Enhancing Industrial Conveyors with FMC Conveyor Rollers
Conveyor rollers are essential components widely utilized in various industrial sectors to facilitate the automated transport of goods and materials. These rollers significantly reduce labor costs and increase the efficiency of material handling operations. FMC Conveyor Rollers are a prominent solution in these settings, esteemed for their reliability and superior performance. Known for their robust construction, FMC conveyor rollers enhance system durability and improve operational throughput. Their design accommodates diverse industrial demands, making them ideal for heavy-duty applications where precision and efficiency are critical. By integrating FMC conveyor rollers into their conveyor systems, industries can achieve a significant optimization of their production processes, ensuring smooth, continuous, and efficient operations. The reputation of FMC conveyor rollers for durability and efficiency not only stems from their build quality but also from their ability to operate under stringent conditions while minimizing downtime and maintenance needs.
What are FMC Conveyor Rollers
FMC Conveyor Rollers are a cornerstone in the design of modern industrial conveyor systems, known for their robustness and adaptability across various applications. These rollers are specifically engineered to enhance conveyor reliability and efficiency, pivotal for continuous operations in industries such as mining, automotive, and food processing.
Model Numbers and Dimensions
Each model of FMC conveyor rollers comes with unique identifiers that specify its dimensions and suitability for certain applications. For instance, the model number 1730-285-G is one of the most popular FMC conveyor rollers. This model boasts a length of 17.12 inches and a cylinder diameter of 6 inches, making it an excellent choice for systems requiring medium to heavy-duty material handling capabilities.
Material Specifications and Build Quality
Typically constructed from high-grade steel, FMC conveyor rollers are designed to withstand the rigors of heavy loads and continuous operation. The choice of material ensures that the rollers are not only durable but also have a low wear rate, which is essential for maintaining the efficiency of the conveyor system over time.
Customization Options
FMC offers customization options for their conveyor rollers, allowing them to be tailored to the specific needs of different conveyor setups. Whether it’s varying the length, diameter, or even the material of the roller, FMC’s flexible manufacturing process ensures that each roller is optimized for its intended use.
Performance and Reliability
The design and manufacture of FMC conveyor rollers focus on performance under diverse environmental conditions. They are capable of operating smoothly in both high and low-temperature environments, which is a testament to their reliability and the quality of materials used.
By integrating FMC conveyor rollers into your systems, you can expect not only an improvement in the physical throughput of materials but also enhanced overall system health due to reduced wear and tear on other components. This strategic improvement can significantly lower maintenance costs and increase the uptime of the entire conveyor system.
Key Features of FMC Conveyor Rollers
FMC Conveyor Rollers are integral to numerous industrial systems, where their design and material choices play critical roles in their functionality and longevity. Below is a detailed exploration of these aspects, highlighting the robust features that FMC conveyor rollers are known for.
Construction Material and Dimensions:
The primary material used for FMC conveyor rollers is steel, which provides excellent strength and durability, necessary for handling substantial loads. The choice of steel is critical not only for its toughness but also for its ability to resist wear, corrosion, and deformation under heavy loads. Regarding dimensions, these rollers are available in various lengths and diameters to accommodate different industrial needs. Standard diameters like the 4-inch rollers are common, but FMC also offers sizes ranging up to 6 inches for heavier applications, ensuring that there is a roller suitable for any conveyor setup.
Types of FMC Conveyor Rollers:
FMC manufactures several types of conveyor rollers, designed to meet the diverse needs of industries from mining to packaging facilities. Here are five examples:
- Heavy-Duty Rollers: These are designed for systems that require high durability and can handle heavy loads. They feature thicker walls and a more robust bearing design to endure the high forces typically seen in mining and quarrying operations.
- 4 Inch Diameter Rollers: Perfect for medium-load applications, these rollers offer a balance between size and capacity, making them suitable for agricultural and manufacturing conveyors.
- Impact Rollers: Built to absorb shocks and impacts at loading points, these rollers extend the life of the conveyor belt and system by reducing the forces transmitted through the framework.
- Guide Rollers: Used to ensure the conveyor belt stays centered and minimizes lateral movement, which can lead to uneven wear and tear on the belt.
