Flexco Belt Scraper vs. Other Cleaning Solutions
A Flexco belt scraper is an essential tool designed to maintain the cleanliness and efficiency of conveyor belts. Flexco belt scrapers are engineered to remove carryback and debris, preventing material buildup that can lead to belt wear and operational inefficiencies. These scrapers play a crucial role in enhancing conveyor system performance by reducing downtime, minimizing maintenance costs, and ensuring smooth belt operation. The innovative design and durable materials used in Flexco belt scrapers make them ideal for a variety of industrial applications, ensuring that conveyor systems run efficiently and effectively. Their importance in maintaining productivity and operational safety cannot be overstated, making them a vital component in modern material handling systems.
Benefits of Using Flexco Belt Scrapers
In the realm of conveyor systems, the importance of maintaining clean and efficient operation cannot be overstated. Flexco belt scrapers play a crucial role in achieving this goal. These scrapers are designed to remove residual material from the conveyor belt, ensuring smooth and uninterrupted operation. This section explores the benefits of using Flexco belt scrapers, including improved conveyor efficiency and reduced downtime, as well as enhanced worker safety and operational productivity.
Improved Conveyor Efficiency and Reduced Downtime
Flexco belt scrapers are integral to maintaining the efficiency of conveyor systems. By effectively removing material buildup on the belt, these scrapers offer several key advantages:
Consistent Material Flow: One of the primary benefits of using a Flexco belt scraper is the consistent removal of residual material from the belt. This ensures that the belt surface remains clean, allowing for a smooth and continuous flow of materials. Consistent material flow reduces the risk of blockages and interruptions, which can significantly impact the efficiency of the conveyor system.
Reduced Belt Wear: Material buildup on conveyor belts can lead to increased friction and wear. Over time, this wear can cause significant damage to the belt, leading to costly repairs and replacements. Flexco belt scrapers help to minimize this wear by keeping the belt clean, thus extending the lifespan of the conveyor belt and reducing maintenance costs.
Minimized Downtime: Downtime in conveyor operations can be costly, both in terms of lost productivity and repair expenses. Flexco belt scrapers contribute to minimizing downtime by preventing material buildup that can cause belt slippage, misalignment, and other operational issues. By ensuring that the belt remains clean and functional, Flexco belt scrapers help maintain continuous operation and reduce the frequency of unplanned shutdowns.
Energy Efficiency: Clean conveyor belts operate more efficiently, requiring less energy to move materials along the system. By removing residual material, Flexco belt scrapers reduce the load on the conveyor drive system, leading to lower energy consumption and cost savings. This improved energy efficiency is particularly beneficial in large-scale operations where energy costs can be substantial.
Enhanced Worker Safety and Operational Productivity
Beyond improving conveyor efficiency, Flexco belt scrapers also play a vital role in enhancing worker safety and overall operational productivity:
Safer Working Environment: Material buildup on conveyor belts can create hazardous conditions for workers. Spilled materials can create slip and fall hazards, while accumulated dust can pose respiratory risks. Flexco belt scrapers help to maintain a clean conveyor belt, reducing the risk of spills and dust accumulation. This contributes to a safer working environment, minimizing the risk of accidents and injuries.
Reduced Manual Cleaning: Manual cleaning of conveyor belts can be a time-consuming and hazardous task. Workers often need to enter confined spaces and use tools that can pose injury risks. Flexco belt scrapers automate the cleaning process, significantly reducing the need for manual intervention. This not only enhances safety but also allows workers to focus on other essential tasks, increasing overall productivity.
Improved Operational Productivity: By maintaining a clean and efficient conveyor system, Flexco belt scrapers contribute to improved operational productivity. The consistent removal of residual material ensures that the conveyor operates at peak efficiency, allowing for higher throughput and faster processing times. This increased productivity can have a direct impact on the bottom line, making operations more profitable and competitive.
Enhanced Equipment Longevity: Flexco belt scrapers help to protect not only the conveyor belt but also other components of the conveyor system, such as pulleys and rollers. By preventing material buildup, the scrapers reduce wear on these components, extending their lifespan and reducing the frequency of repairs and replacements. This leads to lower maintenance costs and more reliable operation.
