: These layers ensure strong adhesion, preventing delamination and enhancing the belt’s overall durability.
5. Edge Reinforcement
- Edge Protection: Some EP belts feature reinforced edges to prevent fraying and damage during operation.
- Materials: Reinforcements can be made from additional layers of rubber or specially designed materials to provide extra protection.
6. Special Treatments
- Surface Coatings: For specific applications, the belt surface may be treated with coatings to enhance properties like grip, chemical resistance, or reduce friction.
- Anti-Static Treatments: In environments where static electricity is a concern, anti-static treatments can be applied to the belt.

EP Conveyor Belt Features
EP fabric, made from Polyester and Polyamide, offers numerous benefits over other materials used in conveyor belt construction, primarily due to its superior durability and strength. Here’s why EP fabric is advantageous:
- Durability: The robustness of EP fabric extends the belt’s operational life and reduces the need for frequent replacements or repairs.
- High Tensile Strength: EP belts can handle higher tensile loads, making them ideal for heavy-duty industrial applications.
- Energy Efficiency: Lower stretch under load means EP belts require less energy to move and maintain tension, which can significantly reduce power consumption.
- Reduced Slippage: Enhanced grip between the conveyor and the load improves operational safety and efficiency.
- High Impact Resistance: EP belts are capable of withstanding substantial impacts, especially important in industries like mining where large, rough materials are common.
- Superior Load Support: The ability to support heavier loads without sagging or breaking makes EP belts highly reliable.
- Resistance to Wear and Tear: EP’s wear-resistant properties are crucial for maintaining performance in environments with abrasive or sharp materials.
- Adaptability to Weather Conditions: EP belts perform consistently across various climates, resisting degradation from UV light, moisture, and temperature extremes.
- Cost-Effectiveness: The long service life and minimal maintenance requirements make EP belts a cost-effective choice for long-term industrial applications.
- Good Troughability:These belts have excellent troughability, meaning they can easily form into a deep trough shape, which helps in carrying materials more effectively.
- Superior Adhesion:The adhesion between the fabric and the rubber is strong, which enhances the belt’s lifespan and performance.
- Low Elongation:EP belts exhibit low elongation in the warp direction, which minimizes the need for frequent tension adjustments.
- Heat Resistance:EP belts can withstand higher temperatures compared to traditional rubber belts, making them suitable for environments with higher operational temperatures.
- Moisture and Mildew Resistance:The polyester fabric in EP belts offers good resistance to moisture and mildew, ensuring longevity even in humid conditions.
- Chemical Resistance:These belts are resistant to various chemicals, which makes them suitable for industries such as chemical processing, fertilizers, and more.
- Flexibility:EP belts maintain flexibility over a wide range of temperatures, which is essential for smooth operation in various environmental conditions.
Understanding the EP conveyor belt specification and its advantages is vital for industries looking to optimize their material handling systems with reliable, efficient, and durable conveyor belts.
EP Conveyor Belt Application
EP conveyor belts are used in a wide range of industrial applications due to their robust properties. Here are some of the key applications:
Mining Industry
- Coal and Ore Transportation: Used for transporting coal, ore, and other mined materials due to their high tensile strength and impact resistance.
- Underground Mining: Suitable for use in underground mines because of their fire-resistant properties.
Construction Industry
- Aggregate and Sand Handling: Ideal for transporting sand, gravel, and aggregates.
- Concrete Plants: Used in concrete plants for moving raw materials like sand, cement, and gravel.
Cement Industry
- Raw Material Handling: Used for transporting limestone, clay, and other raw materials to the processing units.
- Clinker and Finished Product Transport: Efficient in moving clinker and finished cement to storage or shipping areas.
Steel Industry
- Raw Material Transport: Transporting iron ore, coal, and other raw materials to the blast furnace.
- Finished Product Handling: Used in the handling of finished steel products, including coils and sheets.
Power Plants
- Coal Handling: EP belts are used in thermal power plants for transporting coal from storage yards to the furnace.
- Ash Handling: Suitable for moving ash and other by-products from combustion processes.
Chemical Industry
- Chemical Transportation: Suitable for transporting raw materials and finished chemical products, thanks to their chemical resistance.
- Fertilizer Plants: Used in fertilizer plants for moving raw materials and finished products.