- Return Rollers: These are used on the underside of the conveyor to support the return section of the belt. They are typically smoother than drive rollers to minimize the wear on the backside of the belt.
Robustness from Design and Material Choices:
The robustness of FMC conveyor rollers is not just due to their material composition but also their meticulous design. The dimensions of each roller are calculated to provide optimal performance in the environments they are used. This includes considerations for load distribution, belt alignment, and environmental challenges such as temperature fluctuations and exposure to chemicals.
By integrating these key features, FMC conveyor rollers ensure enhanced performance, reliability, and efficiency of conveyor systems, making them a preferred choice in critical industrial applications where failure is not an option. The ability to customize these rollers for specific operations further cements their role as essential components in modern industrial environments.
FMC Conveyor Rollers Applications
FMC Conveyor Rollers are widely recognized for their versatility and reliability, making them ideal for a broad range of industrial applications. Below we explore the various industries that benefit from these robust components and the specific uses within those sectors.
Industries Utilizing FMC Conveyor Rollers:
- Mining and Quarrying:
FMC conveyor rollers are crucial in the mining industry, where they are used on materials handling equipment to transport mined materials such as coal, gold, and iron ore from the mining site to the processing plant. Their robust construction withstands the abrasive and heavy nature of mined substances. - Agriculture:
In agriculture, these rollers are used in conveyor systems that move grain or other bulk products throughout the storage facilities. They help in the efficient transfer of products from silos to trucks or processing areas, minimizing damage to the grains. - Packaging and Distribution:
The packaging sector utilizes FMC conveyor rollers to streamline the movement of products along the production line. From moving boxes within warehouses to handling delicate items during the packaging process, these rollers are essential for efficient operations. - Automotive Manufacturing:
FMC conveyor rollers are employed extensively in the automotive industry, particularly in assembly lines where components need to be moved smoothly through various stages of assembly from chassis construction to final inspection. - Food Processing:
In food processing, these rollers are used to transport food items through cooking, cooling, and packaging processes. Their ability to be customized for hygiene (e.g., stainless steel construction) makes them perfect for applications where cleanliness is paramount.
Specific Uses of FMC Conveyor Rollers in These Industries:
- Underground Mining Operations:
In underground mining, FMC conveyor rollers are used to facilitate the smooth and efficient transport of extracted ore to the surface. Their durability is crucial in reducing downtime and maintenance costs. - Grain Elevator Systems:
Within the agricultural sector, these rollers are integral to grain elevator systems, helping to prevent spillages and manage the flow of grain between different elevations in storage facilities. - Automated Packaging Lines:
FMC rollers streamline packaging operations by ensuring that products are moved swiftly and smoothly across sorting, filling, and sealing stations, which enhances the speed and reliability of packaging processes. - Car Assembly Lines:
In car manufacturing, these rollers support the conveyor belts that carry car parts through the assembly line. Their precision and sturdiness ensure that parts are transported without interruption, which is vital for maintaining production timelines. - Conveying Cooked Foods:
In the food industry, FMC conveyor rollers are used in systems designed to handle cooked products moving through cooling conveyors, which require materials that can withstand high temperatures and regular cleaning without degrading.
By incorporating FMC conveyor rollers into these industries, companies can achieve significant improvements in operational efficiency, product handling safety, and system longevity. The adaptability of these rollers to different environmental and operational demands makes them invaluable in settings that require high reliability and efficiency. Their continued use across these diverse sectors underscores their critical role in modern industrial applications.
Pricing and Purchasing Options for FMC Conveyor Rollers
Understanding the pricing and purchasing options for FMC Conveyor Rollers is crucial for budget planning and procurement strategies in industrial settings. This section provides insight into the various price points of these rollers and offers guidance on where to purchase them.
Price Points of FMC Conveyor Rollers:
Standard Duty Rollers:
- Price Range: $50 – $100 per roller
- Description: Ideal for lightweight and medium applications, these rollers are cost-effective and are widely used in industries like packaging and food processing.
Heavy-Duty Rollers:
- Price Range: $100 – $250 per roller
- Description: Designed for high-load applications such as mining and aggregate processing, heavy-duty rollers are more expensive due to their enhanced durability and material specifications.
