Gravity Conveyor Accessories And Conveyor Parts
In the realm of material handling, gravity conveyors stand out as a fundamental component, streamlining the transportation and processing of goods across various industries. These conveyors, leveraging the natural force of gravity, offer a cost-effective and efficient means to move items, particularly in warehousing and manufacturing settings. However, the true potential of these systems is unlocked through the integration of Gravity Conveyor Accessories. These accessories play a pivotal role in enhancing the functionality, safety, and efficiency of gravity conveyors. From guard rails that ensure product safety to modular components that adapt to different operational needs, Gravity Conveyor Accessories are indispensable in optimizing the performance of gravity conveyor systems. This introduction delves into the significance of gravity conveyors in material handling and explores the transformative impact of Gravity Conveyor Accessories on these essential systems.
Enhancing Operations with Gravity Conveyor Accessories
Gravity conveyors, integral to material handling, operate through a sequence of steps, each significantly optimized by Gravity Conveyor Accessories. Initially, items are placed onto the conveyor at a higher starting point. Due to the inclined angle, gravity pulls these items downwards, allowing them to glide across rollers or skate wheels. This movement is facilitated by the conveyor’s slope, which is carefully calibrated to ensure a steady flow of items. Gravity Conveyor Accessories, such as guide rails, stops, and transfer sections, play a crucial role in this process. They provide stability, control the speed of movement, and direct the items efficiently to their intended destination.
The importance of gravity conveyor systems in industrial applications is highlighted in several key areas:
- Warehousing and Distribution: Here, gravity conveyors expedite the movement of goods from storage to shipping areas. Gravity Conveyor Accessories like chutes and merges are essential for directing products smoothly between different sections of the warehouse.
- Manufacturing and Assembly Lines: In these settings, gravity conveyors facilitate the sequential assembly of products. Accessories such as side guides and lane dividers ensure that components stay aligned and move orderly through each assembly stage.
- Packaging and Sorting Facilities: Gravity conveyors streamline the packaging process by moving products between packing stations. Accessories like end stops and rotary tables aid in the efficient handling and orientation of packages.
- Loading and Unloading Areas: In these zones, gravity conveyors simplify the loading and unloading of goods from vehicles. The use of Gravity Conveyor Accessories, such as extendable conveyors, enhances flexibility and reduces manual labor.
In each of these applications, Gravity Conveyor Accessories not only improve the functionality and efficiency of gravity conveyors but also contribute to safer and more ergonomic working conditions. This makes them an indispensable component in a wide range of industrial settings.
Essential Gravity Conveyor Accessories
Gravity conveyor accessories are vital components that enhance the functionality, safety, and efficiency of gravity conveyor systems. These accessories ensure smooth operations in various industrial environments, from warehouses to manufacturing plants. Here, we will explore the essential gravity conveyor accessories, their purposes, and the different types available.
Guard Rails
Purpose and Benefits
- Ensure Inventory Security and Employee Safety: Guard rails are essential for preventing items from falling off the conveyor, thereby protecting inventory and ensuring the safety of employees working near the conveyor system. They create a barrier that keeps products securely on the conveyor path, reducing the risk of accidents and product loss.
Types Available
- Solid Guard Rails: These provide robust protection and are ideal for heavy-duty applications. Solid guard rails are constructed from durable materials that can withstand significant impact, making them suitable for environments with high traffic and heavy products.
- Angle and Adjustable Guard Rails: These offer flexibility in configuration and can be adjusted to accommodate different inventory sizes. They are perfect for operations that handle a variety of product dimensions, allowing easy modification to suit specific needs.
- Fixed-channel Gravity Conveyor Guard Rails: These guard rails provide consistent protection and are securely attached to the conveyor frame. They are designed to offer long-term durability and are often used in permanent installations where the conveyor layout remains unchanged.
Gravity Conveyor Stops
Purpose and Utility
- Control Product Flow and Stop Items at Specific Points: Gravity conveyor stops are used to manage the movement of items on the conveyor. They help in controlling product flow, ensuring that items stop at designated points for operations such as inspection, sorting, or packing.
Designs Available
- Angle Stops: Simple and cost-effective, angle stops are used for basic stopping needs. They are easy to install and can be placed at any point along the conveyor to halt items temporarily.
- Roller Stops: These use rollers to gently stop items, minimizing the risk of damage. Roller stops are ideal for handling delicate or fragile products that require careful handling.
- Butt-end Stops: Butt-end stops provide a firm stop at the end of the conveyor line. They are used to prevent items from rolling off the end of the conveyor, ensuring they remain on the line until manually removed.
- Manual and Air-operated Blade and Roller Stops: These stops offer more control and can be operated either manually or pneumatically. Manual stops are simple and reliable, while air-operated stops provide automated control for higher efficiency and precision.
Gravity Conveyor Supports
Purpose and Application
- Support Conveyors in Both Temporary and Permanent Installations: Gravity conveyor supports provide stability and support for the entire conveyor system. They ensure that the conveyor remains level and securely in place, which is crucial for safe and efficient operation.
Types of Supports
- Moveable Supports: These supports allow for easy relocation and reconfiguration of conveyor systems. They are ideal for flexible operations that may need to change layout frequently.
- Floor-mounted Supports: Floor-mounted supports offer sturdy, permanent installation options for heavy-duty use. They are fixed to the floor, providing a solid foundation for the conveyor system.
- Ceiling-hung Supports: Ceiling-hung supports save floor space and are ideal for environments with limited ground area. They suspend the conveyor from the ceiling, freeing up valuable floor space for other operations.
Ball Transfer Tables
Purpose and Uses
- Allow Manual Rotation and Transition of Heavy Items: Ball transfer tables enable easy movement and rotation of heavy items on the conveyor. They facilitate the manual handling of products, improving efficiency in various tasks.
Applications Include
- Ergonomics: Reducing the physical strain on workers by allowing them to move heavy items with less effort.
