Key Role: Function of Snub Pulley in Belt Conveyor
The function of snub pulley in belt conveyor systems is crucial for enhancing the performance and reliability of the conveyor. A snub pulley is strategically placed to increase the contact area between the conveyor belt and the drive pulley, thereby improving traction and reducing belt slippage. This positioning helps in effectively managing the belt tension and ensuring smooth operation.Pulleys, in general, play a significant role in the overall efficiency and longevity of belt conveyors. They help guide and support the conveyor belt, reduce stress on the belt, and maintain proper alignment. The function of snub pulley in belt conveyor systems, in particular, is vital for optimizing the wrap angle, which directly influences the efficiency and lifespan of the conveyor belt.
Conveyor Belt Pulleys: Function of Snub Pulley in Belt Conveyor
Types of Pulleys in Belt Conveyors
In the realm of belt conveyors, various types of pulleys play integral roles in ensuring the system operates efficiently and reliably. Each pulley type has a specific function and contributes uniquely to the overall performance of the conveyor system.
Drive Pulley
The drive pulley is the primary component that propels the conveyor belt. Positioned at the discharge end of the conveyor, it is connected to the motor, which supplies the rotational power needed to move the belt. The drive pulley’s function is to transmit power from the motor to the conveyor belt, ensuring the continuous movement of materials along the conveyor system.
Tail Pulley
Located at the opposite end of the conveyor from the drive pulley, the tail pulley serves as a return point for the conveyor belt. It helps in maintaining proper tension in the belt as it returns from the discharge point back to the loading point. The tail pulley is also crucial for guiding the belt and ensuring it runs smoothly and without deviation.
Head Pulley
The head pulley, sometimes referred to as the discharge pulley, is situated at the head of the conveyor belt where the materials are discharged. Similar to the drive pulley, the head pulley provides a means to move the belt but is specifically focused on guiding the belt at the point of discharge, ensuring the materials are offloaded accurately and efficiently.
Take-Up Pulley
The take-up pulley is essential for maintaining appropriate tension in the conveyor belt. This pulley is typically mounted on a movable frame, which can be adjusted to compensate for belt stretch and elongation. By maintaining the correct belt tension, the take-up pulley ensures that the belt operates smoothly and reduces the risk of slippage and misalignment.
Bend Pulley
Bend pulleys are used to change the direction of the belt in the conveyor system. They are strategically placed to redirect the belt’s path, often found in conveyor systems where the belt needs to navigate around obstacles or changes in direction. The bend pulley helps in managing the belt’s alignment and ensures that it follows the desired path without deviating.
Defining the Snub Pulley
What is a Snub Pulley?
The function of snub pulley in belt conveyor systems is pivotal for enhancing the belt’s traction and optimizing its wrap angle around the drive pulley. A snub pulley is typically located close to the drive pulley and is designed to increase the contact area between the belt and the drive pulley. This increased contact area helps in improving the friction and grip, which in turn enhances the drive efficiency and reduces the likelihood of belt slippage.
Placement of the Snub Pulley
The placement of the snub pulley is strategic within the conveyor system. It is positioned on the return side of the conveyor belt, near the drive pulley. By increasing the wrap angle of the belt around the drive pulley, the snub pulley allows for better distribution of the load and tension across the belt. This not only improves the drive efficiency but also extends the lifespan of the belt by reducing wear and tear.
Function and Benefits
The primary function of snub pulley in belt conveyor systems is to increase the wrap angle, which enhances the belt’s grip on the drive pulley. This increased grip is crucial for preventing slippage, especially in high-tension and heavy-load applications. Additionally, the snub pulley helps in maintaining proper belt tension, which is essential for the smooth operation of the conveyor system.
By managing the tension and increasing the wrap angle, the snub pulley also contributes to reducing the stress on other components of the conveyor system. This includes the drive elements and the belt itself, leading to improved durability and reduced maintenance requirements. The function of snub pulley in belt conveyor systems is, therefore, integral to ensuring optimal performance, efficiency, and longevity of the entire conveyor setup.
Understanding the various types of pulleys in belt conveyors and the specific function of snub pulley in belt conveyor systems provides a comprehensive insight into how these components work together to achieve seamless and efficient material handling operations. The snub pulley, with its strategic placement and crucial role in enhancing belt traction and tension management, stands out as a key component that significantly impacts the overall effectiveness of the conveyor system.