Customized Rollers:
- Price Range: $150 – $300 per roller
- Description: Custom rollers can be designed to meet specific operational needs, including unusual sizes or special materials like stainless steel for food-grade applications.
Impact Rollers:
- Price Range: $120 – $200 per roller
- Description: Built to absorb impact at loading zones, these rollers are slightly pricier due to their specialized design and materials that reduce wear on the conveyor belt.
Return Rollers:
- Price Range: $40 – $90 per roller
- Description: These rollers support the return side of the conveyor belt and are less expensive than drive rollers; ideal for cost-sensitive operations.
Where to Find FMC Conveyor Rollers for Sale:
Manufacturer’s Website:
- Direct Purchase: Purchasing directly from FMC’s website ensures that you get genuine products with warranty support. This is recommended for buyers needing custom specifications.
Industrial Supply Companies:
- Distributors Like Grainger and McMaster-Carr: These suppliers stock a wide range of FMC conveyor rollers and often provide next-day shipping. They are ideal for urgent needs.
Online Marketplaces:
- Platforms like Amazon and eBay: These marketplaces offer both new and replacement FMC conveyor rollers, sometimes at discounted rates. They are suitable for buyers looking for convenience and quick delivery.
Local Industrial Retailers:
- Local Stores: Purchasing from local stores can be advantageous for immediate availability and avoiding shipping costs. They might also offer installation services.
Used and Surplus Dealers:
- Economical Options: Dealers in used and surplus industrial equipment can be good sources for purchasing FMC conveyor rollers at significantly lower prices. This option is best for companies looking to reduce upfront costs.
By exploring these pricing and purchasing options, businesses can find the most cost-effective solutions for incorporating FMC conveyor rollers into their systems. Whether opting for new, customized, or even used rollers, there are avenues available to meet various operational demands and budgetary constraints. Each option offers a balance of cost, convenience, and speed of delivery, allowing for strategic procurement that aligns with business objectives.
Advantages of Choosing FMC Conveyor Rollers
Selecting FMC Conveyor Rollers for your industrial conveyor systems offers numerous benefits, from improved operational efficiency to enhanced durability and ease of maintenance. Below, we explore these advantages in detail, demonstrating why FMC stands out in the market.
Key Benefits of Using FMC Conveyor Rollers:
Enhanced Efficiency:
- Reduced Friction: FMC conveyor rollers are designed to minimize friction, which in turn reduces the power consumption of the conveyor system. This efficiency can lead to significant cost savings over the lifecycle of the rollers.
- Optimal Throughput: With precise engineering, these rollers maintain consistent movement of materials, thus optimizing the throughput and reducing bottlenecks in production processes.
Increased Durability:
- Robust Materials: Made from high-quality steel, FMC conveyor rollers are built to last. They are resistant to wear and tear, even under high-load conditions, which prolongs their lifespan and reduces the need for frequent replacements.
- Weather and Chemical Resistant: Whether installed indoors or outdoors, these rollers can withstand harsh environmental conditions including extreme temperatures and corrosive substances, which is critical for industries such as mining and chemicals.
Ease of Maintenance:
- Self-Lubricating Design: Many FMC rollers feature self-lubricating bearings that significantly lower the maintenance requirements and extend the operational life of the rollers.
- Easy to Replace: The standardized design of FMC conveyor rollers makes them easy to install and replace, minimizing downtime and maintenance costs.
Versatility:
- Wide Range of Applications: FMC conveyor rollers are available in a variety of sizes and types, making them suitable for a wide range of applications across different industries, including heavy-duty and precision-required environments.
Noise Reduction:
- Quiet Operation: Engineered to operate quietly, FMC rollers help in reducing noise pollution in the workplace, which is essential for facilities that prioritize creating a better working environment for their employees.
Comparative Benefits Over Other Brands:
- Superior Load Capacity: FMC conveyor rollers are renowned for their heavy-duty performance. They can handle greater loads compared to many other brands, which often translates into fewer performance issues and lower chances of breakdown.
- Longevity: Thanks to the high-quality materials and advanced manufacturing processes used, FMC rollers generally have a longer operational life. This durability is a key factor in reducing the lifecycle cost of the conveyor system.
