Affordable Material Handling with Gravity Feed Conveyor Rollers
In the realm of material handling and logistics, gravity feed conveyor rollers stand out as a cornerstone technology, facilitating the smooth and efficient movement of goods across numerous industries. These systems leverage the force of gravity, allowing items to glide effortlessly along the conveyor path with minimal human intervention or mechanical power. Unlike powered conveyors that require electrical energy to move items, gravity feed conveyor rollers offer a cost-effective and environmentally friendly alternative. Their simplicity in design not only reduces operational costs but also minimizes maintenance needs, making them a preferred choice for businesses looking to optimize their operations. The inherent efficiency and reliability of gravity feed conveyor rollers make them an indispensable tool in the modern logistics and warehousing landscape, underscoring their critical role in streamlining processes and enhancing productivity.
What Are Gravity Feed Conveyor Rollers
Gravity feed conveyor rollers are an integral part of material handling systems, designed to facilitate the movement of goods across short to medium distances without the use of external power sources. These conveyors utilize the natural force of gravity to move items, making them an efficient and cost-effective solution for various industries. Here, we delve into the mechanics and key components that define gravity feed conveyor rollers.
Basic Mechanics of Gravity Feed Conveyor Rollers
The operation of gravity feed conveyor rollers is grounded in several fundamental mechanical principles that enable the smooth and efficient transport of goods. These principles ensure that items move at a controlled pace, with minimal risk of damage or loss. Understanding these mechanics is crucial for optimizing system performance and ensuring the longevity of the conveyor setup.
- Natural Force Utilization: They harness gravity’s pull, allowing items to move downhill or along a flat surface with a slight incline, minimizing manual effort or energy consumption.
- Roller Movement: Items placed on the conveyor make contact with the rollers, which rotate, reducing friction and facilitating smooth movement.
- Adjustable Incline: The angle of incline can be adjusted to control the speed of movement, ensuring safety and efficiency in handling goods.
- Load Distribution: Evenly spaced rollers ensure balanced load distribution, preventing items from tipping or jamming during transit.
- Speed Control: The spacing between rollers can affect the speed at which items travel, with closer rollers providing more support and slower movement for heavier items.
- Directional Flow: Items can be directed using curved sections, guiding them towards specific destinations within a facility.
- Modular Design: Many systems are modular, allowing for easy expansion or reconfiguration to meet changing operational needs.
- Gravity Accumulation: Some systems are designed to accumulate items in certain areas, using brakes or stoppers to control flow without manual intervention.
Key Components of a Gravity Feed Conveyor System
A gravity feed conveyor system comprises several critical components, each playing a pivotal role in its overall functionality and efficiency. From the rollers that facilitate movement to the frames that provide structural support, every element is designed to ensure seamless operation and durability.
- Rollers: The cylindrical components that directly contact moving items. Made from materials like steel, plastic, or coated with rubber for extra grip.
- Frames: The structural support that holds the rollers in place, typically made from steel or aluminum for durability and strength.
- Supports: Legs or stands that hold the conveyor at the required height and incline. Adjustable supports allow for changes in the conveyor’s slope.
- Guide Rails: Optional components that keep items from falling off the sides, ensuring they stay on track during movement.
- End Stops: Placed at the end of the conveyor to prevent items from sliding off, which can be fixed or removable depending on the application.
- Curved Sections: Specialized roller assemblies that allow the conveyor to change direction, facilitating the movement of goods around obstacles.
- Spacers: Used to adjust the spacing between rollers, affecting the speed and stability of items on the conveyor.
- Accumulation Zones: Sections designed with mechanisms to temporarily halt items, allowing for accumulation without back pressure.
Understanding the mechanics and components of gravity feed roller conveyor is crucial for optimizing material handling processes. These systems offer a blend of simplicity, efficiency, and versatility, making them a valuable asset in various operational contexts.
Types of Gravity Feed Conveyor Rollers
Gravity feed conveyor rollers are a versatile and essential component in the material handling industry, offering a range of solutions tailored to various load requirements and operational environments. These rollers are designed to facilitate the smooth and efficient transport of goods with minimal effort, leveraging the natural force of gravity. Below, we explore the diversity within the category of gravity feed conveyor rollers, highlighting their unique features and applications.