Role of the Snub Pulley: Function of Snub Pulley in Belt Conveyor
Increasing the Wrap Angle
One of the primary functions of the snub pulley in belt conveyor systems is to increase the wrap angle around the drive pulley. The wrap angle is the arc of contact between the conveyor belt and the drive pulley. By strategically positioning the snub pulley near the drive pulley, the belt’s contact area with the drive pulley is increased. This enhanced contact area improves the frictional grip between the belt and the drive pulley, which is crucial for effective power transmission.
In practical terms, when the wrap angle is increased, the drive pulley can transfer more force to the conveyor belt without slipping. This is especially important in high-tension applications or when the conveyor system is handling heavy loads. The increased wrap angle provided by the snub pulley ensures that the belt maintains a secure grip on the drive pulley, enhancing the overall efficiency of the conveyor system.
Tension Management
Another critical function of snub pulley in belt conveyor systems is its role in tension management. Maintaining the appropriate tension in the conveyor belt is essential for smooth operation and to prevent issues such as belt slippage or misalignment. The snub pulley aids in achieving and maintaining the correct belt tension.
When the snub pulley increases the wrap angle, it helps distribute the tension more evenly across the belt. This even distribution reduces the likelihood of tension spikes and ensures that the belt runs smoothly over the pulleys. Proper tension management facilitated by the snub pulley also minimizes the risk of the belt stretching or elongating over time, which can lead to maintenance issues and downtime.
Furthermore, the snub pulley’s contribution to tension management helps in reducing wear and tear on the belt and other components. By ensuring that the belt maintains optimal tension, the snub pulley extends the lifespan of the conveyor belt and reduces the need for frequent adjustments or replacements.
Reducing Belt Stress
The snub pulley plays a significant role in reducing the stress on the conveyor belt and other critical components of the conveyor system. By increasing the wrap angle and enhancing tension management, the snub pulley helps in distributing the load more evenly across the belt. This even distribution of load reduces the stress on the belt, preventing premature wear and extending its operational life.
In addition to reducing belt stress, the snub pulley also eases the load on the drive pulley and motor. With an increased wrap angle, the drive pulley does not need to exert as much force to achieve the same level of traction. This reduction in required force translates to less strain on the drive pulley and motor, which can lead to lower energy consumption and reduced operational costs.
Moreover, by easing the load on the drive elements, the snub pulley helps in maintaining the overall health of the conveyor system. Reduced stress on the drive pulley and motor means fewer breakdowns and lower maintenance requirements, contributing to a more reliable and efficient conveyor operation.
The function of snub pulley in belt conveyor systems encompasses several critical roles that enhance the performance and reliability of the conveyor. By increasing the wrap angle, the snub pulley improves the frictional grip between the belt and the drive pulley, ensuring efficient power transmission. It also plays a vital role in tension management, maintaining the appropriate tension in the belt to prevent slippage and misalignment. Additionally, the snub pulley reduces the stress on the belt and other components, extending their lifespan and reducing maintenance requirements.
Understanding the function of snub pulley in belt conveyor systems highlights its importance in achieving optimal conveyor performance. The snub pulley’s ability to enhance wrap angle, manage tension, and reduce stress makes it an indispensable component in conveyor design and operation. Whether handling light materials or heavy loads, the snub pulley’s contribution to improving efficiency and reliability cannot be overstated, making it a critical element in modern conveyor systems.
Comparing Snub Pulleys with Other Pulleys: Function of Snub Pulley in Belt Conveyor
Snub vs. Take-Up Pulley
Differences and Functions
The function of snub pulley in belt conveyor systems and the take-up pulley serve distinct yet complementary roles. While both pulleys contribute to the overall efficiency of the conveyor system, their functions and placements differ significantly.
Snub Pulley vs. Bend Pulley
Roles and Effects
The function of snub pulley in belt conveyor systems and bend pulleys also have distinct roles, each contributing to the overall functionality and efficiency of the conveyor system.
Head and Tail Pulley Interaction
Ensuring Smooth Operation
The interaction between snub pulleys and the head and tail pulleys is crucial for the smooth operation of a conveyor system. Understanding the function of snub pulley in belt conveyor systems in relation to head and tail pulleys helps in appreciating how these components work together.
- Head Pulley:
- Function: Drives the belt at the discharge end, ensuring the materials are offloaded effectively.
- Interaction with Snub Pulley: The snub pulley, by increasing the wrap angle, ensures that the belt has maximum grip on the head pulley. This enhanced grip reduces slippage and ensures efficient power transfer from the motor to the belt, facilitating smooth discharge of materials.
- Tail Pulley:
- Function: Guides the belt at the return end and helps in maintaining tension as the belt returns to the loading point.