Ease of Installation and Maintenance: Flexco belt scrapers are designed for easy installation and maintenance. Their straightforward design allows for quick setup and adjustment, minimizing downtime during installation. Additionally, maintenance of Flexco belt scrapers is simple, with easily replaceable blades and components. This ease of maintenance ensures that the scrapers remain effective over the long term, providing consistent performance without significant upkeep.
Customizable Solutions: Flexco offers a range of belt scraper models and configurations to suit different conveyor systems and applications. This customization ensures that the scrapers can be tailored to meet specific operational needs, providing optimal performance in various environments. Whether dealing with heavy-duty applications or fine materials, Flexco has a belt scraper solution that can enhance conveyor efficiency and productivity.
What is Flexco Belt Scraper
Advanced Cleaning Solutions
Conveyor systems are integral to various industries, ensuring the efficient movement of materials. However, maintaining these systems is crucial for their optimal performance and longevity. One key aspect of conveyor maintenance is keeping the belt clean to prevent material buildup, which can cause operational issues and reduce efficiency. Flexco belt scrapers are advanced cleaning solutions designed to address this challenge effectively.
Conveyor Belt Brush Scrapers: Applications and Benefits
Conveyor belt brush scrapers are a specific type of belt cleaner that utilizes brushes to remove material from the conveyor belt. These scrapers are particularly effective for certain types of materials and applications, offering several unique benefits.
Applications:
- Fine Material Removal:
Brush scrapers are ideal for removing fine materials that may not be effectively cleared by traditional blade scrapers. This includes powders, granules, and other small particulate matter that can accumulate on the belt surface. - Wet or Sticky Materials:
For conveyors handling wet or sticky materials, brush scrapers provide an effective cleaning solution. The bristles of the brush can adapt to the texture of the belt and material, ensuring thorough cleaning without causing damage to the belt. - Delicate Belts:
In applications where the conveyor belt is made of a delicate or soft material, such as those used in the food processing industry, brush scrapers are gentle enough to clean the belt without causing wear or damage. This makes them suitable for maintaining hygiene standards while ensuring belt longevity. - Secondary Cleaning:
Brush scrapers are often used as secondary cleaners in conjunction with primary blade scrapers. After the initial cleaning by the blade scraper, the brush scraper provides a final, thorough cleaning, ensuring that no residual material is left on the belt.
Benefits:
- Enhanced Cleaning Efficiency:
Brush scrapers provide a more comprehensive cleaning compared to traditional blade scrapers, especially for fine and sticky materials. The bristles can reach into the grooves and textures of the belt, ensuring all material is effectively removed. - Reduced Belt Wear:
The flexible nature of brush scrapers means they exert less force on the belt compared to rigid blade scrapers. This reduces the wear and tear on the belt, extending its operational life and reducing maintenance costs. - Versatility:
Brush scrapers can be used in a variety of applications and are suitable for different types of conveyor belts and materials. This versatility makes them a valuable addition to any conveyor system, enhancing overall maintenance efficiency. - Improved Material Recovery:
By effectively removing all residual material from the belt, brush scrapers help in recovering valuable materials that would otherwise be lost. This not only improves operational efficiency but also contributes to cost savings.
Combining Different Types of Scrapers for Maximum Efficiency
To achieve maximum cleaning efficiency, it is often beneficial to combine different types of scrapers within a conveyor system. Flexco belt scrapers, including both blade and brush types, can be strategically used together to provide a comprehensive cleaning solution.
Primary and Secondary Scrapers:
- Primary Scrapers:
Primary scrapers, typically located at the discharge point of the conveyor, are the first line of defense against material buildup. These scrapers are usually made of rigid materials such as tungsten carbide or polyurethane and are designed to remove the bulk of the material from the belt. Flexco offers a range of primary scrapers that provide robust and effective cleaning for various materials and belt types. - Secondary Scrapers:
Secondary scrapers are positioned further along the conveyor belt, following the primary scrapers. These scrapers provide a secondary level of cleaning, removing any residual material left behind by the primary scraper. Brush scrapers are often used as secondary scrapers due to their ability to clean finer materials and reach into the belt’s grooves.
