EP Fabric Conveyor Belt Applications Explained
Conveyor belts are integral to the smooth operation of various industries, facilitating the efficient transport of materials. Among the different types, EP fabric conveyor belts stand out due to their exceptional performance and versatility. These belts are made from polyester fibers in the warp and nylon fibers in the weft, combining strength with flexibility. The EP fabric conveyor belt is lightweight yet durable, making it suitable for a wide range of applications, from mining to chemical industries. Its high modulus, small elongation, and excellent heat and impact resistance make it a preferred choice for medium to long-distance, heavy-load, and high-speed material conveyance.
What is an EP Fabric Conveyor Belt?
Definition
An EP fabric conveyor belt is a type of conveyor belt that is specifically designed for a variety of industrial applications requiring a durable and efficient means of material transportation. The “EP” in EP fabric conveyor belt stands for “Polyester” (E) and “Polyamide” (P), also known as nylon. These belts are a common choice in industries where strength, flexibility, and resistance to various stresses are paramount. The core of the EP fabric conveyor belt is made up of polyester fibers in the warp direction and nylon fibers in the weft direction. This unique composition provides an excellent balance of strength and flexibility, making EP fabric conveyor belts ideal for heavy-duty operations.
Material Composition
The material composition of an EP fabric conveyor belt is crucial to its performance and durability. The warp direction of the belt is constructed from polyester fibers, while the weft direction utilizes nylon fibers. This combination of materials offers several key benefits:
Polyester Fibers in the Warp
Polyester fibers are chosen for the warp direction due to their high tensile strength, stability, and resistance to elongation. These fibers ensure that the belt maintains its shape and structure under heavy loads and high-stress conditions. The high modulus of polyester means that the belt exhibits minimal elongation under tension, which is essential for maintaining consistent operation and reducing maintenance requirements.
Nylon Fibers in the Weft
Nylon fibers are used in the weft direction for their excellent flexibility, abrasion resistance, and impact resistance. Nylon is known for its ability to absorb shock and resist wear, which helps to prolong the life of the conveyor belt in demanding environments. The combination of nylon in the weft and polyester in the warp creates a fabric that is both strong and flexible, capable of withstanding the rigors of industrial use.
Advantages of EP Fabric Conveyor Belts
The unique material composition of EP fabric conveyor belts provides several significant advantages:
Lightweight
EP fabric conveyor belts are lighter than many other types of conveyor belts, which makes them easier to handle and install. The reduced weight also contributes to lower energy consumption during operation, which can result in cost savings over time.
High Modulus
The high modulus of polyester fibers means that the EP fabric conveyor belt has a high resistance to stretching and deformation. This property ensures that the belt maintains its structural integrity and operational efficiency, even under heavy loads and high tension.
Small Elongation
EP fabric conveyor belts exhibit minimal elongation under load, which is a critical factor in maintaining consistent belt tension and alignment. This characteristic helps to reduce the need for frequent adjustments and maintenance, leading to increased operational uptime and efficiency.
Good Heat Resistance
The materials used in EP fabric conveyor belts provide excellent resistance to heat, making them suitable for use in high-temperature environments. This property is particularly important in industries such as metallurgy, where materials may be transported at elevated temperatures.
Good Impact Resistance
The combination of polyester and nylon fibers gives EP fabric conveyor belts superior impact resistance. This capability allows the belts to withstand the shocks and stresses associated with transporting heavy or abrasive materials, thereby extending the belt’s lifespan and reducing downtime.
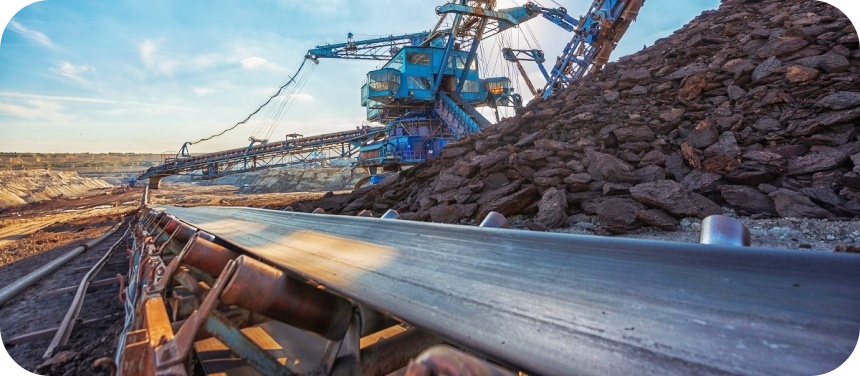
Applications of EP Fabric Conveyor Belts
EP fabric conveyor belts are used in a wide range of industries and applications due to their strength, durability, and versatility. Some common applications include:
Mines
In mining operations, EP fabric conveyor belts are used to transport ore, coal, and other materials from one location to another. The belts’ high tensile strength and resistance to abrasion make them ideal for the harsh conditions typically found in mines.
