Future Trends in Gravity Conveyor Roller Bearings
Gravity conveyors are an essential component of material handling systems, offering a simple yet effective means of moving goods across short to medium distances without the use of power. These systems rely on the force of gravity or a slight decline to facilitate the movement of items, making them a cost-effective and energy-efficient solution for warehouses, manufacturing plants, and distribution centers. At the heart of these conveyors are gravity conveyor roller bearings, critical elements that ensure the smooth and efficient operation of the rollers. These bearings allow the conveyor rollers to rotate freely, minimizing friction and wear, and thereby extending the lifespan of the conveyor system. Understanding the function and importance of gravity conveyor roller bearings is key to optimizing the performance and reliability of gravity conveyor systems.
To Understand the Types of Gravity Conveyor Roller Bearings
The efficiency and reliability of gravity conveyors significantly depend on the types of bearings they employ. Gravity conveyor roller bearings are pivotal in ensuring the seamless movement of goods, with various types designed to meet specific operational needs. Here, we delve into the different types of gravity conveyor roller bearings, highlighting their unique features and applications.
Gravity Conveyor Roller Bearings
Introduction and Functionality: Gravity conveyor roller bearings are designed to facilitate the smooth rotation of conveyor rollers, leveraging gravity to move items along the conveyor system. These bearings are fundamental in reducing friction and supporting the conveyor’s load.
- Material: Typically made from steel or plastic, depending on the application’s requirements for durability and resistance to environmental factors.
- Load Capacity: Engineered to support varying weights, from lightweight packages to heavier goods.
- Speed: Suitable for applications with varying speed requirements, ensuring smooth operation.
- Maintenance: Generally low-maintenance, owing to their simple design.
- Installation: Easy to install, enhancing the conveyor system’s overall efficiency.
- Cost-Effectiveness: Offers an economical solution for many material handling needs.
- Versatility: Compatible with various roller types and conveyor designs.
- Durability: Designed to withstand the rigors of daily use in a busy material handling environment.
- Environmental Resistance: Certain models are built to resist corrosion and other environmental factors.
Heavy Duty Gravity Conveyor Roller Bearings
Characteristics and When They’re Needed: Heavy duty gravity conveyor roller bearings are crafted for more demanding applications, where higher loads and more robust performance are required.
- Enhanced Load Capacity: Capable of handling significantly heavier loads compared to standard bearings.
- Increased Durability: Constructed from materials that offer greater resistance to wear and tear.
- High Impact Resistance: Ideal for environments where the conveyor system is subject to shocks or impacts.
- Extended Lifespan: Designed to last longer, even under strenuous conditions.
- Low Maintenance: Despite their heavy-duty nature, these bearings require minimal maintenance.
- Versatility in Application: Suitable for a wide range of industries, including mining, construction, and heavy manufacturing.
- Cost Efficiency: Provides long-term savings through reduced replacement and maintenance costs.
- Environmental Suitability: Engineered to perform in harsh environmental conditions.
- Customization Options: Available in various sizes and specifications to meet specific conveyor system requirements.
Conveyor Bearings Hex Bore
Features and Applications: Conveyor bearings with a hex bore are uniquely designed to fit hexagonal shafts, offering a secure fit and precise alignment.
- Secure Fit: The hexagonal shape ensures a tight fit, reducing slippage and misalignment.
- Easy Installation: Simplifies the assembly process, allowing for quick setup and adjustments.
- Precision: Enhances the precision of roller movement, improving overall conveyor efficiency.
- Compatibility: Ideal for use with driven rollers or situations requiring precise positioning.
- Load Distribution: Promotes even load distribution, extending the life of the bearing and the conveyor.
- Material Options: Available in various materials to suit different operational environments.
- Maintenance: Facilitates easier maintenance due to the straightforward disassembly process.
- Cost-Effective: Offers an economical solution for improving conveyor precision and reliability.
- Application Diversity: Widely used in packaging and sorting facilities where accuracy is paramount.
Conveyor Roller Bearing Housing
Importance for Bearing Protection and Smooth Operation: The housing of a conveyor roller bearing plays a crucial role in protecting the bearing and ensuring its smooth operation.
- Protection: Shields the bearing from debris, dust, and other contaminants that can affect performance.
- Lubrication Retention: Helps in retaining lubrication, essential for reducing friction and wear.
- Structural Integrity: Provides structural support, ensuring the bearing remains aligned and functional.