Port and Shipping
- Bulk Cargo Handling: Used in ports for the efficient handling of bulk cargo like grains, ores, and coal.
- Container Handling: Suitable for use in container handling systems due to their high load-bearing capacity.
Food Processing Industry
- Raw Material Transport: Used in the initial stages of food processing for transporting raw materials.
- Packaging Lines: Efficient in moving packaged food products to storage or shipping areas.
Agriculture
- Grain Handling: Used in grain elevators and storage facilities for transporting grains.
- Fertilizer Application: Suitable for use in transporting fertilizers in agricultural settings.
Recycling Industry
- Waste Sorting: Used in recycling plants for the transportation and sorting of recyclable materials.
- Scrap Handling: Suitable for moving scrap metal and other recyclable materials.
Quarrying
- Stone and Rock Transportation: Ideal for transporting stones, rocks, and other quarry materials.
- Crushing Plants: Used in crushing plants for moving crushed stone and aggregate.
EP conveyor belts’ durability, strength, and adaptability make them suitable for various demanding applications across different industries.

Key Specifications of EP Conveyor Belt Specification
When exploring the EP conveyor belt specification, it is important to delve into the standard specifications and nomenclature that define their structural and functional characteristics. This detailed understanding assists in selecting the right belt type for various industrial applications, ensuring efficiency and durability.
What Are Standard Specifications
In the realm of conveyor belts, EP 400/3 and EP 630/4 represent common configurations, tailored to meet the demands of diverse operational environments. These specifications highlight the belt’s capacity to handle different loads and conditions:
- EP 400/3: This belt is designed for medium-duty applications, indicating a maximum working tension of 400 N/mm across its width. This specification is suitable for industries like agriculture, where the load and speed are moderate but require durability and flexibility.
- EP 630/4: A more robust belt with a working tension of 630 N/mm, indicating its use in environments that demand high strength and durability, such as in mining or heavy construction. The additional strength helps in transporting heavier loads over longer distances without significant wear.
- Tensile Strength: The first number in these specifications (400 or 630) quantifies the belt’s strength per millimeter of width, critical in assessing its ability to support various weights and pressures during operations.
- Number of Plies: The digit after the slash (3 or 4) tells us about the number of textile layers embedded within the belt. More plies generally increase the belt’s durability and impact resistance, essential for heavy-duty applications.
- Cover Thickness: Typically, the final number in the specification like ‘3’ in EP 400/3, refers to the combined thickness of the top and bottom rubber covers in millimeters. These covers protect the internal fabric from abrasive and sharp materials, thereby extending the belt’s operational life.
- Application Suitability: Choosing between an EP 400/3 and an EP 630/4 depends on the specific requirements of the application, including expected load, the abrasiveness of transported materials, and overall environmental conditions.
Decoding Conveyor Belt Nomenclature
Conveyor belt nomenclature is a coding system that provides detailed information about the belt’s characteristics and capabilities. Understanding these codes is crucial for selecting a conveyor belt that fits the specific needs of a facility:
- EP: This prefix in the nomenclature stands for the combination of Polyester and Polyamide, crucial for the belt’s performance in terms of strength and elasticity.
- First Number (Tensile Strength): Indicates the maximum longitudinal strength per millimeter width of the belt. Higher numbers signify a belt capable of carrying heavier loads, which is vital for applications involving heavy or sharp materials.
- Slash and Following Number (Plies): Reflects the number of fabric layers, which contribute to the belt’s overall strength and resistance to puncture. More plies usually mean better load distribution and reduced risk of belt damage under stress.
- Cover Grade: Specific cover grades, not always explicitly stated, determine the belt’s resistance to external conditions like abrasion, heat, chemicals, and oil. These are chosen based on the environmental challenges present in the belt’s intended application.
- Additional Markings: Such as ‘M’ for oil resistance or ‘FR’ for fire resistance, indicate special treatments or modifications that enhance the belt’s functionality in specific conditions.
- Thickness: It gives a quick insight into the belt’s robustness and potential impact on the conveyor system’s rollers and structures. Thicker belts can handle larger and more abrasive materials but may require more powerful motors and sturdier machinery.