Combining Scraper Types:
- Enhanced Cleaning Coverage:
By combining primary blade scrapers with secondary brush scrapers, conveyor systems can achieve a higher level of cleaning coverage. The primary scraper removes the majority of the material, while the brush scraper ensures that any remaining fine particles or sticky substances are thoroughly cleared. - Optimized Belt Life:
The use of multiple scraper types reduces the overall wear on the belt. Primary scrapers handle the bulk removal, minimizing the load on secondary scrapers. This balanced approach distributes the cleaning force more evenly, preserving the integrity of the belt and extending its life. - Flexibility in Material Handling:
Different materials require different cleaning approaches. By incorporating both blade and brush scrapers, conveyor systems can handle a wider range of materials efficiently. This flexibility ensures that the system remains effective regardless of changes in the material being transported. - Reduced Downtime:
Effective cleaning with a combination of scrapers reduces the frequency of maintenance shutdowns. Cleaner belts lead to fewer operational interruptions and less time spent on manual cleaning, enhancing overall productivity. - Customized Solutions:
Flexco offers a variety of scraper models and configurations, allowing for customized solutions tailored to specific operational needs. By selecting the appropriate combination of scrapers, businesses can optimize their conveyor cleaning systems to meet their unique requirements. - Cost-Effective Maintenance:
While the initial investment in multiple scraper types may be higher, the long-term benefits of reduced maintenance costs, extended belt life, and improved operational efficiency make this approach cost-effective. Businesses can achieve significant savings over time by minimizing unscheduled downtime and maximizing belt performance. - Environmental Benefits:
Efficient belt cleaning reduces material spillage and waste, contributing to a cleaner and more environmentally friendly operation. By recovering more material and preventing contamination, businesses can enhance their sustainability efforts.
How about Flexco Belt Scraper PDF Resources
In the field of conveyor system maintenance and optimization, having access to detailed product information and operational guidelines is essential. Flexco belt scrapers are renowned for their efficiency and reliability, and Flexco provides comprehensive resources to support their products. These resources, available in PDF format, include detailed product information, manuals, specifications, and best practices. This section explores how to access these resources and the benefits they offer for understanding and implementing Flexco belt scrapers effectively.
Accessing Detailed Product Information and Manuals
Flexco provides a wide range of PDF resources that are invaluable for anyone looking to optimize their conveyor systems using Flexco belt scrapers. These documents include product brochures, technical specifications, installation guides, and maintenance manuals. Here’s how you can access and utilize these resources:
Flexco Website: The primary source for accessing Flexco belt scraper PDF resources is the official Flexco website. The website offers a dedicated section for product literature where users can find detailed brochures and manuals for all Flexco products, including belt scrapers. By visiting the website, users can easily download the latest versions of these documents.
Product Brochures: Flexco’s product brochures provide an overview of the various belt scraper models available, highlighting their features, benefits, and applications. These brochures are designed to help users select the right belt scraper for their specific needs. They include information on the materials used, the design of the scrapers, and their compatibility with different conveyor systems.
Installation Guides: Proper installation is crucial for the optimal performance of Flexco belt scrapers. Flexco provides detailed installation guides in PDF format, which outline the step-by-step process for installing the scrapers. These guides include diagrams and illustrations to help users understand the installation procedure, ensuring that the scrapers are installed correctly and securely.
Maintenance Manuals: To maintain the efficiency and longevity of Flexco belt scrapers, regular maintenance is essential. Flexco’s maintenance manuals provide comprehensive instructions on how to care for and maintain the scrapers. These manuals cover routine inspections, cleaning procedures, and how to replace worn components. By following these guidelines, users can ensure that their belt scrapers continue to operate effectively and minimize downtime.
Technical Specifications: For users who need detailed technical information, Flexco offers technical specification documents for their belt scrapers. These PDFs include precise measurements, material specifications, and performance data. Understanding these specifications is crucial for selecting the right scraper and ensuring it meets the operational requirements of the conveyor system.
