Maintenance and Care Tips for EPDM Conveyor Belt
EPDM conveyor belt is made from Ethylene Propylene Diene Monomer, a synthetic rubber known for its excellent heat, ozone, and weather resistance. These properties make EPDM an ideal material for conveyor belts used in harsh environments. The development of EPDM conveyor belts dates back several decades, with continuous improvements enhancing their durability and performance. The importance of EPDM in conveyor belts lies in its ability to withstand extreme temperatures and harsh chemicals, making it a preferred choice in industries such as automotive, mining, and food processing.
EPDM Conveyor Belt: Properties and Advantages
EPDM (Ethylene Propylene Diene Monomer) is a type of synthetic rubber that has become a popular material for manufacturing conveyor belts due to its exceptional properties. The use of EPDM in conveyor belts offers a range of benefits, making it an ideal choice for various industrial applications. This section will provide a detailed explanation of EPDM material properties and the advantages of using EPDM conveyor belts in different industries.
Detailed Explanation of EPDM Material Properties
EPDM conveyor belts are known for their unique set of properties that make them highly effective and reliable in demanding conditions. Here are the key properties of EPDM material:
- Heat Resistance: One of the most notable properties of EPDM is its excellent heat resistance. EPDM conveyor belts can withstand high temperatures, making them suitable for industries where materials are processed or transported at elevated temperatures. This heat resistance ensures that the belts maintain their integrity and performance even under thermal stress.
- Durability: EPDM is renowned for its durability and longevity. The material is resistant to cracking, abrasion, and general wear and tear, which significantly extends the lifespan of the conveyor belts. This durability translates into lower maintenance costs and reduced downtime for industrial operations.
- Flexibility: EPDM conveyor belts exhibit superior flexibility, allowing them to handle various loads and operate efficiently over pulleys and around bends. This flexibility is crucial for applications requiring smooth and consistent movement of materials.
- Chemical Resistance: EPDM has excellent resistance to a wide range of chemicals, including acids, alkalis, and oxidizing agents. This chemical resistance makes EPDM conveyor belts suitable for industries where exposure to harsh chemicals is common, ensuring that the belts do not degrade or lose their functionality over time.
- Weather and Ozone Resistance: EPDM conveyor belts are highly resistant to weathering and the effects of ozone. This makes them ideal for outdoor applications where they are exposed to environmental elements such as UV radiation, ozone, and varying weather conditions. The belts retain their properties and performance, even after prolonged exposure to harsh environments.
- Electrical Insulation: EPDM is an excellent electrical insulator, which can be beneficial in applications where static electricity poses a risk. The material’s insulating properties help prevent static buildup and reduce the risk of electrical discharges that could potentially cause fires or damage to the materials being transported.
- Water Resistance: EPDM’s resistance to water and moisture ensures that the conveyor belts remain functional in wet conditions. This property is particularly useful in industries such as food processing and wastewater treatment, where exposure to water is frequent.
Advantages of Using EPDM Conveyor Belts in Various Industries
The unique properties of EPDM conveyor belts translate into several advantages for various industries. Here are some of the key benefits:
- Extended Service Life: Due to their durability and resistance to wear, EPDM conveyor belts have a longer service life compared to belts made from other materials. This results in lower replacement frequency, reducing overall costs for industries relying on conveyor systems.
- Reduced Maintenance Costs: The robustness of EPDM belts minimizes the need for frequent maintenance and repairs. Industries can benefit from decreased downtime and lower maintenance expenses, enhancing overall operational efficiency.
- Versatility Across Industries: EPDM conveyor belts are suitable for a wide range of industries due to their diverse properties. For example:
- Manufacturing: The heat and chemical resistance of EPDM belts make them ideal for manufacturing processes involving high temperatures and exposure to chemicals.
- Mining: The durability and abrasion resistance ensure that EPDM belts can handle the harsh conditions and heavy loads typical in mining operations.
- Food Processing: The water resistance and flexibility of EPDM belts make them suitable for transporting food products, ensuring hygiene and smooth operation.
- Automotive: EPDM’s ability to withstand high temperatures and chemicals makes these belts perfect for automotive manufacturing and assembly lines.
- Environmental Resistance: The weather and ozone resistance of EPDM conveyor belts allow them to be used in outdoor applications without degrading. This is particularly advantageous for industries with outdoor processing or material handling needs, such as construction and agriculture.
- Safety and Reliability: The electrical insulating properties of EPDM belts enhance safety by reducing the risk of static buildup and electrical discharges. This makes them suitable for environments where flammable materials are present, ensuring safer operations.
- Energy Efficiency: The flexibility and low rolling resistance of EPDM conveyor belts contribute to energy efficiency. These belts require less power to operate, which can result in significant energy savings for industries with extensive conveyor systems.