- Width of the Belt: Critical for determining the volume of material the belt can transport per unit of time. Wider belts are typically used in larger-scale operations where high throughput is necessary.
Each detail in the EP conveyor belt specification provides essential information that helps in making informed decisions about conveyor belt selection, tailored to meet the operational demands and enhance the efficiency of material handling systems.
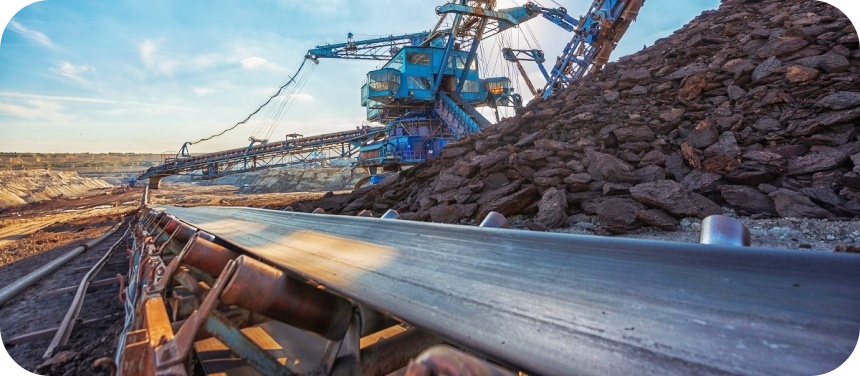
Conveyor Belt Specification Standards for EP Conveyor Belt Specification
Understanding the EP conveyor belt specification in the context of international standards is critical for ensuring that these belts meet global quality and performance benchmarks. Different regions and industries may adopt specific standards to address varying requirements and operational challenges. Here’s an exploration of some key standards that govern the specifications of EP conveyor belts:
- DIN (Deutsche Industrie Normen – Germany): This standard specifies the requirements for EP conveyor belts, including minimum performance criteria for tensile strength, elongation at break, and abrasion resistance. DIN standards are renowned for their rigor and are widely adopted in Europe and globally.
- ISO (International Organization for Standardization): ISO standards for conveyor belts cover general safety requirements, testing methods, and performance specifications. These standards help harmonize practices across different countries, ensuring compatibility and safety in international operations.
- RMA (Rubber Manufacturers Association – USA): RMA standards focus on the quality and performance of rubber conveyor belts. These standards define grade levels for different types of loads and environmental conditions, influencing the selection of belts for various applications.
- BS (British Standards): Similar to DIN, British Standards provide guidelines for the construction, dimensions, and testing of conveyor belts. BS standards are critical for UK manufacturers and are also influential in many Commonwealth countries.
- AS (Australian Standards): These standards ensure that conveyor belts meet the specific needs of the mining-heavy industries prevalent in Australia. They include detailed provisions for fire resistance and other safety features essential in mining applications.
- JIS (Japanese Industrial Standards): JIS standards cover a wide range of industrial equipment, including conveyor belts. These standards ensure high levels of innovation and precision, characteristic of Japanese manufacturing practices.
- SANS (South African National Standards): In a country where mining is a significant industry, SANS standards are crucial for conveyor belts used in harsh mining environments. They specify robust performance criteria to handle abrasive materials and challenging operational conditions.
- IS (Indian Standards): These standards are vital in India’s rapidly growing industrial sectors. They specify the performance of conveyor belts in terms of load, speed, and environmental resilience, ensuring reliability and efficiency in various industries.
- GB (Chinese National Standards): With China being a major global manufacturing hub, GB standards are critical for ensuring the quality and safety of conveyor belts manufactured and used within China and exported internationally.
Each of these standards plays a crucial role in defining the EP conveyor belt specification, ensuring that belts not only meet specific operational needs but also align with international safety and quality expectations. Adherence to these standards helps manufacturers deliver reliable and efficient conveyor belts suitable for a wide range of industrial applications around the world.
Detailed Look at EP Conveyor Belt Specification
In this section, we delve into the specifics of the EP conveyor belt specification, providing a detailed chart and explanation of the terms and numbers commonly used in identifying different types of EP conveyor belts. Understanding these specifications is crucial for selecting the right conveyor belt that meets the operational requirements of various industries.
