Innovations in Gravity Roller Bearings Technology
Gravity roller bearings play a pivotal role in the seamless operation of conveyor systems, serving as the backbone for material handling and logistics across various industries. These bearings are specifically designed to facilitate the movement of goods with minimal effort, leveraging the force of gravity to propel items along the conveyor belt. This not only enhances efficiency but also significantly reduces the energy costs associated with mechanical conveyance. The significance of gravity roller bearings extends beyond their functional benefits; they are instrumental in optimizing workflow, minimizing downtime, and ensuring the smooth transit of products from one point to another. Their application is vast, ranging from manufacturing assembly lines to distribution centers, where the reliable and efficient transportation of goods is paramount. Understanding the role and functionality of gravity roller bearings is essential for anyone involved in the design, operation, or maintenance of conveyor systems, highlighting their indispensable contribution to modern material handling and logistics.
What Are Gravity Roller Bearings
Gravity roller bearings are a fundamental component in the design of conveyor systems, enabling the smooth and efficient transportation of goods across various industries. These bearings are specifically engineered to utilize gravitational forces, facilitating the movement of items without the need for motor power or manual effort. Here’s a detailed look at the definition and basic mechanics of gravity roller bearings:
- Definition: Gravity roller bearings are designed to fit within the roller tubes of conveyor systems, providing a low-friction surface that allows the rollers to move smoothly under the weight of the items being transported.
- Functionality: They work by allowing the conveyor rollers to rotate freely, minimizing the amount of force required to move objects down the line.
- Material: Typically made from durable materials such as steel, stainless steel, or plastic, these bearings are built to withstand heavy loads and continuous operation.
- Design Variability: Available in various sizes and designs to accommodate different roller diameters and load requirements.
- Maintenance: Designed for easy maintenance, gravity roller bearings can be replaced or serviced without significant downtime, ensuring consistent operational efficiency.
- Energy Efficiency: By leveraging gravity, these bearings contribute to energy savings, reducing the need for electrical power in conveyor systems.
- Cost-Effectiveness: They offer an economical solution for material handling, thanks to their simple design and the elimination of complex machinery.
- Versatility: Suitable for a wide range of applications, from light-duty packaging lines to heavy-duty industrial material handling.
To highlight the unique features and benefits of gravity roller bearings compared to other types of conveyor bearings, the following table provides a comparative analysis:
This comparison underscores the distinct advantages of gravity roller bearings, emphasizing their efficiency, cost-effectiveness, and versatility in a wide range of material handling scenarios.
Types of Conveyor Bearings, Including Gravity Roller Bearings
Conveyor systems rely on various types of bearings to ensure smooth and efficient operation. Among these, gravity roller bearings stand out for their simplicity and effectiveness. This section delves into the different conveyor bearing types, with a special focus on gravity roller bearings, and discusses other common types of bearings used in conveyor systems.
Gravity Roller Bearings
Gravity roller bearings are a cornerstone of material handling systems, designed to facilitate the movement of goods using the force of gravity. These bearings are integral to gravity roller conveyors, which are among the most straightforward and cost-effective conveyor types available. Here are six types of conveyor bearings, highlighting the unique position of gravity roller bearings:
- Gravity Roller Bearings: Characterized by their ability to facilitate movement without external power, gravity roller bearings are ideal for a variety of applications, from light-duty packaging to heavy-duty industrial transport.
- Precision Bearings: These are designed for applications requiring high accuracy and speed. Precision bearings offer reduced friction and higher efficiency but at a higher cost compared to gravity roller bearings.
- Non-Precision Bearings: More economical than precision bearings, non-precision bearings are suitable for applications where high speeds and tight tolerances are not critical. They are commonly used in standard conveyor systems.
- Ball Bearings: Utilized in roller conveyors for smooth operation. Ball bearings can support both radial and axial loads, making them suitable for a wide range of applications beyond just conveyor systems.
