Failure Analysis of Belt Conveyor Systems: Typical Issues and Solutions
Belt conveyor systems are integral components across various industries, including manufacturing, logistics, and mining, playing a crucial role in the seamless transportation of goods and materials. These systems, characterized by their efficiency and reliability, significantly contribute to operational productivity. However, like any mechanical system, they are not immune to failures, which can lead to substantial downtime and disrupt the flow of operations. This is where the concept of failure analysis of belt conveyor systems becomes paramount. By systematically examining the causes of failures, businesses can implement strategies to prevent future occurrences, thereby minimizing downtime and enhancing overall operational efficiency. Understanding and addressing the root causes of conveyor system failures is essential for maintaining continuous, efficient, and cost-effective operations.
Common Conveyor Belt Problems in Failure Analysis of Belt Conveyor System
In the realm of failure analysis of belt conveyor systems, identifying and understanding common issues are pivotal steps toward ensuring the longevity and efficiency of these critical components in industrial operations. Here are 10 typical problems that, if not promptly and effectively addressed, can lead to significant system failures:
- Mistracking: When the conveyor belt deviates from its intended path, it can lead to uneven wear, potential damage to the belt edges, and even cause the belt to come off the track entirely. Mistracking is often a result of improper installation, misaligned rollers, or uneven loading.
- Belt Slippage: This occurs when the belt fails to grip the pulleys adequately, often due to insufficient tension, worn pulley surfaces, or environmental factors such as moisture and dust. Slippage can reduce the efficiency of the conveyor system and lead to premature wear.
- Blockages: Material buildup or objects becoming lodged in the conveyor can obstruct the smooth flow of materials, leading to potential damage to the belt and other components, and even causing the system to halt.
- Material Carryback: Residual materials sticking to the belt after the discharge point can cause buildups on rollers and pulleys, leading to belt misalignment and additional wear.
- Material Spillage: Incorrectly aligned conveyor systems, inadequate sealing, or improper loading can lead to materials spilling from the belt, creating safety hazards and requiring additional cleanup.
- Seized Rollers: Rollers that cease to rotate properly can create friction points, leading to belt damage and increased energy consumption.
- Wear and Tear: Continuous operation under harsh conditions can lead to the gradual deterioration of belt material, affecting the conveyor’s performance and lifespan.
- Joint Failure: Conveyor belt joints are critical points that can fail due to poor installation, excessive tension, or wear, leading to belt separation and system downtime.
- Edge Damage: Rough handling, misalignment, and contact with fixed structures can cause damage to the edges of the conveyor belt, compromising its structural integrity.
- Control System Malfunctions: Issues with the conveyor’s control system, such as software glitches or sensor failures, can lead to erratic operation or sudden stops, posing risks to both the system and the materials being transported.
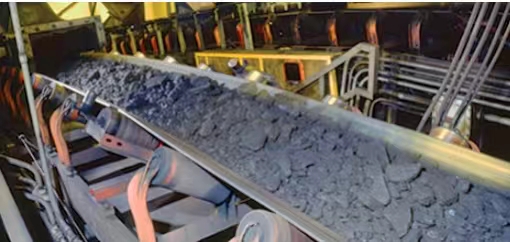
Addressing these issues is a fundamental aspect of the failure analysis of belt conveyor systems. By identifying the root causes of these common problems, maintenance teams can implement targeted interventions to prevent system failures, thereby minimizing downtime and maintaining operational efficiency.
Causes of Conveyor Belt Failure in Failure Analysis of Belt Conveyor System
A thorough failure analysis of belt conveyor systems reveals several root causes that can lead to significant conveyor belt problems. It analyzes typical failure forms of rollers and conveyors in belt conveyor systems and describes preventive maintenance methods for mistracking, slippage, carryback, and spillage. Understanding these causes is crucial for implementing effective preventive measures and ensuring the reliability and efficiency of conveyor systems.
- Mistracking: One of the most prevalent issues in conveyor belt operations is mistracking, where the belt deviates from its intended path. This misalignment can stem from various factors, including improper installation, where the belt isn’t correctly squared or tensioned during setup, leading to uneven forces on the belt. Worn components, such as conveyor idler pulleys that have become uneven or damaged over time, can also contribute to mistracking. Additionally, load imbalance, where materials are unevenly distributed across the belt, can exert unequal forces, causing the belt to drift off its intended course. The failure analysis of belt conveyor systems often identifies mistracking as a primary concern due to its potential to cause extensive damage to the belt and system components if left unaddressed.
