Gravity Feed Rollers: Core to Conveyor Systems
Gravity feed rollers are at the heart of gravity roller conveyors, a fundamental component in the material handling industry. These conveyors leverage the force of gravity to move items across flat or slightly inclined paths, offering a simple yet effective means of transporting goods within warehouses, manufacturing plants, and distribution centers. The gravity feed rollers themselves are cylindrical tubes that freely rotate around a central axis, allowing goods to glide over them with minimal effort. This mechanism significantly reduces manual labor and enhances operational efficiency by facilitating the smooth, uninterrupted flow of products. By capitalizing on gravity, these rollers provide a cost-effective solution for moving items, especially in scenarios where powered conveyance is unnecessary or economically unfeasible. As such, gravity roller conveyors, powered by gravity feed rollers, have become indispensable in environments focused on the swift and reliable handling of goods.
Gravity Roller Conveyor Systems with Gravity Feed Rollers
Gravity roller conveyor systems are an essential part of various industries, enabling the smooth and efficient movement of goods across warehouse floors, production lines, and distribution centers. The core component, gravity feed rollers, play a pivotal role in the operation of these systems, utilizing the natural force of gravity to facilitate movement without the need for an external power source.
How Gravity Roller Conveyor Systems Work
The principle behind gravity roller conveyor systems is straightforward. Items are placed on the conveyor’s surface, which is made up of a series of rollers. These rollers are slightly inclined along the conveyor’s path, allowing items to move from a higher point to a lower one due to gravity. The gravity feed rollers, being free to rotate, reduce friction and allow goods to move smoothly over them.
The efficiency of these systems lies in their simplicity and the fact that they do not require electrical power to operate, making them cost-effective and environmentally friendly. They are especially useful for moving items over short to medium distances within a confined space.
Types of Gravity Roller Conveyors
Gravity roller conveyors come in various types to accommodate different industrial needs, including standard, heavy-duty, and plastic versions. The following table provides a quick comparison:
Each type of gravity roller conveyor is designed with specific applications in mind, ensuring that whether the need is for handling delicate items or enduring tough industrial conditions, there is a suitable option. The choice of conveyor depends on several factors, including the weight of the items to be moved, the environment in which the conveyor will operate, and the required durability and maintenance level.
Integrating gravity feed rollers into these systems, regardless of the type, provides a seamless and efficient method for transporting goods. The adaptability and versatility of gravity roller conveyor systems, coupled with their cost-effectiveness and reliability, make them an indispensable solution in the logistics and manufacturing sectors.
Key Features and Benefits of Gravity Feed Rollers
Gravity feed rollers are a cornerstone technology in the realm of material handling, offering a multitude of advantages that streamline operations and enhance efficiency across various industrial sectors. Their design and functionality bring forth an array of benefits that not only optimize the movement of goods but also contribute to the overall productivity and cost-effectiveness of the operations they support.
Advantages of Using Gravity Feed Rollers
- Cost-Effectiveness: Gravity feed rollers operate without the need for electrical power, significantly reducing energy costs and offering a green, cost-efficient solution.
- Simplicity of Design: With fewer moving parts compared to motorized conveyor systems, gravity roller conveyors are easier to install, operate, and maintain.
- Efficiency: The natural force of gravity ensures smooth and continuous movement of goods, enhancing workflow and operational speed.
- Versatility: They can be easily integrated into existing conveyor systems and are adaptable to various types of goods and packaging, making them suitable for a wide range of industries.
- Durability: Built to last, these systems can handle a significant amount of wear and tear, ensuring long-term reliability.
- Low Maintenance: The simplicity of the gravity feed rollers means there’s less that can go wrong, translating into lower maintenance costs and downtime.
- Safety: With no need for external power, these systems are inherently safer, reducing the risk of accidents and injuries.
- Scalability: As operational needs grow, additional modules can be easily added to extend the conveyor system.
- Environmental Impact: The energy-efficient nature of gravity roller conveyors makes them a more environmentally friendly option compared to powered conveyors.
Importance of Heavy-Duty Options for Industrial Applications
- Enhanced Load Capacity: Heavy-duty gravity feed rollers are designed to handle heavier loads, crucial for industries dealing with bulky or heavy materials.