- Tapered Roller Bearings: Designed to handle large radial and axial loads, tapered roller bearings are ideal for heavy-duty applications. Their unique shape allows them to efficiently manage forces and provide stability.
- Spherical Roller Bearings: These bearings can accommodate misalignment and are suitable for applications involving heavy loads and moderate speeds. Spherical roller bearings are often used in belt conveyor rollers.
Other Common Types of Bearings in Conveyor Systems
Beyond gravity roller bearings, conveyor systems utilize a variety of bearings, each selected based on the specific requirements of the application. Here are expanded details on common types of bearings used in conveyor systems:
- Precision and Non-Precision Bearings: Precision bearings are designed for applications that require high accuracy, such as in high-speed conveyor systems where minimal friction and maximum efficiency are critical. They are manufactured to tight tolerances and can significantly reduce energy consumption. Non-precision bearings, on the other hand, are suited for applications where speeds are moderate, and precision is less critical. They are a cost-effective solution for many standard conveyors, offering reliability without the expense of high-precision engineering.
- Ball Bearings: These are among the most versatile and widely used bearings in conveyor systems. Ball bearings are capable of handling both radial (perpendicular to the shaft) and axial (parallel to the shaft) loads, making them suitable for a variety of applications. Their design allows for smooth operation with minimal friction, contributing to longer conveyor system life and reduced maintenance costs. Ball bearings are available in sealed and shielded versions to protect against contaminants and extend bearing life.
- Tapered Roller Bearings: Ideal for applications that experience heavy radial and axial loads, tapered roller bearings are engineered to handle significant forces. This makes them particularly valuable in heavy-duty conveyor systems used in mining, aggregate, and other industrial applications. The conical shape of the rollers allows the bearing to efficiently manage forces and provide stability under high-load conditions, ensuring reliable operation and longevity.
- Spherical Roller Bearings: These bearings are designed to accommodate shaft misalignment while handling high radial loads and moderate axial loads. Spherical roller bearings are especially useful in belt conveyor systems where misalignment might be a common issue due to uneven loading or installation inaccuracies. Their ability to self-align makes them indispensable in maintaining operational efficiency and reducing wear on the conveyor system.
- Cylindrical Roller Bearings: Characterized by their cylindrical shape, these bearings offer a higher radial load capacity than ball bearings, making them suitable for high-load applications. Cylindrical roller bearings are commonly used in belt conveyors and heavy-duty roller conveyors where high load capacity is essential. Their design allows for slight axial movement of the shaft in relation to the housing, accommodating thermal expansion and contraction.
- Needle Roller Bearings: Needle roller bearings are designed with small diameter cylindrical rollers, allowing them to handle high loads in a compact design. This makes them ideal for applications where space is limited but high load capacity is required. Their compact size and high load-bearing capacity make needle roller bearings suitable for use in conveyor systems where space efficiency is a priority, such as in automated material handling systems.
Each of these bearing types plays a crucial role in the design and function of conveyor systems, chosen based on specific operational requirements, including load capacity, speed, precision, and environmental conditions. Understanding the characteristics and applications of these bearings is essential for optimizing conveyor system performance and reliability.
Key Features of Gravity Roller Bearings
Gravity roller bearings are integral to the functionality and efficiency of conveyor systems, especially in settings where the power-free movement of goods is a priority. Their design and operation principles make them a preferred choice for a wide range of material handling applications. Below, we delve into the characteristics of gravity roller bearings, highlighting their material composition, load capacity, temperature range, and more. Additionally, we explore the critical importance of axle size, tube size, and bearing fit in the selection and performance of these bearings.
Characteristics of Gravity Roller Bearings
Gravity roller bearings are distinguished by several key characteristics that make them suitable for various applications in material handling and conveyor systems. These features ensure that gravity roller bearings can provide reliable service under a wide range of conditions:
- Material Composition: Typically constructed from durable materials such as steel, stainless steel, or high-grade plastics, gravity roller bearings are built to last and resist wear in diverse environments.