- Interaction with Snub Pulley: While the tail pulley ensures proper belt alignment and tension at the return end, the snub pulley complements this by maintaining tension and grip on the drive side. This coordinated effort ensures that the belt remains taut and aligned throughout its cycle, reducing the risk of operational issues such as misalignment or slack.
The function of snub pulley in belt conveyor systems is multifaceted, involving increased wrap angles, improved traction, and enhanced tension management. When comparing snub pulleys with other types such as take-up and bend pulleys, it is clear that each pulley has a unique role but works in conjunction with others to ensure the conveyor system operates efficiently. The interaction between snub pulleys and head and tail pulleys further underscores the importance of understanding each component’s role in achieving seamless and reliable conveyor operations.
Design and Technical Aspects: Function of Snub Pulley in Belt Conveyor
Materials and Durability
The function of snub pulley in belt conveyor systems demands that they are constructed from materials that offer high durability and strength. These materials must withstand the constant friction and tension they encounter. Here are five examples of commonly used materials and their benefits:
Steel:
- Durability: Steel is highly durable and can withstand heavy loads and high tension.
- Wear Resistance: It resists wear and tear, making it ideal for continuous operation.
- Cost-Effective: Despite being highly durable, steel is relatively cost-effective.
- Corrosion Resistance: When treated or coated properly, steel can resist corrosion, enhancing its lifespan.
- Flexibility in Design: Steel can be fabricated into various shapes and sizes, accommodating different design requirements.
Stainless Steel:
- Corrosion Resistance: Stainless steel offers superior resistance to corrosion, making it suitable for harsh environments.
- High Strength: It provides high tensile strength, ensuring the pulley can handle significant stress.
- Longevity: Stainless steel pulleys have a long operational life due to their durability.
- Low Maintenance: They require minimal maintenance, reducing downtime.
- Aesthetic Appeal: Stainless steel also has a clean and polished appearance, which can be beneficial in certain applications.
Aluminum:
- Lightweight: Aluminum is lighter than steel, which can reduce the overall weight of the conveyor system.
- Corrosion Resistance: It is naturally resistant to corrosion, making it suitable for various environments.
- Easy to Fabricate: Aluminum can be easily molded and shaped, allowing for custom designs.
- High Conductivity: It dissipates heat quickly, reducing the risk of overheating.
- Recyclable: Aluminum is recyclable, making it an environmentally friendly option.
Polyurethane:
- Impact Resistance: Polyurethane offers excellent impact resistance, absorbing shocks and vibrations.
- Flexibility: It is flexible and can withstand dynamic loads without cracking.
- Noise Reduction: Polyurethane can help reduce noise generated by the conveyor system.
- Lightweight: It is lighter than metals, which can be beneficial for certain applications.
- Chemical Resistance: Polyurethane is resistant to various chemicals, making it suitable for specific industrial environments.
Cast Iron:
- High Strength: Cast iron provides high compressive strength, suitable for heavy-duty applications.
- Wear Resistance: It resists wear and tear, prolonging the lifespan of the pulley.
- Cost-Effective: Cast iron is a cost-effective material for manufacturing robust pulleys.
- Thermal Stability: It maintains stability under varying temperature conditions.
- Vibration Damping: Cast iron has good vibration damping properties, reducing operational noise and wear on the belt.
Factors Affecting Design Choices
When designing a snub pulley, several factors need to be considered to ensure optimal performance. The function of snub pulley in belt conveyor systems is influenced by various variables, including:
- Load: The amount of weight the pulley needs to support influences the choice of materials and construction. Heavy loads require stronger materials like steel or cast iron.
- Speed: The operational speed of the conveyor belt affects the design. Higher speeds may require materials that can withstand increased friction and heat.
- Environment: The working environment, such as exposure to chemicals, moisture, or extreme temperatures, will dictate material selection. Stainless steel or polyurethane may be chosen for their resistance to specific environmental factors.
- Belt Type: The type of conveyor belt used (e.g., fabric or steel-cord reinforced) can influence the design of the snub pulley, including its surface texture and diameter.
- Maintenance: The ease of maintenance and availability of replacement parts can also impact design choices. Materials that are easier to maintain and replace may be preferred.
The Engineering Behind Wrap Angles
The function of snub pulley in belt conveyor systems is critically dependent on achieving the optimal wrap angle. The wrap angle determines the extent of contact between the conveyor belt and the drive pulley, affecting friction and traction. Here are five technical considerations behind optimal pulley wrap angles:
Friction Maximization:Increasing the wrap angle maximizes the frictional force between the belt and the drive pulley, preventing slippage.In high-tension applications, a larger wrap angle ensures that the belt maintains a secure grip on the drive pulley, enhancing power transmission efficiency.