- Increased Durability: These options are built with stronger materials, offering greater resistance to wear and tear and extending the life of the conveyor system.
- Adaptability to Harsh Environments: Heavy-duty systems can withstand harsh industrial environments, including exposure to chemicals, extreme temperatures, and heavy usage.
- Reduced Downtime: The robust construction of heavy-duty rollers minimizes the risk of breakdowns and maintenance, ensuring continuous operation.
- Higher Efficiency in Tough Conditions: They maintain high efficiency even under the strain of heavy loads and rigorous use, crucial for meeting tight production deadlines.
- Cost Savings Over Time: Although the initial investment may be higher, the longevity and reduced maintenance needs of heavy-duty rollers lead to significant cost savings.
- Customization Options: Heavy-duty gravity feed rollers often come with customization options to meet specific industry needs, including size, material, and resistance properties.
Gravity feed rollers, especially the heavy-duty variants, are indispensable in facilitating the efficient, cost-effective, and safe movement of goods across various industrial settings. Their broad range of benefits underscores their critical role in optimizing operations, demonstrating why they are a preferred choice for businesses aiming to enhance their material handling processes.
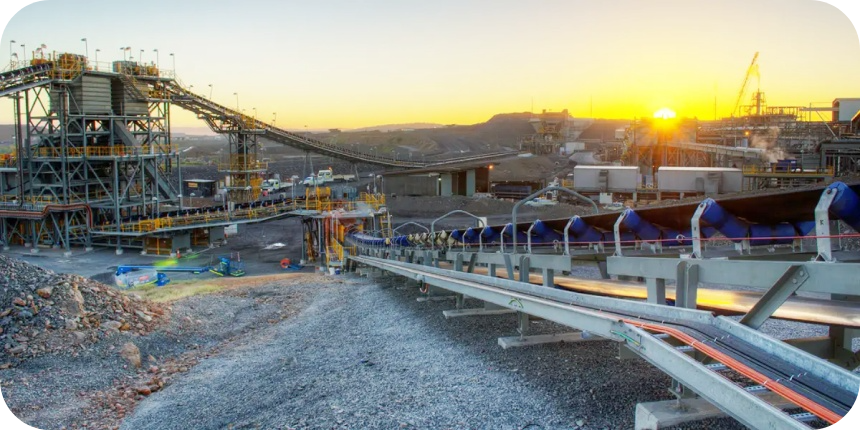
Gravity Feed Rollers for Sale
The market for gravity feed rollers is diverse and vibrant, catering to a wide range of industrial and commercial needs. Whether you’re setting up a new conveyor system or upgrading an existing one, the choice between new and used gravity feed rollers is crucial, impacting both budget and performance.
Overview of the Market for Gravity Rollers
The demand for gravity feed rollers spans across various sectors, including manufacturing, logistics, and retail, reflecting the broad applicability of these systems. The market accommodates this demand by offering both new and used options, providing flexibility in terms of cost and availability.
New Gravity Feed Rollers: Buying new rollers comes with the assurance of top-notch performance, reliability, and the latest technology. Manufacturers often provide warranties and support services, ensuring long-term value for your investment.
Used Gravity Feed Rollers: Opting for used or refurbished rollers can be a cost-effective solution, especially for short-term projects or operations on a tight budget. While used rollers can offer significant savings, it’s important to carefully assess their condition and suitability for your specific needs.
Tips on Where to Find Gravity Feed Rollers for Sale
- Manufacturer Websites: Start by visiting the websites of leading conveyor system manufacturers. They often have catalogues of both new and used gravity feed rollers.
- Industrial Supply Stores: These stores typically stock a range of material handling equipment, including new gravity feed rollers.
- Online Marketplaces: Platforms like eBay, Alibaba, and Amazon can be good sources for finding both new and used options.
- Auctions: Look out for industrial auctions, where you can bid on used gravity feed rollers from businesses that are downsizing or updating their equipment.
- Trade Shows: Material handling and logistics trade shows often feature the latest innovations and products, including gravity feed rollers.
- Local Classifieds: Check out local classified ads in newspapers or online platforms. Businesses in your area might be selling used equipment.