Metallurgy
In the metallurgical industry, EP fabric conveyor belts are employed to move materials such as metal ores, scrap metal, and finished products. The belts’ ability to withstand high temperatures and resist wear is crucial in this demanding environment.
Architecture
In the construction and architectural industries, EP fabric conveyor belts are used to transport building materials such as sand, gravel, and cement. The belts’ durability and resistance to elongation ensure efficient and reliable operation.
Ports
Ports and shipping terminals utilize EP fabric conveyor belts to handle the loading and unloading of bulk materials such as grain, coal, and minerals. The belts’ high strength and impact resistance make them well-suited for the heavy-duty requirements of port operations.
Electricity
In power plants and other energy facilities, EP fabric conveyor belts are used to move coal, biomass, and other fuels. The belts’ resistance to heat and abrasion ensures reliable performance in these high-stress environments.
Chemical Industries
The chemical industry relies on EP fabric conveyor belts to transport a variety of raw materials and finished products. The belts’ resistance to chemical exposure and their ability to maintain structural integrity under load make them an essential component in chemical processing operations.
Detailed Specifications of EP Fabric Conveyor Belts
Understanding the specifications of EP fabric conveyor belts is essential for selecting the right belt for a particular application. Key specifications include:
Fabric Type
EP fabric conveyor belts are classified based on the type of fabric used in their construction. The fabric type is indicated by a code, such as EP80, EP100, EP125, EP150, EP200, EP250, EP300, EP350, EP400, and EP500. These codes represent the tensile strength of the belt in Newtons per millimeter (N/mm).
Single Fabric Thickness
The thickness of the single fabric layer in an EP fabric conveyor belt can vary depending on the fabric code. Typical thicknesses range from 0.9 mm to 2.5 mm. The thickness of the fabric layer influences the overall strength and durability of the belt.
Single Fabric Strength
The single fabric strength of an EP fabric conveyor belt refers to the tensile strength of the fabric layer. This strength is measured in Newtons per millimeter (N/mm) and can range from 80 N/mm to 500 N/mm, depending on the fabric code. Higher strength ratings indicate a stronger and more robust belt.
Cover Thickness
The cover thickness of an EP fabric conveyor belt refers to the thickness of the rubber layers that cover the fabric core. The cover thickness can vary, with the top cover typically ranging from 2 mm to 12 mm and the bottom cover ranging from 0 mm to 5 mm. The cover thickness affects the belt’s resistance to wear, impact, and environmental conditions.
Number of Fabric Ply
The number of fabric plies in an EP fabric conveyor belt can range from 2 to 10. The number of plies affects the belt’s overall strength, flexibility, and load-carrying capacity. More plies generally result in a stronger and more durable belt.
Width and Length
EP fabric conveyor belts are available in a range of widths, typically from 350 mm to 2200 mm. The production length of the belts can be up to 300 meters per roll. Custom widths and lengths can be produced to meet specific application requirements.
Comparing EP Fabric Conveyor Belts with Other Types
To fully appreciate the benefits of EP fabric conveyor belts, it is useful to compare them with other types of conveyor belts, such as NN (Nylon) belts and steel cord belts.
EP vs. NN Belts
NN belts, or nylon belts, are another common type of conveyor belt. They are constructed using nylon fibers in both the warp and weft directions. While NN belts offer good flexibility and impact resistance, they tend to exhibit higher elongation under load compared to EP fabric conveyor belts. This higher elongation can result in more frequent maintenance and adjustments to maintain proper belt tension and alignment.
EP vs. Steel Cord Belts
Steel cord conveyor belts are known for their exceptional strength and low elongation. These belts are constructed using steel cords embedded in the rubber belt. While steel cord belts offer superior tensile strength and are suitable for extremely heavy-duty applications, they are also heavier and less flexible than EP fabric conveyor belts. EP fabric conveyor belts provide a good balance of strength, flexibility, and ease of handling, making them a versatile choice for many applications.
Pricing and Standards
The pricing of EP fabric conveyor belts can vary based on several factors, including the fabric type, number of plies, cover thickness, and customization requirements. Generally, EP fabric conveyor belts offer a cost-effective solution for many industrial applications due to their durability and long service life.
Specification Standards
EP fabric conveyor belts are manufactured according to various international standards to ensure quality and performance. Common standards include:
- DIN 22102: A German standard for conveyor belts, specifying requirements for fabric belts with rubber covers.