About Specifications and Best Practices
Understanding the specifications and best practices for using Flexco belt scrapers is essential for maximizing their effectiveness and ensuring the smooth operation of conveyor systems. Here’s a detailed look at these aspects:
Specifications of Flexco Belt Scrapers:
- Material Specifications: Flexco belt scrapers are made from high-quality materials designed to withstand the harsh conditions of industrial environments. The specifications documents detail the types of materials used, such as different grades of polyurethane or tungsten carbide, and their respective properties. This information helps users choose the right scraper based on the type of materials being conveyed and the conditions of the operating environment.
- Design Features: Flexco belt scraper specifications include information on the design features that enhance their performance. This can include details on the scraper blade angles, tensioning mechanisms, and the construction of the mounting brackets. Understanding these design features allows users to appreciate how the scrapers work and how they can be adjusted for optimal performance.
- Performance Data: The technical specifications provide performance data such as the scraper’s effectiveness in removing different types of materials, its durability, and its expected lifespan under various operating conditions. This data is crucial for assessing the scraper’s suitability for specific applications and for planning maintenance schedules.
Best Practices for Using Flexco Belt Scrapers:
- Proper Installation: Following the installation guides provided by Flexco ensures that the belt scrapers are installed correctly. Best practices include ensuring the scraper is positioned correctly relative to the belt, that the tension is set appropriately, and that all components are securely fastened. Proper installation is key to the scraper’s performance and longevity.
- Regular Maintenance: Adhering to the maintenance schedules and procedures outlined in the Flexco maintenance manuals is essential for keeping the scrapers in good working condition. Best practices for maintenance include regular inspections for wear and damage, cleaning the scraper blades to prevent buildup, and replacing worn parts promptly.
- Correct Adjustment: Flexco belt scrapers need to be adjusted correctly to maintain optimal performance. This includes setting the right tension and ensuring the scraper blade maintains proper contact with the conveyor belt. The specifications documents often include guidance on how to make these adjustments.
- Monitoring Performance: Regularly monitoring the performance of Flexco belt scrapers helps in identifying any issues early on. Best practices include keeping records of maintenance activities, noting any changes in the scraper’s effectiveness, and addressing problems promptly to avoid more significant issues.
- Training and Safety: Ensuring that all personnel involved in the installation, maintenance, and operation of Flexco belt scrapers are properly trained is crucial. Flexco’s manuals often include safety guidelines and training tips to help users understand how to handle the scrapers safely and effectively. Proper training minimizes the risk of accidents and ensures that the scrapers are used to their full potential.
The Types of Flexco Belt Scraper
Installation and Maintenance
Proper installation and maintenance of Flexco belt scrapers are crucial to ensuring their effectiveness and longevity. This guide provides a comprehensive overview of the steps involved in installing Flexco belt scrapers and offers tips for maintaining and replacing them to maximize their lifespan and performance.
Step-by-Step Guide to Installing Flexco Belt Scrapers
Installing a Flexco belt scraper involves several critical steps. Following these steps carefully will ensure that the scraper functions optimally and provides effective cleaning.
1. Preparation:
Before beginning the installation, gather all necessary tools and equipment. This includes wrenches, screwdrivers, measuring tape, and the Flexco belt scraper kit. Ensure that the conveyor belt is stopped, locked out, and tagged out to prevent accidental start-up during installation.
2. Identify the Installation Location:
Determine the correct location for the scraper on the conveyor system. The primary scraper is typically installed at the discharge point of the conveyor, where it can effectively remove material from the belt. The secondary scraper is placed further along the belt, ensuring thorough cleaning.
3. Measure and Mark:
Measure the width of the conveyor belt to ensure that the scraper matches the belt’s width. Mark the positions for the mounting brackets on the conveyor structure. The marks should be evenly spaced and aligned with the belt’s centerline to ensure the scraper’s effective operation.
4. Install Mounting Brackets:
Attach the mounting brackets to the conveyor structure at the marked positions. Use appropriate fasteners and ensure that the brackets are securely fixed. The brackets should be level and aligned to prevent any misalignment of the scraper.
5. Mount the Scraper Blade:
Attach the scraper blade to the mounting brackets. Adjust the blade so that it makes contact with the conveyor belt at the proper angle. The blade should be positioned to clean the belt effectively without causing excessive wear. Tighten the fasteners to secure the blade in place.
