ESS Belt Cleaners: Enhance Your Conveyor System Efficiency
ESS belt cleaners, specifically the ESS secondary scrapers, are designed to ensure conveyor belt systems operate at peak efficiency. These secondary scrapers are installed after primary scrapers to remove any remaining materials, providing an additional layer of cleaning to keep belts free from stubborn debris and residues.
ESS Belt Cleaners: Effective Belt Cleaning Solutions
ESS Plough: Effective Belt Cleaning Solutions
Overview of ESS Plough for Conveyor Belts
ESS belt cleaners are designed to maintain the optimal performance of conveyor systems, and the ESS plough is a key component in this regard. The ESS plough is a specialized device that effectively removes material buildup on the conveyor belt, particularly at the tail end where the belt transitions from carrying material to returning empty. By preventing material from getting stuck and causing belt damage or misalignment, the ESS plough ensures smooth and efficient conveyor operation.
ESS ploughs are typically mounted at strategic points along the conveyor belt to intercept and remove larger chunks of material before they can cause any issues. They are constructed from durable materials to withstand harsh industrial environments and are designed for easy installation and maintenance. The ESS plough operates by applying consistent pressure to the belt surface, scraping off debris and directing it away from the belt to prevent recirculation.
Key Features and Advantages of Using ESS Plough
The ESS plough is equipped with several key features that make it an essential tool for effective belt cleaning:
- Durable Construction: ESS ploughs are made from high-quality, wear-resistant materials that ensure long-lasting performance even in demanding conditions. The robust design minimizes the need for frequent replacements, reducing maintenance costs.
- Adjustable Design: The plough can be easily adjusted to apply the correct pressure on the conveyor belt, ensuring effective cleaning without causing damage to the belt surface. This flexibility allows for customized cleaning solutions tailored to specific operational requirements.
- Efficient Material Removal: The ESS plough is designed to remove large pieces of debris and buildup that primary cleaners might miss. By intercepting these materials, the plough prevents them from recirculating on the return side of the belt, reducing the risk of belt wear and misalignment.
- Easy Installation and Maintenance: The ESS plough is designed for quick and easy installation, with minimal downtime required. Maintenance is straightforward, with easily accessible components that can be replaced or adjusted as needed.
- Versatility: The ESS plough is suitable for use with a wide range of conveyor belt types and sizes, making it a versatile solution for various industrial applications. Whether used in mining, quarrying, or bulk material handling, the plough adapts to different operational environments.
- Improved Safety: By preventing material buildup and reducing the risk of belt slippage, the ESS plough enhances the overall safety of the conveyor system. A cleaner belt means fewer chances of material spillage, which can create hazardous working conditions.
Applications and Effectiveness in Various Industries
The effectiveness of ESS belt cleaners, particularly the ESS plough, is evident across a range of industries that rely on conveyor systems for material handling. Here are some key applications:
- Mining Industry: In mining operations, conveyor belts are used to transport bulk materials such as ore, coal, and minerals. The ESS plough helps maintain the cleanliness of these belts, ensuring efficient and uninterrupted material transport. By preventing material buildup, the plough minimizes the risk of belt damage and extends the lifespan of the conveyor system.
- Quarrying: Similar to mining, quarrying involves the transport of heavy and abrasive materials like stone and gravel. The ESS plough effectively removes these materials from the belt, preventing them from causing wear and tear. This leads to reduced maintenance costs and improved operational efficiency.
- Bulk Material Handling: Industries such as agriculture, food processing, and manufacturing often deal with bulk materials that can cause buildup on conveyor belts. The ESS plough provides an effective solution for keeping belts clean, ensuring smooth and efficient handling of materials. This is particularly important in food processing, where cleanliness is crucial for product quality and safety.
- Recycling: In recycling facilities, conveyor belts are used to transport various types of waste materials. The ESS plough helps keep these belts free from debris and contaminants, improving the efficiency of sorting and processing operations. By preventing material buildup, the plough also reduces the risk of belt jams and equipment damage.
- Cement and Aggregate: In the cement and aggregate industry, conveyor belts transport materials like cement, sand, and aggregate. The ESS plough ensures these materials are effectively removed from the belt, preventing buildup that can lead to belt misalignment and reduced productivity. The plough’s durability and efficiency make it a valuable tool in maintaining the smooth operation of conveyor systems in these industries.