- Belt Slippage: Belt slippage occurs when the conveyor belt loses its grip on the pulleys, primarily due to inadequate tension. Insufficient tension reduces the friction between the belt and pulleys, causing the belt to slip. Worn pulley surfaces, where the pulleys have become smooth or glazed, can also diminish the belt’s grip, leading to slippage. Environmental factors, such as cold temperatures, can stiffen the belt material, reducing its flexibility and traction on the pulleys. Belt slippage not only reduces the efficiency of the conveyor system but can also result in premature wear and tear on the belt.
- Blockages and Material Spillage: Blockages often occur when materials become lodged in the conveyor, typically at transfer points or around the rollers. These blockages can result from sharp edges on the conveyor structure, improper loading techniques, or inadequate containment measures, such as skirt boards or seals. Material spillage is closely related to blockages and can occur when materials fall off the belt, often due to misalignment, high speeds, or insufficient containment. Both blockages and spillage can lead to operational inefficiencies, safety hazards, and additional maintenance requirements.
- Seized Rollers: Rollers play a crucial role in supporting and guiding the conveyor belt. However, without regular maintenance, rollers can seize due to the accumulation of dirt, debris, or corrosion. Seized rollers fail to rotate freely, creating friction points that can wear down the belt and even lead to tearing. The development of sharp edges on seized rollers can further damage the belt, exacerbating the problem.
- Material Carryback: Material carryback refers to the residue that sticks to the belt and conveyor components after the discharge point. This residual material can build up on rollers, pulleys, and other parts of the conveyor, leading to belt mistracking, reduced efficiency, and increased wear on components. Carryback is often a result of sticky or wet materials, but it can also occur with dry materials that have fine particles.
Addressing these root causes is a fundamental aspect of the failure analysis of belt conveyor systems. By identifying and mitigating these issues, organizations can enhance the reliability and efficiency of their conveyor operations, reduce maintenance costs, and prevent unplanned downtime.
Disadvantages of Belt Conveyor Systems in Failure Analysis of Belt Conveyor System
While belt conveyor systems are invaluable to various industries for their efficiency and ability to move materials over long distances, they are not without their limitations and challenges. A comprehensive failure analysis of belt conveyor systems often highlights several disadvantages that can impact their operation and longevity:
- High Maintenance Requirements: Belt conveyor systems require regular maintenance to ensure optimal performance. This includes routine inspections, cleaning, lubrication, and adjustments, which can be time-consuming and require specialized skills.
- Susceptibility to Wear and Damage: The continuous operation of belt conveyors, often in harsh environments, makes them prone to wear and tear. Factors such as abrasive materials, exposure to chemicals, and mechanical stresses can accelerate the deterioration of belts and components.
- Operational Disruptions: Conveyor belt failures, such as belt tears, motor malfunctions, or electrical issues, can lead to significant operational disruptions. These unexpected downtimes can result in lost production time and increased costs.
- Environmental Limitations: Belt conveyors can be sensitive to environmental conditions. Extreme temperatures, humidity, and exposure to water or chemicals can affect their performance and durability.
- Material Spillage and Waste: Inadequate sealing, misalignment, or improper loading can lead to material spillage, creating safety hazards, requiring additional cleanup, and resulting in material waste.
- Limited Versatility: Standard belt conveyor systems may not be suitable for transporting certain types of materials, especially those that are very hot, sticky, or sharp. Specialized roller conveyor designs can be more costly and complex to implement.
- Noise Pollution: The operation of belt conveyors, particularly in enclosed spaces, can generate significant noise levels, contributing to noise pollution and potentially affecting worker health and safety.
- Energy Consumption: Large-scale conveyor systems can consume considerable amounts of energy, especially when operating continuously. This can lead to higher operational costs and environmental impact.
Addressing these disadvantages is a critical component of the failure analysis of belt conveyor systems. By understanding these limitations, engineers and maintenance teams can develop strategies to mitigate their impact, such as implementing advanced materials for belts and components, using energy-efficient motors, and adopting predictive maintenance techniques. This proactive approach can enhance the efficiency, reliability, and sustainability of belt conveyor systems, reducing the likelihood of failures and extending their service life.
