Galvanized Rollers: Backbone of Heavy-Duty Conveyor Systems
Rollers are an integral component of countless industrial applications, offering a blend of mobility and support to facilitate the movement and handling of materials. In particular, galvanized rollers have emerged as a powerful option in these settings, combining robust performance with long-lasting protection. This deep dive into the world of galvanized rollers will unfold their uses, benefits, and types, along with insightful guidance on selection and purchase strategies.
Advantages of Galvanized Rollers Across Industries
In the realm of material handling and conveyor systems, rollers stand as fundamental components that facilitate the smooth and efficient movement of goods. Their application spans across a multitude of industries, ranging from manufacturing and warehousing to retail and distribution. Among the varied types of rollers utilized in these sectors, galvanized rollers have carved a niche for themselves, known for their enduring qualities and superior performance.
The Significance and Uses of Galvanized Rollers
Galvanized rollers are integral to the seamless operation of conveyor systems, supporting the transportation of materials with ease and efficiency. These rollers find extensive use in environments subjected to heavy loads and constant use, where their durability and strength are crucial for maintaining a steady flow of operations. Industries such as mining, automotive, and construction particularly benefit from the robust nature of these rollers, where they are often exposed to harsh conditions.
The utilization of galvanized rollers isn’t confined to heavy-duty applications only. They also play a pivotal role in lighter industries such as packaging, agricultural, and food processing plants. Here, the hygienic and corrosion-resistant properties of galvanized rollers make them an ideal choice, ensuring that products remain uncontaminated and that the rollers themselves maintain a long service life despite exposure to moisture and chemicals.
Unique Benefits of Incorporating Galvanized Rollers
Unmatched Durability
One of the most significant advantages of galvanized rollers lies in their exceptional durability. The galvanization process provides a protective zinc coating to the steel, making it resistant to rust and corrosion. This extends the life of the rollers, ensuring they can withstand demanding environments without deterioration.
Cost-Effectiveness
Despite their superior qualities, galvanized rollers are a cost-effective solution for conveyor systems. The longevity afforded by the galvanization process means fewer replacements over time, translating to lower maintenance and operational costs. This makes galvanized rollers an economical choice for both small and large-scale operations.
Enhanced Performance
Galvanized rollers offer enhanced performance thanks to their smooth surface, ensuring a consistent and reliable movement of materials. This reduces the risk of jams or slowdowns in the conveyor system, enabling a more efficient workflow. Their reliability is a key factor in maximizing productivity in any industrial setting.
Environmental Resistance
The protective coating of galvanized rollers not only guards against corrosion but also provides resilience against various environmental factors, including temperature fluctuations and exposure to chemicals. This makes them suitable for use in both indoor and outdoor settings, as well as in industries where they may come into contact with harsh substances.
Galvanized rollers present a myriad of benefits that make them a preferred choice in numerous industrial applications. Their versatility, combined with unparalleled durability, cost-effectiveness, and consistent performance, underscores their importance in enhancing operational efficiency. As industries continue to evolve, so does the reliance on galvanized rollers, further solidifying their role in maintaining the momentum of global production and distribution networks.
The Robust Characteristics of Galvanized Rollers in Industrial Applications
Within the fabric of industrial mechanics, galvanized rollers are more than just components; they are the robust veins that drive the conveyor system’s functionality. The unique advantage of galvanized rollers is not an industry secret; rather, it is a testament to the power of innovative engineering designed to meet the most challenging demands of myriad industries.
The Galvanization Process and Advantages for Rollers
Galvanization is a metallurgical process that involves coating steel or iron rollers with a protective layer of zinc. This process typically occurs through hot-dip galvanization, where the rollers are submerged in a bath of molten zinc. The high temperature causes a metallurgical reaction between the steel substrate and the zinc, leading to the formation of a series of zinc-iron alloy layers topped with a pure zinc layer.
This galvanized coating works as a sacrificial anode, which means it will corrode and deplete over time in lieu of the underlying metal. Galvanized rollers accrue numerous benefits from this treatment:
Corrosion Resistance
The zinc coating provides a formidable barrier against oxidation, the primary process leading to corrosion. This feature is especially valuable in environments where rollers are exposed to moisture, chemicals, or high humidity, all of which can accelerate rusting.
Extended Longevity
Galvanized rollers enjoy a significantly extended lifespan compared to their non-galvanized counterparts. The durability conferred by the zinc coating helps to maintain structural integrity and functional smoothness over time, translating to less frequent replacements and lower long-term costs.