- Refurbishing Companies: Companies that specialize in refurbishing conveyor systems often sell gravity feed rollers at a reduced cost.
- Direct From Factories: Some factories sell their old equipment directly when they upgrade their systems.
- Industrial Forums and Groups: Online forums and social media groups focused on industrial equipment can be excellent resources for leads.
- Networking: Sometimes, the best way to find what you need is through word-of-mouth. Network with industry peers to discover potential sales not advertised publicly.
When looking for gravity feed rollers for sale, it’s crucial to consider your specific needs, such as the weight and type of materials you’ll be moving, the environment in which the rollers will be used, and your budget. Whether you opt for new or used rollers, thorough research and due diligence will ensure you find the best fit for your operation.
Manufacturers of Gravity Feed Rollers
The market for gravity feed rollers is populated by numerous manufacturers, each bringing its own strengths and specialties to the table. Understanding what sets the leading manufacturers apart can significantly impact the efficiency, reliability, and overall success of your conveyor system.
Leading Manufacturers of Gravity Feed Rollers
Several companies stand out in the production of gravity feed rollers due to their commitment to quality, innovation, and customer service. These manufacturers often offer a wide range of products, from standard to heavy-duty and plastic rollers, catering to the diverse needs of industries worldwide.
Interroll: Known for its high-quality rollers, Interroll offers a wide variety of gravity feed rollers designed for efficiency and durability. Their products are a staple in many industries, thanks to their reliability and the company’s global support network.
Hytrol: Hytrol is a well-regarded manufacturer that specializes in conveyor systems, including gravity feed rollers. They are recognized for their custom solutions and extensive dealer network, ensuring clients receive both top-notch products and support.
Conveyor Systems Ltd: Offering a range of material handling solutions, Conveyor Systems Ltd provides gravity feed rollers that are both versatile and efficient. Their focus on tailor-made systems makes them a go-to for businesses requiring bespoke solutions.
Gravity Conveyor Systems, Inc.: This company stands out for its dedication to sustainable and energy-efficient gravity feed rollers. They cater to businesses looking to reduce their carbon footprint without compromising on efficiency.
These manufacturers distinguish themselves through their innovative designs, quality materials, and comprehensive customer support. Investing in gravity feed rollers from reputable manufacturers ensures that you benefit from the latest advancements in material handling technology, along with reliable and efficient operation.
Importance of Selecting Reputable Manufacturers
- Quality Assurance: Renowned manufacturers adhere to strict quality control standards, ensuring that their gravity feed rollers are durable and reliable.
- Innovation: Leading companies invest in research and development, providing you with the most advanced and efficient solutions.
- Customization: Reputable manufacturers often offer customizable solutions to meet specific operational needs, ensuring your conveyor system operates at peak efficiency.
- Technical Support: Access to expert advice and technical support can be invaluable, helping you to resolve issues quickly and maintain productivity.
- Warranty and After-Sales Service: A strong warranty and responsive after-sales service provide peace of mind, knowing that any problems will be addressed promptly.
- Compliance with Industry Standards: Established manufacturers ensure their products comply with relevant industry standards and regulations, reducing the risk of operational disruptions or legal issues.
Choosing gravity feed rollers from reputable manufacturers not only ensures you receive a product that meets your operational needs but also offers long-term reliability and support. This strategic choice can significantly contribute to the efficiency, safety, and success of your material handling operations.
Price Considerations for Gravity Feed Rollers
When planning to purchase gravity feed rollers or entire conveyor systems, understanding the factors that influence pricing is crucial. This knowledge not only helps in budgeting accurately but also ensures that you obtain the best value for your investment. Below are eight key factors affecting the price of gravity feed rollers and conveyor systems, followed by guidance on budgeting effectively.
Factors Affecting the Price of Gravity Feed Rollers
- Material Quality: Higher quality materials such as heavy-duty steel or specialized plastics increase durability but also cost more.
- Load Capacity: Rollers designed to handle heavier loads require more robust materials and construction, leading to higher prices.
- Size and Length: Larger and longer conveyor systems require more materials and labor to construct, directly impacting the price.
- Customization: Custom-designed systems to fit specific operational needs can significantly increase costs due to the additional engineering and manufacturing required.