Load Distribution:A greater wrap angle helps distribute the load more evenly across the belt, reducing localized stress.In heavy-duty conveyor systems, a well-distributed load minimizes wear and tear on specific belt sections, prolonging the belt’s life.
Tension Management:The wrap angle directly influences the tension applied to the belt, ensuring it remains taut and aligned.In long conveyor systems, maintaining appropriate tension through a larger wrap angle prevents belt sagging and misalignment, ensuring smooth operation.
Energy Efficiency:Optimizing the wrap angle can reduce the energy required to drive the belt, leading to lower operational costs.In systems designed for energy efficiency, the wrap angle is adjusted to minimize resistance and energy consumption, contributing to cost savings.
Operational Stability: A stable wrap angle ensures consistent belt movement, reducing the risk of operational interruptions.In precision applications, maintaining a stable wrap angle is crucial for achieving consistent product handling and reducing downtime due to belt slippage or misalignment.
Understanding the function of snub pulley in belt conveyor systems involves appreciating these design and technical aspects. By selecting the right materials, considering key design variables, and optimizing wrap angles, snub pulleys can significantly enhance the performance, efficiency, and reliability of conveyor systems.
Maintenance and Troubleshooting: Function of Snub Pulley in Belt Conveyor
Regular Maintenance
Routine maintenance is essential to ensure the optimal function of snub pulley in belt conveyor systems. Regular inspections and upkeep help in identifying potential issues before they escalate, ensuring continuous and efficient operation.
Visual Inspections:Regular visual inspections help in identifying signs of wear and tear, misalignment, and other visible issues.Schedule weekly visual checks to spot any abnormal wear, cracks, or misalignment in the snub pulley and associated components.
Lubrication:Proper lubrication reduces friction and wear on the bearings and conveyor belt shaft of the snub pulley.Apply appropriate lubricants to the snub pulley bearings every month or as recommended by the manufacturer to ensure smooth operation.
Alignment Checks:Misalignment can cause uneven wear and increase the risk of belt slippage and damage.Use alignment tools to check and correct the alignment of the snub pulley with the drive pulley during quarterly maintenance.
Tension Adjustment:Maintaining the correct belt tension is crucial for preventing slippage and ensuring efficient power transmission.Measure and adjust the belt tension during bi-monthly maintenance checks to ensure it falls within the recommended range.
Component Replacement:Worn-out components can compromise the function of snub pulley in belt conveyor systems.Replace worn or damaged bearings, belts, and other components annually or as needed based on wear patterns observed during inspections.
Common Issues
Identifying and addressing common issues related to the snub pulley can prevent downtime and extend the lifespan of the conveyor system. Here are some typical problems and their solutions:
Belt Slippage:
- Problem: Insufficient friction between the belt and the drive pulley can cause the belt to slip, reducing efficiency.
- Solution: Increase the wrap angle by adjusting the snub pulley position. Ensure the belt is properly tensioned and replace it if it shows signs of excessive wear.
Misalignment:
- Problem: Misalignment of the snub pulley can lead to uneven wear on the belt and increased risk of belt tracking issues.
- Solution: Use alignment tools to ensure the snub pulley is correctly aligned with the drive and other pulleys. Regularly check and adjust alignment during maintenance.
Excessive Wear:
- Problem: Continuous operation can lead to wear on the snub pulley surface and bearings, affecting performance.
- Solution: Inspect the snub pulley surface and bearings for signs of wear during maintenance checks. Replace worn components promptly to prevent further damage.
Noise and Vibration:
- Problem: Unusual noise and vibration can indicate issues such as bearing failure, misalignment, or inadequate lubrication.
- Solution: Identify the source of the noise or vibration. Check and lubricate bearings, realign the snub pulley, and replace any damaged components.
Material Buildup:
- Problem: Accumulation of material on the snub pulley can cause imbalance and affect performance.
- Solution: Regularly clean the snub pulley and surrounding areas to remove any buildup of material. Implement preventive measures such as installing scrapers or cleaners.
Proper maintenance and troubleshooting are critical for the effective function of snub pulley in belt conveyor systems. Regular inspections, lubrication, alignment checks, tension adjustments, and timely component replacements help in maintaining optimal performance and preventing operational issues. Addressing common problems like belt slippage, misalignment, excessive wear, noise and vibration, and material buildup ensures the conveyor system operates smoothly and efficiently. By adhering to these maintenance practices and promptly addressing issues, the lifespan and reliability of the conveyor system are significantly enhanced.