- Customizability: Unlike some other brands, FMC provides extensive customization options for their rollers, allowing them to be tailored to specific needs and applications, thereby enhancing the overall efficiency and functionality of the conveyors.
- Comprehensive Product Line: FMC offers a more extensive range of conveyor roller types and sizes than many competitors, which ensures that clients can find exactly what they need for any specific application, whether it’s a standard or a highly specialized system.
- Customer Support and Technical Assistance: FMC is known for excellent customer service, providing technical support and guidance from selection through to maintenance, which is often a step above what many other roller manufacturers offer.
Choosing FMC conveyor rollers not only improves the efficiency and productivity of conveyor systems but also provides a reliable, long-term solution that other brands might not match, particularly in heavy-duty and industrial applications. The combination of durability, maintenance ease, and operational efficiency makes FMC a top choice in the market.
Customization and Parts for FMC Conveyor Rollers
FMC Conveyor Rollers are not only renowned for their robustness and efficiency but also for their adaptability to various industrial needs through customization. This flexibility ensures that every industrial setup can achieve optimal performance by using rollers that specifically match their requirements. Additionally, understanding how to obtain parts for these rollers is crucial for maintaining and upgrading your conveyor system.
Customization Options
Size Customization:
- FMC offers customization in the size of the conveyor rollers, allowing them to be tailored to the specific dimensions required by the customer’s conveyor system. This includes varying lengths and diameters to perfectly match the load requirements and the physical space of the conveyor.
Material Choices:
- Steel Rollers: Standard options include high-grade carbon steel and stainless steel, which are perfect for durability and in cases where corrosion resistance is needed, respectively.
- Coated Rollers: For industries requiring additional protection against wear, chemicals, or environmental factors, rollers can be coated with materials such as rubber, polyurethane, or Teflon.
Bearing Types:
- Depending on the operational needs, FMC provides different bearing options including precision, semi-precision, and non-precision bearings to balance between cost and performance efficiency.
Shaft Configurations:
- Custom shaft configurations are available to integrate seamlessly with existing conveyor equipment. Options include different shaft ends such as fixed, floating, or threaded styles, which can be selected based on the mounting and load requirements.
Specialty Rollers:
- Impact and Return Rollers: Custom-built for high impact zones such as loading points and for supporting the return belt.
- Temperature and Chemical Resistant Rollers: Specially designed rollers that can withstand extreme temperatures and exposure to aggressive chemicals.
Obtaining Parts for Maintenance and Upgrades
Replacement Parts:
- Bearings and Shafts: Easily obtainable and replaceable, these parts are critical for regular maintenance to ensure the longevity and proper functioning of the rollers.
- Outer Shell: Should the surface of the roller be damaged or worn out, replacement shells can be fitted without needing to replace the entire roller.
Ordering Parts:
- Parts can be ordered directly from FMC’s parts department or through authorized distributors. It’s important to provide the model number and specifications of your rollers to ensure compatibility.
Technical Support:
- FMC provides technical support for selecting the right parts for your needs, including advice on upgrades that can enhance the performance of your existing system. This support extends to troubleshooting installation issues and providing detailed product manuals.
Custom Parts:
- For systems requiring non-standard parts, FMC can design and manufacture custom parts that meet the specific needs of the customer’s application. This is particularly useful for older systems or unique applications where standard parts may not suffice.
Maintenance Kits:
- FMC also offers maintenance kits that include everything needed to perform standard repairs and maintenance on the conveyor rollers. These kits typically contain bearings, seals, and lubrication supplies to extend the service life of the rollers.
By taking advantage of the customization options FMC offers, industries can enhance the precision and efficiency of their conveyor systems tailored specifically to their operational needs. Additionally, easy access to parts and comprehensive technical support ensures that maintaining and upgrading your FMC conveyor rollers is straightforward and cost-effective, further adding to the overall efficiency and longevity of the conveyor system. This level of support and customization capability sets FMC apart in the market, solidifying their reputation as a leading provider of industrial conveyor solutions.
