Maximize Efficiency with Gravity Roll On Conveyors
In the realm of material handling, businesses constantly seek solutions that optimize efficiency, reduce costs, and streamline operations. Among the myriad of options available, gravity roll on conveyors stand out as a prime choice for those looking to enhance their material flow. These conveyors leverage the natural force of gravity to move products and materials from one point to another, eliminating the need for external power sources. This not only makes them an environmentally friendly option but also significantly reduces operational costs. As an efficient and cost-effective solution, gravity roll on conveyors have become a staple in warehouses, distribution centers, and manufacturing facilities worldwide, offering a simple yet effective way to transport goods across short to medium distances. Their simplicity in design and ease of integration into existing systems make them an attractive option for businesses looking to improve their material handling processes.
What is a Gravity Roll On Conveyor
A gravity conveyor is a pivotal piece of material handling equipment that facilitates the transportation of goods across a defined pathway. Utilizing the natural force of gravity, these conveyors efficiently move items without the need for an external power source. Here, we delve into the essence of gravity conveyors, highlighting their definition, functionality, and diverse applications across industries.
Definition and Explanation of Gravity Conveyors
Gravity conveyors, a cornerstone in the material handling industry, epitomize simplicity and efficiency in motion. These systems harness the natural force of gravity to facilitate the movement of goods, offering a seamless, low-energy solution for transporting items across various distances. Characterized by their straightforward design, gravity conveyors consist of rollers or skate wheels set within a frame, creating an effortless pathway for goods to travel. Below, we explore the fundamental aspects that define gravity conveyors and underscore their significance in operational settings.
- Core Mechanism: Gravity conveyors operate on the basic principle of gravity, leveraging the earth’s pull to initiate movement of goods along the conveyor’s path without the need for motorized power.
- Structure: They are constructed with a series of rollers or skate wheels mounted on a sturdy frame, providing a smooth surface that supports and propels items forward.
- Versatility: Designed to accommodate a diverse array of products, gravity conveyors can handle items ranging from lightweight packages to heavy pallets, making them suitable for various applications.
- Cost-Effectiveness: The absence of electrical components not only minimizes energy consumption but also significantly reduces the operational costs associated with these conveyors.
- Ease of Installation: Their simplistic design ensures that gravity conveyors can be easily installed and integrated into existing workflows with minimal disruption.
- Low Maintenance: With fewer moving parts compared to motorized systems, gravity roll on conveyors demand minimal maintenance, enhancing their reliability and longevity.
- Modularity: Gravity conveyors offer the advantage of modularity, allowing for easy expansion or reconfiguration to meet evolving business needs or spatial constraints.
How Gravity Conveyors Work and Their Applications in Various Industries
Gravity conveyors stand as a testament to the power of simplicity, efficiently moving goods across facilities without the reliance on external energy sources. By capitalizing on the gravitational force, these conveyors ensure a smooth transition of items from one point to another, fostering productivity and operational efficiency. Here, we delve into the operational dynamics of gravity conveyors and their widespread applications across a spectrum of industries.
- Principle of Operation: Items are either manually pushed onto the conveyor at a slight incline or loaded from a height, allowing gravity to facilitate their journey to the designated endpoint.
- Warehouse and Distribution: In these settings, gravity conveyors streamline the sorting, assembly, and transportation of goods, significantly enhancing workflow efficiency.
- Manufacturing: They play a crucial role in moving materials to production lines and transporting finished goods towards packaging sections, thereby optimizing manufacturing processes.
- Retail and E-commerce: Gravity conveyors expedite order fulfillment processes, from the initial picking of items to their eventual packaging and dispatch.
- Food and Beverage: These conveyors are instrumental in moving packaged goods and ingredients through processing areas, adhering to stringent hygiene and safety standards.
- Pharmaceuticals: In the pharmaceutical industry, gravity conveyors facilitate the gentle handling and transport of sensitive products to packaging and distribution areas.
- Agriculture: They assist in the efficient movement of harvested produce and related materials through various stages of processing.
- Recycling and Waste Management: Gravity conveyors efficiently manage the movement of recyclable materials and waste through sorting and processing facilities.
By integrating gravity roll on conveyors into their operations, industries benefit from an eco-friendly, cost-effective, and adaptable solution that significantly enhances material handling processes. These conveyors not only exemplify efficiency and sustainability but also adapt to the unique demands of diverse operational environments.
