High Strength EP Rubber Belt for Multilayer Conveying
EP rubber conveyor belts are integral components in industrial material handling systems, providing reliable and efficient solutions for transporting bulk materials across various sectors. EP stands for Polyester-Nylon, referring to the combination of polyester fabric (for the longitudinal direction) and nylon fabric (for the latitudinal direction). This fabric composition results in a belt with superior strength, flexibility, and durability, making EP belts ideal for heavy-duty applications.
The construction of EP belts typically includes a top rubber cover, carcass (the fabric layers), and a bottom rubber cover. These belts are designed to withstand high tension, offering low elongation, impact resistance, and excellent flexibility. These qualities align with the conveyor belt design parameters, ensuring that the belt performs efficiently under demanding conditions while maintaining its integrity over time. EP belts are particularly suited for transporting bulk or lumpy materials such as ores, aggregates, coal, sand, clinker, chemicals, and more. They excel in long-distance and high-speed transport, making them widely used in industries like mining, cement production, power generation, metallurgy, and chemical processing.
One of the key advantages of EP rubber belts is their resistance to wear, abrasion, moisture, and environmental factors. The polyester fibers provide stability and low stretch, while the nylon fibers contribute flexibility, tear resistance, and impact strength. The result is a durable belt that performs well under extreme conditions and in heavy-load environments.
Thanks to their robust performance characteristics, EP rubber belts are a versatile solution for bulk material handling, ensuring efficient operation across various industrial applications, from quarrying and crushing to transportation in power stations and chemical plants.The rubber conveyor belt, with its strength and durability, is equally vital in these environments, ensuring reliable material transport even under demanding conditions.
What is an EP Rubber Belt?
An EP rubber belt is a type of conveyor belt that is commonly used in industrial material handling applications, particularly for transporting bulk materials over long distances. The “EP” in the name stands for Polyester-Nylon, which refers to the specific combination of synthetic fabrics used in the belt’s construction. This unique blend of polyester and nylon fibers provides the belt with a combination of strength, flexibility, and durability that makes it suitable for a wide range of demanding industrial environments.
Composition
The composition of an EP rubber belt is what sets it apart from other types of conveyor belts. The belt is made up of polyester fabric for the longitudinal direction (warp) and nylon fabric for the latitudinal direction (weft). Polyester is known for its low elongation and high tensile strength, meaning the belt can maintain its shape and resist stretching under load. Nylon, on the other hand, contributes to the belt’s flexibility, tear resistance, and impact strength, making the belt able to handle sudden impacts and heavy loads without sustaining damage. This makes it an ideal material for a conveyor belt for heavy loads, where durability and resistance to wear are essential for reliable performance. Together, these materials provide the EP belt with excellent overall performance, making it suitable for high-load, high-speed, and long-distance applications.
Construction
The construction of an EP rubber belt involves multiple layers to ensure its strength, durability, and resistance to wear. At the core of the belt is the EP fabric, which is made up of layers of polyester and nylon fibers. These fabric plies are then coated with rubber skim coats, which help bond the fabric layers together and provide additional adhesion between the fabric and the rubber covers. This process ensures a strong, durable connection, which is crucial when paired with rubber coated steel rollers, enhancing the overall efficiency and longevity of the conveyor system.
The top and bottom covers are added to protect the fabric carcass from environmental factors such as abrasion, heat, moisture, and chemicals. These covers also help to protect the material being transported from contamination. The number of fabric plies and the thickness of the covers can vary depending on the specific application requirements. Some belts may have as few as two plies, while others may feature up to six or more for added strength and load-bearing capacity.
Performance Characteristics
EP rubber belts are known for their exceptional performance characteristics, which make them ideal for use in heavy-duty industrial applications.