Maintenance Savings
The resilience of galvanized rollers yields lower maintenance requirements. Their capability to resist wear and tear means that there is less need for lubrication, cleaning, and other upkeep activities, thus reducing the maintenance hours and costs associated with the operation of the conveyor systems.
Heavy Duty Galvanized Rollers: Construction and Applications
When addressing the needs of industries that push the boundaries of material handling, heavy-duty galvanized rollers come into play. These rollers boast a construction that is reinforced to endure not just the stress of weight but also the stresses of movement, impact, and environmental conditions.
The augmented design of heavy-duty galvanized rollers generally includes thicker walls, sturdier shafts, and enhanced bearing capabilities. This formidable build ensures that they can tackle the most arduous tasks without failure, whether it’s moving tons of raw materials in a mining operation or continuously transporting heavy automotive components in a manufacturing plant.
Applications in these pressing environments present relentless challenges that could swiftly overwhelm substandard rollers. But heavy-duty galvanized rollers are crafted for such trials—they stand as unyielding supporters in the relentless rhythm of conveyor systems subjected to harsh conditions. They shine in scenarios where toughness is not a luxury but a quintessential requisite for operational continuity and efficiency.
Galvanized rollers, especially of the heavy-duty variety, offer an essential and robust solution within the engineering sphere. Their special attributes, including corrosion resistance, enhanced longevity, and reduced maintenance demands, make them a vital element in an array of strenuous industrial environments, affirming their status as cornerstones of modern material handling and industrial processes.
Comprehensive Overview of Various Galvanized Rollers Types
Galvanized rollers are pivotal components in the effective management and operation of conveyor systems across numerous industrial landscapes. Their galvanization not only imparts superior durability but also equips them with the resilience needed to handle the rigorous demands of various material handling requirements. This detailed exploration dissects the diversity within the realm of galvanized rollers, shedding light on their specific functions, design distinctions, and tailored applications.
Conveyor Rollers: The Backbone of Material Handling Systems
Conveyor rollers are the dynamos behind the seamless movement of goods across the expanse of manufacturing floors, warehouses, and distribution centers. Acting as the support system for conveyor belts, they facilitate the easy transport of materials, thereby optimizing productivity and reducing manual labor costs. Given their critical role, these rollers come in various sizes and capacities to suit specific operational needs, including heavy-duty, 4-inch diameter, and 1-inch diameter options.
- Heavy-duty rollers are engineered for environments where loads are exceedingly heavy or where the conveyor system is subject to constant use. These are typically found in industries like mining, construction, and heavy manufacturing.
- 4-inch diameter rollers strike a balance between capacity and versatility, widely used in automated distribution centers and parcel handling facilities.
- 1-inch diameter rollers are utilized for lightweight materials and precise movements, often employed in electronic assembly plants or pharmaceutical labs.
Heavy Duty Conveyor Rollers: For the Toughest Tasks
Delving deeper into heavy-duty galvanized rollers reveals their robust construction and superior capabilities. These rollers are designed to withstand not just the weight of heavy loads but also the additional forces exerted by rapid or continuous movement. Featuring thick walls, reinforced frames, and high-grade bearings, they ensure the resilience and reliability necessary for industries with no margin for error, such as bulk material handling, steel manufacturing, and automotive assembly lines.
The galvanization of these rollers provides an added layer of protection against corrosion, enabling them to maintain structural integrity in harsh environments. This makes them indispensable in sectors that deal with abrasive materials, moisture, and chemical exposure.
Conveyor Belt Rollers for Sale: A Purchasing Guide
When seeking conveyor belt rollers for sale, selecting the appropriate type for your industry’s specific needs is crucial. A comprehensive understanding of load requirements, environmental conditions, and operational frequencies will guide the decision-making process. Prospective buyers should look for suppliers who offer a range of galvanized rollers, enabling them to match roller capabilities directly to their conveyor system’s demands. Additionally, factors such as warranty, technical support, and compatibility with existing systems should influence the final choice.
Specialty Rollers: Tailored Solutions for Unique Needs
Beyond the standard offerings, specialty galvanized rollers provide bespoke solutions for unique industrial applications. One notable variant is the conveyor roller with bracket. This design integrates a mounting bracket, enabling direct attachment to machinery or equipment frameworks. Such configurations are particularly beneficial for adjustable conveyor sections or mobile conveyor applications.
Other unique galvanized rollers are expressly designed for specific purposes, like heat-resistant models for high-temperature environments or non-marking rollers for sensitive materials. These specialty rollers exemplify the industry’s adaptive response to niche challenges, pushing the boundaries of material handling capabilities.