6. Adjust Tension:
Adjust the tension of the scraper blade to ensure it maintains consistent contact with the conveyor belt. Proper tension is crucial for effective cleaning and to prevent damage to the belt. Flexco scrapers typically come with tensioning mechanisms that allow for easy adjustment.
7. Test and Fine-Tune:
After installing the scraper, run the conveyor belt at a slow speed to test the scraper’s performance. Observe the blade’s contact with the belt and make any necessary adjustments to the angle, tension, or position. Ensure that the scraper is removing material effectively and that there is no excessive wear or noise.
8. Secure and Finalize:
Once the scraper is properly adjusted and functioning, secure all fasteners and recheck the installation. Ensure that all components are tight and that the scraper is stable. Remove any tools and materials from the work area and ensure that the conveyor system is clear before restarting.
Tips for Maintaining and Replacing Scrapers for Longevity
Regular maintenance and timely replacement of Flexco belt scrapers are essential for maintaining their effectiveness and extending their lifespan. Here are some tips to help you keep your scrapers in optimal condition:
1. Regular Inspections:
Conduct regular inspections of the scrapers to check for wear and damage. Look for signs of blade wear, cracks, or material buildup. Inspect the mounting brackets and tensioning mechanisms to ensure they are secure and functioning correctly.
2. Clean the Scrapers:
Keep the scrapers clean to maintain their effectiveness. Remove any material buildup on the blades and brackets. Cleaning the scrapers regularly prevents material accumulation, which can reduce the scraper’s efficiency and cause wear.
3. Monitor Blade Wear:
Monitor the wear of the scraper blades and replace them when necessary. Flexco scrapers are designed with wear indicators that make it easy to determine when the blades need replacing. Timely replacement of worn blades ensures consistent cleaning performance and prevents damage to the conveyor belt.
4. Adjust Tension Regularly:
Check and adjust the tension of the scraper blades regularly. Proper tension ensures effective cleaning and prevents the blades from causing excessive wear on the belt. Flexco scrapers typically have easy-to-use tensioning mechanisms that allow for quick adjustments.
5. Use Genuine Replacement Parts:
When replacing scraper blades or other components, use genuine Flexco replacement parts. Genuine parts are designed to fit and function correctly with the scraper system, ensuring optimal performance and longevity.
6. Keep Spare Parts on Hand:
Maintain an inventory of spare parts, including scraper blades, tensioners, and mounting hardware. Having spare parts readily available reduces downtime when replacements are needed and ensures that the scrapers remain operational.
7. Document Maintenance Activities:
Keep a record of all maintenance activities, including inspections, cleaning, adjustments, and replacements. Documenting these activities helps track the condition of the scrapers and identify any recurring issues. It also provides a reference for future maintenance planning.
8. Train Maintenance Personnel:
Ensure that maintenance personnel are trained in the proper installation, adjustment, and maintenance of Flexco belt scrapers. Proper training ensures that the scrapers are installed and maintained correctly, maximizing their effectiveness and lifespan.
9. Perform Preventive Maintenance:
Implement a preventive maintenance schedule that includes regular inspections, cleaning, and adjustments. Preventive maintenance helps identify and address potential issues before they become major problems, ensuring continuous and reliable scraper performance.
10. Collaborate with Flexco:
Work with Flexco representatives and take advantage of their expertise and support. Flexco offers technical assistance, training, and resources to help you maintain your scrapers effectively. Collaborating with Flexco ensures that you are using the best practices and solutions for your conveyor system.
Material and Design of Flexco Scrapers
The material and design of Flexco scrapers are key factors that contribute to their effectiveness and reliability in maintaining clean conveyor belts. Flexco belt scrapers are engineered to provide superior performance and durability, ensuring efficient operation and reduced maintenance. This section explores the specific materials used in Flexco scrapers, particularly the polyurethane belt scraper, and highlights the innovative design features that enhance their efficiency.
Polyurethane Belt Scraper: Durability and Performance
Polyurethane is a commonly used material in the construction of Flexco belt scrapers due to its excellent properties that suit the demanding conditions of conveyor systems. Here’s an in-depth look at the durability and performance benefits of polyurethane belt scrapers:
Durability: Polyurethane is known for its high durability, making it an ideal material for belt scrapers. It can withstand the continuous contact and friction with the conveyor belt, resisting wear and tear over long periods. This durability ensures that the scrapers remain effective in removing residual materials from the belt, reducing the need for frequent replacements and maintenance.