Advantages of EP Rubber Belts
EP rubber belts offer a wide range of advantages, making them an essential component in industrial material handling systems. These belts are designed to withstand the harsh conditions typical of many industrial environments, providing reliability, durability, and efficiency in transporting bulk materials. Below are the key advantages of EP rubber belts:
Low Longitudinal Elongation for Stability and Efficiency
One of the standout features of EP rubber belts is their low longitudinal elongation, meaning the belt does not stretch or expand significantly under load. This characteristic ensures that the belt maintains its proper tension and alignment throughout its service life, providing stability to the conveyor system. Stability is crucial because excessive elongation can lead to slippage, improper tracking, and eventual failure of the system. The low elongation of EP belts contributes to operational efficiency by reducing the need for frequent adjustments and belt replacements. This makes them ideal for systems that require consistent performance over long distances and high throughput.
Superior Resistance to Wear, Rot, and Moisture
EP rubber belts are known for their superior resistance to wear, rot, and moisture, which makes them highly durable in challenging environmental conditions. The wear resistance of these belts ensures that they can handle abrasive materials, such as gravel, sand, or coal, without quickly showing signs of damage or excessive wear. The moisture resistance is particularly valuable in industries where belts are exposed to wet conditions, such as mining, agriculture, or food processing. EP belts do not absorb water, which helps prevent the growth of mildew and other forms of deterioration, extending the lifespan of the belt and reducing maintenance costs. Additionally, their rot resistance allows them to perform well in environments prone to humidity or wetness, where other belts might degrade over time.
Flexibility and Troughing Ability for Continuous Material Transport
EP rubber belts are highly flexible, which is an essential property for handling materials over both straight and curved sections of the conveyor system. The flexibility of the EP belt ensures that it can easily conform to the curvature of the conveyor path without compromising its structural integrity. This flexibility allows for smooth material transfer and continuous transport of materials, whether they are fine powders, coarse aggregates, or even large lump materials.
In addition to flexibility, EP belts have excellent troughing ability, which means they can form a trough-like shape when loaded with materials. This troughing effect allows the belt to better contain and move materials, reducing the risk of spillage and increasing the efficiency of the transportation process. This is particularly important in industries where high-volume, bulk materials need to be conveyed over long distances, such as in mining, cement production, and grain handling.
High Tensile Strength and Durability for Heavy-Duty Applications
Another key advantage of EP rubber belts is their high tensile strength, which allows them to handle heavy-duty applications with ease. The polyester component of the EP fabric gives the belt exceptional strength, while the nylon fabric contributes to tear resistance and impact strength. This makes EP belts capable of withstanding the weight and force associated with large, heavy, or rugged materials, such as crushed stone, ore, and gravel.
The high tensile strength of these belts ensures that they can carry heavier loads over longer distances without experiencing excessive wear or failure. In heavy-duty environments such as mining, quarrying, or steel manufacturing, where conveyor systems are subject to extreme loads and harsh conditions, the durability of EP rubber belts reduces the frequency of belt replacements and maintenance downtime, ultimately leading to cost savings for businesses.
Compatibility with Various Rubber Types for Diverse Industrial Uses
EP rubber belts are highly compatible with different types of rubber, which makes them adaptable to a wide range of industrial applications. Depending on the specific needs of an industry or application, EP rubber belts can be customized with different rubber compounds for heat resistance, oil resistance, acid and alkali resistance, or even fire resistance. This versatility allows EP belts to be used in diverse environments, ranging from high-temperature applications in steel mills to oil-resistant belts in petrochemical plants, or abrasion-resistant belts in mining.
Furthermore, the high compatibility with various rubbers allows manufacturers to design EP belts that can handle a variety of materials, from fine powders to large lumps, in a multitude of different industries. This flexibility in material and compound selection ensures that EP rubber belts can be optimized for a specific use case, whether it’s for handling food-grade materials, high-temperature environments, or chemical-resistant applications.
Applications of EP Rubber Belts
EP rubber belts are used across a broad spectrum of industries due to their exceptional durability, flexibility, and versatility. They are highly adaptable to a wide range of environmental and operational conditions, making them ideal for material handling in both standard and extreme situations. Below, we explore some of the key industries and applications where EP rubber belts are commonly used.