In sum, the universe of galvanized rollers is marked by its diversity and adaptability. Whether standard conveyor rollers, heavy-duty powerhouses, or niche-specific variants, these components are fundamental to optimizing industrial operations, ensuring materials are moved efficiently, safely, and reliably across the production landscape.
Finding and Choosing Galvanized Rollers
Selecting the appropriate galvanized rollers for your operation can be a decisive factor in the efficiency and longevity of your mechanical systems. Whether you require these rollers for conveyor systems, industrial machinery, or material handling setups, understanding where to find premium products and how to evaluate your purchase options is essential.
Galvanized Rollers for Sale
When in the market for galvanized rollers, knowing where to look is as important as what to look for. Let’s delve into some beneficial tips and critical considerations.
Where to Find Quality Galvanized Rollers
To secure high-quality galvanized rollers for sale:
- Industrial Supply Websites: Begin your search with websites specialized in industrial equipment. These platforms often offer a range of galvanized rollers suitable for various applications.
- Manufacturer Direct Purchases: Consider buying directly from manufacturers. This can often provide access to the latest products and guarantee original equipment that comes with warranties.
- Trade Shows: Industry trade shows are prime spots to discover new and efficient galvanized rollers, as well as to network with suppliers and manufacturers.
- Wholesale Distributors: Reach out to wholesale distributors who can supply bulk orders of galvanized rollers at competitive prices.
Choosing the Right Supplier or Manufacturer
Identifying a reliable supplier:
- Quality and Compliance Standards: Ensure the supplier’s products meet industry quality standards and compliance regulations.
- Range of Options: Look for suppliers offering a diverse range of galvanized rollers to select the ones best suited to your needs.
- Technical Support: A supplier that provides strong technical support and guidance can be invaluable in selecting and maintaining galvanized rollers.
- Delivery and Logistics: Understand their delivery capabilities to ensure they can meet your schedule and location requirements.
- Cost-effectiveness: While affordability is key, ensure it doesn’t come at the cost of quality. Strike a balance between a fair price and high-grade galvanized rollers.
Galvanized Rollers Near Me
Locating nearby suppliers of galvanized rollers can bring a host of advantages.
Advantages of Local Sourcing
The plus points of local procurement include:
- Convenience: Sourcing galvanized rollers from a local supplier adds convenience to your buying process through easier logistics and communication.
- After-Sale Support: Local suppliers are often more accessible for any after-sales support or quick replacements you might need.
- Relationship Building: Establishing a relationship with a nearby supplier can lead to better deals, personalized service, and insights into local market trends.
- Environmental Impact: By cutting down on long-distance shipping, you’re also reducing your carbon footprint, making your purchase more eco-friendly.
Used Conveyor Rollers for Sale
Considering used conveyor rollers can be a cost-effective alternative to new products.
Evaluating the Condition of Used Rollers
Key steps in assessing used conveyor rollers include:
- Wear and Tear: Start by examining the surface and structure for signs of corrosion, excessive wear, or structural compromises.
- Performance Inspection: Whenever possible, test the rollers to check their performance. They should operate smoothly and without disruptions.
- Compatibility: Make sure that the used rollers are compatible with your existing system regarding size, load capacity, and material handling requirements.
- Seller Reputation: Research the seller to ensure they have a history of providing high-quality used equipment.
Acquiring the right galvanized rollers can enhance your system’s efficiency and durability, and taking the time to do careful research and evaluation can lead to significant long-term benefits.
Why Choose the Right Galvanized Rollers?
Choosing the right galvanized rollers isn’t just about fulfilling an equipment checklist; it’s about harnessing the full potential of a key component in your industrial setup. The significance of making an informed decision extends beyond immediate functionality. It’s about investing in the efficiency and durability of your operations, ensuring that each component contributes positively to your industrial applications.
The Importance of Tailored Galvanized Rollers
Selecting galvanized rollers that are perfectly suited to your specific needs is a decision that carries weight in three major aspects of industrial operations:
Optimization of Performance
The right galvanized rollers can significantly increase the efficiency of your conveyor systems or machinery. Custom selections based on size, load capacity, and the specific environment (be it high humidity, exposure to chemicals, etc.) ensure that your operations run smoothly. This means reduced friction and wear, leading to less downtime for maintenance and repairs.
Enhancement of Durability
Galvanized rollers are known for their robustness against corrosion and wear. However, choosing the right type of galvanized roller adds an extra layer of durability. This matches the roller material and galvanization process to the demands of your operational setting. It’s this specificity that can prevent premature failure, extending the lifespan of the rollers and, by extension, the systems they are part of.