- Power Generation: Conveyor belts are used in power plants to transport coal, ash, and other materials. The ESS plough helps keep these belts clean, ensuring efficient and reliable transport of materials essential for power generation. By preventing material buildup, the plough reduces the risk of belt failures and operational disruptions.
ESS belt cleaners, including the ESS plough, are essential tools for maintaining the efficiency and reliability of conveyor systems across various industries. The plough’s durable construction, adjustable design, and efficient material removal capabilities make it a valuable addition to any conveyor belt cleaning system. By preventing material buildup and reducing maintenance requirements, the ESS plough helps improve operational efficiency, safety, and cost-effectiveness. Whether used in mining, quarrying, bulk material handling, recycling, cement and aggregate, or power generation, the ESS plough provides effective belt cleaning solutions that enhance the performance and longevity of conveyor systems.
ESS Belt Cleaners: ESS Engineering – Innovating Belt Cleaning Technologies
The development of advanced belt cleaning technologies has been pivotal in ensuring the efficiency and reliability of conveyor systems across various industries. At the forefront of this innovation is ESS Engineering, a company renowned for its contributions to the field. ESS Belt Cleaners are the result of extensive research, cutting-edge engineering, and a deep understanding of the challenges faced in maintaining clean and efficient conveyor belts. This section delves into the role of ESS engineering in developing these advanced solutions, the engineering principles behind ESS products, and the notable innovations that have had a significant impact on conveyor systems.
Role of ESS Engineering in Developing Advanced Belt Cleaning Solutions
ESS Engineering has played a crucial role in transforming belt cleaning technologies through its commitment to innovation and excellence. The company’s approach to developing ESS belt cleaners involves a thorough analysis of industry needs, continuous research, and the application of advanced engineering techniques. This commitment ensures that ESS products meet the highest standards of performance and reliability.
One of the primary roles of ESS Engineering is to address the common issues associated with conveyor belt systems, such as material carryback, belt mistracking, and excessive wear. By developing effective belt cleaners, ESS Engineering helps minimize these issues, leading to improved operational efficiency, reduced maintenance costs, and enhanced safety. The company’s expertise in mechanical engineering, material science, and fluid dynamics allows it to create products that are not only effective but also durable and easy to maintain.
ESS Engineering also places a strong emphasis on customization. Understanding that different industries and applications have unique requirements, ESS engineers work closely with clients to develop tailored solutions that address specific challenges. This client-centric approach ensures that ESS belt cleaners are versatile and can be adapted to various operational environments.
Overview of Engineering Principles Behind ESS Products
The engineering principles behind ESS belt cleaners are rooted in a combination of advanced technology and practical design. These principles ensure that ESS products are efficient, durable, and easy to maintain. Key engineering concepts include:
- Effective Cleaning Mechanisms:
- ESS belt cleaners are designed with advanced scraping and cleaning mechanisms that effectively remove material carryback from conveyor belts. The use of precise angles and high-quality materials ensures maximum contact with the belt surface, leading to efficient cleaning and reduced wear.
- Durability and Material Selection:
- The materials used in ESS belt cleaners are selected for their durability and resistance to wear and corrosion. This includes high-grade stainless steel, polyurethane, and other specialized materials that can withstand harsh operational conditions. The choice of materials extends the lifespan of the cleaners and reduces maintenance requirements.
- Ease of Maintenance:
- ESS Engineering focuses on designing products that are easy to maintain and service. This includes features like quick-release mechanisms, modular designs, and easy access to replaceable parts. Such features minimize downtime and ensure that maintenance can be carried out quickly and efficiently.
- Customization and Flexibility:
- Understanding that no two conveyor systems are identical, ESS belt cleaners are designed with flexibility in mind. They can be customized to fit different belt widths, speeds, and operational conditions. This adaptability ensures optimal performance in a wide range of applications.
- Energy Efficiency:
- ESS products are engineered to operate efficiently, minimizing energy consumption while maximizing cleaning effectiveness. This includes the use of aerodynamic designs and low-friction materials that reduce the energy required to operate the cleaners.
