The Evolution of Gold Mining Conveyor Belt Technology
In gold mining operations, the gold mining conveyor belt plays a crucial role in enhancing efficiency and productivity. These specialized conveyor belts are designed to transport large volumes of ore seamlessly, reducing the need for manual labor and increasing safety. The significance of the gold mining conveyor belt cannot be overstated, as it revolutionizes the entire mining process. With the continuous evolution of technology, gold mining conveyor belts have become more efficient, durable, and capable of handling harsh mining environments. This advancement allows mining operations to achieve higher output and lower operational costs, making the gold mining conveyor belt an indispensable asset in the industry.
The Role of Gold Mining Conveyor Belt
Conveyor belts have revolutionized the gold mining industry by significantly enhancing the efficiency and safety of ore transportation. The introduction of the gold mining conveyor belt has allowed for the automation of material handling processes, which was previously labor-intensive and time-consuming. This transformation has not only increased productivity but also reduced operational costs and improved safety standards in mining operations.
How Conveyor Belts Revolutionized Gold Mining
The gold mining conveyor belt has fundamentally changed the way ore is transported within mining sites. Traditionally, the transportation of ore relied heavily on manual labor and rudimentary machinery, which were both inefficient and hazardous. The implementation of conveyor belts has streamlined this process, allowing for the continuous movement of ore from the extraction site to the processing plant. This automation reduces the need for manual handling, minimizing the risk of accidents and injuries.
The efficiency gains from using conveyor belts in gold mining are substantial. Conveyor belts can move large volumes of material quickly and continuously, which is essential in an industry where time and productivity are critical. The ability to transport ore over long distances without interruption means that mining operations can maintain a steady flow of materials, leading to higher output and profitability.
Automation and Efficiency in Ore Transportation
The gold mining conveyor belt is a key component of the automation process in modern mining operations. Automation involves the use of advanced technologies and machinery to perform tasks that were once done manually. In the context of gold mining, conveyor belts are integrated with other automated systems to create a seamless and efficient material handling process.
One of the primary benefits of the gold mining conveyor belt is its ability to handle varying loads and adapt to the changing needs of the mining operation. Conveyor belts can be customized to suit specific requirements, such as the type of material being transported, the distance to be covered, and the terrain of the mining site. This flexibility ensures that conveyor belts can operate efficiently in a wide range of conditions.
Automation also enhances the precision and control of ore transportation. Conveyor belts are equipped with sensors and monitoring systems that track the movement of materials and detect any issues in real-time. This level of control allows mining operators to optimize the flow of materials, reduce downtime, and prevent bottlenecks in the production process.
Safety and Environmental Benefits
The gold mining conveyor belt not only improves efficiency but also contributes to safer and more sustainable mining practices. By automating the transportation of ore, conveyor belts reduce the need for manual labor in hazardous areas, thereby lowering the risk of accidents and injuries. Additionally, the continuous and controlled movement of materials minimizes spillage and dust generation, which are common environmental concerns in mining operations.
Conveyor belts are designed to be durable and resilient, capable of withstanding the harsh conditions of mining environments. They are constructed from robust materials that resist wear and tear, ensuring long-term reliability and reducing the need for frequent maintenance and replacements. This durability is essential in maintaining the efficiency and safety of mining operations.
Economic Impact and Future Trends
The economic impact of the gold mining conveyor belt is significant, as it directly influences the cost-efficiency and profitability of mining operations. By reducing labor costs, increasing productivity, and minimizing operational disruptions, conveyor belts contribute to the overall financial performance of mining companies. The investment in conveyor belt technology is often offset by the long-term savings and benefits it provides.
Looking ahead, the future of gold mining conveyor belts lies in further technological advancements and innovations. Developments in materials science, automation, and digitalization are expected to enhance the performance and capabilities of conveyor belts. For example, the integration of smart technologies and the Internet of Things (IoT) can provide real-time data and analytics, enabling predictive maintenance and optimizing the efficiency of material handling processes.
The gold mining conveyor belt plays a pivotal role in modernizing and improving the gold mining industry. Its ability to automate and streamline ore transportation has revolutionized mining operations, leading to increased productivity, safety, and environmental sustainability. As technology continues to evolve, the gold mining conveyor belt will remain a critical asset in the pursuit of more efficient and profitable mining practices.
What Are Gold Mining Conveyor Belts?
Gold mining conveyor belts are specialized types of conveyor systems designed specifically for the demanding requirements of gold mining operations. These belts are essential for transporting extracted ore from the mining site to the processing plant efficiently and safely. They play a crucial role in modern mining, where the scale of operations and the need for continuous productivity necessitate the use of advanced material handling solutions.
Definition and Specific Characteristics of Gold Mining Conveyor Belts
A gold mining conveyor belt is a continuous loop of material that moves a load of ore or other materials from one point to another. These conveyor belts are engineered to withstand the harsh conditions of mining environments, including exposure to abrasive materials, heavy loads, and extreme temperatures. The primary purpose of these belts is to facilitate the transportation of gold-bearing ore from the extraction site to processing facilities, thus streamlining the mining process and enhancing efficiency.
Specific Characteristics:
- Durability and Strength: Gold mining conveyor belts are made from high-strength materials such as rubber, PVC, or reinforced fabric. These materials ensure the belts can handle heavy loads and resist wear and tear from abrasive ore.
