Gravel Conveyor Belt for Rock, Sand, Dirt and Gravel
Conveyor belts play a crucial role in the efficient handling of bulk materials, with gravel conveyor belt standing out as key components in construction and landscaping projects.Gravel conveyor belt transport sand, gravel, rock, ore, Ideal for demanding applications, ensure reliability and efficiency. These belts are designed to transport gravel, a fundamental material used widely in building roads, creating foundations, and enhancing landscapes. The aim of this post is to delve into the specifics of heavy-duty gravel conveyor belts, examining their prices, manufacturers, and the critical design considerations that influence their performance and durability. By focusing on gravel conveyor belts, we aim to provide valuable insights into how these specialized conveyor systems can optimize the handling of gravel, ensuring it is moved efficiently and effectively to meet the high demands of construction and landscaping projects.
What is Gravel Conveyor Belt
Gravel conveyor belts are integral to the construction and landscaping industries, designed specifically for the efficient transport of gravel. These systems are pivotal in moving gravel over both short and long distances, ensuring that materials are delivered where they are needed most, with minimal loss and maximum efficiency. Here, we delve deeper into the essence and functionality of gravel conveyor belts.
Defining Gravel Conveyor Belts and Their Role
- Efficiency in Transport: Gravel conveyor belts excel in moving vast amounts of gravel quickly, surpassing traditional methods in both speed and efficiency. This capability is crucial in keeping up with the high demands of construction projects.
- Versatility Across Distances: Whether it’s moving gravel across a construction site or transporting it from a quarry to a project location, these belts are designed to cover both short and long distances effectively.
- Adaptability to Terrain: Gravel conveyor belts are engineered to navigate various terrains, including steep inclines and declines, making them adaptable to different environmental conditions.
- Continuous Operation: Designed for continuous use, these belts can operate for extended periods without interruption, ensuring a steady supply of gravel.
- Cost Reduction: By automating the transport of gravel, these conveyor belts significantly reduce labor costs and operational expenses.
- Customization and Scalability: Gravel conveyor belts can be customized in size, belt material, and design to meet specific project requirements, offering scalability to operations of any size.
Characteristics Suitable for Handling Abrasive Materials
Gravel, by nature, is abrasive, necessitating specific features in conveyor belts to handle it effectively:
- Durability: Constructed from wear-resistant materials, gravel conveyor belts are built to withstand the abrasive nature of gravel, ensuring longevity and reliability.
- High Tensile Strength: These belts are designed with high tensile strength to support the heavy load of gravel without stretching or breaking.
- Abrasion Resistance: The surface material of the belt is specifically chosen for its ability to resist abrasion, protecting the belt from the rough texture of gravel.
- Low Maintenance Needs: Despite the demanding conditions, gravel conveyor belts are designed for easy maintenance, ensuring they remain operational with minimal downtime.
- Flexibility: The belts are flexible enough to accommodate varying sizes of gravel, ensuring efficient transport without clogging or spillage.
- Impact Resistance: Engineered to absorb the impact of gravel being loaded onto the belt, these systems minimize wear and tear, extending the belt’s service life.
- Environmental Resilience: Gravel conveyor belts are often exposed to outdoor conditions; thus, they are made to be resistant to UV rays, temperature fluctuations, and moisture, ensuring consistent performance regardless of the weather.
Understanding gravel conveyor belts through these detailed points highlights their indispensable role in efficiently handling and transporting gravel, a critical material in construction and landscaping projects. Their design and features make them uniquely suited to the task, ensuring that gravel can be moved effectively, safely, and economically.

Comprehensive Analysis of Gravel Conveyor Belt Types
Gravel conveyor belts are pivotal in the construction, mining, and landscaping industries for their efficiency in moving bulk materials. These specialized belts are designed to handle the abrasive nature of gravel, ensuring minimal loss and maximum productivity. Below, we delve into the different types of gravel conveyor belts, comparing their workings, design, and applications in a detailed table, followed by an exploration of their advantages.
Detailed Comparison of Gravel Conveyor Belt Types
To delve deeper into the specifics of gravel conveyor belt systems, it’s crucial to examine the distinct types available and how they are engineered to meet the demands of transporting gravel efficiently. These systems vary widely in their design, functionality, and application, each tailored to optimize the handling of gravel across different environments and operational scales. The following table offers a comprehensive comparison, shedding light on the unique attributes and operational mechanisms of each conveyor belt type. This analysis aims to provide a clearer understanding of their roles in facilitating the movement of gravel, highlighting the technological innovations and design considerations that make them indispensable in their respective fields.