Flexibility: The flexibility of polyurethane allows the scraper to maintain close contact with the conveyor belt surface, ensuring thorough cleaning. This flexibility is crucial for adapting to the belt’s contours and variations, providing consistent performance even as the belt undergoes changes due to load variations or environmental conditions.
Chemical Resistance: Polyurethane’s resistance to chemicals makes it suitable for use in various industrial environments where exposure to oils, solvents, and other chemicals is common. This resistance ensures that the scraper does not degrade or lose effectiveness when exposed to harsh substances, maintaining its cleaning efficiency.
Impact Resistance: Conveyor systems often handle heavy and abrasive materials that can cause significant impact. Polyurethane belt scrapers are designed to absorb and resist these impacts without cracking or breaking. This impact resistance contributes to the scraper’s longevity and reliability, ensuring continuous operation in demanding conditions.
Temperature Stability: Polyurethane maintains its physical properties across a wide range of temperatures, making it suitable for both high and low-temperature environments. This temperature stability ensures that the scraper performs consistently regardless of the ambient conditions, providing reliable cleaning year-round.
Flexco Scrapers: Innovative Design and Efficiency
Beyond material selection, the design of Flexco scrapers plays a crucial role in their efficiency and effectiveness. Flexco’s innovative approach to scraper design incorporates several features that enhance performance and ease of use:
Modular Design: Flexco belt scrapers often feature a modular design, allowing for easy installation, adjustment, and replacement of individual components. This design flexibility enables operators to customize the scraper setup to meet specific requirements and makes maintenance more straightforward. By replacing only the worn components instead of the entire scraper, maintenance costs and downtime are significantly reduced.
Tensioning Systems: Proper tensioning is essential for maintaining close contact between the scraper and the conveyor belt. Flexco scrapers are equipped with advanced tensioning systems that ensure consistent pressure is applied to the belt, maximizing cleaning efficiency. These tensioning systems can be easily adjusted to adapt to belt wear and changing conditions, ensuring optimal performance over the scraper’s lifespan.
Self-adjusting Mechanisms: Some Flexco scrapers incorporate self-adjusting mechanisms that automatically adapt to belt variations and wear. These mechanisms ensure continuous and consistent contact with the belt, eliminating the need for frequent manual adjustments. This self-adjusting feature enhances the scraper’s efficiency and reduces the need for operator intervention, leading to improved productivity and reduced maintenance efforts.
Blade Design: The design of the scraper blade is critical for effective material removal. Flexco scrapers use blades made from high-performance materials such as tungsten carbide or polyurethane, designed to provide a sharp and consistent edge for thorough cleaning. The blades are shaped to optimize contact with the belt surface, ensuring that even the most stubborn materials are effectively removed.
Compatibility with Belt Types: Flexco scrapers are designed to be compatible with a wide range of conveyor belt types and sizes. This versatility ensures that Flexco belt scrapers can be used in various applications, from mining and quarrying to food processing and packaging. The ability to integrate seamlessly with different conveyor systems makes Flexco scrapers a flexible and reliable solution for maintaining clean belts.
Ease of Installation and Maintenance: Flexco emphasizes ease of installation and maintenance in their scraper designs. Clear installation instructions and intuitive design features allow for quick and hassle-free setup. Maintenance procedures are simplified through the use of modular components and easy-access designs, ensuring that scrapers can be serviced with minimal disruption to operations.
Safety Features: Safety is a paramount consideration in the design of Flexco belt scrapers. Features such as shielded tensioning mechanisms, rounded edges, and secure mounting systems are incorporated to protect operators during installation and maintenance. These safety features help to minimize the risk of accidents and injuries, contributing to a safer working environment.
The Keys of Flexco Belt Scraper
Types of Flexco Belt Cleaners
Flexco belt scrapers play a crucial role in maintaining the cleanliness and efficiency of conveyor systems. By removing residual material from the conveyor belt, they prevent buildup, reduce wear, and ensure smooth operation. Flexco offers a range of belt cleaners, each designed to address specific cleaning needs. This section explores the different types of Flexco belt cleaners, focusing on primary belt cleaners and Flexco secondary scrapers, and their features and benefits.