- Width and Length: The belts can be customized in width and length to suit the specific needs of a mining operation. This flexibility allows for the transportation of varying volumes of ore over different distances.
- Temperature Resistance: Given the extreme temperatures often encountered in mining environments, these conveyor belts are designed to resist both high and low temperatures without compromising performance.
- Tear and Impact Resistance: Gold mining conveyor belts are engineered to be tear-resistant and capable of withstanding significant impacts from falling ore. This characteristic is vital for maintaining belt integrity and preventing downtime.
- Ease of Maintenance: These belts are designed for easy maintenance and quick repairs, ensuring minimal downtime and continuous operation.
Comparison with Traditional Conveyor Belt Systems
Gold mining conveyor belts differ significantly from traditional conveyor belt systems used in other industries. The table below highlights some key differences between gold mining conveyor belts and conventional conveyor systems:
Importance in Gold Mining Operations
The importance of gold mining conveyor belts cannot be overstated. They are integral to the efficiency and productivity of mining operations. By automating the transportation of ore, these belts significantly reduce the need for manual labor, lower operational costs, and improve safety standards.
Efficiency and Productivity
Gold mining conveyor belts enable the continuous movement of ore, ensuring a steady flow from the mining site to the processing plant. This continuous operation is crucial for maintaining high levels of productivity. The ability to transport large volumes of ore quickly and efficiently reduces the time and labor required for material handling, allowing mining operations to focus on extraction and processing.
Safety
Safety is a paramount concern in mining operations. Gold mining conveyor belts help enhance safety by minimizing the need for manual handling of heavy and abrasive materials. Automated conveyor systems reduce the risk of injuries associated with manual lifting, carrying, and transporting of ore. Additionally, the controlled movement of materials reduces the likelihood of accidents and spillage, further improving the safety of mining sites.
Environmental Impact
Gold mining conveyor belts also contribute to minimizing the environmental impact of mining operations. By reducing spillage and dust generation, these belts help maintain a cleaner and more environmentally friendly mining site. The efficient transportation of ore reduces the need for additional transport equipment, thereby lowering fuel consumption and emissions associated with material transportation.
Gold mining conveyor belts are specialized systems designed to meet the rigorous demands of gold mining operations. Their durability, strength, and efficiency make them indispensable in modern mining. By automating ore transportation, these conveyor belts enhance productivity, improve safety, and reduce environmental impact. The significant differences between gold mining conveyor belts and traditional conveyor systems underscore the importance of tailored solutions in achieving optimal mining performance. As technology continues to advance, the role of gold mining conveyor belts will remain crucial in the evolution of the mining industry.
Key Components of Gold Mining Conveyor Belts
The gold mining conveyor belt is an essential piece of equipment in modern mining operations, designed to transport ore efficiently and safely from extraction sites to processing plants. These conveyor belts are engineered with specific materials and technologies to withstand the harsh conditions of mining environments and to ensure durability and efficiency. Understanding the key components of these conveyor belts can provide insights into their construction, functionality, and the innovations that make them indispensable in the mining industry.
Overview of Materials Used in Gold Mining Conveyor Belts
Gold mining conveyor belts are constructed from high-performance materials that provide the necessary strength, flexibility, and resistance to environmental factors. The choice of materials is crucial to ensure the belt can handle the heavy loads and abrasive nature of the mined ore.
Common Materials:
- Rubber: High-grade rubber is commonly used in the manufacturing of gold mining conveyor belts due to its excellent durability and resistance to wear and tear. Rubber belts can withstand the constant friction and impact from the transported ore.
- PVC (Polyvinyl Chloride): PVC is another popular material for conveyor belts. It offers good resistance to chemicals and moisture, making it suitable for wet mining environments. PVC belts are also flexible and easy to maintain.
- Reinforced Fabric: Conveyor belts often incorporate layers of reinforced fabric, such as polyester or nylon, to enhance their tensile strength. This reinforcement helps the belt maintain its shape and resist stretching under heavy loads.
- Steel Cords: In some cases, steel cords are embedded within the belt to provide additional strength and reduce the risk of elongation. These steel-reinforced belts are particularly useful in applications requiring long-distance transportation and high load capacities.
Technology in Manufacturing Gold Mining Conveyor Belts
The manufacturing process of gold mining conveyor belts involves advanced technologies to ensure the belts meet the rigorous demands of mining operations. Innovations in belt design and production contribute to the overall performance, efficiency, and lifespan of the conveyor system.
Technological Innovations:
- Vulcanization: This process involves bonding the belt materials together through heat and pressure, creating a seamless and durable belt. Vulcanized belts have enhanced strength and flexibility, making them ideal for heavy-duty mining applications.
- Heat and Cold Resistance: Technologies are employed to make conveyor belts resistant to extreme temperatures. This is particularly important in mining environments where belts are exposed to both high heat and freezing conditions.
- Abrasion Resistance: The belts are treated with special coatings and additives that increase their resistance to abrasion. This ensures the belts can handle the constant friction from the ore without degrading quickly.
- Anti-Tear Properties: Advanced materials and construction techniques are used to enhance the tear resistance of the belts. This prevents damage from sharp and heavy rocks, extending the belt’s operational life.
Insights into the Design Focused on Durability and Efficiency
The design of gold mining conveyor belts is centered on maximizing durability and efficiency. These belts are not only built to last but also to optimize the transportation process, reducing downtime and maintenance costs.