- Customization and Adaptability: EPDM conveyor belts can be customized to meet specific industry requirements. Whether it’s adjusting the belt thickness, width, or incorporating special features like profiles or cleats, EPDM belts can be tailored to optimize performance for particular applications.
Case Studies of EPDM Conveyor Belt Applications
To illustrate the practical benefits of EPDM conveyor belts, let’s explore a few case studies:
- Steel Industry: In the steel industry, conveyor belts must endure extremely high temperatures and abrasive conditions. EPDM conveyor belts are used to transport hot steel slabs, coils, and other materials, providing excellent heat resistance and durability. This reduces downtime and maintenance costs, improving overall productivity.
- Chemical Processing: Chemical processing plants often deal with corrosive substances that can degrade conventional conveyor belts. EPDM conveyor belts, with their superior chemical resistance, are employed to handle various chemicals, ensuring longevity and reliability. This helps maintain continuous operations and minimizes contamination risks.
- Food and Beverage: In the food and beverage industry, hygiene and safety are paramount. EPDM conveyor belts are used in the transportation of food products, offering resistance to water and cleaning agents. Their flexibility allows for smooth operation, ensuring that delicate food items are not damaged during transit.
- Waste Management: Waste management facilities use conveyor belts to handle various types of waste, including wet and potentially hazardous materials. EPDM conveyor belts, with their water resistance and durability, are ideal for these conditions. They ensure efficient waste processing and reduce the frequency of belt replacements.
EPDM conveyor belts offer a combination of properties that make them highly effective and versatile for a wide range of industrial applications. Their heat resistance, durability, flexibility, and resistance to chemicals, weather, and ozone make them an excellent choice for industries requiring reliable and long-lasting conveyor solutions. By choosing EPDM conveyor belts, industries can benefit from reduced maintenance costs, extended service life, and improved operational efficiency, making them a valuable investment for any conveyor system.
Applications of EPDM Conveyor Belt
EPDM conveyor belts, crafted from Ethylene Propylene Diene Monomer, offer unique properties that make them indispensable across various industries. This section will delve into the common industries utilizing EPDM conveyor belts, specific applications within these sectors, and provide case studies or examples showcasing the successful implementation of these versatile belts.
Common Industries That Use EPDM Conveyor Belts
- Automotive Industry
The automotive industry is one of the primary users of EPDM conveyor belts. These belts are essential for handling components during the manufacturing and assembly processes. EPDM’s excellent resistance to heat and oil makes it ideal for environments where engines and other automotive parts are produced. The belts help in the efficient transportation of heavy components and materials, contributing to streamlined production lines. - Food Processing Industry
In the food processing industry, the hygienic properties of EPDM conveyor belts are highly valued. EPDM is resistant to many chemicals and can withstand high and low temperatures, making it perfect for food production environments that require strict sanitary conditions. These belts are used in the transport of raw materials, packaging of finished products, and even in environments that require rigorous cleaning protocols. - Mining Industry
The mining industry operates in some of the most demanding environments, where equipment must endure extreme conditions. EPDM conveyor belts are used extensively in mining operations for their durability and resistance to harsh weather conditions. These belts can transport heavy loads of minerals and ores, withstand abrasive materials, and perform reliably under constant stress. - Chemical Industry
EPDM conveyor belts are also crucial in the chemical industry, where they are used to transport a variety of chemicals safely. The belts’ resistance to acids, alkalis, and other corrosive substances ensures that they maintain their integrity and functionality over long periods, even when exposed to harsh chemicals. - Pharmaceutical Industry
In the pharmaceutical industry, the purity and reliability of EPDM conveyor belts are essential. These belts are used in the production and packaging of pharmaceuticals, where any contamination must be avoided. EPDM’s resistance to various chemicals and its ability to be thoroughly cleaned make it ideal for this sensitive industry. - Construction Industry
The construction industry uses EPDM conveyor belts for moving construction materials such as sand, gravel, and cement. The belts’ strength and ability to withstand harsh outdoor conditions make them suitable for construction sites where equipment is exposed to the elements.
Specific Applications Within These Industries
- Automotive Industry Applications
- Engine Assembly Lines: EPDM conveyor belts are used to transport engine parts and assemblies through various stages of the production line.
- Body Shop Operations: These belts are essential in moving car body panels and frames between welding, painting, and assembly stations.
- Component Testing and Inspection: EPDM belts ensure that components are moved efficiently through testing and quality control processes.
- Food Processing Industry Applications
- Raw Material Handling: EPDM belts transport raw ingredients to different processing areas.
- Packaging Lines: They are used in automated packaging systems to move products from filling stations to packing and sealing areas.