Different Types of Gravity Feed Conveyor Rollers
- Light-Duty Rollers: Ideal for small packages and lightweight items, these rollers are typically made from plastic or lightweight metal. They are perfect for applications requiring gentle handling and low to moderate volume throughput.
- Medium-Duty Rollers: Constructed from stronger materials like steel, these rollers can handle heavier loads than their light-duty counterparts. They are suited for a wide range of applications, including retail backroom operations and parcel distribution centers.
- Heavy-Duty Rollers: Designed for the toughest applications, heavy-duty rollers are made from reinforced materials capable of supporting large, heavy loads. They are commonly used in industrial settings, manufacturing plants, and anywhere that requires the movement of heavy goods.
- Stainless Steel Rollers: Offering corrosion resistance, stainless steel rollers are ideal for use in harsh environments or where cleanliness is a priority, such as food processing or pharmaceutical manufacturing.
- Coated Rollers: These rollers feature a rubber or polyurethane coating to increase grip and reduce noise. They are particularly useful for moving fragile items or operating in environments where noise reduction is important.
- Grooved Rollers: Equipped with grooves that can accommodate belts or ropes, grooved rollers are used in applications where additional driving force is needed to move items uphill or at a consistent pace across flat surfaces.
- Tapered Rollers: Designed for curved sections of conveyor systems, tapered rollers ensure items stay on track around bends. Their unique shape allows for smooth transitions and consistent movement through curves.
Powered Roller Conveyors vs. Gravity Feed Conveyor Rollers
While gravity feed conveyor rollers rely on the natural force of gravity to move items, powered roller conveyors introduce several distinctions:
- Energy Source: Powered conveyors require an external power source, typically electric motors, to drive the rollers and move items along the conveyor.
- Control: Powered systems offer greater control over the speed and direction of item movement, allowing for precise handling and positioning.
- Load Capacity: Generally, powered conveyors can handle heavier loads than gravity feed systems due to the additional force provided by the motors.
- Operational Environment: Powered roller conveyors are often used in environments where the consistent movement of goods is critical, regardless of incline or distance.
- Cost: The initial investment and operational costs for powered conveyors are higher due to the complexity of the system and energy consumption.
- Maintenance: Powered systems require more maintenance than gravity feed conveyors, given their mechanical and electrical components.
- Flexibility: Gravity feed conveyors offer more flexibility in setup and can be easily reconfigured or expanded with minimal cost.
- Application: While gravity feed conveyor rollers are preferred for simple, cost-effective material transport, powered roller conveyors are chosen for applications requiring more control, higher speeds, or the movement of heavier loads.
Understanding the types of gravity feed conveyor rollers and the differences between them and powered roller conveyors is crucial for selecting the right system for your material handling needs. Each type offers unique benefits suited to specific applications, ensuring efficient and effective transport of goods across various industries.
Benefits of Using Gravity Feed Conveyor Rollers
Gravity feed conveyor rollers are a staple in the material handling sector, offering a myriad of advantages that streamline operations and enhance efficiency. These systems are ingeniously simple, utilizing the natural force of gravity to facilitate the movement of goods, thereby providing a host of benefits that make them an attractive option for a wide range of industries. Here are nine key benefits of using gravity feed conveyor rollers:
- Cost-Effectiveness: One of the most compelling advantages of gravity feed conveyor rollers is their cost-effectiveness. Without the need for motors or electrical power, these systems significantly reduce energy consumption and operational costs, making them an economical choice for moving goods.
- Efficiency in Moving Goods: Gravity conveyors streamline the transportation of goods within facilities. By allowing items to glide smoothly along the rollers, they expedite the movement process, enhancing overall operational efficiency.
- Ease of Installation and Maintenance: The simplicity of gravity feed conveyor rollers extends to their installation and upkeep. These systems can be easily assembled, reconfigured, and expanded with minimal downtime, while their maintenance requirements are notably low, contributing to longer service life and reduced costs.
- Versatility: Gravity conveyors are remarkably versatile, capable of handling a wide array of materials and products. From lightweight packages to heavier items, these systems can be customized with various roller types and sizes to accommodate different loads and applications.