- Brand Reputation: Established brands with proven reliability and customer support may command premium prices for their products.
- Technological Features: Advanced features, such as integrated sensors or automation compatibility, can add to the cost.
- Market Demand: Fluctuations in demand for gravity feed rollers can influence pricing, with higher demand potentially driving up costs.
- Shipping and Installation: The cost of shipping and professional installation can vary widely and should be considered when budgeting.
Budgeting for Gravity Roller Conveyors
Assess Your Needs: Clearly define what you need from your conveyor system. Consider the types of items you’ll be moving, the environment in which the system will operate, and any specific features you require. This assessment will help you avoid paying for unnecessary features.
Get Multiple Quotes: Contact several suppliers to get a range of quotes. This will give you a better idea of the market rates and help identify the best value offers.
Consider Total Cost of Ownership (TCO): Beyond the initial purchase price, consider maintenance, repair, and operational costs over the system’s lifetime. A cheaper initial option might end up being more expensive in the long run.
Look for Modular Options: Modular conveyor systems can offer both flexibility and cost savings, as they allow you to add or reconfigure sections as needed without investing in a completely new system.
Used and Refurbished Options: For tighter budgets, consider high-quality used or refurbished gravity feed rollers. Ensure they have been properly serviced and come from a reputable source.
Plan for Future Needs: Investing a little more upfront for scalability can save significant costs down the line if your operational needs grow.
Negotiate: Don’t be afraid to negotiate on price, especially if you are making a large purchase or planning a long-term partnership with the supplier.
Apply for Financing or Leasing Options: If upfront costs are a concern, inquire about financing or leasing options that can spread the cost over time.
By understanding the factors that influence the cost of gravity feed rollers and employing strategic budgeting, you can ensure that your investment enhances your operational efficiency and provides the best value over its lifespan.
Design and Customization of Gravity Feed Rollers
Gravity feed rollers are a versatile component in the material handling industry, capable of being tailored to meet a wide range of specific operational requirements. The design and customization of these systems play a pivotal role in optimizing efficiency, enhancing productivity, and ensuring the smooth transportation of goods across various sectors. Here, we explore the customization options available for gravity roller conveyors and delve into the critical role design plays in meeting industry-specific needs.
Customization Options for Gravity Roller Conveyors
Length and Width: The size of the conveyor can be adjusted to fit the spatial constraints of the operating environment or to accommodate the size of the goods being transported. This ensures that the system is neither too large nor too small for its intended use, optimizing space and efficiency.
Roller Diameter: Depending on the weight and size of the items to be moved, the diameter of the rollers can be customized. Larger diameters are typically used for heavier items, as they distribute weight more evenly and reduce the chance of deformation under load.
Material: Gravity feed rollers are made from various materials, including steel, aluminum, and plastic. The choice of material can depend on the specific application, such as the need for corrosion resistance in a humid environment or the requirement for a lightweight system that can be easily reconfigured.
Coating and Surface Treatments: Rollers can be coated or treated to enhance their properties, such as increasing grip, reducing noise, or adding resistance to chemicals. This customization option is crucial for industries with specific operational challenges, such as food processing or pharmaceuticals.
Role of Design in Maximizing Efficiency and Meeting Industry Needs
- Ergonomics: Properly designed systems improve the ergonomics for workers, reducing strain and the potential for injury, thereby increasing productivity and safety.
- Integration: Custom designs can ensure seamless integration with existing systems and workflows, minimizing disruptions and enhancing overall operational flow.
- Adaptability: The ability to customize the design for specific items or conditions means that gravity feed rollers can be used across a wide range of industries, from heavy manufacturing to delicate electronics assembly.
- Cost-Effectiveness: Efficient design can reduce the need for excessive manual handling or motorized equipment, leading to significant cost savings in energy and labor.
- Maintenance and Durability: Customization can also focus on making systems easier to maintain and more durable, reducing downtime and extending the life of the equipment.
- Space Optimization: By designing systems to fit specific spaces, businesses can make the most of their available area, improving storage and handling capacities.
- Performance Enhancements: Design can be used to optimize the speed and smoothness of item transportation, reducing bottlenecks and improving throughput.
