Cost-Effective Solutions: Galvanized Steel Roller Purchasing Tips
Conveyor systems play a pivotal role across a multitude of industries, serving as the backbone for efficient material handling and logistics. From agriculture and mining to construction and manufacturing, these systems facilitate the seamless movement of goods, raw materials, and products through production lines and distribution centers. At the heart of these indispensable systems are the rollers that bear the weight and facilitate the movement of items. Among these, galvanized steel roller stands out for their durability, reliability, and ability to withstand harsh environmental conditions. As a key component, they ensure that conveyor systems operate smoothly, minimizing downtime and maximizing productivity. Their galvanized coating not only protects them from corrosion but also extends their lifespan, making them an essential choice for businesses looking to optimize their operations.
What Is Galvanized Steel Roller
A galvanized steel roller is a fundamental component in the realm of conveyor systems, designed to support and move materials efficiently across various industrial settings. These rollers are distinguished by their construction material—steel—that has been treated through the process of galvanization. This treatment enhances their utility and longevity, making them indispensable in sectors that demand durability and reliability. Below, we delve into the specifics of galvanized steel rollers, outlining their defining characteristics and the advantages brought forth by the galvanization process.
To provide a comprehensive understanding of galvanized steel rollers and the significant impact of the galvanization process on their performance, it’s essential to delve into both the fundamental aspects of these components and the transformative benefits of their treatment. This exploration will be divided into two main parts: the definition and description of galvanized steel rollers, followed by an in-depth look at the galvanization process and its myriad benefits for steel rollers. This structured approach aims to illuminate the intrinsic qualities of galvanized steel rollers that make them indispensable in industrial applications and to highlight how galvanization enhances these qualities, ensuring superior performance and longevity.
Description of Galvanized Steel Rollers
Before we examine the specifics, it’s crucial to understand what galvanized steel rollers are and the key characteristics that define their role in conveyor systems. Galvanized steel rollers are not merely components; they are the culmination of precise engineering and material science, designed to meet the rigorous demands of industrial operations. Here, we will outline the essential attributes that make galvanized steel rollers a cornerstone of efficient material handling across various sectors.
- Robust Construction: Galvanized steel rollers are built to endure, capable of handling heavy loads without compromise to their structural integrity.
- Corrosion-Resistant: The galvanization process coats these rollers in a layer of zinc, offering a shield against rust and corrosion.
- Versatile Application: Whether in mining, agriculture, or manufacturing, the galvanized steel roller is versatile enough to fit various industrial applications.
- Enhanced Durability: The protective zinc coating ensures these rollers can withstand harsh environmental conditions, from extreme moisture to chemical exposures.
- Low Maintenance: Thanks to their corrosion resistance, these rollers require less maintenance, reducing downtime and operational costs.
- Eco-Friendly: Steel and zinc are both recyclable materials, making galvanized steel rollers a more sustainable option for environmentally conscious operations.
- Aesthetic Finish: Beyond functionality, the zinc coating provides a sleek, clean appearance that maintains its look over time.
- Cost-Effective: Given their longevity and reduced need for replacement, galvanized steel rollers represent a cost-effective solution for long-term use.
To provide a comprehensive understanding of galvanized steel rollers and the significant impact of the galvanization process on their performance, it’s essential to delve into both the fundamental aspects of these components and the transformative benefits of their treatment. This exploration will be divided into two main parts: the definition and description of galvanized steel rollers, followed by an in-depth look at the galvanization process and its myriad benefits for steel rollers. This structured approach aims to illuminate the intrinsic qualities of galvanized steel rollers that make them indispensable in industrial applications and to highlight how galvanization enhances these qualities, ensuring superior performance and longevity.
The Galvanization Process and Its Benefits for Steel Rollers
Following the foundational understanding of galvanized steel rollers, we will explore the galvanization process—a critical treatment that significantly augments the rollers’ functionality and durability. This section will detail how galvanization, through its chemical and physical properties, provides a robust defense against environmental challenges, thereby extending the operational life of steel rollers. Understanding this process and its advantages is key to appreciating the full value that galvanized steel rollers bring to conveyor systems and the broader industrial landscape.