- Improved Workplace Safety: By automating the movement of goods, gravity feed conveyor rollers minimize the need for manual handling, thereby reducing the risk of injuries and accidents in the workplace. This not only ensures the safety of employees but also contributes to a more productive working environment.
- Scalability: As business needs evolve, gravity conveyor systems can be easily scaled up or down. Additional sections can be integrated seamlessly, allowing businesses to adapt their material handling capacity as required without significant investment.
- Reliability: With fewer moving parts than powered conveyor systems, gravity feed conveyors are less prone to breakdowns and wear, making them a reliable option for continuous, long-term use.
- Environmental Friendliness: By leveraging gravity instead of electrical power, these conveyors are an eco-friendly material handling solution. Their energy-efficient operation aligns with sustainability goals, reducing the carbon footprint of logistics and manufacturing operations.
- Space Optimization: Gravity feed conveyor rollers can be designed to fit specific spatial configurations, including curved paths and flexible layouts. This optimizes the use of available space within facilities, ensuring that material handling processes are streamlined even in constrained environments.
The benefits of using gravity feed roller conveyor underscore their value in efficient, cost-effective, and flexible material handling. Whether for small-scale operations or large industrial applications, these systems offer practical solutions that enhance productivity and operational efficiency.
Choosing the Best Gravity Feed Conveyor Rollers
Selecting the optimal gravity feed conveyor rollers for your operation is crucial to ensure efficiency, durability, and cost-effectiveness. The right system can significantly enhance your material handling processes. Here are key factors and tips to guide you in choosing the best gravity feed conveyor rollers and manufacturers.
Factors to Consider When Selecting Gravity Feed Conveyor Rollers
- Load Capacity: Assess the weight of the items the conveyor will handle. Ensure the rollers and the conveyor structure can support your maximum load without deformation or failure.
- Roller Diameter: The diameter of the rollers affects the types of items the conveyor can handle. Larger diameters are typically used for heavier loads, while smaller diameters are suitable for lighter items.
- Material: Rollers are made from various materials, including steel, plastic, and coated rollers. Choose a material that is suitable for your operation’s environment and the types of goods you are moving.
- Roller Spacing: The distance between rollers impacts the smoothness of the conveyance. Items should span at least three rollers to ensure stability during movement.
- Conveyor Length and Width: Consider the space available in your facility and the size of the items to be transported. Ensure the conveyor dimensions fit your space and operational needs.
- Incline Angle: The slope of a gravity conveyor affects how items move. A steeper incline increases speed but may require additional controls to manage the flow of items.
- Environment: The operating environment can influence your choice. For example, stainless steel rollers are preferable in corrosive environments or where strict hygiene is required.
- Customization Options: Look for flexibility in customization. The ability to add curves, adjustable stands, and side guides can significantly enhance the functionality of your conveyor system.
Tips on Choosing the Right Gravity Roller Conveyor Manufacturers
- Experience: Opt for manufacturers with a proven track record in designing and producing gravity feed conveyor rollers. Experienced manufacturers are more likely to provide reliable and efficient solutions.
- Quality Assurance: Check for quality certifications and standards compliance. Manufacturers committed to quality will ensure their products meet or exceed industry standards.
- Product Range: Choose a manufacturer that offers a wide range of products. A broad selection allows for more tailored solutions to meet your specific needs.
- Customization Capabilities: Ensure the manufacturer can customize conveyor systems to fit unique operational requirements. Customization is key to optimizing your material handling process.
- Technical Support: Look for manufacturers that offer robust technical support, from initial consultation to after-sales service. Good support is crucial for troubleshooting and maintenance.
- Client Testimonials: Seek feedback from current or past customers. Their experiences can provide valuable insights into the manufacturer’s reliability and the performance of their products.
- Warranty and Service Agreements: Understand the warranty coverage and service agreements. A comprehensive warranty indicates the manufacturer’s confidence in their products.
- Lead Times: Consider the manufacturer’s lead times for delivery and installation. Shorter lead times can help minimize downtime and ensure your operations continue smoothly.
- Cost-Effectiveness: While cost should not be the sole deciding factor, compare pricing among manufacturers for similar quality and specifications. Look for competitive pricing without compromising on quality or service.