- Assembly Work: Facilitating multi-directional movement of parts during the assembly process.
- Pallet Building: Making it easier to position products accurately for palletizing.
- Kitting: Streamlining the process of assembling kits of products.
- Picking and Packing: Enhancing efficiency in the picking and packing processes.
Gravity Conveyor Gates
Types of Gate Assemblies
- Manual Lift Gate: A simple and cost-effective solution for creating a passageway through the conveyor line. It can be manually lifted to allow personnel or equipment to pass through.
- Hydraulic-powered Lift Gate: This gate assembly is powered by hydraulics, making it easier to lift and lower the gate with minimal effort. It is ideal for high-traffic areas where frequent access is required.
Features
- Efficiency in Personnel and Equipment Passthrough: Gravity conveyor gates provide a quick and efficient way for personnel and equipment to pass through the conveyor line without disrupting operations.
- Safety Latch to Lock the Raised Gate: For enhanced safety, these gates are equipped with a latch that locks the gate in the raised position, preventing accidental drops.
- Instructional Video for Hydraulic Lift Gate Assembly Installation: To assist with installation, hydraulic lift gates often come with instructional videos, ensuring proper setup and operation.
These gravity conveyor accessories are crucial for optimizing the performance, safety, and flexibility of gravity conveyor systems. By selecting the right accessories, businesses can ensure their conveyor systems meet their specific operational needs, enhancing overall productivity and safety.
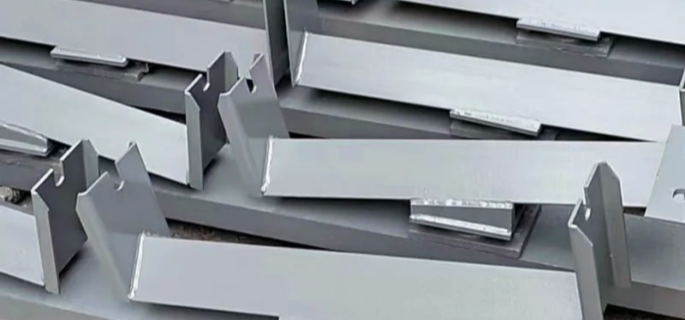
Optimizing with Essential Gravity Conveyor Accessories
In the efficient operation of gravity conveyors, the role of Gravity Conveyor Accessories is pivotal. These accessories not only enhance the functionality of the conveyors but also ensure safety and efficiency in material handling. Key accessories include Guard Rails, Gravity Conveyor Stops, and Gravity Conveyor Supports, each serving a specific purpose in the conveyor system.
1. Guard Rails: Guard Rails are crucial for safety and inventory management in gravity conveyor systems. They prevent items from falling off the conveyor, thereby reducing the risk of damage to goods and injury to workers. Guard Rails also help in guiding products smoothly along the conveyor, ensuring that items stay on track, especially around curves or steep inclines.
2. Gravity Conveyor Stops: The design and application of Gravity Conveyor Stops vary, catering to different operational needs. Here’s a breakdown of their types and applications:
Type of Stop | Description | Application |
Angle Stop | A simple, angled plate | Used for temporary stopping of items |
Roller Stop | Features a roller mechanism | Ideal for stopping and holding items before release |
Butt-End Stop | A solid end stop | Suitable for permanent stopping at the end of a conveyor line |
Manual Blade/Roller | Operated by hand | Used where manual control of stopping is needed |
Air-Operated Blade/Roller | Pneumatically controlled | For automated stopping, especially in high-volume settings |
3. Gravity Conveyor Supports: The selection of Gravity Conveyor Supports depends on the specific requirements of the application. The types include:
- Portable Tripod Stands: Best for temporary setups or where flexibility is needed.
- Stationary Supports: Ideal for permanent installations, providing robust and stable support.
- Ceiling-Mounted Supports: Used when floor space is limited, allowing conveyors to be suspended.
Each of these Gravity Conveyor Accessories plays a vital role in enhancing the functionality, safety, and efficiency of gravity conveyor systems. Their selection and integration should be based on the specific needs of the application, considering factors such as load capacity, conveyor length, and operational environment.
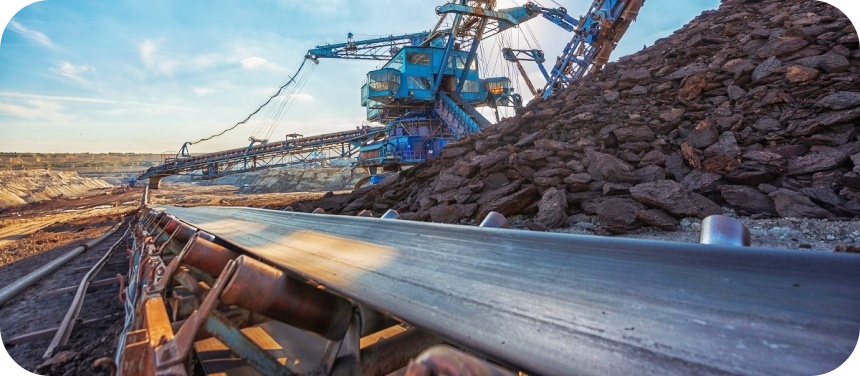
Enhancing Conveyor Functionality with Gravity Conveyor Accessories
The functionality of gravity conveyors can be significantly enhanced with the right Gravity Conveyor Accessories, each designed to meet specific operational needs. Key accessories in this regard include Ball Transfer Tables, Gravity Conveyor Gates, and considerations for Roller Spacing and Capacity.
1. Ball Transfer Tables: These tables are integral Gravity Conveyor Accessories, playing a crucial role in the manual rotation and transition of items across the conveyor system. Comprising a series of ball bearings mounted in a fixed housing, they allow goods to be redirected, rotated, or repositioned with minimal effort. This is particularly useful in assembly lines, packing stations, and sorting areas where multi-directional movement is required. Ball Transfer Tables facilitate a smooth transition of goods between different sections of the conveyor or to different processing points, enhancing overall efficiency and ergonomics.