- Corrosion Resistance: The foremost benefit of galvanization is its ability to protect the steel from rust and corrosion, significantly extending the roller’s lifespan.
- Complete Coverage: Galvanization coats the steel surface entirely, ensuring even hard-to-reach areas are protected from environmental damage.
- Bond Strength: The galvanization process creates a strong bond between the zinc and the steel, enhancing the roller’s overall durability.
- Quick Turnaround: Unlike some protective treatments, galvanization can be completed quickly, allowing for faster production times.
- Thermal Protection: The zinc coating can withstand extreme temperatures, providing thermal protection in varying climates.
- Barrier Protection: Galvanization acts as a physical barrier, protecting the steel from moisture, acids, and other corrosive elements.
- Long-Term Cost Savings: By extending the operational life of rollers, galvanization reduces the need for frequent replacements, offering long-term cost savings.
- Improved Safety: With their enhanced durability and reliability, galvanized steel rollers contribute to safer operational environments by reducing the risk of breakdowns.
A galvanized steel roller is more than just a component; it’s a critical investment in the efficiency and longevity of conveyor systems. Through the process of galvanization, these rollers gain a competitive edge, offering unmatched durability and performance in the face of industrial challenges.
Advantages of Galvanized Steel Roller
The galvanized steel roller stands as a paragon of engineering innovation, designed to meet the exacting standards of modern industrial applications. Its core advantages stem from a meticulous manufacturing process, where steel undergoes galvanization to enhance its physical and chemical properties. This section delves into the multifaceted benefits of the galvanized steel roller, underscoring its pivotal role in conveyor systems across diverse sectors.
- Exceptional Durability: The foremost advantage of a galvanized steel roller is its remarkable durability. The galvanization process coats the roller with a layer of zinc, which significantly increases its resistance to wear and tear. This durability is crucial for maintaining operational efficiency and reducing the need for frequent replacements.
- Corrosion Resistance: A key feature of the galvanized steel roller is its ability to resist corrosion. The zinc coating acts as a protective barrier against moisture, chemicals, and other corrosive elements, ensuring the roller’s longevity even in the most challenging environments.
- Heavy-Duty Performance: Designed for resilience, the galvanized steel roller is ideally suited for heavy-duty applications. Its robust construction enables it to support substantial loads, making it an indispensable component in industries such as mining, construction, and manufacturing.
- Low Maintenance Requirements: The durability and corrosion resistance of the galvanized steel roller translate into lower maintenance needs. This benefit not only reduces operational costs but also minimizes downtime, allowing for uninterrupted productivity.
- Longevity: The protective properties of the zinc coating significantly extend the life span of steel rollers. This longevity is a testament to the galvanized steel roller’s ability to withstand the rigors of daily use without succumbing to the effects of aging and environmental exposure.
- Suitability for Harsh Environments: The galvanized steel roller thrives in harsh industrial environments. Whether exposed to extreme temperatures, moisture, or abrasive materials, it maintains its integrity and performance, thanks to the galvanization process.
- Economic Efficiency: By enhancing the durability and lifespan of steel rollers, galvanization offers an economically efficient solution. The initial investment in galvanized steel rollers pays dividends over time, as the need for replacements and repairs is significantly reduced.
- Environmental Sustainability: The zinc used in galvanizing steel rollers is a recyclable material, contributing to the environmental sustainability of this product. Furthermore, the extended lifespan and reduced maintenance of galvanized rollers minimize waste and resource consumption.
- Uniform Protection: The galvanization process ensures uniform coverage of the steel surface, providing consistent protection against external damages. This uniformity is crucial for maintaining the structural integrity of the roller across its entire length and diameter, ensuring that every part of the roller is equally resistant to corrosion and wear. This comprehensive protection is particularly important in applications where the roller is exposed to uneven or particulate-laden environments, which can otherwise lead to localized wear and premature failure.