Advantages and Benefits of Conveyor Belts for Gravel Handling
Below, we explore the key advantages and benefits that conveyor belts offer in the context of gravel handling, highlighting how these systems contribute to the overarching goals of reducing costs, enhancing safety, and minimizing environmental impact in industrial and construction settings.
- Efficiency: Conveyor belts significantly reduce the time and effort required to move large volumes of gravel, increasing overall productivity.
- Cost-Effectiveness: Despite the initial investment, conveyor belts offer long-term savings on labor and transportation costs.
- Safety: Automated gravel transport minimizes the need for manual handling, reducing the risk of injuries on the worksite.
- Environmental Protection: Enclosed systems like the Tube Belt Conveyor and Beumer Pipe Conveyor minimize dust emissions and spillage, protecting the surrounding environment.
- Versatility: A wide range of conveyor belt types ensures there is a solution for every application, from short-distance transport within a site to long-distance transport between locations.
- Durability: Designed to withstand the abrasive nature of gravel, these belts are built for longevity, reducing the need for frequent replacements.
- Customization: Conveyor belts can be tailored to specific project needs, including length, width, and operational speed, ensuring optimal handling of gravel.
- Reduced Material Loss: Enclosed and trough designs significantly decrease the amount of material lost during transport, ensuring more gravel reaches its intended destination.
- Adaptability: Conveyor systems can be designed to navigate complex terrains, including steep inclines and tight curves, offering solutions where traditional transport methods fall short.
Gravel conveyor belts are essential tools in the efficient handling and transportation of gravel. Their design and operational advantages make them invaluable in industries where bulk material handling is a routine necessity. By choosing the appropriate type of conveyor belt, businesses can achieve optimal efficiency, safety, and cost-effectiveness in their operations.
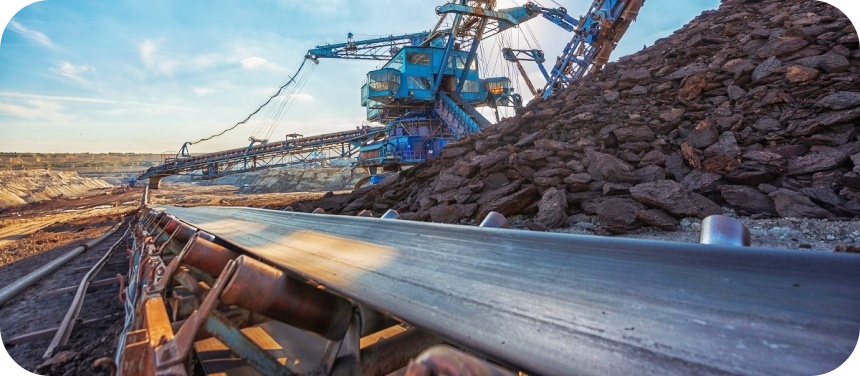
Design Considerations for Gravel Conveyor Belt Systems
When designing gravel conveyor systems, several critical considerations ensure the chosen solution meets the specific needs of handling gravel efficiently and sustainably. Among the various types of conveyor systems available, pipe conveyors have emerged as a particularly suitable option for gravel due to their unique design and operational benefits. Additionally, the customization of conveyor systems plays a vital role in achieving optimal performance, tailored to the specific requirements of each project.
Pipe Conveyor Design
Pipe conveyors offer a distinctive approach to handling gravel, encapsulating the material fully and providing significant advantages over traditional conveyor belt systems:
- Enclosed System: The design minimizes material spillage and dust emissions, crucial for environmental protection and operational safety.
- Reduced Environmental Impact: By containing the gravel, pipe conveyors prevent contamination of surrounding areas, making them ideal for sensitive environments.
- Versatility in Routing: Their ability to navigate tight curves and steep inclines allows for more flexible route planning, reducing the need for transfer points.
- Protection of Material: Enclosing the gravel protects it from the elements, reducing moisture content variability and ensuring quality.
- Energy Efficiency: Modern pipe conveyors are designed for energy efficiency, with reduced power consumption compared to traditional conveyor systems.
- Low Maintenance: The enclosed design protects the conveyor’s moving parts, leading to lower maintenance costs and longer service life.
- High Capacity: Pipe conveyors can be designed to handle a high volume of gravel, making them suitable for large-scale operations.