Comprehensive Chart of EP Conveyor Belt Specification
Here is a detailed breakdown of typical EP conveyor belt specifications, covering essential aspects such as belt width, thickness, tensile strength, and safety factors:
- Belt Width: Ranges typically from 400 mm to over 2000 mm. The width is crucial as it determines the volume of material that can be transported over the conveyor.
- Thickness: Total thickness can vary from 5 mm to over 20 mm depending on the belt type and the use. Thicker belts are generally used for heavier and more abrasive materials.
- Tensile Strength: This is indicated by the first number in the belt specification (e.g., 400 in EP 400/3), which measures the maximum load the belt can handle per millimeter width in Newtons.
- Number of Plies: Indicated by the second number after the slash (e.g., 3 in EP 400/3), representing the number of fabric layers. More plies increase strength and durability.
- Safety Factor: This factor indicates the belt’s capacity to handle sudden increases in load or strong impacts. Typical safety factors range from 10:1 to 12:1.
- Abrasion Resistance: Measured in cubic millimeters, lower values indicate better resistance, crucial for belts used in environments with abrasive materials.
- Elongation at Break: Expressed as a percentage, this specifies how much the belt can stretch before it breaks. Lower elongation indicates higher tensile strength.
- Impact Resistance: Essential for belts in industries like mining where the material dropped on the belt might cause significant wear and tear.
- Temperature Range: Specifies the operating temperature range, which can vary from -30°C to +100°C, essential for belts used in varying climatic conditions.
Explanation of EP Conveyor Belt Specification Terms
Understanding terms like EP 400/3 and EP 630/4 is crucial for identifying the appropriate belt for specific applications:
EP 400/3:
- Tensile Strength: 400 N/mm, suitable for medium-duty applications.
- Plies: 3, offering a balance between flexibility and strength.
- Typical Applications: Used in sectors like agriculture, manufacturing, where operational demands are moderate.
EP 630/4:
- Tensile Strength: 630 N/mm, designed for heavy-duty use.
- Plies: 4, enhancing durability and load-bearing capacity.
- Typical Applications: Ideal for mining, construction, and other high-demand environments.
Safety Factors:
- Higher in belts like EP 630/4 to accommodate sudden increases in load and more extreme operational conditions.
Cover Thickness:
- Often correlates with the second number after the slash; essential for protecting the belt’s inner layers from abrasion and puncture.
Application Suitability:
- EP 400/3 is more suited for less abrasive materials and lower speed operations, whereas EP 630/4 is better for abrasive materials and high-speed conditions.
Durability and Cost Efficiency:
- Each belt is designed to offer optimal performance in specific environments, balancing cost and operational lifespan effectively.
By closely examining the EP conveyor belt specification, industries can ensure that they choose a belt that not only meets their needs but also offers durability and efficiency, thereby enhancing overall productivity and safety in material handling operations.

Importance of Conveyor Belt Safety Factor in EP Conveyor Belt Specification
The safety factor is a fundamental aspect of EP conveyor belt design, playing a pivotal role in ensuring operational security and resilience under extreme conditions. In this section, we will delve deeper into the concept of the safety factor, exploring why it is integral to the EP conveyor belt specification and how it directly influences the durability and longevity of the belts, especially in harsh industrial environments.
Understanding the Safety Factor in Conveyor Belt Design
The safety factor in conveyor belt design is a critical measure that ensures belts can handle significantly more weight and stress than they are normally subjected to during regular operations. Here’s a detailed exploration of its importance:
- Fundamental Concept: The safety factor is essentially the ratio of the belt’s breaking strength to the maximum expected operational load. This buffer helps accommodate unexpected loads and peak forces that could occur during conveyor operation.
- Guideline for Design: It acts as a guideline for designers to create belts that are not only functional under normal conditions but also safe under potential maximum load scenarios.
- Ensures Reliability: By considering a higher safety factor, manufacturers ensure that the belt will not fail unexpectedly, thereby preventing potential accidents and material spillage.
- Compliance with Safety Standards: Adhering to a specific safety factor is often mandated by safety regulations across different industries, ensuring that all operational safety standards are met.
- Affects Belt Selection: The required safety factor influences the selection of belt material, thickness, and construction, directly impacting the conveyor belt’s design and manufacturing cost.
- Reduces Operational Risks: A suitable safety factor is crucial for reducing the risk of operational failures, which can lead to extensive downtime and maintenance costs.