- Improved Operational Efficiency: The combined benefits of durability, longevity, and low maintenance contribute to the overall operational efficiency of conveyor systems equipped with galvanized steel rollers. By ensuring smooth and reliable operation, these rollers minimize potential bottlenecks and disruptions in the production process. The result is a more streamlined operation that can maintain higher throughput rates and better meet the demands of fast-paced industrial environments. This efficiency not only enhances productivity but also contributes to the overall profitability of operations by reducing downtime and maintenance costs.
The galvanized steel roller embodies a synergy of strength, durability, and efficiency. Its resistance to corrosion, suitability for heavy-duty applications, and low maintenance requirements make it a cornerstone of modern conveyor systems. These attributes, coupled with its economic and environmental benefits, underscore the galvanized steel roller’s indispensable role in facilitating seamless industrial operations.
Applications of Galvanized Steel Roller
The galvanized steel roller, a cornerstone of industrial and agricultural machinery, is renowned for its durability, corrosion resistance, and ability to withstand harsh environments. This versatility makes it an essential component across a broad spectrum of industries, where it significantly enhances operational efficiency, safety, and reliability. From the vast fields of agriculture to the demanding environments of mining and construction, the galvanized steel roller is pivotal in streamlining processes and supporting heavy-duty operations. Below, we explore its indispensable role in six key sectors, emphasizing the breadth of its applications and the depth of its impact.
Agriculture
In the realm of agriculture, the galvanized steel roller is instrumental in automating and enhancing various processes, from harvesting to packaging. Its robustness and resistance to environmental factors make it ideal for the demanding conditions of agricultural operations.
- Conveying Grain and Produce: Facilitates the efficient transport of grains and produce from fields to storage or processing facilities, minimizing loss and damage.
- Equipment Maintenance: Ensures the longevity and reliability of farm machinery exposed to the elements, significantly reducing maintenance needs and operational downtime.
- Irrigation Systems: Plays a crucial role in mobile irrigation systems, offering unmatched durability against constant exposure to water and soil.
- Feed Distribution Systems: Automates the distribution of feed in livestock management, enhancing efficiency and ensuring uniform feed delivery.
- Sorting and Packaging: Critical in the sorting and packaging lines for fruits and vegetables, where it helps maintain the quality and freshness of produce.
- Soil Preparation Machinery: Supports soil preparation equipment, enduring the abrasive conditions of soil and debris without degradation.
Mining
The mining industry’s reliance on galvanized steel rollers is a testament to their strength and durability, essential for the transport and processing of raw materials extracted from the earth.
- Material Transport: Key to the movement of ores and minerals from extraction points to processing facilities, capable of handling the weight and abrasiveness of raw materials.
- Equipment Durability: Enhances the durability of conveyor systems in the dusty, corrosive environment of mines, extending equipment lifespan and reducing repair costs.
- Underground Conveyance: Ideal for the challenging conditions of underground mining, where moisture and corrosive agents are prevalent.
- Loading and Unloading Operations: Streamlines the loading and unloading process, improving efficiency and reducing the time materials spend in transit.
- Waste Disposal Systems: Utilized in the disposal of mining waste, ensuring environmental standards are met through efficient waste management.
- Bulk Material Handling: Facilitates the bulk transport of extracted materials, optimizing the efficiency of mining operations and throughput.
Construction
The construction industry benefits immensely from the use of galvanized steel rollers, which facilitate the movement of materials across sites, enhancing efficiency and ensuring the safety of construction processes.
- Material Handling: Essential for the efficient transport of a wide range of building materials, from heavy steel beams to delicate glass panels, ensuring they reach the point of use safely and promptly.
- Debris Removal: Plays a vital role in maintaining clean and safe construction sites by facilitating the removal of debris and waste materials.
- Temporary Conveyor Setups: Adaptable for use in temporary conveyor systems tailored to specific projects, easily withstanding the rigors and variability of construction environments.
- Supply Chain Optimization: Critical in optimizing the construction supply chain, ensuring materials are moved swiftly from delivery trucks to storage or directly to the point of use.