- Sanitation Processes: The belts’ resistance to cleaning chemicals and hot water makes them suitable for conveyor systems that require frequent sanitation.
- Mining Industry Applications
- Ore Transportation: EPDM conveyor belts are used in transporting extracted ores from mining sites to processing plants.
- Crushing and Screening: They move crushed minerals and rocks through various screening and sorting stages.
- Waste Management: EPDM belts are utilized in the disposal and management of mining waste materials.
- Chemical Industry Applications
- Chemical Production Lines: EPDM belts transport raw chemicals through different stages of production, ensuring contamination-free processing.
- Storage and Distribution: They are used in systems that move chemicals to storage tanks and distribution units.
- Safety and Containment: EPDM’s chemical resistance ensures safe handling and containment of hazardous substances.
- Pharmaceutical Industry Applications
- Tablet and Capsule Production: EPDM belts are integral to the machinery that produces and sorts tablets and capsules.
- Packaging Operations: These belts are used in automated systems that package pharmaceuticals into blister packs and bottles.
- Sterilization and Clean Rooms: The belts’ ability to withstand sterilization processes makes them ideal for cleanroom environments.
- Construction Industry Applications
- Material Transport: EPDM belts move construction materials from storage areas to work sites.
- Debris Removal: They are used to transport waste materials and debris away from construction zones.
- Concrete Handling: The belts handle the movement of wet and dry concrete during construction projects.
Case Studies or Examples of Successful EPDM Conveyor Belt Implementations
- Automotive Manufacturer: Efficient Production Line
Nitta automotive manufacturer implemented EPDM conveyor belts in its engine assembly line to replace older belts that frequently failed due to heat exposure. The new EPDM belts significantly reduced downtime and maintenance costs. The belts’ heat resistance allowed for continuous operation without degradation, leading to a 20% increase in production efficiency. - Food Processing Plant: Improved Hygiene Standards
Alea food processing company specializing in dairy products integrated EPDM conveyor belts into its production line. The belts’ resistance to dairy fats and cleaning chemicals ensured compliance with hygiene standards. The seamless, non-porous surface of the EPDM belts prevented bacterial growth, which previously plagued the company with contamination issues. This change led to an overall improvement in product quality and a reduction in health code violations. - Mining Operation: Enhanced Durability
A large mining operation faced challenges with conveyor belts that frequently wore out due to abrasive materials. Switching to EPDM conveyor belts provided enhanced durability and longer life spans. The EPDM belts withstood the harsh conditions, reducing the frequency of belt replacements and operational disruptions. This led to a more consistent workflow and reduced operational costs. - Chemical Plant: Safe Chemical Handling
Purt chemical manufacturing plant adopted EPDM conveyor belts to handle corrosive chemicals. The previous belts degraded quickly under exposure to various chemicals, causing frequent replacements and safety concerns. EPDM belts offered superior chemical resistance, significantly reducing maintenance needs and improving safety protocols. The plant reported a 30% decrease in maintenance costs and enhanced worker safety. - Pharmaceutical Company: Sterile Production Environment
Kitt pharmaceutical company required conveyor belts for its sterile production environment, where contamination was unacceptable. EPDM belts, with their excellent chemical resistance and ease of cleaning, were chosen to replace conventional belts. The EPDM belts maintained sterility and withstood regular sterilization processes. This transition improved compliance with industry regulations and boosted overall production efficiency. - Construction Project: Robust Material Handling
A major construction project involved extensive material handling requirements. EPDM conveyor belts were employed to transport heavy construction materials and debris. The belts demonstrated superior strength and weather resistance, ensuring uninterrupted operation throughout the project’s duration. The use of EPDM belts enhanced project timelines and reduced equipment downtime, contributing to the successful completion of the project ahead of schedule.
EPDM conveyor belts have proven their worth across multiple industries due to their exceptional properties, including heat resistance, chemical resistance, and durability. From automotive and food processing to mining and pharmaceuticals, these belts offer reliable performance in demanding environments. The specific applications and case studies highlighted in this section underscore the versatility and effectiveness of EPDM conveyor belts. As industries continue to seek reliable and efficient solutions for their material handling needs, EPDM conveyor belt remains a top choice for ensuring seamless operations and enhanced productivity.
Selecting the Right EPDM Conveyor Belt
Choosing the right EPDM conveyor belt for your specific needs is a crucial step in ensuring efficient and reliable operation. EPDM (Ethylene Propylene Diene Monomer) belts are prized for their durability, heat resistance, and chemical resistance, making them suitable for a wide range of industrial applications. This section will provide a comprehensive guide on selecting the right EPDM conveyor belt by discussing key factors to consider, tips for selecting the appropriate belt dimensions, and guidance on evaluating belt quality and performance.