- Compliance and Safety: Custom designs can ensure that conveyor systems meet industry-specific regulations and safety standards, protecting both workers and products.
The design and customization of gravity feed rollers are critical components in creating efficient, productive, and safe material handling systems. By leveraging these customization options, businesses can craft solutions that meet their unique requirements, enhancing their operations and providing a competitive edge in their respective industries.
Heavy-Duty Gravity Roller Conveyors with Gravity Feed Rollers
Heavy-duty gravity roller conveyors are designed to withstand the rigors of challenging industrial environments, where durability, strength, and the capacity to handle heavy loads are paramount. These systems incorporate gravity feed rollers that are specifically engineered to manage heavier weights and endure the wear and tear of constant use. Their significance in industrial applications cannot be overstated, offering numerous advantages and proving essential in various sectors.
Significance of Heavy-Duty Options for Challenging Industrial Environments
- Enhanced Durability: Constructed from high-strength materials, heavy-duty conveyors are built to last, resisting damage and deformation under heavy loads.
- Increased Load Capacity: These systems are designed to handle significantly heavier items, making them ideal for industries that transport large, bulky, or heavy products.
- Resistance to Harsh Conditions: Heavy-duty gravity feed rollers are often treated or constructed with materials resistant to corrosion, heat, and other harsh environmental conditions.
- Reduced Maintenance Requirements: The robust construction of heavy-duty systems means they require less frequent maintenance, despite the demanding conditions they operate in.
- Improved Safety: Handling heavy loads with appropriately designed equipment reduces the risk of accidents and injuries, enhancing workplace safety.
- Versatility in Application: These conveyors can be customized to fit specific industrial needs, accommodating a wide range of product sizes and weights.
- Efficiency in Operations: Heavy-duty conveyors facilitate the smooth and efficient movement of goods, improving operational workflows and productivity.
- Long-Term Cost Savings: While the initial investment may be higher, the longevity and reduced maintenance of heavy-duty systems offer substantial cost savings over time.
- Environmental Resilience: Designed to withstand dust, debris, and moisture, these conveyors ensure continuous operation in environments that might compromise less robust systems.
Industries That Benefit from Heavy-Duty Gravity Feed Rollers
Manufacturing: From automotive parts to heavy machinery, manufacturing industries require conveyors that can handle substantial weights and sizes without faltering.
Logistics and Warehousing: These sectors benefit from heavy-duty conveyors for moving large containers, pallets, and bulk goods efficiently across warehouse floors.
Construction Materials: Handling building materials such as bricks, steel beams, and precast concrete demands the strength and durability of heavy-duty systems.
Mining and Minerals Processing: The rough and abrasive materials common in mining operations necessitate the use of conveyors that can endure such conditions and weights.
Agriculture: For moving large quantities of grain, feed, or equipment, heavy-duty gravity feed rollers provide the necessary robustness and capacity.
Food and Beverage: Large-scale operations in this industry, especially those involving bulk ingredients or heavy packaging, benefit from the durability and hygiene features of heavy-duty conveyors.
Recycling and Waste Management: The heavy and unpredictable loads common in recycling centers are well-suited to the strengths of heavy-duty gravity roller conveyors.
Aerospace and Defense: Handling large components and materials in these high-tech industries requires the precision and reliability of heavy-duty systems.
Energy Sector: Whether for oil, gas, or renewable energy components, the ability to transport heavy equipment smoothly and efficiently is crucial.
Heavy-duty gravity roller conveyors, equipped with robust gravity feed rollers, are indispensable in environments where the demands on material handling equipment are greatest. These systems not only enhance operational efficiency and safety but also offer the durability and reliability that industries depend on to maintain continuous, heavy-load operations.
Plastic Gravity Roller Conveyors with Gravity Feed Rollers
Plastic gravity roller conveyors offer a versatile and efficient material handling solution, leveraging the unique properties of plastic gravity feed rollers to provide a range of advantages over traditional metal options. These conveyors are designed to facilitate the smooth and effortless movement of goods, utilizing the natural force of gravity, while addressing specific challenges such as weight limitations and environmental corrosion.
Advantages of Plastic Gravity Rollers
Reduced Weight: Plastic rollers are significantly lighter than their metal counterparts, making the conveyors easier to install, reconfigure, and move as needed. This reduced weight can lead to lower shipping costs and less strain on the conveyor frame and supports.