- Movement of Tools and Equipment: Enhances the accessibility of tools and equipment by facilitating their movement across large or complex construction sites.
- Ergonomics and Safety: By automating the movement of materials, it reduces the need for manual handling, thereby minimizing the risk of injuries and improving overall site safety.
Food Processing
The food processing industry greatly benefits from the hygienic and corrosion-resistant qualities of the galvanized steel roller, ensuring that conveyor systems meet strict health and safety standards.
- Conveying Food Items: Vital for the transport of food products through various stages of processing, including washing, cutting, and packaging, while preventing contamination.
- Resistance to Cleaning Agents: The galvanized coating withstands frequent washdowns with harsh cleaning agents, maintaining the integrity of conveyor systems.
- Temperature Resistance: Performs reliably in both high-temperature baking and freezing environments, crucial for different stages of food processing.
- Compliance with Health Regulations: Meets stringent health and safety regulations, thanks to its non-toxic and corrosion-resistant properties.
- Efficient Production Lines: Enables the design of efficient and streamlined production lines that can handle high volumes of food products with minimal downtime.
- Durability in Wet Environments: Exceptionally suited for use in areas of food processing where moisture is prevalent, preventing rust and ensuring long-term reliability.
Recycling and Waste Management
In recycling and waste management facilities, the galvanized steel roller is key to handling a wide variety of materials under demanding conditions, contributing to environmental sustainability.
- Material Sorting Conveyors: Facilitates the efficient sorting of recyclable materials from waste, crucial for effective recycling processes.
- Heavy Load Handling: Capable of supporting the heavy loads typical of waste management operations, from bulk paper to metal scrap.
- Resistance to Corrosive Materials: Withstands exposure to potentially corrosive substances found in waste materials, maintaining operational efficiency.
- Longevity in Harsh Conditions: Offers extended service life in the abrasive environment of recycling facilities, reducing the need for frequent replacements.
- Operational Efficiency: Enhances the overall efficiency of recycling operations by ensuring the smooth flow of materials through sorting and processing stages.
- Support for Green Initiatives: Plays a supportive role in green initiatives by facilitating the recycling process, contributing to the conservation of resources and reduction of landfill use.
Logistics and Distribution
Galvanized steel rollers are indispensable in the logistics and distribution sector, where they ensure the smooth and efficient movement of goods from warehouses to delivery vehicles.
- Loading and Unloading Systems: Streamlines the loading and unloading of goods, reducing manual labor and speeding up turnaround times.
- Parcel Sorting Systems: Integral to automated parcel sorting systems, ensuring accurate and efficient sorting of packages for delivery.
- Cross-Docking Operations: Facilitates cross-docking operations, where goods are quickly transferred from inbound to outbound transportation, minimizing storage time.
- Warehouse Automation: Key to automated warehouse systems, improving the storage and retrieval processes and maximizing space utilization.
- E-commerce Fulfillment: Supports the fast-paced environment of e-commerce fulfillment centers, handling a high volume of orders with precision.
- Durability and Reliability: Ensures the reliability of conveyor systems in distribution centers, where downtime can significantly impact delivery schedules.
In each sector, the galvanized steel roller not only supports the foundational needs of operational machinery but also contributes to advancements in efficiency, safety, and productivity. Its widespread application is a testament to its reliability and the significant value it adds to industrial and agricultural operations worldwide.
How to Choose the Right Galvanized Steel Roller
Choosing the right galvanized steel roller is not just about selecting a component that fits; it’s about ensuring that every aspect of the roller aligns with the specific demands of your operation. This decision is critical as it directly impacts the efficiency, durability, and overall performance of your conveyor system. The right roller can significantly enhance operational throughput, minimize maintenance requirements, and extend the service life of your system. To navigate this complex selection process, it’s essential to consider a comprehensive range of factors, each contributing to the roller’s performance in its unique operational context. Here’s an in-depth guide with expanded considerations to help you select a galvanized steel roller that perfectly meets your needs.