Notable Innovations and Their Impact on Conveyor Systems
ESS Engineering has introduced several notable innovations in the field of belt cleaning, each contributing to improved performance and reliability of conveyor systems. Some of these innovations include:
- Dynamic Belt Cleaner Designs:
- ESS Engineering has developed dynamic belt cleaners that adjust their cleaning angle and pressure in response to changes in belt conditions. This adaptive technology ensures consistent cleaning performance, even as the belt wears or loads vary.
- Advanced Tensioning Systems:
- Effective tensioning is critical for maintaining contact between the cleaner and the belt. ESS has introduced advanced tensioning systems that automatically adjust tension to compensate for belt stretch and wear. This ensures continuous, effective cleaning without the need for frequent manual adjustments.
- Composite Materials:
- The use of composite materials in ESS belt cleaners has enhanced their durability and performance. These materials offer superior resistance to abrasion and impact, extending the lifespan of the cleaners and reducing the frequency of replacements.
- Integrated Monitoring Systems:
- ESS Engineering has incorporated smart technology into their belt cleaners, including sensors and monitoring systems that provide real-time data on cleaner performance. This information helps operators optimize cleaning processes, predict maintenance needs, and prevent potential issues before they cause downtime.
- Environmentally Friendly Solutions:
- Recognizing the importance of sustainability, ESS has developed environmentally friendly belt cleaners that use less water and energy while still providing effective cleaning. These innovations help reduce the environmental impact of conveyor operations and support sustainable mining and material handling practices.
ESS Belt Cleaners: ESS Parts – Essential Components for Belt Cleaners
High-quality parts are the backbone of any reliable belt cleaning system. ESS parts are designed and manufactured to meet stringent standards, ensuring that ESS belt cleaners operate efficiently and effectively. This section explores the essential components used in ESS belt cleaning systems, the importance of high-quality parts for system performance, and a guide to selecting and replacing ESS parts.
Detailed Look at ESS Parts Used in Belt Cleaning Systems
ESS belt cleaners are composed of various parts, each playing a critical role in the overall functionality and performance of the cleaning system. Some of the essential components include:
- Scrapers and Blades:
- The scrapers and blades are the primary cleaning elements of ESS belt cleaners. They are typically made from high-grade polyurethane, stainless steel, or other durable materials. These parts are designed to effectively remove carryback material from the belt surface, ensuring a clean and efficient conveyor system.
- Tensioners and Mounting Systems:
- Tensioners ensure that the scrapers maintain the correct pressure against the belt. ESS tensioners are designed to be easily adjustable, providing consistent cleaning performance and compensating for belt wear. Mounting systems secure the scrapers and other components to the conveyor frame, ensuring stability and proper alignment.
- Cleaning Systems and Spray Bars:
- In systems where water or other cleaning agents are used, spray bars and cleaning systems are crucial components. These parts distribute the cleaning agents evenly across the belt, enhancing the removal of stubborn materials and reducing the risk of buildup.
- Support and Wear Liners:
- Support and wear liners protect the conveyor frame and extend the life of the belt cleaners. These components are made from materials that resist abrasion and impact, ensuring that the belt cleaners operate smoothly and efficiently.
- Control and Monitoring Systems:
- Advanced ESS belt cleaners may include control and monitoring systems that provide real-time data on the condition and performance of the cleaners. These systems help operators make informed decisions about maintenance and adjustments, ensuring optimal performance.
Importance of High-Quality Parts for System Performance
The use of high-quality parts is essential for the performance and longevity of ESS belt cleaners. High-quality components ensure that the cleaners operate efficiently, reducing the frequency of maintenance and the risk of unexpected failures. Key benefits of using high-quality parts include:
- Enhanced Durability:
- High-quality parts are made from materials that can withstand harsh operational conditions, including abrasion, impact, and chemical exposure. This durability reduces the need for frequent replacements and ensures that the belt cleaners provide consistent performance over time.
- Improved Efficiency:
- Components that are precisely engineered and made from superior materials operate more efficiently. This efficiency translates to better cleaning performance, reduced energy consumption, and lower operational costs.
- Reduced Maintenance Costs:
- Durable, high-quality parts require less frequent maintenance and replacement, leading to lower maintenance costs. This reliability also minimizes downtime, ensuring that conveyor systems operate smoothly and without interruption.
- Optimal Performance:
- Using high-quality parts ensures that ESS belt cleaners function as intended, providing effective cleaning and reducing material carryback. This optimal performance enhances the overall efficiency of conveyor systems, supporting higher productivity and improved operational outcomes.