Key Features of Gravity Roll On Conveyor Design
The design of a gravity roll on conveyor is a marvel of engineering simplicity and efficiency, embodying principles that cater to a wide array of material handling needs. This section delves into the core design features that make gravity roll on conveyors an indispensable asset in warehouses, distribution centers, and manufacturing facilities.
At the heart of gravity roll on conveyor design lies the objective to facilitate smooth, effortless movement of goods by capitalizing on gravity. These conveyors are ingeniously crafted to minimize friction and maximize efficiency, ensuring that goods can be transported with minimal manual intervention. The design is inherently simple, focusing on durability, ease of use, and flexibility, making it a go-to solution for businesses looking to optimize their operations.
Importance of Roller Diameter, Frame Material, and Roller Spacing
The design of gravity roll on conveyors is a study in precision engineering, where every element plays a critical role in the system’s overall efficiency and functionality. Among these, the roller diameter, frame material, and roller spacing are paramount, each contributing uniquely to the conveyor’s performance. These components are the building blocks of a gravity conveyor system, dictating its durability, load capacity, and the range of applications it can efficiently serve. Understanding the interplay between these factors is essential for optimizing conveyor design to meet specific operational requirements.
- Roller Diameter: The diameter of the rollers is a critical factor that influences the type of goods the conveyor can handle. Larger diameters are suited for heavier loads, providing greater stability and reducing the likelihood of deformation under weight.
- Frame Material: The durability and longevity of a gravity roll on conveyor are significantly determined by its frame material. Steel frames offer robustness for heavy-duty applications, while aluminum provides a lightweight alternative for less intensive use.
- Roller Spacing: Optimal roller spacing ensures that items remain stable during transit. Too wide, and small items may sag or get stuck; too narrow, and it may add unnecessary weight and cost to the conveyor.
- Load Capacity: Directly related to roller diameter and spacing, the load capacity must be considered to prevent system overload and ensure efficient operation.
- Ease of Maintenance: Design features like easily replaceable rollers and modular components contribute to the conveyor’s longevity and continuous performance.
- Adaptability: The ability to adjust the height and slope of the conveyor allows for versatile use across different operational setups.
- Safety Features: Incorporating guards and emergency stops enhances the safety of operators, a crucial aspect of conveyor design.
Discussing the Versatility of Gravity Roller Conveyors
Gravity roll on conveyors are celebrated for their adaptability, a feature that stems from their thoughtful design and the variety of configurations available. This versatility is not just about moving goods from point A to B; it’s about how these conveyors can be tailored to fit into any operational environment, whether it involves navigating tight corners, adapting to variable loads, or integrating with other conveyor systems. The ability to customize and adjust these conveyors to specific needs makes them invaluable assets in diverse industries, showcasing their capability to enhance efficiency and productivity in myriad material handling scenarios.
- 90-Degree Solutions: Gravity roll on conveyors can be designed to navigate corners with 90-degree turns, facilitating flexible layout designs within confined spaces.
- Flexible Roller Conveyors: These conveyors extend and bend, allowing for dynamic changes in the path and accommodating irregular warehouse layouts.
- Modular Design: The modular nature allows for easy expansion or reconfiguration, adapting to growing or changing business needs.
- Integration Capability: Gravity roll on conveyors can seamlessly integrate with powered conveyor systems, creating hybrid systems that leverage the best of both worlds.
- Variety of Roller Materials: Rollers can be made from plastic, steel, or coated with rubber, each offering unique benefits for different types of cargo.
- Adjustable Heights: Some designs allow for height adjustment, providing flexibility across various operations and facilitating ergonomic loading and unloading.
- Indoor and Outdoor Use: With the right materials and coatings, these conveyors can be used in both indoor and outdoor settings, resisting weather and wear.
- Sustainability: By using gravity instead of power, these conveyors offer an eco-friendly solution, reducing energy consumption and operational costs.
The design intricacies of gravity roll on conveyors underscore their utility and versatility in material handling. From accommodating heavy loads with ease to offering flexible layout options, these conveyors are tailored to meet the diverse needs of modern businesses, ensuring that goods are moved efficiently, safely, and cost-effectively.