- Load Capacity: Designed to accommodate a spectrum of load capacities, these bearings can handle everything from lightweight packages to heavy industrial components, offering flexibility across different industries.
- Temperature Range: Capable of operating efficiently across a wide temperature range, gravity roller bearings are suitable for use in environments from freezing cold storage to hot industrial processes.
- Low Friction: The bearings are engineered to minimize friction, facilitating smoother conveyor operations and reducing the manual effort needed to move goods.
- Ease of Installation and Replacement: Their straightforward design allows for quick installation and easy replacement, minimizing downtime and maintenance costs.
- Energy Efficiency: Leveraging gravity to move goods, these bearings contribute to energy savings by eliminating the need for powered conveyor systems in many applications.
- Noise Reduction: Gravity roller bearings operate quietly, making them ideal for use in noise-sensitive environments such as retail spaces and office warehouses.
- Corrosion Resistance: Many gravity roller bearings are manufactured with materials or coatings that resist corrosion, enhancing their durability in harsh conditions.
Importance of Axle Size, Tube Size, and Bearing Fit
Selecting the correct axle size, tube size, and bearing fit is crucial for optimizing the performance and longevity of gravity roller bearings within conveyor systems. These factors directly impact the efficiency, maintenance frequency, and operational cost of the conveyor system:
- Axle Size Compatibility: Ensuring that the axle size matches the bearing is vital for a secure fit and optimal performance. Incompatibility can lead to increased wear and potential failure of the bearing.
- Tube Size Consideration: The bearing must be compatible with the roller tube’s inner diameter to ensure even load distribution and prevent premature wear or operational inefficiencies.
- Bearing Fit Precision: A precise fit is essential to prevent slippage and misalignment, which can degrade the conveyor’s efficiency and increase maintenance needs.
- Load Distribution: Proper selection based on axle and tube size ensures even load distribution across the bearing, maximizing its capacity and lifespan.
- Operational Smoothness: The right combination of axle size, tube size, and bearing fit contributes to the smooth and efficient operation of the conveyor system.
- Customization Options: For specific applications, customized bearings may be necessary to meet unique operational requirements, including special axle sizes, tube diameters, or materials.
- Selection for Specific Environments: The operational environment, such as exposure to corrosive materials or extreme temperatures, may influence the choice of axle size, tube size, and bearing fit, ensuring optimal performance and durability.
Understanding and addressing these key features and considerations is crucial when selecting gravity roller bearings for conveyor systems. Making informed choices in these areas ensures the conveyor system operates efficiently, reliably, and with minimal maintenance over its lifespan.
Replacing Gravity Roller Bearings in Conveyor Systems
Maintaining the optimal performance of conveyor systems is crucial for operational efficiency and longevity. A key aspect of this maintenance involves the timely replacement of gravity roller bearings. These components are pivotal in ensuring the smooth and efficient operation of the conveyor, but they can wear down over time due to various factors. Recognizing when and why to replace these bearings, followed by a detailed, step-by-step replacement process, is essential for minimizing downtime and maintaining productivity.
When and Why to Replace Gravity Roller Bearings
The decision to replace gravity roller bearings should not be taken lightly, as it directly impacts the conveyor system’s efficiency and safety. Several indicators and conditions necessitate this replacement:
- Excessive Noise: A clear sign that bearings may be failing is an increase in operational noise, indicating wear or damage.
- Reduced Movement Efficiency: Difficulty in roller movement or a noticeable decrease in efficiency often points to bearing issues.
- Visible Wear and Tear: Physical deterioration, such as rust or visible damage to the bearing, signals the need for immediate replacement.
- Routine Maintenance Schedule: Adhering to a predetermined maintenance schedule can prevent unexpected failures by replacing bearings before they fail.
- Increased Friction: An increase in resistance when rollers are moved indicates that the bearings are no longer functioning smoothly.