2. Gravity Conveyor Gates: These gates are essential for providing access through conveyor lines. Gravity Conveyor Gates come in two main types: manual and hydraulic-powered lift gate assemblies. Manual gates are cost-effective and simple, requiring an operator to Manual gates in gravity conveyor systems require physical lifting, making them a practical choice for areas where access is infrequent. They are straightforward and cost-effective, but they do require manual effort to operate. In contrast, hydraulic-powered gates are designed for ease and convenience, particularly suited for areas with high traffic. Operated with a simple lever or button, these gates can be effortlessly raised or lowered. This feature facilitates quick and seamless movement of personnel or equipment across conveyor lines, streamlining the workflow in busier environments.
3. Roller Spacing and Capacity: Optimizing Roller Spacing and Capacity is crucial for handling different load types effectively. The spacing of rollers on a gravity conveyor affects both the support of the conveyed items and the ease of movement. For smaller items, closer roller spacing is necessary to provide adequate support and prevent items from tipping or getting stuck. For heavier loads, the capacity of each roller must be considered to ensure that the conveyor can handle the weight without failure. This involves calculating the weight distribution across the rollers and selecting rollers with appropriate load capacities. Properly optimized roller spacing and capacity ensure a smooth, efficient conveyor operation and extend the lifespan of the conveyor system.
Incorporating these Gravity Conveyor Accessories into a gravity conveyor setup not only enhances its functionality but also adapts the system to a wider range of applications, making it more versatile and efficient.
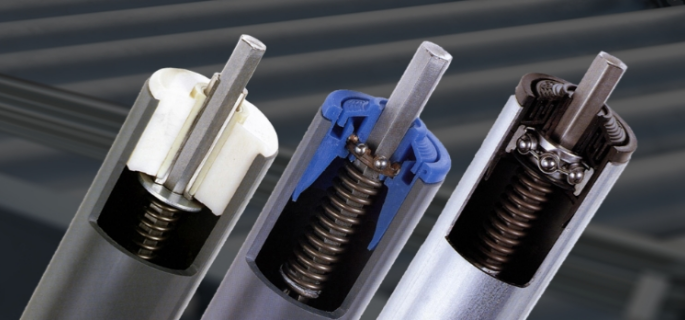
Navigating Complexities with Advanced Gravity Conveyor Accessories
In the realm of material handling, the sophistication of a gravity conveyor system is often defined by its Advanced Gravity Conveyor Accessories. These accessories are pivotal in customizing the system to meet specific operational requirements and environmental conditions. This section delves into the nuances of Curve Selection, Conveyor Width and Pitch, and Operating Conditions, each critical for optimizing the conveyor’s performance.
1. Curve Selection: The choice of curves in a gravity conveyor system is crucial for ensuring smooth product flow. Here’s a comparison of different curve types:
Curve Type | Description | Application |
Straight Roll Curve | Consists of straight rollers | Suitable for boxes and rigid containers; offers a cost-effective solution |
Double Rollers Curve | Features two rows of rollers | Reduces product skewing; ideal for varied package sizes |
Tapered Roller Curve | Rollers are tapered for natural curve | Provides precise product orientation; best for high-speed applications |
2. Conveyor Width and Pitch: Customizing the width and pitch of a conveyor is essential for accommodating specific product dimensions and ensuring efficient flow. The width should be chosen based on the largest item to be conveyed, allowing for a little extra space on each side for safety. The pitch, or the slope of the conveyor, is adjusted according to the weight and type of items being moved, ensuring that they travel at the optimal speed without causing damage or logjams.
3. Operating Conditions: Selecting the right Gravity Conveyor Accessories based on environmental factors is crucial for maintaining efficiency and prolonging the life of the conveyor. For instance, in dusty or humid conditions, dust-tight bearings and corrosion-resistant materials like stainless steel or galvanized steel are recommended. In environments with fluctuating temperatures or exposure to chemicals, materials and lubricants that can withstand these conditions should be chosen.
By carefully considering these aspects of Advanced Gravity Conveyor Accessories, businesses can significantly enhance the functionality and adaptability of their gravity conveyor systems, ensuring they meet the specific needs of their operations while maintaining efficiency and safety.
Assessing Used and Heavy-Duty Gravity Conveyor Accessories
In the diverse world of material handling, the choice of Gravity Conveyor Accessories can significantly impact the efficiency and cost-effectiveness of operations. This section explores the benefits and considerations of using pre-owned Gravity Conveyor Accessories, as well as the necessity of heavy-duty accessories in scenarios involving high loads.
1. Benefits and Considerations of Using Pre-Owned Gravity Conveyor Accessories:
- Cost-Effectiveness: One of the primary benefits of opting for used accessories is the potential for cost savings. Businesses can acquire essential components like guide rails, stops, and supports at a fraction of the price of new items.
- Environmental Impact: Choosing pre-owned accessories contributes to sustainability by reducing waste and the need for new materials.
- Quality Considerations: It’s crucial to thoroughly inspect used accessories for wear and tear. Components should be free from significant damage and retain their structural integrity to ensure safe and efficient operation.
- Compatibility: Ensuring that used accessories are compatible with the existing conveyor system is essential. This includes checking dimensions, load capacities, and material types.
2. Identifying the Need for Heavy-Duty Gravity Conveyor Accessories in High-Load Scenarios:
- Assessing Load Requirements: In environments where conveyors are subjected to heavy or continuous loads, standard accessories might not suffice. It’s important to evaluate the weight and volume of items being transported to determine the need for heavy-duty accessories.
- Durability and Longevity: Heavy-duty accessories are designed to withstand higher stress and wear, offering greater durability and a longer lifespan. This is particularly important in industries like manufacturing, mining, and heavy goods warehousing.