Durability Features:
- Robust Construction: The combination of high-quality rubber, reinforced fabric, and steel cords results in a robust belt capable of withstanding harsh mining conditions. This robust construction minimizes the risk of belt failure and ensures consistent performance.
- Seamless Splicing: The use of vulcanization and other splicing techniques creates seamless joints in the conveyor belt, eliminating weak points that could lead to belt breakage. Seamless splicing also ensures a smooth surface for efficient material movement.
- Enhanced Load-Bearing Capacity: The incorporation of reinforced materials and steel cords allows the belts to carry heavy loads without sagging or stretching. This capability is crucial for transporting large volumes of ore over long distances.
Efficiency Features:
- Optimized Tread Patterns: Conveyor belts are designed with specific tread patterns that enhance grip and traction. This prevents slippage and ensures the steady movement of ore, even on inclines.
- Energy-Efficient Motors: Modern conveyor belts are often paired with energy-efficient motors and drive systems. These systems reduce energy consumption and operational costs while maintaining high performance.
- Automated Control Systems: Integration with automated control systems allows for precise monitoring and adjustment of the conveyor belt’s speed and operation. This automation optimizes the flow of materials, reduces bottlenecks, and increases overall productivity.
The gold mining conveyor belt is a critical component in the mining industry, designed to meet the demanding requirements of transporting ore in harsh environments. The materials and technologies used in the manufacturing of these belts ensure they are durable, efficient, and capable of handling heavy loads. The design features focused on durability and efficiency further enhance their performance, making gold mining conveyor belts indispensable in modern mining operations. As the industry continues to evolve, ongoing innovations in materials and technology will further improve the capabilities and longevity of these essential systems.
Leading Manufacturers of Gold Mining Conveyor Belts
The gold mining conveyor belt is a crucial component in the mining industry, and its manufacturing requires specialized expertise and advanced technology. Several leading global manufacturers excel in producing high-quality conveyor belts specifically designed for gold mining operations. These companies stand out due to their innovative technologies, material innovations, and commitment to durability and efficiency. Here are five top manufacturers in the field:
1. ContiTech AG
Overview: ContiTech AG, a subsidiary of Continental AG, is one of the world’s leading manufacturers of conveyor belts for various industries, including mining. The company is renowned for its extensive range of high-performance conveyor belts tailored to meet the specific needs of gold mining operations.
Key Features:
- Technology: ContiTech utilizes advanced technologies such as their proprietary ContiPlus online service tool, which helps monitor and manage conveyor belt performance.
- Material Innovation: Their conveyor belts are made from high-quality materials that offer excellent abrasion resistance and durability, ensuring a longer lifespan in harsh mining environments.
- Customization: ContiTech offers customized solutions tailored to the specific requirements of gold mining operations, enhancing efficiency and reducing operational costs.
2. Fenner Dunlop
Overview: Fenner Dunlop is a leading manufacturer of conveyor belts with a strong focus on the mining industry. The company’s history dates back over 150 years, and it has built a reputation for producing some of the most durable and reliable conveyor belts in the market.
Key Features:
- Technology: Fenner Dunlop’s EagleEye® monitoring system provides real-time data on the condition of the conveyor belt, enabling proactive maintenance and reducing downtime.
- Material Innovation: Their belts are engineered with advanced materials such as aramid and steel reinforcements, which provide superior strength and resistance to wear and tear.
- Durability: Fenner Dunlop’s belts are designed to withstand the rigorous demands of gold mining, with features such as high impact resistance and low maintenance requirements.
3. Bridgestone Corporation
Overview: Bridgestone Corporation is a global leader in rubber and polymer technologies, offering a wide range of conveyor belts designed for mining applications. Bridgestone’s conveyor belts are known for their exceptional quality and performance in demanding mining environments.
Key Features:
- Technology: Bridgestone employs cutting-edge technologies in their manufacturing processes, ensuring high precision and quality in their conveyor belts.
- Material Innovation: The company uses advanced rubber compounds and reinforcement materials to produce belts that are highly resistant to abrasion and impact.
- Efficiency: Bridgestone’s conveyor belts are designed to enhance operational efficiency by reducing energy consumption and maintenance costs.
4. Goodyear Belting
Overview: Goodyear Belting, a division of Veyance Technologies, Inc., offers a comprehensive range of conveyor belts for the mining industry. Goodyear’s belts are synonymous with quality and reliability, making them a preferred choice for gold mining operations.
Key Features:
- Technology: Goodyear Belting utilizes innovative manufacturing techniques and technologies to produce conveyor belts that meet the highest industry standards.
- Material Innovation: Their conveyor belts incorporate advanced materials that provide excellent durability and resistance to harsh mining conditions.
- Performance: Goodyear’s belts are designed for maximum performance, ensuring efficient material handling and reduced operational disruptions.
5. Sempertrans
Overview: Sempertrans, a division of the Semperit Group, is a leading manufacturer of conveyor belts with a strong focus on the mining sector. Sempertrans offers a variety of conveyor belts that are specifically designed to meet the challenges of gold mining operations.
Key Features:
- Technology: Sempertrans uses state-of-the-art technology in their manufacturing processes, resulting in conveyor belts that are highly efficient and reliable.
- Material Innovation: The company’s belts are made from high-quality materials that offer superior resistance to wear, impact, and extreme temperatures.