Custom Solutions
The importance of custom conveyor designs cannot be overstated, as they ensure that each system is perfectly aligned with the project’s specific needs. Here are seven points highlighting the significance of customization:
- Tailored Capacity: Custom designs allow for the conveyor system to be optimized for the expected volume of gravel, ensuring efficient handling without overburdening the system.
- Specific Material Characteristics: Gravel varies in size, abrasiveness, and moisture content. Custom solutions can accommodate these variations, enhancing durability and efficiency.
- Adaptability to Terrain: Custom-designed systems can be created to fit the unique topography of a project site, minimizing the need for extensive site modification.
- Integration with Existing Systems: Custom conveyors can be designed to seamlessly integrate with existing material handling systems, improving overall operational flow.
- Innovative Features: Manufacturers like Beumer and Kase Conveyors offer innovative features such as advanced monitoring and control systems, improving reliability and performance.
- Compliance with Regulations: Custom designs can ensure compliance with local and international environmental and safety regulations, avoiding potential legal issues.
- Future-Proofing: By considering future expansion or changes in operational needs, custom conveyor systems can be designed for adaptability, protecting the investment over the long term.
Manufacturers like Beumer Group and Kase Conveyors exemplify the benefits of custom conveyor solutions, offering systems that are not only tailored to the specific needs of handling gravel but also incorporate the latest technology and design principles for maximum efficiency and sustainability. These considerations are crucial for any project looking to invest in a gravel conveyor belt system, ensuring that it delivers on both performance and environmental responsibility.
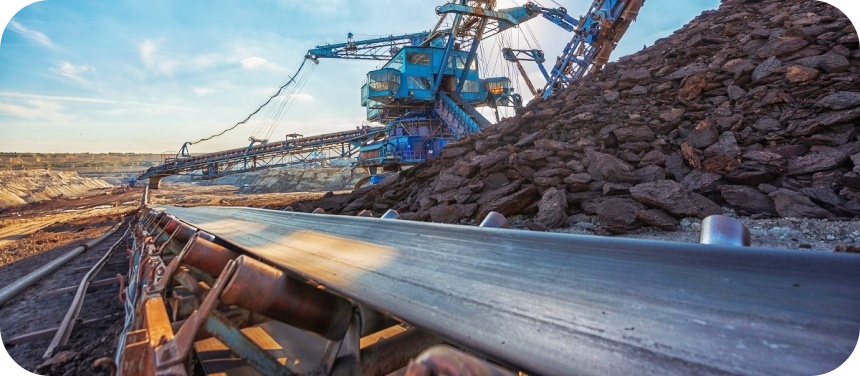
Cost Considerations for Gravel Conveyor Belt
When investing in a gravel conveyor belt system, understanding the cost implications is crucial for budgeting and financial planning. The initial purchase price is just the beginning; the total cost of ownership, which includes maintenance, operation, and potential downtime, also plays a significant role in the financial considerations. Below, we explore the key cost considerations associated with gravel conveyor belts.
Bulk Conveyor Belt Price
The price of gravel conveyor belts can vary widely based on several factors. Here are the main elements that influence the cost:
- Length and Width: The size of the conveyor belt significantly affects the price. Longer and wider belts require more material to manufacture, increasing the cost.
- Design Complexity: Custom features or designs tailored to specific operational needs can add to the cost. Advanced systems with curves, inclines, or integrated technology are typically more expensive.
- Material Quality: Conveyor belts made with high-grade, durable materials designed to withstand the abrasive nature of gravel cost more but offer better longevity and reduced maintenance needs.
- Brand and Manufacturer: Premium brands or manufacturers known for their quality and service may charge more for their conveyor belts.
- Installation Requirements: The complexity of the installation process, including the need for specialized labor or equipment, can impact the overall cost.
- Transportation and Delivery: The cost of shipping the conveyor belt system to the site can also add to the overall expense, especially for long distances or difficult-to-access locations.
Total Cost of Ownership
Beyond the initial purchase price, several long-term costs are associated with owning and operating a gravel conveyor belt:
- Maintenance and Repairs: Regular maintenance is essential to keep the conveyor belt in optimal condition, and repairs may be necessary for wear and tear or unexpected breakdowns. High-quality belts may have lower maintenance costs over time.
- Operation Costs: The energy consumption required to operate the conveyor belt can vary, with more efficient designs offering cost savings in the long term.
- Downtime: Unplanned downtime due to breakdowns or maintenance can lead to significant financial losses due to halted operations. Investing in a reliable conveyor belt system can minimize these risks.
- Replacement Parts: Over time, parts of the conveyor system may need to be replaced, such as rollers, bearings, or the belt itself. The availability and cost of these parts can affect the total cost of ownership.