- Load Capacity Changes: Adjustments in the system’s load requirements might necessitate the use of bearings with a different capacity.
- Operational Environment Changes: Environmental changes, such as increased exposure to dust, moisture, or chemicals, can degrade bearings more quickly.
- Age of the Conveyor System: Over time, bearings will naturally wear out, even under normal use conditions, requiring their replacement.
Understanding these triggers for replacement is crucial in maintaining the operational integrity and efficiency of conveyor systems.
Step-by-Step Instructions on Replacing Gravity Roller Bearings
Replacing gravity roller bearings is a straightforward process that, when done correctly, can significantly extend the life of a conveyor system. Here’s how to approach this task methodically:
- Safety First: Always start by ensuring the conveyor system is powered down and locked out to prevent accidental startup during maintenance.
- Remove the Roller: Detach the roller from the conveyor frame, which might involve loosening or removing fasteners or brackets.
- Access the Bearings: Open the roller to reach the bearings. This step may require removing end caps or retaining rings.
- Remove the Old Bearings: Extract the old bearings from the axle, using a bearing puller if necessary to overcome tight fits.
- Clean the Axle and Roller: Prior to installing new bearings, thoroughly clean the axle and the interior of the roller to ensure no debris interferes with the new bearings.
- Install New Bearings: Carefully position the new gravity roller bearings onto the axle, making sure they fit snugly within the roller.
- Reassemble the Roller: Reattach any components removed during disassembly, ensuring a secure fit to prevent future issues.
- Test the Roller: Manually check the roller’s movement to verify the smooth operation of the new bearings before reinstalling it into the system.
- Reinstall the Roller: Place the roller back into its position on the conveyor frame, securing it firmly with the original fasteners or brackets.
- Operational Test: After the conveyor system is unlocked and powered back on, observe the replaced roller to ensure it integrates seamlessly with the system’s operation.
Following these guidelines for replacing gravity roller bearings not only ensures the maintenance is performed safely but also contributes to the conveyor system’s reliability and efficiency. Regular inspections and timely replacements are key to avoiding unexpected downtime and prolonging the lifespan of the conveyor system.
Gravity Roller Bearings for Sale
Selecting the right gravity roller bearings is a critical step in ensuring the efficiency and longevity of conveyor systems. These bearings are designed to facilitate the movement of conveyor rollers, enabling the smooth transportation of goods across various industries. The process of choosing the appropriate bearings involves understanding specific operational requirements and the unique challenges of your conveyor system. Below, we provide essential tips to guide you in selecting the most suitable gravity roller bearings for your needs.
Tips on Selecting the Right Gravity Roller Bearings
Selecting gravity roller bearings requires careful consideration of several factors to ensure optimal performance and durability:
- Analyze Load Capacities: Understanding the weight of materials the conveyor will handle is crucial in selecting bearings that can support the load without premature wear.
- Environmental Conditions: Bearings should be chosen with the operating environment in mind, especially if they will be exposed to extreme temperatures, moisture, or corrosive substances.
- Service Life Expectations: Consider the expected lifespan of the conveyor system and select bearings that offer a corresponding durability.
- Operational Speeds: The speed at which the conveyor operates can influence the type of bearings needed, as some are better suited to high-speed applications than others.
- Material Suitability: The materials of both the bearings and the conveyed goods should be compatible to prevent contamination or damage.
- Maintenance Requirements: Opt for bearings that are easy to maintain or replace to reduce system downtime.
- Accuracy in Sizing: Ensuring the bearings fit perfectly within the roller tubes is vital for maintaining efficiency and preventing malfunctions.
- Expert Advice: When in doubt, seek advice from industry experts or manufacturers to find the best bearing options for your specific conveyor system.
Reputable Manufacturers and Suppliers
Choosing a reputable manufacturer or supplier is as important as selecting the right bearings. Here are some industry leaders known for their quality and reliability, along with what sets them apart:
- Frantz Bearings: Frantz stands out for its extensive experience and dedication to producing high-quality gravity roller bearings that offer reliability and durability for various applications.