Guide to Selecting and Replacing ESS Parts
Selecting and replacing ESS parts requires careful consideration to ensure that the right components are chosen and properly installed. The following guide provides steps for selecting and replacing ESS parts:
- Identify the Required Parts:
- Begin by identifying the specific parts that need replacement or upgrading. Consult the system’s manual or contact ESS Engineering for assistance in identifying the correct components.
- Consider Material Compatibility:
- Ensure that the replacement parts are compatible with the existing system and the materials being conveyed. Consider factors such as temperature resistance, chemical exposure, and abrasion levels when selecting new parts.
- Verify Specifications:
- Check the specifications of the replacement parts to ensure they match the requirements of the conveyor system. This includes dimensions, material composition, and performance ratings.
- Source Genuine ESS Parts:
- Purchase replacement parts from authorized ESS suppliers or directly from ESS Engineering to ensure authenticity and quality. Avoid using counterfeit or substandard parts, as they can compromise the performance and safety of the belt cleaners.
- Follow Installation Guidelines:
- Adhere to the installation guidelines provided by ESS Engineering to ensure that the parts are installed correctly. Proper installation is critical for achieving optimal performance and longevity of the belt cleaners.
- Conduct Regular Inspections:
- Perform regular inspections of the belt cleaners and their components to identify any signs of wear or damage. Replace parts as needed to maintain the efficiency and reliability of the system.
- Maintain a Spare Parts Inventory:
- Keep an inventory of essential spare parts to minimize downtime in case of unexpected failures. This proactive approach ensures that replacements are readily available when needed.
ESS Belt Cleaners: Conveyor Scrapers: Integral Tools for Belt Cleaning
Role of Conveyor Scrapers in Maintaining Clean Belts
Conveyor scrapers play a vital role in maintaining the cleanliness and efficiency of conveyor belts. They are essential tools in any belt cleaning system, designed to remove material that adheres to the belt after the discharge point. This not only ensures that the belt runs smoothly but also minimizes the buildup of residue, which can lead to various operational issues.
Importance of Clean Conveyor Belts
- Operational Efficiency: Clean conveyor belts reduce the risk of material buildup, which can cause misalignment, increased wear, and potential belt damage. By maintaining a clean belt surface, conveyor systems can run more efficiently, reducing downtime and maintenance costs.
- Safety: Material buildup can create hazardous conditions, such as slipping hazards or obstructed walkways. Clean belts help maintain a safer working environment for personnel.
- Product Quality: For industries where product contamination is a concern, such as food processing or pharmaceuticals, clean conveyor belts are crucial. Scrapers help prevent cross-contamination by ensuring that remnants from previous loads are removed.
- Equipment Longevity: Regular cleaning of conveyor belts with scrapers extends the life of the belts and other conveyor components by reducing abrasion and wear.
Types of Conveyor Scrapers Offered by ESS
ESS offers a variety of conveyor scrapers designed to meet the needs of different industries and applications. These scrapers are engineered for durability, efficiency, and ease of maintenance.
Primary Scrapers
Primary scrapers are installed at the head pulley and are the first line of defense in removing bulk material from the belt. ESS offers several types of primary scrapers:
- Tungsten Carbide Blade Scrapers: These scrapers feature durable tungsten carbide blades that provide effective cleaning and long service life. They are suitable for high-speed belts and abrasive materials.
- Polyurethane Blade Scrapers: Made from flexible and wear-resistant polyurethane, these scrapers are ideal for applications where blade flexibility is essential. They are effective in removing fine particles and are less likely to damage the belt.
- Combination Scrapers: These scrapers combine tungsten carbide and polyurethane blades to offer the benefits of both materials. They provide robust cleaning while being gentle on the belt surface.
Secondary Scrapers
Secondary scrapers are installed further along the conveyor system, typically under the head pulley or at the discharge point. They provide additional cleaning to remove any material missed by the primary scraper. ESS offers the following types of secondary scrapers:
- Segmented Blade Scrapers: These scrapers consist of individual blades mounted on a flexible base. The segmented design allows each blade to conform to the belt’s surface, ensuring thorough cleaning.
- Spring-Loaded Scrapers: Equipped with spring mechanisms, these scrapers maintain constant pressure against the belt, adapting to changes in belt tension and ensuring consistent cleaning performance.