Benefits of Gravity Roll-On Conveyors
The gravity roll on conveyor system stands as a paragon of efficiency and practicality in the realm of material handling. Its design leverages the natural force of gravity to move items, minimizing the need for external power sources and thereby offering a plethora of advantages. Here, we delve into the myriad benefits that underscore the value of incorporating gravity roll on conveyors into operational workflows.
- Cost-Effectiveness: The inherent energy efficiency of gravity roll on conveyors translates directly into cost savings. With no need for electric motors or complex machinery, these systems significantly reduce energy consumption and operational expenses.
- Energy Efficiency: By utilizing gravity as the driving force, these conveyors embody sustainability. They operate without electricity, making them an eco-friendly choice for businesses conscious of their carbon footprint.
- Ease of Installation: The simplicity of gravity roll on conveyor design ensures that installation is straightforward and quick. This ease of setup allows businesses to integrate these systems into their operations without significant downtime.
- Minimal Maintenance: The lack of motorized parts not only reduces energy consumption but also minimizes the need for ongoing maintenance. This leads to lower operational costs and less downtime for repairs.
- Flexibility in Handling Various Types of Goods: Gravity roll on conveyors are adept at transporting a wide range of items, from lightweight packages to heavier pallets, making them versatile tools in numerous industries.
- Modularity and Scalability: These conveyors are designed to be modular, allowing for easy expansion or reconfiguration. Businesses can adapt their conveyor systems as their needs evolve, ensuring long-term utility.
- Improved Safety: With fewer moving parts and no electrical components, gravity roll on conveyors present a lower risk of accidents, contributing to a safer workplace environment.
- Enhanced Productivity: The efficiency of moving goods via gravity assists in streamlining operations, reducing manual handling, and speeding up the process of transporting items within facilities.
- Integration with Other Systems: Gravity roll on conveyors can be seamlessly integrated with powered conveyor systems, creating comprehensive material handling solutions that leverage the strengths of both technologies.
The benefits of gravity roll on conveyors extend beyond mere operational efficiency and cost savings. They embody an approach to material handling that is sustainable, adaptable, and inherently safe. By capitalizing on the simplicity of gravity, these conveyors offer businesses a reliable and effective means of enhancing their operational workflows, making them an indispensable asset in the modern material handling landscape.
Types of Gravity Roll On Conveyors
The gravity roll on conveyor ecosystem is diverse, with each type designed to meet specific operational needs and spatial configurations. This variety ensures that businesses can find the perfect fit for their material handling requirements, enhancing efficiency and productivity. Below, we explore seven distinct types of gravity roll on conveyors, highlighting their unique features and applications.
Standard Gravity Roller Conveyors
The backbone of many material handling systems, standard gravity roller conveyors, are versatile and straightforward, ideal for moving items of various sizes and weights across flat or slightly inclined surfaces.
- Construction: Comprised of a series of metal rollers mounted on a sturdy frame.
- Operation: Utilizes gravity to move goods, requiring a slight incline for optimal performance.
- Load Capacity: Designed to accommodate a wide range of load weights, from lightweight packages to heavier boxes and pallets.
- Applications: Widely used in warehouses, distribution centers, and manufacturing plants for sorting, assembly, and transport tasks.
- Flexibility: Can be customized with different conveyor roller sizes and spacings to handle various product types.
- Ease of Integration: Easily integrates with other conveyor systems for a seamless material handling solution.
- Cost-Effectiveness: Offers an economical solution for moving goods without the need for powered systems.
90-Degree Roller Conveyors for Corner Turns
Specifically designed to navigate corners, 90-degree roller conveyors are essential for facilities that require directional changes in their conveyor layout without manual intervention.
- Design: Features curved sections that guide goods around corners.
- Space Efficiency: Maximizes the use of available space by facilitating sharp turns.
- Compatibility: Works well with standard gravity roller conveyors for a cohesive system.
- Application: Ideal for facilities with limited space or complex layouts.
- Load Handling: Capable of smoothly handling goods as they change direction.
- Installation: Can be easily added to existing conveyor systems to improve layout flexibility.
- Versatility: Suitable for a variety of industries, including packaging, distribution, and manufacturing.
Flexible Roller Conveyors for Adjustable Layouts
Flexible roller conveyors offer unparalleled adaptability, with sections that can be expanded, contracted, and curved to fit the specific needs of any operational space.