Key Factors to Consider When Choosing an EPDM Conveyor Belt
- Application Requirements
Understanding the specific requirements of your application is the first step in selecting the right EPDM conveyor belt. Consider the following:
- Load Capacity: Determine the weight and type of materials the belt will carry. EPDM belts are available in various strengths to handle different load capacities.
- Operating Environment: Consider the environmental conditions, such as temperature extremes, exposure to chemicals, or outdoor use. EPDM is known for its excellent resistance to heat, cold, and chemicals, but specific grades may offer additional benefits.
- Speed and Tension: Assess the speed at which the belt will operate and the tension it will be subjected to. This will influence the belt’s durability and performance.
- Material Characteristics
EPDM conveyor belts are designed with specific material characteristics that provide advantages in various applications:
- Heat Resistance: EPDM belts can withstand high temperatures, making them suitable for applications involving heat exposure.
- Chemical Resistance: The material’s resistance to chemicals, oils, and acids is crucial for industries like food processing and chemicals.
- Durability: EPDM belts offer excellent durability and resistance to wear and tear, ensuring a long service life.
- Regulatory Compliance
Ensure that the EPDM conveyor belt complies with industry standards and regulations relevant to your application. For instance, food-grade EPDM belts should meet FDA regulations, while belts used in explosive environments should comply with ATEX standards. - Cost Considerations
Evaluate the cost of the EPDM conveyor belt in relation to its expected lifespan and performance. While higher-quality belts may have a higher initial cost, they can offer better value through reduced maintenance and longer service life.
Tips for Selecting the Appropriate Belt Thickness, Width, and Length
- Determining the Correct Thickness
The thickness of the EPDM conveyor belt is crucial for its performance and longevity. Here are some tips to determine the correct thickness:
- Load Bearing: Thicker belts are generally more capable of handling heavier loads. Ensure the belt thickness matches the weight requirements of your application.
- Flexibility Needs: For applications requiring high flexibility, such as in smaller pulleys or tight turns, thinner belts are preferable.
- Environmental Factors: Consider the environmental conditions, as thicker belts may provide better resistance to abrasion and wear in harsh environments.
- Choosing the Right Width
The width of the EPDM conveyor belt should correspond to the conveyor system and the material being transported:
- System Specifications: Ensure the belt width matches the specifications of your conveyor system to avoid misalignment or operational issues.
- Material Characteristics: The width should be sufficient to accommodate the materials without spillage or overflow. Wider belts are preferable for bulkier materials.
- Selecting the Appropriate Length
The length of the EPDM conveyor belt is determined by the design of the conveyor system:
- Conveyor Layout: Measure the distance between pulleys and account for any additional length needed for tensioning and splicing.
- Belt Stretch: Consider the potential for belt stretch over time, and factor this into the length measurement to maintain proper tension and alignment.
Guidance on Evaluating Belt Quality and Performance
- Material Quality
Assess the quality of the EPDM material used in the conveyor belt. High-quality EPDM will have uniform thickness, consistent surface finish, and no visible defects. The material should exhibit the expected properties, such as heat and chemical resistance, without degradation. - Manufacturing Standards
Ensure that the EPDM conveyor belt is manufactured to high standards, including:
- Dimensional Accuracy: The belt should meet precise dimensional specifications for thickness, width, and length.
- Tensile Strength: High tensile strength ensures the belt can withstand operational stresses without stretching or breaking.
- Abrasion Resistance: Check for the belt’s resistance to abrasion, which is critical for applications involving heavy or abrasive materials.
- Performance Testing
Evaluate the performance of the EPDM conveyor belt through testing and certification:
- Load Testing: Conduct load tests to ensure the belt can handle the maximum weight requirements of your application.
- Heat and Chemical Resistance Tests: Test the belt’s resistance to heat and chemicals in controlled conditions to verify its suitability for your operating environment.
- Longevity Tests: Assess the belt’s durability through simulated long-term use to predict its service life and maintenance needs.
- Supplier Reputation
Choose a reputable supplier known for producing high-quality EPDM conveyor belts. Consider factors such as:
- Industry Experience: Suppliers with extensive experience in producing conveyor belts for your industry are likely to provide reliable products.
- Customer Feedback: Look for reviews and testimonials from other customers to gauge the supplier’s reliability and product quality.
- Technical Support: Ensure the supplier offers technical support and guidance for installation, maintenance, and troubleshooting.
- Warranty and After-Sales Service
A good warranty indicates confidence in the product’s quality. Check the warranty terms and ensure that the supplier provides comprehensive after-sales service, including:
- Replacement Policies: Understand the conditions under which belts can be replaced under warranty.
- Maintenance Services: Some suppliers offer maintenance and inspection services to ensure optimal belt performance and longevity.