FAQs About FMC Conveyor Rollers
A conveyor roller is a vital component of a roller conveyor system that facilitates the free-moving, automated transport of goods and materials. Typically cylindrical, these rollers spin freely when objects are moved over them, allowing for the efficient transfer of items across a flat or slightly inclined surface. Conveyor rollers are commonly made from metal (such as steel or aluminum), plastic, or rubber, depending on their intended use and the environmental conditions they will face.
Conveyor rollers are essential in numerous industrial applications including manufacturing lines, packaging, sorting facilities, and material handling systems. Their effectiveness in reducing labor costs and enhancing workflow makes them indispensable in modern production and distribution networks. They are particularly valued for their ability to handle a wide range of materials, provide support and direction to goods in transit, and reduce operational times and costs.
Conveyor rollers can vary significantly in type, size, design, and material, each tailored for specific conditions and tasks. Here are the main types commonly used in various industries:
Gravity Rollers: The most simple and inexpensive type, these rollers work without power and utilize gravity when inclined to move items. They are ideal for light to medium weight products and applications where the conveyor path is straightforward.
Motorized Roller (MDR) Conveyors: These rollers are part of a powered roller conveyor system that uses motors embedded within some of the rollers to move the conveyor belt. This setup allows for controlled movements of goods and is energy efficient.
Grooved Rollers: Designed with grooves that are intended to mesh with belts, chains, or o-rings, these rollers are used to power roller belts and move items, particularly in heavy-duty applications.
Impact Rollers: Placed at conveyor loading and transfer points, impact rollers are designed to absorb the shock and impact from falling materials, which helps protect the belt and system from damage.
Live Shaft Rollers: These rollers have shafts that run the full length of the roller and are used in situations where the roller must handle high loads.
Each type of roller is designed for specific environmental conditions and operational needs, providing flexibility in how conveyor systems are structured and used across industries.
While “the best” can vary by specific needs, FMC Technologies is frequently cited as a leading manufacturer of conveyor rollers, known for its robust and efficient designs. FMC’s conveyor rollers are prized for their reliability, durability, and the company’s ability to provide customized solutions that meet specific industrial requirements.
Other notable manufacturers include Hytrol, Interroll, and Rexnord, which offer a range of products from standard rollers to complex conveyor solutions. The choice of the best manufacturer can depend on several factors including:
Specific Application Needs: Different applications require different types of rollers.
Budget Constraints: Prices vary significantly among manufacturers.
Technical Support and Service: After-sales support is crucial, especially for complex installations.
Product Quality and Reliability: Long-term costs are reduced with durable and reliable products.
Evaluating these factors will help determine the best conveyor roller manufacturer for your needs.
An MDR (Motor Driven Roller) conveyor is a type of powered roller conveyor which integrates the motor within the roller itself. MDR systems are highly efficient and provide several benefits over traditional conveyor systems. Each roller in an MDR system has its own built-in motor that is connected to other rollers via cards that allow for electronic communication.
MDR rollers offer precise control over product movement, making them ideal for applications involving fragile items or where accurate product positioning is necessary. They are also energy efficient as the motors can be activated individually when needed, reducing power consumption overall.
Moreover, MDR systems are known for their quiet operation, safety (due to low voltage usage), and ease of maintenance. The modular design also allows for flexibility in layout configurations and easy expansion of conveyor systems. This makes MDR technology popular in distribution centers, fulfillment centers, and manufacturing facilities where variability, control, and space efficiency are key concerns.
Last Updated on May 17, 2024 by Jordan Smith
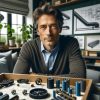
Jordan Smith, a seasoned professional with over 20 years of experience in the conveyor system industry. Jordan’s expertise lies in providing comprehensive solutions for conveyor rollers, belts, and accessories, catering to a wide range of industrial needs. From initial design and configuration to installation and meticulous troubleshooting, Jordan is adept at handling all aspects of conveyor system management. Whether you’re looking to upgrade your production line with efficient conveyor belts, require custom conveyor rollers for specific operations, or need expert advice on selecting the right conveyor accessories for your facility, Jordan is your reliable consultant. For any inquiries or assistance with conveyor system optimization, Jordan is available to share his wealth of knowledge and experience. Feel free to reach out at any time for professional guidance on all matters related to conveyor rollers, belts, and accessories.