- V-Plow Scrapers: Positioned on the return side of the belt, V-plow scrapers prevent material from being carried back into the conveyor system. They are particularly useful for belts that carry sticky or fine materials.
Tertiary Scrapers
For applications requiring the highest level of cleanliness, tertiary scrapers provide an additional layer of cleaning. These scrapers are typically installed after the secondary scraper and are designed to remove any remaining material. ESS offers:
- Brush Scrapers: Featuring rotating brushes, these scrapers effectively remove fine particles and residual material. They are ideal for applications where thorough cleaning is essential.
- Water Spray Scrapers: Combining mechanical scraping with water spray, these scrapers provide enhanced cleaning for particularly stubborn materials. The water spray helps to loosen and wash away residue.
Installation and Operational Tips for Conveyor Scrapers
Proper installation and maintenance of conveyor scrapers are crucial for maximizing their effectiveness and longevity. Here are some tips for installing and operating ESS belt cleaners, particularly conveyor scrapers:
Installation Tips
- Correct Positioning: Ensure that scrapers are positioned correctly relative to the belt. Primary scrapers should be installed at the head pulley, while secondary and tertiary scrapers should be placed further along the conveyor system.
- Angle and Pressure: Adjust the angle and pressure of the scraper blades to optimize cleaning performance. The blades should be in firm contact with the belt surface without causing excessive wear.
- Alignment: Ensure that scrapers are aligned perpendicular to the belt. Misalignment can lead to uneven wear on the scraper blades and the belt.
- Mounting: Use sturdy mounting brackets and hardware to secure the scrapers in place. This will prevent movement or vibration during operation.
- Clearance: Maintain adequate clearance between the scraper and other conveyor components to avoid interference and ensure smooth operation.
Operational Tips
- Regular Inspection: Conduct regular inspections of the scrapers to check for wear, damage, and proper alignment. Replace worn or damaged blades promptly to maintain cleaning efficiency.
- Blade Replacement: Follow the manufacturer’s guidelines for replacing scraper blades. Ensure that replacement blades are compatible with the scraper model and are installed correctly.
- Tension Adjustment: Periodically check and adjust the tension of spring-loaded scrapers to maintain optimal pressure against the belt. Proper tension ensures effective cleaning without causing excessive wear.
- Cleaning and Maintenance: Keep scrapers clean and free of buildup. Remove any accumulated material from the scraper blades and mounting brackets to ensure smooth operation.
- Lubrication: For scrapers with moving parts, such as spring mechanisms or rotating brushes, ensure that these components are properly lubricated to reduce friction and wear.
Troubleshooting Common Issues
- Insufficient Cleaning: If the scrapers are not effectively cleaning the belt, check for proper alignment, blade condition, and pressure. Adjust as necessary to improve cleaning performance.
- Excessive Wear: Excessive wear on the scraper blades or belt may indicate incorrect positioning or excessive pressure. Adjust the angle and pressure of the scraper blades to reduce wear.
- Vibration and Noise: Vibration and noise during operation can be caused by loose mounting hardware or misalignment. Ensure that all components are securely fastened and properly aligned.
- Material Carryback: If material carryback persists despite the use of scrapers, consider using a combination of primary, secondary, and tertiary scrapers to achieve more thorough cleaning.
By understanding the role of conveyor scrapers and following best practices for their installation and operation, industries can maintain clean and efficient conveyor systems. ESS belt cleaners, including their range of conveyor scrapers, provide reliable solutions for various applications, ensuring optimal performance and reduced maintenance costs.
ESS Belt Cleaners: Ensuring Longevity of Belt Cleaners
Maintaining ESS belt cleaners is crucial for ensuring the longevity and optimal performance of conveyor belt systems. Proper maintenance practices not only enhance the efficiency of the cleaning systems but also reduce operational costs and prevent downtime. This section explores the best practices for ESS maintenance of belt cleaning systems, scheduled maintenance routines, and tips for prolonging the life of ESS belt cleaners.
Best Practices for ESS Maintenance of Belt Cleaning Systems
Maintaining ESS belt cleaners requires a proactive approach to prevent issues before they become significant problems. Here are some best practices for ensuring that ESS belt cleaners operate efficiently and have a long lifespan:
- Regular Inspections
- Conduct regular inspections of the belt cleaners and the conveyor system to identify any signs of wear, damage, or misalignment. Early detection of potential issues allows for timely intervention and prevents more severe problems.