Choosing the best gravity feed conveyor rollers involves careful consideration of your specific operational needs and thorough research on potential manufacturers. By focusing on these factors and tips, you can select a system and a partner that will provide long-term value and efficiency to your material handling operations.
Heavy Duty Gravity Roller Conveyors
Heavy-duty gravity feed conveyor rollers are engineered to handle more demanding material handling tasks. These robust systems are designed to convey heavier loads over longer distances, providing a reliable and efficient solution for various industrial applications. Below, we delve into the features, benefits, and applications of heavy-duty gravity roller conveyors.
Features and Benefits of Heavy-Duty Gravity Roller Conveyors
- Increased Load Capacity: Heavy-duty conveyors are built with stronger materials and thicker roller walls, enabling them to support significantly heavier loads compared to standard models.
- Durability: Constructed from high-grade steel or reinforced aluminum, these conveyors are designed to withstand harsh industrial environments and resist wear and tear, ensuring long-term reliability.
- Larger Roller Diameter: The rollers in heavy-duty systems are larger in diameter, providing a greater contact area with the items being conveyed. This feature enhances stability and reduces the risk of items toppling over.
- Enhanced Frame Strength: The frames of heavy-duty conveyors are reinforced to support the additional weight, preventing bending or warping under heavy loads.
- Adjustable Height and Width: Many heavy-duty models offer adjustable heights and widths, allowing for customization to specific operational needs and facilitating the handling of a wide range of item sizes.
- Versatile Configuration Options: These systems can be configured with curves, junctions, and merges, enabling complex conveyor layouts that can navigate around obstacles and through various processing areas.
- Low Maintenance: The robust construction and simplicity of gravity feed systems result in lower maintenance requirements, reducing downtime and operational costs.
- Energy Efficiency: Like all gravity conveyors, heavy-duty models require no power to operate for downward or level transport, making them an energy-efficient option for moving heavy items.
Applications and Industries That Benefit Most from Heavy-Duty Options
- Manufacturing and Assembly: Heavy-duty conveyors are ideal for moving large parts and assemblies through manufacturing processes, from initial fabrication to final assembly and inspection.
- Warehousing and Distribution: These systems can handle the heavy loads typical of warehousing operations, including pallets, large containers, and bulky items, facilitating efficient storage and retrieval processes.
- Automotive Industry: Used for transporting engine parts, chassis, and other heavy automotive components through various stages of assembly and testing.
- Construction and Building Materials: Suitable for moving heavy building materials such as bricks, tiles, and lumber, streamlining the supply chain from production to delivery.
- Aerospace: Capable of handling large and heavy aerospace components, including fuselage sections and wings, through the manufacturing and assembly process.
- Food and Beverage: Heavy-duty conveyors can transport large containers, pallets of goods, and bulk items through processing, packaging, and distribution areas.
- Mining and Heavy Equipment: Ideal for moving raw materials, parts, and finished products in the mining and heavy equipment manufacturing sectors.
- Agriculture: Used for transporting feed, grain, and other heavy agricultural products, supporting the operations of large-scale farming and processing facilities.
Heavy-duty gravity feed conveyor rollers offer the strength, durability, and versatility required to handle the most challenging material handling tasks. Their robust construction and efficient operation make them a valuable asset in industries where heavy loads are the norm, ensuring smooth, reliable, and cost-effective movement of goods.
Price Considerations for Gravity Feed Conveyor Rollers
When integrating gravity feed conveyor rollers into your material handling system, understanding the pricing landscape is crucial for budgeting and ensuring you receive value for your investment. The cost of gravity feed conveyor rollers can vary widely based on several factors, from the materials used in their construction to the complexity of the conveyor system.
General Price Range and Influencing Factors
The price for gravity feed conveyor rollers can range from a few dollars per roller for basic models to several hundred dollars for more advanced, heavy-duty versions. Several factors influence the cost:
- Material: Rollers made from high-grade steel or specialized coatings for increased durability tend to be more expensive than basic plastic or aluminum rollers.
- Size and Load Capacity: Larger rollers designed to handle heavier loads typically cost more due to the increased material and structural requirements.