Corrosion Resistance: Plastic is inherently resistant to corrosion, making plastic gravity feed rollers ideal for environments where moisture, chemicals, or corrosive substances are present. This characteristic extends the life of the conveyor and reduces maintenance needs.
Lower Noise Levels: Plastic rollers operate more quietly than metal rollers, contributing to a more pleasant and less disruptive work environment. This can be particularly beneficial in settings where noise reduction is a priority.
Cost-Effectiveness: While offering comparable durability, plastic rollers can be more cost-effective than metal rollers, especially when considering their longevity and reduced maintenance requirements.
Gentler on Materials: The smoother surface of plastic rollers can be gentler on the items being transported, reducing the risk of damage. This makes plastic conveyors suitable for delicate or finely finished products.
Customization: Plastic offers excellent customization options, including the ability to incorporate colors or additives for UV protection, anti-static properties, or increased strength, allowing for tailored solutions to meet specific operational needs.
Suitable Applications for Plastic Gravity Roller Conveyors
Food and Beverage Industry: The corrosion resistance and easy-to-clean nature of plastic make these conveyors suitable for food processing areas, especially where washdown processes are frequent.
Pharmaceuticals and Cleanrooms: Plastic conveyors are ideal for environments that require high levels of cleanliness and contamination control, as they can withstand regular cleaning and do not rust.
Packaging and Distribution: The lightweight and adaptable design of plastic gravity roller conveyors make them perfect for packaging lines and distribution centers, where flexibility and efficiency are key.
Marine and Outdoor Applications: The corrosion-resistant properties of plastic are advantageous for operations exposed to saltwater or outdoor conditions.
Electronics Manufacturing: Anti-static plastic rollers can be used to safely transport sensitive electronic components, reducing the risk of electrostatic discharge (ESD).
Chemical Industry: For environments where chemical exposure is common, plastic conveyors offer a durable solution without the risk of corrosion.
Plastic gravity roller conveyors with gravity feed rollers represent a flexible, efficient, and cost-effective solution for a wide range of material handling challenges. By providing significant advantages in terms of weight, noise reduction, and resistance to corrosion, these systems are well-suited to meet the needs of industries requiring delicate handling, clean operations, and adaptability to harsh environments.
Selecting the Right Gravity Roller Conveyor with Gravity Feed Rollers
Choosing the appropriate gravity roller conveyor is crucial for optimizing efficiency, minimizing maintenance, and ensuring smooth operations in various industrial settings. The selection process involves a detailed assessment of operational needs, including considerations for load capacity, size of goods, and the operating environment. This guide outlines how to select the right gravity roller conveyor with gravity feed rollers to meet your specific requirements.
Assessing Operational Needs
Load Capacity: The first step in selecting a conveyor is to determine the maximum weight of the goods it will need to handle. This includes both the weight of individual items and the total weight when multiple items are on the conveyor at the same time. Heavy-duty gravity feed rollers are designed for larger, heavier loads and offer enhanced durability and strength.
Size of Goods: The size of the items to be transported will influence the width of the conveyor and the spacing between rollers. Ensure that the conveyor you choose can accommodate the largest item’s dimensions without risk of tipping or jamming. For very small items, consider conveyors with smaller roller diameters and closer spacing to prevent items from falling between rollers.
Environment: The operating environment is a critical factor in selecting a gravity roller conveyor. For example, plastic gravity feed rollers are ideal for environments with moisture or chemical exposure, while steel rollers might be preferable in high-temperature conditions. Additionally, the environment will dictate whether you need rollers with special coatings or materials for resistance to corrosion, static, or other factors.
Request a quote and more details about our Gravity roller conveyor by filling out the form.
Key Considerations for Selection
Flexibility and Scalability: Consider future needs and the potential for operational changes. Modular conveyors offer the flexibility to be reconfigured or expanded as required.
Material and Construction: The material of the gravity feed rollers and the frame construction affect the conveyor’s durability, maintenance requirements, and suitability for specific applications. Choose materials that match your operational demands, such as aluminum for lightweight operations or steel for high-capacity applications.