Mining
Mining operations involve transporting heavy, abrasive, and often sharp materials such as coal, minerals, ores, and aggregates. EP rubber belts are essential in these settings due to their high tensile strength, abrasion resistance, and flexibility, which enable them to withstand the wear and tear associated with bulk material handling. They can efficiently convey materials over long distances, whether through tunnels, underground shafts, or open-pit mines, while maintaining optimal performance even in harsh conditions.
The ability of EP belts to handle extreme impact forces, as well as their resistance to wear and tear, makes them ideal for transporting mined materials from extraction points to processing plants or stockpiles.
Steel Mills
In steel mills, conveyors are tasked with moving hot, heavy materials such as molten slag, steel scrap, and finished steel products. EP rubber belts used in these applications must be capable of enduring high temperatures, abrasive surfaces, and heavy loads. Specially designed EP belts with heat-resistant rubber compounds can withstand extreme temperatures without degrading, ensuring consistent material transport from the furnaces to other parts of the mill.
The flexibility and impact resistance of EP rubber belts are also critical in steel mills where materials are often subjected to sudden drops and heavy impact forces.
Power Stations
Power stations, especially coal-fired and nuclear plants, rely on conveyor systems to move coal, fly ash, and other materials throughout the facility. A coal conveyor system is essential in these settings, ensuring efficient and continuous transportation of bulk materials while maintaining safety and operational efficiency. EP rubber belts are commonly used in these settings for material handling, particularly for coal transport from storage areas to boilers or to other parts of the plant. Their resistance to abrasion, moisture, and wear makes them well-suited for these environments, where materials are often moved in large volumes and over long distances.
Moreover, EP rubber belts can be designed with additional fire-resistant coatings to meet safety standards in power stations, where there is a heightened risk of fire due to the flammable nature of certain materials.
Chemical Plants
Chemical plants handle a wide range of substances, from granules and powders to liquids and chemicals. EP rubber belts are used for transporting these materials safely and efficiently. Their resistance to various chemicals—such as acids, alkalis, oils, and solvents—makes them an ideal choice for material handling in chemical manufacturing, especially in environments where contamination or degradation of the belt could affect the final product.
EP belts are also capable of handling high-load and abrasive materials commonly used in chemical processing, including sand, granules, and pharmaceutical ingredients. The belts’ flexibility and ability to withstand moisture also make them effective for wet-processing applications.
Cement Plants
Cement production involves the handling of raw materials such as limestone, clay, gypsum, and various additives, which are moved between different stages of production. EP rubber belts are widely used in cement plants due to their abrasion resistance and ability to convey heavy and sharp materials over long distances. The durability of EP belts helps ensure the continuous operation of cement production lines, even under the high-impact and dusty conditions typical of these plants.
The belts’ resistance to moisture and chemical exposure is also essential, as cement production involves a significant amount of moisture and exposure to alkaline substances. EP belts are designed to handle these challenges, ensuring long service life and minimal downtime for maintenance.
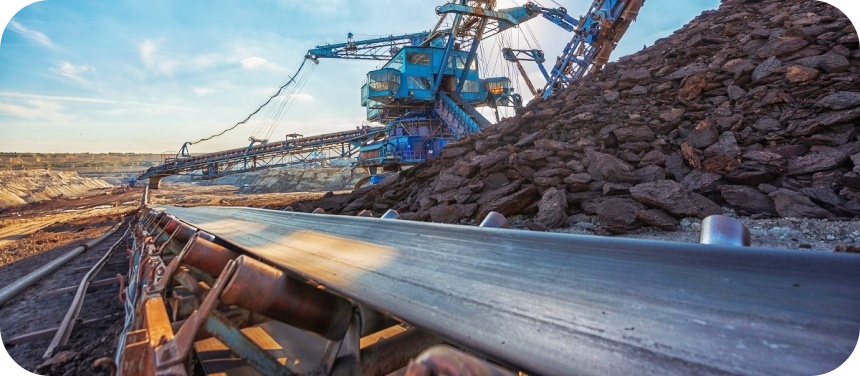
Agriculture
In agriculture, EP rubber belts are used for grain handling, fertilizer transport, and seed processing, among other tasks. These belts are suitable for transporting a wide variety of agricultural materials, ranging from fine powders like flour to bulk grains such as wheat, rice, and corn. Their flexibility and ability to handle fragile products without causing damage make them an essential part of agricultural processing systems.