- Cleaning and Lubrication
- Keep the belt cleaners and related components clean and well-lubricated. Dirt and debris can cause abrasion and wear, while proper lubrication ensures smooth operation and reduces friction between moving parts.
- Tension Adjustment
- Regularly check and adjust the tension of the belt cleaners to ensure optimal contact with the conveyor belt. Proper tensioning is critical for effective cleaning and preventing excessive wear on both the belt and the cleaner.
- Replacement of Worn Parts
- Replace worn or damaged parts promptly to maintain the performance of the belt cleaners. Using high-quality ESS parts for replacements ensures compatibility and durability.
- Alignment Checks
- Ensure that the belt cleaners are properly aligned with the conveyor belt. Misalignment can cause uneven wear and reduce the effectiveness of the cleaning system.
- Monitoring System Performance
- Use monitoring systems to track the performance of the belt cleaners. Sensors and automated systems can provide real-time data on the condition of the cleaners, allowing for proactive maintenance.
- Training and Safety Protocols
- Train maintenance personnel on the correct procedures for maintaining ESS belt cleaners. Ensure that safety protocols are followed to prevent accidents and injuries during maintenance activities.
Scheduled Maintenance Routines and Their Benefits
Implementing a scheduled maintenance routine is essential for the long-term performance and reliability of ESS belt cleaners. A well-planned maintenance schedule offers several benefits:
- Improved Efficiency
- Regular maintenance ensures that the belt cleaners operate at peak efficiency, providing consistent and effective cleaning. This reduces material carryback and enhances the overall performance of the conveyor system.
- Reduced Downtime
- Scheduled maintenance helps prevent unexpected breakdowns and reduces downtime. By addressing potential issues during routine checks, companies can avoid costly interruptions to their operations.
- Extended Lifespan
- Consistent maintenance extends the lifespan of ESS belt cleaners and their components. This reduces the frequency of replacements and lowers overall maintenance costs.
- Safety and Compliance
- Regular maintenance ensures that the belt cleaners meet safety and compliance standards. Properly maintained equipment reduces the risk of accidents and ensures a safe working environment for personnel.
- Cost Savings
- Proactive maintenance helps identify and address minor issues before they escalate into major problems. This approach minimizes repair costs and maximizes the return on investment in ESS belt cleaners.
A typical maintenance schedule for ESS belt cleaners may include the following activities:
- Daily Checks
- Perform visual inspections to check for signs of wear, damage, or misalignment.
- Ensure that the belt cleaners are operating correctly and are in proper contact with the conveyor belt.
- Weekly Maintenance
- Clean the belt cleaners and remove any accumulated debris.
- Check and adjust the tension of the belt cleaners if necessary.
- Lubricate moving parts as required.
- Monthly Inspections
- Conduct a more thorough inspection of the belt cleaners and related components.
- Replace any worn or damaged parts.
- Verify the alignment of the belt cleaners with the conveyor belt.
- Quarterly Maintenance
- Perform a comprehensive inspection and maintenance of the entire belt cleaning system.
- Calibrate monitoring systems and sensors to ensure accurate performance data.
- Review and update maintenance records and schedules.
- Annual Maintenance
- Conduct a detailed assessment of the belt cleaning system’s performance over the past year.
- Replace any parts that show signs of significant wear or have reached the end of their service life.
- Evaluate the effectiveness of the maintenance program and make adjustments as needed.
Tips for Prolonging the Life of ESS Belt Cleaners
To maximize the lifespan of ESS belt cleaners, consider the following tips:
- Use High-Quality Parts
- Always use genuine ESS parts for replacements and repairs. High-quality components are designed to withstand the rigors of conveyor belt operations and provide longer service life.
- Monitor Operational Conditions
- Keep track of the operational conditions, such as material types, load weights, and environmental factors. Adjust maintenance practices accordingly to address specific challenges posed by these conditions.
- Implement Preventive Maintenance
- Adopt a preventive maintenance approach to address potential issues before they affect the performance of the belt cleaners. This includes regular inspections, timely part replacements, and adherence to maintenance schedules.
- Optimize Cleaner Design
- Ensure that the belt cleaners are designed and installed correctly to match the specific requirements of the conveyor system. Proper design and installation optimize cleaning performance and reduce wear.