- Ease of Replacement: Designed for easy access, facilitating quick bearing replacement or maintenance.
- Noise Reduction: Contributes to quieter conveyor operation by dampening vibration and noise.
- Heat Dissipation: Assists in dissipating heat generated by the bearing, preventing overheating.
- Customization: Available in various sizes and materials to match specific bearing and conveyor requirements.
- Durability: Made from robust materials to withstand the operational demands of the conveyor system.
- Cost Efficiency: Protects the bearing, extending its lifespan and reducing the need for frequent replacements.
Understanding the types of gravity conveyor roller bearings and their specific applications is crucial for selecting the right components for your conveyor system. Each bearing type offers unique advantages tailored to different operational needs, ensuring the efficiency and longevity of your gravity conveyor.
Key Features of Gravity Conveyor Roller Bearings
Gravity conveyor roller bearings are integral components of material handling systems, ensuring the efficient and smooth operation of gravity conveyors. Their design, material selection, and specific features like coating and size significantly impact their performance, longevity, and the overall effectiveness of the conveyor system.
Design and Material Selection
The design and material selection of gravity conveyor roller bearings are crucial for their functionality and durability. Here are key considerations:
- Material Durability: Steel bearings are known for their strength and durability, making them suitable for heavy-duty applications. Plastic bearings, on the other hand, offer corrosion resistance and are lighter, making them ideal for environments where chemical exposure or weight is a concern.
- Load Capacity: The design must accommodate the expected load, with steel bearings generally supporting heavier loads compared to plastic ones.
- Environmental Resistance: Plastic bearings resist corrosive substances and moisture, making them preferable in harsh environments, whereas steel bearings are better suited for high-temperature applications.
- Speed Compatibility: The bearing design should match the conveyor’s operational speed. High-speed operations may require specially designed bearings to reduce friction and heat buildup.
- Lubrication Requirements: Steel bearings often require lubrication to operate smoothly, whereas many plastic bearings are self-lubricating, reducing maintenance needs.
- Noise Reduction: Plastic bearings tend to operate more quietly than steel bearings, an important consideration in noise-sensitive environments.
- Installation Ease: Bearings should be designed for easy installation and replacement, minimizing downtime for maintenance or upgrades.
- Cost-Effectiveness: The overall cost, including initial purchase and long-term maintenance, should align with the budget and expected lifespan of the conveyor system.
Benefits of Coated Conveyor Rollers
Coated conveyor rollers, integral to the operation of gravity conveyor roller bearings, offer several benefits:
- Reduced Friction: Coatings can significantly reduce friction between the roller and the bearing, enhancing efficiency and extending the lifespan of both components.
- Corrosion Resistance: Protective coatings shield both the roller and bearing from corrosive substances, increasing their durability in challenging environments.
- Noise Reduction: Coatings can dampen operational noise, contributing to a quieter workspace.
- Wear Resistance: Enhanced wear resistance means less frequent replacements and maintenance, saving time and money.
- Improved Product Protection: Coatings can provide a smoother surface that minimizes damage to conveyed materials.
- Increased Load Capacity: Certain coatings can improve load distribution, allowing for heavier items to be transported without damaging the bearings or rollers.
- Enhanced Moisture Protection: Coatings can prevent moisture ingress, protecting the bearing internals from rust and corrosion.
- Temperature Resistance: Some coatings are designed to withstand extreme temperatures, making them suitable for environments with high thermal variability.
- Customizability: Coatings can be tailored to specific operational needs, including material compatibility and environmental conditions.
Selecting the Right Bearing Size
Choosing the correct size for gravity conveyor roller bearings is vital for optimal performance:
- Load Distribution: Properly sized bearings ensure even load distribution, preventing premature wear and extending the system’s lifespan.
- Fit and Alignment: Correct sizing is crucial for the fit and alignment within the roller, ensuring smooth operation and reducing the risk of malfunctions.
- Speed Efficiency: The size of the bearing can affect the maximum operational speed of the conveyor, with smaller bearings typically suitable for higher speeds.
- Space Optimization: Small diameter conveyor rollers can be advantageous in tight spaces, allowing for more flexible conveyor design and layout.
- Weight Considerations: The size and material of the bearing influence the overall weight of the conveyor system, impacting its stability and structure.
- Maintenance Accessibility: Appropriately sized bearings are easier to inspect, maintain, and replace, contributing to lower downtime.