- Safety Considerations: Using accessories that are not designed for high-load conditions can pose safety risks. Heavy-duty components ensure stability and reduce the likelihood of breakdowns and accidents.
- Customization for Specific Needs: In some cases, heavy-duty accessories may need to be customized to meet specific operational requirements. This could include reinforced materials, specialized coatings, or unique designs for extreme conditions.
While used Gravity Conveyor Accessories offer an economical and eco-friendly option, it’s crucial to ensure their quality and compatibility. On the other hand, heavy-duty accessories are indispensable in high-load scenarios, providing the necessary strength, durability, and safety for efficient operations.
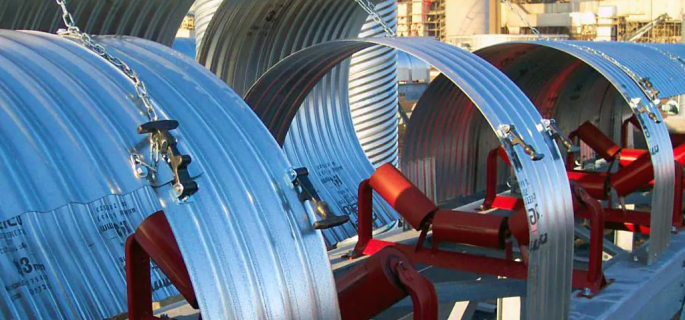
Selecting Roller Types and Their Gravity Conveyor Accessories
In the configuration of gravity conveyor systems, the selection of roller types and their associated Gravity Conveyor Accessories plays a crucial role in determining the efficiency and suitability of the conveyor for specific applications. This section focuses on differentiating between skate wheels and rollers, as well as selecting the right bearings for gravity rollers, both of which are key considerations in the design and functionality of gravity conveyors.
1. Differentiating Between Skate Wheels and Rollers:
- Skate Wheels: These are small, individual wheels that provide a high level of maneuverability and are ideal for lightweight items. Skate wheels allow for more fluid directional changes, making them suitable for curved sections of the conveyor. However, they may not provide as much support for heavier or unevenly distributed loads.
- Rollers: Rollers offer a larger surface area for supporting goods and are better suited for heavier or larger items. They ensure smoother movement for items with flat bottoms and are more effective in maintaining the orientation of the goods being transported. Rollers are typically used in straight sections of the conveyor where directional flexibility is less of a concern.
- Accessory Compatibility: When choosing between skate wheels and rollers, it’s important to consider the compatibility of Gravity Conveyor Accessories. For instance, guide rails and stops may need to be adjusted depending on the type of roller system in use.
2. Selecting the Right Bearings for Rollers:
- Load Capacity: The choice of bearings is directly influenced by the load capacity of the conveyor. Heavier loads require bearings that can withstand higher levels of stress without compromising efficiency.
- Operating Environment: Bearings must be selected based on the operating conditions of the conveyor. In environments with dust, moisture, or temperature extremes, bearings designed to withstand these conditions are essential.
- Maintenance Requirements: The selection of bearings also impacts the maintenance needs of the conveyor. Sealed bearings, for example, may offer lower maintenance requirements but might not be suitable for certain high-load or high-speed applications.
- Compatibility with Gravity Conveyor Accessories: The bearings should be compatible with other Gravity Conveyor Accessories, ensuring that the entire system works harmoniously. This includes considering the integration of accessories like speed controllers, which can be affected by the type of bearings used.
By carefully considering these aspects when selecting roller types and bearings, businesses can ensure that their gravity conveyor systems are optimized for their specific material handling needs, enhanced by the appropriate Gravity Conveyor Accessories. This careful selection process not only improves the functionality of the conveyor but also contributes to its longevity and reliability.
Ensuring Safety and Efficiency with Gravity Conveyor Accessories
The integration of safety features in Gravity Conveyor Accessories is paramount to maintaining a secure and efficient working environment. This section emphasizes the importance of these safety features and outlines best practices for testing conveyors before operation, ensuring that Gravity Conveyor Accessories contribute positively to the overall safety and functionality of the conveyor system.
1. Importance of Safety Features in Gravity Conveyor Accessories:
- Preventing Accidents: Accessories like guard rails and emergency stops are crucial for preventing accidents. They help in safely guiding products and providing immediate halting capabilities in case of an emergency.
- Reducing Wear and Tear: Accessories such as impact plates and reinforced bearings can reduce the wear and tear on the conveyor, thereby preventing potential malfunctions that could lead to safety hazards.
- Enhancing Stability: Supports and anchoring systems are essential for maintaining the stability of the conveyor, especially in areas with heavy loads or high traffic, thus preventing tipping or collapsing incidents.
- Compliance with Regulations: Ensuring that Gravity Conveyor Accessories comply with industry safety standards and regulations is not only a legal requirement but also a moral obligation to protect workers.
2. Best Practices for Testing Conveyors Before Operation:
- Load Testing: Before full operation, it’s crucial to conduct load testing with the intended weight to ensure the conveyor and its accessories can handle the load without issues.
- Speed and Flow Checks: Testing the conveyor at different speeds and observing the flow of materials helps in identifying any potential issues with roller movement or product handling.
- Inspection of Accessories: A thorough inspection of all Gravity Conveyor Accessories should be conducted to check for proper installation, potential obstructions, or misalignments.
- Emergency Response Testing: Testing emergency stops and other safety features to ensure they are functioning correctly is vital for worker safety.
- Documentation and Record Keeping: Keeping detailed records of all tests and conveyor belt inspections is important for maintenance schedules and potential audits.
By prioritizing safety features in Gravity Conveyor Accessories and adhering to rigorous testing protocols, businesses can significantly enhance the safety and efficiency of their gravity conveyor systems. This proactive approach not only safeguards the well-being of employees but also ensures the longevity and reliability of the conveyor system.