- ISO 14890: An international standard specifying the requirements for conveyor belts with textile carcasses.
- BS 490: A British standard for conveyor belts, specifying requirements for various types of conveyor belts, including EP fabric belts.
Compliance with these standards ensures that EP fabric conveyor belts meet the necessary quality and performance criteria for industrial use.
Engineering and Customization
EP fabric conveyor belts can be engineered and customized to meet specific application requirements. Customization options include:
- Belt Width and Length: Custom widths and lengths can be produced to fit specific conveyor systems.
- Cover Thickness: The thickness of the top and bottom covers can be customized to provide the desired level of wear resistance and impact protection.
- Number of Plies: The number of fabric plies can be adjusted to achieve the required strength and flexibility.
- Special Formulations: EP fabric conveyor belts can be formulated with special compounds to enhance resistance to heat, oil, chemicals, and other environmental factors.
By working with manufacturers, customers can obtain EP fabric conveyor belts that are tailored to their specific needs and operational conditions.
EP fabric conveyor belts are a versatile and durable solution for a wide range of industrial applications. Their unique material composition, combining polyester and nylon fibers, provides a balance of strength, flexibility, and resistance to various stresses. The advantages of EP fabric conveyor belts, including their lightweight, high modulus, small elongation, heat resistance, and impact resistance, make them an ideal choice for
Advantages of EP Fabric Conveyor Belts
EP fabric conveyor belts are widely used in various industries due to their numerous advantages. These advantages stem from their unique material composition and engineering, making them suitable for demanding applications that require strength, durability, and resilience. Below, we delve into the specific benefits of EP fabric conveyor belts, detailing how each feature contributes to their overall performance and suitability for industrial use.
Lightweight
One of the primary advantages of EP fabric conveyor belts is their lightweight nature. Compared to other types of conveyor belts, EP fabric belts are significantly lighter, which offers several benefits:
Ease of Handling and Installation
The reduced weight of EP fabric conveyor belts makes them easier to handle and install. This is particularly important in industries where conveyor belts need to be frequently replaced or repaired. The lightweight nature of these belts reduces the physical strain on workers and speeds up the installation process, leading to increased efficiency and reduced downtime.
Lower Energy Consumption
A lighter conveyor belt requires less energy to operate. This can result in significant cost savings over time, as the energy consumption of the conveyor system is reduced. In large-scale operations where conveyor belts run continuously, the energy savings can be substantial, contributing to lower operational costs and improved sustainability.
Improved System Efficiency
The lower weight of EP fabric conveyor belts also contributes to improved system efficiency. Lighter belts generate less friction and require less power to move, which can extend the life of conveyor components such as motors, pulleys, and rollers. This results in a more efficient and reliable conveyor system, with fewer maintenance requirements and longer service intervals.
High Modulus
The high modulus of EP fabric conveyor belts is another significant advantage. The term “modulus” refers to the stiffness or rigidity of the material, and a high modulus indicates that the belt can withstand high tensile forces without significant stretching or deformation. This property offers several benefits:
Enhanced Strength and Durability
The high modulus of EP fabric conveyor belts ensures that they are strong and durable, capable of handling heavy loads and high-stress conditions. This makes them ideal for applications where the belt is subjected to significant tension and pressure, such as in mining, construction, and material handling industries. The enhanced strength and durability of EP fabric conveyor belts result in a longer service life and reduced need for frequent replacements.
Consistent Performance
Because EP fabric conveyor belts exhibit minimal stretching or deformation under load, they provide consistent performance throughout their lifespan. This is crucial in industrial applications where precise material handling and transport are essential. The high modulus ensures that the belt maintains its shape and alignment, reducing the risk of misalignment, slippage, and other operational issues.
Reduced Maintenance
The high modulus of EP fabric conveyor belts also contributes to reduced maintenance requirements. Since the belts do not stretch or deform easily, they do not need to be frequently retensioned or realigned. This results in fewer maintenance interventions and lower maintenance costs, allowing for more efficient and uninterrupted operations.
Small Elongation
EP fabric conveyor belts are designed to exhibit small elongation under load. This means that the belts stretch very little when subjected to tension, which is a critical factor in maintaining proper belt tension and alignment. The small elongation of EP fabric conveyor belts offers several advantages:
Stable and Reliable Operation
The minimal elongation of EP fabric conveyor belts ensures stable and reliable operation. When the belt stretches less, it maintains consistent tension and alignment, which is essential for efficient material transport. This stability reduces the risk of belt slippage, misalignment, and other issues that can disrupt operations and lead to downtime.