- Customization: Sempertrans provides customized solutions to meet the specific needs of their clients, ensuring optimal performance and longevity of their conveyor belts.
The gold mining conveyor belt is an essential component in the mining industry, and its production requires specialized expertise and advanced technology. Leading manufacturers like ContiTech AG, Fenner Dunlop, Bridgestone Corporation, Goodyear Belting, and Sempertrans stand out due to their innovative technologies, material innovations, and commitment to producing high-quality, durable, and efficient conveyor belts. These manufacturers not only provide superior products but also offer customized solutions and advanced monitoring systems that enhance the overall performance and efficiency of gold mining operations.
Types and Applications of Gold Mining Conveyor Belts
The gold mining conveyor belt is a versatile tool essential for transporting ore and other materials efficiently within mining operations. There are various types of conveyor belts used in gold mining, each designed for specific applications and operational conditions. Understanding these types and their applications helps in selecting the most suitable conveyor belt for particular mining needs.
1. Steel Cord Conveyor Belts
Description: Steel cord conveyor belts are reinforced with steel cables, which provide exceptional strength and durability. These belts are ideal for long-distance transportation of heavy loads.
Applications:
- Long Haul Transportation: Used for transporting gold ore over long distances, from the mining site to the processing plant.
- High Load Capacity: Suitable for carrying large volumes of ore, reducing the number of trips required.
Advantages:
- High tensile strength, ensuring minimal elongation and reduced maintenance.
- Excellent resistance to impact and abrasion, making them durable in harsh mining conditions.
2. Textile Conveyor Belts
Description: Textile conveyor belts are reinforced with fabric materials such as polyester, nylon, or cotton. These belts offer a good balance between strength and flexibility.
Applications:
- Short to Medium Distances: Ideal for shorter transportation routes within the mining site.
- General Purpose: Used for various material handling tasks, including transporting crushed ore and waste rock.
Advantages:
- Flexible and easy to install, making them suitable for operations with frequent belt changes.
- Cost-effective solution for less demanding applications.
3. Chevron Conveyor Belts
Description: Chevron conveyor belts feature a unique V-shaped pattern on the surface, which provides additional grip. These belts are designed to prevent materials from slipping back on inclined surfaces.
Applications:
- Inclined Transportation: Perfect for transporting materials up steep inclines, such as from underground mines to the surface.
- Wet and Slippery Conditions: Effective in environments where materials are wet or prone to slipping.
Advantages:
- Enhanced grip prevents material rollback, ensuring efficient transportation on slopes.
- Versatile design suitable for various materials, including ore and loose rock.
4. Heat-Resistant Conveyor Belts
Description: Heat-resistant conveyor belts are designed to withstand high temperatures without degrading. These belts are made from materials that can endure extreme heat.
Applications:
- High-Temperature Areas: Used in areas where the ore or environment generates significant heat, such as near processing equipment.
- Hot Materials: Suitable for transporting ore that has been heated as part of the extraction process.
Advantages:
- Maintains structural integrity at high temperatures, ensuring longevity.
- Reduces the risk of belt damage and downtime in high-heat environments.
5. Pipe Conveyor Belts
Description: Pipe conveyor belts are designed to form a pipe-like shape during operation. This design completely encloses the transported material, protecting it from external conditions.
Applications:
- Dusty Environments: Ideal for transporting materials in areas where dust control is critical.
- Sensitive Materials: Used for materials that need protection from contamination or spillage.
Advantages:
- Completely encloses materials, preventing spillage and reducing dust generation.
- Protects materials from external contamination and environmental conditions.
Analysis of Preference in Specific Mining Conditions
Certain types of gold mining conveyor belts are preferred over others based on specific mining conditions and operational requirements:
- Steel Cord Conveyor Belts are preferred for their high tensile strength and durability, making them ideal for long-distance and heavy-load applications. Their resistance to impact and abrasion ensures they can withstand the harshest mining environments, reducing maintenance and downtime.
- Textile Conveyor Belts are chosen for their flexibility and cost-effectiveness. They are suitable for shorter distances and less demanding applications where frequent belt changes are necessary.
- Chevron Conveyor Belts are favored in operations involving inclined transportation. The V-shaped pattern provides additional grip, preventing material rollback and ensuring efficient transport on slopes.
- Heat-Resistant Conveyor Belts are essential in high-temperature areas. They maintain their integrity under extreme heat, making them indispensable in environments near processing equipment or for transporting heated materials.
- Pipe Conveyor Belts are the go-to choice for dusty environments and sensitive materials. Their ability to enclose the material completely prevents spillage and contamination, ensuring a clean and controlled transportation process.
The gold mining conveyor belt comes in various types, each tailored to specific applications and conditions within the mining industry. Selecting the right type of conveyor belt is crucial for optimizing efficiency, durability, and safety in gold mining operations. By understanding the unique characteristics and advantages of each type, mining operations can choose the most suitable conveyor belt to meet their specific needs.
Purchasing a Gold Mining Conveyor Belt
Purchasing a gold mining conveyor belt is a critical investment for any mining operation. The right conveyor belt can significantly improve efficiency, reduce operational costs, and enhance overall productivity. This section provides an overview of where to find gold mining conveyor belts for sale and what factors to consider in terms of cost.
For Sale Options
Finding the right gold mining conveyor belt involves exploring various platforms and outlets.