- Future-Proofing: Incorporating a robust safety factor during the design phase anticipates future increases in load or changes in usage that could otherwise compromise the belt’s performance.
How Safety Factors Influence Durability and Longevity of EP Belts
The choice of safety factor significantly impacts how well EP conveyor belts can withstand harsh working conditions over their operational life. Here’s how a well-calculated safety factor enhances belt durability and longevity:
- Builds Tougher Belts: A higher safety factor often means the belt is built with stronger, more resilient materials or has a more durable construction, which enhances its ability to endure harsh conditions.
- Withstands Abrasive Materials: In environments with abrasive or sharp materials, a robust safety factor ensures that the belts resist cuts, tears, and wear more effectively.
- Sustains Repeated High Loads: Belts designed with appropriate safety factors are more capable of handling high load cycles repeatedly without degradation, extending their usable life.
- Minimizes Environmental Damage: By accounting for environmental factors such as temperature extremes and chemical exposure in the safety factor, belts are less likely to fail due to external conditions.
- Maintains Structural Integrity: Higher safety factors help maintain the belt’s shape and alignment under stress, preventing issues like stretching or misalignment that could lead to operational problems.
- Enhances Impact Resistance: The ability to absorb and dissipate energy from impacts is improved in belts with higher safety factors, reducing the likelihood of damage from sudden shocks or large dropped materials.
The safety factor is not just a numerical value but a critical component of the EP conveyor belt specification that ensures safety, durability, and efficiency in the long-term operation of conveyor systems.
Have questions about our conveyor belts? Reach out today!
How to Choose the Right EP Conveyor Belt Specification
Selecting the right EP conveyor belt for specific applications involves careful consideration of various operational and environmental factors. This section provides detailed guidelines on how to choose an EP conveyor belt that aligns with the ep conveyor belt specification and meets the unique demands of different industrial settings.
Guidelines for Selecting the Appropriate EP Conveyor Belt
Choosing the appropriate EP conveyor belt requires a detailed understanding of the application’s specific needs. Here are key considerations to guide your selection process:
- Load Capacity: Assess the weight and nature of the materials the belt will carry. Ensure the belt’s tensile strength and design are adequate to handle the expected load without overstressing the belt.
- Operational Speed: Consider the speed at which the belt will operate. High-speed applications may require belts with enhanced features to reduce wear and tear and minimize the risk of belt slippage.
- Environmental Conditions: Analyze the working environment where the belt will be used. Factors such as temperature extremes, exposure to chemicals, and the presence of water or oils can dictate the type of belt required.
- Conveyance Length and Incline: Determine the length of the conveyance route and any incline angles. Longer routes or significant inclines may require belts with higher durability and specific elastic properties to maintain efficiency.
- Material Abrasiveness: If the conveyed materials are abrasive, select a belt with a higher abrasion resistance rating to prolong the life of the belt.
- Safety Requirements: Consider the safety requirements specific to your industry. This may involve selecting belts with fire-resistant or anti-static properties.
- Maintenance and Repair: Evaluate the ease of maintenance and repair of the belt. Some belts are easier to mend and maintain, which can reduce downtime and operational costs.
- Cost Efficiency: While the initial cost is an important factor, consider the total cost of ownership, which includes maintenance, durability, and potential downtime costs.
Tips on Interpreting Conveyor Belt Specification Charts and PDFs
To match the ep conveyor belt specification to application requirements, one must understand how to read and interpret specification charts and PDFs effectively:
- Decoding Specifications: Learn to decode the information provided in specification charts such as belt width, thickness, material type, and tensile strength. Each parameter has a direct impact on the belt’s suitability for different applications.
- Tensile Strength Ratings: Pay attention to the tensile strength ratings, which indicate the maximum load the belt can handle. Ensure this aligns with the operational load requirements.
- Abrasion Resistance Levels: Identify the abrasion resistance level listed in the specifications. This indicates how well the belt can withstand wear and tear from rough materials.
- Chemical Resistance: Check for any mention of chemical resistance if the belt will be exposed to corrosive substances. This can prevent premature degradation of the belt material.
- Temperature Suitability: Make sure the belt’s material is suitable for the temperature conditions of the environment in which it will operate, whether high or low.