Precise Material Handling
In applications where precise material handling is required, such as in manufacturing and packaging, the small elongation of EP fabric conveyor belts ensures accurate and consistent transport of materials. This precision is crucial for maintaining product quality and ensuring that production processes run smoothly.
Longevity
Belts that exhibit minimal elongation tend to have a longer lifespan. Excessive stretching can cause the belt to wear out more quickly and lose its structural integrity. The small elongation of EP fabric conveyor belts helps to preserve their strength and durability over time, resulting in a longer service life and reduced need for replacements.
Heat Resistance
Heat resistance is a critical property for conveyor belts used in high-temperature environments. EP fabric conveyor belts are designed to withstand elevated temperatures without degrading or losing their performance characteristics. The heat resistance of EP fabric conveyor belts provides several benefits:
Suitable for High-Temperature Applications
EP fabric conveyor belts are suitable for use in high-temperature applications, such as in the metallurgical, glass, and ceramics industries. These belts can withstand the heat generated during material processing and transport, ensuring reliable and continuous operation.
Prevention of Belt Degradation
Exposure to high temperatures can cause some conveyor belts to degrade, leading to cracking, hardening, and loss of flexibility. EP fabric conveyor belts are engineered to resist thermal degradation, maintaining their structural integrity and performance even under prolonged exposure to high temperatures. This resistance helps to extend the lifespan of the belt and reduce the frequency of replacements.
Enhanced Safety
The heat resistance of EP fabric conveyor belts also enhances safety in high-temperature environments. Belts that can withstand elevated temperatures are less likely to fail or become damaged due to heat exposure. This reduces the risk of accidents and ensures a safer working environment for employees.
Impact Resistance
Impact resistance is another key advantage of EP fabric conveyor belts. These belts are designed to withstand the physical impacts and shocks that occur during material loading and transport. The impact resistance of EP fabric conveyor belts offers several benefits:
Protection Against Abrasive Materials
In industries such as mining, construction, and recycling, conveyor belts are often exposed to abrasive materials that can cause significant wear and tear. EP fabric conveyor belts are engineered to resist abrasion, ensuring that they can handle the toughest materials without becoming damaged. This resistance helps to extend the lifespan of the belt and reduce maintenance costs.
Reduced Risk of Belt Damage
The impact resistance of EP fabric conveyor belts reduces the risk of belt damage caused by heavy or sharp objects. This is particularly important in applications where materials are dropped onto the belt from a height or where heavy loads are transported. The ability of the belt to absorb and dissipate impact forces helps to prevent damage and ensures continuous operation.
Enhanced Durability
EP fabric conveyor belts are built to last, withstanding the rigors of demanding industrial environments. The impact resistance of these belts contributes to their overall durability, ensuring that they can handle the stresses of material transport without failing. This durability results in a longer service life and reduced need for frequent replacements.
The numerous advantages of EP fabric conveyor belts make them an ideal choice for a wide range of industrial applications. Their lightweight nature, high modulus, small elongation, heat resistance, and impact resistance provide a combination of strength, durability, and efficiency that is unmatched by other types of conveyor belts. By choosing EP fabric conveyor belts, industries can benefit from improved performance, reduced maintenance requirements, and increased operational efficiency.
Applications of EP Fabric Conveyor Belts
EP fabric conveyor belts are highly versatile and widely used across various industries due to their robust construction, durability, and efficient performance. They are particularly suitable for applications involving medium to long-distance material conveyance, heavy load handling, and high-speed operations. Below, we explore the specific applications of EP fabric conveyor belts in different industries and scenarios, highlighting their suitability and benefits.
Medium to Long Distance
One of the primary applications of EP fabric conveyor belts is the transportation of materials over medium to long distances. These belts are designed to handle extended runs with minimal stretching and deformation, ensuring consistent and reliable performance.
Consistent Material Flow
EP fabric conveyor belts maintain consistent tension and alignment, which is crucial for ensuring a steady flow of materials over long distances. This is particularly important in industries such as mining and agriculture, where materials need to be transported from extraction or harvesting sites to processing facilities.
Reduced Maintenance
The durability and small elongation of EP fabric conveyor belts reduce the need for frequent maintenance and adjustments, even over long distances. This leads to lower operational costs and increased uptime, making them an ideal choice for continuous and extended operations.
Energy Efficiency
The lightweight nature of EP fabric conveyor belts contributes to their energy efficiency, particularly in long-distance applications. Reduced belt weight means lower energy consumption, which can result in significant cost savings over the lifespan of the conveyor system.
Heavy Load Handling
EP fabric conveyor belts are engineered to handle heavy loads with ease. Their high tensile strength and impact resistance make them suitable for transporting large and bulky materials in various industrial settings.