EP belts also perform well in humid and dusty environments, both of which are common in agricultural settings. Their moisture resistance helps to prevent the absorption of water, which can degrade other types of conveyor belts and affect material flow. In addition, the low elongation of EP belts ensures efficient grain handling and minimizes the need for constant re-tensioning.
Bulk Material Handling (General Industries)
EP rubber belts are also used in a variety of general industries that require bulk material handling. These industries include construction, recycling, food processing, and automotive. Whether conveying building materials, food products, or waste, EP rubber belts provide a reliable solution for moving materials from one stage of production to another.
For example, in construction, EP belts are used for transporting aggregates such as gravel, sand, and crushed stone, where their abrasion resistance and high tensile strength come into play. Similarly, in food processing, EP belts are used to convey everything from grains to fresh produce, where they need to meet hygiene and material handling requirements.
Heavy-Duty Loads and Extreme Conditions
EP rubber belts are particularly well-suited to environments where heavy-duty loads and extreme conditions prevail. Their ability to handle materials in high-impact settings (such as mining, steel mills, and quarries) makes them indispensable for industries that require continuous and reliable material transport. Additionally, EP belts are engineered to resist challenges such as temperature fluctuations, oily or greasy environments, and abrasive forces, ensuring they perform effectively across a variety of difficult conditions.
Adaptability to Temperature Variations and Environmental Stress
One of the significant benefits of EP rubber belts is their adaptability to temperature extremes and environmental stresses. Whether exposed to freezing temperatures in cold storage facilities or high heat in manufacturing plants, EP rubber belts retain their integrity and performance. Some EP belts are specifically designed with heat-resistant compounds to withstand temperatures of up to 150°C (302°F) or more, making them ideal for high-temperature environments like those in steel production or power generation.
EP Rubber Belt Sizes: Understanding Belt Specifications and Selection
The size and specifications of EP rubber belts play a crucial role in determining their effectiveness for a specific industrial application. The right belt size ensures optimal performance, durability, and reliability in material handling, while preventing issues such as excessive wear, slippage, or overloading. Below, we will explore the common sizes available, the relationship between key dimensions such as width, thickness, and tensile strength, and how to select the appropriate size based on the application’s requirements.
Overview of Common Belt Sizes Available in the Market
EP rubber belts come in a wide range of sizes and specifications to cater to various material handling applications. These belts are typically available in widths ranging from 300mm to 2500mm and thicknesses from 3mm to 25mm, with varying numbers of plies to provide different levels of strength and durability. The most commonly used EP rubber belts are available in widths from 300mm to 2500mm and thicknesses from 3mm to 25mm. The number of plies can range from 2 to 6, depending on the required strength and load-bearing capacity.
What is the Relationship Between Belt Width, Thickness, and Tensile Strength
The width, thickness, and tensile strength of an EP rubber belt are interconnected, and each affects the belt’s overall performance and suitability for a given task. Here’s how they relate:
Belt Width
The width of a rubber belt determines how much material it can carry at once. Wider belts have higher load-bearing capacities, which is especially important for industries like mining, steel mills, or cement plants, where large volumes of heavy materials need to be transported. Belt widths typically range from 300mm to 2500mm. The appropriate width is selected based on the amount of material to be conveyed and the width of the conveyor system.
Belt Thickness
The thickness of the rubber belt influences its strength, resistance to wear, and ability to withstand heavy loads. Thicker belts are typically used for transporting heavier and more abrasive materials, as they provide added impact resistance and longer service life. Belt thickness usually ranges from 3mm to 25mm, with thicker belts (around 15mm to 25mm) being used for heavy-duty applications where the material handling involves sharp or abrasive objects.
Tensile Strength
Tensile strength is a measure of a belt’s resistance to breaking under tension. It is directly related to the number of plies and the type of fabric used. Higher tensile strength is required for applications involving high-load conditions. The strength of the EP rubber belt is generally determined by the fabric ply count and the tensile properties of the rubber compound itself. EP belts usually have tensile strengths ranging from 400N/mm to 2500N/mm, depending on the ply and fabric type.