- SKF: A global leader in the bearing industry, SKF is renowned for its innovative bearing solutions and commitment to research and development, ensuring high performance and efficiency.
- Timken: With a focus on longevity and performance, Timken’s bearings are engineered for precision and durability, making them ideal for demanding industrial environments.
- NSK: NSK bearings are celebrated for their precision engineering and quality, backed by extensive research and technological advancement, suitable for a wide range of applications.
- NTN: NTN offers a broad array of bearing solutions, including options for unique and challenging applications, emphasizing versatility and innovation.
- Rexnord: Known for heavy-duty bearing solutions, Rexnord provides products that excel in performance and reliability, even in the most challenging conditions.
- Regal Beloit: Through brands like McGill and Sealmaster, Regal Beloit offers customized bearing solutions, ensuring a perfect fit for specific operational needs, backed by comprehensive technical support.
What to Look for When Purchasing
In addition to quality certifications, technical support, and warranty, here are more factors to consider when purchasing gravity roller bearings:
- Compatibility with Existing Systems: Ensure the bearings are compatible with your current conveyor setup to avoid integration issues.
- Innovative Features: Look for bearings with innovative features that can enhance performance, such as self-lubricating materials or integrated sensors for condition monitoring.
- Supplier Reputation: Research the supplier’s reputation in the market, including customer reviews and industry endorsements, to gauge reliability and service quality.
- Delivery and Logistics: Consider the supplier’s ability to meet your delivery timelines and the logistics of shipping and handling, especially for large or urgent orders.
- Cost-Effectiveness: While quality should not be compromised, compare prices and terms from different suppliers to ensure you are getting the best value for your investment.
- Environmental Sustainability: Consider manufacturers that adhere to sustainable practices and offer eco-friendly products, aligning with corporate social responsibility goals.
By carefully considering these additional factors, along with the insights from reputable manufacturers and detailed selection tips, you can ensure the successful integration of gravity roller bearings into your conveyor system, enhancing its performance and reliability.
Conveyor Bearings Hex Bore and Other Configurations for Gravity Roller Bearings
The versatility of gravity roller bearings is evident in the variety of bore configurations available to meet diverse operational needs. Among these, hex bore bearings stand out for their unique advantages in conveyor roller applications. This section explores the benefits of hex bore bearings and provides an overview of other bearing configurations, highlighting their respective applications without overlapping with the previously discussed content.
Hex Bore Bearings and Their Advantages
Hex bore bearings are designed with a hexagonal inner ring that matches a hexagonal axle or shaft, providing a secure fit that prevents rotation of the bearing on the shaft. This configuration is particularly beneficial for gravity roller bearings in conveyor systems due to several key advantages:
- Secure Fit: The hexagonal shape ensures a tight fit, reducing slippage and wear on the shaft.
- Easy Installation: Hex bore bearings are straightforward to install, as their shape naturally aligns with the hex shaft.
- High Torque Transmission: The secure engagement between the bearing and shaft allows for efficient torque transmission, ideal for applications requiring precise control.
- Reduced Maintenance: The secure fit minimizes the need for frequent adjustments, leading to lower maintenance requirements.
- Improved Load Distribution: The hexagonal contact surface provides better load distribution across the bearing, enhancing its load-bearing capacity.
- Versatility in Applications: Suitable for various applications, from light-duty conveyors to heavy-duty material handling systems.
- Enhanced Durability: The design reduces the risk of deformation under high loads, contributing to the bearing’s longevity.
- Quick Replacement: The hex bore configuration facilitates easy removal and replacement, minimizing downtime during maintenance.
Other Bearing Configurations and Their Applications
Beyond hex bore bearings, several other configurations are utilized in gravity roller bearings to accommodate different operational requirements and applications:
- Round Bore Bearings: The most common configuration, suitable for a wide range of conveyor systems with standard round shafts, offering ease of installation and versatility.