- Customization: Customized conveyor systems designed to fit specific operational needs can significantly increase costs, reflecting the additional design and manufacturing work involved.
- Quantity: Purchasing in bulk often results in lower per-unit costs due to economies of scale.
- Manufacturer: Prices can vary between manufacturers based on their production capabilities, material quality, and additional services offered.
- Additional Features: Rollers with special features, such as coatings for improved grip or noise reduction, can also add to the cost.
- Shipping and Installation: The cost of shipping and professional installation can significantly affect the overall investment in gravity feed conveyor rollers.
- Maintenance and Warranty: Systems that come with extended warranties or lower maintenance requirements might have higher upfront costs but can offer savings over time.
Finding the Best Deals on Gravity Feed Conveyor Rollers
To secure the best deals on gravity feed conveyor rollers, consider the following strategies:
- Compare Quotes: Obtain quotes from multiple suppliers to compare prices and offerings.
- Bulk Purchases: Consider buying in bulk if possible to leverage discounts for large orders.
- Refurbished or Used Options: Explore the market for refurbished or used gravity feed conveyor rollers, which can offer significant savings over new equipment.
- Direct from Manufacturer: Purchasing directly from manufacturers can sometimes offer better deals than buying through distributors due to reduced markups.
- Negotiate: Don’t hesitate to negotiate on price, especially for large orders or if you’re a repeat customer.
- Trade Shows and Industry Events: These can be great opportunities to find deals, as companies often offer special pricing for event attendees.
- Seasonal Sales and Overstock: Manufacturers and distributors sometimes have sales to clear out overstocked items or during certain times of the year.
- Long-term Partnerships: Building a long-term relationship with a supplier can lead to better pricing and terms over time.
By understanding the factors that influence the cost of gravity feed conveyor rollers and employing strategic purchasing practices, businesses can find high-quality conveyor solutions that meet their operational needs without exceeding their budget.
Where to Find Gravity Feed Conveyor Rollers for Sale
Finding the right source for gravity feed conveyor rollers is essential for acquiring quality equipment that meets your material handling needs. Whether you’re looking for new or used options, several avenues can lead you to the best deals and products.
Recommendations for Sourcing Gravity Feed Conveyor Rollers
- Direct Manufacturers: Purchasing directly from manufacturers of gravity feed conveyor rollers often ensures you get the best price and access to the latest technology and customization options.
- Industrial Distributors: Distributors specializing in material handling equipment can offer a wide range of products from different manufacturers, providing the convenience of one-stop shopping.
- Online Marketplaces: Websites like Alibaba, Amazon Business, and eBay offer listings for gravity feed conveyor rollers from various sellers, including both new and used options.
- Trade Shows: Industry trade shows are excellent places to connect directly with manufacturers and distributors, often offering show-exclusive deals.
- Local Dealers: Some local dealers stock gravity feed conveyor rollers and can provide valuable advice, installation services, and after-sales support.
- Refurbished Equipment Suppliers: Companies that specialize in refurbished or reconditioned industrial equipment can be a good source for durable gravity feed conveyor rollers at a reduced cost.
- Auction Sites: Industrial auction sites occasionally list gravity feed conveyor systems as companies upgrade or liquidate assets.
- Specialty Online Retailers: Online retailers focusing on industrial and warehouse equipment often have a selection of gravity feed conveyor rollers, providing detailed product information and customer reviews.
Tips on Purchasing Used Gravity Roller Conveyors for Sale
- Verify Condition: Inspect the condition of the used gravity roller conveyors or request detailed photos and condition reports from the seller.
- Check for Wear and Tear: Pay special attention to the rollers and the frame for any signs of excessive wear, corrosion, or damage.
- Inquire About History: Ask about the age of the conveyor, previous usage, and any repairs or modifications that have been made.
- Consider Compatibility: Ensure the used conveyor will integrate seamlessly with your existing systems in terms of size, load capacity, and material handling requirements.
- Look for Reputable Sellers: Purchase from reputable sellers or platforms that offer buyer protection and have positive reviews or ratings.
- Ask About Returns or Warranties: While used equipment often comes “as-is,” some sellers may offer a short-term warranty or return policy for peace of mind.