- Adjustability: Length and shape can be adjusted to accommodate temporary or changing layouts.
- Portability: Often designed to be lightweight and easily moved to where they are needed most.
- Ease of Storage: Can be compacted for storage when not in use, saving valuable floor space.
- Application: Perfect for loading docks, shipping areas, and temporary assembly lines.
- Material: Constructed from durable materials that can withstand varying weights and usage intensities.
- Setup: Quick and easy to set up, requiring minimal tools and effort.
- Efficiency: Enhances operational efficiency by allowing for rapid reconfiguration of material handling routes.
Skatewheel Gravity Conveyors
Overview: Skatewheel gravity conveyors are a lightweight alternative to roller conveyors, using a series of small wheels to transport goods. They are particularly effective for lighter loads and items with a solid base.
- Design: Consists of multiple skatewheels mounted on axles and attached to the conveyor frame.
- Operation: The skatewheels provide less friction than rollers, making it easier for lighter goods to move.
- Load Capacity: Best suited for lighter items; however, they can accommodate a variety of shapes and sizes.
- Applications: Ideal for parcel handling, packaging lines, and assembly areas where items need to be manually pushed or gravity moved.
- Flexibility: The wheel arrangement allows for smooth movement in straight or curved paths.
- Ease of Integration: Can be easily connected with other types of gravity conveyors for a comprehensive system.
- Portability: Often designed to be more portable than roller conveyors, allowing for quick reconfiguration.
Heavy-Duty Gravity Roller Conveyors
Overview: Engineered for the toughest applications, heavy-duty gravity roller conveyors are built to handle heavy loads, such as pallets, drums, and large containers, with ease and reliability.
- Construction: Features robust rollers, usually made of steel, and a heavy-duty frame to support substantial weights.
- Operation: Utilizes gravity to move heavy loads along the conveyor path, often requiring a more significant incline than standard conveyors.
- Load Capacity: Designed to support the heaviest loads in a warehouse or manufacturing environment.
- Applications: Commonly used in manufacturing, warehousing, and distribution centers dealing with heavy goods.
- Durability: Constructed to withstand harsh conditions and heavy use without significant wear.
- Integration: Can be integrated with powered conveyor systems for a seamless transition between different sections of a material handling system.
- Safety Features: Often equipped with additional safety features to handle heavy loads safely, such as wider roller centers and enhanced side guards.
Each type of gravity roll on conveyor brings its own set of advantages to the table, catering to different operational needs and spatial configurations. From the standard workhorse of the material handling industry to specialized solutions for corner navigation and layout flexibility, gravity roll on conveyors continue to be an essential component of efficient, cost-effective, and adaptable material handling systems.
Gravity Roll On Conveyor Prices and Purchasing Tips
Navigating the market for gravity roll on conveyors can be a complex process, with a variety of factors influencing the price and considerations to ensure you select the right system for your needs. Understanding these elements can help you make an informed decision, ensuring optimal efficiency and value for your investment.
Factors Affecting the Price of Gravity Roll-On Conveyors
When delving into the market for gravity roll on conveyors, it’s crucial to recognize that a myriad of factors come into play, influencing the final price tag of these essential material handling solutions. From the construction materials to the intricacies of design and manufacturer reputation, each element contributes to the overall cost. Understanding these factors is key to navigating the purchasing process effectively, ensuring you get the best value for your investment while meeting your operational requirements.
- Material Quality: The durability and type of materials used (steel, aluminum, plastic) significantly impact the cost.
- Length and Width: The dimensions of the conveyor affect material usage and, consequently, the price.
- Roller Diameter: Larger diameters can handle heavier loads but also increase the cost.
- Load Capacity: Conveyors designed to support heavier loads require more robust materials and construction, raising the price.
- Customization: Custom features tailored to specific operational needs can add to the overall cost.
- Brand and Manufacturer: Premium brands or manufacturers with a reputation for quality may command higher prices.
- Shipping and Handling: The cost of shipping large and heavy equipment can be significant, especially for international orders.
- Installation and Support: Some suppliers include installation and ongoing support in their pricing, while others charge extra.