- Energy Efficiency: Correctly sized bearings minimize energy loss due to friction, contributing to more energy-efficient conveyor operations.
- Customization Options: The availability of various sizes allows for customization according to specific application requirements, ensuring that each conveyor system operates at its best.
Incorporating the right features in gravity conveyor roller bearings, from material selection and design to coating and sizing, is essential for achieving a high-performing, durable, and efficient gravity conveyor system.
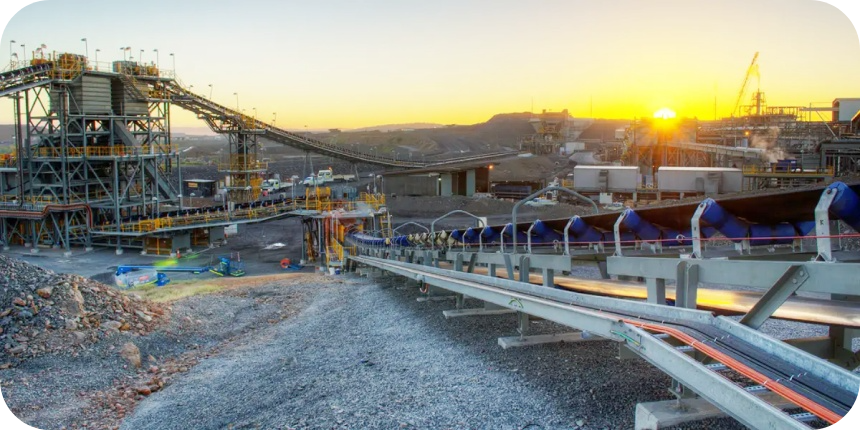
Applications and Selection Guide for Gravity Conveyor Roller Bearings
Choosing the right gravity conveyor roller bearingsis crucial for the efficiency,durability, and smooth operation of your material handling system. Understanding the specific needs of your application and the capabilities of different bearings can significantly impact your system’s overall performance.
How to Choose the Right Gravity Conveyor Roller Bearings
When selecting gravity conveyor roller bearings, several factors must be considered to ensure optimal performance:
- Load Capacity: Assess the maximum weight the conveyor will need to support. Bearings must be chosen based on their ability to handle the expected load without compromising performance.
- Operating Environment: Consider the environment in which the conveyor will operate. For harsh conditions, such as extreme temperatures or exposure to corrosive materials, select bearings made from materials designed for these conditions.
- Conveyor Speed: The speed at which the conveyor will operate can influence the type of bearing needed. High-speed applications may require bearings designed to minimize friction and heat buildup.
- Maintenance Requirements: Evaluate the ease of maintenance and the need for lubrication. Self-lubricating bearings may be preferable in applications where maintenance access is challenging.
- Durability and Lifespan: Consider the expected lifespan of the bearings and their durability under continuous use. This can affect the overall cost-effectiveness of the conveyor system.
- Noise Levels: In environments where noise reduction is important, choose bearings that operate quietly.
- Installation and Replacement: Look for bearings that are easy to install and replace to minimize downtime.
- Compatibility with Conveyor Rollers: Ensure the bearings are compatible with the conveyor rollers in terms of size, material, and design.
Applications of Gravity Conveyor Roller Bearings
Gravity conveyor roller bearings are versatile and can be used in a wide range of applications:
- Warehousing and Distribution: For sorting, staging, and loading activities.
- Manufacturing: As part of assembly lines or for moving materials between processes.
- Packaging: In packaging lines for moving products into packaging stations.
- Food and Beverage: For transporting products through processing areas, considering food-grade materials for bearings.
- Retail: In back-of-house operations for stock management and order fulfillment.
- Cold Storage: Specially designed bearings for low-temperature environments.
- Heavy Industry: Bearings designed for heavy loads, such as in metal manufacturing or automotive assembly.
- Pharmaceuticals: For clean environments, requiring bearings that can be easily sanitized.
Choosing Reputable Gravity Conveyor Manufacturers
Selecting the right manufacturer for gravity conveyor roller bearings is as crucial as choosing the bearings themselves:
- Experience: Look for manufacturers with extensive experience in your industry.
- Quality Assurance: Choose suppliers that adhere to high-quality standards and offer warranties.
- Product Range: Ensure the manufacturer offers a wide range of bearings to suit various applications.