- Manufacturer Websites: Directly purchasing from manufacturers like ContiTech, Fenner Dunlop, Bridgestone, Goodyear, and Sempertrans ensures you get belts that meet your specific requirements. These companies offer detailed product descriptions, customization options, and technical support.
- Industrial Equipment Suppliers: Companies such as Grainger and Motion Industries specialize in providing a wide range of industrial equipment, including conveyor belts. They often carry products from multiple manufacturers, allowing you to compare options and find the best fit for your needs.
- Online Marketplaces: Websites like Alibaba and Amazon offer a broad selection of conveyor belts from various suppliers worldwide. While purchasing through these platforms can be convenient, it’s essential to verify the credibility of the sellers and the quality of the products.
- Mining Equipment Dealers: Specialized mining equipment dealers often stock high-quality conveyor belts designed specifically for mining applications. These dealers can provide expert advice on selecting the right belt and may offer installation and maintenance services.
- Auctions and Liquidation Sales: Occasionally, mining operations upgrade their equipment or close down, resulting in surplus conveyor belts being sold at auctions or liquidation sales. These events can be an opportunity to purchase belts at a reduced cost, though it’s important to thoroughly inspect the items for wear and damage.
Tips on Choosing the Right Dealer or Platform
- Reputation and Reviews: Look for dealers and platforms with positive reviews and a strong reputation in the industry. This can provide assurance of product quality and customer service.
- Product Range and Customization: Choose a supplier that offers a wide range of conveyor belts and customization options to ensure the belt meets your specific needs.
- Technical Support and Services: Opt for dealers who provide technical support, installation, and maintenance services. This can be invaluable in ensuring the longevity and optimal performance of your conveyor belt.
- Warranty and Return Policies: Ensure the supplier offers a warranty and has clear return policies. This protects your investment in case of defects or issues with the belt.
- Price Comparisons: Compare prices from multiple sources to ensure you get the best value for your money. However, prioritize quality and suitability over the lowest price.
Cost Considerations
The cost of a gold mining conveyor belt can vary significantly based on several factors.
- Material Quality: High-quality materials such as reinforced rubber, PVC, or steel cords can increase the cost of the conveyor belt but offer superior durability and performance.
- Customization and Specifications: Customizing the conveyor belt to meet specific requirements, such as size, load capacity, and resistance properties, can add to the overall cost.
- Length and Width: The dimensions of the conveyor belt significantly impact the price. Longer and wider belts require more material and labor to manufacture.
- Technological Features: Advanced features such as heat resistance, anti-tear properties, and integrated monitoring systems can raise the cost but provide significant operational benefits.
- Brand and Manufacturer: Established brands with a reputation for quality and reliability may charge a premium for their products. However, this often translates to better performance and longer lifespan.
Investment vs. Operational Benefit Ratio
When purchasing a gold mining conveyor belt, it’s essential to consider the investment versus the operational benefits. A higher upfront cost for a durable, high-quality belt can result in significant long-term savings and operational efficiencies. Here’s a closer look at this ratio:
- Longevity and Durability: Investing in a robust conveyor belt reduces the frequency of replacements and repairs, lowering long-term maintenance costs.
- Efficiency and Productivity: A high-quality conveyor belt ensures smooth and reliable transportation of ore, enhancing overall productivity and reducing downtime.
- Safety: Superior belts with advanced features improve safety by minimizing the risk of accidents and material spillage, which can be costly and hazardous.
- Energy Savings: Energy-efficient conveyor belts can reduce power consumption, resulting in lower operational costs over time.
- Resale Value: High-quality belts from reputable manufacturers retain better resale value if you need to upgrade or sell them in the future.
Purchasing a gold mining conveyor belt involves careful consideration of where to buy and the factors that influence cost. By selecting the right dealer or platform and investing in a high-quality belt, mining operations can achieve significant long-term benefits in efficiency, safety, and cost savings.
Choosing the Right Gold Mining Conveyor Belt
Selecting the right gold mining conveyor belt is crucial for ensuring efficiency, durability, and safety in mining operations. The conveyor belt is a vital component in transporting ore and materials, and choosing the right one involves considering several factors and guidelines to match the specific needs of the mining operation.
Factors to Consider When Selecting a Gold Mining Conveyor Belt
When choosing a gold mining conveyor belt, it’s essential to evaluate several key factors that impact its performance and suitability for the mining environment.
Tensile Strength:
- Importance: The tensile strength of a conveyor belt indicates its ability to withstand the tension and load applied during operation.
- Consideration: For gold mining, where heavy loads of ore are transported, selecting a belt with high tensile strength is crucial to prevent breakage and ensure continuous operation. Look for belts with reinforced materials like steel cords or high-strength fabric.
Material Composition:
- Importance: The materials used in the construction of the conveyor belt determine its durability, resistance to wear and tear, and overall performance.
- Consideration: Choose belts made from high-quality rubber, PVC, or reinforced fabric that can withstand the abrasive nature of ore and harsh mining conditions. Heat-resistant materials are also essential if the belt will be exposed to high temperatures.
Environmental Conditions:
- Importance: The operating environment plays a significant role in the selection of a conveyor belt. Factors like temperature, humidity, and exposure to chemicals can affect the belt’s longevity and performance.
- Consideration: For mining operations in extreme conditions, opt for belts that are specifically designed to resist temperature fluctuations, moisture, and chemical exposure. Heat-resistant and cold-resistant belts are available for such environments.