Tracking Conveyor Belt Problems in Failure Analysis of Belt Conveyor System
Effective tracking and monitoring of conveyor belt problems are crucial components in the failure analysis of belt conveyor systems. Identifying issues early on can prevent minor problems from escalating into major failures that disrupt operations. Here are seven strategies for effectively monitoring and identifying early signs of conveyor belt issues, followed by the importance of regular inspections, maintenance routines, and advanced monitoring technologies.
Strategies for Monitoring and Identifying Issues
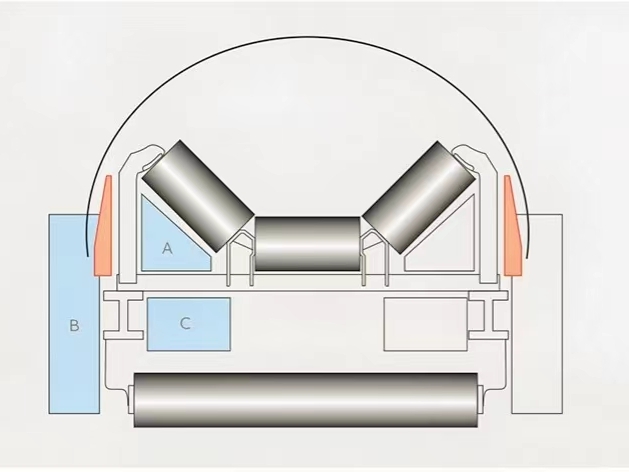
- Regular Visual Inspections: Conduct daily visual inspections of the conveyor belt and its components to check for signs of wear, damage, or misalignment. Look for frayed edges, cracks, or any deformities on the belt.
- Implementing a Scheduled Maintenance Program: Establish a routine maintenance schedule based on the manufacturer’s recommendations and operational demands. This program should include detailed checklists for each component of the conveyor system.
- Use of Advanced Monitoring Technologies: Employ technologies such as vibration analysis, thermal imaging, and acoustic monitoring to detect early signs of wear or failure in bearings, motors, and other critical components.
- Belt Tension Monitoring: Ensure that the belt tension is regularly checked and adjusted as necessary. Incorrect tension is a common cause of belt slippage and misalignment.
- Tracking Belt Performance Over Time: Keep detailed records of belt performance, including any incidents of downtime, repairs, and replacements. This historical data can help identify patterns or recurring issues.
- Employee Training: Train operational staff to recognize the early signs of belt conveyor problems and understand the correct reporting procedures. A well-informed team can be the first line of defense against conveyor belt failures.
- Incorporating Real-Time Monitoring Systems: Consider installing real-time monitoring systems that can provide instant alerts in case of deviations from normal operating conditions, allowing for immediate corrective actions.
Importance of Regular Inspections and Maintenance
Regular inspections and maintenance are the cornerstones of preventing conveyor belt failures. These routines allow for the early detection of potential issues, enabling corrective measures before they lead to significant problems. Scheduled maintenance not only extends the lifespan of the conveyor belt and its components but also ensures consistent operational efficiency.
Advanced Monitoring Technologies
The integration of advanced monitoring technologies plays a pivotal role in the proactive maintenance of conveyor belt systems. These technologies can detect subtle changes in equipment behavior that may indicate an impending failure, often well before the issue becomes apparent through visual inspections or operational performance. By leveraging data from these monitoring systems, maintenance teams can perform targeted interventions, reducing downtime and maintenance costs.
Effective tracking of conveyor belt problems is an integral part of the failure analysis of belt conveyor systems. By combining regular inspections, scheduled maintenance, employee vigilance, and advanced monitoring technologies, organizations can significantly reduce the risk of conveyor belt failures, ensuring smooth and uninterrupted operations.