Case Study: Successful Implementation of EPDM Conveyor Belts
Company Overview
Alea food processing company faced challenges with their existing conveyor belts, which frequently degraded due to exposure to cleaning chemicals and high temperatures. The company decided to switch to EPDM conveyor belts to improve reliability and reduce maintenance costs.
Application Requirements
The company needed conveyor belts that could handle:
- Frequent Cleaning: The belts had to withstand daily cleaning with hot water and chemical disinfectants.
- High Temperatures: The belts were exposed to high temperatures during certain processing stages.
- Heavy Loads: The belts needed to transport heavy loads of raw and processed food products.
Selection Process
The company followed a detailed selection process:
- Identified Key Factors: They prioritized chemical resistance, heat resistance, and load capacity.
- Selected Appropriate Dimensions: Based on their conveyor system, they chose belts with the correct thickness, width, and length.
- Evaluated Quality: They tested sample belts for material quality, tensile strength, and abrasion resistance.
Implementation and Results
After selecting and installing the EPDM conveyor belts, the company observed significant improvements:
- Reduced Downtime: The new belts required less frequent replacements, reducing downtime.
- Enhanced Hygiene: The belts’ resistance to chemicals ensured better hygiene and compliance with food safety standards.
- Cost Savings: Maintenance costs dropped due to the belts’ durability and longer service life.
Selecting the right EPDM conveyor belt involves a thorough understanding of your application requirements, careful consideration of key factors, and a meticulous evaluation of belt quality and performance. By following these guidelines, you can ensure that your EPDM conveyor belt meets your operational needs, enhances efficiency, and provides long-term reliability. Whether for automotive, food processing, mining, or any other industry, the right EPDM conveyor belt can significantly improve your material handling processes and contribute to the overall success of your operations.
Maintenance and Care of EPDM Conveyor Belt
EPDM conveyor belts are known for their durability and resilience in various industrial applications. However, like all industrial equipment, proper maintenance and care are essential to ensure their longevity and optimal performance. This section delves into best practices for maintaining EPDM conveyor belts, common issues and troubleshooting tips, as well as recommended cleaning and storage methods to extend the belt’s lifespan.
Best Practices for Maintaining EPDM Conveyor Belts
Maintaining EPDM conveyor belts involves regular inspection, timely repairs, and adherence to operational guidelines. Here are some best practices to follow:
- Regular Inspections: Conduct routine inspections to identify signs of wear and tear, such as cracks, abrasions, or misalignment. Regular checks help detect potential issues early, preventing costly repairs and downtime.
- Proper Tensioning: Ensure that the conveyor belt is properly tensioned. Over-tensioning can lead to excessive wear and damage, while under-tensioning can cause slippage and inefficient operation. Use tension gauges and follow the manufacturer’s recommendations for optimal tension levels.
- Alignment Checks: Misalignment can cause uneven wear and reduce the belt’s lifespan. Regularly check the alignment of the belt and pulleys, and make necessary adjustments to keep the belt running straight and true.
- Lubrication: Lubricate the conveyor components, such as bearings and rollers, to reduce friction and wear. Use lubricants recommended by the manufacturer to ensure compatibility with EPDM materials.
- Load Management: Avoid overloading the conveyor belt, as excessive weight can strain the belt and its components. Distribute the load evenly to prevent localized wear and extend the belt’s operational life.
- Environmental Controls: Protect the conveyor belt from extreme environmental conditions. For instance, if the belt operates in high-temperature environments, ensure that cooling mechanisms are in place to prevent overheating. Similarly, in chemical exposure settings, ensure that the belt is resistant to the specific chemicals used.
Common Issues and Troubleshooting Tips
Despite the robustness of EPDM conveyor belts, certain issues can arise during their operation. Here are common problems and troubleshooting tips:
- Belt Slippage: This occurs when the belt loses traction with the drive pulley. Causes include insufficient tension, worn pulleys, or contamination on the belt or pulley. To troubleshoot, increase the belt tension, replace worn pulleys, and clean any contaminants from the belt and pulleys.
- Tracking Problems: If the belt does not run straight, it may wander off course, leading to edge damage and reduced efficiency. Check for misaligned pulleys or improper loading. Adjust the pulleys to ensure proper alignment and evenly distribute the load on the belt.
- Excessive Wear: Abrasion and wear are common issues in conveyor belts. Causes can include rough material handling, improper belt tension, or environmental factors. To mitigate wear, use wear-resistant covers, ensure proper tensioning, and protect the belt from harsh environmental conditions.
- Belt Breakage: This can be due to overloading, excessive tension, or physical damage. Inspect the belt for any visible signs of stress or damage and replace it if necessary. Ensure that the belt is not overloaded and that the tension is within recommended limits.