High Tensile Strength
The combination of polyester and nylon fibers provides EP fabric conveyor belts with high tensile strength, allowing them to carry heavy loads without stretching or breaking. This is essential in industries such as mining and metallurgy, where the belts are subjected to significant tension and pressure.
Durability Under Stress
The robust construction of EP fabric conveyor belts ensures that they can withstand the physical stresses associated with heavy load handling. This includes resistance to abrasion, impact, and wear, which helps to prolong the lifespan of the belt and reduce the need for frequent replacements.
Enhanced Safety
By effectively handling heavy loads, EP fabric conveyor belts contribute to a safer working environment. The risk of belt failure or material spillage is minimized, which helps to prevent accidents and injuries in the workplace.
High-Speed Operations
In addition to their strength and durability, EP fabric conveyor belts are also designed for high-speed operations. Their ability to maintain stability and performance at high speeds makes them suitable for applications where rapid material conveyance is required.
Stability at High Speeds
EP fabric conveyor belts exhibit minimal elongation and maintain their structural integrity even at high speeds. This stability is crucial for ensuring smooth and efficient material transport, particularly in manufacturing and packaging industries where speed is a critical factor.
Reduced Vibration and Noise
The construction of EP fabric conveyor belts helps to reduce vibration and noise during high-speed operations. This not only enhances the efficiency of the conveyor system but also contributes to a quieter and more comfortable working environment.
Precision and Accuracy
In applications where precise material handling is required, such as in the electronics or food processing industries, the stability and consistency of EP fabric conveyor belts at high speeds ensure accurate and reliable transport of materials.
Industry-Specific Uses
EP fabric conveyor belts are used in a wide range of industries due to their versatility and performance characteristics. Below, we explore some of the key industries and specific applications where EP fabric conveyor belts are commonly employed.
Mines
In the mining industry, EP fabric conveyor belts are essential for the transportation of ore, coal, and other extracted materials. The harsh conditions and heavy loads associated with mining operations require conveyor belts that are durable, resistant to abrasion, and capable of handling significant tension.
- Material Transport: EP fabric conveyor belts are used to transport materials from extraction sites to processing plants, stockpiles, or loading facilities.
- Crushing and Screening: These belts are also used in crushing and screening operations to move processed materials to different stages of production.
- Safety and Efficiency: The robustness and reliability of EP fabric conveyor belts enhance the safety and efficiency of mining operations by reducing the risk of belt failure and downtime.
Metallurgy
The metallurgical industry involves the processing of metals and alloys, which requires conveyor belts that can withstand high temperatures and abrasive materials.
- High-Temperature Applications: EP fabric conveyor belts are suitable for transporting hot materials, such as molten metal or heated ore, within smelting and refining processes.
- Durability: The belts’ resistance to heat and abrasion ensures long-lasting performance in the demanding conditions of metallurgical operations.
- Efficiency: By maintaining consistent performance under high-stress conditions, EP fabric conveyor belts contribute to the efficiency of metal processing and production.
Architecture
In the construction and architectural industries, EP fabric conveyor belts are used to transport building materials such as sand, gravel, cement, and aggregates.
- Material Handling: These belts facilitate the efficient movement of construction materials to various sites, reducing the need for manual labor and enhancing productivity.
- Robust Construction: The durability and strength of EP fabric conveyor belts ensure that they can handle the rough and heavy materials commonly used in construction.
- Versatility: The belts can be customized to meet specific requirements, such as different widths, lengths, and cover thicknesses, to suit various construction applications.
Ports
Ports and shipping terminals rely on EP fabric conveyor belts for the loading and unloading of bulk materials, such as grain, coal, and minerals.
- Bulk Material Handling: EP fabric conveyor belts are used to transport materials from ships to storage facilities or directly to transport vehicles.
- Efficiency: The belts’ high-speed capabilities and durability enhance the efficiency of port operations by enabling rapid and reliable material movement.
- Environmental Resistance: The belts are designed to withstand the harsh environmental conditions often found in port settings, such as exposure to saltwater, humidity, and varying temperatures.
Electricity
In power generation facilities, EP fabric conveyor belts are used to transport fuel sources, such as coal, biomass, and other materials, to the processing and combustion areas.
- Fuel Transport: The belts facilitate the continuous supply of fuel to power plants, ensuring uninterrupted energy production.
- Heat Resistance: EP fabric conveyor belts’ resistance to high temperatures is crucial for handling materials that are often subjected to elevated temperatures during processing.
- Reliability: The belts’ robust construction ensures reliable performance in the demanding environment of power generation, reducing the risk of operational disruptions.