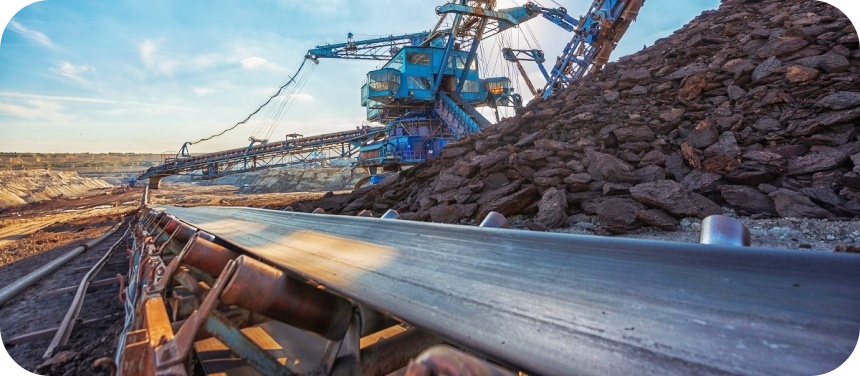
Failure Analysis of Belt Conveyor System
The failure analysis of belt conveyor systems is a critical process that helps in identifying the underlying causes of operational issues, thereby facilitating the implementation of effective solutions. This systematic approach involves several key steps, from the initial recognition of symptoms to the identification of root causes. Additionally, examining case studies of common failure scenarios provides valuable insights into the analytical approaches used to resolve these issues.
Step-by-Step Guide to Conducting a Failure Analysis
- Initial Symptom Recognition: The first step involves identifying the early signs of a problem, such as unexpected noises, belt misalignment, reduced efficiency, or visible wear and damage.
- Data Collection: Gather all relevant operational data, maintenance records, and any recent changes to the system or its environment that could have contributed to the failure.
- Visual Inspection: Perform a thorough visual inspection of the conveyor belt and its components to identify any obvious signs of wear, damage, or misalignment.
- Detailed Analysis: For issues not immediately identifiable through visual inspection, conduct a more detailed analysis using specialized tools and techniques, such as vibration analysis, thermal imaging, or material testing.
- Root Cause Identification: Analyze the collected data and findings to pinpoint the root causes of the failure. This may involve considering multiple factors, including mechanical issues, material defects, operational errors, or environmental conditions.
- Solution Implementation: Develop and implement solutions to address the identified root causes, which may include repairing or replacing damaged components, adjusting operational parameters, or redesigning aspects of the system.
- Monitoring and Evaluation: After implementing corrective measures, closely monitor the system to ensure the effectiveness of the solutions and make any necessary adjustments.
Case Studies in Failure Analysis of Belt Conveyor Systems
Case Study 1: Excessive Belt Wear at Alpha Manufacturing
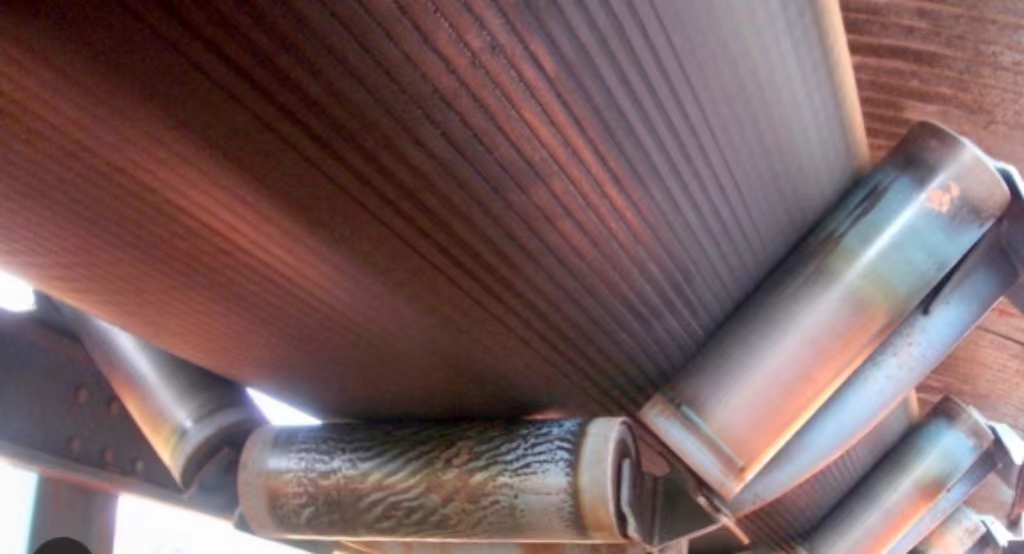
Scenario: Alpha Manufacturing reported excessive wear on their conveyor belt, leading to frequent replacements and increased operational costs.