- Material Build-Up: Accumulation of materials on the belt or components can cause operational issues. Regularly clean the belt and components to prevent build-up. Use scrapers and brushes to remove debris and ensure smooth operation.
Recommended Cleaning and Storage Methods to Extend Belt Lifespan
Proper cleaning and storage of EPDM conveyor belts are crucial for maintaining their performance and extending their lifespan. Here are some recommended methods:
- Cleaning:
- Regular Cleaning: Clean the conveyor belt regularly to remove dirt, debris, and any spilled materials. Use mild detergents and water to wash the belt surface. Avoid using harsh chemicals that can degrade the EPDM material.
- Deep Cleaning: Periodically perform deep cleaning to remove stubborn residues. Use soft brushes or sponges to scrub the belt gently. Ensure that all cleaning agents are thoroughly rinsed off to prevent chemical damage.
- Drying: After cleaning, ensure the belt is completely dry before resuming operation. Moisture can cause slippage and promote the growth of mold or mildew, which can damage the belt over time.
- Storage:
- Proper Positioning: Store the conveyor belt in a cool, dry, and well-ventilated area. Avoid direct sunlight, as UV radiation can degrade the EPDM material. Roll the belt loosely and place it on a flat surface to prevent deformation.
- Temperature Control: Store the belt in an environment with stable temperatures. Extreme temperature fluctuations can cause the material to expand and contract, leading to potential damage.
- Protection from Contaminants: Keep the belt away from oils, chemicals, and sharp objects during storage. These can cause contamination and physical damage to the belt.
- Periodic Inspections: Even during storage, periodically inspect the belt for signs of damage or degradation. Address any issues promptly to ensure the belt remains in good condition for future use.
By adhering to these best practices for maintenance, troubleshooting common issues effectively, and following recommended cleaning and storage methods, the lifespan and performance of EPDM conveyor belts can be significantly enhanced. Proper care ensures that these belts continue to provide reliable service in various industrial applications, maximizing their value and efficiency.
The maintenance and care of EPDM conveyor belts are essential for ensuring their optimal performance and longevity. By following best practices, addressing common issues promptly, and maintaining proper cleaning and storage methods, industries can benefit from the robust and durable properties of EPDM conveyor belts, ensuring smooth and efficient operations across various applications.
Leading Manufacturers of EPDM Conveyor Belt
When it comes to selecting an EPDM conveyor belt, choosing the right manufacturer is crucial for ensuring quality, reliability, and performance. This section provides an overview of some of the top EPDM conveyor belt manufacturers, highlighting their products, services, and innovations. It also outlines key factors to consider when choosing a manufacturer, ensuring you make an informed decision that meets your operational needs.
Overview of Top EPDM Conveyor Belt Manufacturers
- Nitta Corporation
Nitta Corporation is a well-known name in the conveyor belt industry, particularly noted for its high-quality EPDM conveyor belts. Founded in 1885, Nitta has a long history of innovation and excellence in producing industrial belts. Their EPDM belts are used across various industries, including automotive, food processing, and mining, due to their exceptional durability and resistance to heat and chemicals. - ContiTech AG
ContiTech AG, a division of Continental AG, is one of the leading manufacturers of conveyor belts, including EPDM variants. With a strong focus on technological advancements and sustainability, ContiTech offers a wide range of EPDM conveyor belts designed to meet the needs of different industries. Their belts are known for their superior quality, longevity, and performance under extreme conditions. - Fenner Dunlop
Fenner Dunlop is a global leader in the manufacture of conveyor belts, providing innovative solutions for over 150 years. Their EPDM conveyor belts are engineered to withstand harsh environments, making them ideal for industries such as mining and construction. Fenner Dunlop’s commitment to research and development ensures their products incorporate the latest advancements in material science and manufacturing techniques. - Habasit
Habasit is a leading manufacturer of conveyor belts and power transmission belts, including a range of EPDM conveyor belts. Founded in 1946, the Swiss company is renowned for its dedication to quality and customer satisfaction. Habasit’s EPDM belts are widely used in the food and beverage industry, thanks to their hygienic properties and resistance to cleaning agents. - Ammeraal Beltech
Ammeraal Beltech is a global conveyor belt manufacturer known for its innovative and high-performance products. Their EPDM conveyor belts are designed for various applications, including logistics, automotive, and food processing. Ammeraal Beltech’s focus on continuous improvement and customer-centric solutions has positioned them as a trusted partner in the industry. - Sparks Belting
Sparks Belting is a leading manufacturer and supplier of custom conveyor belts, including EPDM varieties. With a strong emphasis on customer service and bespoke solutions, Sparks Belting caters to a wide range of industries, offering belts that are tailored to specific operational requirements. Their EPDM belts are known for their durability, flexibility, and resistance to extreme temperatures.