Load Capacity and Size:
- Importance: The conveyor belt must be able to handle the volume and weight of the materials being transported.
- Consideration: Assess the required load capacity and select a belt that matches these needs. The belt’s width and length should be suitable for the conveyor system and the amount of ore to be transported. Customizable options are available to fit specific requirements.
Maintenance and Durability:
- Importance: The ease of maintenance and the durability of the conveyor belt affect the operational efficiency and cost-effectiveness of the mining operation.
- Consideration: Select belts that are known for their low maintenance requirements and high durability. Features like tear resistance, impact resistance, and abrasion resistance are crucial for minimizing downtime and extending the belt’s lifespan.
Guidelines on Assessing Belt Quality and Compatibility with Mining Operations
Ensuring the chosen gold mining conveyor belt meets the quality standards and is compatible with the mining operations involves several steps:
Quality Certifications and Standards:
- Check if the conveyor belt complies with industry standards and certifications. Look for ISO certifications or other relevant quality marks that indicate the belt’s reliability and adherence to safety and performance standards.
Supplier Reputation and Experience:
- Choose belts from reputable manufacturers with a proven track record in the mining industry. Manufacturers with extensive experience are more likely to produce high-quality belts and provide better customer support and warranties.
Field Testing and Performance Data:
- Request performance data and case studies from the supplier to understand how the belt performs in real mining conditions. Field testing results can provide valuable insights into the belt’s durability, efficiency, and suitability for specific applications.
Customization Options:
- Ensure the supplier offers customization options to tailor the conveyor belt to the specific needs of your mining operation. This includes adjusting the belt’s size, material composition, and additional features like heat resistance or impact protection.
After-Sales Support and Services:
- Evaluate the supplier’s after-sales support, including maintenance services, technical support, and availability of spare parts. A reliable support system can help address any issues quickly and minimize downtime.
Choosing the right gold mining conveyor belt involves careful consideration of various factors, including tensile strength, material composition, environmental conditions, load capacity, and maintenance requirements. By following these guidelines and assessing the quality and compatibility of the belt with your mining operations, you can ensure a reliable, efficient, and durable conveyor system that enhances productivity and reduces operational costs. Investing in the right conveyor belt is crucial for the success and sustainability of your gold mining endeavors.
Safety and Maintenance of Gold Mining Conveyor Belts
The gold mining conveyor belt is a critical component in mining operations, and its safety and maintenance are paramount for ensuring continuous and efficient operation. Proper attention to these aspects can significantly extend the life of the conveyor belt, enhance safety, and reduce downtime. This section explores the importance of safety standards and provides essential maintenance tips.
Importance of Opting for Belts that Adhere to Safety Standards
Safety is a top priority in mining operations, and selecting a gold mining conveyor belt that adheres to safety standards is crucial. Conveyor belts that meet recognized safety standards are designed to minimize risks and protect workers, equipment, and the environment.
Safety Standards to Consider:
- Fire Resistance: Conveyor belts used in mining must be fire-resistant to prevent the spread of fires, which can be catastrophic in underground mining environments. Look for belts that comply with fire safety standards such as ISO 340 or MSHA (Mine Safety and Health Administration) regulations.
- Anti-Static Properties: Static electricity can pose a significant risk in mining operations, potentially igniting flammable materials. Anti-static conveyor belts help dissipate static charges, reducing the risk of explosions.
- Durability and Robustness: Conveyor belts should be robust enough to withstand the harsh conditions of mining, including exposure to abrasive materials, extreme temperatures, and heavy loads. Durable belts reduce the likelihood of accidents caused by belt failure.
- Compliance with International Standards: Ensure the conveyor belt complies with international safety standards such as ISO, DIN, and ASTM. These standards provide guidelines for the construction, performance, and safety of conveyor belts.
- Regular Safety Audits: Choose suppliers who conduct regular safety audits and inspections to ensure their products meet safety standards. Regular audits help identify potential risks and ensure continuous compliance with safety regulations.
Tips on Maintenance Practices to Prolong the Life of Gold Mining Conveyor Belts
Proper maintenance practices are essential to prolong the life of a gold mining conveyor belt and ensure its efficient operation.
Regular Inspections:
- Conduct regular visual and technical inspections of the conveyor belt to identify signs of wear, damage, or misalignment. Inspections should include checking the belt surface, splices, pulleys, and rollers.
- Use advanced monitoring systems to detect issues such as belt slippage, abnormal vibrations, and temperature variations. Early detection of problems can prevent major failures and costly downtime.
Proper Belt Tensioning:
- Maintain the correct tension in the conveyor belt to ensure smooth operation. Over-tensioning can cause excessive wear on the belt and components, while under-tensioning can lead to slippage and misalignment.
- Use tensioning systems and regularly check and adjust the tension according to the manufacturer’s recommendations.
Lubrication and Cleaning:
- Regularly lubricate the moving parts of the conveyor system, such as bearings, pulleys, and rollers, to reduce friction and wear. Use the appropriate lubricants recommended by the manufacturer.
- Keep the conveyor belt and surrounding areas clean to prevent the accumulation of dirt, debris, and material spillage. Regular cleaning reduces the risk of belt damage and improves overall efficiency.