Tips for Purchasing the Right Gravity Conveyor for Your Needs
Selecting the right gravity roll on conveyor for your business is more than just a purchase; it’s an investment in your operational efficiency and future growth. With numerous options available, making an informed decision requires a deep dive into specific considerations that can impact both the performance and cost-effectiveness of your conveyor system. These tips aim to guide you through the purchasing process, highlighting critical aspects to consider, from assessing your current and future needs to understanding the total cost of ownership. Armed with this knowledge, you can confidently choose a gravity conveyor that aligns with your operational goals and budget constraints.
- Assess Your Load Requirements: Understand the weight, size, and type of materials you’ll be moving to determine the necessary specifications.
- Consider Future Needs: Opt for a system that can accommodate potential growth or changes in your operations.
- Compare Material Durability: Choose materials that offer the best balance of durability and cost for your specific environment.
- Look for Modularity: Modular systems can be easily expanded or reconfigured, providing greater flexibility.
- Evaluate the Total Cost of Ownership: Consider not just the purchase price but also maintenance, repair, and operational costs over the conveyor’s lifespan.
- Request Quotes from Multiple Suppliers: This will give you a better understanding of the market and help identify the best value proposition.
- Check for Warranty and Support: Understanding the warranty and what support is offered post-purchase can save future headaches.
- Consider Ease of Installation: Systems that are easy to install can reduce initial setup costs and disruptions to operations.
- Read Reviews and Case Studies: Insights from other users can highlight potential strengths and weaknesses of different systems.
When purchasing a gravity roll on conveyor, taking the time to research and understand these factors can lead to significant savings and ensure that you invest in a system that meets your operational needs efficiently and effectively.
Gravity Roll On Roller Conveyor for Sale and Rental Options
Exploring options for acquiring a gravity roll on conveyor presents a spectrum of possibilities, from purchasing outright to opting for rental solutions. Each route offers distinct advantages and considerations, tailored to different operational needs and financial strategies. Below, we delve into where to find gravity roll on conveyors for sale, the benefits of renting, and tips for locating rental options near you.
Where to Find Gravity Roller Conveyors for Sale
Navigating the marketplace for gravity roll on conveyors presents a variety of avenues through which businesses can secure these essential components of material handling systems. Whether you’re outfitting a new facility or upgrading an existing operation, knowing where to look for gravity roller conveyors for sale is the first step towards enhancing your logistical capabilities. From direct manufacturer purchases to exploring online marketplaces, the options are plentiful, each offering unique benefits and considerations.
- Manufacturer Websites: Directly purchasing from manufacturers not only offers the latest models but also provides access to comprehensive support and customization options.
- Industrial Supply Companies: These entities often stock a wide range of material handling equipment, including gravity roll on conveyors, catering to various specifications.
- Online Marketplaces: Platforms like eBay, Alibaba, and Amazon can be valuable resources for finding both new and used conveyors.
- Trade Shows and Expos: Attending industry-specific events can provide opportunities to see the equipment in action and negotiate deals.
- Local Dealers and Distributors: Purchasing through local suppliers can facilitate easier logistics and quicker access to maintenance services.
- Auctions: Industrial auctions, both online and in-person, can be sources for acquiring gravity roll on conveyors at competitive prices.
- Refurbished Equipment Sellers: Companies specializing in refurbished or reconditioned equipment often offer quality conveyors at reduced prices.
- Industry Forums and Networks: Engaging with industry peers can lead to leads on available equipment and recommendations based on firsthand experience.
Advantages of Renting a Gravity Roller Conveyor
Opting to rent a gravity roll on conveyor can offer a strategic advantage for businesses facing variable demand, short-term projects, or those wishing to trial equipment before making a purchase. Renting provides a flexible and often cost-effective solution, allowing operations to adapt to their immediate needs without the long-term financial commitment of purchasing. Understanding the myriad benefits of renting over buying can help decision-makers choose the most efficient path for their material handling needs, ensuring operational flexibility and financial prudence.
- Cost Efficiency: Renting can be more cost-effective for short-term needs, avoiding the capital expenditure of purchasing.
- Flexibility: Rental agreements allow for adapting to fluctuating operational demands without long-term commitments.
- Maintenance and Support: Rentals typically include maintenance services, reducing the burden on your operational resources.
- Trial Opportunities: Renting offers the chance to test different models and configurations to determine the best fit for your needs before committing to a purchase.