- Understanding Safety Factors: Look for safety factor ratings, which provide insight into the belt’s ability to handle overloads and operational stresses.
- Special Features: Be aware of any special features like rip-stop reinforcements, energy efficiency ratings, or low-noise properties that might be necessary for your specific application.
- Consulting Experts: When in doubt, consult with a conveyor belt expert or refer to technical support provided by the belt manufacturer to ensure that your interpretation of the specifications aligns with practical requirements.
By following these guidelines and tips, you can effectively choose and interpret the ep conveyor belt specification to ensure optimal performance and alignment with your specific industrial needs. This careful selection process helps in maximizing the efficiency and longevity of the conveyor system.
FAQs about EP Conveyor Belt Specification
Conveyor belt EP refers to a type of conveyor belt that is made using EP fabric, which stands for “Polyester” in the warp (lengthwise direction) and “Polyamide” (commonly known as nylon) in the weft (crosswise direction). This construction provides a unique blend of strength, flexibility, and durability, which is essential for various conveying applications. EP conveyor belts are recognized for their low stretch (elongation), high tensile strength, and good resistance to moisture, mildew, and rot. This makes them suitable for a wide range of applications, from mining and quarrying to agriculture and manufacturing. The polyester in the warp direction provides strength and resistance to elongation, making the belts stable under tension. Meanwhile, the nylon in the weft adds flexibility and shock absorption properties, enhancing the belt’s capability to handle sudden loads and impacts.
The main difference between EP (Polyester-Polyamide) and NN (Nylon-Nylon) conveyor belts lies in the type of fabric used in their construction. EP belts are made with polyester in the warp direction and polyamide (nylon) in the weft, whereas NN belts use nylon fibers both in the warp and the weft. This distinction gives each belt different mechanical properties and suitability for various applications. EP belts generally have a lower stretch (elongation) compared to NN belts, making them more suitable for long-distance conveying where minimal belt stretch is desired. They are also better suited for conditions involving moisture and high humidity because polyester is less absorbent than nylon. On the other hand, NN belts are known for their exceptional flexibility and excellent resistance to abrasion, which makes them ideal for heavy-duty applications involving sharp or rugged materials.
The specification of a conveyor belt encompasses a range of technical details that describe its suitability for certain applications. These specifications typically include the belt width, thickness, material type, layer count (plies), tensile strength, and abrasion resistance. Additional specifications might address factors like temperature resistance, chemical resistance, and safety features such as fire-resistance or anti-static properties. For example, a common specification like EP 400/3 would indicate an EP belt with a tensile strength of 400 N/mm and 3 fabric plies. Each aspect of a conveyor belt’s specification is crucial for ensuring it meets the operational demands and environmental conditions of its intended use, helping to optimize performance and durability.
Elongation in the context of EP conveyor belts refers to the extent to which a belt can stretch under tension before it ultimately breaks. This property is critical because it affects the belt’s ability to maintain stability and alignment on the conveyor system under operational load. EP belts are designed to have low elongation properties, which helps in maintaining a consistent belt length during operation, reducing the need for frequent re-tensioning and adjustments. Typically, the elongation for EP belts ranges from 1.5% to 2% at 10% of the belt’s ultimate tensile strength. This low elongation rate is particularly beneficial in applications requiring precise and stable material handling, such as in the case of long-distance conveying or where precise positioning of items on the belt is critical
Last Updated on July 26, 2024 by Jordan Smith
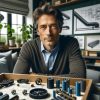
Jordan Smith, a seasoned professional with over 20 years of experience in the conveyor system industry. Jordan’s expertise lies in providing comprehensive solutions for conveyor rollers, belts, and accessories, catering to a wide range of industrial needs. From initial design and configuration to installation and meticulous troubleshooting, Jordan is adept at handling all aspects of conveyor system management. Whether you’re looking to upgrade your production line with efficient conveyor belts, require custom conveyor rollers for specific operations, or need expert advice on selecting the right conveyor accessories for your facility, Jordan is your reliable consultant. For any inquiries or assistance with conveyor system optimization, Jordan is available to share his wealth of knowledge and experience. Feel free to reach out at any time for professional guidance on all matters related to conveyor rollers, belts, and accessories.