Tailoring and Integrating Gravity Conveyor Accessories for Optimal Performance
Customization and integration are key aspects when it comes to enhancing the functionality of gravity conveyor systems with Gravity Conveyor Accessories. This section delves into the process of tailoring these accessories to meet specific industrial needs and the best practices for integrating new accessories into existing conveyor systems.
1. Tailoring Accessories for Specific Industrial Needs:
- Assessment of Operational Requirements: The first step in customization is to assess the specific needs of the industry. This includes understanding the types of items being handled, their weight, size, and the overall speed and volume of operations.
- Designing for Specific Applications: Based on the assessment, Gravity Conveyor Accessories such as custom-sized guide rails, specialized rollers, or unique stops and diverts can be designed. For instance, in a packaging industry, accessories might be tailored for gentle handling to prevent damage to fragile items.
- Material Selection: The choice of materials for Gravity Conveyor Accessories is crucial, especially in industries with specific requirements like food processing or pharmaceuticals, where hygiene and cleanliness are paramount.
- Innovative Solutions: Sometimes, unique challenges require innovative solutions. This could involve developing new types of accessories or modifying existing ones to suit novel applications or to improve efficiency and safety.
2. Integrating New Accessories into Existing Conveyor Systems:
- Compatibility Check: Before integration, it’s essential to ensure that the new Gravity Conveyor Accessories are compatible with the existing system in terms of size, load capacity, and functionality.
- Seamless Integration Process: The integration process should be planned to minimize downtime. This might involve phased implementation or scheduling installation during non-operational hours.
- Testing and Calibration: Once the accessories are integrated, thorough testing and calibration are necessary to ensure they work harmoniously with the existing system. This includes checking for smooth transitions, proper alignment, and efficient operation.
- Training and Documentation: Providing training to the staff on how to operate and maintain the new system is crucial. Additionally, updating operational manuals and maintenance guides to include the new accessories ensures ongoing proper usage.
By carefully tailoring and integrating Gravity Conveyor Accessories, businesses can significantly enhance the efficiency, safety, and functionality of their gravity conveyor systems. This customization allows for a more flexible and responsive approach to material handling, adapting to the evolving needs of various industries.
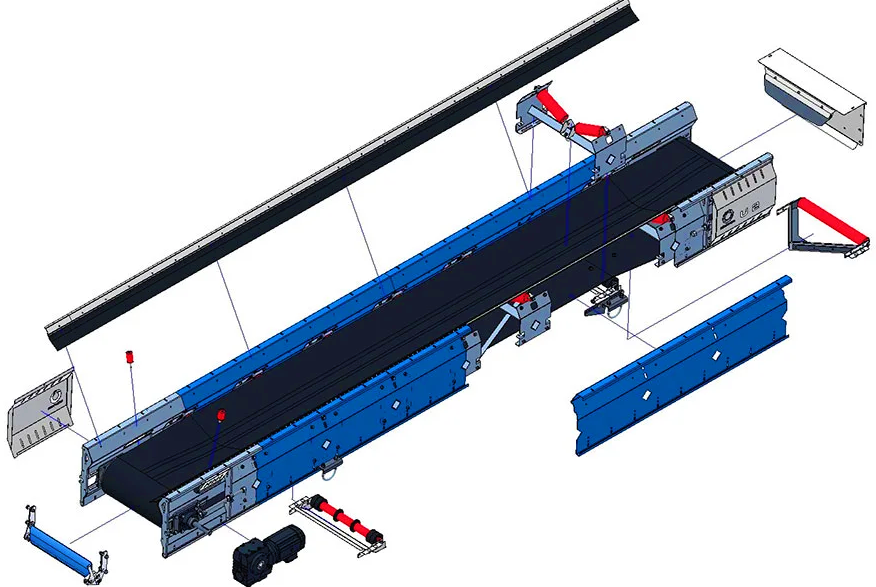
Analyzing Cost-Effective Solutions with Gravity Conveyor Accessories
In this section, we delve into the cost benefits of incorporating Gravity Conveyor Accessories into material handling systems and compare these with the alternatives offered by powered conveyors. The analysis is presented in a tabular format for clarity and ease of understanding.
1. Analyzing the Cost Benefits of Gravity Conveyor Accessories:
- Initial Investment: Gravity Conveyor Accessories typically require a lower initial investment compared to more complex systems. This affordability makes them an attractive option for businesses looking to enhance efficiency without significant capital expenditure.
- Maintenance Costs: Due to their simpler design and fewer moving parts, Gravity Conveyor Accessories generally incur lower maintenance costs. This aspect contributes to a lower total cost of ownership over the conveyor’s lifespan.
- Energy Efficiency: Gravity conveyors, aided by these accessories, do not require electrical power for movement, leading to savings in energy costs.
- Flexibility and Scalability: The modular nature of many Gravity Conveyor Accessories allows for scalability and adaptability to changing business needs without substantial additional costs.
2. Comparing Gravity Conveyor Accessories with Powered Conveyor Alternatives:
Feature | Gravity Conveyor Accessories | Powered Conveyor Systems |
Initial Cost | Generally lower | Higher due to more complex mechanisms |
Energy Consumption | None, operates on gravity | Higher, requires electrical power |
Maintenance | Lower, simpler design | Higher, more components and wear parts |
Flexibility | High, easily reconfigurable | Lower, more fixed in design |
Suitability | Ideal for light to medium loads and shorter distances | Better for heavy loads, long distances, and complex routes |
Noise Level | Typically quieter | Can be noisier due to motors and drives |
This comparative analysis highlights that while Gravity Conveyor Accessories offer cost-effectiveness and are suitable for a range of applications, powered conveyor systems might be necessary for more demanding operations. The choice between the two should be based on specific operational requirements, budget constraints, and long-term business goals. By carefully considering these factors, businesses can make informed decisions that balance cost with functionality and efficiency.