FAQs About Function of Snub Pulley in Belt Conveyor
The main function of a snub pulley in a conveyor system is to increase the wrap angle of the conveyor belt around the drive pulley. By enhancing this wrap angle, the snub pulley ensures greater frictional contact between the belt and the drive pulley, thereby improving the traction and efficiency of the drive mechanism. This is particularly important in preventing belt slippage, which can lead to inefficiencies and disruptions in material handling. Additionally, the snub pulley helps in maintaining the proper alignment of the belt, ensuring smooth and continuous operation. By reducing the slippage and improving belt control, snub pulleys also help in extending the lifespan of both the conveyor belt and the drive pulley, reducing maintenance costs and downtime.
A snub roller, often referred to as a snub pulley when it performs the same function, is a component in a conveyor system used to increase the wrap angle of the conveyor belt around the drive pulley. This increased wrap angle enhances the friction between the belt and the drive pulley, preventing slippage and ensuring efficient power transmission. The snub roller is strategically positioned close to the drive pulley, redirecting the belt to achieve the desired wrap. In addition to improving traction, snub rollers also contribute to better belt alignment and tension, which are crucial for the smooth operation of the conveyor system. They play a vital role in maintaining the efficiency and reliability of the conveyor by ensuring consistent belt movement and reducing wear and tear on the belt and drive components.
The function of a pulley in a conveyor system is multifaceted and critical for the efficient operation of the conveyor. Pulleys are used to support, drive, and redirect the conveyor belt as it moves through the system. Here are some key functions:
Driving the Belt: The drive pulley, connected to a motor, provides the necessary rotational force to move the conveyor belt, facilitating the transport of materials along the conveyor path.
Maintaining Tension: Pulleys help maintain the appropriate tension in the conveyor belt, preventing slippage and ensuring smooth operation. This includes both drive pulleys and tail pulleys, which are positioned at opposite ends of the conveyor.
Redirecting the Belt: Bend and snub pulleys are used to change the direction of the conveyor belt or to increase the wrap angle around the drive pulley, enhancing traction and belt control.
Supporting the Belt: Idler pulleys, or rollers, provide support to the belt and the material being conveyed, ensuring that the belt remains aligned and stable throughout its travel.
Each type of pulley plays a crucial role in maintaining the efficiency, reliability, and longevity of the conveyor system.
While both snub pulleys and bend pulleys are used in conveyor systems to guide and support the conveyor belt, their functions and positions within the system differ.
Function:
Snub Pulley: The primary function of a snub pulley is to increase the wrap angle of the conveyor belt around the drive pulley. By doing so, it enhances the frictional grip between the belt and the drive pulley, preventing slippage and improving traction. This is essential for efficient power transmission and belt control.
Bend Pulley: A bend pulley is used to change the direction of the conveyor belt, typically by redirecting it to different sections of the conveyor path. Bend pulleys help in navigating the belt through complex conveyor layouts and ensuring smooth transitions around corners or over obstacles.
Position:
Snub Pulley: Snub pulleys are usually positioned close to the drive pulley. Their placement is strategic to maximize the wrap angle and enhance the belt’s contact with the drive pulley.
Bend Pulley: Bend pulleys can be positioned at various points along the conveyor system where directional changes are needed. They are not necessarily near the drive pulley and are used more for routing the belt through the desired path.
Design:
Snub Pulley: Typically smaller in diameter compared to drive pulleys, snub pulleys are designed to fit close to the drive pulley and provide additional wrap.
Bend Pulley: Bend pulleys can vary in size depending on the specific requirements of the conveyor layout and are designed to smoothly guide the belt through direction changes without causing excessive wear.
Understanding the distinct roles and characteristics of snub pulleys and bend pulleys is essential for designing and maintaining an efficient conveyor system.
Last Updated on August 1, 2024 by Jordan Smith
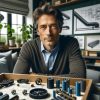
Jordan Smith, a seasoned professional with over 20 years of experience in the conveyor system industry. Jordan’s expertise lies in providing comprehensive solutions for conveyor rollers, belts, and accessories, catering to a wide range of industrial needs. From initial design and configuration to installation and meticulous troubleshooting, Jordan is adept at handling all aspects of conveyor system management. Whether you’re looking to upgrade your production line with efficient conveyor belts, require custom conveyor rollers for specific operations, or need expert advice on selecting the right conveyor accessories for your facility, Jordan is your reliable consultant. For any inquiries or assistance with conveyor system optimization, Jordan is available to share his wealth of knowledge and experience. Feel free to reach out at any time for professional guidance on all matters related to conveyor rollers, belts, and accessories.