Highlighting Their Products, Services, and Innovations
- Nitta Corporation
- Products: Nitta offers a comprehensive range of EPDM conveyor belts that are designed for high performance in demanding applications. Their belts are available in various thicknesses, widths, and lengths to suit different industrial needs.
- Services: Nitta provides extensive customer support, including installation, maintenance, and technical assistance. They also offer custom belt solutions to meet specific operational requirements.
- Innovations: Nitta continuously invests in research and development to enhance the performance and longevity of their EPDM conveyor belts. Their innovations include advanced manufacturing techniques and the use of high-quality materials to ensure superior product performance.
- ContiTech AG
- Products: ContiTech’s EPDM conveyor belts are known for their high resistance to heat, chemicals, and abrasion. They offer a wide range of belts for various applications, including heavy-duty and high-temperature environments.
- Services: ContiTech provides comprehensive services, including belt installation, maintenance, and technical support. They also offer belt monitoring systems to ensure optimal performance and longevity.
- Innovations: ContiTech is at the forefront of innovation in the conveyor belt industry, with a focus on sustainability and energy efficiency. Their latest products incorporate advanced materials and technologies to reduce energy consumption and environmental impact.
- Fenner Dunlop
- Products: Fenner Dunlop offers a diverse range of EPDM conveyor belts designed for durability and reliability in harsh environments. Their belts are available in various specifications to meet the demands of different industries.
- Services: Fenner Dunlop provides a full suite of services, including belt installation, repair, and maintenance. They also offer custom belt solutions and technical support to ensure optimal performance.
- Innovations: Fenner Dunlop’s commitment to innovation is evident in their continuous development of new products and technologies. Their focus on material science and manufacturing techniques ensures their EPDM belts are at the cutting edge of performance and durability.
- Habasit
- Products: Habasit’s EPDM conveyor belts are designed for high performance and hygienic applications, particularly in the food and beverage industry. Their belts are available in various configurations to suit different operational needs.
- Services: Habasit offers extensive customer support, including installation, maintenance, and training services. They also provide custom belt solutions to meet specific application requirements.
- Innovations: Habasit’s dedication to innovation is reflected in their development of advanced belt materials and manufacturing processes. Their focus on quality and performance ensures their EPDM belts meet the highest industry standards.
- Ammeraal Beltech
- Products: Ammeraal Beltech offers a wide range of EPDM conveyor belts designed for various applications, including logistics, automotive, and food processing. Their belts are known for their high performance and reliability.
- Services: Ammeraal Beltech provides comprehensive services, including belt installation, maintenance, and technical support. They also offer custom belt solutions to meet specific operational needs.
- Innovations: Ammeraal Beltech’s focus on continuous improvement and customer-centric solutions drives their innovation. Their latest products incorporate advanced materials and technologies to enhance performance and reduce environmental impact.
- Sparks Belting
- Products: Sparks Belting’s EPDM conveyor belts are designed for durability, flexibility, and resistance to extreme temperatures. They offer a range of belts tailored to specific industrial applications.
- Services: Sparks Belting provides a full range of services, including custom belt design, installation, and maintenance. Their customer-centric approach ensures they meet the unique needs of each client.
- Innovations: Sparks Belting continuously invests in research and development to enhance the performance and longevity of their EPDM conveyor belts. Their innovations include the use of advanced materials and manufacturing techniques to ensure superior product quality.
Factors to Consider When Choosing a Manufacturer
- Reputation and Experience
- Choose a manufacturer with a strong reputation and extensive experience in producing EPDM conveyor belts. Established manufacturers are more likely to offer high-quality products and reliable services.
- Look for customer reviews and testimonials to gauge the manufacturer’s reliability and customer satisfaction levels.
- Product Quality
- Ensure the manufacturer uses high-quality materials and advanced manufacturing processes to produce EPDM conveyor belts. High-quality belts will offer better performance, durability, and longevity.
- Check for certifications and compliance with industry standards, which indicate the manufacturer’s commitment to quality.
- Customization and Flexibility
- Select a manufacturer that offers custom solutions to meet your specific operational requirements. Customization options include belt thickness, width, length, and material composition.
- Flexibility in manufacturing and design allows for tailored solutions that enhance the efficiency and performance of your conveyor system.
- Technical Support and Services
- Choose a manufacturer that provides comprehensive technical support and after-sales services. This includes installation assistance, maintenance services, and troubleshooting support.
- A manufacturer with a robust support system can help ensure the optimal performance and longevity of your EPDM conveyor belts.
- Innovation and Sustainability
- Consider manufacturers that are committed to innovation and sustainability. Look for companies that invest in research and development to improve their products and incorporate environmentally friendly practices.
- Innovative manufacturers are more likely to offer advanced products that enhance efficiency and reduce operational costs.