Selecting the Right Gravity Conveyor Accessories for Your Needs
Choosing the appropriate gravity conveyor accessories is essential for ensuring that your conveyor system operates efficiently and safely. The right accessories can enhance productivity, minimize downtime, and protect both your products and employees. Here are some key factors to consider when selecting gravity conveyor accessories.
Factors to Consider
Load Requirements and Weight Capacity
- Understanding Load Requirements: Before selecting gravity conveyor accessories, it is crucial to understand the load requirements of your conveyor system. This includes knowing the maximum weight that the conveyor will need to support at any given time. Overloading the conveyor can lead to equipment failure and safety hazards.
- Weight Capacity of Accessories: Each accessory, from guard rails to conveyor stops, has a specific weight capacity. Ensure that the accessories you choose can handle the weight of the items being conveyed. For instance, heavy-duty guard rails and supports are necessary for systems carrying heavy loads, while lighter accessories may suffice for lighter products.
Specific Application Needs
- Type of Products Being Conveyed: The nature of the products you are conveying will significantly influence your choice of gravity conveyor accessories. For example, fragile items may require roller stops to gently halt movement, while robust products might be suitable for butt-end stops. Consider whether your products are delicate, irregularly shaped, or have special handling requirements.
- Operational Tasks: Different operational tasks such as sorting, packing, or assembly work may require specific accessories. Ball transfer tables are ideal for tasks that involve manual rotation and transition of heavy items, enhancing ergonomics and efficiency. Similarly, gravity conveyor gates can facilitate easy access for personnel and equipment, improving workflow.
Space Constraints and Installation Environment
- Available Space: The space available in your facility will determine the type and size of accessories you can install. Ceiling-hung supports, for example, are excellent for facilities with limited floor space as they suspend the conveyor from the ceiling. Floor-mounted supports, on the other hand, provide a stable base but require sufficient floor space.
- Installation Environment: The environment where the conveyor system will be installed also affects accessory selection. In environments exposed to moisture or chemicals, choosing accessories made from corrosion-resistant materials like galvanized steel is essential. Additionally, environments with high traffic or heavy machinery may require more robust and durable accessories to withstand the conditions.
Making the Best Choice
- Evaluate Your Needs: Start by thoroughly evaluating your operational needs, considering factors such as the type of products being conveyed, the required load capacity, and the specific tasks to be performed.
- Consult with Experts: Seek advice from conveyor system experts or suppliers who can provide insights into the best gravity conveyor accessories for your specific application. They can help you understand the capabilities and limitations of different accessories and recommend the most suitable options.
- Consider Future Expansion: When selecting accessories, think about future growth and expansion of your operations. Choose accessories that can be easily adjusted or expanded to accommodate changes in product lines or increased load requirements.
- Test and Adjust: Once you have selected and installed the accessories, monitor their performance and make any necessary adjustments. Regular maintenance and inspections will ensure that the accessories continue to function effectively and safely.
By carefully considering these factors, you can select the right gravity conveyor accessories that will enhance the efficiency, safety, and longevity of your conveyor system. Properly chosen accessories will not only meet your current operational needs but also provide the flexibility to adapt to future changes and expansions.
Need Conveyor Accessories? Contact us for top quality!
Finding Gravity Conveyor Accessories Near You
When it comes to purchasing gravity conveyor accessories, finding the right suppliers and distributors is crucial. The quality and reliability of the accessories you choose will significantly impact the performance and safety of your conveyor system. Here are some detailed steps and considerations for locating the best sources for gravity conveyor accessories near you.
Local Suppliers and Distributors
How to Locate Suppliers and Distributors of Gravity Conveyor Accessories
- Online Search: Start by conducting an online search for suppliers and distributors of gravity conveyor accessories. Use search engines and online directories to find businesses that specialize in conveyor systems and accessories. Keywords such as “gravity conveyor accessories near me” can help narrow down your search to local suppliers.
- Industry Directories and Trade Associations: Utilize industry directories and trade association websites. These resources often provide comprehensive lists of reputable suppliers and distributors. Examples include the Material Handling Industry (MHI) directory and the Conveyor Equipment Manufacturers Association (CEMA) directory.
- Networking and Referrals: Reach out to industry peers and colleagues for recommendations. Networking with other businesses in your industry can provide valuable insights into reliable suppliers. Attend industry events, trade shows, and conferences to connect with suppliers and see their products firsthand.
- Local Business Listings: Check local business listings such as Yelp, Yellow Pages, and Google My Business. These platforms often feature reviews and ratings from other customers, helping you gauge the reliability and quality of potential suppliers.
- Contacting Manufacturers: Many manufacturers of gravity conveyor systems also supply accessories. Contact manufacturers directly to inquire about purchasing accessories or to get referrals to authorized distributors.
Importance of Choosing Reputable and Experienced Suppliers
- Quality Assurance: Reputable and experienced suppliers are more likely to provide high-quality gravity conveyor accessories. They have established standards and quality control processes that ensure the accessories meet industry requirements and perform reliably.
- Technical Expertise: Experienced suppliers have in-depth knowledge of gravity conveyor systems and their accessories. They can offer expert advice on selecting the right accessories for your specific needs, helping you make informed decisions that enhance the efficiency and safety of your conveyor system.
- Customer Support: Reliable suppliers offer excellent customer support, including after-sales service, installation assistance, and maintenance tips. They are available to address any issues or concerns you may have, ensuring a smooth and hassle-free experience.
- Product Availability and Timely Delivery: Established suppliers typically have a wide range of gravity conveyor accessories in stock and can ensure timely delivery. This minimizes downtime and ensures that your operations continue without interruption.
- Reputation and Reviews: Suppliers with a strong reputation and positive customer reviews are more likely to provide satisfactory products and services. Look for testimonials, case studies, and reviews to gauge the experiences of other customers.
- Warranty and Guarantees: Reputable suppliers often offer warranties and guarantees on their products, providing you with peace of mind. This ensures that you can get replacements or repairs if any issues arise with the accessories.