- Lifespan: The durability and expected lifespan of the conveyor belt play a crucial role in its overall cost-effectiveness. A more expensive belt that lasts longer may offer better value than a cheaper option that requires frequent replacement.
- Resale Value: Should the conveyor belt system no longer be needed, its potential resale value can offset some of the initial investment costs.
Understanding these cost considerations is essential for anyone looking to invest in a gravel conveyor belt system. By considering both the initial purchase price and the total cost of ownership, businesses can make informed decisions that align with their operational needs and financial constraints, ensuring a cost-effective solution for their gravel handling requirements.

How to Choose the Right Gravel Conveyor Belt
Selecting the appropriate gravel conveyor belt for your operation is crucial to ensuring efficiency, safety, and cost-effectiveness. The right conveyor belt not only handles the specific demands of gravel transportation but also aligns with operational goals and environmental considerations. Below, we delve into the essential factors to consider when choosing a gravel conveyor belt, followed by a comparison of new versus used conveyor belts.
Factors to Consider
- Material Characteristics: Understanding the abrasiveness, size, and weight of the gravel is crucial. Conveyor belts designed for heavy, abrasive materials are essential for durability and longevity.
- Conveyor Length: The distance over which the gravel needs to be transported affects the type of conveyor belt needed. Longer distances may require belts with higher strength and durability.
- Environmental Considerations: Factors such as exposure to weather, temperature variations, and potential environmental impact (e.g., dust emissions) influence the choice of conveyor belt. Enclosed systems may be necessary in sensitive areas.
- Throughput Requirements: The volume of gravel that needs to be moved per unit of time dictates the capacity the conveyor belt must support. Higher throughput rates may necessitate wider or faster conveyor belts.
- Operational Demands: Consider the operational environment, including the terrain and the need for mobility. Fixed or portable systems each have their advantages depending on the project’s scope.
- Budget Constraints: The cost of the conveyor belt system, including initial purchase, installation, and maintenance, must align with the project’s budget. Operational efficiency and potential downtime costs should also be considered.
New vs. Used Bulk Conveyor Belt: Pros and Cons
Choosing between a new and used gravel conveyor belt involves weighing the immediate financial savings against the potential for increased operational costs and downtime. Factors such as the project’s duration, the criticality of the conveyor belt to ongoing operations, and the availability of spare parts for older models should also be considered. Ultimately, the decision should align with the project’s specific needs, budget, and long-term operational goals.
Key Manufacturers and Brands of Gravel Conveyor Belt
The gravel conveyor belt industry is supported by a robust network of manufacturers and brands, each contributing significantly to advancements in material handling technologies. These entities specialize in developing solutions that cater to the rigorous demands of transporting gravel and other bulk materials, ensuring efficiency, durability, and environmental compliance. Below, we explore the key players in this sector, detailing their offerings and impact on the gravel conveying landscape.
GRAM Conveyor
GRAM Conveyor Renowned for their high-quality belts and extensive industry experience, GRAM Conveyor offers a wide range of products suitable for various applications.Their key features include:
- Durability: Produces belts that are highly resistant to abrasion and wear, ideal for transporting abrasive materials like gravel.
- Innovative Technology: Incorporates advanced technologies to improve conveyor belt performance and lifespan.
- Global Operations: With a strong international presence, SKE supports projects worldwide, ensuring global standards in quality and service.
- Environmental Commitment: Focuses on reducing environmental impact through dust control and energy-efficient designs.
- Comprehensive Support: Offers end-to-end services from consultation and design to installation and after-sales support.
- Quality Assurance: Adheres to strict quality standards, ensuring that their products consistently meet or exceed industry expectations.
Beumer Group
Beumer Group is renowned for its comprehensive range of material handling solutions, particularly in the realm of gravel and bulk materials. Key highlights include:
- Innovative Solutions: Specializes in advanced conveyor systems like the Beumer Pipe Conveyor, ideal for long-distance gravel transport.
- Environmental Focus: Offers systems designed to minimize dust emissions and material spillage, aligning with sustainability goals.
- Global Presence: With a worldwide network, Beumer Group supports global projects with localized service and support.
- Custom Engineering: Provides tailor-made conveyor solutions to meet specific project requirements, ensuring optimal handling of gravel.
- Industry Leadership: Recognized for pushing the boundaries of material handling technology with continuous research and development.