Assessing Load Capacity
The load capacity of a roller is foundational to its selection, determining its ability to handle the operational demands placed upon it without succumbing to deformation or failure.
- Understanding Maximum Load: It’s crucial to accurately determine the heaviest load the roller will need to support, ensuring it can withstand operational stresses.
- Steel Thickness Consideration: The thickness of the steel used in the roller’s construction must be appropriate for the load, providing the necessary strength and durability.
- Bearing Load Capacity: Choosing bearings with the right load capacity is essential for the roller’s longevity and smooth operation.
- Influence on Roller Lifespan: Rollers designed to handle heavier loads typically feature construction elements that extend their operational life.
- Even Load Distribution: Selecting a roller that ensures even load distribution across its surface can prevent premature wear and extend its service life.
- Tailored Solutions for Unique Loads: Operations with unique load-bearing requirements might benefit from custom-designed rollers to meet specific operational demands.
Determining Roller Spacing and Diameter
Optimal roller spacing and diameter are critical for the conveyor’s ability to efficiently and safely transport materials.
- Alignment with Material Dimensions: The size and shape of the materials being conveyed dictate the necessary roller diameter and spacing to ensure stability and prevent material loss.
- Customization for Operational Efficiency: Adjusting roller spacing and diameter to match your specific operational needs can dramatically improve material handling efficiency.
- Special Requirements Adaptation: For unique material handling challenges, consider working with manufacturers to customize roller specifications to your exact needs.
- Consideration for Small Items: Ensuring closer roller spacing for small items can prevent them from falling through and causing system disruptions.
- Heavy Load Accommodation: Larger diameter rollers are better suited for distributing the weight of heavy loads, reducing stress on individual rollers.
- Flexibility in Design: Adjustable spacing options can offer the flexibility needed to handle a variety of materials with a single system.
Considering Environmental Factors
The operating environment plays a significant role in selecting the right galvanized steel roller, influencing the choice of materials and the level of protection required.
- Appropriate Galvanization for Environment: The thickness and type of galvanization should be chosen based on the environmental conditions to which the roller will be exposed, ensuring optimal corrosion resistance.
- Adaptability to Specific Conditions: Rollers must be selected with materials and coatings that can withstand the specific challenges of their operating environment, including chemical exposure, moisture, and temperature extremes.
- Outdoor Versus Indoor Applications: Rollers intended for outdoor use require additional considerations for weather resistance compared to those used in controlled indoor environments.
- Chemical Exposure Resilience: In environments where chemicals are prevalent, rollers need coatings that can resist corrosion and maintain integrity over time.
- Temperature Range Compatibility: The selected rollers should be capable of operating efficiently within the temperature range they will be exposed to, ensuring reliability under varying conditions.
- Moisture and Humidity Resistance: For operations in wet or humid conditions, choosing rollers with enhanced moisture resistance is crucial to prevent rust and ensure longevity.
By thoroughly evaluating these detailed factors, you can make an informed decision, ensuring the galvanized steel roller you choose is perfectly suited to your operational requirements, environmental conditions, and long-term performance expectations.
Galvanized Steel Roller Price and Purchasing Tips
The cost of integrating galvanized steel rollers into your conveyor system is a significant consideration that goes beyond the initial purchase price. Understanding the various factors that influence the cost of these rollers is essential for budgeting and financial planning. Similarly, knowing how to navigate the market to find the best deals ensures that you secure high-quality components without overspending. Below, we delve into the intricacies of what affects the price of galvanized steel rollers and provide strategic tips for making cost-effective purchasing decisions without compromising on quality or performance.
Factors Affecting the Price of Galvanized Steel Rollers
The price of galvanized steel rollers is not a fixed figure but rather the result of a combination of several variables. From the materials used to market dynamics, understanding these factors can help you anticipate cost implications and make informed choices.
- Material Quality: The grade of steel and the quality of the galvanization process directly impact the roller’s durability and, consequently, its price.
- Size and Dimensions: Custom dimensions and larger sizes require more material and labor, increasing the manufacturing cost.