- Quick Deployment: Rental options can be quickly deployed, ideal for meeting sudden increases in demand or project-based needs.
- No Depreciation Concerns: Renting avoids the depreciation and obsolescence issues associated with owning equipment.
- Tax Benefits: Rental payments can often be deducted as business expenses, potentially offering tax advantages.
- Access to Latest Models: Rental companies frequently update their inventory, providing access to the latest technology without a significant investment.
How to Find Gravity Roller Conveyor Rental Near You
In today’s fast-paced industrial landscape, finding a gravity roll on conveyor rental near your operation can significantly enhance your logistical efficiency, especially when immediate or short-term solutions are needed. With the right approach and resources, locating a rental service that meets your specific requirements can be straightforward. This process involves leveraging a combination of online tools, industry contacts, and local suppliers to find a rental option that offers the convenience, flexibility, and cost-effectiveness necessary to support your operational goals.
- Online Searches: Utilize search engines with specific keywords like “gravity roll on conveyor rental near me” to find local providers.
- Industry Directories: Many industry associations maintain directories of suppliers, including rental companies.
- Local Industrial Equipment Suppliers: Some suppliers offer both sales and rental options and can be a convenient local resource.
- Social Media and Forums: Industry-related groups on platforms like LinkedIn or specialized forums can offer recommendations and reviews.
- Trade Publications: Magazines and newsletters specific to the material handling industry often advertise rental services.
- Networking: Leveraging contacts within your industry can lead to personal recommendations for rental providers.
- Consulting with Manufacturers: Some manufacturers may offer rental services directly or can recommend trusted rental partners.
- Rental Service Aggregators: Websites that aggregate industrial equipment rental options can simplify the search process, offering comparisons and direct links to providers.
Choosing between purchasing and renting a gravity roll on conveyor depends on your specific operational requirements, budget constraints, and long-term business strategy. By carefully considering these options and utilizing the resources available, you can ensure that your material handling needs are met efficiently and cost-effectively.
To Customize Your Gravity Roll On Conveyor System
Tailoring a gravity roll on conveyor system to meet the unique demands of your operation can significantly enhance efficiency, productivity, and safety. Customization allows for a perfect fit with your existing processes, space, and material handling requirements. Below, we explore the myriad options available for customizing your gravity conveyor system and the critical importance of consulting with manufacturers to achieve the best custom solutions.
Options for Customizing Gravity Conveyors to Fit Specific Needs
Customizing a gravity roll on conveyor system offers a unique opportunity to tailor material handling solutions precisely to the operational requirements of a facility. This customization process goes beyond mere adaptation; it involves a strategic selection of components and features designed to optimize efficiency, enhance safety, and ensure the seamless movement of goods. From the choice of materials to the integration of advanced features, the options for customization allow businesses to address specific challenges and leverage their conveyor system as a competitive advantage. Here, we explore the diverse options available for customizing gravity conveyors, each aimed at enhancing the system’s functionality and alignment with specific operational needs.
- Adjustable Heights and Lengths: Modify the height and length of your conveyor to match specific operational areas and tasks, ensuring ergonomic and efficient material handling.
- Roller Materials and Sizes: Choose from various roller materials (steel, plastic, coated) and diameters to handle different load types and weights optimally.
- Frame Materials: Select frame materials (steel, aluminum) based on the required durability and the environment (indoor, outdoor, corrosive) in which the conveyor will operate.
- Roller Spacing: Customize the spacing between rollers to accommodate the size and stability of the goods being transported, preventing slippage or damage.
- Curve and Corner Modules: Incorporate curved sections and corners to navigate facility layouts effectively, maintaining smooth product flow.
- Side Guides and Rails: Add adjustable side guides and rails to keep products aligned during transport, especially useful for irregularly shaped items.
- Stops and Gates: Implement manual or automatic stops and gates for controlled product flow, accumulation, and access points along the conveyor path.
- Mobile and Flexible Options: Opt for mobile units with casters or flexible conveyors that can be extended, curved, or contracted, offering versatility in dynamic operational environments.