Analysis: The failure analysis conducted by their maintenance team revealed that abrasive materials being transported and improper belt tension were causing accelerated wear on the conveyor belt.
Solution: Alpha Manufacturing introduced a more durable belt material suited for abrasive conditions and implemented a tension monitoring system to maintain optimal belt tension. This solution significantly reduced the frequency of belt replacements and improved overall system reliability.
Case Study 2: Motor Failures at Beta Logistics
Scenario: Beta Logistics faced repeated motor failures on one of their main conveyor belts, disrupting their logistics operations.
Analysis: The investigation showed that dust and debris accumulation in the motor housing led to overheating and subsequent motor failures. This issue was exacerbated by the facility’s dusty environment and inadequate cleaning protocols.
Solution: Beta Logistics improved their cleaning routines and installed protective covers to shield the motors from debris. These measures helped to prevent dust accumulation and overheating, thereby reducing motor failures and enhancing the reliability of their conveyor system.
Case Study 3: Belt Mistracking at Gamma Airport
Scenario: Gamma Airport’s baggage handling system experienced frequent belt mistracking, causing delays and baggage mishandling, which affected passenger satisfaction.
Analysis: The failure analysis identified worn tracking rollers and uneven loading as the primary causes of mistracking. The worn rollers failed to guide the belt properly, while uneven loading created imbalances that exacerbated the problem.
Solution: Gamma Airport replaced the worn tracking rollers and implemented a training program for staff to ensure even loading of baggage. These actions improved the tracking of the conveyor belt, reducing delays and enhancing the efficiency of the baggage handling system.
Case Study 4: Conveyor System Blockages at Delta Mining
Scenario: Delta Mining reported recurrent blockages in their conveyor system, leading to operational stoppages and decreased productivity.
Analysis: The failure analysis revealed that oversized materials and a lack of proper screening mechanisms were causing the blockages. These large materials would clog the conveyor, leading to frequent stoppages.
Solution: Delta Mining installed additional screening equipment upstream of the conveyor and adjusted the crusher settings to produce smaller material sizes. This intervention helped to prevent blockages, ensuring smoother operation and improving the overall efficiency of their conveyor system.
Through these case studies, it is evident that a comprehensive failure analysis of belt conveyor systems is essential for diagnosing and resolving operational issues. By systematically identifying and addressing the root causes of failures, organizations can enhance the reliability and efficiency of their conveyor systems, ultimately improving overall operational performance.
Preventive Measures and Solutions in Failure Analysis of Belt Conveyor System
In the context of failure analysis of belt conveyor systems, implementing preventive measures and solutions is crucial for minimizing the risk of failures and ensuring the longevity and reliability of these systems. Here are ten recommendations for preventing conveyor belt failures, followed by ten tips for maintaining the longevity and reliability of conveyor belt systems.
Recommendations for Preventing Conveyor Belt Failures
- Proper Installation: Ensure that conveyor belts and their components are installed correctly according to manufacturer specifications, with particular attention to alignment and tensioning.
- Regular Maintenance: Establish a routine maintenance schedule that includes inspections, cleaning, lubrication, and adjustments to prevent wear and tear.
- Use of Quality Materials: Select high-quality materials for the conveyor belt and components to withstand operational demands and environmental conditions.
- Employee Training: Train employees on proper operation procedures, symptom recognition, and immediate response strategies to prevent further damage.
- Real-Time Monitoring Systems: Implement advanced monitoring systems that can detect and alert staff to potential issues before they escalate.
- Environmental Controls: Implement measures to protect the conveyor system from environmental factors such as moisture, temperature extremes, and corrosive substances.
- Load Management: Ensure that the conveyor system is not overloaded and that materials are evenly distributed to prevent imbalance and reduce wear.
- Innovative Solutions: Consider adopting innovative solutions like modular plastic conveyor chains, which offer enhanced durability and flexibility.
- Emergency Preparedness: Develop and maintain an emergency response plan for addressing and mitigating issues as they arise.
- Continuous Improvement: Regularly review and update maintenance practices and operational procedures based on the latest industry standards and technological advancements.
Tips for Ensuring Longevity and Reliability
- Regular Inspections: Conduct thorough inspections of the conveyor belt and components to identify signs of wear or damage early.