- Load Capacity: Rollers designed for higher load capacities are constructed with more robust materials, affecting the price.
- Galvanization Thickness: A thicker zinc coating offers better protection but also adds to the production cost.
- Bearing Type: The selection of bearings, especially high-performance ones, can significantly influence the roller’s price point.
- Quantity Ordered: Ordering in bulk often allows for discounts, affecting the unit price of each roller.
- Custom Features: Customizations to meet specific operational requirements can lead to higher costs due to additional manufacturing processes.
- Market Fluctuations: The cost of raw materials can vary with market conditions, impacting the final price of the rollers.
Tips for Finding the Best Deals on High-Quality Rollers for Sale
Securing the best deals requires a strategic approach to purchasing, focusing on both the price and the quality of the rollers. Here are some tips to guide you in finding high-quality galvanized steel rollers at competitive prices.
- Compare Suppliers: Research and comparison are key to identifying suppliers who offer the best value for money.
- Bulk Purchases: Consider the advantages of bulk buying, which can significantly reduce the cost per unit.
- Negotiate Pricing: Engage in negotiations with suppliers to secure better deals, especially for large or repeat orders.
- Look for Promotions: Stay alert to promotional offers and clearance sales that can provide substantial savings.
- Assess Total Cost of Ownership: Evaluate the long-term costs associated with the rollers, including maintenance and replacement expenses.
- Check for Warranties: A warranty can offer additional value, providing assurance against defects or premature failure.
- Prioritize Quality: Investing in higher-quality rollers can result in lower long-term costs due to reduced maintenance and longer service life.
- Request Samples: If possible, obtaining samples can help you assess the quality of the rollers before making a large investment.
- Read Reviews: Customer reviews and testimonials can offer insights into the reliability and performance of the rollers from different suppliers.
By carefully considering these factors and employing strategic purchasing tips, you can ensure that you invest wisely in galvanized steel rollers that meet your operational needs while adhering to your budgetary constraints.
Installation and Maintenance of Galvanized Steel Rollers
Ensuring the proper installation and maintenance of galvanized steel rollers is crucial for maximizing their efficiency and lifespan within conveyor systems. These guidelines and tips are designed to help you achieve optimal performance from your galvanized steel rollers, from the moment of installation through their operational life.
Basic Guidelines for Installing Galvanized Steel Rollers
The correct installation of galvanized steel rollers is foundational to the smooth operation of your conveyor system. Here are essential steps and considerations:
- Review Specifications: Before installation, thoroughly review the roller specifications to ensure compatibility with your conveyor system.
- Prepare the Conveyor Frame: Ensure the conveyor frame is clean and level. Proper alignment is crucial to prevent undue wear on the rollers.
- Check for Damage: Inspect each galvanized steel roller for any transport or manufacturing damage before installation to avoid future operational issues.
- Install with Care: When installing the rollers, handle them with care to avoid damaging the galvanized coating, which could lead to corrosion.
- Securely Fasten: Make sure all rollers are securely fastened in place, with no room for excessive movement that could affect the conveyor’s operation.
- Alignment Check: After installation, check the alignment of the rollers to ensure they are perfectly parallel to each other and perpendicular to the conveyor frame.
- Lubricate Bearings: If the rollers have bearings that require lubrication, ensure they are adequately lubricated before the first use.
- Test Run: Conduct a test run with no load to check for any installation issues. Listen for unusual noises that could indicate a problem.
Maintenance Tips to Ensure Longevity and Optimal Performance
Regular maintenance is key to extending the life of your galvanized steel rollers and maintaining the efficiency of your conveyor system.
- Regular Inspections: Conduct regular inspections to check for signs of wear, damage, or misalignment.
- Clean Regularly: Keep the rollers clean from debris and dust that could cause wear or operational issues. Use appropriate cleaning agents that will not damage the galvanized coating.
- Lubrication Schedule: Adhere to a regular lubrication schedule for bearings, if applicable, to ensure smooth operation and prevent overheating.
- Adjust as Needed: Make adjustments to alignment and tension as needed to ensure optimal performance and reduce wear.