Belt Alignment:
- Ensure the conveyor belt is properly aligned to prevent uneven wear and potential damage. Misalignment can cause the belt to rub against the structure, leading to fraying and tears.
- Use alignment tools and regularly inspect the belt tracking to make necessary adjustments. Proper alignment also reduces energy consumption and extends the life of the belt.
Splice Maintenance:
- Regularly inspect and maintain belt splices, as they are critical points that can weaken over time. Ensure splices are correctly installed and periodically check for signs of wear or separation.
- Use high-quality splice materials and follow best practices for splicing techniques to ensure strong and durable connections.
Maintaining the safety and longevity of a gold mining conveyor belt requires a commitment to adhering to safety standards and implementing effective maintenance practices. By selecting conveyor belts that meet recognized safety standards and conducting regular inspections, tensioning, lubrication, alignment, and splice maintenance, mining operations can ensure the efficient and safe operation of their conveyor systems. Proper maintenance not only extends the life of the conveyor belt but also enhances productivity, reduces downtime, and minimizes the risk of accidents, ultimately contributing to the overall success and sustainability of mining operations.
Future Trends in Gold Mining Conveyor Belts
The gold mining industry continuously evolves, driven by the need for efficiency, safety, and sustainability. The gold mining conveyor belt, a critical component in these operations, is also subject to advancements and innovations. Future trends in conveyor belt technology promise to enhance the performance and reliability of mining operations. This section explores predicted technological advancements and material innovations, and how these trends could further optimize gold mining operations.
Predictions on Technological Advancements and Material Innovations in Conveyor Belt Manufacturing
Smart Conveyor Belts with IoT Integration:
- Technology: The integration of the Internet of Things (IoT) into conveyor belts is set to revolutionize monitoring and maintenance processes. Smart conveyor belts equipped with sensors can provide real-time data on belt performance, wear, and tear, enabling predictive maintenance and reducing downtime.
- Example: Sensors embedded in the belt can monitor tension, temperature, and vibration, sending data to a central system for analysis. This helps in identifying potential issues before they lead to failures.
Advanced Materials for Enhanced Durability:
- Technology: The development of new materials such as graphene-enhanced composites and ultra-high molecular weight polyethylene (UHMWPE) can significantly improve the durability and longevity of conveyor belts.
- Example: Graphene, known for its exceptional strength and lightness, can be used to create conveyor belts that are both lightweight and extremely resistant to abrasion and impact, reducing the frequency of replacements.
Energy-Efficient Conveyor Belt Systems:
- Technology: Innovations aimed at reducing energy consumption are becoming increasingly important. Conveyor belts with energy-saving features such as low rolling resistance and optimized motor efficiency can lower operational costs and environmental impact.
- Example: Low rolling resistance belts use special compounds that reduce the friction between the belt and the rollers, decreasing energy usage and extending the life of the belt.
Automated and Autonomous Conveyor Systems:
- Technology: The future of conveyor belts in gold mining includes automation and the use of autonomous systems. Automated conveyor belts can adjust their speed, loading, and unloading processes based on real-time data, improving efficiency and throughput.
- Example: Autonomous conveyor systems can operate with minimal human intervention, using advanced algorithms and machine learning to optimize material handling and reduce operational errors.
Eco-Friendly and Sustainable Belt Materials:
- Technology: The shift towards sustainability is driving the development of eco-friendly conveyor belts made from recyclable and biodegradable materials. These belts not only perform well but also reduce the environmental footprint of mining operations.
- Example: Conveyor belts made from biodegradable polymers or recycled materials can be used in mining operations, reducing waste and promoting environmental sustainability.
How These Trends Could Further Optimize Gold Mining Operations
The advancements and innovations in gold mining conveyor belts will have a profound impact on the efficiency, safety, and sustainability of mining operations.
Enhanced Operational Efficiency:
- Smart conveyor belts with IoT integration will enable real-time monitoring and predictive maintenance, reducing downtime and ensuring continuous operation. This leads to higher productivity and more efficient use of resources.
- Automated and autonomous systems can optimize material handling processes, ensuring that ore is transported more quickly and accurately, reducing delays and increasing throughput.
Increased Safety:
- Advanced materials that enhance durability and resistance to wear will reduce the risk of belt failures and accidents, ensuring a safer working environment for miners.
- Real-time monitoring systems can detect potential issues before they become serious problems, allowing for proactive maintenance and reducing the risk of accidents caused by sudden belt failures.
Cost Savings:
- Energy-efficient conveyor belts can significantly reduce energy consumption, lowering operational costs and making mining operations more economically viable.
- The use of durable and advanced materials will extend the lifespan of conveyor belts, reducing the frequency and cost of replacements and maintenance.
Sustainability and Environmental Impact:
- Eco-friendly and sustainable belt materials will help mining companies reduce their environmental footprint, promoting more sustainable mining practices.
- The reduction in energy consumption and the use of recyclable materials contribute to the overall sustainability goals of the mining industry.
Adaptability and Flexibility:
- Innovations in material and design will allow conveyor belts to be more adaptable to various mining conditions and requirements. This flexibility ensures that belts can be customized to meet specific operational needs, enhancing overall efficiency.
- Autonomous systems can adapt to changes in the mining environment, adjusting operations in real-time to maintain optimal performance and efficiency.