- Prompt Repairs: Address any identified issues promptly to prevent minor problems from developing into major failures.
- Lubrication: Keep all moving parts adequately lubricated to reduce friction and wear.
- Cleanliness: Maintain cleanliness around the conveyor system to prevent the buildup of materials that could cause blockages or wear.
- Belt Alignment Checks: Regularly check and adjust the alignment of the conveyor belt to prevent mistracking and uneven wear.
- Component Upgrades: Consider upgrading components to more durable versions as part of regular maintenance and improvement efforts.
- Operational Audits: Periodically conduct operational audits to assess the efficiency and effectiveness of the conveyor system and identify areas for improvement.
- Documentation: Keep detailed records of maintenance activities, repairs, and replacements to track the system’s history and performance.
- Feedback Mechanism: Establish a feedback mechanism for operators to report issues or suggest improvements based on their day-to-day experiences.
- Partnership with Experts: Collaborate with conveyor system experts and manufacturers for specialized support, especially when dealing with complex issues or upgrades.
Connect with us for superior conveyor belt options.
By integrating these preventive measures and solutions into the operational and maintenance strategies, organizations can significantly reduce the likelihood of conveyor belt failures. This proactive approach, grounded in the principles of failure analysis of belt conveyor systems, ensures that conveyor belts operate reliably and efficiently, supporting uninterrupted production and operational excellence.
FAQs about Failure Analysis of Belt Conveyor System
Conveyor system failures encompass a range of issues that can disrupt the smooth operation of the conveyor belt and, by extension, the entire production or transportation process they are part of. These failures can be mechanical, electrical, or operational in nature. Mechanical failures often involve the physical components of the conveyor system, such as the belt itself, rollers, bearings, and motors. For instance, the belt might tear, fray, or misalign, while rollers and bearings might seize or wear out, leading to increased friction and potential system stoppages. Electrical failures could include issues with the conveyor’s motor, sensors, or control systems, leading to sudden stoppages, incorrect speed control, or erratic belt movement. Operational failures are often due to human error or inadequate maintenance practices, such as overloading the belt, improper loading techniques leading to uneven belt wear, or failure to conduct regular maintenance checks and replacements. Each type of failure requires a specific approach to troubleshooting and repair, emphasizing the importance of a comprehensive understanding of the system’s components and their functions.
Conveyor belts can fail in several distinct modes, each affecting the system’s efficiency and safety. Common failure modes include:
Belt Mistracking: This occurs when the belt deviates from its intended path, potentially leading to edge damage, material spillage, and increased wear on the belt and structure.
Belt Slippage: Caused by insufficient tension or grip between the belt and pulleys, resulting in reduced conveyor efficiency and potential damage to the belt.
Tears and Rips: Sharp objects, heavy impacts, or overloading can cause tears and rips in the belt, compromising its integrity and leading to potential system failure.
Splice Failure: Conveyor belt splices can fail due to poor installation, wear, or excessive tension, leading to belt separation and operational stoppages.
Wear and Abrasion: Continuous use, especially in the presence of abrasive materials, can wear down the belt surface, reducing its lifespan and efficiency.
Understanding these failure modes is crucial for effective maintenance and operation of conveyor systems, allowing for timely interventions to prevent more significant issues.
Troubleshooting a conveyor belt involves a systematic approach to identify and resolve issues causing the system to operate suboptimally or fail. The process typically includes:
Observation: Begin by visually inspecting the conveyor belt while it’s running, if possible, to identify any obvious signs of mistracking, slippage, or damage.
Listening: Pay attention to any unusual noises, such as grinding, squealing, or thumping, which can indicate specific issues like bearing failures, belt misalignment, or blockages.
Checking Tension: Ensure the belt is properly tensioned, as both over-tensioning and under-tensioning can lead to problems like slippage and excessive wear.
Inspecting Components: Examine the belt’s components, including rollers, pulleys, bearings, and splices, for signs of wear, damage, or improper alignment.
Reviewing Maintenance Records: Consult the conveyor’s maintenance history to identify recurring issues or recent repairs that might be related to the current problem.
Effective troubleshooting often requires a combination of technical knowledge, observational skills, and practical experience with conveyor systems.