By following these steps and considering these factors, you can find reliable local suppliers and distributors of gravity conveyor accessories. Ensuring that you purchase from reputable and experienced sources will help you acquire high-quality accessories that enhance the performance, safety, and longevity of your gravity conveyor system.
Exploring Innovative Designs in Gravity Conveyor Accessories
The field of material handling is constantly evolving, with recent innovations in Gravity Conveyor Accessories leading the way in enhancing efficiency and functionality. This section explores these advancements and provides case studies to illustrate the practical applications of these innovative designs.
1. Recent Innovations and Advancements in Gravity Conveyor Accessories:
- Smart Roller Technology: The integration of sensors and IoT technology in rollers allows for real-time tracking and monitoring of goods. This innovation enhances transparency in the supply chain and improves inventory management.
- Modular and Adjustable Accessories: Recent designs in Gravity Conveyor Accessories focus on modularity and adjustability. For instance, adjustable guide rails and reconfigurable stops offer greater flexibility to accommodate various product sizes and shapes.
- Eco-Friendly Materials: There is a growing trend towards using sustainable materials in conveyor accessories. Recycled plastics and biodegradable components are being incorporated to reduce environmental impact.
- Enhanced Safety Features: Safety remains a paramount concern, with new designs featuring improved emergency stops, better guard rails, and anti-slip surfaces to enhance worker safety.
2. Case Studies of Innovative Accessory Implementations:
- Case Study 1: Smart Roller Implementation in E-Commerce: An e-commerce fulfillment center implemented smart roller technology in their gravity conveyors. This led to a 30% improvement in package sorting efficiency and a significant reduction in misplacements.
- Case Study 2: Modular Accessories in Manufacturing: A manufacturing plant utilized modular Gravity Conveyor Accessories to quickly reconfigure their assembly line for different products. This flexibility resulted in a 20% increase in production line efficiency.
- Case Study 3: Sustainable Accessories in Retail Logistics: A retail logistics company adopted eco-friendly Gravity Conveyor Accessories, significantly reducing their carbon footprint and aligning with their sustainability goals.
These examples and advancements in Gravity Conveyor Accessories demonstrate the industry’s commitment to innovation, sustainability, and efficiency. By embracing these new designs, businesses can not only improve their operations but also contribute positively to environmental conservation and worker safety.
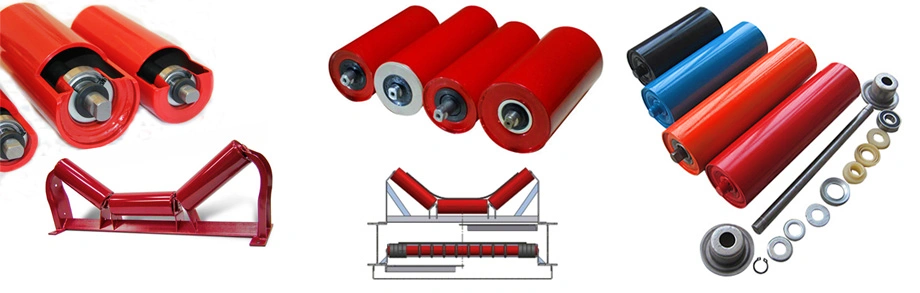
Ensuring Maintenance and Longevity of Gravity Conveyor Accessories
Maintaining the efficiency and extending the lifespan of Gravity Conveyor Accessories are crucial for the smooth operation of conveyor systems. This section provides valuable tips for maintenance and addresses common challenges, offering practical solutions to ensure the longevity of these essential components.
1. Tips for Maintaining and Extending the Life of Gravity Conveyor Accessories:
- Regular Inspections: Conduct periodic inspections of all Gravity Conveyor Accessories. Check for signs of wear, damage, or misalignment, particularly in high-use areas like rollers, stops, and guide rails.
- Proper Cleaning: Keep the conveyor and its accessories clean. Remove debris and dust that can accumulate and cause wear or operational issues. Use appropriate cleaning agents that do not corrode or damage the accessories.
- Lubrication:To keep your conveyor running smoothly, it’s important to regularly apply lubricant to the moving parts like bearings and rollers. This practice helps in minimizing friction and warding off wear and tear. However, it’s crucial to choose a lubricant that’s compatible with the conveyor’s materials and the conditions under which it operates. This ensures that your conveyor maintains its efficiency and longevity.
- Tightening and Adjustments: Ensure that all bolts, nuts, and adjustable components are tightened and correctly aligned. Loose components can lead to malfunctions and increased wear.
- Replacement of Worn Parts: Replace parts that show significant wear or damage promptly. Using worn-out accessories can lead to inefficiencies and potential safety hazards.
2. Common Maintenance Challenges and Solutions:
- Challenge: Buildup of Debris: In environments with high levels of dust or debris, accumulation can occur, leading to blockages or operational issues.
- Solution: Implement a regular cleaning schedule and consider installing scrapers or brushes to automatically clear debris from moving parts.
- Challenge: Environmental Wear: Accessories exposed to harsh conditions, such as extreme temperatures or corrosive substances, can degrade faster.
- Solution: Use materials and coatings that are designed to withstand specific environmental challenges. Regularly check for any signs of corrosion or thermal damage.
- Challenge: Misalignment and Slippage: Continuous use can lead to misalignment of rollers or belts, affecting the conveyor’s efficiency.
- Solution: Regularly check and adjust the alignment of rollers and belts. Consider installing self-aligning accessories where feasible.
- Challenge: Inconsistent Performance: Fluctuations in performance can be caused by uneven wear or improper settings.
- Solution: Conduct comprehensive audits of the conveyor system to identify and rectify uneven wear patterns. Ensure that all settings are optimized for the load and operational speed.
By adhering to these maintenance tips and addressing common challenges, the performance and longevity of Gravity Conveyor Accessories can be significantly enhanced. Regular and proactive maintenance not only ensures the smooth operation of the conveyor system but also contributes to a safer and more productive working environment.