- Replace Worn Rollers: Do not hesitate to replace rollers that show significant wear or damage. Delaying replacement can lead to system inefficiencies or failures.
- Monitor Load Capacities: Continuously monitor the loads being placed on the conveyor to ensure they do not exceed the specified capacity of the rollers.
- Protect from Excessive Moisture: While galvanized steel rollers are corrosion-resistant, protecting them from excessive moisture can prevent the potential for rust and prolong their life.
- Use Genuine Parts for Repairs: When repairs are necessary, use genuine parts that match the original specifications to maintain performance and safety standards.
- Training for Maintenance Staff: Ensure that maintenance staff are properly trained in the care and upkeep of galvanized steel rollers to prevent accidental damage during routine maintenance.
By following these installation and maintenance guidelines, you can significantly enhance the operational life and efficiency of your galvanized steel rollers, ensuring they continue to provide reliable service in your conveyor system.
Where to Buy Galvanized Steel Roller
In the quest for high-quality galvanized steel rollers, the choice of supplier is as critical as the product itself. The market is replete with options, each offering varying degrees of quality, service, and value. Identifying a supplier that not only provides a product that meets your specific needs but also supports your purchase with exceptional service can significantly impact the success of your operations. Below, we delve into recommendations for identifying reputable suppliers known for their heavy-duty conveyor rollers and outline essential criteria to consider when evaluating potential suppliers. This guidance aims to streamline your selection process, ensuring you partner with a supplier capable of contributing positively to your operational efficiency.
Recommendations for Reputable Suppliers
Selecting the right supplier for your galvanized steel roller involves navigating a complex market landscape. Here are curated recommendations designed to direct you towards suppliers with a proven track record of reliability and quality in providing heavy-duty conveyor components.
- Industry Recognition: Suppliers with a strong presence and positive reputation in the industry are often synonymous with quality and reliability.
- Specialization and Expertise: Providers specializing in conveyor technology typically offer a depth of expertise and product innovation that general industrial suppliers might not.
- Global and Local Options: Both globally recognized brands and local distributors have their unique advantages, from cutting-edge technology to personalized service and quick delivery.
- Peer Recommendations: Insights from industry peers can be invaluable, offering real-world feedback on suppliers’ product quality and customer service.
- Certification and Standards Compliance: Suppliers that adhere to industry standards and hold relevant certifications demonstrate a commitment to quality and safety.
What to Look for in a Supplier
Choosing a supplier is a decision that goes beyond product selection, encompassing factors that ensure a beneficial and enduring partnership.
- Comprehensive Quality Assurance: A supplier’s commitment to quality assurance is fundamental, ensuring that every roller meets stringent standards for performance and durability.
- Diverse Product Offerings: A broad selection of products indicates a supplier’s capability to cater to a wide range of operational needs, offering solutions that are precisely aligned with your requirements.
- Exceptional Customer Support: The level of customer service provided, from initial inquiry through to after-sales support, can significantly influence your satisfaction and the success of your project.
- Technical and Maintenance Support: Access to expert technical support for product selection, installation guidance, and ongoing maintenance can enhance the operational lifespan of your rollers.
- Warranty and Return Policies: Clear and favorable warranty terms and return policies are indicators of a supplier’s confidence in their products and their commitment to customer satisfaction.
- Customization Capabilities: The ability to customize products to meet specific operational challenges is a valuable service that can lead to more effective and efficient conveyor system solutions.
- Timeliness and Reliability of Delivery: Ensuring that your supplier can meet your timeline with reliable delivery services is crucial to maintaining project schedules and operational efficiency.
- Value for Investment: While the cheapest option is not always the best, competitive pricing for the quality offered ensures that you receive value for your investment, balancing cost with the benefits of durability, reliability, and service.
By carefully considering these recommendations and criteria, you can select a supplier that not only meets your immediate product needs but also aligns with your long-term operational goals, ensuring a successful and productive partnership.