Chemical Industries
The chemical industry involves the handling and processing of various chemicals and raw materials, requiring conveyor belts that can resist chemical exposure and maintain their integrity under different conditions.
- Chemical Resistance: EP fabric conveyor belts are designed to resist degradation from exposure to chemicals, ensuring long-lasting performance in chemical processing applications.
- Material Transport: The belts are used to transport raw materials, intermediate products, and finished chemicals between different stages of production.
- Safety and Compliance: By providing reliable and safe material handling, EP fabric conveyor belts help chemical plants comply with safety regulations and standards.
EP fabric conveyor belts are an essential component in a wide range of industrial applications, offering numerous advantages that make them ideal for demanding environments. Their suitability for medium to long-distance material conveyance, heavy load handling, and high-speed operations, combined with their industry-specific benefits, ensures that they are a reliable and efficient choice for various sectors. Whether in mining, metallurgy, construction, ports, power generation, or chemical processing, EP fabric conveyor belts provide the strength, durability, and performance needed to enhance productivity and operational efficiency. By understanding the specific applications and benefits of EP fabric conveyor belts, industries can make informed decisions and optimize their material handling processes for improved outcomes.
Detailed Specifications of EP Fabric Conveyor Belt
In the manufacturing and industrial sectors, the use of conveyor belts featuring EP (polyester-polyamide) fabric is prevalent due to their enhanced durability and performance under challenging operational conditions. This detailed section aims to provide a comprehensive understanding of the specifications, properties, and applications of EP fabric conveyor belts, focusing specifically on their construction, fabric types, and performance metrics.
Fabric Type: EP Fabric
The primary material in EP fabric conveyor belts is a blend of polyester and polyamide, commonly known as EP fabric. This fabric is favored in the conveyor belt industry for its excellent balance of flexibility, strength, and cost-effectiveness. Polyester in the warp (lengthwise lay) and polyamide in the weft (crosswise lay) provide these belts with exceptional strength and resistance to mechanical damage and degradation from environmental factors.
Fabric Codes and Properties
EP80 to EP500
EP fabric conveyor belts are categorized based on their fabric type and tensile strength, ranging from EP80 up to EP500. This classification indicates the belt’s capability to withstand maximum working tension without exceeding the prescribed elongation limits. The numbers (80, 100, 150, etc.) typically represent the tensile strength in Newtons per millimeter width of the belt.
Thickness and Strength
Corresponding to the fabric codes, the thickness of the EP fabric layers can vary from 0.9 mm to 2.5 mm. The thickness is crucial as it impacts the belt’s overall durability and its ability to handle various load sizes. Similarly, the strength of the belt, measured in Newtons per millimeter (N/mm), is directly linked to the fabric type and weave density, with options ranging from 80 N/mm to 500 N/mm. These properties ensure that the belts can perform under significant stress and varying pressures, typical in heavy-duty industrial environments.
Cover Thickness
The cover of an EP fabric conveyor belt plays a vital role in protecting the fabric carcass from abrasion, impact, and other surface wear factors. The top cover thickness can vary significantly depending on the intended use of the belt, ranging from 2 mm to 12 mm. Conversely, the bottom cover is generally thinner, varying from 0 to 5 mm. This variation helps in balancing protection with flexibility and weight, which is critical for the efficient operation of the conveyor system.
Number of Fabric Ply
The construction of an EP fabric conveyor belt often involves multiple plies or layers of fabric stacked together to enhance the belt’s structural integrity and operational capabilities. The number of plies in a conveyor belt can vary typically between 2 to 10. Each ply adds to the overall strength and impact resistance of the belt, making it more suitable for different loading conditions and operational demands.
Width and Length
Standard widths of EP fabric conveyor belts range from 350 mm to 2200 mm, accommodating a variety of industrial applications and machinery dimensions. The production length of these belts can extend up to 300 meters per roll, providing substantial coverage and operational continuity for extensive conveyor systems. This flexibility in dimensions allows for tailored solutions to meet specific industrial needs, enhancing efficiency and throughput in operations ranging from mining to packaging.
EP fabric conveyor belts offer a robust, versatile, and efficient solution for various conveying needs. Their detailed specifications, including fabric type, strength, ply count, and dimensional flexibility, make them ideal for a wide range of industrial applications. Understanding these specifications is crucial for selecting the right conveyor belt that meets operational demands while ensuring durability and cost-efficiency.
Comparing EP Fabric Conveyor Belts with Other Types
Conveyor belts are essential components in various industries, and selecting the right type can significantly impact the efficiency and cost-effectiveness of operations. Among the most commonly used are EP (polyester-polyamide) fabric conveyor belts. This section provides a detailed comparison between EP fabric conveyor belts and other prevalent types, specifically NN (Nylon-Nylon) belts and steel cord belts. The comparison covers construction differences, characteristics, properties, and specific applications, offering insights to help choose the most suitable conveyor belt for specific needs.