Importance of Consulting with Manufacturers for Custom Solutions
Engaging with manufacturers in the customization of your gravity roll on conveyor system is not just a step in the process—it’s a partnership that can significantly impact the success of your material handling strategy. Manufacturers bring a wealth of knowledge, experience, and resources to the table, offering insights that can transform a standard conveyor setup into a highly efficient, customized solution. This collaboration ensures that every aspect of the conveyor system is optimized for the unique demands of your operation, from throughput capacity to spatial constraints. Consulting with manufacturers for custom solutions is about leveraging expertise to achieve not just a functional conveyor system, but one that is precisely tuned to enhance operational efficiency and productivity.
- Expertise and Experience: Manufacturers possess deep knowledge of material handling challenges and solutions, guiding you to the most effective customizations for your needs.
- Compatibility: Ensure that custom components integrate seamlessly with existing systems, maintaining or enhancing operational efficiency.
- Innovation: Benefit from the latest advancements in conveyor technology and materials, which manufacturers can incorporate into your customized solution.
- Cost-Effectiveness: Manufacturers can advise on the most cost-effective customizations, balancing performance needs with budget constraints.
- Safety Compliance: Custom solutions designed by manufacturers will comply with industry safety standards, protecting your workforce and operations.
- Warranty and Support: Customized systems provided by manufacturers typically come with warranties and ongoing support, offering peace of mind.
- Scalability: Manufacturers can design custom solutions with future expansion in mind, ensuring your system can grow with your business.
- Efficiency Optimization: Through consultation, manufacturers can identify potential bottlenecks or inefficiencies in your current system and tailor solutions to address these issues directly.
Customizing your gravity roll on conveyor system is a strategic investment in your operation’s efficiency and adaptability. By working closely with manufacturers, you can leverage their expertise to develop a tailored solution that meets your specific needs, ensuring that your material handling processes are as efficient, safe, and cost-effective as possible.
Roller Conveyor Design PDF Resources for Gravity Roll On Systems
In the quest to design or enhance a gravity roll on conveyor system, access to comprehensive resources and guides is invaluable. These materials not only deepen understanding but also provide practical insights into the intricacies of conveyor design. Below, we explore a selection of PDF resources that are instrumental in planning and implementing effective gravity conveyor systems.
Key PDF Resources for Understanding Gravity Roll On Conveyor Design
Embarking on the journey to design or refine a gravity roll on conveyor system necessitates a deep dive into specialized knowledge and best practices. Fortunately, a wealth of PDF resources is available, offering everything from foundational principles to advanced design techniques. These documents serve as essential tools for engineers, designers, and operational managers, providing the insights needed to navigate the complexities of conveyor system design. By exploring these key resources, professionals can ensure their gravity conveyor systems are not only efficient and effective but also aligned with industry standards and innovations.
- Industry Standards and Guidelines: Documents detailing industry standards offer foundational knowledge on safety, design criteria, and operational efficiency for gravity roll on systems.
- Manufacturer Design Manuals: Specific manuals provided by conveyor manufacturers contain detailed specifications, installation instructions, and customization options.
- Technical Design Guides: Comprehensive guides that delve into the engineering principles behind conveyor design, including calculations for load capacities, roller spacing, and material selection.
- Case Studies: Real-world examples of conveyor system implementations, highlighting challenges, solutions, and outcomes, offering practical insights.
- Maintenance and Troubleshooting Manuals: Resources focusing on the upkeep of gravity roll on conveyors, including routine maintenance schedules and troubleshooting common issues.
- Innovation and Trends Reports: Documents exploring new materials, technologies, and trends in conveyor design, providing a glimpse into future possibilities.
- Safety Protocols and Procedures: Guides dedicated to ensuring the safe operation of conveyor systems, including ergonomic considerations and hazard prevention.
- Customization and Modification Guides: Resources that offer guidance on how to tailor standard conveyor systems to meet specific operational needs, enhancing functionality and efficiency.
How These Resources Can Help in Planning and Implementing Gravity Conveyor Systems
The strategic planning and implementation of gravity conveyor systems are critical processes that determine the efficiency, safety, and productivity of material handling operations. Leveraging the right PDF resources can transform these tasks from daunting challenges into manageable projects. These documents offer a structured approach to understanding the nuances of conveyor design, ensuring that every decision—from the initial concept to the final installation—is informed and deliberate. By utilizing these resources, businesses can optimize their conveyor systems for peak performance, ensuring they meet both current needs and future demands.