FAQs about Galvanized Steel Roller
Steel rollers are integral components in conveyor systems, used across a wide range of industries to facilitate the movement of goods, materials, and products along a defined path. Their primary function is to support and transport items efficiently from one point to another within a facility, whether it’s in manufacturing plants, distribution centers, packaging lines, or material handling setups. Due to their strength and durability, steel rollers are particularly favored for heavy-duty applications where they bear substantial loads. They are also used in environments that require resistance to abrasion, impact, and high temperatures. Beyond industrial applications, steel rollers find utility in agricultural machinery, cargo loading areas, and even in certain types of equipment like gym machines, offering smooth operation and longevity. The versatility of steel rollers, combined with their robust construction, makes them indispensable in optimizing operational workflows and enhancing productivity in various operational contexts.
A stainless steel roller is a specific type of conveyor roller made from stainless steel, an alloy known for its corrosion resistance, hygiene, and aesthetic appeal. These rollers are particularly utilized in environments where corrosion resistance is paramount, such as in food processing, pharmaceutical, chemical, and marine applications. Stainless steel rollers are chosen not only for their durability but also for their ability to maintain cleanliness, making them ideal for applications where sanitary conditions are critical. The non-reactive properties of stainless steel ensure that these rollers do not contaminate the materials they come into contact with, which is essential for industries adhering to strict health and safety standards. Additionally, stainless steel rollers can withstand washdowns with harsh chemicals without deteriorating, ensuring they remain operational in aggressive environments. Their application is widespread, from small-scale operations to large, complex conveyor systems, providing a reliable and hygienic solution for material handling needs.
The spacing for roller conveyors, often referred to as roller pitch, is a critical design parameter that determines the distribution of rollers along the conveyor frame. The correct spacing is essential for the smooth and efficient transportation of goods, as it affects the conveyor’s ability to support the items being moved. Generally, the spacing is determined based on the size and type of items the conveyor will handle. A common guideline is that the smallest item on the conveyor should be supported by at least three rollers at any given time. This ensures stability and prevents items from tipping or getting stuck. For heavier loads or larger items, rollers may be spaced more closely to distribute the weight evenly and reduce the stress on individual rollers. Conversely, for lighter or uniformly shaped items, rollers can be spaced further apart. The specific spacing is often customized to the application’s needs, taking into account factors such as load weight, item dimensions, and the desired speed of movement. Consulting with conveyor design experts or manufacturers is advisable to determine the optimal roller spacing for a particular application.
Conveyor rollers come in a variety of sizes to accommodate different loads, conveyor widths, and application requirements. The size of a conveyor roller is typically described by its diameter and length. Roller diameters can range widely, with common sizes including but not limited to 1.9 inches, 2.5 inches, and 3.5 inches. These diameters are chosen based on the weight of the materials being conveyed and the required roller capacity. The length of the roller is usually determined by the width of the conveyor belt or frame it needs to fit into, ensuring it provides adequate support across the entire width of the conveyor. For specialized applications, rollers can be custom-sized to meet specific operational needs. It’s important to select the appropriate roller size to ensure efficient operation, minimize wear and tear, and extend the lifespan of the conveyor system. Manufacturers and suppliers can provide guidance on selecting the right roller size based on the specific parameters of the conveyor system and the materials being transported.
Last Updated on February 28, 2024 by Jordan Smith
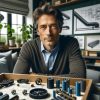
Jordan Smith, a seasoned professional with over 20 years of experience in the conveyor system industry. Jordan’s expertise lies in providing comprehensive solutions for conveyor rollers, belts, and accessories, catering to a wide range of industrial needs. From initial design and configuration to installation and meticulous troubleshooting, Jordan is adept at handling all aspects of conveyor system management. Whether you’re looking to upgrade your production line with efficient conveyor belts, require custom conveyor rollers for specific operations, or need expert advice on selecting the right conveyor accessories for your facility, Jordan is your reliable consultant. For any inquiries or assistance with conveyor system optimization, Jordan is available to share his wealth of knowledge and experience. Feel free to reach out at any time for professional guidance on all matters related to conveyor rollers, belts, and accessories.