- Customization: The ability to customize bearings to meet specific requirements can be a significant advantage.
- Technical Support: Manufacturers that offer excellent technical support can help you choose the right bearings and provide assistance during installation and maintenance.
- Lead Times: Consider the manufacturer’s lead times to ensure they align with your project timelines.
- Cost: While cost should not be the only factor, it is important to ensure that the bearings offer value for money.
- Reputation: Research the manufacturer’s reputation in the market. Reviews and testimonials from other customers can provide valuable insights.
Selecting the right gravity conveyor roller bearings involves a careful consideration of your system’s requirements and the specific characteristics of different bearings. Partnering with a reputable manufacturer ensures that you receive high-quality bearings tailored to your needs, along with the support necessary to maintain optimal performance over time.
Maintenance and Replacement of Gravity Conveyor Roller Bearings
Maintaining and replacing gravity conveyor roller bearings are critical practices to ensure the longevity and efficiency of your conveyor system. Proper attention to these components can significantly reduce downtime and enhance operational performance.
Tips on Conveyor Roller Bearing Replacement
- Regular Inspections: Schedule regular inspections to assess the condition of bearings and identify any signs of wear or damage early.
- Follow Manufacturer Guidelines: Always adhere to the manufacturer’s instructions for replacement procedures to ensure compatibility and maintain warranty coverage.
- Use the Right Tools: Employ the correct tools for bearing replacement to avoid damaging the new bearings or the conveyor structure.
- Keep Bearings Clean: Ensure that new bearings are clean and free from debris before installation to prevent premature failure.
- Lubrication: Properly lubricate bearings according to the manufacturer’s recommendations, unless they are self-lubricating, to reduce friction and wear.
- Training: Ensure that maintenance personnel are adequately trained in the correct replacement techniques and safety procedures.
- Inventory Management: Keep a stock of replacement bearings to minimize downtime when a bearing needs to be replaced urgently.
- Alignment Checks: After replacement, check the alignment of rollers and bearings to ensure smooth operation and prevent uneven wear.
Maintenance Best Practices
- Regular Cleaning: Keep the conveyor and bearings clean from dust, dirt, and debris that can cause wear or jamming.
- Lubrication Schedule: Adhere to a lubrication schedule for bearings that require it, using the correct type of lubricant.
- Load Monitoring: Regularly monitor and adjust the load distribution on the conveyor to prevent overloading bearings in certain areas.
- Environmental Controls: Implement controls to manage the environment around the conveyor, such as humidity and temperature, to prevent bearing damage.
- Visual Inspections: Conduct visual inspections frequently to catch any early signs of wear or damage.
- Vibration Analysis: Use vibration analysis tools to detect abnormalities in bearing operation that may indicate issues.
- Bearing Upgrades: Consider upgrading to higher quality or more suitable bearings for your application to improve longevity and performance.
- Record Keeping: Maintain records of maintenance, replacements, and inspections to track bearing performance and predict future maintenance needs.
Signs Indicating the Need for Bearing Replacement or Maintenance
- Increased Noise: Unusual or increased noise from the conveyor may indicate bearing wear or failure.
- Reduced Movement Efficiency: Difficulty in roller movement or increased resistance can signal bearing issues.
- Visible Wear or Damage: Any visible signs of wear, such as cracks or pitting on the bearing surface.
- Excessive Vibration: An increase in vibration during operation can indicate misalignment or bearing deterioration.
- Heat Generation: Bearings becoming excessively hot during operation may be failing or improperly lubricated.
- Contaminant Presence: Signs of dirt, dust, or water ingress into the bearing assembly necessitate immediate attention.
- Irregular Roller Movement: Rollers not moving smoothly or evenly can be a symptom of bearing issues.
- Seized Rollers: Rollers that are stuck and refuse to turn are likely experiencing bearing failure.
- Age and Usage: Bearings have a service life; those reaching or exceeding their expected lifespan should be inspected and likely replaced.
Adhering to these guidelines for the maintenance and replacement of gravity conveyor roller bearings will help ensure the reliability and efficiency of your conveyor system, reducing potential downtime and extending the operational life of the equipment.
Innovative Solutions and Future Trends in Gravity Conveyor Roller Bearings
The field of material handling is continuously evolving, with gravity conveyor roller bearings at the forefront of innovation. These advancements aim to enhance efficiency, reduce maintenance, and extend the lifespan of conveyor systems. Here’s a look at the cutting-edge technologies and materials shaping the future of gravity conveyor roller bearings, along with the emerging trends in gravity conveyor systems.