Primary Belt Cleaners: Features and Benefits
Primary belt cleaners, also known as pre-cleaners, are the first line of defense against material buildup on conveyor belts. Installed at the head pulley, these cleaners remove the bulk of the material adhering to the belt as it exits the discharge point. Here are the key features and benefits of Flexco primary belt cleaners:
Features:
- Durable Blades:
Flexco primary belt cleaners are equipped with durable blades made from high-quality materials such as tungsten carbide or polyurethane. These blades are designed to withstand harsh conditions and provide effective cleaning over a long service life. - Spring Tensioning Systems:
Many primary belt cleaners from Flexco feature spring tensioning systems that maintain consistent pressure against the belt. This ensures continuous, effective cleaning even as the blades wear down, reducing the need for frequent adjustments. - Easy Installation and Adjustment:
Flexco primary belt cleaners are designed for easy installation and adjustment. They come with detailed instructions and mounting hardware, making it simple to set up and fine-tune the cleaner for optimal performance. - Multiple Blade Options:
Flexco offers a variety of blade options to suit different applications and materials. Whether dealing with abrasive materials or sticky substances, there is a blade designed to handle the specific challenge.
Benefits:
- Enhanced Conveyor Efficiency:
By removing the bulk of the material at the discharge point, primary belt cleaners prevent material buildup and reduce the risk of carryback. This enhances the overall efficiency of the conveyor system, ensuring smooth and reliable operation. - Reduced Maintenance Costs:
Effective primary cleaning minimizes the wear and tear on the conveyor belt and other components. This reduces the frequency of maintenance and replacement, leading to significant cost savings over time. - Improved Safety:
Cleaner belts reduce the risk of material spillage, which can create hazardous working conditions. Primary belt cleaners help maintain a safer working environment by keeping the conveyor system clean and free of debris. - Prolonged Belt Life:
Removing abrasive and damaging materials from the belt surface extends the life of the conveyor belt. Primary belt cleaners protect the belt from premature wear, ensuring longer service life and reduced downtime.
Flexco Secondary Scraper: Ensuring Optimal Belt Cleanliness
While primary belt cleaners are essential for removing the bulk of the material, secondary scrapers provide a final, thorough cleaning to ensure optimal belt cleanliness. Installed further along the conveyor, secondary scrapers address any residual material left by the primary cleaner.
Features:
- Flexible Blade Design:
Flexco secondary scrapers often feature flexible blades that can conform to the belt’s surface. This flexibility allows the scraper to clean effectively even if the belt has minor imperfections or variations in thickness. - Adjustable Tensioning Mechanisms:
Secondary scrapers from Flexco come with adjustable tensioning mechanisms that allow for precise control of the blade pressure against the belt. This ensures effective cleaning while minimizing blade wear. - Corrosion-Resistant Materials:
To withstand harsh environmental conditions, Flexco secondary scrapers are made from corrosion-resistant materials. This durability ensures long-lasting performance even in challenging settings. - Dual Blade Systems:
Some Flexco secondary scrapers utilize a dual blade system for enhanced cleaning efficiency. The primary blade removes most of the residual material, while the secondary blade provides a final sweep to ensure a spotless belt.
Benefits:
- Complete Cleaning Solution:
By working in conjunction with primary belt cleaners, Flexco secondary scrapers provide a comprehensive cleaning solution. They ensure that even the smallest particles are removed, preventing carryback and material buildup. - Enhanced Material Recovery:
Secondary scrapers help recover valuable materials that might otherwise be lost. By ensuring thorough cleaning, they contribute to more efficient material handling and reduced waste. - Increased Conveyor Reliability:
Thorough cleaning reduces the risk of operational issues caused by material buildup, such as belt misalignment and increased wear. Secondary scrapers help maintain the reliability and performance of the conveyor system. - Reduced Environmental Impact:
Keeping the conveyor system clean reduces the risk of material spillage and contamination. Secondary scrapers contribute to a cleaner, more environmentally friendly operation by minimizing waste and ensuring proper material handling. - Ease of Maintenance:
Flexco secondary scrapers are designed for easy maintenance. Blade replacement and tension adjustments can be performed quickly and efficiently, reducing downtime and ensuring continuous operation. - Customizable Solutions:
Flexco offers a range of secondary scraper options to meet specific operational needs. This customization ensures that each conveyor system can achieve optimal cleanliness and performance, regardless of the material being conveyed. - Longevity and Durability:
The high-quality materials and robust construction of Flexco secondary scrapers ensure long-lasting durability. This reliability translates to fewer replacements and lower overall maintenance costs.