Kase Conveyors
Kase Conveyors stands out for its expertise in belt conveying systems that efficiently manage gravel transportation. Their strengths are highlighted as follows:
- Custom Design: Engineers conveyor systems that are specifically designed to handle the abrasive nature of gravel.
- Versatility: Offers a wide range of conveyor types, including trough belt conveyors, to suit various material handling needs.
- Durability: Focuses on building long-lasting conveyor systems that can withstand the rigors of gravel handling.
- Expertise: Boasts extensive experience in providing solutions for both small-scale and large-scale gravel handling projects.
- Support Services: Provides comprehensive customer support, from design through to installation and maintenance.
ContiTech
A division of Continental AG, ContiTech is known for its high-performance conveyor belts that are specifically engineered for the demanding conditions of gravel handling. Their strengths are:
- Technological Leadership: Leverages cutting-edge technology to improve conveyor belt performance and lifespan.
- Wide Range: Offers a diverse portfolio of conveyor belts to suit various applications and industries.
- Sustainability: Emphasizes eco-friendly production processes and materials, aligning with environmental conservation efforts.
- Global Network: Benefits from Continental AG’s extensive global network, providing accessible support and service worldwide.
Fenner Dunlop
Fenner Dunlop specializes in conveyor belting for mining and industrial applications, making it a go-to source for gravel handling solutions. Their highlights include:
- Heavy-Duty Products: Known for their heavy-duty conveyor belts that offer exceptional durability and performance in abrasive conditions.
- Custom Engineering: Provides tailor-made belting solutions that meet the specific needs of gravel handling operations.
- Industry Expertise: Brings decades of experience in the conveyor belt industry, ensuring high-quality products and services.
- Safety Focus: Prioritizes safety in all product designs, contributing to safer work environments in the industries they serve.
- Global Presence: With manufacturing and service locations around the world, Fenner Dunlop ensures reliable access to their products and expertise.
Flexco
Flexco is recognized for its comprehensive range of belt maintenance tools and conveyor accessories that enhance the operation of gravel conveyor belts. Their contributions are:
- Maintenance Solutions: Offers innovative products designed to keep conveyor belts running smoothly and efficiently.
- Operational Efficiency: Focuses on solutions that reduce downtime and increase productivity for gravel handling operations.
- Safety Products: Provides a variety of safety tools and accessories to improve workplace safety around conveyor systems.
- Global Support: With a global distribution network, Flexco ensures that customers have access to their products and expertise wherever they operate.
These manufacturers collectively enrich the gravel conveyor belt industry with their specialized solutions, ensuring that businesses have access to a wide range of options to meet their material handling needs. Their commitment to innovation, quality, and customer service continues to drive advancements in gravel transportation technologies.
Looking for reliable conveyor belts? Contact us now!

Replacement Parts for Gravel Conveyor Belt
Gravel conveyor belts are essential components in industries like mining, construction, and agriculture. Ensuring their efficient operation requires regular maintenance and timely replacement of worn-out parts. Here are some key replacement parts for gravel conveyor belts:
1. Conveyor Belt
- Description: The primary moving part made from durable materials like rubber or synthetic polymers.
- Function: Transports gravel and other materials from one point to another.
- Replacement Indicators: Cracks, tears, fraying edges, or significant wear.
2. Rollers and Idlers
- Description: Cylindrical components that support and guide the conveyor belt.
- Function: Reduce friction and support the weight of the material being transported.
- Replacement Indicators: Excessive wear, abnormal noises, or visible damage.
3. Pulleys
- Description: Rotating components around which the conveyor belt loops.
- Function: Drive and redirect the conveyor belt.
- Replacement Indicators: Worn grooves, slippage, or uneven rotation.
4. Bearings
- Description: Mechanical components that reduce friction between moving parts.
- Function: Ensure smooth rotation of rollers and pulleys.
- Replacement Indicators: Increased vibration, noise, or overheating.
5. Motors and Drives
- Description: Power sources that drive the conveyor belt.
- Function: Provide the necessary force to move the belt and the transported material.
- Replacement Indicators: Reduced power, overheating, or failure to start.
6. Scrapers and Cleaners
- Description: Devices that remove debris and material buildup from the belt.
- Function: Maintain belt cleanliness and prevent material carryback.
- Replacement Indicators: Ineffective cleaning, excessive material buildup, or wear on cleaning blades.
7. Skirting and Seals
- Description: Components that prevent material spillage at transfer points.
- Function: Contain material on the belt and minimize dust and spillage.
- Replacement Indicators: Visible gaps, spillage, or deterioration of the material.