New Technologies and Materials in Conveyor Roller Bearing Design
- Self-Lubricating Materials: Bearings made from materials that inherently reduce friction and eliminate the need for external lubrication, enhancing longevity and reducing maintenance.
- High-Performance Polymers: The use of advanced polymers that offer superior wear resistance, lower weight, and resistance to a wide range of chemicals, improving the versatility of gravity conveyors in different environments.
- Composite Materials: Bearings crafted from composite materials that combine the strength of metal with the corrosion resistance of plastics, offering a balanced solution for challenging applications.
- Smart Bearings: Integration of sensors within bearings to monitor their condition in real-time, allowing for predictive maintenance and reducing unexpected downtime.
- 3D Printed Bearings: Customizable and rapidly produced bearings that can be tailored to specific applications, reducing lead times and allowing for innovative design features.
- Nanotechnology Coatings: Application of nanotechnology-based coatings to enhance the durability and performance of bearings, including improved wear resistance and reduced friction.
Future Trends in Gravity Conveyor Systems and the Role of Advanced Bearings
- Increased Automation: As industries move towards more automated processes, the demand for gravity conveyor roller bearings that can reliably operate in automated environments will grow.
- Sustainability Focus: A shift towards materials and manufacturing processes that are more environmentally friendly, with bearings playing a key role in reducing energy consumption and waste.
- Customization and Flexibility: The need for conveyor systems that can be easily reconfigured or customized for different applications, supported by versatile and adaptable bearings.
- Enhanced Durability: Bearings designed to last longer, even under harsh conditions, reducing the need for frequent replacements and lowering the total cost of ownership.
- IoT Integration: Bearings that can communicate with other components of the conveyor system and beyond, enabling better system integration and operational efficiency.
- Advanced Material Handling: The development of bearings that can handle a wider range of materials, including those that are sensitive, abrasive, or irregularly shaped.
- Global Supply Chain Resilience: The role of bearings in enhancing the resilience and reliability of global supply chains, particularly in critical industries such as food and pharmaceuticals.
- Health and Safety Enhancements: Bearings that contribute to safer working environments, including those that operate more quietly, reduce the risk of failures, and minimize maintenance-related downtime.
The future of gravity conveyor systems is closely tied to the evolution of gravity conveyor roller bearings, with advances in technology and materials driving significant improvements in conveyor performance, efficiency, and adaptability. As these trends continue to develop, the role of innovative bearing solutions in meeting the challenges of modern material handling will become increasingly important.
Need help selecting the perfect conveyor roller? Contact us now!
Need help selecting the perfect conveyor roller? Contact us now!FAQs about Gravity Conveyor Roller Bearings
For conveyor belt rollers, the choice of bearings significantly impacts the efficiency, durability, and maintenance requirements of the conveyor system. Typically, we recommend two main types of bearings: ball bearings and roller bearings, specifically designed for conveyor applications. These bearings are engineered to withstand the demands of continuous operation, heavy loads, and varying environmental conditions.
Ball bearings are ideal for applications requiring low friction and high-speed capabilities. They are precision-engineered for smooth operation and are suitable for lighter loads. On the other hand, roller bearings are better suited for heavier load applications due to their larger contact area, which distributes the load more evenly and enhances durability. Within roller bearings, cylindrical roller bearings are often preferred for their ability to handle high radial loads and operate efficiently under high-speed conditions.
Moreover, for environments that are prone to contamination, harsh chemicals, or require washdowns, stainless steel or plastic composite bearings might be recommended due to their corrosion-resistant properties. In dusty or outdoor environments, sealed or shielded bearings can provide additional protection against contaminants, extending the lifespan of the bearings and the conveyor system.
When selecting bearings for conveyor belt rollers, it’s crucial to consider the specific requirements of your application, including load capacity, speed, environmental conditions, and maintenance accessibility, to ensure optimal performance and longevity of your conveyor system.
Roller bearings are designed to carry heavy loads and come in various types, each suited for different applications and load-handling capabilities. The three primary types of roller bearings are cylindrical, tapered, and spherical roller bearings.