FAQS about Flexco Belt Scraper
Yes, conveyor belts are a critical component in various industries, including mining, manufacturing, and food processing. They consist of a continuous loop of material that transports products or materials from one point to another. Conveyor belts can be made from different materials, such as rubber, fabric, or metal, depending on the application. They come in various types, including flat belts, modular belts, and steel cord belts, each designed for specific purposes. Key components of conveyor systems include pulleys, idlers, scrapers, and drive units. Proper maintenance, including regular cleaning and inspection, is essential to ensure the efficient and reliable operation of conveyor belts. Understanding the specific requirements of the conveyed material and the operating environment is crucial for selecting the appropriate belt type and ensuring optimal performance.
The angle of a belt scraper refers to the positioning of the scraper blade relative to the conveyor belt’s surface. This angle is critical for effective cleaning and minimizing belt wear. Typically, the angle ranges from 20 to 30 degrees, depending on the type of material being conveyed and the design of the scraper. The goal is to achieve optimal contact between the scraper blade and the belt without exerting excessive pressure that could damage the belt. Adjusting the scraper angle can help enhance cleaning efficiency, reduce the risk of material buildup, and prolong the belt’s life. Proper installation and regular maintenance are essential to ensure that the scraper operates at the correct angle for optimal performance.
Cleaning a conveyor belt involves several methods and tools to ensure thorough and efficient removal of debris and buildup. Here are some common steps:
Scrapers: Install primary and secondary scrapers to remove the bulk of the material. Primary scrapers are usually placed at the head pulley to remove large pieces, while secondary scrapers follow to clean finer residues.
Brushes: Rotating brushes can be installed to sweep off finer particles that scrapers may miss.
Wash Stations: For belts handling sticky or wet materials, wash stations use water jets to rinse off residues. Detergents or cleaning solutions can be added for a more effective clean.
Vacuum Systems: In some cases, vacuum systems are used to suck up dust and fine particles from the belt.
Manual Cleaning: Regular manual cleaning with brushes or cloths might be necessary for thorough maintenance, especially in hard-to-reach areas. Regular cleaning of conveyor belts is crucial for preventing material buildup, ensuring smooth operation, and extending the lifespan of the conveyor system.
A scraper in a belt conveyor is a device used to clean the conveyor belt by removing material residue, buildup, or carryback. Scrapers are essential for maintaining the efficiency and longevity of conveyor systems. They are typically mounted at strategic points along the belt, especially near the discharge point, to ensure that debris and excess material do not stick to the belt as it returns. Scrapers are made from various materials, including polyurethane, rubber, and tungsten carbide, each suited for different applications and material types. By keeping the belt clean, scrapers help prevent material spillage, reduce maintenance costs, and minimize downtime due to belt wear or damage.
Last Updated on June 25, 2024 by Jordan Smith
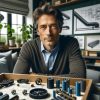
Jordan Smith, a seasoned professional with over 20 years of experience in the conveyor system industry. Jordan’s expertise lies in providing comprehensive solutions for conveyor rollers, belts, and accessories, catering to a wide range of industrial needs. From initial design and configuration to installation and meticulous troubleshooting, Jordan is adept at handling all aspects of conveyor system management. Whether you’re looking to upgrade your production line with efficient conveyor belts, require custom conveyor rollers for specific operations, or need expert advice on selecting the right conveyor accessories for your facility, Jordan is your reliable consultant. For any inquiries or assistance with conveyor system optimization, Jordan is available to share his wealth of knowledge and experience. Feel free to reach out at any time for professional guidance on all matters related to conveyor rollers, belts, and accessories.