Ease of Maintenance: Look for systems designed for easy maintenance, including accessible roller bearings and modular components that can be easily replaced or upgraded.
Manufacturer and Support: Selecting a conveyor from a reputable manufacturer ensures reliability and quality. Consider manufacturers who offer good customer support, including installation, maintenance, and access to replacement parts.
Cost: While cost is always a consideration, it should be balanced against quality, durability, and the long-term operational efficiency of the conveyor system. Investing in a higher-quality system may offer better value over its lifespan.
Customization Options: Depending on your specific needs, you may require customized solutions, such as adjustable heights, specific roller coatings, or built-in curves and bends. Ensure the manufacturer can accommodate these customizations.
By thoroughly assessing these factors, you can ensure that you select the right gravity roller conveyor for your operations. The ideal system will not only meet current operational needs but also accommodate future growth and changes, providing a scalable, efficient, and cost-effective solution for material handling.
FAQs about Gravity Feed Rollers
What is gravity roller?
A gravity roller is a pivotal component of a gravity roller conveyor system, which is designed to facilitate the movement of goods across short to medium distances without the use of external power. These rollers are cylindrical tubes that allow items to glide over them with ease, leveraging the natural force of gravity. Mounted within a frame and aligned in a series, gravity rollers create a smooth and flat surface for goods to transit from one point to another. The simplicity of their design and operation makes gravity rollers a cost-effective and efficient solution for many material handling needs, ensuring the seamless transport of goods in warehouses, manufacturing plants, and distribution centers.
Gravity rollers can be made from various materials, each selected for its specific properties and the requirements of the application. Common materials include steel, aluminum, and plastic. Steel rollers are renowned for their strength and durability, making them ideal for heavy-duty applications where they might bear significant weights. Aluminum rollers are lighter, making them easier to install and maneuver, and are often used in applications where portability or ease of adjustment is important. Plastic rollers offer the advantage of being corrosion-resistant, quieter in operation, and lighter than metal options, making them suitable for environments sensitive to noise, corrosion, or where a lightweight system is beneficial. The choice of material affects the roller’s performance, durability, and suitability for different environments and loads.
The primary purpose of rollers in a conveyor system is to provide a smooth, stable surface that supports and moves goods along the conveyor’s length. Rollers minimize friction and facilitate the easy flow of goods, either by manual push, gravity (in the case of gravity rollers), or motor-driven force in powered conveyor systems. They are crucial for distributing the weight of goods evenly, preventing damage to both the conveyor system and the products being moved. Rollers also play a significant role in determining the conveyor’s load capacity, speed, and efficiency. In essence, rollers are the backbone of a conveyor system, enabling the efficient, safe, and controlled movement of goods across various distances and environments.
Conveyors are used to transport goods, materials, and products within a facility, between different stages of a process, or along assembly and packing lines. They are instrumental in increasing efficiency, reducing manual handling, improving safety, and optimizing workflows in various settings, including manufacturing plants, warehouses, distribution centers, airports, and supermarkets. Conveyors are versatile tools that can handle a wide range of items, from small components to large pallets of goods, across different industries. They are used for sorting, assembling, inspecting, and packing products, making them indispensable in the automotive, food and beverage, pharmaceutical, electronics, and many other industries. By automating the movement of goods, conveyors help minimize labor costs, reduce processing times, and enhance overall productivity within operational processes.
Last Updated on July 31, 2024 by Jordan Smith
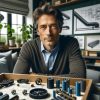
Jordan Smith, a seasoned professional with over 20 years of experience in the conveyor system industry. Jordan’s expertise lies in providing comprehensive solutions for conveyor rollers, belts, and accessories, catering to a wide range of industrial needs. From initial design and configuration to installation and meticulous troubleshooting, Jordan is adept at handling all aspects of conveyor system management. Whether you’re looking to upgrade your production line with efficient conveyor belts, require custom conveyor rollers for specific operations, or need expert advice on selecting the right conveyor accessories for your facility, Jordan is your reliable consultant. For any inquiries or assistance with conveyor system optimization, Jordan is available to share his wealth of knowledge and experience. Feel free to reach out at any time for professional guidance on all matters related to conveyor rollers, belts, and accessories.