- Cost and Value
- Evaluate the cost of the EPDM conveyor belts in relation to their expected performance and lifespan. While higher-quality belts may have a higher initial cost, they often offer better value through reduced maintenance and longer service life.
- Consider the total cost of ownership, including installation, maintenance, and replacement costs, to make an informed decision.
Selecting the right manufacturer for your EPDM conveyor belt is a critical decision that can significantly impact the performance and efficiency of your conveyor system. By considering factors such as reputation, product quality, customization options, technical support, innovation, and cost, you can choose a manufacturer that meets your specific needs and provides reliable, high-quality EPDM conveyor belts. The leading manufacturers highlighted in this section—Nitta Corporation, ContiTech AG, Fenner Dunlop, Habasit, Ammeraal Beltech, and Sparks Belting—are renowned for their excellence and innovation in the conveyor belt industry, making them worthy contenders for your consideration.
FAQs about EPDM Conveyor Belt
Conveyor belts typically utilize various types of rubber depending on the specific application and operational environment. The most common types of rubber used are natural rubber and synthetic rubbers like SBR (Styrene-Butadiene Rubber), NBR (Nitrile Butadiene Rubber), and EPDM (Ethylene Propylene Diene Monomer). Natural rubber is prized for its flexibility and resilience, making it suitable for general-purpose conveyor belts. SBR is commonly used for its abrasion resistance and durability, making it ideal for heavy-duty applications. NBR is preferred for oil-resistant belts due to its ability to withstand exposure to oils and chemicals. EPDM is chosen for its excellent heat, weather, and ozone resistance, making it suitable for outdoor and high-temperature applications. The selection of rubber type is crucial to ensure the conveyor belt’s longevity, performance, and suitability for specific industrial needs.
The strongest conveyor belts are typically steel cord conveyor belts. These belts are reinforced with steel cables, which provide exceptional tensile strength and durability, allowing them to handle high-tension applications and heavy loads over long distances. Steel cord conveyor belts are commonly used in mining, port facilities, and other heavy industries where reliability and strength are paramount. The tensile strength of these belts can exceed 10,000 N/mm, making them suitable for the most demanding tasks. Additionally, their construction allows for a high degree of flexibility and resistance to impact and abrasion, further enhancing their longevity and performance. By using steel cord reinforcement, these conveyor belts can effectively transport large volumes of materials with minimal maintenance and downtime, ensuring efficient and continuous operations.
Conveyor belts are made from a variety of materials, each chosen for specific properties suited to different applications. Common materials include natural rubber, synthetic rubbers like SBR and NBR, and fabric reinforcements such as polyester, nylon, and cotton. For higher durability and strength, materials such as steel cables are used in steel cord conveyor belts. In specialized applications, materials like PVC (polyvinyl chloride), PU (polyurethane), and silicone are used for their unique properties, such as chemical resistance, heat resistance, and flexibility. The choice of material depends on factors like the type of material being transported, environmental conditions, and the required belt properties. For instance, food-grade conveyor belts might use polyurethane due to its non-toxic and easy-to-clean nature, while high-temperature applications might require silicone for its heat resistance.
Grade 1 and Grade 2 conveyor belts differ primarily in their abrasion resistance and intended applications. Grade 1 conveyor belts are designed for high abrasion resistance, making them suitable for transporting materials that are particularly abrasive, such as rocks, ore, and gravel. These belts are built to withstand more wear and tear, thus offering a longer service life in harsh conditions. Grade 2 conveyor belts, on the other hand, provide moderate abrasion resistance and are used in less demanding applications where the materials being transported are not as abrasive. These belts are more economical and are often used in industries like agriculture, light manufacturing, and logistics. While Grade 2 belts are still durable and reliable, they are not intended for the extreme conditions that Grade 1 belts can handle. Choosing between Grade 1 and Grade 2 belts depends on the specific requirements of the operation and the nature of the materials being conveyed.
Last Updated on May 22, 2024 by Jordan Smith
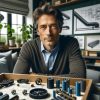
Jordan Smith, a seasoned professional with over 20 years of experience in the conveyor system industry. Jordan’s expertise lies in providing comprehensive solutions for conveyor rollers, belts, and accessories, catering to a wide range of industrial needs. From initial design and configuration to installation and meticulous troubleshooting, Jordan is adept at handling all aspects of conveyor system management. Whether you’re looking to upgrade your production line with efficient conveyor belts, require custom conveyor rollers for specific operations, or need expert advice on selecting the right conveyor accessories for your facility, Jordan is your reliable consultant. For any inquiries or assistance with conveyor system optimization, Jordan is available to share his wealth of knowledge and experience. Feel free to reach out at any time for professional guidance on all matters related to conveyor rollers, belts, and accessories.