How to Select the Appropriate Size Based on Application Needs
Choosing the correct EP rubber belt size depends on several factors such as load capacity, conveying distance, conveyor speed, and the material characteristics being transported. Here’s how to approach selecting the right belt for your application:
1. Load Capacity
The belt must be able to carry the load without excessive stretching or damage. The higher the load, the more important it becomes to select a belt with sufficient tensile strength and thickness. For heavy-duty applications, choose a belt with a high number of plies (e.g., 5 or 6 plies) and a thicker rubber cover.
2. Conveying Distance
The distance over which the material will be transported affects the belt width and the number of plies. Longer conveyors may require wider belts to accommodate the increased material volume, while the number of plies should be increased to ensure the belt can handle the added tension and weight over longer distances.
3. Conveyor Speed
Conveyor speed can also influence belt selection. Higher speeds require belts that are more resistant to wear and elongation. For high-speed conveyors, a belt with lower elongation properties (typically thicker and with more plies) is ideal to maintain tension and minimize stretch.
4. Material Characteristics
The characteristics of the material being conveyed are crucial to selecting the correct belt size. For example, sharp, heavy, or abrasive materials require a thicker belt with a higher ply count to withstand impact and abrasion. On the other hand, light, non-abrasive materials can be handled with a thinner, less robust belt.
5. Environmental Conditions
Consider the operating environment, including temperature extremes, moisture, and exposure to chemicals. EP belts can be customized with various rubber compounds to improve abrasion resistance, heat resistance, or chemical resistance depending on the environment.
Example: Selecting an EP Rubber Belt for a Mining Application
For a mining operation where the material being transported is coal (which is abrasive and heavy), a wide, thick belt with a high number of plies (e.g., 1600mm width, 20mm thickness, 6-ply design) would be needed to support the load and resist wear over long distances.
For lighter material like grains in an agricultural setting, a narrower belt (e.g., 600mm width) with a lower ply count (e.g., 2-ply, 8mm thick) might suffice.
Choosing the Right EP Rubber Belt Size
Selecting the appropriate EP rubber belt size is essential for optimizing performance, ensuring safety, and maximizing the lifespan of the conveyor system. Several key factors should be considered to ensure the belt meets the specific demands of the application. Below are the most important considerations when choosing the right EP belt size:
Belt Length and Width Relative to Material Volume and Transport Distance
The length and width of the EP rubber belt should be selected based on the volume of material being transported and the distance it needs to be conveyed.
For high-volume applications, such as mining or cement manufacturing, where large amounts of bulk materials need to be moved, the belt width might range from 1200mm to 2500mm.
For lighter loads, such as in agriculture or packaging, narrower belts (e.g., 300mm to 600mm) may be sufficient.
Environmental Factors (Temperature, Moisture, Chemical Exposure)
The operating environment plays a crucial role in determining the appropriate EP rubber belt size and type. Belts used in harsh conditions, such as high temperatures, chemical exposure, or environments with high moisture levels, require specific rubber compounds and construction features to ensure performance and durability.
Required Strength and Flexibility for Specific Applications
The strength and flexibility of the belt should match the specific demands of the material being conveyed and the conditions under which the belt will operate.
Belt Tension, Elongation, and Safety Considerations
Proper belt tension is crucial for ensuring the efficient operation of the conveyor system and preventing unnecessary wear or damage to the belt.
Durability and Maintenance Requirements
Durability is another essential factor in choosing the right EP rubber belt size. Belts used in heavy-duty applications like mining, construction, or steel mills need to be able to handle high-impact loads and abrasive materials without premature wear. Maintenance should also be a key consideration: certain applications may require frequent inspections or specific repair techniques. EP belts that are more abrasion-resistant and require less maintenance are often favored in environments where high material throughput is a priority.