EP vs. NN Belids
Construction
The primary difference between EP and NN conveyor belts lies in their fabric composition. EP belts are made from polyester in the warp direction and polyamide (nylon) in the weft, offering a good balance between strength and elongation. NN belts, on the other hand, are constructed entirely from nylon both in warp and weft. This difference significantly influences their overall mechanical properties and suitability for various applications.
Characteristics and Properties
EP belts are known for their excellent resistance to mechanical wear and their ability to handle high tensile loads with minimal elongation. NN belts, while also strong, tend to stretch more under load, which can be a crucial factor in applications requiring precise dimensions and alignment.
EP vs. Steel Cord Belts
When comparing EP fabric conveyor belts with steel cord belts, the distinctions become clear in terms of strength, flexibility, and suitable applications. Steel cord belts are ideal for long-distance, high-tensile applications due to their construction, which involves steel cords running longitudinally to provide extraordinary strength.
Strength and Flexibility
Steel cord belts typically offer greater strength and are able to carry larger loads over longer distances without significant elongation, making them suitable for heavy-duty applications. However, EP belts provide better flexibility and are easier to handle and install, especially in systems that require belts to navigate curves and small radii.
Applications
EP belts are generally preferred in industries where flexibility and maneuverability are critical, such as in packaging industries or smaller-scale mining operations. Steel cord belts are favored in applications involving long-distance conveying or where operational conditions are harsh, such as in large-scale mining or aggregate industries.
The choice between EP fabric conveyor belts, NN belts, and steel cord belts should be based on specific operational requirements, including the desired strength, flexibility, environmental conditions, and budget constraints. Each type offers unique benefits and is suited to particular applications, making understanding these differences crucial for optimal selection and use.
Pricing and Standards of EP Fabric Conveyor Belt
The market for EP fabric conveyor belts is complex, with numerous factors influencing both pricing and standards. Understanding these elements is crucial for businesses to make informed purchasing decisions and optimize their operations accordingly. This detailed section will explore the various price factors, applicable standards and specifications, and the engineering and customization possibilities for EP fabric conveyor belts.
Price Factors
The pricing of EP fabric conveyor belts is determined by a multitude of factors, each contributing in various degrees to the final cost of the product. Here are ten critical elements affecting the pricing:
- Material Quality and Type: The quality of the polyester and polyamide used in the fabric impacts the price significantly. Higher-grade materials typically cost more but offer better durability and performance.
- Manufacturing Complexity: The complexity involved in the manufacturing process, including the number of plies and the precision required in aligning and bonding these layers, affects the cost. More complex constructions generally lead to higher prices.
- Belt Dimensions: The width and length of the belt play crucial roles in determining the price. Larger belts require more material and more precise manufacturing processes, increasing the overall cost.
- Strength and Load Capacity: Belts designed to handle higher loads (reflected in their EP rating, such as EP 400/3 or EP 1000/4) are more expensive due to the increased quality and quantity of materials needed.
- Cover Thickness and Material: Thicker and more abrasion-resistant covers cost more. The choice of cover material, whether it is standard or specialized for specific conditions (like oil resistance), also plays a role in the pricing.
- Customization and Modifications: Any custom features, such as special coatings, edge seals, or integrated sensors for monitoring wear and performance, add to the cost.
- Market Demand and Availability: Fluctuations in market demand and the availability of raw materials can affect prices. Higher demand or limited availability of materials can lead to increased prices.
- Geographical Factors: Prices can vary significantly depending on the region, influenced by local economic conditions, the cost of labor, and logistical expenses.
- Regulatory and Safety Standards: Compliance with international safety and quality standards can increase manufacturing costs, which are often passed on to the consumer.
- Volume and Scale of Purchase: Larger orders typically attract lower per-unit prices due to economies of scale in production and shipping.
Standards and Specifications
EP fabric conveyor belts are subject to various standards that specify requirements for their design, testing, and use. These standards ensure that the belts meet minimum safety and performance criteria necessary for their intended applications.
- ISO Standards: The International Organization for Standardization provides globally recognized standards that cover various aspects of conveyor belt specifications, including tensile strength, elongation at break, and abrasion resistance.
- DIN Standards: Deutsches Institut für Normung, which provides standards used primarily in Europe, offers detailed specifications for conveyor belts, including the DIN 22102 standard which covers belt conveyors for bulk material handling.