Cost Efficiency Over Time
Investing in high-quality galvanized rollers that are optimal for your applications may seem like an upfront cost. Still, it’s a decision that pays dividends in the long run. By aligning with appropriate specifications, you minimize the potential for operational hindrances, maintenance costs, and the need for early replacements. This strategic choice ensures that your investment yields maximum efficiency and durability, proving cost-effective over the lifecycle of your equipment.
Invest in Quality for Enhanced Industrial Applications
Choosing the right galvanized rollers is not a decision to be taken lightly. By carefully considering your needs and investing in quality, you ensure that your operations benefit from enhanced efficiency and durability. High-quality galvanized rollers become a pivotal part of your industrial applications, contributing to a smoother, more reliable, and cost-effective operation.
FAQs about Galvanized Rollers
Steel rollers serve a critical role in various industries, predominantly in conveying systems. They are used to facilitate the smooth and efficient transport of materials across short and long distances within a facility. Their robust nature makes them ideal for handling hefty loads and operating in harsh environments where durability and strength are paramount. Industries such as mining, automotive, agriculture, and heavy manufacturing prefer steel rollers due to their resistance to impact, abrasion, and corrosion. Additionally, steel rollers are a fundamental component in pallet and drum conveyors, as well as in heavy-duty gravity and powered roller conveyor systems, where they are favored for their capacity to withstand high-speed operations and heavy-duty use, maintaining functionality over extended periods with minimal maintenance.
Conveyor rollers can be made from a variety of materials, each selected for its unique properties that cater to the needs of different conveying applications and environments. The most commonly used materials include:
Steel: Known for its strength and durability, steel is often used in heavy-duty conveyors that carry large or abrasive materials.
Stainless Steel: Offers corrosion resistance, making it suitable for food processing, pharmaceutical, and other clean or harsh environments where cleanliness and non-reactive surfaces are required.
Aluminum: A lightweight alternative to steel, aluminum rollers are used in applications where reduced weight is beneficial, like gravity or portable conveyors.
Plastic: These rollers are utilized in lightweight or low-load situations. They also offer corrosion resistance and quieter operation.
Rubber-Coated or Polyurethane-Coated: Coating materials provide additional grip and reduce noise, and are often used in applications where extra traction is needed.
The choice of material is crucial and based on factors like weight capacity, environmental conditions, cost, and the type of material being conveyed.
In a conveyor belt system, there are primarily two categories of rollers, each with different types and functions:
Carrying Rollers: These are the most common type and support the conveyor belt and the material being moved. Varieties of carrying rollers include flat belt rollers, troughing rollers, and impact rollers.
Return Rollers: As the name suggests, return rollers support the return section of the conveyor belt. Types include flat return rollers, return disc rollers (used where sticky materials may adhere to the belt), and rubber disc return rollers (for additional grip and cleaning action).
In addition to these primary types, there are other specialized rollers, such as:
Self-aligning Rollers: To keep the conveyor belt in alignment.
Guide Rollers: To prevent the belt from sideways movement.
Spiral Rollers: To clean the belt and give it a slight turn.
Each type of roller serves a specific purpose and ensures the efficient and smooth operation of the conveyor belt.
An idler roller, also known simply as an idler, is a component found in a conveyor system that is used to support the conveyor belt and the materials being transported on it. The primary function of the idler is to provide a smooth surface for the conveyor belt to travel over, maintaining its shape and direction as it moves, carrying the load. Idlers are strategically placed along the conveyor path to reduce friction and wear on the belt. Additionally, they help to distribute the load evenly, which minimizes belt sag between the main support rollers and enhances the belt life. There are different types of idler rollers designed to perform specific tasks, such as impact idlers, which absorb shock at loading points and return idlers, which support the belt on its return journey. In essence, idlers play a vital role in minimizing downtime and maintaining the efficiency of the conveyor system.
Last Updated on March 12, 2024 by Jordan Smith
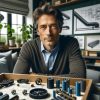
Jordan Smith, a seasoned professional with over 20 years of experience in the conveyor system industry. Jordan’s expertise lies in providing comprehensive solutions for conveyor rollers, belts, and accessories, catering to a wide range of industrial needs. From initial design and configuration to installation and meticulous troubleshooting, Jordan is adept at handling all aspects of conveyor system management. Whether you’re looking to upgrade your production line with efficient conveyor belts, require custom conveyor rollers for specific operations, or need expert advice on selecting the right conveyor accessories for your facility, Jordan is your reliable consultant. For any inquiries or assistance with conveyor system optimization, Jordan is available to share his wealth of knowledge and experience. Feel free to reach out at any time for professional guidance on all matters related to conveyor rollers, belts, and accessories.