- Educate and Train Personnel
- Provide ongoing training for maintenance personnel to keep them informed about the latest maintenance techniques and best practices. Well-trained staff can perform maintenance tasks more efficiently and effectively.
- Utilize Advanced Technologies
- Incorporate advanced technologies, such as automated monitoring systems and predictive maintenance tools, to enhance the maintenance program. These technologies provide real-time data and insights that help optimize maintenance practices.
- Document and Review Maintenance Activities
- Maintain detailed records of all maintenance activities, including inspections, part replacements, and repairs. Regularly review these records to identify trends and areas for improvement in the maintenance program.
Proper maintenance of ESS belt cleaners is essential for ensuring their longevity and optimal performance. By following best practices for maintenance, implementing scheduled maintenance routines, and adopting proactive measures, companies can maximize the efficiency and reliability of their belt cleaning systems. High-quality ESS parts, regular inspections, and timely interventions play a crucial role in maintaining the performance of ESS belt cleaners and reducing operational costs. With a comprehensive maintenance program in place, businesses can achieve long-term benefits, including improved productivity, reduced downtime, and enhanced safety in their conveyor operations.
FAQs about ESS Belt Cleaners
To clean a conveyor belt effectively, you can use a combination of mechanical and chemical cleaning methods. For mechanical cleaning, belt scrapers or brushes are commonly used. These devices are installed on the conveyor system and scrape off debris and contaminants from the belt surface. For chemical cleaning, specialized cleaning agents or solvents can be applied to remove stubborn residues, oils, and greases. It’s essential to choose a cleaning agent that is compatible with the belt material to avoid any damage. Regular cleaning schedules and maintenance practices help in prolonging the life of the conveyor belt and ensuring efficient operation.
Belt cleaners are devices used to remove unwanted materials from the surface of conveyor belts. They are typically mounted at strategic points along the conveyor system, such as the head pulley or tail pulley, to scrape off debris, residues, and other contaminants. Belt cleaners help maintain the efficiency and longevity of conveyor belts by preventing material buildup that can cause belt misalignment, increased wear, and operational inefficiencies. There are various types of belt cleaners, including primary and secondary cleaners, which work together to provide comprehensive cleaning solutions. Properly maintained belt cleaners can significantly reduce downtime and maintenance costs.
Cleaning a polyurethane (PU) conveyor belt requires careful handling to avoid damaging the material. Begin by removing any loose debris using a soft brush or cloth. For thorough cleaning, use a mild detergent solution and a non-abrasive sponge or cloth. Gently scrub the belt surface to remove any residues or contaminants. Rinse the belt thoroughly with clean water to remove any soap residue. It’s crucial to avoid using harsh chemicals or abrasive tools that can damage the PU material. Regular cleaning and maintenance help keep PU belts in optimal condition, ensuring smooth operation and extending their service life.
Belt cleaners are typically made from durable materials that can withstand the harsh conditions of conveyor operations. Common materials used include stainless steel, polyurethane, and rubber. Stainless steel is favored for its strength, corrosion resistance, and durability, making it suitable for heavy-duty applications. Polyurethane is known for its flexibility, wear resistance, and gentle cleaning action, which is ideal for delicate belt surfaces. Rubber is also used for its flexibility and cost-effectiveness. The choice of material for belt cleaners depends on the specific application requirements, including the type of material being conveyed, operating conditions, and the conveyor belt material.
Last Updated on May 17, 2024 by Jordan Smith
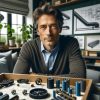
Jordan Smith, a seasoned professional with over 20 years of experience in the conveyor system industry. Jordan’s expertise lies in providing comprehensive solutions for conveyor rollers, belts, and accessories, catering to a wide range of industrial needs. From initial design and configuration to installation and meticulous troubleshooting, Jordan is adept at handling all aspects of conveyor system management. Whether you’re looking to upgrade your production line with efficient conveyor belts, require custom conveyor rollers for specific operations, or need expert advice on selecting the right conveyor accessories for your facility, Jordan is your reliable consultant. For any inquiries or assistance with conveyor system optimization, Jordan is available to share his wealth of knowledge and experience. Feel free to reach out at any time for professional guidance on all matters related to conveyor rollers, belts, and accessories.