The future of gold mining conveyor belts is bright, with numerous technological advancements and material innovations on the horizon. These trends will significantly enhance the efficiency, safety, and sustainability of mining operations. By embracing smart technologies, advanced materials, energy-efficient systems, automation, and eco-friendly practices, the gold mining industry can look forward to a future where conveyor belts play an even more critical role in optimizing operations and achieving long-term success.
FAQs About Gold Mining Conveyor Belt
In mining, several types of conveyor belts are used to transport materials efficiently and safely. The most common types include:
Steel Cord Conveyor Belts: Known for their high tensile strength, these belts are reinforced with steel cords, making them ideal for transporting heavy loads over long distances. They are durable and resistant to impact and abrasion.
Textile Conveyor Belts: These belts are reinforced with fabric materials such as polyester, nylon, or cotton. They are flexible, cost-effective, and suitable for short to medium distances. Textile belts are often used for less demanding applications within the mining site.
Chevron Conveyor Belts: Featuring a unique V-shaped pattern, these belts provide additional grip and are used for transporting materials up steep inclines. They are effective in wet and slippery conditions, preventing material rollback.
Heat-Resistant Conveyor Belts: Designed to withstand high temperatures, these belts are made from materials that can endure extreme heat, making them suitable for areas near processing equipment or where ore is heated.
Pipe Conveyor Belts: These belts form a pipe-like shape during operation, enclosing the transported material to protect it from external conditions and prevent spillage. They are ideal for dusty environments and transporting sensitive materials.
The longest conveyor belt on Earth is the Bou Craa conveyor belt in Western Sahara. It is used to transport phosphate from the Bou Craa mine to the port city of El Aaiun. This conveyor belt stretches approximately 98 kilometers (61 miles) across the desert. It was built in the 1970s and has been in continuous operation since then.
The Bou Craa conveyor belt is a remarkable feat of engineering. It consists of a series of interconnected belts that transport large quantities of phosphate rock efficiently and continuously. The conveyor system helps in reducing the need for traditional transportation methods such as trucks, which are less efficient and more environmentally damaging.
This conveyor belt’s immense length and continuous operation highlight the importance of conveyor systems in modern mining operations. They play a crucial role in improving efficiency, reducing transportation costs, and minimizing environmental impact by providing a reliable and sustainable means of moving materials over long distances.
Gold separation in mining involves several processes designed to extract the precious metal from ore. The most common methods include:
Gravity Separation: This technique leverages the difference in density between gold and other minerals. Miners use equipment like shaking tables, jigs, and spirals to separate gold particles from the surrounding material. Gravity separation is effective for coarse gold particles and is often the first step in the extraction process.
Flotation: This method involves adding chemicals to a slurry of ground ore. The chemicals cause gold to become hydrophobic (repelled by water) and attach to air bubbles, which rise to the surface and form a froth that can be skimmed off. Flotation is effective for fine gold particles and complex ores.
Cyanidation: One of the most widely used methods, cyanidation involves dissolving gold from ore using a cyanide solution. The gold-cyanide complex is then adsorbed onto activated carbon or precipitated from the solution. The gold is subsequently recovered through smelting or other refining processes.
Heap Leaching: In this process, ore is piled into large heaps and sprayed with a cyanide solution. The solution percolates through the heap, dissolving gold as it moves. The gold-laden solution is collected at the base and processed to recover the metal.
Amalgamation: Historically, mercury was used to extract gold by forming an amalgam with the metal. This method is now largely obsolete due to environmental and health concerns.
The thickness of a mining conveyor belt varies depending on its application and the specific requirements of the mining operation. Generally, mining conveyor belts range in thickness from 1/4 inch (6 mm) to over 1 inch (25 mm).
Light-Duty Belts: These belts, typically used for less demanding applications or lighter loads, have a thickness of around 1/4 inch (6 mm) to 3/8 inch (9.5 mm). They are suitable for short distances and lower load capacities.
Medium-Duty Belts: Commonly used in standard mining operations, medium-duty belts range from 3/8 inch (9.5 mm) to 1/2 inch (12.7 mm) in thickness. These belts offer a balance between strength and flexibility, making them suitable for various material handling tasks.
Heavy-Duty Belts: Designed for the most demanding applications, heavy-duty belts can be 1/2 inch (12.7 mm) to over 1 inch (25 mm) thick. These belts are reinforced with multiple layers of fabric or steel cords, providing exceptional durability and resistance to impact and abrasion.
The specific thickness required for a mining conveyor belt depends on factors such as the type of material being transported, the load capacity, the distance of transportation, and the environmental conditions. Proper selection of belt thickness ensures optimal performance, longevity, and safety in mining operations.
Last Updated on May 31, 2024 by Jordan Smith
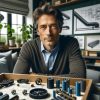
Jordan Smith, a seasoned professional with over 20 years of experience in the conveyor system industry. Jordan’s expertise lies in providing comprehensive solutions for conveyor rollers, belts, and accessories, catering to a wide range of industrial needs. From initial design and configuration to installation and meticulous troubleshooting, Jordan is adept at handling all aspects of conveyor system management. Whether you’re looking to upgrade your production line with efficient conveyor belts, require custom conveyor rollers for specific operations, or need expert advice on selecting the right conveyor accessories for your facility, Jordan is your reliable consultant. For any inquiries or assistance with conveyor system optimization, Jordan is available to share his wealth of knowledge and experience. Feel free to reach out at any time for professional guidance on all matters related to conveyor rollers, belts, and accessories.