8. Belt Fasteners and Splices
- Description: Connectors that join the ends of the conveyor belt.
- Function: Ensure a continuous loop for the conveyor belt.
- Replacement Indicators: Weak or broken connections, misalignment, or visible wear.
9. Tensioners
- Description: Devices that maintain proper belt tension.
- Function: Prevent belt slippage and ensure smooth operation.
- Replacement Indicators: Belt slack, uneven belt movement, or difficulty in maintaining tension.
10. Impact Beds and Cradles
- Description: Support structures at loading points to absorb impact.
- Function: Protect the belt from damage due to heavy loading.
- Replacement Indicators: Visible damage, excessive wear, or insufficient impact absorption.
Regular inspection and timely replacement of these key components can significantly enhance the longevity and efficiency of gravel conveyor belts, ensuring smooth and uninterrupted operations in various industrial applications.
FAQs about Gravel Conveyor Belt
An alternative to a conveyor belt is a pneumatic conveying system. This system uses air pressure or vacuum to transport bulk materials through pipelines. Pneumatic conveyors are particularly advantageous for moving fine, granular, or powdery materials over long distances and through complex routes where traditional conveyor belts might not be feasible. They offer flexibility in routing, reduced maintenance due to fewer moving parts, and the ability to transport materials in a closed system, which minimizes contamination and dust. Other alternatives include screw conveyors, which use a rotating helical screw blade to move materials within a tube, and bucket elevators, which lift materials vertically using a series of buckets attached to a belt or chain. Each of these alternatives is chosen based on specific application requirements, material characteristics, and the nature of the industrial process involved.
The three types of conveyors commonly used in industries are belt conveyors, roller conveyors, and chain conveyors. Belt conveyors consist of a continuous belt looped over pulleys, ideal for moving bulk materials and products over long distances in manufacturing and processing industries. Roller conveyors use cylindrical rollers to transport items and are often used in warehouses and distribution centers for sorting and moving packages. They can be powered or gravity-driven, depending on the application. Chain conveyors utilize chains to move heavy or bulky items, making them suitable for applications such as automotive assembly lines and heavy equipment manufacturing. Each type of conveyor serves a specific purpose based on the materials being handled, the required speed of movement, and the environmental conditions of the operation, ensuring efficient and effective material handling solutions in various industries.
The average price of a conveyor belt varies widely depending on factors such as the type of conveyor belt, the materials used in its construction, its size, and the specific requirements of the application. Generally, a standard flat belt conveyor can range from $1,000 to $5,000 for a basic model. For more specialized or heavy-duty conveyor belts, such as those used in mining or high-temperature environments, the cost can be significantly higher, ranging from $10,000 to $50,000 or more. Custom-designed conveyor systems tailored to specific industrial needs can further increase the price. Additionally, the total cost of ownership includes not only the initial purchase price but also installation, maintenance, and potential downtime costs. Therefore, when budgeting for a conveyor belt, it’s essential to consider the specific operational needs and long-term costs associated with its use.
A skid conveyor is a type of conveyor system designed to transport large, heavy items, typically within manufacturing and assembly processes. Instead of using a continuous belt or roller system, a skid conveyor moves items on skids or pallets, providing a stable platform for transporting bulky goods. This type of conveyor is commonly used in automotive manufacturing, where it facilitates the movement of car bodies and other heavy components through various stages of assembly. Skid conveyors can be either floor-mounted or overhead and can be designed to move skids linearly or through complex paths. They offer advantages in handling large and heavy items, maintaining precise positioning, and integrating easily with robotic and automated systems for seamless production workflows. Their robust construction and ability to handle significant loads make them essential in industries where durability and reliability are paramount.
Last Updated on July 23, 2024 by Jordan Smith
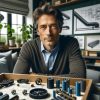
Jordan Smith, a seasoned professional with over 20 years of experience in the conveyor system industry. Jordan’s expertise lies in providing comprehensive solutions for conveyor rollers, belts, and accessories, catering to a wide range of industrial needs. From initial design and configuration to installation and meticulous troubleshooting, Jordan is adept at handling all aspects of conveyor system management. Whether you’re looking to upgrade your production line with efficient conveyor belts, require custom conveyor rollers for specific operations, or need expert advice on selecting the right conveyor accessories for your facility, Jordan is your reliable consultant. For any inquiries or assistance with conveyor system optimization, Jordan is available to share his wealth of knowledge and experience. Feel free to reach out at any time for professional guidance on all matters related to conveyor rollers, belts, and accessories.