Performance and Durability of EP Rubber Belt
EP rubber belts are designed to perform reliably under high load and long-distance transport conditions. Their performance and durability are critical factors in industries that rely on continuous material movement, such as mining, cement production, steel mills, and agriculture. Here’s an overview of how EP belts perform in these demanding environments and how to ensure their longevity through proper maintenance.
High Load and Long-Distance Transport Conditions
EP rubber belts are specifically engineered to handle heavy-duty loads and operate efficiently over long distances. The combination of polyester fabric (for warp) and nylon fabric (for weft) gives EP belts superior tensile strength, flexibility, and resistance to wear, making them suitable for continuous transport of bulk materials.
Maintenance Tips to Ensure the Longevity of EP Belts
To maximize the performance and service life of EP rubber belts, regular maintenance is necessary. Below are some key maintenance tips:
Common Issues Faced with EP Belts and Troubleshooting
Despite their durability, EP rubber belts can face various issues over time, especially under heavy usage and harsh conditions. Below are some common issues and their troubleshooting methods:
FAQs about EP Rubber Belt
What does EP mean in conveyor belts?
EP stands for Polyester-Nylon fabric in conveyor belts, where “E” refers to polyester and “P” refers to nylon. These materials are chosen for their specific properties that make them ideal for heavy-duty applications. Polyester, used for the longitudinal strength (warp), offers high tensile strength and low elongation, ensuring the belt can carry heavy loads without stretching too much. Nylon, used for the transverse strength (weft), gives the belt greater flexibility and resilience, making it highly resistant to impacts and wear. Together, these materials create a robust, durable, and flexible belt that can withstand various harsh conditions in industries such as mining, agriculture, and manufacturing. EP conveyor belts are especially favored for their strength, low elongation, and ability to perform efficiently over long distances. They are widely used in the transport of bulk materials such as coal, gravel, and cement.
What is the difference between EP and NN belts?
The primary difference between EP (Polyester-Nylon) and NN (Nylon-Nylon) conveyor belts lies in the materials used for their construction, specifically the fabric plies. EP belts are made with polyester for the longitudinal direction and nylon for the transverse direction, while NN belts use nylon for both directions. This difference in fabric composition impacts the belts’ performance characteristics. EP belts are known for their low elongation, making them ideal for applications where minimal stretch is needed, particularly when transporting heavy loads over long distances. In contrast, NN belts have higher elasticity due to the use of nylon in both directions, which makes them more flexible but also more prone to elongation. NN belts are better suited for applications where flexibility and impact resistance are required, such as in mining, while EP belts are preferred in applications that demand strength, low stretch, and resistance to moisture, oil, and chemicals.
What is a conveyor belt EP 800 4?
A conveyor belt labeled EP 800/4 refers to a specific type of EP rubber belt with certain technical specifications. The “EP” signifies the use of Polyester-Nylon fabric, while the number 800 indicates the tensile strength of the belt, measured in N/mm (Newton per millimeter). In this case, 800 N/mm represents the maximum force the belt can withstand before it breaks, indicating that this belt is designed for medium-heavy to heavy-duty applications. The “4” refers to the number of plies (fabric layers) in the belt construction. Therefore, an EP 800/4 conveyor belt has four layers of fabric for additional strength and durability. This type of belt is typically used in industries such as mining, cement production, power plants, and other heavy industries where robust performance is essential for transporting bulk materials over long distances with high load capacity.
What is EP fabric?
EP fabric refers to the specific type of fabric used in the construction of EP conveyor belts, which are made from a combination of Polyester and Nylon fibers. The term “EP fabric” specifically indicates that the belt is woven with Polyester fibers running in the longitudinal direction (warp), providing high tensile strength and low elongation for strength under heavy loads. The Nylon fibers are used in the transverse direction (weft) to provide flexibility, impact resistance, and enhanced durability. This combination of fabrics is chosen for its ability to withstand heavy loads, high tension, and long-distance transportation, making EP belts particularly suited for mining, construction, and agriculture. The Polyester-Nylon fabric design results in a conveyor belt with improved performance characteristics, such as resistance to moisture, wear, and aging, as well as reduced elongation compared to other types of conveyor belts like NN belts.
CONTACT US
Let us help you find a better solution!