As we conclude our exploration of Gravity Conveyor Accessories, it’s essential to summarize the key takeaways that underscore their significance in the realm of material handling. These accessories, ranging from basic components like guide rails and stops to advanced innovations like smart roller technology, play a pivotal role in enhancing the functionality, safety, and efficiency of gravity conveyor systems. The integration of these accessories not only streamlines operations but also extends the lifespan and reliability of the conveyor systems. The adaptability offered by modular and adjustable accessories ensures that gravity conveyors can meet the evolving needs of various industries, from manufacturing to distribution.
Furthermore, the importance of selecting the right Gravity Conveyor Accessories cannot be overstated. The right choice of accessories directly impacts the efficiency and productivity of the conveyor system. Whether it’s choosing between skate wheels and rollers based on load requirements, or opting for heavy-duty accessories for high-load scenarios, each decision should be made with a thorough understanding of the operational demands. The implementation of these accessories, when aligned with the specific needs of a business, can lead to significant improvements in material handling processes, ultimately contributing to the overall success and growth of the organization. Therefore, investing time and resources in carefully selecting and maintaining Gravity Conveyor Accessories is a wise decision for any business looking to optimize its conveyor systems.
FAQs on Gravity Conveyors Accessories
Gravity conveyor accessories enhance push-conveyor with ball transfer tables, adjustable rails, gates, custom supports & more.available for light duty and medium duty conveyors.Slowing down a gravity conveyor involves adjusting various components to reduce the speed at which items travel. One common method is to decrease the conveyor’s slope or pitch, as a lesser angle reduces the gravitational pull and hence the speed. Another approach is to use accessories like speed controllers or friction inserts on the rollers, which add resistance and slow down the movement. Additionally, installing stops or dampers at intervals can help in controlling the speed. It’s important to note that any modifications should maintain the conveyor’s efficiency and safety, and should be tested thoroughly to ensure they meet the operational requirements.
The typical pitch of a gravity conveyor varies depending on the application but generally ranges between 1/4 inch to 1/2 inch per foot of conveyor length. The pitch is essentially the slope or incline of the conveyor, and it’s crucial for ensuring that items move at the desired speed. The right pitch depends on factors like the weight and type of items being conveyed, the desired speed of movement, and the length of the conveyor. A steeper pitch increases the speed of movement, while a gentler pitch slows it down. The pitch must be carefully calibrated to ensure efficient and safe operation.
rstly, they are cost-effective since they use gravity to move items, eliminating the need for a power source. This also makes them energy-efficient and environmentally friendly. Gravity conveyors are relatively simple in design, which means they have fewer parts that can break down, leading to lower maintenance costs. They are also versatile and can be used in various settings, including warehouses, manufacturing plants, and distribution centers. Furthermore, gravity conveyors can be easily integrated with other conveyor systems and can be customized with different accessories to meet specific operational needs.
No, gravity conveyors do not require electricity to operate. As the name suggests, they rely on the natural force of gravity to move items. Items are placed on the conveyor at a higher elevation and move down the slope due to gravitational pull. This makes gravity conveyors an energy-efficient and cost-effective solution for transporting goods, especially over short distances or in processes where items need to be moved at a controlled speed. Their simplicity also means less maintenance and fewer parts that can malfunction, further reducing operational costs.
The minimum angle for a gravity conveyor, also known as the pitch, is typically around 2 to 3 degrees. This angle can vary based on the type of items being conveyed and the desired speed of movement. A minimal angle is necessary to ensure that items can move by the force of gravity without manual assistance. However, the angle should not be so steep that it causes items to move too quickly or become uncontrollable. The ideal angle ensures a balance between efficient movement and safety, and it may require adjustments based on the specific requirements of the operation.
Speeding up a gravity conveyor can be achieved by increasing the pitch or slope of the conveyor. A steeper angle allows gravity to move items more quickly. However, it’s important to ensure that the increased speed does not compromise safety or the integrity of the items being conveyed. Another method is to use smoother and more efficient rollers, which reduce friction and allow items to move faster. Additionally, ensuring that the conveyor is well-maintained and free of debris or obstructions can also help in maintaining optimal speed. It’s crucial to consider the nature of the items being conveyed and operational safety when making adjustments to speed up a conveyor.
A gravity conveyor works by using the force of gravity to move products along a conveyor path without the need for motor power. The conveyor is typically set at a slight decline, allowing items placed on it to roll or slide downwards naturally. The decline creates a gentle slope that enables the products to move smoothly from the higher end (infeed) to the lower end (discharge).
Gravity conveyors consist of a series of rollers or wheels mounted on a frame. When products are placed on the conveyor, the force of gravity causes them to move down the slope. The rollers or wheels reduce friction, making it easier for the items to travel along the conveyor with minimal effort.
This type of conveyor is ideal for moving lightweight, uniform items such as boxes, totes, and trays. It is commonly used in warehouses, distribution centers, and manufacturing facilities for tasks like assembly, packaging, and order picking. Gravity conveyors are cost-effective, energy-efficient, and require little maintenance, making them a popular choice for various material handling applications.
Last Updated on June 19, 2024 by Jordan Smith
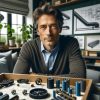
Jordan Smith, a seasoned professional with over 20 years of experience in the conveyor system industry. Jordan’s expertise lies in providing comprehensive solutions for conveyor rollers, belts, and accessories, catering to a wide range of industrial needs. From initial design and configuration to installation and meticulous troubleshooting, Jordan is adept at handling all aspects of conveyor system management. Whether you’re looking to upgrade your production line with efficient conveyor belts, require custom conveyor rollers for specific operations, or need expert advice on selecting the right conveyor accessories for your facility, Jordan is your reliable consultant. For any inquiries or assistance with conveyor system optimization, Jordan is available to share his wealth of knowledge and experience. Feel free to reach out at any time for professional guidance on all matters related to conveyor rollers, belts, and accessories.