- Square Bore Bearings: Used in applications requiring a secure fit for square shafts, preventing rotation and providing high load capacity.
- Flanged Bearings: Incorporate a flange on the outer ring, preventing axial movement and simplifying assembly in conveyor rollers.
- Extended Inner Ring Bearings: Feature an extended inner ring that provides additional surface area for securing to the shaft, ideal for applications where side loads are prevalent.
- Sealed Bearings: Equipped with seals to protect against contaminants and lubricant leakage, extending the life of the bearing in dirty or harsh environments.
- Shielded Bearings: Have metal shields that offer protection from debris while allowing for lubricant retention, suitable for environments where minimal contamination occurs.
- Stainless Steel Bearings: Offer corrosion resistance for applications in wet or corrosive environments, ensuring durability and reliability.
- Plastic Bearings: Provide a lightweight, corrosion-resistant option for light-duty applications or environments where metal bearings are unsuitable.
Each bearing configuration offers unique advantages tailored to specific operational needs and environments. Understanding these configurations and their applications is crucial for selecting the right gravity roller bearings for your conveyor system, ensuring optimal performance and longevity.
Conveyor Roller Bearing Housing for Gravity Roller Bearings
The housing of a bearing plays a pivotal role in the performance and durability of gravity roller bearings within conveyor systems. It not only supports the bearing but also protects it from environmental contaminants and helps maintain alignment and load distribution. This section delves into the significance of bearing housing in enhancing the functionality of gravity roller bearings and outlines various types of bearing housings along with their specific applications.
Importance of Bearing Housing
Bearing housing is crucial for several reasons, significantly impacting the longevity and efficiency of gravity roller bearings:
- Protection: It shields the bearings from dust, debris, and other environmental contaminants that can degrade performance and shorten lifespan.
- Load Support: Proper housing provides a stable platform that supports axial and radial loads, ensuring the bearing operates within its designed load parameters.
- Alignment: Housing helps maintain the correct alignment of the bearing, reducing stress and uneven wear.
- Lubrication Containment: It often contains a lubrication system that ensures the bearing is consistently lubricated, reducing friction and wear.
- Heat Dissipation: Good housing design can aid in dissipating heat generated by the bearing during operation, preventing overheating and potential damage.
Different Types of Bearing Housings and Their Applications
Various bearing housing types are designed to meet the diverse needs of conveyor systems and the specific challenges they face:
- Pillow Block Housings: These are the most common type of bearing housing, mounted on surfaces parallel to the shaft axis. They are ideal for applications where the conveyor needs support from below and are easy to install and maintain.
- Flanged Housings: These housings are equipped with flanges that allow for mounting on vertical surfaces. They are suitable for conveyors that require side-mounted support, providing stability and load support in multiple directions.
- Take-up Housings: Used in tensioning conveyor belts, take-up housings allow for adjustment in the position of the bearings to maintain belt tension. This is crucial for preventing slippage and ensuring smooth operation.
- Split Housings: Designed for ease of installation and maintenance, split housings are divided into two pieces, allowing them to be placed around the shaft without disassembling the conveyor. They are ideal for applications where bearing replacement is challenging due to space constraints or operational demands.
- Plummer Block Housings: Similar to pillow blocks but designed to accommodate larger bearings, plummer blocks are used in heavy-duty applications where robust support and alignment are critical.
- Cartridge Housings: These housings enclose the bearing completely, offering high levels of protection against contaminants and external impacts. Cartridge housings are used in environments where the bearing is exposed to harsh conditions.
Each type of bearing housing offers unique advantages tailored to specific operational needs, from simple support and alignment to protection against harsh environmental conditions. Selecting the appropriate housing is as crucial as choosing the right gravity roller bearings, ensuring the conveyor system operates efficiently, reliably, and with minimal maintenance over its lifespan.