- RMA (Rubber Manufacturers Association) Standards: In the United States, RMA standards provide guidelines on belt construction, dimensions, and performance characteristics.
- Specific Product Standards: References like EP 400/3 and EP 1000/4 indicate the tensile strength of the belt and the number of fabric plies, guiding buyers in selecting belts that meet their specific operational needs.
Engineering and Customization
The engineering of EP fabric conveyor belts involves detailed design and customization processes to meet specific operational requirements. Customization can range from adjusting the belt size and material type to integrating advanced features for performance monitoring and maintenance.
- Tailored Dimensions: Engineering teams design belts to specific widths and lengths to fit particular conveyor systems and operational parameters.
- Custom Fabric Layers and Ply Configurations: Depending on the required strength and flexibility, belts can be engineered with varying numbers of plies and specific types of fabric weaves.
- Specialized Covers: Depending on the application, the covers of the belts can be engineered to resist specific environmental challenges such as oils, chemicals, heat, or cold.
- Integrated Technologies: Incorporation of sensors and RFID tags to monitor belt wear and track usage is an increasingly common customization that adds value by enhancing maintenance capabilities and operational efficiency.
The pricing and standards of EP fabric conveyor belts are influenced by a wide range of factors, from material and manufacturing details to market dynamics and regulatory frameworks. Understanding these elements is essential for making strategic decisions regarding conveyor belt investments, ensuring both cost-efficiency and operational effectiveness.
Request a quote and more details about our EP fabric conveyor belts by filling out the form.
FAQs about EP Fabric Conveyor Belt
EP in conveyor belts stands for “Polyester-Polyamide,” commonly referred to as Polyester-Nylon. This type of belt construction utilizes Polyester (E) fibers in the warp direction—responsible for the belt’s length—and Nylon (P) fibers in the weft direction, which contributes to the width’s tensile strength. EP belts are renowned for their exceptional strength, durability, and low stretch properties, making them ideal for long-distance, high-abuse, and heavy-duty applications in various industries. The Polyester component provides strength and resistance to moisture and heat, while Nylon adds flexibility and impact resistance, enhancing the overall performance of the belt under challenging conditions.
The primary difference between EP (Polyester-Nylon) belts and NN (Nylon-Nylon) belts lies in their construction materials. EP belts are made with a Polyester warp and Nylon weft, while NN belts are constructed entirely from Nylon fibers both in the warp and the weft. This difference in material construction affects the belt’s overall properties and suitability for specific applications. EP belts generally offer higher tensile strength, lower stretch, and better heat resistance compared to NN belts, making them suitable for longer and more demanding conveyance needs. NN belts, on the other hand, are more suited to applications requiring greater elasticity and shock absorption due to the high elasticity of the Nylon fibers.
The elongation of an EP (Polyester-Nylon) conveyor belt is a critical factor in determining its operational efficiency. Typically, EP belts are designed to have low elongation, which translates to less stretch under load. This property is crucial for maintaining stable and aligned operations, especially over long distances. The elongation percentage of EP belts generally ranges between 1.5% to 2% at 10% of the maximum belt strength. This low elongation helps in reducing the maintenance requirements and enhances the longevity of the belt, making EP belts a preferred choice in heavy-load and long-distance conveying systems.
A fabric conveyor belt consists of multiple layers of fabric materials that are coated with rubber compounds for protection and to aid in the transmission of force. The primary types of fabrics used in these belts are Nylon (NN), Polyester (EP), and sometimes cotton. Each fabric layer, known as a ply, contributes to the belt’s overall tensile strength and impact resistance. Fabric conveyor belts are versatile and can be tailored to meet various industrial applications based on the type of fabric and the specific properties required, like heat resistance, abrasion resistance, or oil resistance. They are widely used across different sectors such as mining, agriculture, manufacturing, and packaging due to their efficiency, durability, and cost-effectiveness.
Last Updated on July 31, 2024 by Jordan Smith
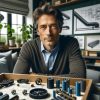
Jordan Smith, a seasoned professional with over 20 years of experience in the conveyor system industry. Jordan’s expertise lies in providing comprehensive solutions for conveyor rollers, belts, and accessories, catering to a wide range of industrial needs. From initial design and configuration to installation and meticulous troubleshooting, Jordan is adept at handling all aspects of conveyor system management. Whether you’re looking to upgrade your production line with efficient conveyor belts, require custom conveyor rollers for specific operations, or need expert advice on selecting the right conveyor accessories for your facility, Jordan is your reliable consultant. For any inquiries or assistance with conveyor system optimization, Jordan is available to share his wealth of knowledge and experience. Feel free to reach out at any time for professional guidance on all matters related to conveyor rollers, belts, and accessories.