Cylindrical Roller Bearings: These bearings consist of cylinders used as the rolling elements, providing a larger contact area than ball bearings. This design allows them to handle higher radial loads, making them suitable for applications requiring high-speed operation and heavy-duty performance. They are commonly used in electric motors, automotive applications, and large industrial machinery.
Tapered Roller Bearings: Characterized by their tapered rollers and raceways, these bearings are designed to handle both radial and axial loads simultaneously. The angle of the taper allows the bearing to efficiently manage large axial forces, making them ideal for use in vehicle hubs, gearboxes, and other applications where forces are applied in multiple directions.
Spherical Roller Bearings: These bearings feature rollers that are thick in the middle and thinner at the ends, with a spherical shape that allows the inner ring to pivot within the outer ring. This design provides self-aligning capabilities, making spherical roller bearings suitable for applications where misalignment may occur, such as in shafts prone to bending. They are commonly used in wind turbines, mining equipment, and heavy machinery.
Each type of roller bearing offers unique advantages and is selected based on the specific needs of the application, including the direction and magnitude of the loads it must support.
A gravity roller conveyor is a type of material handling equipment that relies on gravity to move products and materials along a flat or slightly inclined path. It consists of a series of rollers mounted on a frame, over which goods can be moved manually or by the force of gravity. These conveyors are a simple, efficient, and cost-effective solution for transporting items across short to medium distances within manufacturing plants, warehouses, and distribution centers.
Gravity roller conveyors are versatile and can be used for a wide range of applications, including product sorting, assembly lines, and packaging processes. They are particularly beneficial in settings where power is not available or where operations require minimal energy consumption. The design of a gravity roller conveyor can be customized with different roller diameters, materials, and spacings to accommodate various types of goods and operational requirements.
One of the key advantages of gravity roller conveyors is their ease of installation and maintenance. They can be easily integrated into existing material handling systems and reconfigured as needed to adapt to changes in production processes. Additionally, their simplicity and the absence of motorized parts reduce the risk of breakdowns and the need for frequent maintenance, making them a reliable and cost-effective choice for many material handling applications.
Choosing the right roller bearings for your application involves considering several critical factors to ensure optimal performance, durability, and cost-efficiency. Here are key considerations when selecting roller bearings:
Load Capacity: Determine the radial and axial loads the bearing will need to support. Different types of roller bearings have varying load capacities, with cylindrical roller bearings typically handling higher radial loads and tapered roller bearings accommodating both radial and axial loads.
Speed Requirements: Consider the operational speed of the application. Bearings are rated for maximum speed, and selecting a bearing that can handle the application’s speed is crucial to prevent overheating and failure.
Operating Environment: Assess the environment in which the bearing will operate. Factors such as temperature, moisture, and exposure to corrosive substances can significantly affect bearing material and type selection.
Shaft and Housing Fit: Ensure the bearing fits correctly within the shaft and housing to maintain proper alignment and prevent undue stress on the bearing components.
Lubrication: Choose a bearing that is compatible with the type of lubrication available in the application, whether it’s grease, oil, or self-lubricating. Proper lubrication is essential for reducing friction and wear.
Sealing: If the bearing will be exposed to contaminants, consider bearings with sealing options to protect against dust, dirt, and moisture.
Maintenance and Accessibility: Consider the ease of maintenance and replacement. Bearings that are easier to inspect, lubricate, and replace can reduce downtime and maintenance costs.
Cost: While cost should not be the only factor, it’s important to consider the total cost of ownership, including purchase price, maintenance costs, and potential downtime.
By carefully evaluating these factors in the context of your specific application, you can select roller bearings that offer the best performance, reliability, and value for your needs.
Last Updated on July 4, 2024 by Jordan Smith
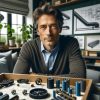
Jordan Smith, a seasoned professional with over 20 years of experience in the conveyor system industry. Jordan’s expertise lies in providing comprehensive solutions for conveyor rollers, belts, and accessories, catering to a wide range of industrial needs. From initial design and configuration to installation and meticulous troubleshooting, Jordan is adept at handling all aspects of conveyor system management. Whether you’re looking to upgrade your production line with efficient conveyor belts, require custom conveyor rollers for specific operations, or need expert advice on selecting the right conveyor accessories for your facility, Jordan is your reliable consultant. For any inquiries or assistance with conveyor system optimization, Jordan is available to share his wealth of knowledge and experience. Feel free to reach out at any time for professional guidance on all matters related to conveyor rollers, belts, and accessories.