Additional Components: Conveyor Rollers and Belt Conveyor Rollers with Gravity Roller Bearings
The integration of gravity roller bearings into conveyor systems significantly enhances their efficiency, reliability, and functionality. This section delves deeper into the role of conveyor rollers in optimizing the performance of gravity roller bearings, outlines the differences between gravity rollers and belt conveyor rollers through a comparative table, and explains how these components complement each other within conveyor systems.
Role of Conveyor Rollers in the Efficiency of Gravity Roller Bearings
Conveyor rollers equipped with gravity roller bearings play a crucial role in the efficiency and smooth operation of conveyor systems:
- Reduced Friction: Gravity roller bearings minimize friction, allowing rollers to move smoothly and effortlessly, which reduces the energy required for operation.
- Enhanced Durability: The robust design of gravity roller bearings extends the lifespan of conveyor rollers, leading to lower replacement costs and maintenance needs.
- Improved Load Handling: Bearings enable rollers to handle varying loads efficiently, ensuring consistent performance across diverse applications.
- Versatility: The adaptability of gravity roller bearings to different environments and operational requirements makes them suitable for a wide range of conveyor systems.
- Energy Savings: By facilitating smooth roller movement, these bearings contribute to energy savings, especially in systems where gravity assists in material transport.
- Ease of Maintenance: The simple design of gravity roller bearings allows for easy maintenance and replacement, minimizing downtime.
Differences Between Gravity Rollers and Belt Conveyor Rollers
The table below highlights the key differences between gravity rollers and belt conveyor rollers, showcasing their unique features and applications:
The comparison between gravity rollers and belt conveyor rollers underscores the diversity of conveyor system components and their tailored applications to specific operational needs. Gravity rollers, driven by the force of gravity and requiring minimal mechanical intervention, offer a cost-effective and efficient solution for moving goods, especially in scenarios where manual loading and unloading are prevalent. Their simplicity, ease of maintenance, and energy efficiency make them an ideal choice for many material handling tasks.
How They Complement Each Other in Conveyor Systems
Integrating gravity rollers and belt conveyor rollers within the same system offers a comprehensive material handling solution:
- Strategic Placement: Gravity rollers can be used in areas where manual intervention is common, while belt conveyor rollers are ideal for automated sections.
- Energy Efficiency: Combining the low-energy requirements of gravity rollers with the controlled movement of belt conveyor rollers optimizes overall energy use.
- Operational Flexibility: This hybrid approach allows for the handling of a wide variety of goods and operational scenarios, enhancing system versatility.
- Cost-Effectiveness: Gravity rollers can reduce operational costs in certain sections of the conveyor, while belt conveyor rollers add value where precise control is needed.
- Load Distribution: Using gravity rollers for lighter loads and belt conveyor rollers for heavier or more delicate items ensures optimal load distribution.
- System Scalability: The combination of both types of rollers makes it easier to scale the system up or down based on changing operational requirements.
By leveraging the strengths of both gravity rollers and belt conveyor rollers, conveyor systems can achieve unparalleled efficiency, adaptability, and performance, meeting the diverse needs of modern material handling operations.
Last Updated on February 28, 2024 by Jordan Smith
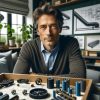
Jordan Smith, a seasoned professional with over 20 years of experience in the conveyor system industry. Jordan’s expertise lies in providing comprehensive solutions for conveyor rollers, belts, and accessories, catering to a wide range of industrial needs. From initial design and configuration to installation and meticulous troubleshooting, Jordan is adept at handling all aspects of conveyor system management. Whether you’re looking to upgrade your production line with efficient conveyor belts, require custom conveyor rollers for specific operations, or need expert advice on selecting the right conveyor accessories for your facility, Jordan is your reliable consultant. For any inquiries or assistance with conveyor system optimization, Jordan is available to share his wealth of knowledge and experience. Feel free to reach out at any time for professional guidance on all matters related to conveyor rollers, belts, and accessories.