Impact damage in conveyor belts refers to the harm caused by heavy or sharp objects falling onto the belt surface. This type of damage is common in industries where materials are dropped from a height onto the conveyor, such as mining, quarrying, and some manufacturing processes.
The impact can create tears, holes, or deep indentations in the belt, compromising its structural integrity and leading to potential failures. Over time, repeated impacts can weaken the belt, making it more susceptible to other forms of damage and reducing its overall lifespan. To mitigate impact damage, conveyor systems may be equipped with impact beds or plates designed to absorb the force of falling materials, distributing it more evenly across the belt’s surface and minimizing the risk of damage.
Belt conveyors are widely used in various industries for material handling. Despite their efficiency and reliability, they can encounter several common problems. Here are some of the most frequent issues:
Belt Misalignment: This occurs when the belt does not run in the center of the conveyor structure. Misalignment can cause the belt to wear unevenly, damage conveyor components, and result in material spillage.
Slippage: Belt slippage happens when the belt slips on the drive pulley. This can be due to insufficient tension, worn out pulley lagging, or a build-up of materials on the pulley.
Excessive Wear: Conveyor belts are subject to wear and tear due to the abrasive nature of the materials they transport. Over time, this can lead to the belt becoming thin and prone to breaking.
Material Spillage: When materials spill off the sides of the conveyor belt, it can create messes and require frequent cleaning. Spillage is often caused by overloading, improper loading, or misaligned belts.
Belt Tears and Rips: Sharp or heavy objects can cause tears and rips in the belt. This can lead to belt failure and require costly repairs or replacements.
Noise and Vibration: Excessive noise and vibration can indicate problems with the conveyor belt system. This can be due to misalignment, worn out components, or improper tensioning.
Blocked Chutes: Blockages in the conveyor chutes can cause material back-up and disrupt the flow. This can be due to material sticking to the sides or due to improper chute design.
Overheating Motors: Conveyor motors can overheat if they are overworked or if there is insufficient ventilation. This can lead to motor failure and halt production.
Belt misalignment or improper tracking is a common issue with belt conveyors. Here are some probable causes:
Improper Belt Tension: If the belt tension is not correctly adjusted, the belt can drift off-center. Over-tightening can cause excessive wear, while under-tightening can lead to slippage and misalignment.
Uneven Loading: If the material is not loaded evenly across the width of the belt, it can cause the belt to shift to one side. This uneven loading creates an imbalance that affects tracking.
Worn or Damaged Components: Rollers, pulleys, and idlers that are worn out or damaged can cause the belt to track improperly. Regular maintenance and replacement of these components are essential to prevent misalignment.
Misaligned Conveyor Structure: If the conveyor frame is not perfectly aligned, the belt will not track properly. Regular inspections and adjustments are necessary to ensure the structure is aligned.
Material Build-Up: Accumulated materials on the pulleys or rollers can affect the belt’s path. Regular cleaning is necessary to prevent this build-up and ensure smooth operation.
Improper Splicing: If the belt splice is not done correctly, it can cause the belt to run off-center. Ensuring that splicing is done accurately and properly can help maintain proper tracking.
Environmental Factors: Factors such as temperature changes, humidity, and exposure to harsh conditions can affect belt tracking. Regular inspections and adjustments are needed to accommodate these environmental changes.
Incorrect Pulley Alignment: Pulleys must be aligned correctly to ensure proper tracking. Misaligned pulleys can cause the belt to drift and not run straight.
Last Updated on June 21, 2024 by Jordan Smith
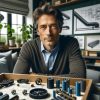
Jordan Smith, a seasoned professional with over 20 years of experience in the conveyor system industry. Jordan’s expertise lies in providing comprehensive solutions for conveyor rollers, belts, and accessories, catering to a wide range of industrial needs. From initial design and configuration to installation and meticulous troubleshooting, Jordan is adept at handling all aspects of conveyor system management. Whether you’re looking to upgrade your production line with efficient conveyor belts, require custom conveyor rollers for specific operations, or need expert advice on selecting the right conveyor accessories for your facility, Jordan is your reliable consultant. For any inquiries or assistance with conveyor system optimization, Jordan is available to share his wealth of knowledge and experience. Feel free to reach out at any time for professional guidance on all matters related to conveyor rollers, belts, and accessories.