- Calculate Total Cost: Consider additional costs such as shipping, installation, and any necessary repairs or modifications when evaluating the price.
- Seek Professional Advice: If unsure, consult with a material handling professional or engineer to assess the suitability and value of the used conveyor for your needs.
- Negotiate Price: Don’t hesitate to negotiate the price based on your findings or if you’re making a bulk purchase.
By carefully selecting your source and doing due diligence when purchasing used gravity feed conveyor rollers, you can secure high-quality equipment that provides reliable service without overspending. Whether opting for new or used, the right gravity feed conveyor rollers can significantly enhance your operation’s efficiency and productivity.
FAQs about Gravity Feed Conveyor Rollers
A gravity conveyor roller is a vital component of a material handling system that utilizes the force of gravity to move goods and materials along a predetermined path. Unlike powered conveyor systems, gravity conveyors do not require electrical power or mechanical systems to operate. Instead, they rely on the slight inclination of the conveyor track or the natural force of gravity to facilitate the movement of items from one point to another. This simple yet effective mechanism makes gravity conveyor rollers an energy-efficient and cost-effective solution for transporting goods, especially over short to medium distances. They are widely used in various industries, including warehousing, manufacturing, and distribution centers, to streamline operations and enhance workflow efficiency.
Conveyor rollers come in several types, each designed to meet specific operational needs and material handling requirements. The primary types include:
Gravity Conveyor Rollers: These rollers rely on gravity to move materials and are typically used in inclined or straight sections for easy movement of goods.
Powered Conveyor Rollers: Equipped with motors, these rollers are used in automated conveyor systems to move materials along the conveyor belt at a controlled speed.
Grooved Conveyor Rollers: Designed with grooves, they are used in conjunction with belts or chains to drive the conveyor.
Tapered Conveyor Rollers: Ideal for curves, tapered rollers ensure materials stay on track when the conveyor changes direction.
Impact Conveyor Rollers: These are used in loading zones to absorb the impact of materials being dropped onto the conveyor, reducing damage to both the conveyor and the materials.
Plastic Conveyor Rollers: Made from durable plastic, these rollers are suitable for light-duty applications and environments where corrosion resistance is necessary.
Stainless Steel Conveyor Rollers: Best for harsh environments, stainless steel rollers are used in food processing, pharmaceuticals, and other industries requiring high levels of cleanliness and corrosion resistance.
The angle of a gravity roller conveyor, often referred to as the pitch or incline, is crucial for its efficient operation. The optimal angle depends on various factors, including the type of materials being transported, their weight, and the desired speed of movement. Typically, the angle ranges from 2 to 5 degrees for most applications, providing a gentle slope that allows items to move smoothly without manual assistance. However, the specific angle can be adjusted based on the operational requirements, with steeper inclines used for lighter items and shallower angles for heavier goods to control their descent and prevent damage.
The type of conveyor that uses gravity to transport materials is known as a gravity conveyor. These conveyors are an economical and efficient solution for moving goods within a facility. Gravity conveyors are particularly favored for their simplicity, low maintenance, and energy efficiency, as they do not require power to operate. They are versatile and can be used in various configurations, including straight sections, curves, and spirals, to accommodate different layouts and space constraints. Gravity conveyors are ideal for a wide range of applications, from warehousing and distribution to manufacturing and retail backrooms, facilitating the smooth and effortless transport of products, boxes, and other materials.
Last Updated on May 23, 2024 by Jordan Smith
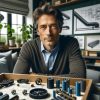
Jordan Smith, a seasoned professional with over 20 years of experience in the conveyor system industry. Jordan’s expertise lies in providing comprehensive solutions for conveyor rollers, belts, and accessories, catering to a wide range of industrial needs. From initial design and configuration to installation and meticulous troubleshooting, Jordan is adept at handling all aspects of conveyor system management. Whether you’re looking to upgrade your production line with efficient conveyor belts, require custom conveyor rollers for specific operations, or need expert advice on selecting the right conveyor accessories for your facility, Jordan is your reliable consultant. For any inquiries or assistance with conveyor system optimization, Jordan is available to share his wealth of knowledge and experience. Feel free to reach out at any time for professional guidance on all matters related to conveyor rollers, belts, and accessories.