Access to a diverse range of roller conveyor design PDF resources for gravity roll on systems empowers businesses to make informed decisions throughout the planning and implementation phases. These resources serve as a bridge between theoretical knowledge and practical application, ensuring that conveyor systems are not only designed for optimal performance but are also safe, compliant, and tailored to meet the unique challenges of each operational environment.
FAQs about Gravity Roll On
Gravity roller conveyors utilize the natural force of gravity to move goods along the conveyor path without the need for an external power source. This type of conveyor consists of rollers mounted on a slight incline, allowing items placed at the higher end to roll down to the lower end smoothly. The rollers reduce friction and facilitate the easy movement of goods, making gravity roller conveyors an efficient, cost-effective solution for transporting items across short to medium distances within warehouses, distribution centers, and manufacturing facilities. The simplicity of their design not only minimizes maintenance requirements but also makes them adaptable to various operational layouts and needs. By leveraging gravity, these conveyors offer an eco-friendly alternative to powered systems, reducing energy consumption and operational costs.
The spacing between rollers on a conveyor, also known as roller pitch, is a critical design aspect that influences the conveyor’s ability to transport goods effectively. The optimal spacing depends on the size and type of items being moved; generally, the rule of thumb is that the conveyed item should span at least three rollers at any given time. This ensures stability and prevents items from getting stuck or tipping over. For smaller items, rollers are placed closer together, while larger, heavier items can be accommodated with wider spacing. The specific spacing is determined based on the load characteristics, with common intervals ranging from 1.5 inches to 6 inches or more, depending on the application. Consulting with conveyor manufacturers or utilizing design guides can help determine the ideal roller spacing for a particular operation, ensuring efficient and smooth conveyor performance.
Roller conveyors come in various types to suit different operational needs and material handling requirements. The primary types include:
Gravity Roller Conveyors: Use gravity to move items, ideal for short distances and light to medium loads.
Powered Roller Conveyors: Equipped with motors to drive the rollers, suitable for heavier loads and longer distances.
Flexible Roller Conveyors: Feature segments that can be extended, curved, or contracted, offering versatility in layout and handling.
Accumulation Conveyors: Allow items to accumulate without pressure, using mechanisms to control the flow and prevent damage.
Curve Roller Conveyors: Designed to navigate corners, maintaining continuous flow around bends.
Incline/Decline Conveyors: Facilitate movement up or down between different levels, with rollers aiding in controlled descent or ascent.
Pallet Conveyors: Specifically designed to handle pallets, with robust rollers and frames to support heavy loads.
Each type offers unique advantages, with selection based on factors such as load type, operational layout, and specific handling requirements. Understanding the distinctions between these conveyor types is crucial for optimizing material handling processes.
A power conveyor, also known as a motorized or powered conveyor, is a material handling system equipped with motors that drive the movement of the conveyor belt or rollers. Unlike gravity conveyors that rely on inclines and gravity to move goods, power conveyors use electric motors to transport items across flat surfaces, up inclines, or around curves, providing greater control over speed and product flow. Power conveyors are versatile and can be designed to handle a wide range of items, from small packages to large pallets, making them suitable for various industries, including manufacturing, warehousing, and distribution. They can be customized with features like accumulation zones, sorting mechanisms, and adjustable speeds to meet specific operational needs. Power conveyors offer the advantage of automating material handling processes, improving efficiency, reducing manual labor, and enhancing overall productivity in facilities.
Last Updated on May 21, 2024 by Jordan Smith
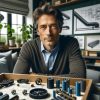
Jordan Smith, a seasoned professional with over 20 years of experience in the conveyor system industry. Jordan’s expertise lies in providing comprehensive solutions for conveyor rollers, belts, and accessories, catering to a wide range of industrial needs. From initial design and configuration to installation and meticulous troubleshooting, Jordan is adept at handling all aspects of conveyor system management. Whether you’re looking to upgrade your production line with efficient conveyor belts, require custom conveyor rollers for specific operations, or need expert advice on selecting the right conveyor accessories for your facility, Jordan is your reliable consultant. For any inquiries or assistance with conveyor system optimization, Jordan is available to share his wealth of knowledge and experience. Feel free to reach out at any time for professional guidance on all matters related to conveyor rollers, belts, and accessories.